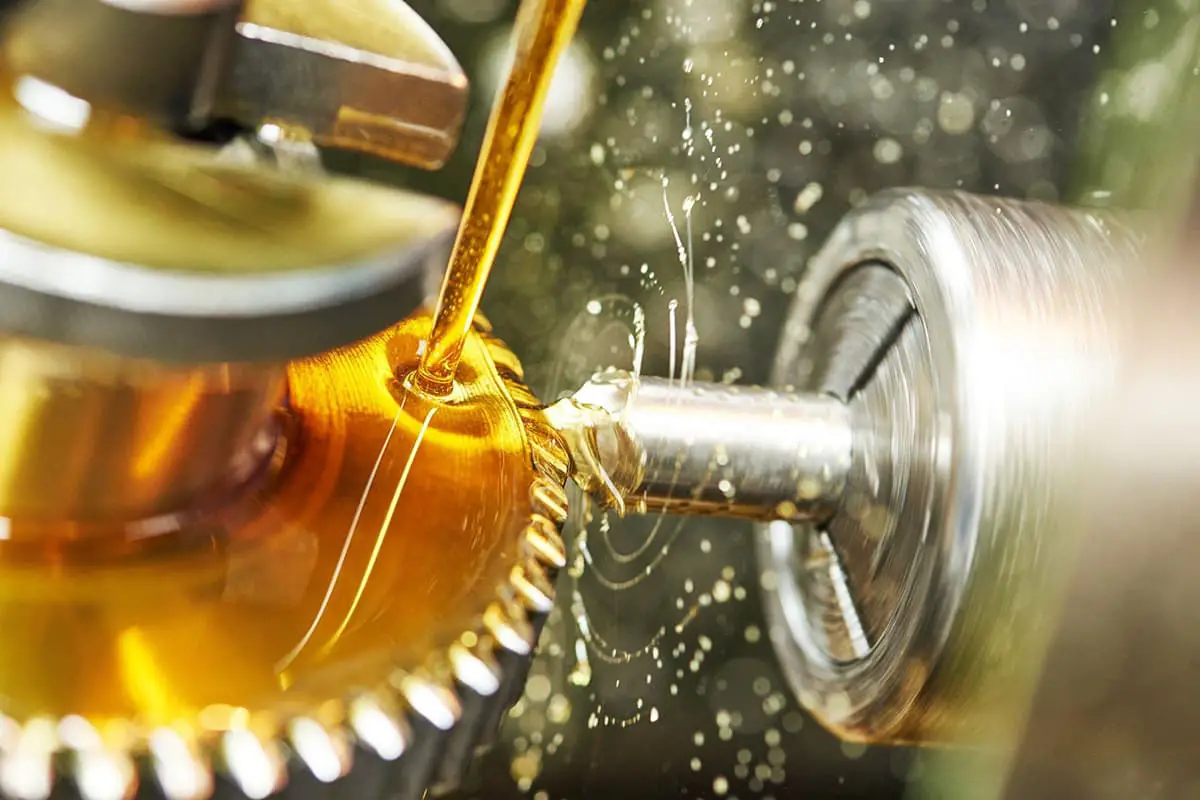
Pourquoi les alliages de molybdène sont-ils essentiels pour l'industrie moderne ? Cet article explore la classification du molybdène et de ses alliages, en détaillant leurs propriétés uniques et leurs applications dans les environnements à haute température. Du molybdène pur aux alliages complexes à plusieurs composants, les lecteurs comprendront comment ces matériaux sont développés et utilisés pour améliorer les performances dans divers secteurs. Le lecteur découvrira les différents types d'alliages de molybdène, leurs mécanismes de renforcement et les perspectives d'avenir dans le domaine de la science des matériaux.
Avec le développement de la science des matériaux métalliques réfractaires, comme l'acier, l'aluminium, le titane et d'autres industries métalliques, le développement du molybdène et des alliages de molybdène a progressivement formé un système structurel relativement complexe et complet.
J'ai examiné un grand nombre de documents nationaux et étrangers pertinents et, sur cette base, je propose des points de vue et des méthodes de classification des alliages de molybdène, ainsi que des prévisions concernant l'orientation du développement des alliages de molybdène, dans l'espoir d'aider les chercheurs et les producteurs engagés dans l'étude et la production d'alliages de molybdène.
Depuis sa découverte en 1778, le molybdène métal est largement utilisé dans la métallurgie, les sources de lumière électrique, l'industrie électronique, l'industrie chimique, l'industrie du verre et de la fibre de verre, l'industrie médicale, etc.
Cependant, en raison de ses défauts de performance inhérents (tels que la faible température de transition entre le plastique et le fragile, la résistance limitée, la dureté, etc.), diverses méthodes ont été tentées pour l'améliorer, favorisant ainsi son passage à l'alliage.
Dans un premier temps, les oligo-éléments tels que titane et le zirconium ont été ajoutés au molybdène pour former des alliages à oligo-éléments (tels que Mo-0,5Ti, Z-6, etc.), dans le but d'améliorer ses performances en renforçant les oligo-éléments en solution solide, en éliminant la phase fragile à la limite des grains et en utilisant ses produits de réaction (TiC, ZrC) comme phases de dispersion pour renforcer l'alliage.
Parallèlement, le molybdène a été associé au tungstène, au rhénium et à d'autres métaux dans certaines proportions pour fabriquer les alliages correspondants (tels que Mo-5Re, Mo-25W, etc.) afin d'améliorer leur résistance à la chaleur par le biais d'un alliage extensif de solutions solides, formant ainsi des séries d'alliages molybdène-tungstène et molybdène-rhénium.
Sur la base des alliages micro-alliés, l'ajout d'une certaine quantité d'éléments d'alliage peut améliorer la fragilité à température ambiante des alliages de molybdène après une utilisation à haute température.
Ces alliages ont évolué pour devenir les alliages de la série Mo-Ti-Zr-C. Les alliages TZM et TZC de cette série sont devenus les principaux alliages de molybdène actuellement utilisés et constituent une partie importante de la famille des alliages de molybdène.
Ces dernières années, on a découvert qu'en utilisant le hafnium pour remplacer le titane comme élément additif, son produit de réaction, le HfC, a un effet de renforcement plus important que le TiC, ce qui peut encore améliorer les performances des alliages de molybdène.
Sur cette base, les séries d'alliages Mo-Hf-C (MHC) et Mo-Hf-Zr-C (ZHM) ont été établies.
Parallèlement, on essaie de combiner l'effet de renforcement de la dispersion en solution solide des oligo-éléments avec l'effet de renforcement en solution solide d'une grande quantité d'alliage de molybdène et de tungstène, afin de réaliser une percée fondamentale dans les performances globales des alliages de molybdène.
C'est ainsi que sont nées les séries d'alliages Mo-W-Zr-Hf-C et Mo-W-Hf-C, qui sont encore en cours de développement.
En utilisant une méthode de dopage humide, l'ajout de potassium, de silicium, d'aluminium et d'autres oligo-éléments au molybdène forme du molybdène dopé, qui est actuellement considéré comme l'alliage de molybdène ayant les meilleures performances à haute température.
Sa température de recristallisation peut atteindre 1800 et même après la recristallisation, il conserve une certaine résistance, une certaine plasticité et de vastes perspectives de développement. Parallèlement, l'ajout de rhénium métallique aux alliages de molybdène dopés peut produire des alliages aux performances globales encore supérieures.
Actuellement, des rapports font état de l'ajout d'oxydes de terres rares au molybdène pur et à divers types d'alliages de molybdène. Cela a donné naissance à plusieurs grades d'alliages de molybdène plus matures. À ce stade, un diagramme évolutif complexe des alliages de molybdène a été formé (voir figure).
Cet article classe les alliages de molybdène de deux manières : en fonction de l'épaisseur de la couche de molybdène et en fonction de l'épaisseur de la couche de molybdène. éléments d'alliage et les types de renforcement de l'alliage. L'annexe est un tableau de classification détaillé pour le molybdène et les alliages de molybdène.
Note :
(1) Alliage binaire
Les alliages binaires sont des alliages de molybdène dans lesquels un seul élément d'alliage est ajouté au molybdène. Ce type d'alliage peut être divisé en deux catégories. Le premier est un alliage de molybdène avec du tungstène et du rhénium comme éléments d'alliage.
Dans ce type d'alliage, la quantité d'éléments d'alliage ajoutés est importante et la performance de l'alliage est principalement caractérisée par une bonne dureté et une bonne résistance à la chaleur. L'autre type d'alliage est un alliage de molybdène avec du titane, du zirconium et du hafnium comme éléments d'alliage.
La caractéristique de ce type d'alliage est que la quantité ajoutée est faible et que les performances de l'alliage sont légèrement améliorées par rapport au molybdène pur. Les principaux alliages sont le Mo0,5Ti, le Z-6 et le MHC.
(2) Alliage à plusieurs composants
Les alliages de molybdène à composants multiples sont basés sur des alliages de molybdène binaires. Afin d'améliorer encore les performances de l'alliage, un deuxième ou plusieurs composants d'alliage sont ajoutés pour former des alliages ayant d'excellentes performances. Les principaux alliages comprennent les séries suivantes :
Série Mo-Ti-Zr-C : Ce type d'alliage est basé sur le Mo0,5Ti, auquel on ajoute une certaine quantité de zirconium et d'éléments de carbone. Il s'agit actuellement de l'excellent alliage de molybdène le plus abouti et le plus largement utilisé, souvent sous forme de plaques, de bandes et de feuilles, mais moins sous forme de fil machine. Les principales qualités sont le TZC et le TZM.
Série Mo-Hf-Zr-O : Ce type d'alliage est basé sur la série MoTi-Zr-C. Pour améliorer encore les performances de l'alliage, le hafnium est utilisé pour remplacer le titane. En raison des différents ratios d'hafnium utilisés par les chercheurs, plusieurs qualités ont été créées, telles que ZHM, ZHM4, ZHM6, ZHM7 et ZHM8. Ces alliages sont également tout à fait excellents, mais il n'existe actuellement aucun rapport faisant état d'une utilisation généralisée, tant au niveau national qu'international.
Les alliages de la série Mo-W-Hf-C et de la série Mo-W-Hf-Zr-C sont développés pour combiner les effets de renforcement de grandes quantités d'alliage dans la solution de la matrice avec le renforcement de la dispersion des carbures d'oligo-éléments, produisant ainsi des alliages avec d'excellentes propriétés globales (haute résistance, dureté et bonne performance à haute température) et surmontant la fragilité à température ambiante après l'utilisation à haute température. Il existe actuellement plusieurs nuances telles que M25WH1, M25WH2, HWM25, M25WZH1, mais aucune n'est parvenue à maturité.
Les alliages de molybdène dopé sont fabriqués par dopage humide ou sec, où une certaine quantité de potassium, de silicium et d'aluminium est ajoutée au molybdène pur. Cela permet d'augmenter considérablement la température de recristallisation du molybdène et de maintenir une bonne plasticité même après la recristallisation.
Ce type d'alliage de molybdène présente la température de recristallisation la plus élevée, atteignant jusqu'à 1800. Il n'est pas seulement utilisé sous forme de barres et de fils, mais aussi dans une large gamme d'applications sous forme de tôles, de bandes et de feuilles.
Dans certaines applications militaires, l'effet dopant du potassium, du silicium et de l'aluminium est combiné à l'effet de renforcement de la solution solide du rhénium pour produire des produits répondant à des exigences particulières de haute performance.
Les alliages de molybdène à base de terres rares ont été largement testés dans des alliages à un ou plusieurs composants en raison de la température de recristallisation et des propriétés anti-fléchissement du molybdène. Les alliages les plus aboutis sont les alliages MLa et MY, qui ajoutent 1%~2% La2O3 ou Y2O3 au molybdène pur.
Ces alliages présentent de bonnes performances à haute température et de vastes perspectives d'application. Mo-0,5Ti+Y ajoute Y2O3 pour former un alliage de dispersion basé sur un alliage à un seul élément, qui devrait trouver sa place dans le domaine des tôles, des bandes et des feuilles.
L'ajout d'oxydes de terres rares aux alliages TZM, TZC, ZHM est actuellement au stade de la recherche et du développement. L'ajout d'oxydes de terres rares peut améliorer de manière significative la stabilité de la structure chimique et l'effet de renforcement.
Le diagramme du processus d'évolution et de la méthode de renforcement de l'alliage de molybdène montre que les alliages peuvent être répartis dans les catégories suivantes en fonction du type de renforcement de l'alliage :
(1) Alliages de type renforcement en solution solide
Alliages de renforcement en solution solide à l'état de traces : Ce type d'alliage se réfère principalement à l'alliage de molybdène Mo-0,5Ti Z-6 à élément unique, qui repose principalement sur l'ajout d'une petite quantité d'éléments d'alliage à la solution solide pour améliorer les performances de l'alliage.
Cet effet de renforcement est très faible et les performances de l'alliage ne peuvent être que légèrement supérieures à celles du molybdène pur. Par conséquent, une certaine quantité de carbone est souvent ajoutée à l'alliage tout en ajoutant des traces d'éléments en solution solide, ce qui permet au carbone et aux éléments de l'alliage de former des carbures pour jouer un rôle dans le renforcement de la dispersion.
Alliages de renforcement en solution solide en grande quantité : Ce type d'alliage fait référence aux alliages de la série molybdène-tungstène et molybdène-rhénium. Ils reposent principalement sur l'ajout d'un grand nombre d'éléments d'alliage pour former une solution solide d'alliage avec le molybdène afin d'améliorer la résistance à la chaleur et la dureté de l'alliage, mais l'usinabilité devient moins bonne.
(2) Alliages renforcés par dispersion
Alliages renforcés par dispersion de carbure : En dehors de l'effet de renforcement des oligo-éléments dans les alliages de molybdène multiéléments, le renforcement par carbure ne peut pas être adopté.
Des éléments actifs comme le titane, le zirconium et le hafnium, ajoutés aux alliages de molybdène, réagissent avec le carbone pour générer des carbures réfractaires (TiC, ZrC, HfC) qui existent sous la forme de fines phases dispersées, jouant un rôle dans le renforcement de la dispersion à haute température.
Les alliages TZM, TZC de la série Mo-Ti-Zr-C et ZHM de la série Mo-Hf-Zr-C appartiennent tous à cette catégorie d'alliages.
Alliages renforcés par dispersion d'oxyde de terre rare : Ces alliages améliorent la résistance de l'alliage grâce à l'effet de renforcement par dispersion de fines particules d'oxyde de terre rare. Comparé au renforcement par carbure, l'effet de renforcement par dispersion est plus important. Parmi les exemples de ces alliages, on peut citer ML10, MY et Mo-0,5Ti+Y.
(3) Alliages renforcés par dopage
Cette catégorie se réfère aux alliages avec différentes quantités de dopage de molybdène. Ils s'appuient non seulement sur l'effet de renforcement de la solution solide des éléments de dopage à l'état de traces, mais aussi sur la présence de bulles de potassium à haute température pour améliorer encore les performances de l'alliage.
(4) Alliages renforcés globaux
D'une manière générale, il existe une relation étroite entre les différents mécanismes de renforcement des alliages de molybdène. L'effet de renforcement des oligo-éléments se produit principalement à des températures comprises entre 1100 et 1300.
Lorsque la température augmente encore, il s'effondre. L'effet de renforcement de la dispersion des carbures est le plus évident à 1400-1500. Entre 1500 et 1800, les carbures se ramollissent et deviennent instables. À cette température, l'effet de renforcement des oxydes de terres rares à point de fusion élevé est significatif.
Au-delà de 2000, les oxydes de terres rares commencent à s'adoucir, tandis que l'effet de renforcement des bulles de potassium et de silicium dopées est évident. La recherche de matériaux plus performants a toujours été constante, et les alliages renforcés complets sont actuellement l'un des points chauds de la recherche et du développement des alliages de molybdène.
(1) Le processus de production des alliages de molybdène et du molybdène pur étant très similaire, avec le développement des matériaux réfractaires, les matériaux à base de molybdène pur seront progressivement remplacés par des matériaux à base d'alliages de molybdène à haute performance.
(2) Pendant une période considérable, les alliages TZM et TZC de la série Mo-Ti-Zr-C, avec leurs excellentes performances et leur technologie mature, resteront le courant dominant dans l'application des plaques, des bandes et des feuilles. Le molybdène des terres rares, qui présente une bonne résistance à l'affaissement et des performances à haute température, remplacera progressivement le molybdène pur dans les barres et les fils.
(3) Le molybdène dopé et le molybdène dopé avec ajout d'éléments de rhénium, ces deux types d'alliages de molybdène, avec leurs excellentes performances globales, vont progressivement se développer et croître dans les produits civils et militaires, avec des perspectives de développement prometteuses.
(4) Les alliages de molybdène renforcés seront la nouvelle cible recherchée.
Classification | Série alliage | Grade | Composition nominale | Température de recristallisation |
Molybdène pur | Métallurgie des poudres Molybdène | Mo1Mo2 | Molybdène pur | 1000℃-1100℃ |
Molybdène fondu | Mo1-1Mo1-2 | |||
Appartient à la catégorie des matériaux céramiques | Alliage molybdène-tungstène | MoW20 | Mo-25%W | ~1200℃ |
MoW25 | Mo-25%W | |||
MoW30 | Mo-30%W | |||
MoW5o | Mo-50%W | |||
Alliage de molybdène et de rhénium | Mo-5Re | Mo-5%Re | 1200℃-1300℃ | |
Mo-41Re | Mo-41%Re | |||
Mo-50Re | Mo-50%Re | |||
Alliage de molybdène et de zirconium | Z-6 | Mo-0,5ZrO | ~1250℃ | |
Cermatherm | 40%-90%Mo-60%-10%ZrO | Appartient à Matériaux céramiques | ||
Alliage de molybdène et de titane | Mo-0,5Ti | Mo-0,5Ti-0,01-0,04C | 1100℃-1300℃ | |
Alliage de molybdène et d'hafnium | MHC | Mo-1,2Hf-0,005C | 1550℃ | |
Dopage au molybdène | Alliage HIM | MH(HD) | Mo-0,0015K-0,002Si | -1800℃ |
KW | Mo-0.002K-0.003Si-0.001A1 | |||
Alliage de molybdène et de terres rares | Alliage de molybdène, de titane et d'yttrium | Mo-0,5Ti-Y | Mo-0,5Ti-1,6%Y | 1500℃ |
Alliage de molybdène | MLa | Mo-1%-2%La2O3 | 1400℃-1500℃ | |
Alliage de molybdène et d'yttrium | HY | Mo-0.5%-1.5%Y | 1500℃-1600℃ | |
Alliage de molybdène à éléments multiples | Mo-Ti-Zr-C | TZM | Mo-0.5Ti-0.07~0.12%Zr-0.01~0.04C | 1300 ℃~1500℃ |
TZC | Mo-1.0~1.5Ti-0.1~0.3Zr-0.02~0.04C | |||
Mo-Hf-Zr-C | ZHM | Mo-0,5Zr-1,5Hf-0,2C | 1550℃ | |
ZHM4 | Mo-1.2Hf-0.4Zr-0.15C* | |||
ZHM6 | Mo-1.5Hf-0.5Zr-0.19C* | |||
ZHM7 | Mo-1.8Hf-0.6Zr-0.23C* | |||
ZHM8 | Mo-2.1Hf-0.7Zr-0.27C* | |||
Mo-W-Hf-C | HWM25 | Mo-1.0Hf-25W-0.07C | ~1650℃ | |
M25WH1 | Mo-23.72W-1.2Hf-0.08C* | |||
M25WH2 | Mo-23.9W-1.0Hf-0.006C* | |||
Mo-W-Hf-Zr-C | Mo25WZH1 | Mo-23.3W-1.2Hf-0.4Zr-0.1C* | ||
Note : * indique que la recherche n'a pas encore été pleinement établie au niveau national. |