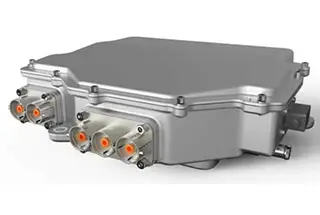
¿Alguna vez se ha preguntado qué impulsa la precisión y la automatización de la fabricación moderna? En este artículo, nos sumergimos en el mundo de los sistemas CNC, el cerebro de las máquinas que dan forma a nuestro mundo. Descubra los 10 principales sistemas CNC que están revolucionando las industrias, a medida que exploramos sus características, beneficios y las tecnologías de vanguardia que los distinguen. Prepárese para descubrir los secretos de las máquinas que están impulsando la innovación y la eficiencia en la fabricación actual.
Las máquinas CNC de control en bucle abierto funcionan sin mecanismos de realimentación. Estos sistemas se basan únicamente en señales de entrada para controlar los movimientos de la máquina. Debido a la ausencia de realimentación en tiempo real, suelen ser menos costosos, pero tienden a tener menor precisión y estabilidad. Los sistemas de bucle abierto son adecuados para aplicaciones más sencillas, como proyectos básicos de carpintería o de aficionados, en los que la precisión no es crítica. Por ejemplo, una máquina de grabado a pequeña escala utilizada para manualidades puede utilizar eficazmente un sistema de control de bucle abierto.
Las máquinas CNC de control en bucle cerrado incorporan mecanismos de realimentación que supervisan y ajustan continuamente las operaciones de la máquina basándose en datos en tiempo real. Este bucle de realimentación permite una mayor exactitud y precisión, por lo que estos sistemas son ideales para aplicaciones de alta precisión. Son más caros, pero ofrecen un rendimiento y una fiabilidad superiores. Industrias como la aeroespacial y la automovilística, en las que la precisión es primordial, suelen utilizar sistemas CNC de bucle cerrado. Por ejemplo, una fresadora CNC de bucle cerrado puede producir intrincados componentes aeroespaciales con tolerancias muy ajustadas.
Los sistemas de contorneado están diseñados para seguir trayectorias y formas complejas, lo que permite a la máquina CNC realizar cortes y movimientos intrincados. Estos sistemas son esenciales para producir componentes detallados y precisos. Por ejemplo, en la industria de la joyería, los sistemas de contorneado se utilizan para crear grabados detallados y diseños complejos en superficies metálicas.
Los sistemas de control punto a punto desplazan los componentes de la máquina con precisión entre puntos concretos. Este tipo de control es adecuado para operaciones como el taladrado o el roscado, en las que la herramienta debe desplazarse con precisión de una ubicación a otra sin seguir una trayectoria continua. Un ejemplo es una taladradora CNC utilizada en la fabricación de placas de circuitos impresos (PCB), donde la colocación precisa de los orificios es crucial.
El control del avance regula la velocidad a la que se mueven las herramientas de corte, garantizando la calidad del corte y evitando daños en la herramienta o la pieza. Un control adecuado del avance ayuda a optimizar el proceso de mecanizado equilibrando velocidad y precisión. Por ejemplo, en el mecanizado de metales, el ajuste de la velocidad de avance puede evitar el sobrecalentamiento y el desgaste de la herramienta, garantizando un acabado más suave en el producto final.
Las máquinas CNC de 2 ejes funcionan a lo largo de los ejes X e Y, lo que las hace adecuadas para tareas sencillas como taladrar agujeros o cortar líneas rectas. Estas máquinas suelen utilizarse en aplicaciones en las que solo se requieren movimientos bidimensionales, como el corte de formas básicas a partir de láminas.
Las máquinas CNC de 3 ejes añaden un eje Z que permite controlar la profundidad y realizar operaciones básicas de mecanizado tridimensional. Estas máquinas se utilizan normalmente para fresar, taladrar y otras operaciones que requieren movimiento en tres dimensiones. Un ejemplo es una fresadora CNC de 3 ejes utilizada en carpintería para crear tallas y relieves detallados.
Las máquinas CNC de 4 ejes incluyen un eje de rotación adicional, conocido como eje A, que permite a la máquina realizar cortes más complejos. Este eje es especialmente útil para operaciones que impliquen el corte por arco o el mecanizado de piezas con geometrías intrincadas. Por ejemplo, un torno CNC de 4 ejes puede crear piezas cilíndricas complejas con ranuras helicoidales.
Las máquinas CNC de 5 ejes incorporan dos ejes de rotación (ejes A y C), lo que permite a la máquina acceder a cinco de las seis caras de una pieza sin necesidad de reposicionamiento. Esta capacidad permite realizar operaciones de mecanizado muy complejas y es esencial para producir componentes detallados y precisos en sectores como el aeroespacial y el de automoción. Un ejemplo es una fresadora CNC de 5 ejes utilizada para fabricar álabes de turbina.
Las máquinas CNC de 7 ejes cuentan con siete ejes, tres de ellos para la rotación de la pieza, tres para el movimiento de la herramienta de corte y uno para la rotación del brazo. Estas máquinas son capaces de realizar operaciones de mecanizado muy complejas y se utilizan en aplicaciones de fabricación avanzadas que requieren una precisión y versatilidad extremas. Un ejemplo es un brazo robótico CNC de 7 ejes utilizado en aplicaciones de soldadura automatizada.
Los controladores CNC utilizan varios protocolos de comunicación industrial para interactuar con otros sistemas y componentes. Los protocolos más comunes son ARCNET, CANbus, ControlNet, DeviceNet, Ethernet y PROFIBUS. Estos protocolos garantizan una comunicación fiable y eficaz entre el controlador CNC y otros dispositivos, facilitando una integración perfecta en entornos de fabricación automatizados.
Las interfaces serie y paralelo, como RS232, RS422, RS485, IEEE 1284 y USB, se utilizan para conectar controladores CNC a dispositivos externos como ordenadores y equipos periféricos. Estas interfaces facilitan la transferencia de datos y permiten la integración de funcionalidades adicionales, como la carga de programas de mecanizado o la actualización del firmware.
Los controladores CNC funcionan con lenguajes y códigos de programación específicos, como código G, código M, HPGL y lógica de escalera. Funciones como el comando de coordenadas polares, la compensación de fresa, la interpolación lineal o circular y el autoescalado están disponibles para mejorar las capacidades del controlador y simplificar el proceso de programación. Por ejemplo, el código G se utiliza ampliamente para controlar el movimiento de máquinas CNC, especificando coordenadas y acciones para operaciones de mecanizado precisas.
Los controladores CNC se presentan en varias configuraciones, como tarjetas de ordenador, armarios independientes, controladores de sobremesa, controladores montados en bastidor, controladores colgantes y controladores de pedestal. Algunos controladores incluyen pantallas integrales, pantallas táctiles, teclados o paneles táctiles para facilitar la interacción y el control por parte del usuario. Por ejemplo, un controlador colgante con pantalla integrada permite al operario controlar y supervisar manualmente las operaciones de la máquina CNC.
Los controladores CNC modernos ofrecen diversas opciones de almacenamiento y gestión de programas, como disquete, almacenamiento en disquete, almacenamiento en cinta, almacenamiento en disco zip, almacenamiento multiprograma y capacidades de control simultáneo. Estas funciones permiten una gestión eficaz de los programas y garantizan el buen funcionamiento de la máquina CNC. Por ejemplo, el almacenamiento multiprograma permite a los operarios cambiar rápidamente entre distintos programas de mecanizado, lo que aumenta la productividad en un entorno de fabricación.
Los controladores de máquinas CNC (control numérico por ordenador) son fundamentales en la fabricación moderna, ya que proporcionan la precisión y automatización necesarias para una producción de alta calidad. Este capítulo explora los principales controladores de máquinas CNC disponibles en el mercado, destacando sus características, aplicaciones industriales e historias de éxito en el mundo real.
Siemens ofrece una amplia gama de sistemas CNC SINUMERIK, conocidos por su precisión y funcionalidad. Los modelos SINUMERIK 828D y SINUMERIK 840D sl son especialmente populares. Estos controladores se utilizan en industrias como la automovilística y la aeroespacial, donde el mecanizado de alto rendimiento es fundamental. Un caso notable es su aplicación en los procesos de fabricación de Airbus, donde los controladores de Siemens han mejorado la eficiencia y la precisión de la producción.
Heidenhain es conocida por sus controles CNC de alta calidad, como el TNC 640, que se utilizan ampliamente en aplicaciones de fresado, torneado y rectificado. Un caso de éxito es el papel de Heidenhain en la producción de dispositivos médicos, donde sus sistemas CNC han permitido el mecanizado preciso de componentes complejos, garantizando altos estándares de calidad y fiabilidad.
Fagor Automation fabrica sistemas CNC como el Fagor CNC 8070, que soporta complejas tareas de mecanizado con alta precisión. Los controladores Fagor se utilizan ampliamente en la industria metalúrgica. Por ejemplo, han desempeñado un papel decisivo en la optimización de los procesos de producción de varios fabricantes europeos de componentes de automoción, lo que se ha traducido en mejoras significativas de la productividad y la calidad de los productos.
El sistema CNC Flexium+ de NUM es capaz de controlar hasta 200 ejes y husillos CNC, lo que lo hace adecuado para una amplia gama de aplicaciones industriales. En el sector aeroespacial, los controladores de NUM se han utilizado para lograr el mecanizado preciso que requieren los componentes de aeronaves, contribuyendo a mejorar los estándares de seguridad y rendimiento.
FANUC es líder en sistemas de control CNC y ofrece productos como FANUC Serie 0i-MODEL F y FANUC Serie 30i/31i/32i-MODEL B. Estos controladores son conocidos por su fiabilidad y adaptabilidad. En la industria electrónica, los controladores FANUC se han utilizado para lograr un mecanizado preciso y de alta velocidad de placas de circuitos, lo que ha aumentado significativamente la eficacia de la producción.
Las series M700V y M80 de Mitsubishi Electric soportan el mecanizado multieje, esencial para industrias como la automovilística y la aeroespacial. Un estudio de caso destaca el papel de Mitsubishi en la mejora de los procesos de mecanizado de un importante fabricante de automóviles japonés, donde sus sistemas CNC han reducido los tiempos de ciclo y mejorado la calidad del producto.
Los controladores de la serie HNC-8 de HuazhongCNC están diseñados para aplicaciones de torno y fresadora. Estos sistemas son ampliamente utilizados en la industria de fabricación de maquinaria pesada. Por ejemplo, los controladores HuazhongCNC han sido cruciales en la producción de equipos de construcción, proporcionando la precisión y durabilidad requeridas para aplicaciones tan exigentes.
Los sistemas CNC de Haas, como el Haas Next Generation Control (NGC), están diseñados para integrarse perfectamente con las máquinas herramienta Haas. Estos controladores destacan especialmente por sus interfaces fáciles de usar. En un caso notable, una empresa de fabricación mediana de EE.UU. adoptó los controladores Haas para racionalizar sus operaciones, lo que se tradujo en una mayor eficiencia y una reducción de los tiempos de inactividad.
El uso de controladores CNC avanzados mejora significativamente la precisión y la eficacia de los procesos de mecanizado en diversos sectores. Por ejemplo, en el sector de la automoción, los controladores CNC de FANUC y Siemens se han utilizado para producir componentes de alta precisión para motores, lo que ha mejorado el rendimiento y la eficiencia del combustible. En la industria aeroespacial, los controladores NUM y Heidenhain han permitido la producción de piezas complejas de alta precisión, garantizando la seguridad y la fiabilidad.
Al conocer las capacidades y aplicaciones de estos controladores de máquinas CNC de primer nivel, los fabricantes pueden tomar decisiones informadas para mejorar sus procesos de producción, garantizando altos niveles de precisión, eficacia y fiabilidad.
Los controladores CNC desempeñan un papel crucial en los procesos de fabricación modernos al automatizar las máquinas herramienta y garantizar movimientos precisos y repetibles. Estos controladores son esenciales para alcanzar altos niveles de precisión, eficacia y flexibilidad en diversas tareas de mecanizado. Este capítulo ofrece una comparación en profundidad de los principales controladores CNC, destacando sus características, rendimiento e idoneidad para diferentes aplicaciones.
Los controladores CNC SYIL son famosos por su precisión y adaptabilidad. Disponibles en modelos de 5 y 4 ejes, estos controladores incorporan supervisión en tiempo real y algoritmos de control adaptativos. Son especialmente adecuados para los complejos movimientos multieje necesarios en tornos CNC, fresadoras y routers. Los controladores SYIL ofrecen un alto grado de personalización y compatibilidad, lo que los hace ideales para tareas que exigen una precisión excepcional.
Mach 3 y Mach 4 son controladores basados en PC que funcionan con Microsoft Windows. Mach 3 es popular en el mercado de gama baja por su precio asequible y su interfaz fácil de usar, mientras que Mach 4 ofrece funciones más avanzadas y estabilidad. Estos controladores son fáciles de configurar y utilizar, por lo que son adecuados para usuarios que necesitan un equilibrio entre coste y funcionalidad.
LinuxCNC es un controlador CNC de código abierto que funciona con Linux. Ofrece amplias opciones de personalización y es conocido por su estabilidad y potencia. Sin embargo, la configuración de LinuxCNC requiere más conocimientos técnicos en comparación con Mach 3 o Mach 4. Es ideal para usuarios que necesitan una solución flexible y potente y se sienten cómodos con un mayor grado de implicación técnica.
FlashCut es un controlador CNC plug-and-play conocido por su facilidad de configuración y su interfaz de fácil uso. Ofrece capacidades similares a Mach 3 cuando está totalmente configurado. Aunque FlashCut puede ser más caro, su diseño maduro y su funcionamiento intuitivo lo convierten en una excelente opción para los usuarios que buscan una configuración sin complicaciones y un rendimiento fiable.
TinyG y PlanetCNC son sistemas basados en microcontroladores que proporcionan algoritmos avanzados de control de movimiento y soporte para múltiples ejes. TinyG admite hasta 6 ejes y destaca por sus suaves perfiles de movimiento y su microcontrolador de alto rendimiento. Estos sistemas son adecuados para usuarios que necesitan funciones avanzadas de control de movimiento a un precio rentable.
Los controladores Fanuc y Mitsubishi son sinónimo de fiabilidad y funciones avanzadas. Estos controladores, que suelen utilizar sistemas de bucle cerrado con tarjetas de control de movimiento como Galil, garantizan un control y una realimentación precisos. Están equipados con capacidades de offset mejoradas y buffers de anticipación más grandes, lo que los hace ideales para aplicaciones de alta precisión en industrias como la automovilística y la aeroespacial.
Los controladores SYIL están diseñados para tareas de mecanizado complejas de alta precisión y ofrecen funciones avanzadas como la supervisión en tiempo real y el control adaptativo. Por el contrario, Mach 3 y Mach 4 son soluciones más accesibles y rentables, adecuadas para usuarios que priorizan la facilidad de uso sobre el rendimiento de gama alta.
LinuxCNC proporciona una gran capacidad de personalización y potencia, pero exige mayores conocimientos técnicos. FlashCut ofrece una experiencia plug-and-play fácil de usar, por lo que es ideal para los usuarios que prefieren una configuración sencilla y un funcionamiento fiable sin profundizar en complejidades técnicas.
TinyG y PlanetCNC ofrecen un control de movimiento avanzado para usuarios que necesitan un alto rendimiento a un coste menor, adecuado para aficionados y pequeñas y medianas empresas. Por el contrario, los controladores Fanuc y Mitsubishi están diseñados para aplicaciones industriales que requieren la máxima fiabilidad y precisión, por lo que son más adecuados para operaciones de fabricación a gran escala.
Al considerar detenidamente estos factores, los fabricantes pueden seleccionar el controlador CNC más adecuado para sus necesidades específicas, equilibrando el rendimiento, la facilidad de uso y la compatibilidad para lograr resultados óptimos en sus procesos de mecanizado.
FANUC, con sede en Japón, es la empresa líder mundial en investigación, diseño, producción y venta de sistemas CNC, con un total de 4.549 empleados (en septiembre de 2005) y 1.500 especialistas en investigación y diseño.
Las cinco características clave del sistema CNC de FANUC incluyen:
En conclusión, la serie estándar de FANUC es el sistema CNC más completo del mundo en la actualidad.
El sistema CNC de Siemens es un producto del Grupo de Automatización y Accionamiento del Grupo Siemens. El sistema CNC de Siemens, SINUMERIK, se ha desarrollado a lo largo de muchas generaciones y en la actualidad, existen principalmente 802, 810, 840, y otros tipos ampliamente utilizados.
El dispositivo CNC de Siemens está diseñado con una estructura modular que resulta rentable. Está equipado con una variedad de software en hardware estándar, por lo que es capaz de una variedad de tipos de procesamiento y satisfacer las necesidades de diversas máquinas herramientas, lo que resulta en una serie de productos.
De 1960 a 1964, se introdujo en el mercado el sistema CNC industrial de Siemens. De 1965 a 1972, Siemens introdujo hardware basado en tecnología de transistores para tornos, fresadoras y rectificadoras, a partir de la generación anterior de sistemas CNC.
De 1973 a 1981, Siemens introdujo el sistema SINUMERIK 550. De 1982 a 1983, se lanzó el sistema SINUMERIK 3, seguido del sistema SINUMERIK 840C de 1984 a 1994. De 1996 a 2000, Siemens introdujo los sistemas SINUMERIK 840D, SINUMERIK 810D y SINUMERIK 802D.
El software incluye funciones de integración de seguridad relacionadas con las personas y las máquinas. ShopMill y ShopTurn proporcionan una interfaz gráfica de programación, lo que ayuda a los operarios a iniciarse rápidamente con una formación mínima. En 1964, Siemens registró el sistema CNC con la marca SINUMERIK.
Mitsubishi se ha dedicado a mejorar el rendimiento de sus productos. La línea de productos de FA abarca controladores programables (PLC), interfaces hombre-máquina (HM), servosistemas de CA, inversores, robots industriales y productos de distribución de energía de baja tensión, muy solicitados en Asia. El negocio de mecatrónica también incluye el suministro de máquinas de descarga eléctrica y equipos completos para procesamiento láser de sangre. Para aumentar aún más la productividad, es esencial el nuevo concepto de soluciones integradas FA.
Los sistemas CNC Mitsubishi más utilizados en la industria son: Serie M700V, serie M70V, serie M70, serie M60S, serie E68, serie E60, serie C6, serie C64 y serie C70. Entre ellos, la serie M700V es un producto de gama alta que cuenta con un completo sistema de control nanométrico, alta precisión y procesamiento de alto grado, y soporta 5 ejes que permite procesar piezas con superficies de formas complejas.
Las ventas de sistemas de automatización industrial ocupan la primera posición dentro del Grupo Mitsubishi.
HEIDENHAIN desarrolla y fabrica encóderes lineales y angulares, encóderes rotativos, lectores digitales y controles numéricos de alta calidad. Estos productos se utilizan ampliamente en máquinas herramienta de precisión, equipos de producción y procesamiento de componentes electrónicos y sistemas de máquinas independientes, especialmente en las industrias de fabricación de semiconductores y electrónica.
El sistema CNC de HEIDENHAIN es un sistema CNC de mecanizado de contornos diseñado para aplicaciones de taller. Dispone de un lenguaje de programación en formato de diálogo fácil de usar, que permite a los operarios escribir programas de mecanizado según la norma ISO en la máquina herramienta. Este sistema es adecuado para fresadoras y puede controlar hasta 12 ejes.
El sistema iTNC530 viene con un disco duro que proporciona un área de almacenamiento de clientes de 26 G, lo que ofrece un amplio espacio de almacenamiento para guardar un gran número de programas, incluidos los escritos sin conexión.
Cabe señalar que la fábrica de Heidenheim, en Berlín, fue destruida durante la Segunda Guerra Mundial en 1934.
Bosch Rexroth, anteriormente Rexroth en Alemania y Departamento de Tecnología de Automatización de Bosch, se convirtió en una filial al 100% del Grupo Bosch en 2001. A pesar de su propiedad, opera de forma independiente, ofreciendo hidráulica industrial, transmisión y control electrónicos, transmisión lineal y tecnología de montaje, neumática e hidráulica servicios de transmisión y soluciones para la hidráulica de maquinaria móvil.
El IndraMotion MTX es a CNC desarrollado por Bosch Rexroth. Con su modelo MTX Advanced de gama alta, puede soportar hasta 250 ejes NC y 60 canales CNC. Este sistema CNC se basa en una arquitectura escalable y utiliza la comunicación por bus Ethernet de alta velocidad (serie 3), la plataforma Open Core Engineering (ingeniería de núcleo abierto) y el protocolo de comunicación M2M de OPCUA. Además, está mejorado con la plataforma de sistema de ejecución de fabricación OpCon MES de Bosch, que permite la comunicación y conexión en tiempo real entre personas, equipos y productos, lo que da como resultado un modelo de fabricación altamente flexible, personalizado y digitalmente inteligente.
El sistema también incluye el sistema de gestión dinámica de la producción inteligente Active Cockpit, que proporciona supervisión de la interconexión en tiempo real, lo que mejora en gran medida la eficiencia del intercambio de información, la eficiencia de la producción, el procesamiento de productos y la calidad de la producción, la precisión de los materiales y los procedimientos, y reduce el desperdicio de materiales y el inventario. En la era de la Industria 4.0, Bosch Rexroth tiene como objetivo hacer que su CNC un actor clave del sector.
NUM es una empresa internacional de renombre con sede en Francia especializada en el desarrollo y la investigación de sistemas de control numérico CNC. Es una filial de Schneider Electric y el segundo mayor proveedor de sistemas CNC de Europa.
Características técnicas del sistema CNC NUM:
El sistema CNC NUM1020/1040 es un producto totalmente nuevo desarrollado por NUM en 1995. Se trata de un sistema CNC de 32 bits compacto y totalmente funcional, y es totalmente compatible con el sistema de la serie NUM1060, especialmente para sistemas de 1 a 6 ejes. Máquina CNC herramientas.
La unidad básica NUM1020T se ha diseñado específicamente para los 2-CNC de 4 ejes controlador programable incorporado (PLC) con una CPU VLSI CISC de 32 bits para fresadoras. Por otro lado, la configuración básica NUM1040M es adecuada para el controlador programable incorporado (PLC) CNC con una CPU CISC de 32 bits para fresadoras, mandrinadoras y centros de mecanizado.
El sistema CNC multieje modular de alta potencia NUM1060 está diseñado para el procesamiento de metales (fresado, torneado, rectificado), el procesamiento de madera y diversas máquinas de tallado de engranajes, máquinas herramienta especiales y máquinas herramienta combinadas lineales o rotativas.
Como recordatorio, NUM es el segundo mayor proveedor de sistemas CNC de Europa.
FAGOR AUTOMATION es un fabricante profesional de renombre de sistemas CNC, visualizadores digitales (DRO) y sistemas de medición por rejilla. Es una filial del Grupo Mondragón de España, fundada en 1972, centrada en el desarrollo de la automatización de máquinas herramienta.
Introducción a la serie de sistemas CNC:
FAGOR lleva el sistema CNC "ficticio" a un nuevo nivel.
Yamazaki Mazak se fundó en 1919 y es uno de los principales fabricantes de tornos CNC, centros de mecanizado de torneado y fresado de materiales compuestos, centros de mecanizado verticales y horizontales, sistemas láser CNC, FMS producción flexible sistemas CAD/CAM, dispositivos CNC y software de apoyo a la producción.
El sistema CNC Mazatrol Fusion 640 cuenta con una CPU RISC de 64 bits de alta velocidad y alto rendimiento que proporciona capacidades avanzadas de procesamiento de datos para un control de movimiento rápido y eficaz. Este sistema también cuenta con tecnología de fusión de CNC y PC, que es una primicia mundial y permite funciones en red e inteligentes.
Al conectar el sistema CNC directamente a Internet, puede acceder a los servicios de mantenimiento en línea 24 horas al día, 7 días a la semana, de Little Giant Machine Tool Co.
El exclusivo lenguaje de programación de mecanizado del sistema CNC Mazatrol Fusion 640, que utiliza tecnología de inteligencia artificial, incluye un sistema experto inteligente con más de 70 años de experiencia en mecanizado de MAZAK. Esto hace que sea extremadamente sencillo escribir programas de mecanizado.
MAZAK es líder mundial en sistemas CNC inteligentes.
HNC es una marca muy conocida en China especializada en el desarrollo y la producción de sistemas CNC con derechos de propiedad intelectual independientes. Ofrece una gama de productos de gama alta, media y baja, incluido el sistema CNC de gama alta de la serie HNC 8.
Decenas de estos sistemas se han aplicado en grandes proyectos especiales nacionales de alta gama. Máquinas herramienta CNC. El rendimiento de los dispositivos de servoaccionamiento y accionamiento de husillo de HNC, que también tienen derechos de propiedad intelectual independientes, ha alcanzado el nivel avanzado internacional.
El dispositivo CNC HNC-848 es un sistema de gama alta de tipo bus totalmente digital diseñado para competir con los sistemas CNC extranjeros de gama alta. Presenta una estructura de módulo de CPU dual con arquitectura abierta y tecnología de bus de campo industrial NCUC con derechos de propiedad intelectual independientes.
El dispositivo CNC HNC-848 está equipado con funciones avanzadas como tecnología de control multicanal, mecanizado de cinco ejes, alta velocidad y alta precisión, torneado y fresado, y control síncrono. Cuenta con una pantalla LCD de 15 pulgadas y se utiliza principalmente en centros de mecanizado verticales y horizontales de alta velocidad y alta precisión, multieje y multicanal, complejos de torneado y fresado y máquinas herramienta de pórtico de 5 ejes.
HNC es una de las pocas marcas de sistemas CNC de China que ofrece productos y servicios de gama alta.
GSK es la principal base de investigación y desarrollo de sistemas CNC para máquinas herramienta del país, y cuenta con más de 800 personas dedicadas a la investigación y el desarrollo. Con equipos de producción y procesos tecnológicos de vanguardia, GSK ha alcanzado el primer puesto en producción y ventas anuales de sistemas CNC del país durante diez años consecutivos.
GSK ofrece sistemas CNC para diversos campos, como tornos, taladradoras y fresadoras, centros de mecanizado, rectificadoras y mucho más. El sistema GSK27, en particular, cuenta con un control a nivel nanométrico que se consigue mediante el uso de varios procesadores y una interfaz de interacción persona-ordenador fácil de usar con menús configurables.
Diseñado pensando en la ergonomía, el sistema GSK27 se adapta mejor a los hábitos de procesamiento de los operarios y cuenta con una plataforma de software abierta que puede conectarse fácilmente con software de terceros. Además, su hardware de alto rendimiento admite hasta 8 canales y un control de 64 ejes.
A continuación encontrará respuestas a algunas preguntas frecuentes:
Los controladores de máquinas CNC pueden clasificarse en varios tipos según su función y complejidad, bucle de control, tipo de movimiento y control de ejes. Los principales tipos incluyen controladores CNC industriales OEM, controladores CNC retrofit, controladores CNC basados en PC (como Mach 3, Mach 4, LinuxCNC y FlashCut), sistemas de bucle cerrado, sistemas de bucle abierto, sistemas de control de contorneado, sistemas de control punto a punto, controladores CNC multieje (de 2 a 7 ejes) y sistemas basados en microcontroladores (como TinyG y PlanetCNC). Cada tipo se adapta a las necesidades y aplicaciones específicas de la industria manufacturera, ofreciendo una amplia gama de opciones para el control de máquinas CNC.
Para aplicaciones de alta precisión en el mecanizado CNC, varios controladores destacan por su fiabilidad, funciones avanzadas y capacidades de precisión. Los controladores CNC de FANUC gozan de gran prestigio por sus algoritmos avanzados, paquetes de funciones personalizables y componentes de alta fiabilidad, lo que los hace ideales para un mecanizado óptimo en 5 ejes y tareas de alta precisión. El software de control next de DATRON es otra opción excelente, ya que ofrece una interfaz de pantalla táctil fácil de usar, sensores auxiliares para una supervisión precisa y una función de asistencia CAM que simplifica la configuración y reduce los errores. Los controladores Centroid Acorn son conocidos por sus funciones avanzadas y su fiable comunicación Ethernet, mientras que los controladores UCCNC son alabados por su facilidad de uso y su sólido rendimiento, con modelos como el UC400ETH que ofrece amplias capacidades de entrada/salida. Los sistemas de control CNC EX de Avid, basados en la tecnología de control de movimiento de Centroid, ofrecen un rendimiento suave, fiable y de alta precisión en un paquete plug-and-play. Al elegir un controlador CNC para aplicaciones de alta precisión, tenga en cuenta factores como la interfaz de software, la flexibilidad, la asistencia y la compatibilidad para asegurarse de que satisface las demandas específicas de sus operaciones de mecanizado.
La elección del controlador CNC adecuado para su máquina implica varias consideraciones críticas para garantizar que cumple sus requisitos específicos y mejora el rendimiento de su máquina CNC. En primer lugar, determine el tipo de controlador CNC que mejor se adapta a su aplicación. Los controladores OEM industriales de marcas como Haas o Siemens son ideales para entornos industriales de gama alta por sus funciones avanzadas y su robustez. Por otro lado, los controladores para bricolaje y aficionados como PlanetCNC, TinyG y GRBL son más asequibles y accesibles, por lo que son adecuados para proyectos personales y operaciones a menor escala.
La compatibilidad es otro factor crucial. Asegúrese de que el controlador es compatible con los componentes de su máquina CNC, incluidos los motores paso a paso, los servoaccionamientos y los finales de carrera. Esta compatibilidad se extiende a la fuente de alimentación, que debe ajustarse a los requisitos de corriente y tensión de los motores y el controlador.
La interfaz del software es igualmente importante. Opte por un controlador con un software fácil de usar, estable y potente. PathPilot, por ejemplo, es conocido por su facilidad de uso y estabilidad. El software también debe ser compatible con el nivel de automatización que necesite y el número de ejes de su máquina.
Tenga en cuenta sus conocimientos y experiencia. Si te sientes cómodo diagnosticando problemas eléctricos y seleccionando componentes, quizá te convenga una solución más personalizada. De lo contrario, un kit llave en mano con amplio apoyo comunitario puede ser más práctico.
Tenga en cuenta las necesidades futuras y la escalabilidad. Elija un controlador que pueda soportar su configuración actual y cualquier ampliación futura que pueda planificar, como añadir más ejes.
La fiabilidad y eficacia del controlador son primordiales. Asegúrese de que el sistema de control es estable y puede hacer frente a las exigencias de sus procesos de mecanizado con eficacia, contribuyendo a prolongar la vida útil de las herramientas y a mejorar la capacidad de la máquina.
Por último, considere aspectos prácticos como la fuente de alimentación y el modo en que conectará el ordenador al controlador CNC, garantizando la compatibilidad con sus protocolos de comunicación.
Si evalúa detenidamente estos factores, podrá seleccionar un controlador CNC que optimice el rendimiento de su máquina, se adapte a sus conocimientos y recursos y satisfaga sus necesidades actuales y futuras.
Al seleccionar un controlador CNC, varias características clave son cruciales para garantizar un rendimiento, una precisión y una eficacia óptimos. En primer lugar, el controlador debe interpretar y ejecutar eficazmente los comandos de los archivos de código G o M, convirtiéndolos en señales eléctricas que accionen los motores de la máquina. La capacidad de controlar varios ejes con gran precisión también es esencial, especialmente en máquinas complejas que pueden requerir un control de tres, cuatro o cinco ejes.
Un sistema de bucle cerrado es importante para mantener una alta precisión, ya que proporciona información de la máquina al controlador para garantizar que los movimientos se ajustan a las entradas programadas. Las funciones de seguridad, como las paradas de emergencia y la supervisión de sensores, son vitales para un funcionamiento seguro.
Además, el controlador debe gestionar funciones auxiliares como el control del refrigerante, las operaciones del husillo y los cambios de herramienta, con opciones para ajustar la velocidad del husillo y el avance. Para un funcionamiento eficaz, también es necesaria una interfaz fácil de usar con un panel de control bien diseñado, que incluya teclas de función, interruptores y una pantalla de visualización.
Los componentes internos como la protección de circuitos, las placas de conexión y los puertos de conectividad (por ejemplo, USB a PC) mejoran la funcionalidad y la fiabilidad. Para aplicaciones de precisión, resultan beneficiosas características avanzadas como las funciones de plano espacial, la supervisión de la desviación del contorno y la compatibilidad con encóderes lineales. La capacidad de mitigar las vibraciones y ajustar el avance y la velocidad de forma dinámica puede evitar defectos y mejorar la calidad de las piezas.
Por último, una fuente de alimentación robusta y una carcasa duradera son fundamentales para evitar el sobrecalentamiento y proteger contra la suciedad, garantizando un rendimiento constante y fiable de la máquina. Teniendo en cuenta estas características, puede seleccionar un controlador CNC que satisfaga sus necesidades específicas de mecanizado, ya sea para tareas sencillas o complejas de alta precisión.
Sí, puede actualizar el controlador de su máquina CNC actual. Este proceso, conocido como actualización del controlador CNC, es una opción práctica y a menudo recomendada para mejorar el rendimiento de la máquina, reducir el tiempo de inactividad y ahorrar costes en comparación con la compra de una máquina nueva. La actualización le permite conservar componentes funcionales, como servomotores y accionamientos, al tiempo que sustituye sistemas de control obsoletos.
El proceso de modernización suele constar de varios pasos. En primer lugar, cree un plan detallado para asegurarse de que se tienen en cuenta todos los componentes y pasos necesarios. A continuación, desconecte de forma segura la alimentación de la máquina y retire el antiguo controlador y los componentes relacionados sin cortar cables innecesariamente. A continuación, instale el nuevo cuadro eléctrico y el controlador CNC a una altura cómoda para el operario. Pase con cuidado los cables de los motores al nuevo armario, evitando puntos de pellizco y bordes afilados, y conecte el cableado de E/S de acuerdo con los esquemas de la máquina antigua.
Una vez instalado el hardware, encienda el nuevo controlador e instale el software, configurando parámetros como la herramienta y las compensaciones de trabajo específicas de su máquina.
Varias máquinas CNC, como fresadoras, tornos, centros de mecanizado, fresadoras y chorros de agua, son candidatas idóneas para una actualización de controladores. Empresas como MachMotion, CENTROID y MS-Tech ofrecen soluciones de retrofit completas, que incluyen nuevos controladores, servos, motores y sistemas eléctricos, junto con un sólido soporte y guías de instalación detalladas.
Actualizando su controlador CNC, puede mejorar significativamente el rendimiento de su máquina y prolongar su vida útil, todo ello evitando los costes más elevados asociados a la compra de una máquina nueva.
Los modernos controladores de máquinas CNC ofrecen una amplia gama de ventajas que mejoran significativamente el proceso de mecanizado. Una de las principales ventajas es la mejora de la productividad, ya que estos controladores automatizan el proceso de mecanizado, reduciendo los errores humanos y aumentando la velocidad de producción. Esto es especialmente valioso en industrias en las que la precisión y el tiempo son fundamentales, como la aeroespacial, la automoción y la fabricación de dispositivos médicos.
La exactitud y la precisión son también ventajas importantes, ya que los controladores modernos garantizan una alta precisión y repetibilidad al interpretar con exactitud el código G y traducirlo en comandos específicos para la máquina. El resultado es una calidad uniforme en múltiples piezas y una reducción de los residuos.
Otra ventaja clave es la formación simplificada del operario. El software de control CNC moderno suele incluir interfaces intuitivas y funciones inteligentes que facilitan el aprendizaje y la rápida productividad de los nuevos operarios, lo que reduce la curva de aprendizaje y permite a las empresas contratar a operarios con menos experiencia.
Las funciones avanzadas y la automatización también son ventajas significativas. Los controladores modernos suelen incluir reconocimiento de materiales, selección automática de herramientas, supervisión en tiempo real, diagnósticos y sistemas de retroalimentación. Estas funciones permiten a los operarios supervisar de cerca el proceso de mecanizado, abordar los problemas con rapidez y optimizar el rendimiento de la máquina de forma dinámica en función del material que se esté procesando.
La mejora de la seguridad es otra ventaja fundamental. El mecanizado CNC automatiza muchos procesos peligrosos, reduciendo los riesgos de seguridad en el taller. Además, la naturaleza cerrada de las máquinas CNC minimiza aún más el riesgo de lesiones.
La eficiencia energética también mejora con las modernas máquinas CNC, que consumen menos energía en comparación con los métodos tradicionales, lo que supone un ahorro de costes y una reducción del impacto medioambiental.
La versatilidad en el manejo de tareas de mecanizado complejas, incluidos el contorneado 3D y los movimientos multieje, permite la creación de piezas intrincadas que son difíciles o imposibles de lograr con los métodos tradicionales. La integración con tecnologías modernas como IoT e IA facilita procesos de fabricación más inteligentes, mantenimiento predictivo y análisis de datos mejorados.
La experiencia del usuario se mejora con funciones como interfaces de pantalla táctil y pantallas gráficas, que hacen que el funcionamiento sea más intuitivo y eficaz. Estas interfaces permiten a los operarios reiniciar desde piezas o contornos específicos, programar hojas de retales y ajustar las condiciones de corte con facilidad.
Por último, los modernos controladores CNC reducen la necesidad de operaciones manuales, lo que se traduce en una mayor eficiencia de la máquina y una menor intervención humana. Al aprovechar estas ventajas, los fabricantes pueden optimizar sus procesos de mecanizado, impulsar la innovación y lograr una mayor eficiencia y productividad en sus operaciones.