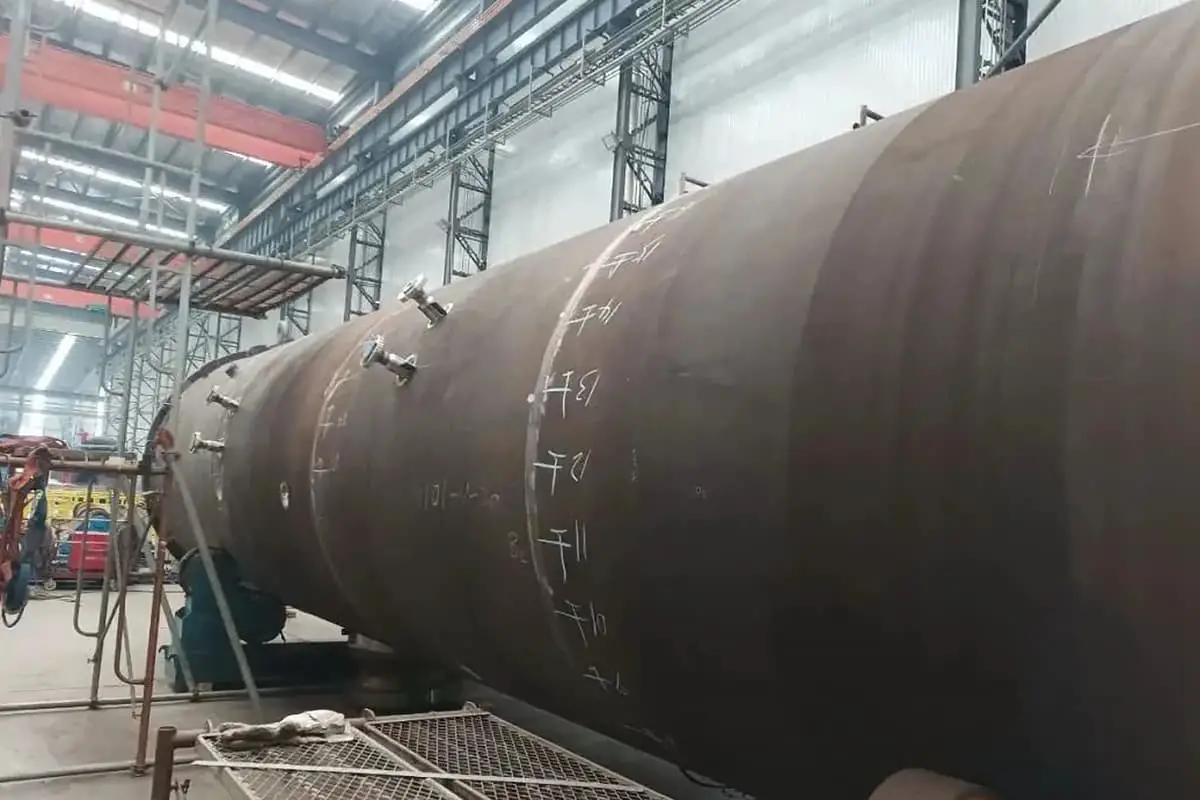
¿Cómo podemos unir aluminio y acero, dos metales con propiedades muy diferentes, sin comprometer su integridad estructural? Este artículo profundiza en las técnicas avanzadas de soldadura láser para abordar este reto, explorando métodos que minimizan los compuestos intermetálicos frágiles y mejoran la resistencia de la unión. Descubra las últimas investigaciones y conocimientos prácticos para crear uniones de aluminio y acero fuertes y fiables, cruciales para industrias como la automovilística y la aeroespacial. Descubra cómo las innovaciones en la tecnología de soldadura están allanando el camino hacia estructuras metálicas más eficientes, ligeras y duraderas.
Conectando aluminio y acero se pueden conseguir piezas de automoción ligeras. Sin embargo, el agrietamiento del compuesto intermetálico causado por la soldadura de estos metales disímiles puede afectar significativamente al rendimiento de la unión.
Este post presenta los principales métodos de soldadura láser de aluminio y acero y explica el estado de la investigación en los últimos años.
El acero galvanizado es un sustrato de acero recubierto con capas de zinc de distintos grosores. El proceso de galvanizado se clasifica en galvanoplastia y galvanizado en caliente.
La capa de zinc no sólo proporciona blindaje físico, sino que también ofrece protección electroquímica al sustrato de acero.
Debido a su excelente resistencia a la corrosión, el acero galvanizado se utiliza ampliamente en diversas industrias como el transporte, la energía eléctrica, la construcción, las instalaciones de calefacción, los instrumentos y el mobiliario.
En particular, la aplicación de acero galvanizado ordinario, acero galvanizado de alta resistencia y acero galvanizado de ultra alta resistencia en la industria del automóvil mejora la resistencia a la corrosión y prolonga la vida útil de la carrocería y otras piezas.
Sin embargo, la presencia de una capa de zinc dificulta la soldadura por fusión de las chapas de acero galvanizado. Esto se debe a que el punto de fusión del zinc es de 420 ℃, su punto de ebullición es de 908 ℃, mientras que el punto de fusión del acero base es de 1300 ℃ y su punto de ebullición es de 2861 ℃.
Durante la fusión y proceso de soldaduraEl zinc tiende a evaporarse y oxidarse mucho, lo que provoca defectos como poros, fusiones incompletas y grietas.
El aluminio y sus aleaciones son conocidos por sus propiedades de ligereza (con una densidad de 2,7 g/cm3), alta resistencia específica, excelente conductividad eléctrica y térmica, resistencia a la corrosión y capacidad para conservar buenas propiedades mecánicas incluso a bajas temperaturas.
En el mundo actual, la energía, la seguridad y la protección del medio ambiente se han convertido en cuestiones cruciales. Con la creciente preocupación por la contaminación ambiental y la crisis energética, conseguir vehículos ligeros se ha convertido en un objetivo mundial.
En consecuencia, se han llevado a cabo numerosas investigaciones sobre estructuras compuestas de aluminio/magnesio, aluminio/titanio, titanio/aluminio y aluminio/acero en todo el mundo.
Las estructuras compuestas de aluminio y acero aprovechan al máximo las ventajas de ambos materiales para reducir el peso y la contaminación, y han encontrado amplias aplicaciones en los sectores de la automoción, la aviación y la construcción naval.
La aplicación de conexiones de aluminio-acero en el panel de la puerta del automóvil se representa en la figura siguiente.
Conectar aluminio y acero es extremadamente difícil debido a sus importantes diferencias en propiedades termofísicas.
El hierro tiene un punto de fusión de 1538 ℃ y una densidad de 7870 kg/m3, mientras que el aluminio tiene un punto de fusión de 660 ℃ y una densidad de 2700 kg/m3.
Durante el proceso de soldadura de aluminio y acero, el aluminio flotará sobre el acero cuando este último esté totalmente fundido, lo que dificultará la creación de una soldadura. Además, el aluminio tiene un coeficiente de dilatación lineal casi dos veces superior al del hierro, lo que provoca una gran tensión térmica y un mayor riesgo de grietas durante la soldadura.
El diagrama de fases binario Fe-Al muestra que el hierro y el aluminio pueden formar soluciones sólidas, compuestos intermetálicos y eutécticos.
Sin embargo, el límite de solubilidad sólida del hierro en el aluminio es mínimo.
A temperaturas comprendidas entre 225 y 600℃, la solubilidad sólida del Fe en Al oscila entre 0,01% y 0,022%. A la temperatura eutéctica de 652℃, la solubilidad del Fe en Al es de 0,53%. Numerosos estudios han demostrado que el Fe y el Al pueden combinarse para formar compuestos intermetálicos, como Fe3Al, FeAl, FeAl2, Fe2Al5 y FeAl3, que pueden causar estructuras frágiles en la soldadura.
Sin embargo, no todos los compuestos intermetálicos se desarrollan durante el proceso de soldadura, según el análisis termodinámico del Fe-Al. Según los cálculos de la energía libre de Gibbs, sólo Fe2Al5 y FeAl3 son las últimas estructuras frágiles estables.
La presencia de estructuras frágiles puede reducir las propiedades mecánicas de uniones soldadas y conducen fácilmente a la formación de grietas.
La soldadura por fusión de aluminio y acero puede ser un reto debido a la limitada solubilidad del Fe en el aluminio, lo que dificulta la obtención de una unión sólida.
Para evitar la formación de compuestos intermetálicos frágiles entre el acero y el aluminio, la superficie de acero debe recubrirse con metales compatibles tanto con el aluminio como con el hierro, como Ni, Zn, Ag y Cu.
Este revestimiento ayudará a evitar o minimizar la formación o el crecimiento de compuestos intermetálicos Fe-Al.
Los distintos metales de revestimiento tienen efectos diferentes en la reacción entre las interfaces de acero y aluminio, y la soldabilidad de metales distintos también puede variar.
Además de mejorar la soldabilidad del acero y aluminio, la selección de materiales de aportación y fundentes adecuados también puede mejorar la soldabilidad de metales distintos y ampliar su aplicación en diversas industrias.
La principal característica del láser profundo soldadura por penetración es su capacidad para crear agujeros de penetración profundos.
Este proceso implica la irradiación de la superficie metálica con láser de alta densidad de potencia, lo que provoca que el metal de la superficie alcance su punto de ebullición y se funda y vaporice rápidamente.
La evaporación resultante del metal genera una presión de aire que hace que la superficie se vuelva cóncava y forme pequeños agujeros.
Estos pequeños orificios aumentan la absorción de energía del láser.
El calor generado durante este proceso procede de la fusión del metal alrededor del pequeño orificio, así como del flujo de líquido fuera del orificio, la tensión superficial de la pared interior del orificio y la presión continua del vapor en la cavidad interior del orificio.
A medida que el rayo láser sigue entrando en el pequeño orificio, el material del exterior se funde y fluye continuamente.
Con el movimiento del rayo láser, el pequeño orificio permanece en estabilidad dinámica.
A medida que el haz de luz se desplaza, el metal fundido que rodea el pequeño orificio se desplaza con él, llenando continuamente el pequeño orificio hasta que se enfría y solidifica para formar una soldadura.
En la soldadura por penetración profunda con láser para unir acero-aluminio, la forma de unión más utilizada es la superior de acero e inferior de aluminio.
El rayo láser se dirige a la superficie de acero, provocando que tanto el acero como el placas de aluminio para fundirse y formar un orificio de soldadura.
Gsierra et al. realizaron un estudio sobre la soldadura por penetración profunda con láser de acero con la configuración de solapa superior de aluminio y junta de solapa inferior.
Los resultados de la investigación sugieren que controlar la penetración de la soldadura por debajo de 500 μm puede reducir la formación de compuestos intermetálicos Fe-Al y minimizar la fragilidad de la soldadura.
Controlando la penetración de la soldadura por debajo de 500 μm, la resistencia de la unión puede alcanzar los 250 MPa.
Sin embargo, puede haber algunos compuestos intermetálicos y bandas fundidas blancas, que se forman debido a compuestos ricos en aluminio, presentes en la soldadura.
Cuando la profundidad de penetración es inferior a 500 μm, la unión entre la soldadura y la aleación de aluminio es el punto de fallo de la unión.
Al aumentar la profundidad de penetración, la posición de fallo de la unión se desplaza y la resistencia de la unión disminuye significativamente. Kouadri David et al. realizaron un estudio sobre la microestructura y las propiedades de la soldadura por penetración profunda con láser y la soldadura por conductividad térmica con láser de acero galvanizado. acero y aleación de aluminio.
Limitando la penetración de la soldadura a 600μm, la resistencia de la unión soldada por penetración profunda láser alcanzó 140MPa. El estudio señaló que la penetración a lo largo de la dirección del espesor del acero tenía un impacto significativo en la resistencia de la unión.
De forma similar, Katsuyama et al. demostraron que la profundidad de penetración del acero en el aluminio era el factor clave que afectaba al rendimiento de la unión.
Toryamany et al. examinaron el Nd: YAG pulsado soldadura láser de acero de bajo carbono / 5754 aleación de aluminio utilizando láser de penetración profunda de soldadura estructura superpuesta en el experimento.
Se realizó un estudio sobre los efectos de potencia del láserLos resultados indican que la cantidad de compuestos intermetálicos aumenta con el aumento de la potencia pico del láser (a energía de pico constante, anchura de pulso y factor de solapamiento). Los resultados indican que la cantidad de compuestos intermetálicos aumenta con el incremento de la potencia pico del láser (a energía de pulso constante), la anchura de pulso (a potencia pico constante) y el factor de solapamiento (a energía de pulso y potencia pico constantes).
Jinyang et al. investigaron la relación entre la penetración y la formación de la soldadura en la soldadura por penetración profunda con láser de aluminio puro/acero inoxidable. Los resultados muestran que cuando la penetración es grande (354μm), se forma un compuesto intermetálico Fe-Al con microfisuras en la interfaz aluminio/zona de fusión, que es rica en aluminio. La resistencia de la unión es de (27,2 ± 1,7) MPa. La fractura se produce de tres formas: fractura frágil por cizallamiento, fractura frágil por escisión y fractura mixta.
Por el contrario, cuando la penetración es pequeña (108), la interfaz del Al/Fe zona de fusión es un compuesto intermetálico sin fisuras, y la resistencia de la unión es de (46,2 ± 1,9) MPa. Sólo se observa una forma de fractura, la fractura frágil por hendidura a lo largo de la soldadura.
Las ventajas de la soldadura por penetración profunda con láser incluyen un alto índice de utilización de la energía láser y una soldadura eficaz.
El ojo de la cerradura desempeña un papel crucial en la penetración y la anchura de la soldadura, y es un factor vital en el proceso de soldadura por penetración profunda con láser.
Sin embargo, el plasma y los agujeros de penetración profunda que se forman durante la soldadura pueden hacer que el proceso sea inestable y difícil de controlar.
Además, la entrada de gas en pequeños orificios y la formación de poros de solidificación son fenómenos habituales durante el proceso de soldadura por penetración profunda con láser.
La presión de vapor generada por el vapor metálico puede provocar depresiones superficiales y soldaduras antiestéticas debido a la contracción del metal durante la solidificación.
Cuando un rayo láser irradia la superficie de un material, parte del láser se refleja mientras que el resto es absorbido por el material. La energía láser absorbida se convierte en energía térmica, lo que provoca la fusión del material.
El calor en la superficie del material se propaga a través de éste por conducción térmica y acaba soldando los dos materiales.
La soldadura por conducción térmica láser es un proceso de soldadura importante en la soldadura láser, especialmente para piezas delgadas. La conducción térmica domina el proceso de propagación del calor en este modo de soldadura, mientras que la radiación y la convección desempeñan un papel menor que puede ignorarse.
Además, el baño de soldadura en la soldadura por conducción térmica láser es pequeño, por lo que puede ignorarse el impacto de los parámetros termofísicos con la temperatura y el estado en el proceso térmico de soldadura y la liberación de calor latente de cambio de fase en el baño de soldadura.
MECO y otros investigadores han utilizado calor láser soldadura por conducción para unir una placa de acero de 2 mm de espesor y una placa de aluminio de 6 mm de espesor de forma solapada, con el acero en la parte superior y el aluminio en la inferior. Cuando el láser irradia la superficie de la chapa de aceroEl calor transmitido funde la aleación de aluminio en su punto de fusión.
El espesor resultante del compuesto intermetálico fue de 4-20μm, siendo la microdureza máxima del Fe2Al5 de 1145HV.
Arco láser híbrido tecnología de soldaduracomo se muestra en el diagrama esquemático experimental de la Fig. 2, es un método de soldadura nuevo y eficaz desarrollado en la década de 1970.
La alta densidad de energía del láser permite una penetración más profunda, pero el puenteado del hueco es deficiente y la precisión de montaje debe ser alta.
El rango de calentamiento del arco es amplio, lo que permite obtener una soldadura más ancha, pero el puenteo del arco a la separación es bueno.
Aprovechando sus respectivas características, la tecnología de soldadura híbrida por arco láser puede obtener una soldadura de gran penetración y de amplio ángulo superior.
El plasma producido por el láser puede estabilizar el arco, lo que hace que el proceso de soldadura híbrida sea adaptable y eficaz.
Honggang Donga et al. inventaron un método para conectar metales distintos utilizando láser de punto grande y fuentes de calor compuestas de arco.
La patente se centra en la soldadura con fuente de calor híbrida por arco láser con un punto pequeño, que no puede aplicarse a la unión entre acero y aluminio, acero y cobre y otros metales distintos.
En este método, el láser tiene un efecto estabilizador evidente sobre el arco, que se utiliza para fundir el metal de aportación y el metal base de bajo punto de fusión.
El láser de punto grande puede controlar con precisión la entrada de calor.
Los ensayos de propiedades a la tracción en uniones de aleación de aluminio 5A02 y acero galvanizado obtenidos por este método muestran que la posición de fallo de la muestra se produce en el calor de soldadura zona afectada en un lado del metal base de aleación de aluminio, en lugar de la zona de conexión de soldadura fuerte. La resistencia de la unión puede alcanzar 153,1 MPa. Qin y otros adoptan la soldadura compuesta MIG láser de acero galvanizado/aleación de aluminio e hilo de soldadura AlSi5.
Los resultados experimentales muestran que la interfaz de soldadura fuerte produce de 2 a 4 μm, y los grupos de fases son FeAl2, Fe3Al5 y Fe4Al13. La resistencia máxima a la tracción de la unión es de 247,3 MPa.
Wangshujun et al. también utilizaron la tecnología de soldadura híbrida MIG láser y experimentaron con tres soldaduras diferentes: AlSi5, AlSi12 y AlMg5 para estudiar los efectos de los compuestos intermetálicos, la microestructura de la soldadura y la formación tras la adición de Si y Mg.
Los resultados muestran que el aumento del contenido de Si puede refinar los granos en la zona de fusión y aumentar la microdureza de la zona de fusión. La microdureza de la soldadura Al-Si en la zona de fusión es mayor que la de la soldadura Al-Mg.
El espesor medio de la capa de compuesto intermetálico para las soldaduras AlSi12, AlSi5 y AlMg5 es de 0,90 μm, 1,49 μm y 2,64 μm, respectivamente.
Se ha llegado a la conclusión de que la presencia de Si en las soldaduras inhibe la difusión del Fe y reduce la formación de compuestos intermetálicos.
El análisis por DRX de la capa intermedia revela que las capas de compuestos intermetálicos correspondientes a AlSi5 y AlSi12 están formadas por fases Fe2Al5, Fe4Al13 y Al0,5Fe3Si0,5, mientras que las correspondientes a AlMg5 están formadas por fases FeAl2, Fe2Al5 y Fe4Al13.
La resistencia de las soldaduras AlMg5, AlSi5 y AlSi12 es de 178,9 MPa, 172,43 MPa y 144 MPa, respectivamente.
Se ha llegado a la conclusión de que un aumento del contenido de Si es perjudicial para la resistencia de la junta, mientras que la adición de Mg la mejora. Sin embargo, no se ha explicado cómo afectan el Si y el Mg a la resistencia de las juntas.
Thomy et al. realizaron un estudio sobre la interacción entre láser y arco de plasma durante la soldadura híbrida por arco láser y desarrolló un cabezal de soldadura híbrida por arco láser coaxial.
La soldadura fuerte consiste en utilizar una soldadura con un punto de fusión inferior al del metal base. Al calentar a una temperatura superior al punto de fusión de la soldadura e inferior al punto de fusión del metal base, la soldadura se funde mientras que el metal base permanece sólido.
A continuación, la soldadura líquida humedece el metal base y, bajo la acción capilar de la brecha de soldadura, rellena automáticamente cualquier hueco en el metal base y se difunde con él para crear una unión resistente.
La soldadura por fusión combina las características de la soldadura fuerte y la soldadura por fusión, por lo que resulta ideal para unir materiales distintos con grandes diferencias en sus propiedades físicas.
Cuando se sueldan por fusión el acero y el aluminio, el acero permanece sólido mientras que el aluminio y la soldadura se funden. La conexión de soldadura fuerte resultante se forma en el lado acero/soldadura, mientras que la soldadura por fusión se produce en el lado soldadura/aluminio.
El principio básico de la soldadura por fusión de acero y aluminio consiste en combinar aluminio fundido y soldadura con acero sólido mediante una reacción de interfase.
En este método, se puede añadir o no soldadura para soldar.
Peyre et al. realizaron un estudio sobre la unión de acero galvanizado y aluminio aleación mediante soldadura por fusión con láser sin soldadura.
Sus hallazgos indican que se forma una capa de interfaz de 2 a 20 μm de espesor a lo largo de la interfaz acero-aluminio.
La capa está formada principalmente por la fase Fe2Al5, con una dureza de hasta 1200HV. Esto provoca grietas en la unión, causando una reducción significativa de las propiedades mecánicas de la unión.
La evaporación del zinc produce poros, pero un recubrimiento de zinc de 10μm de espesor favorece la humectación y la extensión del aluminio sobre el acero.
Los ensayos de tracción indican que el fundente de revestimiento en la superficie del acero galvanizado puede inhibir la evaporación del zinc. Sin embargo, el acero no galvanizado presenta una baja resistencia mecánica.
Para controlar la formación de compuestos intermetálicos Fe-Al y mejorar el rendimiento de la unión, algunos investigadores han utilizado soldadura durante soldadura láser para alterar la composición química de la junta.
Sierra et al. utilizaron soldadura 4047 (Al-12Si) en la conexión de soldadura fuerte por fusión láser de aluminio/acero, lo que dio como resultado una unión continua sin macrodefectos significativos y una fina capa de compuesto intermetálico Fe Al-Si en la interfaz acero/soldadura.
Se investigó el efecto del Si en el crecimiento de los compuestos intermetálicos Fe-Al utilizando soldadura Al-12Si. El mecanismo propuesto sugiere que el Si reduce la temperatura de fusión del aluminio, influye en la viscosidad y la tensión superficial del aluminio fundido y, posteriormente, afecta al ángulo y la anchura de humectación de la soldadura.
Además, algunos estudiosos han añadido Mg, Cu y otros elementos a la soldadura para explorar el efecto de la aleación de la soldadura en la microestructura y las propiedades de la soldadura.
Dharmendra et al. realizaron un ensayo de soldadura por fusión en una unión solapada de acero galvanizado DP600 y aleación de aluminio AA6016 utilizando láser Nd:YAG de pulso continuo.
En la prueba utilizaron alambre de soldadura Zn-Al con 85% de Zn y 15% de Al, y variaron la potencia del láser, la velocidad de soldadura y la velocidad de alimentación del alambre.
Los investigadores comprobaron que el grosor de la capa de reacción oscilaba entre 3 y 23μm.
Cuando el aporte térmico se situó entre 60 y 110J/mm, la resistencia a la tracción de la unión alcanzó los 220MPa, con la posición de fractura situada lejos de la soldadura y cerca del lado de la aleación de aluminio.
A velocidades de soldadura de 0,5 y 0,8m/min, los espesores correspondientes del compuesto intermetálico fueron de 8 y 12μm, respectivamente.
Las pruebas de tracción mostraron que la unión presentaba la mayor resistencia mecánica cuando el espesor del compuesto intermetálico se situaba entre 8 y 12μm.
Si el espesor era inferior a 8μm, la resistencia mecánica aumentaba a medida que aumentaba la capa intermetálica, mientras que si era superior a 12μm, la resistencia mecánica disminuía.
Se ha explicado que cuando la capa de compuesto es fina, la grieta se inicia a lo largo de la capa frágil de compuesto intermetálico, lo que da lugar a una resistencia a la fractura muy baja.
Por otra parte, cuando la capa de compuesto es gruesa, la resistencia mecánica también es baja debido a la fragilidad de la capa en relación con otras zonas.
Laukant et al. realizaron una prueba de soldadura por fusión con láser utilizando soldadura ZnAl2 en aluminio/acero. Los resultados mostraron que se produjeron capas de compuesto intermetálico de aproximadamente 5μm FeAl, y la fuerza de cizallamiento de la unión alcanzó hasta 9 KN.
Del mismo modo, Rajashekhara Shabadi et al. realizaron una prueba de soldadura por fusión con láser utilizando soldadura ZnAl30 en AA6016 y acero galvanizado con bajo contenido en carbono. El compuesto intermetálico formado en los resultados del ensayo es principalmente Fe2Al5Znx, que también puede contener ZnFeAl3, con un espesor de aproximadamente 10μm.
Recientemente, algunos estudiosos han realizado experimentos de soldadura por fusión láser en acero aluminizado de alta resistencia y aleación de aluminio.
Por ejemplo, Windmann et al. realizaron una prueba de soldadura por fusión láser con soldadura AlSi3Mn y descubrieron la formación de la fase Al8Fe2Si en la interfaz AlSi3Mn/Mn22B5.
Además, el espesor del compuesto intermetálico creado en la interfaz Mn22B5/AlSi3Mn es de 2 a 7μm, y la resistencia al cizallamiento de la unión es de 21 a 74MPa.
Precalentando la superficie de acero antes de soldar, la resistencia de la unión puede aumentar de 210 a 230 MPa.
Investigaciones recientes han demostrado que tanto la soldadura Al-Si como la soldadura Zn-Al crean inevitablemente compuestos intermetálicos.
No obstante, la secuencia de crecimiento de los compuestos intermetálicos Fe Al-Si y la identificación de la fase de reacción de la soldadura Zn-Al requieren más investigación.
La soldadura por fusión láser es una tecnología prometedora para unir acero y aluminio.
La soldadura híbrida por arco láser se utiliza principalmente para soldar chapas más gruesas debido a su gran eficacia de soldadura.
La soldadura por fusión láser tiene un gran potencial de aplicación en la fabricación de automóviles ligeros.
La fusión láser proceso de soldadura se utilizó para conectar metales delgados disímiles de aluminio y acero, utilizando soldaduras Al-Si y Zn-Al.
Sin embargo, la soldadura láser de aleaciones de acero/aluminio galvanizadas para la fabricación de automóviles sigue planteando varios retos. Por ejemplo, la baja capacidad de absorción del material a la energía láser da lugar a la generación de plasma, lo que puede afectar a la estabilidad del proceso de soldadura.
Además, el proceso de unión del aluminio y el acero puede producir compuestos intermetálicos Fe-Al quebradizos. Además, hay que tener en cuenta la compatibilidad metalúrgica de la soldadura fundida con el metal base de aleación de aluminio y su humectabilidad con el acero del metal base.
Por último, es crucial controlar y prevenir defectos de soldadura como poros, grietas, fusión incompleta e inclusión de escoria.