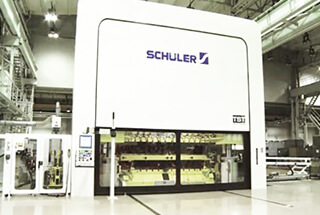
Have you ever considered what makes fiber cement board an essential material in modern construction? This versatile, durable material is crafted from a blend of natural fibers and cement, offering remarkable fire and water resistance. It’s ideal for various applications, from interior walls to roofing. In this article, we’ll explore the production process, benefits, and pricing factors of fiber cement board, ensuring you understand its pivotal role in building innovation. Discover how it enhances construction efficiency while providing long-lasting performance and aesthetic appeal.
Fiber cement board is a novel type of building material formed from natural fiber and cement through processes of pulping, molding, cutting, pressing, and curing.
It features lightweight, high strength, water resistance, fire resistance, decay resistance, large size, good workability, and improved construction efficiency.
It is extensively used in both residential and industrial buildings. It can be applied to interior walls, exterior wall panels, ceiling panels, curtain wall linings, composite wall panels, insulation materials, sound-absorbing barriers, and roof installations.
Fiber cement board is a composite material made of sand, cement, and plant fibers. It comes in several visual variations, including cross-grain, wood grain, wall-protective, and ovate surface designs.
Available in block form, the board can be used for attic floors, wall linings, soffit/eave panels, or as a base layer beneath bathroom tiles. Not only can it serve as external wall cladding, but it can also function as a fireboard.
What factors determine the price of fiber cement boards?
By adding fibers to high-grade cement substrates, the material’s crack resistance and brittleness can be improved, enhancing its deformation capacity.
The type, length, cross-sectional dimensions, and bonding characteristics of the fiber with the cement substrate will all influence the macro performance of the fiber cement board material.
Fiber cement boards can be formed through various methods, such as conventional casting, papermaking, mold pressing, extrusion, and more. The forming method usually has some impact on its performance.
Different raw materials and production processes determine the price of fiber cement boards, along with the inherent properties of the boards themselves.
Factors affecting the price of fiber cement board’s raw materials include:
1. Component composition: fiber type, cement grade, pulp
2. Production process: type of production equipment, whether the production equipment is complete (hydraulic press and its tonnage)
3. Post-production care: national regulations require a mandatory seven-day curing period in a designated curing chamber.
Fire and Insulation Resistance: The board is classified as Class A non-combustible; in the event of a fire, it will not ignite nor produce toxic smoke. It has a low electrical conductivity, making it an ideal insulating material.
Water and Moisture Resistance: In semi-open air and high humidity environments, it retains stable performance without sagging or deformation.
Heat and Sound Insulation: The board has a low thermal conductivity, providing excellent insulation, and its high density ensures good soundproofing.
Lightweight and High Strength: The boards pressed with a 5,000-ton flat hydraulic press not only have high strength but also resist deformation and warping. They are lightweight and suitable for roofing.
Simple Construction: The board can be installed and constructed easily and quickly with a dry operation, including fitting onto frames and wooden panels. Deep-processed products also offer simplicity and improved performance.
Economical and Aesthetic: With its lightweight nature and compatibility with frames, it effectively reduces construction and renovation costs. Its uniform color and smooth surface can enhance the appearance of buildings when used directly.
Safe and Harmless: It falls below the national “Radiation Health Protection Standards for Building Materials,” with an index equal to that of a lawn 20 meters away from surrounding buildings.
Long Service Life: Resistant to acids, alkalis, corrosion, and not susceptible to damage by moisture or insects, the board’s strength and hardness increase over time, ensuring longevity.
Excellent Workability and Secondary Decorating Performance: The fiber cement board can be sawn, perforated, carved, nailed, painted, tiled, wallpapered, etc., according to actual conditions.
To install, first lay out lines according to the blueprint requirements and actual on-site dimensions. Use a dynamic arm to horizontally fix the main keel onto the floor, with an approximate distance of 1m between each keel, ensuring that the cladding keels are installed on the same level.
When laying the fiber cement board, the long side of the board must be perpendicular to the direction of the auxiliary keel, and the joints in the board width direction should be staggered.
The distance from the screw to the edge of the board should be 15mm, and from the screw to the corner of the board, 50mm. The distance between screws should be between 180 and 200mm.
Prior to sealing the steel plate, snap a line on the surface of the steel plate according to the partition of the keel, and pre-drill a shallow pit at the position where the nail head passes to ensure that after the installation screw, the board surface is flat, the screw head sinks into the board, and is less than 0.5mm from the board surface.
When fixing the fiber cement board, start from the center and then secure the perimeter. The gap between each panel should not be less than 5mm, and there should be an expansion joint 10-15m from the top of the longitudinal channel.
The Fiber Cement Board Press is primarily used for compressing stacked calcium silicate fiber/cement board blanks to facilitate water drainage, increase density, and meet requirements. The machine is composed of a main host, hydraulic control system, and an electrical control system.
The widely used cement brick pallets are molded from GMT glass fiber materials. This composite material pallet is a replacement for bamboo glue boards, wooden boards, rubber boards, and plywood, and features wear resistance, impact resistance, vibration resistance, waterproofing, corrosion resistance, and anti-aging properties. GMT glass fiber cement brick pallet molding equipment is specifically the Four-Column Hydraulic Press.
The Four-Column Hydraulic Press works by leveraging a hydraulic control system to enhance the hydraulic regulating valve. The electrical control system, through the pump, hydraulic cylinder, and various hydraulic valves, accomplishes energy conversion, regulation, and delivery to complete the entire molding process.
This machine is characterized by its compact structure, responsive and reliable operation, fast speed, low energy consumption, low noise, and the ability to adjust pressure and stroke within a specified range. Operation is straightforward.
By changing molds, one machine can produce various models of brick pallets and perform the pressing process for cement bricks. Common specifications for composite brick pallets are as follows:
1400*1400* 30mm, 1350*1150* 30mm, 1350* 880* 28mm, 1250*900* 25mm, 1180* 880* 25mm, 1350* 700* 30mm, 980*860*22mm, 850*850* 20mm, 980*680* 20mm, 1100*560*25mm
The molding process of cement brick pallets in a Four-Column Hydraulic Press includes:
Crushing and mixing: the fiber, felt, and plastic are mixed in a weighed ratio. The mix is then added to a crusher for crushing and blending.
(1) Heating and melting: The crushed mixture is added to a heater for melting at a temperature between 600°C-850°C, with a heating time of 6min-10min.
(2) Compression molding: The heated and melted fiber material is stacked and placed into the mold of the Four-Column Hydraulic Press. The molding process is completed by applying a pressure between 5000MPA-6000MPA.
(3) Forming: The initially compressed fiber material is placed into a laminating machine to be shaped into fiber boards using the hydraulic press.
Features of the molded cement brick pallets:
By utilizing a mix of crushed glass fiber (hereafter referred to as “fiber”), felt, and plastic, which is then heated to a high temperature and melted, stacked, and inserted into a composite material molding hydraulic press for high-pressure compression molding.
After which, it is placed into a laminating machine for shaping. The final fiber boards, in addition to possessing the characteristics of conventional fiber boards like light weight, sound absorption, heat insulation, environmental friendliness, and flame retardance, have an aesthetic and smooth exterior due to the inclusion of felt and plastic. The boards are also more wear-resistant and pressure-resistant, making them less prone to breaking during use.
Precautions for operation of the Four-Column Hydraulic Press:
The Four-Column Hydraulic Press is also suitable for molding SMC, EMC, GMT, LFT-D, and other thermosetting and thermoplastic composite materials. Molded products are efficient, precise, reliable, energy-saving, environmentally friendly, and economical.
Related reading: Four Column Hydraulic Press: The Basic Guide