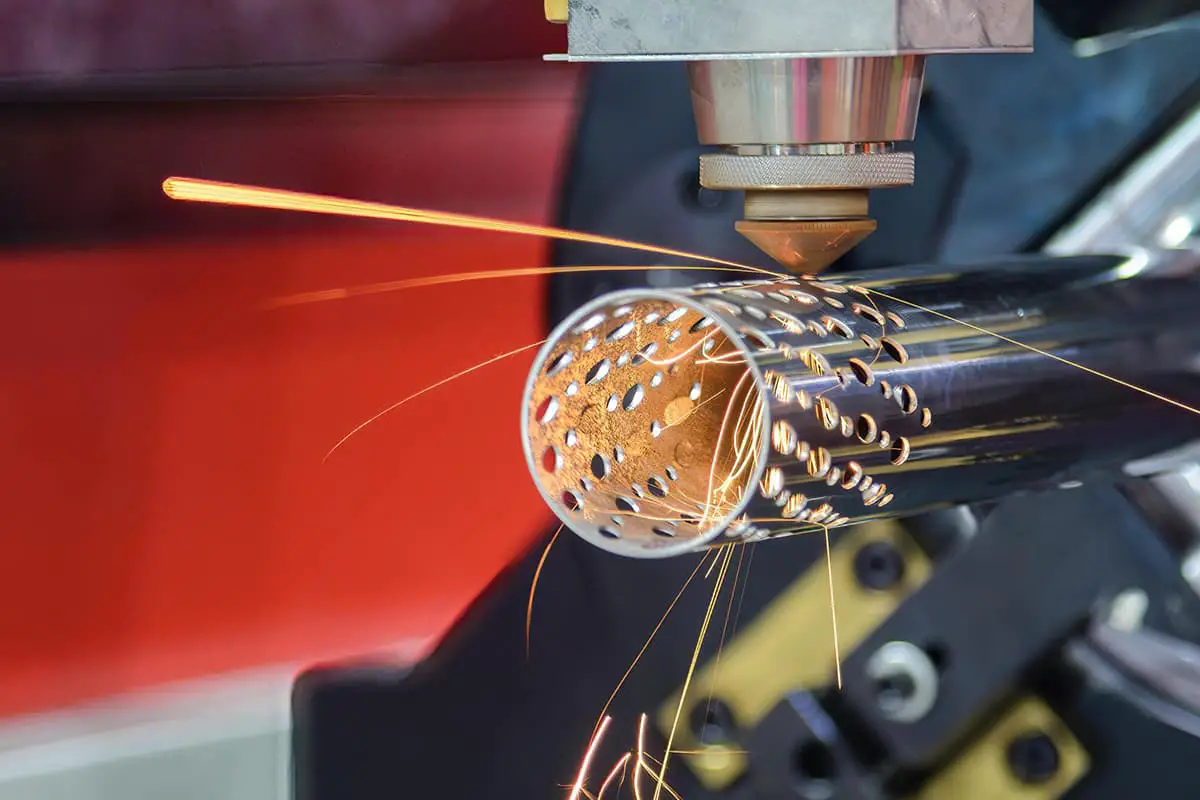
¿Qué garantiza un corte perfecto en oxicorte? Desde la elección del gas de corte hasta la altura exacta de la boquilla, todos los factores desempeñan un papel fundamental. Este artículo profundiza en los elementos clave que influyen en la calidad de los cortes con oxicorte y ofrece información sobre cómo optimizar los procesos de corte para obtener resultados superiores. Los lectores aprenderán a seleccionar los parámetros adecuados, ajustar las velocidades de corte y aplicar técnicas avanzadas para lograr cortes precisos y eficaces. Explore estos consejos esenciales para mejorar su rendimiento de corte y minimizar los defectos.
El control de calidad del proceso de corte es crucial en el primer paso de producción de las empresas. Dado que el oxicorte es el método principal de corte y blanking, garantizar su calidad de producción tendrá un gran impacto en el proceso global de corte y blanking.
Este artículo se centra en los factores que influyen en la calidad del oxicorte y ofrece soluciones a los problemas de corte habituales mediante métodos de proceso.
A pesar de su importancia como principal método de corte para pequeñas, medianas y grandes empresas, corte con llama no está exenta de desafíos.
A lo largo de los años, el oxicorte ha evolucionado y los equipos de corte CNC se han vuelto avanzados y sofisticados. Como resultado, se han desarrollado diversos métodos y técnicas de proceso para mejorar la calidad del oxicorte.
En este artículo, utilizamos el software de anidado automático XSuperNEST para examinar los factores que afectan a la calidad de las piezas cortadas mediante oxicorte y las formas de mejorar su rendimiento.
La industria del corte de metales ofrece actualmente una amplia gama de métodos y equipos de corte, cada uno con ventajas distintas. Tecnologías avanzadas como el corte por láser, plasma y chorro de agua han surgido como alternativas superiores, ofreciendo una mayor precisión de corte y una eficiencia de producción significativamente mejorada en comparación con el oxicorte tradicional. A pesar de estos avances, el oxicorte mantiene su relevancia en la industria debido a su rentabilidad y versatilidad, especialmente para aplicaciones de chapa gruesa.
Las máquinas de oxicorte de control numérico por ordenador (CNC) se han generalizado en los procesos de producción de corte modernos. Estos sistemas ofrecen la ventaja de una programación automatizada y sin interferencias, lo que permite patrones de corte complejos y una mayor repetibilidad. Sin embargo, esta automatización presenta un reto único: la incapacidad de intervención del operario en tiempo real para compensar la deformación térmica durante el proceso de corte. Esta limitación puede dar lugar a imprecisiones dimensionales en el producto final, especialmente cuando se cortan placas gruesas o materiales con alta conductividad térmica.
Varios factores intrínsecos a las máquinas de corte CNC pueden afectar significativamente a la calidad del corte:
La elección del gas de corte tiene un impacto significativo en la calidad de los cortes de las máquinas de oxicorte. Actualmente, los gases disponibles son acetileno, propileno, propano y MPS. Cada gas tiene unas características de combustión únicas, que dan lugar a diferentes escenarios de corte, y la elección del gas adecuado puede maximizar los beneficios de corte con gasde corte eficiente y rentable.
La llama de acetileno se caracteriza por su calor concentrado, alta temperatura, corto tiempo de precalentamiento, bajo consumo de oxígeno, alta eficacia de corte y mínima deformación de los componentes. Esto la hace adecuada para cortar chapas finas y piezas cortas.
Por otra parte, la llama de propano tiene calor disperso, baja temperatura y un tiempo de precalentamiento más largo en comparación con el acetileno. También da como resultado un borde superior del corte liso y plano y menos escoria en el borde inferior, que es más fácil de eliminar. Además, su coste relativamente bajo lo convierte en una opción económica para cortar grandes piezas de chapas gruesas.
La llama de propileno tiene una temperatura más alta y un tiempo de precalentamiento más corto que la de propano, ligeramente superior a la de acetileno. Su alto contenido de calor en la llama exterior lo hace adecuado para cortar grandes partes de chapas gruesas.
Además de la selección del gas adecuado, la presión del oxígeno de corte, la velocidad y el ajuste de la altura de la boquilla también son factores cruciales que afectan a la calidad del oxicorte.
Se ha observado que el aumento de la concentración de oxígeno disminuye tiempo de corte mientras se reduce la demanda de oxígeno, con la misma presión de oxígeno.
La elección de la velocidad de corte es especialmente importante. Si la velocidad es demasiado alta, pueden producirse defectos de calidad como "flameado", desbastado cortey una menor eficacia de corte. Por otra parte, si la velocidad es demasiado lenta, puede dar lugar a la adhesión de escoria de oxidación y desigual. corte superficie.
Basándonos en la experiencia práctica, la mejor velocidad de corte debería estar en el rango medio-alto o medio-alto de la velocidad nominal de la máquina. boquilla de corte. Por ejemplo, si se utiliza una boquilla n.º 5 para cortar una placa de 40 mm. chapa de aceroLa velocidad nominal es de 250 ~ 380 mm/min, con una velocidad media de 315 mm/min. Dividiendo la gama en 10 niveles, se encuentra que la mejor velocidad está entre 336,6 ~ 358mm/min, siendo 340mm/min la elección óptima.
La elección de la altura de la boquilla de corte también afecta a la calidad del corte. Si el centro de la llama es demasiado bajo, puede entrar en contacto con la superficie de la pieza, provocando el colapso del corte, el bloqueo de la boquilla por salpicaduras de escoria o incluso el revenido. Por otro lado, si la altura es demasiado alta, la llama no puede calentar completamente la sangría, reduciendo la capacidad de corte y dificultando la eliminación de escoria. En general, se recomienda mantener una distancia de 3 a 5 mm entre el centro de la llama y la superficie de trabajo para obtener los mejores resultados.
Un orden de corte razonable favorece el calentamiento uniforme de la chapa de acero y compensa las tensiones internas, reduciendo la deformación térmica de las piezas.
Al cortar el contorno de las piezas, se recomienda seguir el principio de primero dentro y luego fuera, primero pequeño y luego grande, primero redondo y luego cuadrado, salto en cruz, primero complicado y luego sencillo, para evitar el desplazamiento, la deformación y la desviación de tamaño de las piezas.
Una posición y una forma de avance adecuadas pueden mantener la integridad de la muesca de la pieza y mejorar la estabilidad del corte, garantizando la calidad del contorno.
En la producción práctica, la posición de introducción del contorno exterior suele estar situada a la derecha de la parte inferior del contorno, y la forma de introducción del contorno interior se representa mejor mediante un arco circular.
Incluso después de una perfecta configuración y depuración de los parámetros del equipo de oxicorte, no hay garantía de que las piezas se corten sin defectos. La forma de la pieza, el grosor de la chapa, la posición del material de anidado y el método de corte pueden afectar a la calidad del corte.
Por ejemplo, las placas oxicortadas pueden dividirse en placas finas (grosor <20 mm), placas de grosor medio y placas gruesas.
Las chapas finas son fáciles de perforar durante el proceso de corte, pero propensas a la deformación térmica. Para reducir la deformación térmica y el arqueamiento de las piezas, se recomienda cortar desde el interior de la placa de acero en lugar de hacerlo desde el borde. Esto ayuda a mantener la integridad del marco exterior de la placa de acero.
El uso del proceso de "corte continuo" puede reducir el número de perforaciones, mientras que el proceso de "corte estacionario" puede reducir eficazmente la deformación térmica.
En el caso de las chapas de espesor medio y grueso, la deformación térmica es mínima durante el proceso de corte, pero las perforaciones pueden provocar escoriaciones y daños en la boquilla de corte. Para reducir las perforaciones, se recomienda utilizar el precalentamiento del borde antes de iniciar el corte. La figura 1 muestra el método convencional de corte con precalentamiento de bordes.
Figura 1 Método convencional de precalentamiento del filo de corte de plomo
El método convencional de precalentamiento de los bordes puede resolver eficazmente el problema de la perforación de materiales de grosor medio y grueso. corte de chapapero requiere mucho ajuste humano en la descarga y requiere personal de anidado de alta calidad y precisión de la máquina de corte.
Para solucionar este problema, el software XSuperNEST ofrece un nuevo "proceso de perforación en I" para optimizar la trayectoria de corte y perforación.
El método de corte de plomo de precalentamiento del borde de perforación I encuentra automáticamente una ubicación adecuada para cortar un orificio circular inferior basándose en el contorno exterior de la pieza cortada y utiliza el orificio circular para introducir la siguiente pieza para precalentarla, reduciendo las perforaciones.
Figura 2 I Método de corte de plomo con precalentamiento del borde perforado
Para mejorar el aprovechamiento del material, las piezas pequeñas suelen estar anidadas dentro del contorno interior de piezas más grandes, y la trayectoria de corte suele implicar cortar primero la pieza del contorno interior, luego saltar para cortar la siguiente pieza del contorno interior y, por último, cortar los dos contornos interiores por separado. Esto da como resultado una baja eficiencia de corte, ya que la máquina de corte tiene que levantar la pistola varias veces y perforar el agujero varias veces.
Para solucionar este problema, se puede optimizar la trayectoria de corte utilizando el proceso de "corte continuo" para reducir el proceso de perforación y vaciado. La figura 3 muestra la secuencia de corte optimizada tras utilizar el proceso de "corte continuo".
En la figura 3, cada parte dentro del contorno interior se corta en una fila, seguida del corte del plomo del contorno interior en una fila. Esto permite cortar las piezas dentro del contorno interior y el contorno interior con una sola perforación, mejorando enormemente la eficiencia del corte.
Figura 3 Secuencia de corte tras la optimización del proceso de "corte continuo
En el proceso de corte del contorno interior de una pieza, puede producirse un desajuste entre el tamaño real y el tamaño teórico entre los contornos interior y exterior.
Por ejemplo, como se muestra en la figura 4, las dimensiones teóricas marcadas para una pieza con un grosor de 50 mm son de 610 mm, pero las dimensiones reales tras el corte son entre 3 y 5 mm menores.
Esto se debe a la acumulación de calor al cortar el contorno interior, que aumenta aún más al cortar el contorno exterior. Como no hay apoyo en el contorno interior durante el corte del contorno exterior, éste se extruye hacia dentro por el calor, provocando la deformación de la pieza.
Figura 4 Diagrama de anidamiento de piezas
En esta situación, añadir un proceso de "corte de estancia" puede ser una solución.
Como se muestra en la Figura 5, el "corte de sujeción" se añade alrededor del contorno interior para mantener el contorno del marco del contorno interior y proporcionar soporte a la pieza.
Este método reduce eficazmente los errores de corte y mejora la precisión de corte, pero el inconveniente es que el contorno interior requiere pulido.
Figura 5 Trayectoria de corte tras la optimización del proceso "stay cut
El método de introducción tradicional consiste en cortar en el contorno de la pieza utilizando una línea recta a lo largo del borde recto del contorno y, a continuación, a lo largo del borde recto de la introducción. Esto no afecta a la calidad del corte siempre que el inicio de la introducción de la pieza sea recto.
Sin embargo, al cortar el orificio circular interior, el método de introducción tradicional conduce a una falta de transición suave al cortar directamente en el contorno, lo que provoca el sobrecalentamiento del contorno y afecta a la calidad del corte, como se muestra en la Figura 6.
Figura 6 Sobrecalentamiento del agujero redondo interior
Durante el proceso de investigación, XSuperNEST introdujo el método de introducción del arco para evitar la sobrecombustión del arco y mejorar la calidad del corte del orificio circular interior de la pieza.
El método de corte por introducción de arco, que se muestra en la figura 7, utiliza un arco tangente al orificio circular interior para crear una transición suave, dejando un hueco con el punto de inicio de la introducción y conectando suavemente con un arco circular.
La eficacia de este método se ha comprobado y confirmado mediante la producción real, como se muestra en la figura 8.
Figura 7 Arco circular que conduce al corte
Figura 8 Utilización de arcos circulares para conducir a piezas cortadas
El corte por soplete, como paso inicial de la producción, es fundamental para el éxito de una empresa. El oxicorte, al ser el principal método de corte, repercute directamente en la calidad y la productividad de la producción.
Por lo tanto, es imperativo controlar eficazmente la calidad del oxicorte.
Hay varios factores que afectan a la calidad del corte, como el propio equipo, la elección del gas, la velocidad de corte, la altura de la boquilla, la secuencia de corte, etc.
Utilizando los parámetros adecuados en función de las condiciones reales de producción, se puede mejorar la calidad del corte y aumentar la tasa de piezas cualificadas.
Además, al optimizar la trayectoria de corte mediante el uso del proceso de corte adecuado en función del grosor, la forma del contorno y otras características de las piezas, se puede reducir el error de producción de las piezas, mejorar la eficiencia y la calidad del corte de las piezas y, en última instancia, aumentar la eficiencia de la producción de la empresa.