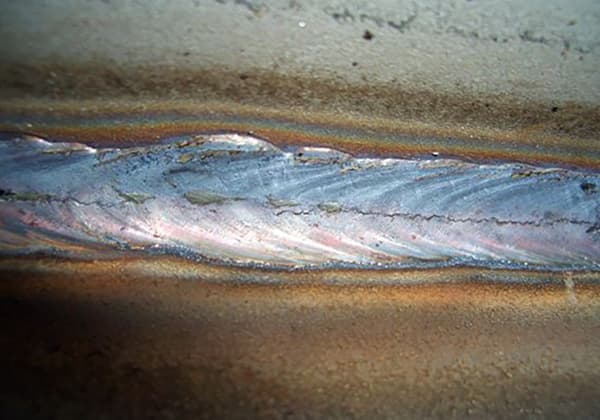
¿Qué pasaría si una pequeña fuga en su proyecto de soldadura pudiera provocar fallos importantes? Conocer y prevenir las fugas de soldadura es crucial para mantener la integridad y seguridad de tuberías, contenedores y otros equipos. Este artículo profundiza en seis métodos eficaces para la prevención de fugas en soldadura, proporcionando consejos prácticos y medidas de seguridad. Al final, estará equipado para abordar las fugas con eficacia y garantizar operaciones seguras e ininterrumpidas.
En la producción industrial, algunos equipos de funcionamiento continuo, como tuberías, válvulas y contenedores, desarrollan fugas por diversas razones. Estas fugas comprometen la estabilidad de la producción normal y la calidad de los productos, contaminan el entorno de producción y provocan pérdidas innecesarias.
En los casos más graves, la fuga de determinadas sustancias, como gases tóxicos y aceites, puede plantear riesgos significativos para la seguridad de las operaciones y el medio ambiente circundante.
Por lo tanto, las fugas de algunos productos industriales no pueden ignorarse y deben abordarse con prontitud. Sin embargo, es un reto técnico remediar las fugas de equipos que están bajo presión, contienen sustancias químicas inflamables, explosivas o tóxicas.
El sellado de fugas en equipos presurizados que contienen aceite o sustancias tóxicas implica una forma especial de soldadura en condiciones de trabajo anormales. Esto difiere de los procedimientos de soldadura estándar y hace hincapié en la seguridad durante las operaciones.
Antes de soldar, deben establecerse medidas de seguridad preventivas para proteger de accidentes el espacio de trabajo, al soldador y a otros trabajadores. El soldador debe tener experiencia y destreza, y la orientación de un ingeniero de soldadura con experiencia técnica es esencial para un funcionamiento seguro.
Por ejemplo, cuando se trata de un determinado tipo de depósito de aceite, es crucial conocer la capacidad, el punto de inflamación y la presión del aceite que contiene. Sólo cuando se esté seguro de que el proceso de soldadura no causará daños personales ni incidentes de seguridad mayores, en caso de que comiencen las operaciones de construcción.
Por lo tanto, antes y durante la operación de soldadura, deben respetarse los siguientes puntos:
1. Liberación segura de la presión.
Antes de proceder a la soldadura de estanqueidad, es fundamental verificar si la presión del equipo que se va a soldar podría causar daños personales. Además, bajo la influencia de la calor de soldadura fuente, el equipo debe tener un paso seguro de liberación de presión, como una válvula de seguridad instalada.
2. Control de temperatura.
Antes de soldar, deben estar bien preparadas todas las medidas de prevención de incendios y explosiones y de refrigeración. Durante la soldadura, el soldador debe respetar estrictamente el aporte térmico mínimo especificado en la documentación del proceso. Al mismo tiempo, deben aplicarse medidas de refrigeración seguras durante la soldadura para evitar la ignición o la explosión.
3. Prevención de intoxicaciones.
Al realizar soldaduras de sellado de fugas en un contenedor o tubería que contenga sustancias tóxicas, es vital garantizar la ventilación oportuna de cualquier fuga de gases tóxicos y el suministro de aire fresco. También deben tomarse medidas para aislar cualquier posible contaminación derivada de la fuga de sustancias tóxicas.
A continuación se presentan varios métodos de sellado de fugas por soldadura utilizados habitualmente en la práctica de la ingeniería para el aprendizaje y la mejora de todos.
Este método es aplicable a grietas de soldaduraEn los recipientes de baja presión y en las tuberías, se pueden producir fisuras, sopladuras y porosidades. En la medida de lo posible, deben utilizarse varillas de pequeño diámetro, y la corriente de soldadura debe seguir estrictamente los requisitos del proceso.
La operación adopta el método de soldadura rápida, utilizando el calor del arco para calentar los alrededores del punto de fuga. Tras apagar el arco, apriete rápidamente hacia la fuga con un martillo de mano o una pala afilada, martilleando la soldadura mientras suelda.
Cuando algunas grietas son más anchas, o el diámetro de los orificios o la porosidad es mayor, la torsión del martillo se convierte en un reto. Puede ser útil remachar primero la grieta o el agujero con alambre de hierro adecuado o varilla para soldar para reducir la presión y el flujo de la fuga y, a continuación, completar la soldadura con una soldadura rápida de baja corriente.
El punto clave de este método es bloquear sólo una sección cada vez y luego soldar rápidamente, repitiendo el proceso de bloquear y soldar como se muestra en la figura 1.
Algunas fugas se producen debido a la corrosión y al desgaste. En tales casos, debe evitarse la soldadura directa en el lugar de la fuga, ya que puede provocar agujeros más grandes. En su lugar, soldadura por puntos debe realizarse en posiciones adecuadas adyacentes o por debajo de la fuga. Estas zonas, que no presentan fugas, sirven de base para establecer un baño de soldadura.
A continuación, de forma similar a como las golondrinas construyen sus nidos con barro, rodee gradualmente la fuga con soldadura, reduciendo poco a poco el área de la fuga. Por último, selle la fuga utilizando una varilla de soldadura de pequeño diámetro a una corriente de soldadura adecuada, como se ilustra en la figura 2.
Este método es aplicable a la soldadura cuando el área de fuga es grande, el caudal es elevado o la presión es sustancial, como se muestra en la figura. Se crea un parche con un dispositivo de cierre basado en la forma de la fuga.
Para fugas graves, el dispositivo de cierre emplea una sección de una tubería de desviación provista de una válvula; para fugas menores, se suelda previamente una tuerca al parche. La superficie del parche debe ser superior a la de la fuga, y el dispositivo de cierre del parche debe estar orientado directamente hacia la fuga.
Se aplica una capa de sellante alrededor de la zona de contacto del parche y la fuga, lo que permite que el medio fugado escape a través del tubo de desviación, reduciendo la fuga alrededor del parche. Una vez que el parche está bien soldado, se cierra la válvula o se aprieta el perno.
Cuando una tubería tiene muchas fugas debido a la corrosión o al desgaste, se utiliza un tubo manguito del mismo diámetro o uno que pueda encerrar con precisión la tubería con fugas. La longitud del tubo manguito se determina en función de la zona de la fuga.
El tubo manguito se corta simétricamente en dos mitades y se suelda un tubo de desviación, utilizando el mismo procedimiento de soldadura que para la soldadura de desviación. En cuanto a la secuencia de soldadura, en primer lugar debe soldarse la costura circunferencial entre el tubo y el manguito, seguida de la costura circunferencial entre el tubo y el manguito. costura de soldadura del propio manguito, como se ilustra en la figura siguiente.
Soldadura continua no puede emplearse; es crucial asegurarse de que la temperatura del cordón de soldadura no suba demasiado. Se realiza una soldadura por puntos, seguida de un enfriamiento inmediato. Por ejemplo, después de soldar por puntos unos cuantos puntos, los puntos soldados se enfrían inmediatamente con una gasa empapada en agua.
A veces, puede ser necesario combinar varios métodos de detención de fugas. El proceso de soldadura para detener fugas requiere flexibilidad para garantizar el éxito.
Sin embargo, no todos los materiales metálicos son adecuados para el método de sellado por soldadura. Sólo el acero común de bajo contenido en carbono y el acero de bajo acero aleado pueden aplicar estos métodos de detención de fugas.
El acero inoxidable austenítico sólo puede repararse mediante soldadura si se confirma que el metal base próximo al punto de fuga puede sufrir una deformación plástica significativa. De lo contrario, no puede repararse mediante soldadura.
El medio en el interior del tubo de acero resistente al calor suele ser vapor a alta temperatura y alta presión. Las fugas que se producen tras un servicio prolongado no pueden repararse bajo presión. El acero para bajas temperaturas no permite soldadura a presión reparaciones.
Todos los métodos de detención de fugas por soldadura mencionados anteriormente son medidas temporales. No poseen las propiedades mecánicas que suele alcanzar la soldadura en sentido estricto.
Cuando el equipo no está bajo presión y no está equipado con un medio, es necesario eliminar por completo este estado temporal de la soldadura para evitar fugas, y volver a soldar o reparar de otra forma para cumplir los requisitos de uso del producto.
Fugas tecnología de soldadura es una técnica de emergencia necesaria en el proceso de producción continua con el desarrollo de la producción moderna.
La gestión de los accidentes de fuga requiere puntualidad y, posteriormente, debe llevarse a cabo un tratamiento de sustitución exhaustivo en el lugar de la fuga. La aplicación de la tecnología de detención de fugas requiere flexibilidad.
Se pueden combinar varios métodos de soldadura para tratar una fuga, con el objetivo principal de que no se produzcan fugas después de la soldadura.