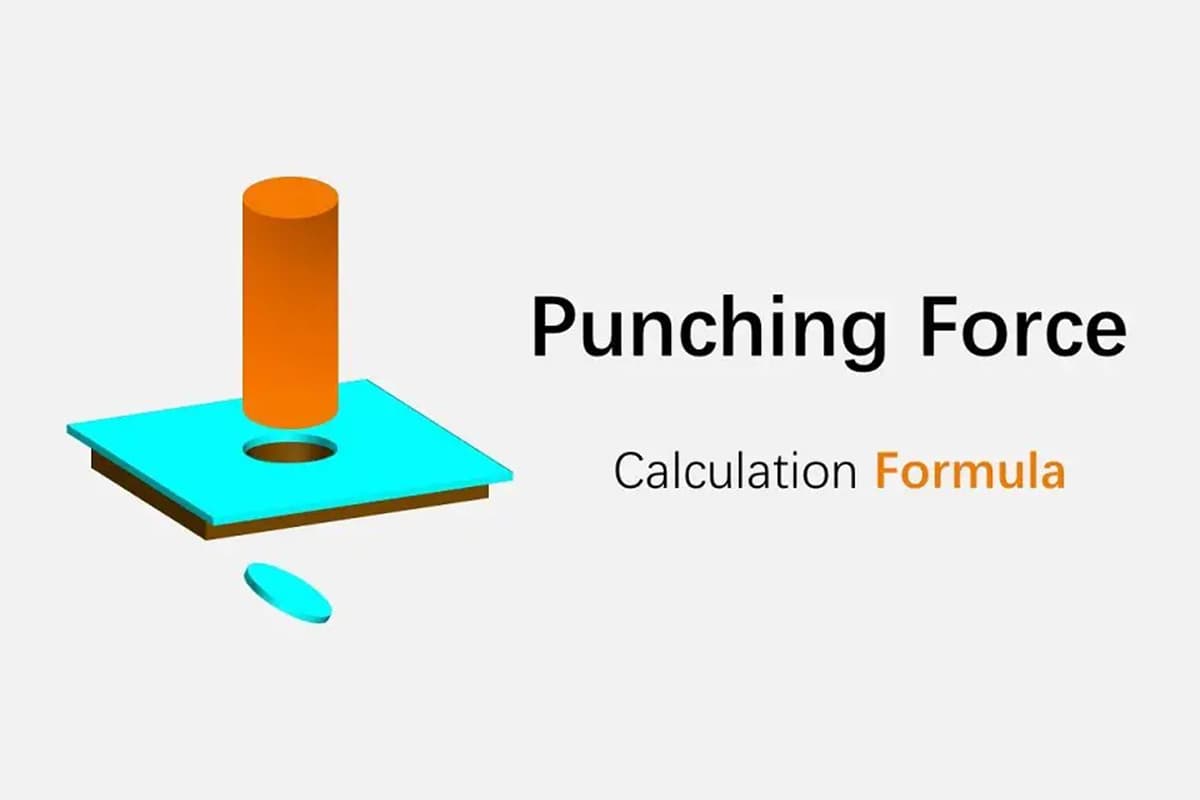
Le niveau de fabrication des moules est un indicateur important pour mesurer le niveau de fabrication des produits d'un pays, et le moule lui-même est d'un coût élevé, connu sous le nom d'"or noir". Avec le développement de l'industrie automobile, en particulier le développement rapide des véhicules à énergie nouvelle en Chine, la demande de moules n'a cessé d'augmenter, et les [...]
Le niveau de fabrication des moules est un indicateur important pour mesurer le niveau de fabrication des produits d'un pays, et le moule lui-même est d'un coût élevé, connu sous le nom d'"or noir".
Avec le développement de l'industrie automobile, en particulier le développement rapide des véhicules à énergie nouvelle en Chine, la demande de moules n'a cessé d'augmenter, et les exigences en matière de qualité et de durée de vie des moules sont de plus en plus élevées.
Il est donc nécessaire de choisir raisonnablement le matériau du moule, de mettre au point le processus de traitement thermique adéquat, de sélectionner la méthode de traitement de surface appropriée et de rechercher et développer de nouveaux matériaux pour les moules.
Dans cet article, nous prenons l'exemple de la production d'un moule de coulée sous pression de notre entreprise pour analyser et discuter des méthodes de traitement permettant d'allonger la durée de vie des moules.
Les exigences techniques pour la fabrication des moules de coulée sous pression sont les suivantes :
Processus de production : Electroslag Lingot → Découpe → Chauffage → Forgeage → Traitement thermique → Usinage → Inspection → Expédition.
⑴ Dureté de surface requise : ≤229HBW, différence de dureté unique : ≤40HBW.
⑵ Rapport de forgeage : ≥5.
⑶ Exigences en matière d'essais de performance : Énergie d'impact de l'entaille : pas moins de 25J, énergie d'impact de l'absence d'entaille : pas moins de 350J.
⑷ Essai non destructif UT défaut individuel équivalent : ≤1,0 mm. Les défauts denses ne sont pas autorisés.
⑸ Taille des grains : plus fine que le niveau 6.
⑹ Exigences d'inclusion : Voir le tableau 1.
Tableau 1 : Exigences d'inclusion pour les matériaux de moulage
Classe A | Classe B | Classe C | Classe D | Classe Ds (Niveau) | ||||
Grossière | Bien | Grossière | Bien | Grossière | Bien | Grossière | Bien | |
≤0.5 | ≤0.5 | ≤1.0 | ≤1.0 | ≤0.5 | ≤0.5 | ≤1.0 | ≤1.0 | ≤1.0 |
⑺ Les matières premières sont fabriquées à l'aide d'un four à arc électrique + raffinage + dégazage sous vide + électroslag refonte. La composition chimique est indiquée dans le tableau 2, avec [H] ≤2.0PPm, [O] ≤25PPm, et [N] = 70~170PPm.
Tableau 2 : Composition chimique des matériaux de moulage (fraction de masse, %)
Élément | C | Si | Mn | P | S | Cr | Mo | V |
Min | 0.36 | 0.25 | 0.25 | – | – | 4.95 | 2.2 | 0.50 |
Max | 0.42 | 0.45 | 0.45 | 0.015 | 0.005 | 5.25 | 2.8 | 0.80 |
⑴ Utiliser un lingot électroslag de 12,5t pour enlever la carotte et le flash de la plaque de lingot, puis le charger dans le four de chauffage au gaz. La température de chauffage est contrôlée à 1260℃. Après 24 heures d'isolation, le forgeage est lancé en utilisant le processus de deux refoulements et deux tirages avec un rapport de forgeage supérieur à 6, comme le montre la figure 1.
⑵ Après le forgeage, le contrôle du refroidissement à l'air est adopté et le produit est placé à temps dans la chambre de combustion. recuit four pour le traitement thermique post-forgeage à environ 400°C. La température de chauffage pour le traitement thermique est de 850°C pendant 20 heures d'isolation, puis de 730°C pendant 30 heures d'isolation. Le four de chauffage est refroidi à moins de 30°C/h, et le moule est retiré du four lorsque la température de celui-ci est inférieure à 450°C.
⑶ Après le traitement thermique, effectuer le traitement mécanique conformément aux exigences du dessin. Une fois le traitement terminé, effectuer des essais UT. Les produits qualifiés sont expédiés.
⑴ La pureté de l'intérieur du matériau.
⑵ Le raisonnable sélection des matériaux le processus de fabrication.
⑶ La rationalité de la conception des moules de coulée sous pression et les conditions de travail.
⑴ Selon le processus de production précédent, la durée de vie du matériau de moulage H68M n'était pas sensiblement améliorée par rapport à d'autres matériaux nationaux.
Notre personnel technique a suivi et analysé le processus de fusion, le contrôle du processus de forgeage et le contrôle du traitement thermique sur place pour obtenir des informations sur la pureté, la structure et la taille des grains, comme le montrent les figures 2, 3 et 4. Cela a permis d'acquérir de l'expérience pour améliorer le contrôle de la durée de vie du matériau à l'avenir.
Sur la base des nombreuses données expérimentales susmentionnées, notre équipe de recherche technique a analysé et mis en œuvre les améliorations suivantes pour la fusion, le forgeage et le traitement thermique après le forgeage.
La microstructure idéale de l'alliage de base a été obtenue grâce à une conception raisonnable de la composition. La composition chimique améliorée est indiquée dans le tableau 3.
Tableau 3 Composition chimique ajustée (fraction de masse, %) de H68M après amélioration
Élément | C | Si | Mn | P | S | Cr | Mo | V |
Min | 0.36 | 0.20 | 0.30 | – | – | 4.95 | 2.350 | 0.55 |
Max | 0.40 | 0.40 | 0.45 | 0.015 | 0.005 | 5.15 | 2.65 | 0.75 |
Des déchets d'acier et d'alliage propres ont été utilisés comme matières premières et des mesures efficaces telles que l'affinage LF, le dégazage sous vide et le laitier électrique sous atmosphère protectrice ont été employées pour réduire la teneur en éléments impurs, en gaz nocifs et en inclusions dans l'acier.
Cela a permis d'obtenir des billettes de forgeage pures. Dans le processus de fusion, le risque de défaillance du matériau a été contrôlé et la pureté du matériau peut être contrôlée jusqu'au niveau indiqué dans le tableau 4. L'image à fort grossissement des inclusions est présentée à la figure 5.
Tableau 4 Données de détection à fort grossissement ajustées après amélioration
Grade | Classe A | Classe B | Classe C | Classe D | Classe Ds (Niveau) | ||||
H68M | Grossière | Bien | Grossière | Bien | Grossière | Bien | Grossière | Bien | |
≤0.5 | ≤0.5 | ≤1.0 | ≤1.0 | ≤0.5 | ≤0.5 | ≤1.0 | ≤1.0 | ≤1.0 |
Pendant le chauffage, une diffusion à haute température de 1280℃ a été utilisée. Le processus de forgeage a utilisé le contrôle du processus d'étirage et de dimensionnement en trois étapes et le processus d'ébauche de matrice croisée avec la quantité de déformation finale contrôlée pour être supérieure à 30%.
La combinaison du forgeage par compression multidirectionnelle et du processus EFS (raffinage ultrafin) a été utilisée pour obtenir des grains raffinés et une microstructure recuite uniforme.
Cela a permis d'obtenir une bonne microstructure de traitement à chaud même après l'usinage et le conditionnement, ce qui a constitué une bonne base pour l'utilisation dans les moules. L'image de la microstructure ajustée est présentée à la figure 6, et l'image de la taille des grains est présentée à la figure 7.
Grâce à la mise en œuvre des mesures susmentionnées, notre matériau H68M produit est conforme aux normes de l'Association nord-américaine de normalisation (ANOR). Moulage sous pression Association.
Le matériau du moule de coulée sous pression doit être testé pour la valeur d'impact de l'encoche en V afin d'inspecter la ténacité du matériau.
Parallèlement, la ductilité du matériau doit être testée en vérifiant son énergie d'impact sans entailles. Le H68M est conforme aux exigences de l'essai Dievar et obtient la valeur d'impact dans des conditions d'utilisation durcies à 44-46HRC, comme le montre le tableau 5.
Tableau 5 Valeur d'impact du matériau H68M durci à 44-46HRC dans des conditions de fonctionnement
Grade | En forme de V (J) | Pas d'écart (J) | ||
valeur moyenne | valeur minimale | valeur moyenne | valeur minimale | |
1.2367 | ≥19 | ≥14.9 | ≥300 | ≥269 |
H68M | ≥25 | ≥18 | ≥350 | ≥300 |
Grâce à une conception optimisée de la composition de l'alliage du matériau et à un contrôle strict des processus de dosage, de fusion, de laitier électrique, de forgeage et de traitement thermique après forgeage pendant la production, le matériau H68M présente d'excellentes performances en termes de trempabilité élevée, de dureté rouge élevée, de ténacité élevée et de ductilité élevée.
(1) En ajustant la composition chimique du matériau H68M, celui-ci est devenu une nuance d'acier pour moules de travail à chaud avec une trempabilité élevée, une dureté rouge élevée, une ténacité élevée et une ductilité élevée.
(2) Le matériau H68M a été soumis à un laitier électrique, à une homogénéisation à haute température, à un traitement d'affinage du grain et à trois fois un processus d'emboutissage et de calibrage rigoureux pour dépasser les attentes des clients. La durée de vie des 10 000 moules requis par les commandes contractuelles des clients peut désormais être portée à plus de 20 000, ce qui réduit considérablement le coût d'utilisation des moules et crée de la valeur pour les clients.
En tant que fondateur de MachineMFG, j'ai consacré plus d'une décennie de ma carrière à l'industrie métallurgique. Ma vaste expérience m'a permis de devenir un expert dans les domaines de la fabrication de tôles, de l'usinage, de l'ingénierie mécanique et des machines-outils pour les métaux. Je suis constamment en train de réfléchir, de lire et d'écrire sur ces sujets, m'efforçant constamment de rester à la pointe de mon domaine. Laissez mes connaissances et mon expertise être un atout pour votre entreprise.