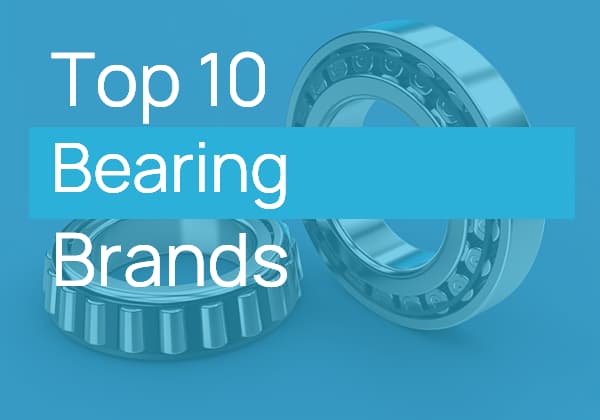
What makes the right bearing crucial for machine performance? Selecting a bearing involves considering space constraints, load capacity, rotation speed, accuracy, rigidity, and noise levels. This article dives into the essential factors engineers must evaluate to optimize bearing selection for various applications. Readers will gain insights into choosing the right bearing type and specifications to enhance machinery efficiency and longevity.
Various types of bearings have different characteristics due to their different designs.
Due to the variability and complexity of specific installation locations and bearing applications, there is no fixed mode for selecting a bearing type.
To adapt to the specific installation position and application conditions of a given host, it’s recommended to comprehensively consider the following main factors when selecting a bearing type.
In mechanical design, the size of the shaft is typically determined first, and then the bearing is selected based on the size of the shaft.
Generally, ball bearings are used for small shafts. Cylindrical roller bearings, self-aligning roller bearings, and tapered roller bearings are used for large shafts (although ball bearings can also be used).
If the radial space of the bearing installation position is limited, a bearing with a smaller radial section height should be used.
Examples of such bearings include needle bearings, some series of deep groove ball bearings, angular contact ball bearings, cylindrical roller or self-aligning roller bearings, and thin-walled bearings.
If the axial space of the bearing installation position is limited, a bearing with a smaller width can be used.
Load size is usually the decisive factor in the selection of bearing size.
The bearing capacity of roller bearings is larger than that of ball bearings with the same dimensions.
Generally, ball bearings are suitable for light or medium loads, while roller bearings are suitable for bearing heavy loads.
For pure radial loads, deep groove ball bearings and cylindrical roller bearings can be chosen.
For pure axial loads, thrust ball bearings and thrust cylindrical roller bearings can be selected.
When there is a combination of radial and axial loads, angular contact ball bearings or tapered roller bearings are generally selected.
If the radial load is large and the axial load is small, deep groove ball bearings and cylindrical roller bearings with ribs in the inner and outer rings can be selected.
If there is a large deformation of the shaft or shell and poor alignment, self-aligning ball bearings and self-aligning roller bearings can be selected.
If the axial load is large and the radial load is small, thrust angular contact ball bearings and four-point contact ball bearings can be selected.
If self-aligning performance is required, thrust self-aligning roller bearings can be selected.
The working speed of a rolling bearing mainly depends on its allowable operating temperature.
Bearings with low friction resistance and less internal heating are suitable for high-speed operation.
When only bearing radial loads, deep groove ball bearings and cylindrical roller bearings can achieve higher speeds.
If bearing combined loads, angular contact ball bearings should be selected.
High-precision angular contact ball bearings with a special design can achieve very high speeds.
The rotational speed of thrust bearings is lower than that of radial bearings.
For most machines, bearings with grade 0 tolerance are enough to meet the requirements of the main engine.
However, when there are strict requirements on the rotational accuracy of the shaft, such as machine tool spindles, precision machinery, and instruments, deep groove ball bearings, angular contact ball bearings, tapered roller bearings, cylindrical roller bearings, and thrust angular contact ball bearings with higher tolerance levels should be selected.
The rigidity of a rolling bearing is determined by its elastic deformation under load. In general, this deformation is very small and can be ignored. But in some machines, such as machine tool spindle systems, the static stiffness and dynamic stiffness of the bearing have a great influence on the characteristics of the system.
Generally, roller bearings have higher stiffness than ball bearings. The rigidity of all kinds of bearings can also be improved by proper “pre-tightening”.
The noise and vibration of the bearing itself are generally very low. However, for small and medium-sized motors, office machinery, household appliances, and instruments that have special requirements for noise and running stability, low-noise bearings are usually used.
The most common configuration for bearings is to install a set of axially positioned “fixed bearings” at one end of the shaft and a set of axially movable “floating bearings” at the other end to prevent the shaft from sticking due to thermal expansion and contraction.
The commonly used “floating bearing” is a cylindrical roller bearing with no rib on the inner or outer ring. At this time, the fit between the inner ring and the shaft, or the fit between the outer ring and the shell hole can adopt an interference fit.
Sometimes, a non-separable deep groove ball bearing or self-aligning roller bearing can be selected as a floating bearing, but a clearance fit should be selected when the inner ring is matched with the shaft or the outer ring is matched with the housing hole during installation, to ensure that the inner ring or outer ring has enough freedom of axial movement.
The friction resistance of a ball bearing is smaller than that of a roller bearing, and the friction resistance of a radial contact bearing is smaller under pure radial load.
Similarly, under pure axial load, the friction resistance of an axial contact bearing is small. Under the combined load, the friction resistance of an angular contact bearing whose contact angle is close to the load angle is the smallest.
In instruments and machines that require low friction torque, it is more appropriate to choose ball bearings or cylindrical roller bearings.
Moreover, low friction torque bearings should avoid contact seals. At the same time, it is suggested to use oil drop lubrication, oil-air lubrication, or other lubrication methods that are conducive to reducing wear.
When bearings with cylindrical inner holes are used in machinery that requires frequent installation and disassembly, it is recommended to use separable angular contact ball bearings, tapered roller bearings, separable cylindrical roller bearings, needle roller bearings, and thrust bearings.
Bearings with conical inner holes can be installed on the journal or on cylindrical journals with the help of fixing sleeves or dismounting sleeves, making installation and disassembly more convenient.
In the process of bearing selection, considering factors such as durability and precision is essential to achieve optimal performance and longevity. Durability refers to the ability of bearings to withstand various loads and operating conditions without succumbing to wear or failure.
Precision, on the other hand, pertains to the accuracy of a bearing’s rotation and the minimization of noise and vibration during operation.
To ensure durability, it is crucial to select the appropriate bearing size, material, and type based on the specific requirements and operating conditions. Assessing factors such as speed, temperature, and lubrication can significantly impact a bearing’s lifespan and overall performance.
Furthermore, adherence to ISO-approved methodologies for sizing bearings can help guarantee suitable load ratings and life expectancy for a given application.
Precision in bearing selection is achieved by examining the requirements of the application, such as desired rotational accuracy, speed, and loading conditions. Selecting bearings with suitable tolerances and clearances, along with compatible sealing and proper lubrication, contributes to improved precision and reliability.
In conclusion, a thorough understanding of bearing selection criteria is required for successful implementation in various industries. By considering durability and precision in the selection process, engineers and designers can optimize system performance and extend the service life of bearings.
As result, potential mechanical issues and costly maintenance processes can be reduced, ultimately leading to the overall success of countless projects and applications.