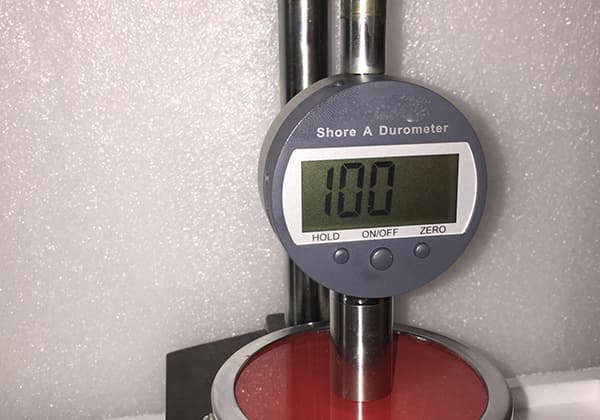
Vous êtes-vous déjà interrogé sur l'art et la science qui se cachent derrière les boîtiers métalliques élégants de vos gadgets préférés ? Dans cet article de blog, nous allons plonger dans le monde fascinant de la fabrication de la tôle. En tant qu'ingénieur mécanique expérimenté, je vais vous donner un aperçu des matériaux, des processus et des principes de conception qui transforment les feuilles de métal plates en formes complexes qui abritent nos appareils électroniques modernes. Préparez-vous à explorer les techniques de pointe et la résolution créative de problèmes qui font de la fabrication de tôles un élément essentiel du développement de produits.
La fabrication de tôles est un processus complet de fabrication à froid de tôles (généralement inférieures à 6 mm), qui comprend les éléments suivants cisaillement, mise à blanc, flexion, soudagerivetage, formage sous pression et traitement de surface, etc.
Sa particularité est que l'épaisseur d'une même pièce est la même.
Le processus de fabrication de la tôle, y compris :
Les matériaux en tôle sont les plus couramment utilisés dans la conception structurelle des produits de communication.
Comprendre les performances globales des matériaux et les sélection des matériaux ont un impact important sur le coût du produit, sa performance, sa qualité et son aptitude à la transformation.
1) Utiliser des matériaux métalliques communs pour réduire les spécifications des matériaux et contrôler autant que possible dans le cadre du manuel des matériaux de l'entreprise ;
2) Dans un même produit, réduire autant que possible la variété des matériaux et des épaisseurs de tôle ;
3) En partant du principe qu'il faut assurer la fonction des pièces, essayer d'utiliser des matériaux bon marché, de réduire la consommation de matériaux et de réduire le coût des matériaux ;
4) Pour l'armoire et certaines grandes boîtes à fiches, il est nécessaire d'envisager pleinement la réduction du poids de l'ensemble de la machine ;
5) Outre le fait de garantir la fonction des pièces, il faut également tenir compte du fait que les performances d'emboutissage du matériau doivent répondre aux exigences de transformation afin de garantir la rationalité et la qualité de la transformation des produits.
Tôle d'acier
1) Tôle d'acier laminée à froid
La tôle d'acier laminée à froid est l'abréviation de tôle laminée à froid en acier de construction au carbone.
Il est ensuite laminé à froid à partir d'un feuillard d'acier de construction au carbone laminé à chaud en une tôle d'acier d'une épaisseur inférieure à 4 mm.
Comme elle est laminée à température normale, il n'y a pas de dépôt d'oxyde de fer. Par conséquent, la qualité de la surface de la plaque à froid est bonne et la précision dimensionnelle est élevée.
En outre, le processus de recuit permet d'obtenir des propriétés mécaniques et des performances de traitement supérieures à celles de l'acier inoxydable. acier laminé à chaud feuilles.
Les nuances couramment utilisées sont l'acier à faible teneur en carbone 08F et l'acier 10#, qui présentent de bonnes caractéristiques de résistance à la corrosion. mise à blanc et les propriétés de flexion.
2) Tôle d'acier laminée à froid et galvanisée en continu
Tôle d'acier laminée à froid, zinguée par électrolyse en continu, c'est-à-dire "tôle électrolytique".
Se réfère au processus de dépôt continu de zinc à partir d'une solution aqueuse de sel de zinc sur une bande d'acier préparée à l'avance pour obtenir une couche galvanisée en surface sous l'action d'un champ électrique sur une ligne d'électrogalvanisation.
En raison des limites du procédé, le revêtement est mince.
3) Tôle d'acier galvanisée à chaud en continu
La tôle d'acier galvanisée à chaud en continu est appelée tôle galvanisée ou du fer blanc.
Les tôles et bandes d'acier galvanisées à chaud en continu et laminées à froid, d'une épaisseur de 0,25 à 2,5 mm, sont d'abord soumises à un four de préchauffage chauffé à la flamme pour brûler l'huile résiduelle en surface.
En même temps, un film d'oxyde de fer se forme à la surface.
Il est ensuite chauffé à 710~920 °C dans un four de recuit de réduction contenant des gaz mélangés H2 et N2 pour réduire le film d'oxyde de fer en fer éponge.
Après avoir été refroidie à une température légèrement supérieure à celle du zinc en fusion, la bande activée et purifiée entre dans le pot de zinc à 450-460 °C.
L'épaisseur de la couche de zinc est contrôlée par une lame d'air.
Enfin, adopter un traitement de passivation avec une solution de chromate pour améliorer la résistance à la rouille blanche.
Par rapport à la surface de la tôle électro-galvanisée, le revêtement est plus épais et est principalement utilisé pour les pièces de tôle qui nécessitent une résistance élevée à la corrosion.
4) Plaque d'aluminium-zinc
Le revêtement en alliage aluminium-zinc de la plaque aluminium-zinc est composé de 55% d'aluminium, 43,4% de zinc et 1,6% de silicium à 600°C.
Formation d'une couche protectrice dense de cristaux quaternaires avec une excellente résistance à la corrosion, une durée de vie normale allant jusqu'à 25 ans, soit 3 à 6 fois plus longue qu'une couche protectrice de cristaux quaternaires, avec une excellente résistance à la corrosion. tôle galvanisée et comparable à l'acier inoxydable.
La résistance à la corrosion de la plaque aluminium-zinc provient de la fonction de barrière de l'aluminium et de la protection sacrificielle du zinc.
Lorsque le zinc est sacrifié pour l'ébarbage, le grattage et la rayure du revêtement, l'aluminium forme une couche d'oxyde insoluble qui agit comme une barrière.
Les plaques d'acier 2), 3) et 4) ci-dessus sont collectivement appelées tôles d'acier revêtues et sont largement utilisées dans les équipements de communication.
Après l'enrobage tôle d'acier est traité, il ne peut plus être galvanisé ou peint.
L'incision peut être utilisée directement sans traitement spécial, et un traitement spécial de phosphatation peut être effectué pour améliorer la résistance à la rouille de l'incision.
D'après l'analyse des coûts, la tôle d'acier électro-galvanisée en continu est utilisée, et l'usine de transformation n'a pas besoin d'envoyer les pièces à la galvanisation, ce qui permet d'économiser du temps de galvanisation et des coûts de transport.
En outre, les pièces ne sont pas décapées avant la pulvérisation, ce qui améliore l'efficacité du traitement.
5) Acier inoxydable assiette
Il est largement utilisé en raison de sa forte résistance à la corrosion, de sa bonne conductivité électrique, de sa grande solidité, etc.
Mais nous devons également tenir compte de ses lacunes :
Plaques d'aluminium et d'alliage d'aluminium
Les tôles d'aluminium et d'alliage d'aluminium couramment utilisées sont principalement composées des trois matériaux suivants :
L'aluminium antirouille 3A21, qui est l'ancienne marque LF21, est un alliage AL-Mn. Il s'agit de l'aluminium antirouille le plus utilisé.
La résistance de cet alliage n'est pas élevée (elle est seulement supérieure à celle de l'aluminium industriel pur) et ne peut pas être traitée thermiquement et renforcée.
Par conséquent, la méthode d'écrouissage est souvent utilisée pour améliorer ses propriétés mécaniques, et il présente une plasticité élevée à l'état recuit, ainsi qu'une bonne plasticité à l'état semi-trempé.
Il présente une faible plasticité, une bonne résistance à la corrosion et une bonne résistance à l'usure. soudabilité pendant l'écrouissage à froid.
L'aluminium antirouille 5A02 est l'ancienne marque de l'aluminium antirouille AL-Mg de la série LF2.
Par rapport au 3A21, le 5A02 présente une résistance plus élevée, en particulier une résistance élevée à la corrosion. résistance à la fatigueLes produits de l'industrie de l'acier ont une grande plasticité et une grande résistance à la corrosion.
Le traitement thermique ne peut pas être renforcé, la soudabilité par contact et par atome d'hydrogène est bonne, et des fissures cristallines ont tendance à se former pendant le traitement thermique. soudage à l'arc sous argonet l'alliage a tendance à former des fissures cristallines lors de l'écrouissage.
L'alliage présente une bonne usinabilité à l'état de trempe à froid et de semi-trempe à froid, et une faible usinabilité à l'état recuit, et il peut être poli.
L'aluminium dur 2A06 est l'ancien LY6, qui est une qualité d'aluminium dur couramment utilisée.
L'aluminium dur et l'aluminium super-dur ont des caractéristiques la résistance et la dureté que les alliages d'aluminium ordinaires, et peuvent être utilisés comme matériaux pour certains panneaux.
Cependant, la plasticité est faible, et le pliage ne peut pas être effectué, et le pliage peut provoquer des fissures ou des craquelures dans la partie arrondie extérieure.
Il existe de nouvelles normes pour la qualité et le statut de l'alliage d'aluminium. Le code standard de la méthode de représentation de la qualité est GB/T16474-1996, le code d'état est GB/T16475-1996, et le tableau de comparaison avec l'ancienne norme est présenté dans le tableau 1-1 ci-dessous :
Tableau 1-1 Tableau comparatif entre le nouveau et l'ancien système nuances d'alliages d'aluminium
Grade | États | ||||||||
Nouveau | Ancienne | Nouveau | Ancienne | Nouveau | Ancienne | Nouveau | Ancienne | Nouveau | Ancienne |
1070A | L1 | 5A06 | LF6 | 2A80 | LD8 | 2A14 | LD10 | H12 | R |
1060 | L2 | 5A12 | LF12 | 2A90 | LD9 | 2A50 | LD5 | O | M |
1050A | L3 | 8A06 | L6 | 4A11 | LD11 | 6A02 | LD2 | T4 | CZ |
1035 | L4 | 3A21 | LF21 | 6063 | LD31 | 7A04 | LC4 | T5 | RCS |
1200 | L5 | 2A02 | LY2 | 6061 | LD30 | 7A09 | LC9 | T6 | CS |
5A02 | LF2 | 2A06 | LY6 | 2A11 | LY11 | ||||
5A03 | LF3 | 2A16 | LY16 | 2A12 | LY12 | ||||
5A05 | LF5 | 2A70 | LD7 | 2A13 | LY13 |
Plaques de cuivre et d'alliages de cuivre
Il existe deux principaux types de feuilles de cuivre et d'alliages de cuivre couramment utilisés : le cuivre T2 et le laiton H62.
Le cuivre T2 est le cuivre pur le plus couramment utilisé. Il a un aspect violet et est également appelé cuivre. Il présente une conductivité électrique et thermique élevée, une bonne résistance à la corrosion et une bonne aptitude à la mise en forme.
Mais la résistance et la dureté sont bien inférieures à celles du laiton, et le prix est très élevé.
Il est principalement utilisé comme élément de corrosion pour les produits conducteurs, les produits de conduction thermique et les biens de consommation. Il est généralement utilisé pour les pièces de l'alimentation électrique qui doivent transporter des courants importants.
rass H62, qui est un laiton à haute teneur en zinc, présente une résistance élevée et une excellente aptitude à la déformation à froid et à chaud. travail de presse et le découpage.
Principalement utilisé pour divers types d'emboutissage et de force de flexion La conductivité de ses pièces n'est pas aussi bonne que celle du cuivre, mais sa résistance et sa dureté sont meilleures, et son prix est relativement modéré.
Pour répondre aux exigences de conductivité électrique, le laiton H62 est utilisé autant que possible à la place du cuivre, ce qui permet de réduire considérablement le coût des matériaux.
Par exemple, les barres omnibus, la plupart des barres omnibus actuelles sont en laiton H62, ce qui s'est avéré tout à fait satisfaisant.
Il y a trois principaux types de tôles transformation : poinçonnage et découpage, pliage et étirement.
Les différentes techniques de traitement ont des exigences différentes pour la feuille.
Le choix de la tôle doit également se faire en fonction de la forme générale et de la technologie de transformation du produit.
L'impact des matériaux sur le découpage
Le découpage nécessite que la feuille soit suffisamment plastique pour ne pas se fissurer lors de la perforation.
Les matériaux tendres (tels que l'aluminium pur, l'aluminium inoxydable, le laiton, le cuivre, l'acier à faible teneur en carbone, etc.) ont de bonnes performances de poinçonnage, et des pièces avec une section transversale lisse et une faible inclinaison peuvent être obtenues après le poinçonnage ;
Les matériaux durs (tels que acier à haute teneur en carbone) ont une qualité médiocre après le poinçonnage et les irrégularités de la section sont importantes, en particulier pour les tôles épaisses.
Pour les matériaux fragiles, une déchirure est susceptible de se produire après le poinçonnage, et en particulier dans le cas d'une petite largeur, une déchirure est susceptible de se produire.
L'effet des matériaux sur la flexion
Les plaques qui doivent être pliées et formées doivent avoir une plasticité suffisante et une limite d'élasticité basse.
Une feuille hautement plastique qui a moins tendance à se fissurer lorsqu'elle est pliée.
Les tôles dont la limite d'élasticité et le module d'élasticité sont inférieurs ont moins de dos d'âne La déformation après le pliage est faible et il est facile d'obtenir une forme courbe précise.
Les matériaux plastiques tels que l'acier à faible teneur en carbone, le laiton et l'aluminium avec une couche d'aluminium. teneur en carbone de <0,2% sont facilement pliés et formés ;
Les matériaux plus fragiles, tels que le bronze phosphoreux (QSn6.5 ~ 2.5), l'acier à ressort (65Mn), l'aluminium dur, l'aluminium super dur, etc. rayon de courbure (r / t) lors de la flexion, sinon des fissures risquent de se produire pendant la flexion.
Une attention particulière doit être accordée au choix de l'état dur et mou du matériau, qui a une grande influence sur les propriétés de flexion.
Pour de nombreux matériaux fragiles, la flexion peut entraîner la fissuration, voire la rupture, du rayon extérieur.
Il existe également des tôles d'acier à plus forte teneur en carbone.
Si vous choisissez un état dur, la flexion provoquera également des fissures, voire une rupture du rayon extérieur.
Ces derniers doivent être évités autant que possible.
Effet des matériaux sur le traitement des dessins
L'étirement de la feuille, en particulier l'étirement en profondeur, est une tâche difficile dans le domaine de la santé. transformation de la tôle processus.
Non seulement la profondeur de l'étirement doit être aussi faible que possible, mais la forme doit être aussi simple et lisse que possible. En outre, le matériau doit avoir une bonne plasticité.
Dans le cas contraire, la pièce entière est facilement déformée, partiellement plissée ou même tirée au niveau de la partie étirable.
La limite d'élasticité est faible et le coefficient directionnel de l'épaisseur de la plaque est important.
Plus la limite élastique σs/σb de la tôle est faible, meilleure est la performance du poinçonnage et plus grande est la limite de la déformation primaire.
Lorsque le coefficient de directivité de l'épaisseur de la plaque est >1, la déformation dans le sens de la largeur est plus facile que la déformation dans le sens de l'épaisseur.
Plus la valeur du rayon d'étirement R est grande, moins il y a de risques d'amincissement et de fracture pendant le processus d'étirement, et meilleures sont les propriétés de résistance à la traction.
Les propriétés de traction courantes sont les suivantes : tôle d'aluminium pur, 08Al, ST16, SPCD.
Impact des matériaux sur la rigidité
Lors de la conception des structures en tôle, la rigidité des pièces structurelles en tôle n'est souvent pas respectée.
Les concepteurs de structures utilisent souvent de l'acier à faible teneur en carbone ou de l'acier inoxydable à la place de l'acier à faible teneur en carbone, ou remplacent l'alliage d'aluminium ordinaire par un alliage d'aluminium dur à haute résistance et dureté, ce qui devrait augmenter la rigidité de la pièce.
En fait, il n'y a pas d'effet évident.
Pour les matériaux du même substrat, la résistance et la dureté du matériau peuvent être considérablement améliorées par le traitement thermique et l'alliage.
Mais le changement de rigidité est faible.
Pour améliorer la rigidité de la pièce, il suffit de modifier le matériau et la forme de la pièce pour obtenir un certain effet.
Voir le tableau 1-2 pour le module d'élasticité et le module de cisaillement de différents matériaux.
Tableau 1-2 Module d'élasticité et module de cisaillement de matériaux courants
Module d'élasticité E | Module de cisaillement G | |
---|---|---|
Objet | GPa | GPa |
Fonte grise | 118~126 | 44.3 |
Fonte ductile | 173 | |
Acier au carbone, Acier au nickel-chrome | 206 | 79.4 |
Acier moulé | 202 | |
Cuivre pur laminé | 108 | 39.2 |
Cuivre pur étiré à froid | 127 | 48 |
Bronze phosphoreux laminé | 113 | 41.2 |
Laiton étiré à froid | 89~97 | 34.3~36.3 |
Bronze au manganèse laminé | 108 | 39.2 |
Aluminium laminé | 68 | 25.5~26.5 |
Retirer le fil d'aluminium | 69 | |
Aluminium moulé bronze | 103 | 11.1 |
Bronze étain coulé | 103 | |
Alliage d'aluminium dur | 70 | 26.5 |
Zinc de laminage | 82 | 31.4 |
Plomb | 16 | 6.8 |
Verre | 55 | 1.96 |
Plexiglas | 2.35~29.4 | |
Caoutchouc | 0.0078 | |
Bakélite | 1.96~2.94 | 0.69~2.06 |
Plastique phénolique | 3.95~8.83 | |
Celluloïd | 1.71~1.89 | 0.69~0.98 |
Nylon 1010 | 1.07 | |
Tétrachloroéthylène dur | 3.14~3.92 | |
Polytétrachloroéthylène | 1.14~1.42 | |
Polyéthylène basse pression | 0.54~0.75 | |
Polyéthylène haute pression | 0.147~0.24 | |
Béton | 13.73~39.2 | 4.9~15.69 |
Comparaison des performances des plaques couramment utilisées
Tableau 1-3 Comparaison des performances de plusieurs plaques couramment utilisées
Coefficient de prix | Résistance à l'arrachement (mΩ) | Performances du traitement du poinçonnage CNC | Traitement au laser performance | Performance de flexion | Technologie de l'écrou riveté | Technologie des rivets à presser | Revêtement de surface | Protection de l'incision |
---|---|---|---|---|---|---|---|---|
1 | bon | bon | bon | bon | bon | Moyenne | Très bon | |
1.2 | 27 | bon | bon | bon | bon | bon | Moyenne | bon |
1.7 | 26 | bon | bon | bon | bon | bon | Moyenne | les plus pauvres |
1.3 | 26 | bon | bon | bon | bon | bon | Moyenne | relativement pauvre |
1.4 | 23 | bon | bon | bon | bon | bon | Moyenne | pauvres |
6.5 | 60 | pauvres | bon | moyenne | pauvres | très faible | pauvres | bon |
2.9 | 46 | Moyenne | extrême pauvreté | bon | bon | bon | Moyenne | bon |
3 | 46 | Moyenne | extrême pauvreté | extrême pauvreté | bon | bon | Moyenne | bon |
5.6 | bon | extrême pauvreté | bon | bon | bon | Moyenne | bon | |
5 | bon | extrême pauvreté | bon | bon | bon | Moyenne | bon |
Remarque :
Piercing et le blanking par Poinçonneuse CNC
Le poinçonnage et le découpage CNC consistent à utiliser le micro-ordinateur à puce unique de la poinçonneuse CNC pour saisir à l'avance le programme d'usinage (taille, trajectoire d'usinage, outil de traitement, etc.) de la pièce de tôle, ce qui permet à la poinçonneuse CNC d'adopter divers outils et une multitude de commandes NC pour réaliser une variété de formes de traitement telles que le poinçonnage, l'ébarbage, le formage, etc.
Le poinçonnage CNC ne peut généralement pas réaliser le perçage et le découpage de formes trop compliquées.
Caractéristiques :
Il est fondamentalement capable de répondre aux besoins de la production d'échantillons.
Problèmes d'attention et exigences :
Le poinçonnage CNC est généralement adapté au poinçonnage de l'acier à faible teneur en carbone, des tôles électrolytiques, des tôles aluminium-zinc, des tôles aluminium, des tôles cuivre avec T=3,5~4mm ou moins, et des tôles en acier inoxydable avec T=3mm ou moins.
L'épaisseur de tôle recommandée pour le poinçonnage CNC est la suivante :
Le processus de poinçonnage CNC entraîne une déformation importante de la plaque de cuivre, tandis que le PC de traitement et la plaque de PVC présentent des bavures importantes sur les bords de traitement et une faible précision.
Lors du poinçonnage, le diamètre et la largeur de l'outil utilisé doivent être supérieurs à l'épaisseur du matériau. Par exemple, un outil d'un diamètre de Φ1,5 ne peut pas perforer un matériau de 1,6 mm.
Les matériaux inférieurs à 0,6 mm ne sont généralement pas traités par NCT.
Matériaux en acier inoxydable ne sont généralement pas traités par NCT. (Bien sûr, les matériaux de 0,6 à 1,5 mm peuvent être traités par NCT, mais l'usure de l'outil est importante et la probabilité de rebut lors du traitement sur le terrain est beaucoup plus élevée que pour les autres matériaux GI).
Le perçage et le découpage d'autres formes sont de préférence aussi simples et uniformes que possible.
La taille du poinçon CNC doit être normalisée (trous ronds, trous hexagonaux, etc.) et la largeur minimale de la rainure de traitement est de 1,2 mm.
Piercing et le blanking par cold punch die
Pour le poinçonnage et le découpage de pièces à grand rendement et de petite taille, des matrices d'emboutissage de tôle spécialement conçues sont fabriquées et utilisées pour accroître l'efficacité de la production.
Il se compose généralement d'un poinçon et d'une matrice.
Les matrices sont généralement de deux types : les matrices à enfoncer et les matrices à incruster.
Les poinçons comprennent généralement : le type rond, qui peut être remplacé ; le type combiné ; le type à chargement et déchargement rapides.
Les matrices les plus courantes sont les suivantes
Caractéristiques :
Parce que la poinçonnage et découpage Avec la matrice froide, il est possible de réaliser un seul emboutissage, l'efficacité est élevée, l'uniformité est bonne et le coût est faible.
Par conséquent, pour les pièces structurelles dont la capacité de traitement annuelle est supérieure à 5 000 pièces et dont la taille n'est pas trop importante, l'usine de transformation procède généralement à un traitement à froid.
Lors de la conception de la structure, il est nécessaire de prendre en compte la conception de la caractéristiques du processus de la transformation en filière à froid.
Par exemple, les pièces ne doivent pas avoir d'angles vifs (sauf pour l'utilisation). Elles doivent être conçues pour être arrondies afin d'améliorer la qualité et la durée de vie du moule et de rendre la pièce belle, sûre et durable.
Afin de répondre aux exigences fonctionnelles, la forme structurelle de la pièce peut être conçue de manière plus complexe.
Perçage à l'aide d'un poinçon à trous denses
Le poinçon à trous denses peut être considéré comme une sorte de poinçon à commande numérique. Pour les pièces comportant un grand nombre de trous denses, l'efficacité et la précision du poinçonnage peuvent être améliorées.
Une matrice de poinçonnage spécialement conçue à cet effet peut perforer un grand nombre de trous denses pour traiter la pièce à usiner.
Par exemple : pochoir de ventilation, déflecteur d'entrée et de sortie d'air.
Voir la figure 1-1.
La partie ombrée de la figure est un moule à trous denses, et le trou dense de la pièce peut être rapidement poinçonné par le moule à trous denses. Par rapport à un seul poinçon, l'efficacité s'en trouve grandement améliorée.
Problèmes et exigences liés à la conception d'agencements de trous denses
La conception du trou dense sur le produit doit tenir compte du fait que les caractéristiques de traitement de la matrice de poinçonnage du trou dense sont répétées plusieurs fois, de sorte que le principe suivant doit être adopté lors de la conception de l'agencement du trou dense :
Le moule à trous denses de la figure 1-1 a peut être conçu comme indiqué dans la figure 1-4.
Le moule à trous denses de la figure 1-1 b ne peut être conçu que comme indiqué dans la figure 1-5.
Lors de la conception de la disposition des trous denses, il convient d'essayer de respecter les exigences susmentionnées et de veiller à ce qu'ils soient continus et présentent une certaine régularité, ce qui facilite l'ouverture du moule à trous et réduit le coût de l'emboutissage.
Dans le cas contraire, seuls quelques poinçons ou plusieurs jeux de moules peuvent être utilisés pour achever le traitement.
Comme le montre la figure 1-6,
Découpe au laser
La découpe laser est une technologie de découpe sans contact qui utilise une décharge d'électrons comme source d'énergie pour focaliser un laser comme source de chaleur en utilisant un groupe de miroirs réfléchissants. Cette énergie lumineuse à haute densité est utilisée pour réaliser le poinçonnage et le découpage de pièces en tôle.
Caractéristiques :
Cependant, le coût est élevé, la table de support de la pièce est endommagée en même temps, et la surface coupée peut facilement déposer un film d'oxyde, ce qui est difficile à manipuler.
Généralement, il ne convient qu'au traitement d'un seul lot ou d'un petit lot.
Attention : généralement utilisé uniquement pour les tôles d'acier.
Les plaques d'aluminium et de cuivre ne sont généralement pas utilisées car le transfert de chaleur du matériau est trop rapide, ce qui provoque une fusion autour de l'incision et ne garantit pas la précision et la qualité du traitement.
Les découpe au laser La face frontale de l'acier présente une couche d'oxyde qui ne peut pas être éliminée par lavage ; la face frontale de l'acier de coupe doit être polie pour répondre à des exigences particulières ;
Les trous denses découpés au laser sont plus déformés ; en général, on n'utilise pas le laser pour découper des trous denses.
Electro-érosion à fil
Le découpage par fil est une méthode de traitement dans laquelle une pièce et un fil (fil de molybdène, fil de cuivre) sont chacun utilisés comme pôle et maintenus à une certaine distance, et un éclateur est formé lorsqu'une tension est suffisamment élevée, et la pièce est soumise à une gravure électrolytique. La matière enlevée est entraînée par le fluide de travail.
Caractéristiques : grande précision de traitement, mais faible vitesse de traitement, coût élevé, et modification des propriétés de surface du matériau.
Généralement utilisé pour le traitement des moules, il n'est pas utilisé pour le traitement des pièces de production.
Certains trous carrés des panneaux profilés n'ont pas de coins arrondis qui ne peuvent pas être fraisés, et comme les alliages d'aluminium ne peuvent pas être découpés au laser, s'il n'y a pas d'espace de poinçonnage, ils ne peuvent être poinçonnés que par électroérosion à fil.
La vitesse est très lente, l'efficacité est très faible et elle n'est pas adaptée à la production de masse. La conception doit éviter cette situation.
Comparaison des trois méthodes de blanking et de piercMéthodes d'apprentissage
Tableau 1-4 Comparaison de trois caractéristiques communes de traitement du poinçonnage et du découpage
Note : Les données suivantes sont des données pour tôles d'acier laminées à froid.
Laser | Découpage | Guignol | |
---|---|---|---|
Matériau usinable | tôle d'acier | Plaque d'acier, plaque de cuivre, plaque d'aluminium | Plaque d'acier, plaque de cuivre, plaque d'aluminium |
Épaisseur du matériau usinable | 1mm ~ 8mm | 0,6 mm ~ 3 mm | généralement <4mm |
Dimensions minimales de transformation (tôles d'acier normales laminées à froid) | Fente minimale 0,2 mm | Trou de perforation Ø≧t | Trou de perforation Ø≧t |
Cercle minimal 0,7 mm | Trou carré petit bord W≧t | Trou carré petit bord W≧t | |
Largeur de la rainure longue W≧t | Largeur de la rainure longue W≧2t | ||
Distance minimale entre le trou et le trou, le trou et le bord | ≧t | ≧t | ≧1t |
De préférence, la distance entre les trous et les trous, les trous et les bords | ≧1.5t | ≧1.5t | ≧1.5t |
Précision générale de l'usinage | ±0,1 mm | ±0,1 mm | ±0,1 mm |
Gamme de traitement | 2000X1350 | 2000X1350 | |
Effet d'apparence | Bord extérieur lisse, une couche d'écailles sur la face de l'extrémité coupée | Grands bords bruts avec bavures | une petite quantité de bords bruts |
Effet de courbe | Forme lisse et modifiable | Grosses bavures et formes régulières ; | Forme lisse et modifiable |
Vitesse de traitement | Découper rapidement le cercle extérieur | Perforer rapidement des trous denses | le plus rapide |
Traitement du texte | Gravure à l'eau-forte, moins profonde, taille illimitée | Texte concave estampillé avec des symboles plus profonds ; la taille est limitée par le moule | Texte concave estampillé avec des symboles plus profonds ; la taille est limitée par le moule |
Formation | ne peut | Concave, contre-percé, petit étirement, etc. | Possibilité de réaliser des formes plus complexes |
Coût de la transformation | Plus élevé | Faible | Faible |
Technique de la conception des l'arangement
Dans la production de grands et moyens volumes, le coût des pièces représente une part importante.
L'utilisation complète et efficace des matériaux est un indicateur économique important pour la production de tôles.
Par conséquent, à condition que les exigences de conception ne soient pas affectées, le concepteur structurel doit s'efforcer d'adopter la méthode d'arrangement sans déchets ou avec moins de déchets.
Comme le montre la figure 1-7, il n'y a pas de disposition des déchets.
Certaines pièces ont une forme légèrement modifiée, ce qui permet d'économiser beaucoup de matière.
Comme le montre la figure 1-8, la figure 2 utilise moins de matériel que la figure 1.
Possibilité de traitement des pièces découpées
Pour que la poinçonneuse CNC puisse traiter le rayon extérieur, un outil externe spécial est nécessaire. Afin de réduire l'outil du cercle extérieur, l'arrondi d'angle standard de ce manuel, tel qu'il est illustré à la figure 1-9, est le suivant :
1) Série d'arrondis d'angle droit à 90 degrés, le rayon est r2.0, r3.0, r5.0, r10
2) Le rayon de l'angle biseauté à 135 degrés est uniforme à R5.0.
Le poinçonnage est préférable pour utiliser des trous ronds.
Les trous ronds doivent être sélectionnés en fonction de la série de trous ronds spécifiée dans le manuel du moule à tôle.
Cela permet de réduire le nombre d'outils pour les trous ronds et de réduire le temps de changement de lame pour le poinçonnage CNC.
En raison des limites de résistance du poinçon, l'ouverture ne peut pas être trop petite. L'ouverture minimale est liée à l'épaisseur du matériau.
Le diamètre minimal du trou ne doit pas être inférieur à la valeur indiquée dans le tableau 1-5 ci-dessous.
Tableau 1-5 Taille minimale pour le poinçonnage avec un poinçon commun
Le diamètre minimal ou la longueur minimale de l'arête du poinçon (t est l'épaisseur du matériau) | |||
---|---|---|---|
Matériau | Trou rond D(D est le diamètre) | Trou carré L(L est la longueur du bord) | Trou de taille, trou rectangulaire a(a est la longueur minimale du bord) |
Acier à haute et moyenne teneur en carbone | ≥1.3t | ≥1.2t | ≥1t |
Acier à faible teneur en carbone et laiton | ≥1t | ≥0.8t | ≥0.8t |
Aluminium, zinc | ≥0.8t | ≥0.6t | ≥0.6t |
Tissu bakélite stratifié | ≥0.4t | ≥0.35t | ≥0.3t |
La distance entre les trous et entre le trou et le bord ne doit pas être trop faible. La valeur est indiquée dans la figure 1-10 :
La précision entre le trou et la forme, le trou et le trou traité par le moule composite est facile à assurer pendant le processus de fabrication. processus d'estampage du moule.
En outre, l'efficacité de traitement est élevée et le coût d'entretien du moule est pratique.
Compte tenu des raisons susmentionnées, la distance entre le trou et le trou, si la distance entre le trou et la forme peut répondre à l'exigence d'épaisseur de paroi minimale du moule composite, le processus est meilleur, comme le montre la figure 1-11 :
Tableau 1-6 Taille minimale du bord du découpage de la matrice composite
t (<0.8 ) | t (0.8~1.59) | t (1.59~3.18) | t (>3.2) | |
---|---|---|---|---|
D1 | 3mm | 2t | ||
D2 | 3mm | 2t | ||
D3 | 1,6 mm | 2t | 2.5t | |
D4 | 1,6 mm | 2t | 2.5t |
Comme le montre la figure 1-12, le trou est d'abord percé, puis plié. Afin de s'assurer que le trou n'est pas déformé, la distance minimale entre le trou et la bride X≥2t+R
Lors du poinçonnage des trous sur les pièces d'emboutissage, voir figure 1-13, afin de garantir la précision de la forme et de la position des trous ainsi que la résistance du moule, la paroi du trou et la paroi droite des pièces doivent être maintenues à une certaine distance, c'est-à-dire que les distances a1 et a2 doivent répondre aux exigences suivantes :
Dans la formule, R1, R2 est le rayon de l'angle et t est l'épaisseur.
Précision de traitement des pièces découpées
Tableau 1-7 Tableau de tolérance de la distance au centre du trou (Unité:mm)
Précision de poinçonnage ordinaire | Précision de poinçonnage avancée | |||||
---|---|---|---|---|---|---|
Taille nominale L | Taille nominale L | |||||
Épaisseur | <50 | 50~150 | 150~300 | <50 | 50~150 | 150~300 |
<1 | ±0.1 | ±0.15 | ±0.20 | ±0.03 | ±0.05 | ±0.08 |
1~2 | ±0.12 | ±0.20 | ±0.30 | ±0.04 | ±0.06 | ±0.10 |
2~4 | ±0.15 | ±0.25 | ±0.35 | ±0.06 | ±0.08 | ±0.12 |
4~6 | ±0.20 | ±0.30 | ±0.40 | ±0.08 | ±0.10 | ±0.15 |
Note : Tous les trous doivent être perforés une seule fois lorsque les valeurs de ce tableau sont utilisées.
Principe de sélection de la taille de conception des pièces embouties
1) La référence dimensionnelle de conception de la pièce estampée est aussi proche que possible de la référence de positionnement fabriquée, de sorte que l'erreur de fabrication de la dimension peut être évitée.
2) La référence de la taille du trou de la pièce à emboutir doit être sélectionnée autant que possible entre le début et la fin du processus d'emboutissage, et ne doit pas être associée à la pièce participant à la déformation.
3) Pour les pièces qui sont dispersées et estampillées sur différents moules en plusieurs étapes, la même référence de positionnement doit être utilisée autant que possible.
Tableau 1-8 Tableau des tolérances de la distance entre le centre du trou et le bord
Épaisseur | Tailles b | |||
---|---|---|---|---|
≤50 | 50<b≤120 | 120<b≤220 | 220<b≤360 | |
<2 | ±0.2 | ±0.3 | ±0.5 | ±0.7 |
≥2~4 | ±0.3 | ±0.5 | ±0.6 | ±0.8 |
>4 | ±0.4 | ±0.5 | ±0.8 | ±1.0 |
Note : Cette table est adaptée à la perforation de trous après la découpe.
Coupe secondaire
Le découpage secondaire est également appelé découpage secondaire ou découpage supplémentaire (procédé très médiocre, à éviter lors de la conception).
La découpe secondaire est due au fait que l'étirement entraîne une déformation du matériau. Lorsque la déformation par pliage est importante, le découpage est accru. Le formage d'abord, puis la découpe des trous ou des contours pour enlever le matériau réservé et obtenir la taille correcte de la structure complète.
Application : lorsque le bossage de tension est proche du bord, une coupe supplémentaire doit être effectuée.
Prenons l'exemple du lamage, comme le montre la figure 1-16.
Vous pouvez lire cet article pour tout savoir sur le pliage de la tôle.
Les formes les plus courantes d'écrous rivetés sont les suivantes : écrous auto-agrippants, écrous auto-agrippants, écrous à rivets d'ancrage, écrous à rivets de traction et écrous à rivets flottants.
Sl'impasse sur les elfes
Le rivetage par pression signifie que dans le processus de rivetageSous l'effet de la pression extérieure, la pièce à riveter déforme plastiquement le matériau de base et s'insère dans la rainure préfabriquée spécialement conçue dans la structure de la vis et de l'écrou rivetés, réalisant ainsi une connexion fiable entre les deux pièces.
Il existe deux types d'écrous non standard pour le rivetage, l'un est une pièce d'écartement auto-agrippante et l'autre est un écrou auto-agrippant.
La liaison avec le substrat est réalisée à l'aide d'une telle forme rivetée.
Ces formes de rivetage exigent généralement que la pièce rivetée ait une dureté supérieure à celle du substrat.
L'acier ordinaire à faible teneur en carbone, la tôle en alliage d'aluminium et la tôle en cuivre conviennent pour le sertissage de l'entretoise auto-agrippante.
Pour les tôles en acier inoxydable et en acier à haute teneur en carbone, en raison de la dureté du matériau, il est nécessaire d'utiliser une colonne d'écrous rivetés spéciale à haute résistance, qui est non seulement coûteuse, mais aussi difficile à sertir, et le sertissage n'est pas fiable, et il est facile de se détacher après le sertissage.
Afin de garantir la fiabilité, les fabricants doivent souvent ajouter des soudures sur le côté de la colonne d'écrou, ce qui n'est pas bon pour le processus.
Par conséquent, les pièces en tôle avec la colonne de l'écrou à rivets et l'écrou à rivets ne sont pas aussi inoxydables que possible.
Il en va de même pour les vis et les écrous à rivets, qui ne conviennent pas aux tôles d'acier inoxydable.
Le processus de sertissage de la colonne d'écrous rivetés est illustré à la figure 1-41 :
Spincement d'elfe écrou de rivet
Le processus de sertissage de la vis à rivet est illustré à la figure 1-42 :
AEcrou rivet nchor
Le rivetage d'ancrage signifie que, pendant le processus de rivetage, une partie du matériau de la vis ou de l'écrou riveté est plastiquement déformée sous l'action d'une force extérieure, et un ajustement serré est formé avec le matériau de base, réalisant ainsi une connexion fiable des deux parties.
Le ZRS couramment utilisé est relié au substrat par ce type de rivetage.
Le processus de rivetage est relativement simple et la résistance de l'assemblage est faible. Il est généralement utilisé pour limiter la hauteur de la fixation et pour supporter un petit couple. Comme le montre la figure 1-43 :
Tirer écrou de rivet
Le rivetage par traction signifie que l'élément de rivetage est déformé plastiquement sous l'action d'une tension externe pendant le processus de rivetage.
La position de la déformation se trouve généralement dans une pièce spécialement conçue, et le substrat est serré par la partie déformée afin d'obtenir une connexion fiable.
Les écrous rivetés couramment utilisés sont reliés au substrat par ce type de rivetage.
Le rivetage est effectué à l'aide d'un pistolet à rivets spécial, qui est souvent utilisé dans les endroits où l'espace d'installation est réduit et où il n'est pas possible d'utiliser des outils de rivetage universels, tels que les tuyaux fermés. Comme le montre la figure 1-44 :
FEcrou pour rivets de fixation
Certains des écrous à rivets de la structure en tôle, parce que la structure globale du châssis est complexe, l'erreur d'accumulation de la structure est trop importante, de sorte que l'erreur de position relative de ces écrous à rivets est grande, ce qui rend l'assemblage d'autres pièces difficile.
Il s'agit d'une bonne amélioration par rapport à l'utilisation d'un écrou flottant riveté à l'emplacement de l'écrou riveté correspondant.
Comme le montre la figure 1-45 : (Note : il doit y avoir suffisamment d'espace dans la position de rivetage)
Ancre récrou ivet ou auto-bloquant l'écrou du rivet à la distance latérale
L'écrou de rivet d'ancrage ou l'écrou de rivet autoserrant sont rivetés avec la feuille en pressant cette dernière.
Lorsque le rivet d'ancrage ou le rivet auto-agrippant est trop proche du bord, il est facile de déformer cette partie.
En l'absence d'exigence particulière, la distance minimale entre l'axe de la fixation rivetée et le bord de la tôle doit être supérieure à L, voir figure 1-46.
Dans le cas contraire, des pinces spéciales doivent être utilisées pour éviter que les bords de la feuille ne soient déformés par la force.
Facteurs affectant la qualité du rivetage
De nombreux facteurs influencent la qualité du rivetage. En résumé, il s'agit principalement des facteurs suivants : performance du substrat, taille du trou inférieur et méthode de rivetage.
1) Propriétés du substrat.
Lorsque la dureté du substrat est appropriée, la qualité du rivetage est bonne et la force de l'élément de rivetage est bonne.
2) Taille du trou inférieur.
La taille du trou inférieur a une incidence directe sur la qualité du rivetage. Si l'ouverture est grande, l'écart entre le substrat et le rivet est important.
Pour le rivetage, la déformation ne doit pas être suffisante pour remplir la rainure de la pièce à riveter, de sorte que la force de cisaillement est insuffisante, ce qui affecte directement la résistance à la poussée de l'écrou à riveter (clou).
Pour la vis à rivet, le trou inférieur est trop grand, et la force de pression générée par la déformation plastique pendant le processus de rivetage devient faible, ce qui affecte directement la résistance à la poussée et la résistance à la torsion de la vis à rivet (femelle).
Il en va de même pour le rivetage : le trou inférieur est trop grand, de sorte que la friction effective entre les deux pièces après la déformation plastique est réduite, ce qui affecte la qualité du rivetage.
La taille du trou inférieur est petite, et bien que la force du rivetage puisse être augmentée dans une certaine mesure, la qualité de l'apparence du rivetage risque d'être médiocre.
La force de rivetage est importante, l'installation n'est pas pratique et la déformation de la plaque de fond est facilement provoquée, ce qui affecte l'efficacité de production du travail de rivetage et la qualité du rivetage.
3) Méthode de rivetage.
Il a été présenté dans la section précédente. Les vis et écrous à riveter doivent faire l'objet d'une grande attention lors de leur utilisation. Des situations différentes et des exigences de force différentes requièrent des types de vis et d'écrous différents.
S'il n'est pas utilisé correctement, il réduira la plage de force des vis et des écrous rivetés, ce qui entraînera une défaillance de la connexion.
Voici quelques exemples illustrant l'utilisation correcte de la situation normale.
1) Ne pas installer de fixations rivetées en acier ou en acier inoxydable avant que la plaque d'aluminium ne soit anodisée ou traitée en surface.
2) S'il y a trop de rivets sur la même ligne droite, il n'y a pas d'endroit où le matériau extrudé peut s'écouler, ce qui génère des contraintes importantes et déforme la pièce en une forme courbée.
3) Essayez de vous assurer que la surface de la planche est plaquée avant d'installer les fixations rivetées.
4) Les écrous M5, M6, M8, M10 sont généralement soudés. Les écrous trop grands nécessitent généralement une résistance élevée. Soudage à l'arc peuvent être utilisés. En dessous de M4 (y compris M4), il convient d'utiliser l'écrou rivet d'ancrage. S'il est galvanisé, on peut utiliser l'écrou de rivet avec galvanisation.
5) Lors du rivetage de l'écrou sur le côté plié, afin d'assurer la qualité du rivetage de l'écrou riveté, il est nécessaire de faire attention aux points suivants 1.
La distance entre le bord du trou de rivetage et le côté du pli doit être supérieure à la zone de déformation de la pièce pliée. 2.
La distance L entre le centre de l'écrou riveté et l'intérieur du côté plié doit être supérieure à la somme du rayon cylindrique extérieur de l'écrou riveté et du rayon intérieur du pli. Autrement dit, L>D/2+r.
Les soudure par projection (écrou soudé par points) est largement utilisé dans la conception de pièces en tôle.
Cependant, dans de nombreux cas, la taille de l'avant-trou n'est pas conforme à la norme et ne peut être positionnée avec précision.
Le type et les dimensions de la structure sont indiqués dans les figures 1-47 et 1-48. Les valeurs recommandées pour le diamètre du trou D0 et l'épaisseur H avant le soudage de la plaque d'acier pour le soudage sont spécifiées dans le tableau 1-17.
Tableau 1-17 Dimensions des écrous hexagonaux soudés et épaisseur de l'ouverture de la plaque d'acier correspondante (mm)
Taille du filetage (D ou D×P) | M4 | M5 | M6 | M8 | M10 | M12 | M16 | |
---|---|---|---|---|---|---|---|---|
─ | ─ | ─ | M8×1 | M10×1 | M12×1. 5 | M16×1. 5 | ||
─ | ─ | ─ | ─ | (M10×1.25) | (M12×1. 25) | ─ | ||
e | min | 9.83 | 10.95 | 12.02 | 15.38 | 18.74 | 20.91 | 26.51 |
dy | max | 5.97 | 6.96 | 7.96 | 10.45 | 12.45 | 14.75 | 18.735 |
min | 5.885 | 6.87 | 7.87 | 10.34 | 12.34 | 14.64 | 18.605 | |
h1 | max | 0.65 | 0.7 | 0.75 | 0.9 | 1.15 | 1.4 | 1.8 |
min | 0.55 | 0.6 | 0.6 | 0.75 | 0.95 | 1.2 | 1.6 | |
h2 | max | 0.35 | 0.4 | 0.4 | 0.5 | 0.65 | 0.8 | 1 |
min | 0.25 | 0.3 | 0.3 | 0.35 | 0.5 | 0.6 | 0.8 | |
m | max | 3.5 | 4 | 5 | 6.5 | 8 | 10 | 13 |
min | 3.2 | 3.7 | 4.7 | 6.14 | 7.64 | 9.64 | 12.3 | |
D0 | max | 6.075 | 7.09 | 8.09 | 10.61 | 12.61 | 14.91 | 18.93 |
min | 6 | 7 | 8 | 10.5 | 12.5 | 14.8 | 18.8 | |
H | max | 3 | 3.5 | 4 | 4.5 | 5 | 5 | 6 |
min | 0.75 | 0.9 | 0.9 | 1 | 1.25 | 1.5 | 2 |
Note : Dans la mesure du possible, n'utilisez pas les spécifications entre parenthèses.
Taille courante d'un alésage à filetage grossier
Diamètre du filetage M | Épaisseur t | Diamètre intérieur D1 | Diamètre extérieur D2 | Hauteur h | Diamètre de pré-poinçonnage D0 | Rayon |
---|---|---|---|---|---|---|
M2.5 | 0.6 | 2.1 | 2.8 | 1.2 | 1.4 | 0.3 |
0.8 | 2.8 | 1.44 | 1.5 | 0.4 | ||
1 | 2.9 | 1.8 | 1.2 | 0.5 | ||
1.2 | 2.9 | 1.92 | 1.3 | 0.6 | ||
M3 | 1 | 2.55 | 3.5 | 2 | 1.4 | 0.5 |
1.2 | 3.5 | 2.16 | 1.5 | 0.6 | ||
1.5 | 3.5 | 2.4 | 1.7 | 0.75 | ||
M4 | 1 | 3.35 | 4.46 | 2 | 2.3 | 0.5 |
1.2 | 4.5 | 2.16 | 2.3 | 0.6 | ||
1.5 | 4.65 | 2.7 | 1.8 | 0.75 | ||
2 | 4.56 | 3.2 | 2.4 | 1 | ||
M5 | 1.2 | 4.25 | 5.6 | 2.4 | 3 | 0.6 |
1.5 | 5.75 | 3 | 2.5 | 0.75 | ||
2 | 5.75 | 3.6 | 2.7 | 1 | ||
2.5 | 5.75 | 4 | 3.1 | 1.25 |
Distance minimale entre la prise et l'arête de pliage
Tableau 1-19 Distance entre le centre du taraudage et l'arête de pliage Tableau de comparaison des valeurs H
Épaisseur/diamètre du filet | 1 | 1.2 | 1.5 | 2 |
---|---|---|---|---|
M3 | 6.2 | 6.6 | - | - |
M4 | 7.7 | 8 | - | |
M5 | - | 7.6 | 8.4 | - |
Tableau 1-20 Comparaison de l'écrou riveté, de l'écrou autoserrant, du rivetage par traction et du taraudage
Méthode de connexion/caractéristique | Ecrou de rivet d'ancrage | écrou à rivets auto-agrippants | rivetage par traction | bridage et taraudage |
---|---|---|---|---|
Capacité de traitement | c'est bien | bon | bon | moyenne |
Exigences en matière de tôlerie | Rivets en acier inoxydable, faciles à détacher | Le rivetage en acier inoxydable est très médiocre, il faut utiliser des écrous spéciaux pour les rivets, et il faut soudage par points | aucun | Plaque mince et cuivre, aluminium matériau souple facile à glisser |
Précision | bon | bon | bon | moyenne |
Durabilité | bon | bon | bon | Cuivre et aluminium les matériaux souples sont pauvres, les fils d'autres matériaux ont 3 ou 4 boucles ou plus |
Coût | élevé | élevé | moyenne | faible |
qualité | bon | bon | bon | moyenne |
L'étirement de la tôle est illustré à la figure 1-50.
Considérations relatives à l'étirement de la tôle :
En ce qui concerne la forme et la taille de la tôle convexe, plusieurs tailles de série sont spécifiées dans le manuel du moule à tôle. Il existe un modèle Form correspondant dans la bibliothèque Intralink.
Le modèle doit être sélectionné en fonction de la taille spécifiée dans le manuel, et le moule de la bibliothèque est directement utilisé.
Limiter la taille du pas convexe et de la marge convexe
Tableau 1-21 Dimensions limites du pas convexe et de la marge convexe
Schéma | L | B | D |
---|---|---|---|
![]() | 6.5 | 10 | 6 |
8.5 | 13 | 7.5 | |
10.5 | 15 | 9 | |
13 | 18 | 11 | |
15 | 22 | 13 | |
18 | 26 | 16 | |
24 | 34 | 20 | |
31 | 44 | 26 | |
36 | 51 | 30 | |
43 | 60 | 35 | |
48 | 68 | 40 | |
55 | 78 | 45 |
Comme le montre l'illustration 1-52, un gaufrage de 0,3 pouce sur une tôle peut être utilisé comme autocollant pour une étiquette ou un objet similaire afin d'améliorer la fiabilité de l'étiquette.
Dans ce cas, la déformation est beaucoup plus faible que l'étirement normal, mais il subsiste une certaine déformation pour une plaque de couverture de grande surface et une plaque de fond qui n'est pas pliée ou dont la hauteur de pliage est faible.
Autre méthode : Deux lignes à angle droit peuvent être poinçonnées dans la zone d'étiquetage pour améliorer la déformation.
Cependant, la fiabilité de l'attachement de l'étiquette est réduite.
Cette méthode peut également être utilisée pour des traitements tels que le codage des produits, la date de production, la version et même le motif.
La pression des nervures sur les pièces métalliques en forme de plaque (voir figure 1-53) permet d'augmenter la rigidité de la structure.
Comme le montre la figure 1-54,
Les forage Le rivetage est une méthode de rivetage entre tôles, principalement utilisée pour l'assemblage de plaques d'acier revêtues ou de plaques d'acier inoxydable.
L'une des parties est perforée, et l'autre partie est perforée et munie d'une manchette pour en faire un connecteur non détachable.
Avantages : la bride est adaptée au trou droit et possède une fonction de positionnement. La résistance du rivetage est élevée et l'efficacité du rivetage à travers le moule est également élevée.
La méthode spécifique est illustrée à la figure 1-55 :
Tableau 1-22 Dimensions de perçage et de rivetage
Paramètres | Épaisseur T(mm) | Flasque hauteur H(mm) | Diamètre extérieur de la bride D(mm) | |||||||||||
---|---|---|---|---|---|---|---|---|---|---|---|---|---|---|
Non. | 3 | 3.8 | 4 | 4.8 | 5 | 6 | ||||||||
Diamètre intérieur du trou droit correspondant d et trou de pré-poinçonnage d0 | ||||||||||||||
d | d0 | d | d0 | d | d0 | d | d0 | d | d0 | d | d0 | |||
1 | 0.5 | 1.2 | 2.4 | 1.5 | 3.2 | 2.4 | 3.4 | 2.6 | 4.2 | 3.4 | ||||
2 | 0.8 | 2 | 2.3 | 0.7 | 3.1 | 1.8 | 3.3 | 2.1 | 4.1 | 2.9 | 4.3 | 3.2 | ||
3 | 1 | 2.4 | 3.2 | 1.8 | 4 | 2.7 | 4.2 | 2.9 | 5.2 | 4 | ||||
4 | 1.2 | 2.7 | 3 | 1.2 | 3.8 | 2.3 | 4 | 2.5 | 5 | 3.6 | ||||
5 | 1.5 | 3.2 | 2.8 | 1 | 3.6 | 1.7 | 3.8 | 2 | 4.8 | 3.2 |
Note : Avec le principe général H=T+T'+(0.3~0.4)
D = D'-0.3 ;
D-d=0,8T
Lorsque T≧0,8mm, l'épaisseur de la paroi du trou à bride est de 0,4T.
Lorsque T<0,8 mm, l'épaisseur de la paroi de la bride est généralement de 0,3 mm. H est généralement de 0,46±0,12
Dans la méthode de rivetage de la tôle, il existe également une méthode de rivetage qui est le rivetage Tox.
Le principe est que deux piles sont placées l'une à côté de l'autre, comme le montre la figure 1-56.
L'emboutissage et l'étirage à l'aide d'un moule, principalement utilisés pour l'assemblage de tôles d'acier revêtues ou de tôles d'acier inoxydable.
Il présente les avantages d'économiser l'énergie, de protéger l'environnement et d'être très efficace.
Dans le passé, les châssis de l'industrie de la communication utilisaient davantage le rivetage, mais le contrôle de la qualité de la production de masse était difficile. Il a été moins utilisé et n'est pas recommandé.
Les dimensions structurelles de l'alésage de la vis sont sélectionnées comme indiqué dans le tableau suivant.
Pour la tête fraisée de la vis à tête fraisée, si la plaque est trop mince, il est difficile d'assurer le passage d2 et le lamage D en même temps, et le passage d2 doit être garanti de préférence.
Tête fraisée et via pour les vis à tête fraisée : (l'épaisseur de la tôle sélectionnée t est de préférence supérieure à h)
Tableau 1-23 Dimensions de l'alésage de la vis
![]() | d1 | M2 | M2.5 | M3 | M4 | M5 |
---|---|---|---|---|---|---|
d2 | Φ2.2 | Φ2.8 | Φ3.5 | Φ4.5 | Φ5.5 | |
D | Φ4.0 | Φ5.0 | Φ6.0 | Φ8.0 | Φ9.5 | |
h | 1.2 | 1.5 | 1.65 | 2.7 | 2.7 | |
Épaisseur minimale souhaitée | 1.2 | 1.5 | 1.5 | 2 | 2 | |
α | 90° |
Tableau 1-24 Dimensions des trous d'alésage pour les rivets à tête fraisée
![]() | d1 | Φ2 | Φ2.5 | Φ3 | Φ4 | Φ5 |
---|---|---|---|---|---|---|
d2 | Φ2.2 | Φ2.7 | Φ3.3 | Φ4.3 | Φ5.3 | |
D | Φ4.0 | Φ5.0 | Φ5.5 | Φ7.0 | Φ9.0 | |
h | 1 | 1.1 | 1.2 | 1.6 | 2 | |
α | 120° |
L'assemblage de la tôle est complété par des vis à tête fraisée M3.
Si l'épaisseur du trou plaqué est de 1 mm, il est problématique selon la méthode conventionnelle.
Toutefois, un grand nombre de problèmes de ce type se posent lors de la conception réelle.
L'écrou riveté est utilisé en dessous, et le diamètre de l'alésage est de 6 mm, ce qui permet de compléter efficacement la connexion, comme le montre la figure.
Cette taille est utilisée dans un grand nombre de boîtes d'insertion.
Il est important de noter que ce type d'assemblage nécessite que l'écrou inférieur soit un écrou de rivet d'ancrage.
L'écrou rivet auto-agrippant et le taraud ne peuvent pas compléter la connexion de serrage.
Afin de normaliser ces dimensions, le d/D devrait être le suivant :
Tableau 1-25 Unification du contre-perçage des plaques minces
Epaisseur de la tôle | 1 | 1.2 | 1.5 |
---|---|---|---|
M3 | 4/6 | 3.6/6.0 | 3.5/6 |
M4 | - | - | 5.8/8.8 |
En tant que fondateur de MachineMFG, j'ai consacré plus d'une décennie de ma carrière à l'industrie métallurgique. Ma vaste expérience m'a permis de devenir un expert dans les domaines de la fabrication de tôles, de l'usinage, de l'ingénierie mécanique et des machines-outils pour les métaux. Je suis constamment en train de réfléchir, de lire et d'écrire sur ces sujets, m'efforçant constamment de rester à la pointe de mon domaine. Laissez mes connaissances et mon expertise être un atout pour votre entreprise.