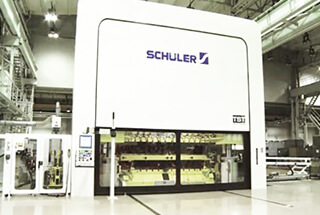
Ever wondered how metals transform into everyday objects? This article unravels the differences between forging, stamping, and casting, three fundamental manufacturing processes. You’ll discover how each method uniquely shapes materials, the specific techniques involved, and the resulting product characteristics. By the end, you’ll understand which process is best suited for different applications and why these methods are crucial in the manufacturing industry.
(1) Casting:
It involves transforming shapeless liquid metal into a solid object with a specific shape.
Forging: It involves transforming a solid object of one shape into another shape.
Casting is similar to molding wax. You purchase the wax (scrap steel, or pig iron), melt it into a liquid, pour it into a mold, and obtain objects of various shapes (solid-liquid-solid process).
Forging, on the other hand, is akin to making dough patties. You knead small dough balls, put them into a mold, and create products of different shapes. Essentially, a solid at high temperatures can be reshaped (solid-to-solid process).
Casting refers to the process of pouring molten metal into a mold to obtain castings. The casting specialty focuses on the metal melting process and the control of the casting process.
Forging is plastic molding in a solid state, with hot and cold processing. Operations like extrusion, drawing, upsetting, and punching are all part of forging.
(2) Forging is gradual shaping, while casting is one-time shaping.
Casting: Molten liquid metal fills the mold cavity and cools. Easy to generate gas holes in the middle of the workpiece.
Forging: Mainly uses the method of extrusion for shaping under high temperatures. It can refine the grains in the workpiece.
Free forging involves placing a heated metal blank between the upper and lower anvil of the forging equipment, applying impact force or pressure, directly causing plastic deformation of the blank, and obtaining the required forged part.
Free forging is flexible in operation and suitable for single-piece, small-batch, and heavy-duty forging production due to its simple shape. It is divided into manual free forging and machine free forging.
Manual free forging has low production efficiency and high labor intensity, and is only used for repair or simple, small, small-batch forging production.
In modern industrial production, machine free forging has become the main method of forging production, and it plays a particularly important role in heavy machinery manufacturing.
Die forging, also known as model forging, shapes the heated blank placed in the forging die fixed on the die forging equipment.
Die forging can be performed on various equipment. In industrial production, die forging on hammers mostly uses steam-air hammers, with a tonnage ranging from 5KN to 300KN (0.5~30t). Die forging on press machines often uses hot die forging presses, with a tonnage from 25000KN to 63000KN.
The die forging die structure includes single-cavity die forging die and multi-cavity die forging die. The single-cavity die forging die is shown in Figure 3-13. It uses a dovetail groove and a wedge to keep the forging die fixed and prevent it from moving left and right.
The key and keyway are used to accurately position the forging die and prevent it from moving forward and backward. The single-cavity is generally the final forging die.
During forging, the air hammer is often used to make the blank, and then it is formed in one shot by the multiple strikes of the final forging die. The forged part is finally removed and the flash is cut off.
(1) Casting involves melting raw materials and letting them naturally take shape in a mold.
Forging entails heating raw materials to a specific temperature, then forming them into shape with the help of tools.
Stamping involves shaping raw materials using an appropriate stamping mold.
Die casting builds upon casting; it involves injecting molten material into a mold under pressure, achieving a higher density or more precise shape.
Casting: The molten, liquid metal fills a mold cavity and cools. This process can result in gas pores within the part.
(2) Forging: Primarily, it shapes materials under high temperature through compression.
This process can refine the grains within the parts.
Parts with relatively equal thickness are suitable for forming with sheet metal, using stamping.
Parts with varying thickness, complex shapes, and those that do not require heating are suitable for die casting.
1. Casting can be divided into two types: high-pressure casting and low-pressure casting. Simply put, after melting the metal, the difference lies in the pressure applied when injecting the metal into the mold, and the temperature of the heated metal and casting machine used are also different.
2. Forging is a type of casting method, but it operates at a lower temperature, with some methods allowing for the metal to be shaped into a finished product in a semi-molten state.
3. Stamping is a process where semi-finished products are shaped into finished products at room temperature using machines like a punch press.
4. Die casting is a type of high-temperature casting method. When dealing with structurally complex, difficult-to-cast parts, a die casting machine can be used to melt the metal into a liquid state, inject it into a mold, and then cool it. After cooling, the mold is opened to remove the product.