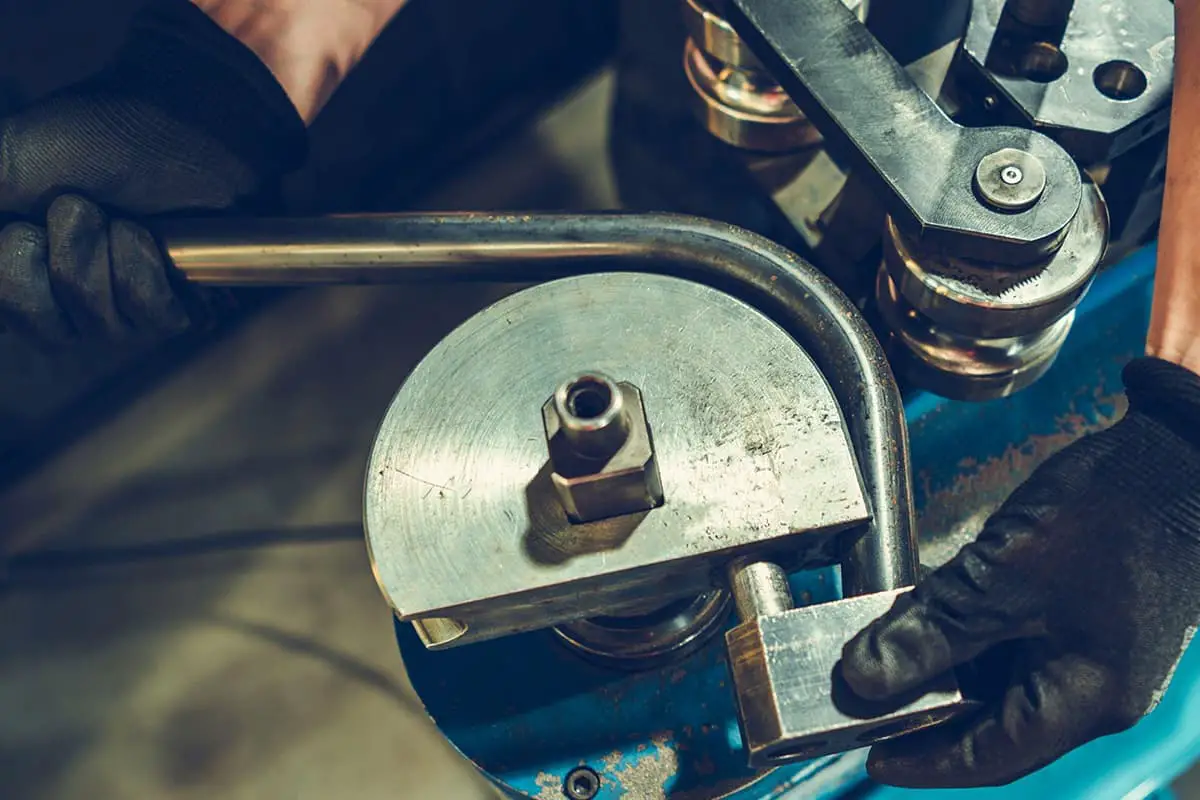
Doblar tubos con precisión exige conocer unas directrices y unos parámetros específicos. ¿Cómo se garantiza un curvado suave y preciso en todo momento? Este artículo explora los aspectos cruciales del curvado de tubos, incluidos los parámetros de la máquina, la instalación de matrices y los defectos más comunes. Aprenda a configurar y ajustar su equipo, calcular los ángulos de curvado y evitar problemas como grietas y arrugas. Descubra consejos prácticos y técnicas que pueden ayudarle a conseguir resultados óptimos en las operaciones de curvado de tubos.
1.1 Este procedimiento es aplicable a la máquina curvadora de tubos CNC utilizada para el curvado en frío de tubos metálicos.
1.2 Este procedimiento es aplicable a las máquinas curvadoras de tubos hidráulicas de un cabezal de los modelos DW63 y DW114 en el taller de piezas estructurales de equipos agrícolas.
Los siguientes documentos son esenciales para la aplicación de este documento. Para los documentos de referencia fechados, sólo la versión fechada se aplica a este documento. Para los documentos de referencia sin fecha, la última versión se aplica a este documento.
Máquina curvadora de tubos CNC GB/T 28763-2012
Máquina curvadora de tubos CNC: Una máquina curvadora de tubos que debe tener al menos tres ejes de movimiento, incluyendo la rotación del husillo, el movimiento lineal del mandril y la rotación del mandril, y es controlada por un Sistema CNC.
4.1 El parámetro principal de la máquina curvadora de tubos es el diámetro exterior máximo del tubo.
4.2 Los parámetros principales y los parámetros básicos de la máquina curvadora de tubos deben ajustarse a las normas prescritas en la tabla siguiente.
Nombre del parámetro | Diámetro exterior máximo del tubo/mm | Espesor máximo de la pared del tubo/mm |
Parámetro Valor | 10 | 1.2 |
16 | 1.2 | |
25 | 3 | |
38 | 4 | |
42 | 4 | |
60 | 5 | |
63 | 5 | |
76 | 5 | |
89 | 6 | |
114 | 8 | |
159 | 12 | |
168 | 12 | |
219 | 16 | |
273 | 20 |
Cuando el diámetro exterior es mayor o igual a 114 mm, es de 0,4 a 1 veces el radio máximo del tubo curvado.
4.4 Parámetros de la máquina curvadora de tubos para talleres de piezas estructurales:
Modelo de máquina curvadora de tubos | Diámetro exterior del tubo (mm) | Espesor de la pared del tubo (mm) | Radio de curvatura (mm) |
DWFB63 | 19 a 63 años | ≤5 | De 50 a 250 |
DWFB114 | 48 a 114 | ≤8 | De 100 a 750 |
Tipo de material | Material Especificación mm | Espesor de pared mm | Radio de curvatura (por defecto como mediana) mm | Equipo correspondiente |
Tubo cuadrado | φ16 | 2 | 58 | DWFB63 |
φ25 | 2 | 50 | DWFB63 | |
φ25 | 2 | 150 | DWFB63 | |
φ33 | 3 | 101.5 | DWFB63 | |
Φ35 | 4 | 60 | DWFB63 | |
Φ42 | 3 | 100 | DWFB63 | |
Φ48 | 3.5 | 130 | DWFB63 | |
Φ50 | 6 | 100 | DWFB114 | |
Φ60 | 5 | 150 | DWFB63 | |
Φ60 | 5 | 200 | DWFB63 | |
Φ60.5 | 2 | 150 | DWFB114 | |
Tubo redondo | Tubo cuadrado 30×30 | 2 | 外径220 | DWFB114 |
Tubo cuadrado 40×80-8 | 2.5 | 100 | DWFB114 | |
Tubo cuadrado 40×80-8 | 3 | 180 | DWFB114 | |
Tubo cuadrado 40×80-8 | 2 | Diámetro exterior: 220 | DWFB114 | |
Tubo cuadrado 50×50 | 2.5 | Diámetro interior: 170 | DWFB114 | |
Tubo cuadrado 50×70-7 | 2.5 | 120 | DWFB114 | |
Tubo cuadrado 50×70-7 | 3 | 120 | DWFB114 | |
Tubo cuadrado 60×80-6 | 4.5 | 150 | DWFB114 | |
Tubo cuadrado 60×80-8 | 4.5 | 150 | DWFB114 |
6.1 Instalación del molde principal
6.1.1 Coloque el molde de rueda plegable con la ranura de la chaveta hacia abajo sobre la chaveta de ajuste del asiento fijo. Después de colocarlo plano, ajuste el molde de la rueda a la izquierda y a la derecha de modo que el orificio del perno del molde de la rueda coincida con el orificio del perno del asiento fijo.
6.1.2 Apriete la tuerca fija, no debe quedar floja.
6.2 Instalación y ajuste de los moldes de prensado
6.2.1 Asegure el molde de prensado al deslizador con pernos, gire el perno de ajuste, mueva el molde de prensado hacia arriba y hacia abajo, alinee el centro del molde de prensado con el centro de la ranura del molde de doblado para asegurar un ajuste apretado entre los dos durante la alimentación del molde de prensado, sin ninguna interferencia.
6.2.2 Afloje la tuerca de fijación de la corredera del molde de prensado y, a continuación, utilice una llave para aflojar el perno de ajuste de la corredera.
6.2.3 Coloque un material de molde de prueba de unos 300 mm de longitud en la ranura de flexión del molde de rueda. Controle el molde de presión para sujetar el tubo hacia adelante y no debe haber ningún aflojamiento. Apriete el perno de ajuste deslizante del molde de presión con una llave. Controle el molde de presión para que retroceda y, a continuación, vuelva a apretar el perno de ajuste deslizante del molde de presión media vuelta con una llave. Por último, apriete la tuerca de fijación de la corredera del molde de presión.
6.3 Instalación y ajuste de Sujeción Moho
6.3.1 Conecte y fije el molde de sujeción y la corredera con pernos. Gire el perno de ajuste, mueva el molde de sujeción hacia arriba y hacia abajo para que tenga la misma altura que el molde de sujeción principal.
6.3.2 Afloje la tuerca de fijación de la corredera del troquel de sujeción y utilice una llave para aflojar el perno de ajuste de la corredera.
6.3.3 Coloque un segmento de molde de prueba de aproximadamente 300 mm de longitud en la ranura del tubo del molde de rueda y apriete el perno de ajuste deslizante de la abrazadera del molde con una llave para sujetar el tubo. No debe aflojarse. Retire el tubo del molde de prueba, utilice la llave para apretar aún más el perno de ajuste del deslizador de la mordaza del molde 1/3 de vuelta y apriete la tuerca de fijación del deslizador de la mordaza del molde.
6.4 Instalación y ajuste de la varilla del núcleo
6.4.1 Conecte el orificio roscado de la varilla de núcleo con el perno de la barra de tracción de la varilla de núcleo. Después de apretarlo, ajuste el asiento trasero de la barra de tracción de la varilla del núcleo de modo que la posición tangente de la superficie del arco en la varilla del núcleo en la dirección horizontal no cruce la línea central del molde de doblado.
7.1 Cálculo para tubos curvados a 90
Para los tubos curvados estirados en frío, se toma R=(4~6)D. Como se muestra en la Figura 1-3, después de curvar el tubo, las longitudes del arco exterior y del arco interior del segmento curvado no son la longitud real del tubo recto original, sino que sólo la longitud de la línea central del tubo curvado permanece inalterada antes y después del curvado.
Su longitud desplegada es igual a la longitud de la sección recta original del tubo. Supongamos ahora que los puntos inicial y final de la sección doblada son a y b respectivamente. Cuando el ángulo de flexión es de 90°, la longitud de la sección doblada del tubo es exactamente 1/4 de la circunferencia del círculo trazado con r como radio. Su longitud de arco está representada por el radio de curvatura, que es:
Longitud del arco ab=2πR/4=1,57R
A partir de la fórmula (1-3), puede saberse que la longitud desplegada de la curva de 90° es 1,57 veces el radio de curvatura.
7.2 Cálculo de arbitrarios Doblar tubos
Por tubo de curvatura arbitraria se entiende un tubo con un ángulo y un radio de curvatura arbitrarios. La longitud desplegada de la parte de flexión de este tubo puede calcularse mediante la siguiente fórmula:
L=παR/180=0,01745αR
En la fórmula, L es la longitud desplegada de la pieza doblada (mm); α- es el ángulo de flexión (°); π- es Pi; R es el radio de flexión (mm).
Además, el cálculo de la longitud desplegada de cualquier segmento de tubo curvado también puede realizarse según la Figura 1-6 y la Tabla 1-1.
El siguiente ejemplo ilustra cómo utilizar la Tabla 1-1.
Tabla 1-1 Cálculo del curvado de tubos arbitrarios
Ángulo de flexión | Medio Longitud de plegado C | Longitud de flexión L |
1 | 0.0087 | 0.0175 |
2 | 0.0175 | 0.0349 |
3 | 0.0261 | 0.0524 |
4 | 0.0349 | 0.0698 |
5 | 0.0436 | 0.0873 |
6 | 0.0524 | 0.1047 |
7 | 0.0611 | 0.1222 |
8 | 0.0699 | 0.1396 |
9 | O.0787 | 0.1571 |
10 | O.0875 | 0.1745 |
11 | 0.0962 | 0.1920 |
12 | 0.1051 | 0.2094 |
13 | 0.1139 | 0.2269 |
14 | 0.1228 | 0.2443 |
15 | 0.1316 | 0.2618 |
16 | 0.1405 | 0.2793 |
17 | 0.1494 | O.2967 |
18 | 0.1584 | 0.3142 |
19 | 0.1673 | 0.3316 |
20 | 0.1763 | 0.3491 |
21 | 0.1853 | O.3665 |
22 | 0.1944 | 0.3840 |
23 | 0.2034 | 0.4014 |
24 | 0.2126 | 0.4189 |
25 | 0.2216 | 0.4363 |
26 | 0.2309 | 0.4538 |
27 | 0.2400 | 0.4712 |
28 | 0.2493 | 0.4887 |
29 | 0.2587 | 0.5061 |
30 | 0.2679 | 0.5236 |
31 | O.2773 | 0.5411 |
32 | 0.2867 | O.5585 |
33 | O.2962 | 0.5760 |
34 | O.3057 | 0.5934 |
35 | 0.3153 | 0.6109 |
36 | 0.3249 | O.6283 |
37 | O.3345 | 0.6458 |
38 | O.3443 | O.6632 |
39 | 0.3541 | O.6807 |
40 | 0.3640 | 0.6981 |
41 | 0.3738 | 0.7156 |
42 | 0.3839 | O.7330 |
43 | 0.3939 | 0.7505 |
44 | 0.4040 | 0.7679 |
45 | 0.4141 | O.7854 |
46 | O.4245 | 0.8029 |
47 | 0.4348 | O.8203 |
48 | 0.4452 | O.8378 |
49 | 0.4557 | 0.8552 |
50 | 0.4663 | O.8727 |
51 | 0.4769 | O.8901 |
52 | 0.4877 | 0.9076 |
53 | 0.4985 | O.9250 |
54 | O.5095 | 0.9425 |
55 | O.5205 | 0.9599 |
56 | 0.5317 | 0.9774 |
57 | O.5429 | 0.9948 |
58 | 0.5543 | 1.0123 |
59 | O.5657 | 1.0297 |
60 | 0.5774 | 1~0472 |
61 | 0.5890 | 1.0647 |
62 | 0.6009 | 1.0821 |
63 | 0.6128 | 1.0996 |
64 | O.6249 | 1.1170 |
65 | 0.6370 | 1.1345 |
66 | 0.6494 | 1.1519 |
67 | 0.6618 | 1.1694 |
68 | 0.6745 | 1.1868 |
69 | O.6872 | 1.2043 |
70 | 0.7002 | 1.2217 |
71 | 0.7132 | 1.2392 |
72 | O.7265 | 1.2566 |
73 | O.7399 | 1.2741 |
74 | 0.7536 | 1.2915 |
75 | 0.7673 | 1.3090 |
76 | 0.7813 | 1.3265 |
77 | 0.7954 | 1.3439 |
78 | O.8098 | 1.3614 |
79 | O.8243 | 1.3788 |
80 | 0.8391 | 1.3963 |
81 | 0.8540 | 1.4173 |
82 | O.8693 | 1.4312 |
83 | O.8847 | 1.4486 |
84 | 0.9004 | 1.4661 |
85 | 0.9163 | 1.4835 |
86 | 0.9325 | 1.5010 |
87 | 0.9484 | 1.5184 |
88 | O.9657 | 1.5359 |
89 | 0.9827 | 1.5533 |
90 | 1.000 | 1.5708 |
Nota:
Al utilizar los valores de C y L de la tabla, deben multiplicarse por el radio de curvatura R. Por ejemplo, dado que el ángulo de curvatura del codo de la figura 1-7 es de 25°, el radio de curvatura R=500 mm y la distancia desde la sección de tubo instalada hasta el punto de inflexión M es de 911 mm, si se toma un tubo recto para hacer el codo, ¿cómo debe marcarse la línea?
Solución:
La longitud de la sección recta de la tubería en el extremo de la tubería que se va a procesar, b = 911-CR
Según la tabla 1-1, cuando el ángulo es de 25°, C=0,2216, L=0,4363; por lo tanto, CR es: 0,2216R=0,2216×500=111mm. Por lo tanto, b=911-111=800 mm
La longitud real desplegada de la pieza de flexión L=0,4363R=0,4363×500=218 mm
A partir de las longitudes calculadas de la sección recta del tubo b y de la longitud desplegada L de la pieza de flexión, puede marcar la línea. Como se muestra en la Figura 1-7b.
A partir de los ejemplos anteriores, siempre que se definan el ángulo y el radio de curvatura, la tabla 1-1 puede utilizarse para calcular cómodamente la curvatura de tuberías de cualquier ángulo y radio.
8.1 La máquina curvatubos debe ser manejada por personal especialmente formado. Se prohíbe el manejo no autorizado por otras personas.
8.2 Los operarios deben ponerse el equipo de protección antes de la operación e inspeccionar cuidadosamente la máquina y el entorno de trabajo. Compruebe los alrededores del lugar de trabajo y despeje todos los objetos que puedan obstaculizar el trabajo y el tráfico.
8.3 Antes del funcionamiento, compruebe primero si falta aceite en cada punto de lubricación, si el mecanismo móvil está suelto y si el dispositivo de protección de seguridad es fiable. Después de la confirmación, la operación puede ser realizada; objetos duros y accesorios de tubería no deben ser utilizados para pulse la pantalla de control principal.
8.4 Después de arrancar la máquina, debe ponerse en marcha en vacío 1-2 veces antes de su funcionamiento normal. Si la máquina ha estado inactiva durante varios días, debe arrancarse durante diez minutos antes de su funcionamiento normal.
8.5 Los distintos materiales conformados deben utilizar moldes correspondientes y no deben mezclarse ni utilizarse incorrectamente. Sólo se puede doblar un material con forma a la vez; no se permite doblar dos o más materiales superpuestos para evitar daños en el equipo y los moldes.
9.1 Para la producción de piezas por primera vez, prepare plantillas como referencia. Una vez instalados y depurados los moldes según sea necesario, y cortados los materiales de acuerdo con la longitud de corte teórica, marque los puntos de doblado, realice operaciones de doblado en el material y, a continuación, compare las piezas dobladas con la plantilla.
Si hay un error, ajuste la longitud de corte y los puntos de doblado hasta que no haya error entre la pieza doblada y la plantilla, entonces puede guardar el tamaño de corte y el programa modelo. La próxima vez que fabrique este tipo de pieza, podrá consultar directamente los datos guardados para el curvado de tubos.
9.2 Para piezas producidas en serie, prepare plantillas como referencia. Llame el programa de tamaño de corte y modelo guardado, haga una pieza primero, luego compare la primera pieza con la plantilla para determinar si hay algún error.
Si hay un error, ajuste el tamaño de corte y el programa del modelo hasta que no haya error entre la pieza doblada y la plantilla, entonces puede guardar los datos para la producción en masa.
10.1 Aplanamiento severo en el lado exterior del arco
Durante el proceso de curvado de tubos con un núcleo, seleccione el mandril adecuado (si es necesario, puede utilizarse un mandril flexible ensamblado a partir de varias secciones), instálelo correctamente y asegúrese de que el eje de la ranura del tubo de todos los componentes se encuentra en el mismo plano horizontal al instalar el molde.
10.2 Adelgazamiento en el exterior del arco
Para evitar un adelgazamiento excesivo, un método eficaz habitual es utilizar una curvadora de tubos con un dispositivo de refuerzo lateral o un dispositivo de empuje de cola.
Al impulsar o empujar, se compensa parte de la resistencia durante la flexión de la tubería, mejorando la distribución de la tensión en la sección transversal de la tubería, desplazando la capa neutra hacia el exterior, con lo que se consigue el propósito de reducir el adelgazamiento de la pared exterior de la tubería.
10.3 Fisuración en el exterior del arco
En primer lugar, asegúrese de que el material del tubo tiene una buena tratamiento térmico compruebe si la presión del molde de sujeción es demasiado alta y ajústela a una presión adecuada.
Por último, asegúrese de que haya una buena lubricación entre el mandril y la pared del tubo para reducir la resistencia a la flexión y la fricción entre la pared interior del tubo y el mandril.
10.4 Arrugas en el interior del arco
Deben tomarse las medidas adecuadas en función de la localización de las arrugas. Si el punto de corte delantero está arrugado, la posición del mandril debe ajustarse hacia delante para conseguir un apoyo razonable del tubo durante el curvado.
Si el punto de corte trasero está arrugado, se debe instalar un bloque de prevención de arrugas para asegurar la posición correcta y ajustar la presión del troquel a un nivel adecuado.
Si toda la cara interior del arco está arrugada, indica que el diámetro del mandril utilizado es demasiado pequeño, lo que provoca una separación demasiado grande entre el mandril y la pared del tubo, o que la presión de la matriz es demasiado baja, lo que no puede hacer que el tubo encaje bien con el matriz dobladora y bloque de prevención de arrugas durante el plegado.
Por lo tanto, el mandril debe ser sustituido y la matriz de sujeción ajustada para proporcionar la presión adecuada de la matriz.