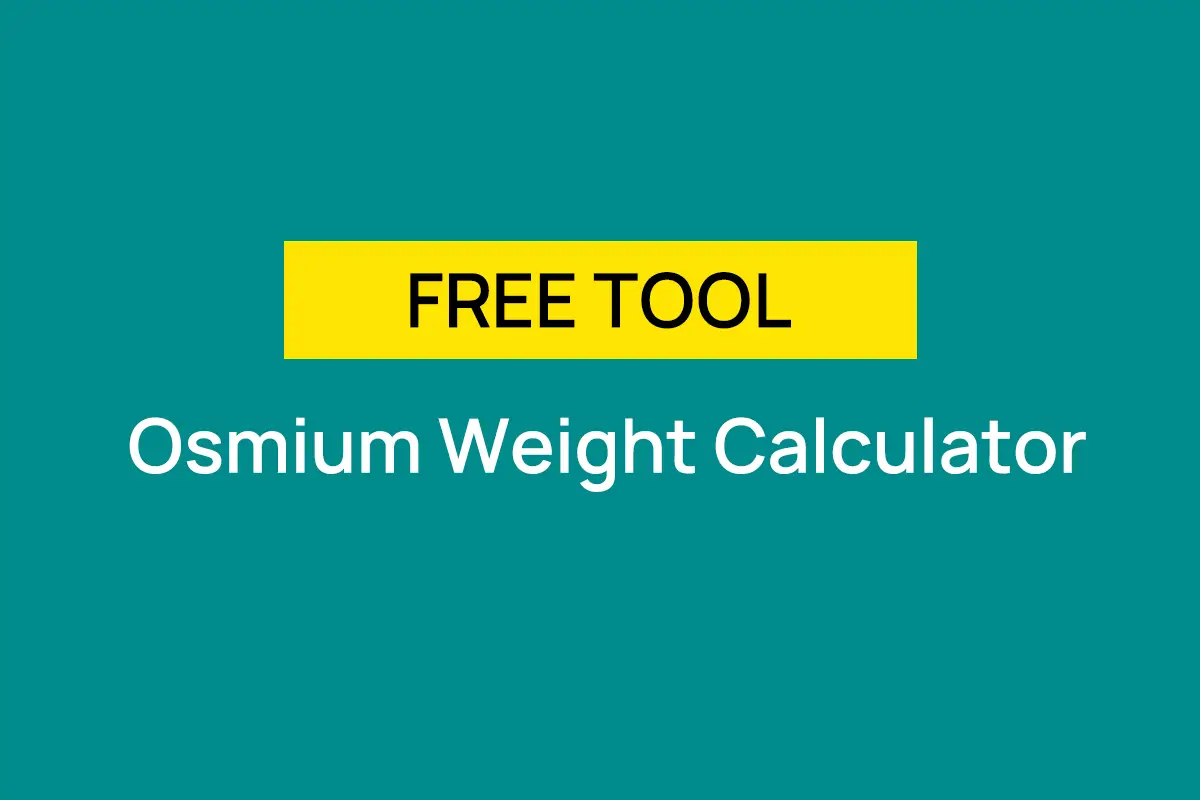
I. Aperçu théorique Le placage chimique, également connu sous le nom de "placage autocatalytique", est un processus qui ne dépend pas d'un courant électrique externe. Au lieu de cela, il utilise les agents réducteurs contenus dans la solution de placage pour effectuer une réaction d'oxydation-réduction. Ce processus, à son tour, entraîne le dépôt continu d'ions métalliques sur la surface du métal, facilité par [...]
Le placage chimique, également connu sous le nom de "placage autocatalytique", est un processus qui ne dépend pas d'un courant électrique externe.
En revanche, il utilise les agents réducteurs de la solution de placage pour effectuer une réaction d'oxydation-réduction.
Ce processus entraîne à son tour un dépôt continu d'ions métalliques sur la surface du métal, facilité par l'effet catalytique de la surface.
Étant donné que le placage chimique ne se produit que sur des matériaux ayant des propriétés autocatalytiques, les méthodes qui produisent des revêtements métalliques à partir de réactions de déplacement ou d'autres réactions chimiques, et non de réactions de réduction autocatalytique, ne sont pas définies comme étant du placage chimique.
Le placage chimique est une technique qui, basée sur le principe des réactions d'oxydo-réduction, utilise des agents réducteurs puissants dans une solution contenant des ions métalliques pour réduire ces derniers en métal et les déposer sur diverses surfaces matérielles, formant ainsi une couche de placage dense.
Les solutions couramment utilisées pour le placage chimique sont l'argent, le nickel, le cuivre, le cobalt, le nickel phosphore et le nickel bore phosphore.
Le nickelage chimique consiste à utiliser un agent réducteur pour réduire les ions de nickel dans la solution et les déposer sur une surface catalytiquement active.
Différents agents réducteurs peuvent être utilisés dans le nickelage chimique, mais le processus industriel le plus courant utilise l'hypophosphite de sodium comme agent réducteur.
Les mécanismes de réaction largement acceptés sont la "théorie de l'hydrogène atomique" et la "théorie de l'hydrure".
Le placage chimique est un nouveau métal traitement de surface technologie. Sa simplicité, son efficacité énergétique et son respect de l'environnement attirent de plus en plus l'attention. L'application de la métallisation chimique est étendue et permet d'obtenir des couches d'or uniformes avec de bonnes caractéristiques décoratives.
Il améliore la résistance à la corrosion et la durée de vie des produits en termes de protection et augmente la résistance à l'usure, conductivité électriqueIl s'agit d'une tendance croissante dans les technologies de traitement de surface au niveau mondial.
La technologie de placage chimique facilite le dépôt de métal par des réactions d'oxydation-réduction contrôlables sous l'effet catalytique du métal.
Par rapport à la galvanoplastie, le placage chimique offre des avantages tels qu'un revêtement uniforme, des trous d'épingle minimes, l'absence de nécessité d'une alimentation en courant continu, la possibilité de déposer sur des non-conducteurs et certaines propriétés spéciales.
En outre, en raison de la réduction des rejets de déchets, de la diminution de la pollution de l'environnement et de la rentabilité, le placage chimique remplace progressivement le placage électrolytique dans de nombreux domaines, devenant ainsi un procédé respectueux de l'environnement. technique de traitement de surface.
Actuellement, il est largement utilisé dans diverses industries, notamment l'électronique, la fabrication de vannes, les machines, la pétrochimie, l'automobile et l'aérospatiale.
L'application de la technologie de nickelage chimique dans l'industrie de la microélectronique se développe rapidement.
Des rapports suggèrent que Xerox Corporation a adopté la technologie de placage chimique sélectif d'alliage nickel-phosphore dans le processus de planarisation du remplissage des interconnexions et des trous d'interconnexion dans les puces multicouches de circuits intégrés à très grande échelle. Leurs produits ont passé avec succès les tests de résistance au cisaillement, de résistance à la traction, de cyclage à haute et basse température et de diverses performances électriques.
Ces pratiques indiquent que l'application de la technologie de nickelage chimique améliore les aspects techniques et économiques de la fabrication de produits microélectroniques et accroît la fiabilité des produits.
Composition de la solution de placage et conditions du procédé | Contenu |
Sulfate de nickel (NiSO4-7H2O) /g- L-1 | 26 |
Hypophosphite de sodium (NaH2PO2-H2O) /g- L-1 | 28 |
Acétate de sodium (CH3COONa) /g- L-1 | 10 |
Acide propionique (CH3CH2COOH) /g- L-1 | 2 |
Acide lactique (C3H6O3) /g- L-1 | 33 |
Sulfa /mg.L-1 | 4 |
Valeur du pH | 4.5 |
Température /℃ | 85 |
Taux de dépôt /μm-h-1 |
La stabilité de la solution chimique de nickelage est mesurée par une méthode d'ébullition. Deux cents millilitres de la solution sont portés à ébullition sur une cuisinière électrique. Après une certaine période d'ébullition, la solution est évaluée pour la décomposition.
Si aucune décomposition ne se produit après 30 minutes d'ébullition, cela indique une bonne stabilité de la solution.
Sinon, la stabilité de la solution est mauvaise. La température initiale de la solution est de 60℃. La surface plaquée a une brillance de niveau 3 (semi-brillant). L'adhérence du placage est bonne, avec une résistance à la corrosion de 30~180s et une porosité de 16cm².
Après traitement par la méthode de précipitation chimique, l'eau filtrée est incolore. Augmenter progressivement la température de la solution de placage à partir d'un point bas.
Lorsqu'il est chauffé à une certaine température, un échantillon de fer préparé est immergé dans la solution de placage. Si une réaction se produit (les bulles débordent), cela indique que la réaction chimique de placage a commencé à cette température, qui est la température de placage initiale.
Dans ce projet, la température de chauffage est divisée en cinq niveaux : 50℃, 60℃, 70℃, 80℃ et 90℃.
Les pièces en acier et en cuivre sont poli avec du papier de verre pour éliminer les oxydes de surface et autres impuretés.
Préparation de l'échantillon - Polissage mécanique - Dégraissage aux solvants organiques - Dégraissage chimique - Lavage à l'eau chaude - Lavage à l'eau froide - Activation - Lavage à l'eau froide - Lavage à l'eau déionisée - Nickelage chimique - Lavage à l'eau - Séchage à l'air
Performance du placage :
L'inspection visuelle de la couche de galvanoplastie sur les pièces métalliques est la méthode la plus élémentaire et la plus couramment utilisée. Les pièces plaquées qui échouent à l'inspection visuelle n'ont pas besoin de subir d'autres tests. Les inspections sont effectuées visuellement et, sur la base de l'apparence, les pièces plaquées peuvent être classées comme acceptables, défectueuses ou déchets.
Les défauts de surface comprennent les trous d'épingle, les marbrures, les boutons, les cloques, la desquamation, les ombres, les taches, les brûlures, les zones sombres, les dépôts dendritiques et spongieux, et les zones qui devraient être revêtues mais qui ne le sont pas.
Contrôle des défauts de surface du placage
Types et caractéristiques des défauts : La surface de placage ne doit pas présenter de défauts tels que des trous d'épingle, des marbrures, un écaillage, des bavures, des cloques, des taches, des boutons, des ombres, des zones brumeuses, des revêtements brûlants, dendritiques et spongieux. Lors des essais, il convient de les différencier strictement. Voici une brève présentation de leurs caractéristiques pour l'évaluation visuelle.
Test de porosité du placage
Essai de résistance à la corrosion du placage
Recueillir le liquide usagé → Chauffer → Ajouter de l'hydroxyde de sodium 15% jusqu'à ce que le pH du liquide usagé soit compris entre 10 et 12 → Remuer et maintenir la température pendant 1 heure → Ajouter le précipitant → Filtrer → Refroidir à 50 degrés Celsius, puis utiliser de l'acide sulfurique dilué pour ajuster le pH de la solution à 8,0 → Ajouter de la poudre de Ca(ClO)2 (le rapport entre Ca(ClO)2 et le P total est de 3,5:1,0) → Remuer pendant 2 heures → Ajouter la quantité appropriée de précipitant → Précipiter et filtrer.
La précipitation chimique est une méthode courante de traitement des eaux usées contenant des métaux lourds. Lorsque le pH du liquide de vieillissement est ajusté à plus de 8 à l'aide de soude caustique, de chaux ou de carbonate de soude, Ni(OH)2 peut se former. Après décantation, le résidu peut être séparé, ce qui permet d'éliminer le nickel du liquide de vieillissement.
En outre, le sulfure de fer, le xanthate d'amidon jaune insoluble (ISX) et d'autres peuvent également être utilisés comme précipitants pour le traitement des eaux usées de nickel. Les recherches susmentionnées portent généralement sur le traitement des eaux usées de nickel dont la concentration en nickel est inférieure à 500/mg L-1.
Le phosphore dans le liquide de vieillissement du nickelage chimique peut être traité par la méthode de précipitation par oxydation chimique, c'est-à-dire que des oxydants tels que le permanganate de potassium et le peroxyde d'hydrogène sont utilisés pour détruire le complexe de chrome dans la solution de placage et pour oxyder l'hypophosphite et d'autres éléments en phosphate.
Ensuite, le sel de phosphate est précipité à l'aide d'un précipitant afin de réduire le rejet total de phosphore dans les eaux usées. Le traitement des eaux usées contenant du nickel et du phosphore par précipitation chimique produit une grande quantité de résidus.
S'ils ne sont pas traités correctement, ils entraîneront une pollution secondaire. À l'heure actuelle, il n'existe pas de meilleure méthode de traitement des résidus que l'enfouissement.
1. Brillance du revêtement
Par rapport au nickel électrodéposé jaune clair, la plupart des revêtements de nickel chimique sont blancs argentés, avec une excellente résistance à la décoloration, et la luminosité peut être maintenue plus longtemps.
Pour le dépôt chimique nickel-phosphore, la brillance du revêtement augmente avec la teneur en phosphore.
Après l'ajout d'une certaine quantité d'azurants à la solution de dépôt chimique, la réflectivité du revêtement peut atteindre plus de 80%. Des études récentes montrent que la brillance de l'alliage nickel-cuivre-phosphore chimique est bonne et qu'il résiste mieux à la décoloration.
2. Dureté du revêtement
La dureté du chrome dur électrodéposé est de 960 HV. Sa dureté diminue fortement lorsqu'il est chauffé. La dureté d'une couche de nickel plaquée chimiquement, après traitement thermique à 400°C pendant 1 heure, peut atteindre 1100HV.
En outre, la dureté du revêtement varie peu entre la température ambiante et 400°C.
Par conséquent, le nickel plaqué chimiquement est un revêtement résistant à la chaleur, adapté à une utilisation dans des conditions où le frottement génère de la chaleur, tandis que le chrome dur plaqué par électrolyse ne peut être utilisé qu'à température ambiante.
3. Résistance à l'usure
Pour les revêtements à teneur moyenne en phosphore élevée, après l'application d'une dose appropriée de traitement thermiqueLes revêtements en alliage nickel-phosphore ont de bonnes propriétés autolubrifiantes. Les revêtements à faible teneur en phosphore ont une dureté plus élevée.
Cependant, les tests de résistance à l'usure montrent que la résistance à l'usure des revêtements à haute teneur en phosphore est supérieure à celle des revêtements en alliage à faible teneur en phosphore.
Afin d'améliorer la résistance à l'usure des revêtements de nickel-phosphore, il est nécessaire d'utiliser des revêtements de nickel-phosphore très durs. tungstène (W) est ajouté au revêtement de nickel-phosphore pour former un revêtement d'alliage ternaire, ce qui améliore considérablement sa résistance à l'usure.
4. Résistance à la corrosion
Le nickel plaqué chimiquement présente une structure amorphe uniforme. Il ne présente pas de défauts tels que des joints de grains, des dislocations et des défauts d'empilement. Chaque substrat est densément lié, ce qui rend difficile le passage de fluides corrosifs à travers l'interface de liaison pour corroder le métal du substrat, d'où une meilleure résistance à la corrosion que le chromage.
En outre, le nickel plaqué chimiquement n'est pratiquement pas affecté par la corrosion due à l'eau de mer, à l'eau salée et à l'eau douce. Sa résistance à la corrosion dans l'HCL et l'acide sulfurique est meilleure que celle de l'acier inoxydable, et il peut résister à la corrosion dans divers milieux, tels que la soude caustique à haute concentration, le sulfure d'hydrogène, l'acide lactique, et bien d'autres encore.
5. Soudabilité
La principale application du nickel plaqué chimiquement dans l'industrie électronique concerne les dispositifs discrets. Pour cela, le revêtement doit non seulement présenter une bonne résistance à l'usure, à la corrosion et aux contacts électriques, mais aussi une bonne soudabilité.
Par exemple, le soudabilité de l'aluminium La soudabilité des dissipateurs thermiques dans les générateurs est médiocre. Cependant, en plaquant une couche de 7 à 8 μm de nickel chimique sur la surface du substrat d'aluminium, sa soudabilité peut être améliorée, ce qui résout le problème de connexion entre le dissipateur thermique en aluminium et le transistor.
En outre, le nickel plaqué chimiquement peut être utilisé sur des dispositifs à micro-ondes à haute énergie, des connecteurs et des composants de communication sous-marine. En général, la soudabilité du nickel plaqué chimiquement est mesurée par la méthode de la zone élargie. Un fil de soudure de φ1,5 mm est placé sur la surface du revêtement.
Après avoir été chauffée à 400°C dans un mélange gazeux hydrogène-azote pendant 30 minutes, la zone de diffusion est mesurée afin de déterminer la relation entre la soudabilité et la teneur en phosphore du revêtement. Plus la zone de diffusion est grande, meilleure est la soudabilité du revêtement.
Un bain-marie à température constante à deux trous, quatre béchers de 100 mL, trois béchers de 200 mL, un bécher de 500 mL, une éprouvette graduée de 10 mL et une de 50 mL, une balance électronique de 0,001g (ou 0,0001g), une balance de 0.2 grammes, un micromètre, un pH-mètre, un four électrique de 1000 watts, deux thermomètres, une pissette, un jeu de pinces, du papier filtre, des anneaux en fer pour le support et le support de l'autoclave, un entonnoir en verre, une tige en verre, une cuillère à pharmacie, une burette semi-automatique, une pipette, une poire à oreille, une brosse à tubes à essai, des gants résistant aux acides, une ampoule à eau, un tube à essai, un tube à essai, un tube à essai, un tube à essai, un tube à essai. lame de scieune demi-feuille de papier de verre (No. 100~800), quatre piles sèches No.1.
Produits chimiques : Purpurate d'ammonium, chlorure de sodium, hydroxyde de sodium, EDTA, carbonate de sodium, phosphate de sodium, OP-10, acide chlorhydrique, acide sulfurique, acide nitrique, sulfate de nickel, phosphate monosodique, acide propionique, acétate de sodium, acide lactique, dodécylbenzènesulfonate de sodium, thiourée, ferricyanure de potassium, hydroxyde de calcium, peroxyde d'hydrogène, tungstate de sodium, coagulants tels que le chlorure de polyaluminium, plusieurs échantillons d'acier et de cuivre.
Les principes de base et le processus de nickelage chimique ont été résumés. La stabilité de la solution de nickel chimique et la température initiale de dépôt ont été testées.
Des essais de nickelage chimique ont été réalisés sur les surfaces d'échantillons d'acier et de cuivre ; l'aspect, la porosité, la résistance à la corrosion, l'épaisseur, l'adhérence, la fragilité, la dureté et d'autres propriétés de la couche de nickelage chimique ont été testés.
La solution de déchets de nickelage chimique a été traitée à l'aide de la méthode de précipitation chimique. Le processus et les résultats de l'expérience indiquent que la solution de nickelage chimique utilisée dans cette expérience a une excellente stabilité et ne se décompose pas, même en état d'ébullition pendant 30 minutes.