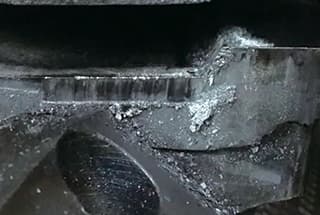
Pourquoi certaines matrices de forgeage présentent-elles des défaillances inattendues ? Cet article examine le problème courant des fissures dans les matrices d'une ligne de forgeage à grande vitesse de 3500 tonnes. En explorant les causes et en présentant des mesures d'amélioration efficaces, l'article fournit des solutions pratiques qui peuvent prolonger la durée de vie des matrices et améliorer l'efficacité de la production. Les lecteurs comprendront mieux les défis techniques et apprendront des stratégies pour prévenir des défaillances similaires dans leurs opérations.
En 2005, notre entreprise a acheté à l'Allemagne une ligne de production automatique de forgeage de classe mondiale (figure 1). Cette ligne de production est capable de forger à grande vitesse et a une capacité de 3500 tonnes.
Fig. 1 Panorama de la ligne de production automatique de forgeage à grande vitesse de 3500 tonnes
La cadence de production maximale du modèle est de 25 pièces par minute.
L'alimentation, le chauffage, le forgeage et le traitement de post-chauffe sont tous contrôlés automatiquement.
Le processus de forgeage fermé est adopté, ce qui implique cinq étapes pour réaliser la mise en forme du forgeage : le préréglage, le refoulement, le préforgeage, le forgeage final et le poinçonnage.
Comme le montre la figure 2, le système de refroidissement du moule utilise la technologie de pulvérisation automatique. Le système de refroidissement du moule utilise la technologie de pulvérisation automatique. moyen de refroidissement est un mélange d'eau et d'agent de démoulage dans une proportion spécifique.
Fig. 2 refroidissement et lubrification automatiques par pulvérisation
Au cours de la production réelle, il a été observé que certaines variétés de forgeage n'atteignent pas leur durée de vie normale, la principale forme de défaillance étant la fissuration de la matrice (voir Fig. 3).
En moyenne, environ 1 500 pièces sont affectées par des fissures, ce qui entraîne la mise au rebut d'environ 2 500 moules. Dans les cas plus graves, environ 300 pièces sont fissurées, ce qui entraîne la mise au rebut d'environ 1 200 moules.
Fig. 3 Position et forme de la fissure du moule (fissure dans le cercle rouge)
La première étape a consisté à récupérer les dossiers d'inspection physique et chimique, ainsi que les dossiers d'inspection physique et chimique du traitement thermique du acier matricé. La dureté de la matrice défectueuse a également été vérifiée et aucune anomalie évidente n'a été constatée.
Deuxièmement, une observation minutieuse de la forme, de la taille et de la profondeur de la fissure sur le moule de rupture a été effectuée. On a découvert que la hauteur de la fissure semblait avoir été progressivement formée par le découpage à l'aide de gaz à haute température et à haute pression.
La troisième étape a consisté à assembler les matrices supérieures et inférieures du forgeage final et les ébauches chaudes préforgées à l'aide de la CAO (comme le montre la figure 4).
Malgré la présence d'un espace fermé d'une hauteur d'environ 1,9 mm, avec un trou d'échappement, il a été constaté que la fissure de la matrice était apparente pendant la production réelle. Il a donc été nécessaire d'analyser soigneusement cette question à l'aide d'un logiciel de simulation de déformation.
Fig. 4 Dessin CAO des matrices supérieure et inférieure de forgeage final et de l'assemblage des ébauches chaudes préforgées
Quatrièmement, à l'aide de la simulation Deform et d'une observation attentive, il a été noté que, pendant la simulation du formage du forgeage final, à l'étape 16, les arcs des deux côtés des rayons supérieurs de la matrice du forgeage final entrent d'abord en contact avec l'ébauche préforgée chaude. Il en résulte la formation d'un espace confiné indépendant entre les deux trous d'échappement les plus proches à gauche et à droite, comme le montre la figure 5.
Fig. 5 Simulation de la déformation du moule de rupture (espace confiné indépendant dans le cercle vert)
Après avoir effectué une analyse de simulation de la déformation sur plusieurs matrices à fissures anormales, il a été découvert qu'un espace confiné indépendant se forme pendant le processus de forgeage entre l'ébauche chaude et les deux trous d'échappement les plus proches à gauche et à droite des matrices supérieure et inférieure. Ce phénomène est illustré aux figures 6, 7 et 8.
Fig. 6 simulation de déformation du moule de rupture II (espace confiné indépendant dans le cercle vert)
Fig. 7 Simulation de trois déformations d'un moule de rupture (espace confiné indépendant dans le cercle vert)
Fig. 8 Simulation de déformation de quatre moules défaillants (espace confiné indépendant dans le cercle vert)
La cinquième étape consiste à analyser en détail les informations présentées ci-dessus.
Les caractéristiques de production de la ligne automatique de forgeage à grande vitesse de 3500 tonnes imposent que, lorsque le curseur atteint le point mort supérieur, le système de pulvérisation s'étende rapidement aux moules supérieurs et inférieurs des cinq étapes et y applique une quantité importante d'agent de démoulage et de mélange d'eau pendant environ une seconde.
L'application en temps voulu d'une grande quantité de liquide de refroidissement (c'est-à-dire le mélange d'agent de démoulage et d'eau) remplit deux fonctions importantes. Premièrement, elle garantit un démoulage et une éjection rapides et stables des pièces forgées chaudes et, deuxièmement, elle permet de maintenir la température de travail de la matrice dans une plage de basses températures spécifique. Ceci est crucial pour éviter que la matrice ne soit endommagée en raison d'une usure ou d'une déformation sévère causée par une augmentation soudaine de la température dans un court laps de temps.
En résumé, l'application en temps voulu d'une quantité importante de liquide de refroidissement est une mesure cruciale pour garantir le bon fonctionnement du forgeage automatique à grande vitesse et est absolument essentielle.
Pendant le forgeage, l'ébauche chaude (dont la température est d'environ 1150300 ℃) est soumise à une vitesse élevée. Ce contact instantané peut entraîner la transformation du liquide de refroidissement en gaz à haute température et à haute pression. Toutefois, en particulier dans un espace confiné indépendant, le gaz à haute température et à haute pression ne peut pas être évacué en douceur par l'orifice d'échappement, et il finit par agir sur le moule chaud, entraînant des dommages de coupe.
Les mesures d'amélioration ont été formulées sur la base des résultats de l'analyse ci-dessus.
Dans un premier temps, la prématrice de forgeage pour la matrice I, qui avait précédemment échoué, a fait l'objet de modifications expérimentales. La surface du rayon de la matrice supérieure de forgeage final entre maintenant en premier contact avec le rayon ébauche de préforgeage chaud lorsqu'il est placé dans la cavité de forgeage final pour le forgeage. Il n'y a pas d'espace confiné indépendant entre les deux trous d'échappement les plus proches à gauche et à droite.
Pendant le forgeage, une grande quantité de gaz à haute température et à haute pression est générée, qui peut maintenant être évacuée en douceur et en temps voulu par le trou d'échappement, l'espace entre les tiges d'éjection supérieure et inférieure et le moule, et l'espace entre les moules fendus, comme le montre la figure 9.
Le programme expérimental d'amélioration du moule I défaillant s'est avéré très efficace lors de la vérification pratique. La durée de vie du moule a maintenant atteint 15 000 pièces, et il n'y a pas eu d'autres ruptures de fissures dans le moule.
Fig. 9 Simulation de la déformation du moule après amélioration (il n'y a pas d'espace confiné indépendant dans le cercle vert)
Sur la base d'expériences réussies, nous avons amélioré de manière séquentielle d'autres moules problématiques. Ainsi, lorsqu'une nouvelle ébauche de forgeage à chaud atteint l'étape problématique, il n'y a pas d'espace confiné isolé entre l'ébauche et les deux trous d'échappement les plus proches sur les côtés gauche et droit du moule. La méthode d'amélioration est décrite en détail dans les figures 10, 11 et 12.
Fig. 10 Simulation de déformation après amélioration du moule défaillant II (il n'y a pas d'espace confiné indépendant dans le cercle vert)
Fig. 11 Simulation de déformation après amélioration du moule de rupture III (il n'y a pas d'espace confiné indépendant dans le cercle vert)
Fig. 12 Simulation de déformation après amélioration du moule défaillant IV (il n'y a pas d'espace confiné indépendant dans le cercle vert)
Les moules, à savoir I, II, III et IV, ont été améliorés individuellement et les résultats ont été très efficaces. La durée de vie moyenne des moules est passée à 15 000 pièces sans aucun cas de rupture de fissure.
En plus de garantir la qualité esthétique des pièces forgées, des économies significatives peuvent être réalisées (tableau 1) grâce à la réduction des coûts des matrices. En outre, en évitant la nécessité d'une réparation ultérieure des pièces forgées, on évite également un gaspillage inutile de main-d'œuvre et de ressources matérielles.
Tableau 1 - Tableau de réduction des coûts des moules améliorés
NON. |
Demande de forgeage (10000 pièces / mois) |
Demande de moules avant amélioration (pièce/mois) |
Demande de moules après amélioration (pièce/mois) |
Die saved after improvement (piece / month) |
Coût économisé après amélioration (10000 yuans / mois) |
Épargne mensuelle (10000 yuans / mois) |
Économies annuelles (10000 yuans) |
Moule I |
3 |
12~20 |
3~4 |
10 |
4.5 |
18 |
216 |
Moule II |
|||||||
Moule III |
|||||||
Moule IV |
(1)Pour maintenir un fonctionnement stable de la ligne de production automatique de forgeage à grande vitesse de 3500 tonnes, une grande quantité de liquide de refroidissement doit être pulvérisée. Cependant, lorsque le dispositif de pulvérisation fonctionne mal, par exemple en cas de défaillance de la vanne d'air (absence d'air pour la pulvérisation des moules supérieur et inférieur) ou de défaillance de la vanne d'eau (la vanne de pulvérisation du moule supérieur ne pulvérise pas, la vanne de pulvérisation du moule inférieur pulvérise pendant longtemps, ou les moules supérieur et inférieur pulvérisent tous deux pendant longtemps), des problèmes peuvent survenir.
En outre, la défaillance de la valve de l'agent de démoulage (la valve de l'agent de démoulage du moule supérieur ne vaporise pas, la valve de l'agent de démoulage du moule inférieur vaporise pendant longtemps, ou les deux moules, supérieur et inférieur, vaporisent pendant longtemps) peut entraîner la présence d'eau ou d'un mélange d'eau et d'agent de démoulage dans le contre-battement inférieur de l'ébauche chaude. Le moule supérieur peut alors ne pas être lubrifié et refroidi à temps, ce qui entraîne une augmentation rapide de la température. Le moule est alors plus susceptible d'être coupé et endommagé par des gaz à haute température et à haute pression.
(2) Lorsque des gaz à haute température et à haute pression agissent sur une matrice chaude, ils peuvent provoquer des dommages de coupe. Cela soulève la question de savoir pourquoi la forge à chaud n'est pas coupée, mais seulement la matrice.
On a découvert par la suite que le forgeage à chaud, dont la température est d'environ 1150 ~ 1200 ℃, présente une plasticité extrêmement élevée, alors que la matrice, dont la température de travail est d'environ 200 ~ 300 ℃, n'a pas la même plasticité.
Les pièces forgées à chaud et les matrices à chaud sont toutes deux soumises à des températures élevées et à des gaz à haute pression, mais la trace de coupe sur les pièces forgées à chaud se répare d'elle-même en raison de leur grande plasticité. En revanche, la matrice doit rester à une température relativement basse pour conserver sa dureté, et ne peut présenter aucune plasticité en raison d'une forte augmentation de la température. Par conséquent, même une petite fissure causée par la haute température et la haute pression coupe au gaz La fissure ne peut pas se réparer d'elle-même et, à mesure que le travail de forgeage et de formage se poursuit, la fissure s'étend lentement et finit par entraîner la mise au rebut du moule.
(3) La pratique a prouvé que cette amélioration est réussie et que l'effet est très perceptible, ce qui peut être considéré comme un remède au problème.
Après une longue période d'observation et de vérification, la ligne de production automatique de forgeage à grande vitesse de 3500 tonnes ne connaît plus de défaillance de la fissure de la matrice.
Les concepteurs de la salle des procédés de forgeage du groupe de formage à chaud du centre de physique et de chimie des matériaux de la société du groupe ont également reconnu cette amélioration, et des dessins mis à jour ont été publiés.
La résolution du problème de la rupture de la fissure de la matrice dans la ligne de production automatique de forgeage à grande vitesse de 3500 tonnes fournit des indications précieuses pour la mise en œuvre de la politique de l'Union européenne en matière de forgeage. conception de la filière de la même ligne de production.
Cette amélioration a permis d'améliorer la qualité esthétique des pièces forgées et de réduire considérablement le coût des matrices.