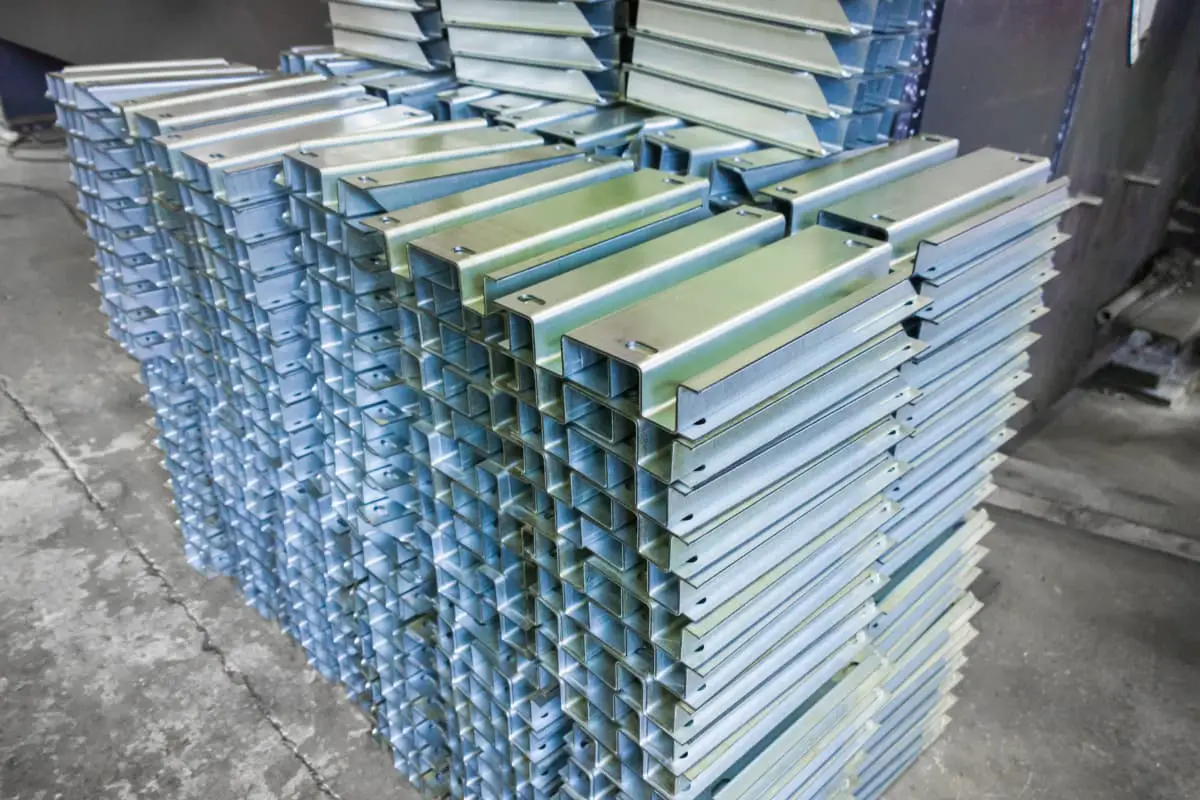
Avez-vous déjà réfléchi à la manière dont les processus complexes de fabrication des tôles façonnent nos produits de tous les jours ? Cet article se penche sur des techniques essentielles telles que le pliage, le cisaillement et le soudage, et met en lumière les méthodes et les principes qui garantissent la qualité et l'efficacité de la fabrication. La compréhension de ces processus vous permettra d'optimiser la production et de réduire les erreurs, ce qui améliorera vos compétences techniques et les résultats de vos projets. Explorez le monde fascinant de la fabrication de tôles et découvrez comment la maîtrise de ces techniques peut révolutionner votre approche de l'ingénierie.
Les techniques utilisées pour fabriquer des pièces en tôle présentent des caractéristiques uniques.
L'étude et la compréhension de ces techniques peuvent améliorer les compétences des techniciens en tôlerie, ce qui permet de concevoir des processus et des plans de fabrication plus optimisés.
Compte tenu des limites de l'équipement existant et de la structure du produit, il est important d'optimiser la structure du point de vue du processus. La responsabilité première d'un tôle Le rôle du technologue est de développer la méthode de traitement la plus efficace tout en tenant compte de l'efficacité de la production et de la flexibilité de la coordination.
Les pièces en tôle possèdent des caractéristiques uniques, telles que leur faible épaisseur et leur facilité de mise en forme.
Grâce au soudage, à l'assemblage et au rivetage, il est possible de créer des composants multi-structurés.
Toutefois, ces mêmes caractéristiques peuvent également entraîner des déformations au cours de la fabrication, telles que la flexion, la torsion et les déformations concaves ou convexes, qui peuvent avoir une incidence sur la taille ou la forme du composant et entraîner des problèmes de qualité.
Le processus de production de pièces en tôle a ses propres principes, qui permettent d'ajuster la séquence de fabrication en fonction de l'équipement et de la main-d'œuvre disponibles. En sélectionnant les processus technologiqueIl est possible de prévenir et de résoudre efficacement ce type de problèmes.
Le développement d'un itinéraire technologique doit tenir compte à la fois de la forme du produit et de l'équipement de transformation existant de l'entreprise, afin de répondre aux exigences de qualité du produit et d'obtenir un avantage économique maximal.
Les principes généraux de la création d'une technique de fabrication sont les suivants :
⑴ Répondre aux exigences de qualité du produit
⑵ La technique de fabrication est économiquement viable
⑶ Optimiser les processus ultérieurs
⑷ Traitement pratique
Le personnel technique doit tenir compte de la qualité du produit d'un point de vue fonctionnel et esthétique, ainsi que de sa connaissance des capacités de traitement de l'équipement.
Lors de la préparation d'une technique, il est important de tenir compte de l'erreur d'intégration globale de la machine, d'optimiser les méthodes de traitement des produits pour réduire les difficultés et d'établir une voie technologique relativement stable pour la production par lots.
La coordination des erreurs cumulées est un reflet complet de la tolérance cumulée du produit, et il est nécessaire d'attribuer les tolérances correspondantes au cours de l'analyse du processus pour s'assurer que l'erreur cumulée se situe dans une fourchette acceptable.
Par exemple, l'armoire de commande électrique à courant alternatif est un produit typique qui nécessite un examen minutieux de la coordination des erreurs cumulées.
L'armoire de commande électrique à courant alternatif peut être transformée en armoire de montage ou en armoire de soudage.
L'assemblage de l'armoire à encastrer est courant et se compose généralement d'un cadre supérieur, d'un cadre inférieur, d'un montant, d'une porte avant, d'une porte arrière et d'une porte latérale (panneau).
Si ces composants sont bien fabriqués, la qualité de l'armoire sera garantie.
En règle générale, les clients ont certaines exigences concernant la taille globale de l'armoire après l'assemblage, avec une exigence selon laquelle l'erreur de taille des dimensions diagonales X1 et X2, X3 et X4 doit être inférieure à 2 mm.
En fonction des conditions d'installation, les clients peuvent contrôler la largeur de L3, mais il n'y a pas d'exigence stricte en ce qui concerne la hauteur et l'épaisseur. En effet, la conception de l'armoire par le client utilise souvent la forme de la carrosserie pour déterminer la taille requise, sans tenir compte de l'épaisseur du film de revêtement, ce qui peut entraîner des erreurs de taille dans les dimensions de l'armoire après la pulvérisation et l'assemblage.
Il est donc nécessaire d'ajuster la quantité de pulvérisation et de couverture sur chaque composant afin de respecter la largeur de L3 tout en assurant les dimensions L1 et L2.
En règle générale, le cadre supérieur, le cadre inférieur et la colonne sont ajustés en fonction des besoins, avec des ajustements différents selon les assemblages.
La porte d'entrée et la porte latérale sont généralement encastrées lors de l'installation dans le linteau supérieur et inférieur de la porte, ce qui entraîne généralement une déviation négative des dimensions du contour.
La marge de revêtement doit être ajustée en conséquence en fonction du type de pulvérisation. En tenant compte du jeu d'assemblage et d'autres facteurs, la marge de pulvérisation doit être réajustée pour contrôler l'écart de taille (pour la planche de la porte, il faut laisser une marge de 0,5 à 1 mm pour la couche de revêtement après avoir pris en compte l'écart négatif).
L'optimisation de la méthode de traitement consiste à ajuster la séquence de traitement ou à améliorer le processus, ce qui peut être démontré à l'aide d'un exemple simple.
Si un panneau de porte doit être agrandi, la qualité et le temps peuvent être pris en compte dans le traitement d'une seule pièce.
Le processus de fabrication typique est le suivant :
Découpage par cisaille → Poinçonnage de la forme et du trou intérieur → Pliage par cisaille presse plieuse → Coins de soudure
Ce procédé permet de gagner du temps et de l'énergie, mais dans le cadre d'une production de masse, il augmente l'usure de la machine. outil de coupe et augmente considérablement les coûts d'entretien de la machine. En outre, une erreur de programmation mineure peut causer des dommages irréparables.
Étant donné que la zone de forme de ce type de porte est utilisée pour installer la poignée de porte, une solution couramment adoptée pour la production en série de ces panneaux de porte est la suivante :
Découpe à la cisaille (coupe séparée pour la butée à trois portes) → Poinçonnage du trou intérieur → Entaillage des coins → Pliage à la presse plieuse → Soudage des coins et de la butée à trois portes
Ce processus amélioré permet non seulement d'économiser des matières premières et des coûts de maintenance des équipements, mais aussi de réduire considérablement le taux d'erreur dans la programmation.
La stabilité du choix de l'itinéraire de traitement doit s'aligner sur le lot de production, car le choix des itinéraires de traitement peut varier en fonction des changements dans la production. La phase de développement se concentre sur la validation de la structure globale du produit et sur le traitement en temps voulu, et est moins sensible aux facteurs suivants coût de fabricationtandis que la production en petites séries se concentre sur la validation du processus, l'optimisation des structures individuelles et la préparation d'un nombre modéré de moules.
Pour la production de petits lots, le coût est la priorité absolue et le processus est optimisé autant que possible pour réduire les coûts.
Prenons l'exemple du soutien aux petits angles :
TechniqueⅠ : Découpe à la cisaille → Pliage à la presse plieuse → Poinçonnage et taraudage pour marquage
TechniqueⅡ : Découpe à la cisaille (les éléments peuvent être fusionnés) → Perçage du trou inférieur → Découpe en pièces détachées → Pliage à la presse plieuse → Taraudage
TechniqueⅢ : Réalisation d'un moule pour la fabrication
Après avoir comparé ces trois voies technologiques, on constate que les trois options répondent efficacement aux exigences des clients, mais que chacune a ses propres atouts.
TechniqueⅠ
Elle nécessite une main-d'œuvre importante et prend beaucoup de temps (en raison du poinçonnage et du taraudage des marquages), ce qui entraîne des pertes de processus considérables. Elle ne convient qu'à la fabrication d'un seul produit et n'est pas recommandée pour la production en série.
TechniqueⅡ
Utilise plus de machines-outils, est plus rapide et peut produire plusieurs pièces à la fois. Il convient à la production de lots de taille moyenne ou petite, mais le processus de découpe peut entraîner de petits déplacements dans les trous.
TechniqueⅢ
Il convient à la production de masse, car il repose sur l'utilisation d'un moule approprié, ce qui permet d'économiser du temps et des efforts.
Le choix de la technique de fabrication est étroitement lié à l'impact de la perte de traitement et de la production par lots, et doit être effectué sur la base d'un examen approfondi de divers facteurs. Le choix du plan de fabrication approprié est particulièrement important compte tenu des différentes conditions de production.
La technologie de traitement des pièces en tôle est une question complexe.
Ce billet donne un bref aperçu des principes de base de la mise en place d'une technique de fabrication de pièces de tôlerie générale, dans le but d'identifier la méthode de base pour la mise en place d'une technique de fabrication.
En conclusion, en tant qu'ingénieurs, il est important d'adopter une approche soucieuse des coûts, de prendre en compte les coûts tout au long du processus et d'envisager le processus dans une perspective globale et complète.