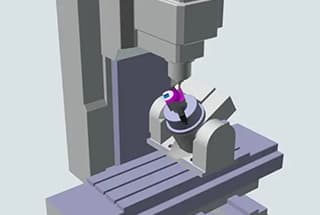
Vous êtes-vous déjà interrogé sur l'histoire fascinante du tour, une machine-outil qui a révolutionné la fabrication ? Dans cet article de blog captivant, nous vous emmenons dans un voyage à travers le temps, en explorant l'évolution remarquable du tour et son impact profond sur diverses industries. De ses humbles débuts à sa sophistication moderne, découvrez comment cet outil polyvalent a façonné notre monde et continue de jouer un rôle essentiel dans l'usinage de précision.
Un tour est une machine-outil polyvalente qui fait principalement tourner une pièce autour d'un axe de rotation pour effectuer diverses opérations d'usinage. L'outil de coupe principal, généralement un outil de tournage monopoint, reste relativement immobile pendant qu'il façonne la pièce en rotation. Outre le tournage, les tours peuvent accueillir une large gamme d'outils de coupe et d'accessoires, notamment des forets, des alésoirs, des tarauds, des filières de filetage et des outils de moletage, ce qui permet de diversifier les processus d'usinage.
Les tours sont principalement utilisés pour produire des pièces cylindriques de haute précision, telles que des arbres, des broches, des axes et des manchons. Ils excellent dans la création de caractéristiques externes et internes sur des surfaces rotatives, y compris des profils droits, coniques et profilés. En raison de leur polyvalence et de leur rôle fondamental dans la production de pièces, les tours sont souvent appelés la "mère des machines-outils" et sont omniprésents dans les installations de fabrication, les ateliers d'usinage et les centres de réparation de diverses industries.
L'évolution de la technologie des tours, depuis les anciennes versions manuelles jusqu'aux machines modernes à commande numérique par ordinateur (CNC), reflète la progression plus générale de la fabrication industrielle. Cette histoire riche et ce développement continu soulignent l'importance cruciale du tour dans le façonnement du passé, du présent et de l'avenir de l'usinage de précision et de la production industrielle.
Le premier prototype de machine-outil, le tour, a été créé par nos ancêtres il y a environ 2 000 ans pour faciliter le travail avec des outils.
Au cours du XIIIe siècle, le développement des machines-outils s'est poursuivi et il a fallu trouver d'autres méthodes de fonctionnement, car il n'était plus possible de les suspendre à un arbre. C'est ainsi qu'est né le "tour à pédale", qui utilisait une pédale pour faire tourner le vilebrequin et entraîner le volant d'inertie. Celui-ci entraînait à son tour la broche, la faisant tourner, et était également connu sous le nom de "tour à barre flexible".
À la même époque en Chine, la dynastie Ming a publié un ouvrage remarquable intitulé "Tian Gong Kai Wu", qui documente les technologies de la dynastie Ming et de la dynastie qui l'a précédée, démontrant ainsi la signification de la "sagesse des anciens".
Le livre décrit également la structure d'une machine à broyer, dont le principe est similaire à celui de la machine médiévale européenne actionnée par le pied. Cette machine utilisait la méthode de la pédale pour faire tourner une plaque de métal et utilisait du sable et de l'eau pour façonner le jade.
Structure d'une machine à broyer Tian Gong Kai Wu
de Tian Gong Kai Wu
Ce processus est similaire aux techniques d'usinage modernes telles que l'alésage, où un outil spécialisé, appelé "steelyard", est utilisé pour retirer de petites quantités de matériau de l'intérieur du jade. Il est remarquable de constater le niveau de compétence et d'expertise des artisans de l'Antiquité.
de Tian Gong Kai Wu
En 1774, l'inventeur britannique Wilkinson a créé la première véritable machine à aléser au monde, la machine à aléser à barillet.
Le tonneau machine d'alésage inventée par Wilkinson a d'abord été utilisée pour forger des armes à feu. En 1775, Wilkinson a utilisé le cylindre foré par cette machine pour construire une nouvelle version du cylindre fuyant de Wattner, qui répondait aux spécifications requises pour la machine à vapeur de Watt.
Pour permettre le perçage de cylindres plus grands, il a construit la même année une machine à percer les cylindres actionnée par une roue hydraulique, ce qui a grandement contribué à l'avancement des machines à vapeur.
La machine à aléser les cylindres de Wilkinson, conçue pour forger des cylindres de plus grande taille, a marqué un tournant dans l'évolution des machines-outils. Dès lors, la machine-outil est entraînée par une machine à vapeur au moyen d'un vilebrequin. L'assistance mutuelle entre la machine-outil et la machine à vapeur a facilité leur développement simultané et a ouvert une ère dynamique de révolution industrielle.
Il est important de mentionner Henry Maudslay, l'inventeur britannique connu comme le "père du tour". Maudslay est au tour ce que James Watt est à la machine à vapeur.
En 1797, Maudslay crée le premier tour à fileter au monde, équipé d'une vis et d'une tige polie. Ce tour moderne, équipé d'un porte-outil coulissant, permet de réaliser des filetages de pas différents.
Tour Maudslay 1797
Maudslay continue à perfectionner le tour et, en 1800, il apporte une amélioration significative en remplaçant le cadre triangulaire en barres de fer par un banc en fonte massif et la roue folle par des paires d'engrenages interchangeables.
Cela permettait de produire des filets de pas différents sans avoir à changer la vis. Ce prototype du tour moderne, connu sous le nom de tour à cadre d'outils, a joué un rôle crucial dans la révolution industrielle anglaise.
Tour Maudslay 1800
Pour être précis, Maudslay n'a pas inventé le tour, mais l'a plutôt réinventé en se basant sur les travaux de ses prédécesseurs et en y ajoutant la capacité de coupe automatique. Néanmoins, c'est la réimagination de Maudslay qui a rendu le tour largement populaire et a donné naissance au tour tel que nous le connaissons aujourd'hui.
Le développement rapide de tous les les types de machines-outils
Au XIXe siècle, avec la croissance de diverses industries, la demande de divers types de machines-outils a augmenté. En 1817, Roberts crée le tour à portique et en 1818, l'Américain Whitney invente la première fraiseuse polyvalente au monde.
Tour à portique Roberts
Pour améliorer encore la mécanisation et l'automatisation, l'Américain Fitch a créé en 1845 le tour à tourelle. En 1848, les tours rotatifs ont été introduits aux États-Unis et, en 1873, l'Américain Spencer a mis au point un tour automatique monobroche. L'invention d'un tour automatique à trois broches a rapidement suivi.
Au début du 20e siècle, des tours équipés d'une boîte de vitesses actionnée par un seul moteur sont apparus.
Machines-outils Spencer
En 1900, la société américaine Norton a utilisé l'émeri et le corindon pour produire une meule large et de grande taille, ainsi qu'une meule robuste et résistante. Cela a marqué un grand pas en avant dans le développement des meules et a élevé la technologie de fabrication des machines à un nouveau niveau de précision.
La révolution industrielle a été une période de croissance et de développement explosifs. À cette époque, les machines-outils n'ont cessé d'évoluer et de s'améliorer pour accroître l'efficacité de l'industrie et de la production. Les inventeurs de ces machines-outils ont joué un rôle crucial dans l'évolution du monde.
Avec l'avènement de l'acier à outils à haute vitesse et l'utilisation généralisée des moteurs électriques, les machines-outils ont connu une nouvelle évolution historique, passant de la vapeur à l'électricité. Cela démontre les progrès remarquables réalisés par l'humanité au cours de centaines d'années, en passant de l'énergie humaine à l'énergie hydraulique, à l'énergie à vapeur et enfin à l'énergie électrique.
1910, vieux tour britannique
Après la Première Guerre mondiale, le développement de divers tours automatiques à haut rendement et de tours spécialisés s'est accéléré rapidement en raison de la demande des industries des munitions, de l'automobile et d'autres machines.
À la fin des années 1940, pour améliorer la productivité des petites séries de pièces, des tours équipés de dispositifs de profilage hydrauliques ont été introduits. À la même époque, des tours à outils multiples ont également été mis au point.
Machine-outil électrique après la Seconde Guerre mondiale
Au milieu des années 50, des tours à commande programmée équipés de cartes perforées, de plaques de verrouillage et de cadrans ont été mis au point. L'utilisation de la technologie CNC dans les tours a commencé dans les années 1960 et, dans les années 1970, les microprocesseurs ont été directement intégrés dans les machines CNC, ce qui a permis de populariser et de développer rapidement la technologie CNC. Machine CNC qui n'a cessé d'évoluer jusqu'à aujourd'hui.
Précoce Machines-outils à commande numérique
L'histoire du tour a connu des avancées significatives au cours des périodes romaine et médiévale, chacune apportant des innovations cruciales qui ont amélioré sa fonctionnalité et son efficacité.
Les Romains ont considérablement amélioré le tour en introduisant l'archet de tournage, une innovation majeure par rapport à la conception égyptienne antérieure qui nécessitait deux opérateurs. L'arc de tournage permettait à une seule personne d'utiliser le tour, ce qui simplifiait le processus et le rendait plus efficace. Cette méthode consistait à utiliser un arc pour tourner la pièce, ce qui permettait une rotation plus régulière et mieux contrôlée.
Grâce à l'arc tournant, les artisans romains ont obtenu une plus grande précision dans leur travail. Cette avancée leur a permis de produire des objets finement ouvragés tels que des boîtes à couvercle, des récipients et des pièces de mobilier sophistiquées à partir de matériaux tels que le buis. Des objets spécifiques tels que des bols en bois au design complexe et des pièces de mobilier en bois sculptées datant de l'époque romaine illustrent le haut niveau de compétence et d'art atteint grâce à ces tours améliorés.
Les innovations introduites par les Romains ont jeté des bases solides pour les progrès ultérieurs de la période médiévale. De l'époque romaine au Moyen Âge, le tour a continué d'évoluer, incorporant de nouveaux mécanismes qui ont encore amélioré ses capacités.
Au cours du Moyen Âge, le tour a subi une autre transformation importante avec l'introduction du système à pédale. Ce système a remplacé la méthode de tournage manuelle, permettant à l'artisan d'utiliser ses deux mains pour manipuler les outils de coupe. La pédale était généralement reliée à un poteau, souvent un jeune arbre à grain droit, créant ainsi ce que l'on appelle le "tour à ressort".
Le tour à perche à ressort permettait une rotation plus continue et plus régulière de la pièce. Cette innovation a permis aux artisans de produire des objets plus complexes et plus détaillés, tels que des maillets, des bols, des manches d'outils et des pieds de meubles. La possibilité d'actionner le tour à l'aide d'une pédale permettait aux artisans de contrôler plus finement le processus de coupe, ce qui se traduisait par des produits plus complexes et de meilleure qualité.
Les artisans médiévaux, y compris ceux qui vivaient en Europe à l'époque des Vikings, utilisaient largement le tour pour la vie quotidienne et les objets domestiques. Des découvertes archéologiques, comme celles faites à York, ont révélé que le tournage du bois faisait partie intégrante de la vie quotidienne, de nombreux bols en bois et d'autres objets étant fabriqués à l'aide de tours à perche. Ces découvertes soulignent l'importance et la polyvalence du tour dans la société médiévale.
Les progrès réalisés au cours des périodes romaine et médiévale ont jeté les bases du rôle central du tour dans la révolution industrielle. Les améliorations de la précision et de l'efficacité obtenues grâce à l'arc de tournage et aux systèmes actionnés par une pédale ont ouvert la voie à d'autres innovations. Au cours de la révolution industrielle, le tour est devenu un outil essentiel pour fabriquer des pièces destinées à d'autres machines-outils et a été intégré à des sources d'énergie mécanisées telles que les moteurs à vapeur et les roues hydrauliques afin d'accroître la productivité.
Ces développements historiques ont consolidé la position du tour en tant que "mère de toutes les machines-outils", ce qui a conduit au développement de technologies plus avancées telles que les tours hydrauliques et les tours à commande numérique par ordinateur (CNC) au cours des siècles suivants. Les innovations des périodes romaine et médiévale ont joué un rôle crucial dans l'évolution du tour, contribuant à son importance durable dans la fabrication et l'ingénierie.
La révolution industrielle a marqué une période de transformation dans l'histoire du tour, en introduisant des avancées significatives dans sa conception, sa puissance et sa fonctionnalité. C'est à cette époque que l'on est passé des tours à commande manuelle à des tours alimentés par des sources mécanisées, ce qui a permis d'accroître l'efficacité et la précision.
L'introduction de sources d'énergie mécanisées pour les tours a été l'une des principales évolutions de la révolution industrielle. Les moteurs à vapeur et les roues hydrauliques ont remplacé l'énergie humaine et animale, permettant aux tours de fonctionner à des vitesses plus élevées et avec une plus grande régularité. Ces sources d'énergie étaient reliées aux tours par des arbres de transmission. L'arbre de ligne est un système d'arbres rotatifs utilisé pour transmettre l'énergie d'un moteur central aux différentes machines d'un atelier. Cette innovation a permis de tourner la pièce plus rapidement et plus efficacement, ce qui a considérablement augmenté la productivité. Par exemple, l'adoption généralisée des tours à eau et à vapeur à la fin du XVIIIe siècle a permis un fonctionnement continu, ce qui était essentiel pour répondre aux exigences des industries en pleine croissance.
La fin du 18e et le début du 19e siècle ont vu l'avènement des tours de précision pour l'usinage des métaux. Des innovations telles que le support à glissière, qui permettait à l'outil de coupe de se déplacer de manière contrôlée, ont permis de produire des surfaces cylindriques et coniques précises. Le tour à aléser les canons de Jan Verbruggen, actionné par un cheval et installé à l'Arsenal royal de Woolwich, en Angleterre, en 1772, en est un exemple notable. Cette machine a permis de produire des canons plus solides et plus précis, démontrant ainsi l'amélioration de la précision obtenue avec ces nouveaux tours. La demande de pièces standardisées dans l'économie industrielle en plein essor a fait naître le besoin d'une plus grande précision, ce qui a conduit à des améliorations constantes de la technologie des tours.
La révolution industrielle a également entraîné une augmentation de la demande de machines-outils, notamment de tours, pour la fabrication de pièces destinées à diverses industries telles que le transport et la fabrication. Les tours sont devenus plus grands et plus robustes, avec des composants plus épais et plus lourds pour faire face à l'augmentation de la charge de travail. David Wilkinson, un inventeur américain, a apporté une contribution importante avec son tour à fileter, qui a ensuite évolué pour devenir un tour à usage général. Ce développement illustre l'importance accordée à l'époque à l'amélioration de la polyvalence et de la productivité de ces machines, permettant la production en masse de pièces interchangeables.
À la fin du XIXe siècle et au début du XXe siècle, les moteurs électriques ont commencé à remplacer les arbres de transmission comme principale source d'énergie pour les tours. Cette évolution a permis d'accroître l'efficacité et de simplifier le processus d'alimentation de plusieurs machines dans un atelier. Les moteurs électriques fournissent une puissance plus fiable et plus constante, réduisant ainsi la complexité associée à l'entretien et à l'exploitation des systèmes d'arbres de transmission. Cette transition a marqué une étape importante dans la modernisation des processus de fabrication, en permettant un contrôle plus précis des opérations de tournage.
La seconde moitié du XXe siècle a vu l'introduction des tours à commande numérique informatisée (CNC), qui ont à nouveau révolutionné l'industrie. Apparus dans les années 1950, les tours à commande numérique permettent aux opérateurs de saisir des spécifications préprogrammées, ce qui améliore considérablement la précision et l'automatisation. Ces machines pouvaient effectuer des opérations complexes avec une intervention humaine minimale, augmentant ainsi l'efficacité et la précision des processus de fabrication. Depuis, les tours à commande numérique sont devenus un élément essentiel des ateliers modernes, capables de produire des composants extrêmement complexes et précis. L'avènement de la technologie CNC a représenté une avancée majeure dans les capacités des tours, s'alignant sur les besoins des industries manufacturières de pointe.
La révolution industrielle a été une période critique dans l'évolution du tour, introduisant l'énergie mécanique, l'ingénierie de précision et l'automatisation. Ces progrès ont consolidé le rôle du tour en tant que pierre angulaire de la fabrication moderne et ont ouvert la voie aux innovations technologiques futures.
L'histoire des tours a connu des avancées remarquables à l'ère moderne, améliorant considérablement leurs capacités, leur précision et leur efficacité. Ces progrès ont révolutionné les processus de fabrication et élargi les applications des tours dans diverses industries.
L'introduction de la technologie de la commande numérique par ordinateur (CNC) au 20e siècle a marqué une étape importante pour les tours. Les tours à commande numérique ont apporté une précision et une complexité sans précédent aux tâches d'usinage. Les opérateurs pouvaient désormais saisir des spécifications préprogrammées, ce qui permettait d'automatiser les opérations et de produire des modèles complexes avec une précision et une répétabilité élevées. Par exemple, les tours à commande numérique ont permis de réduire les temps de production de 50% et d'améliorer la qualité des produits en maintenant des tolérances constantes de l'ordre du micron.
En outre, les tours CNC modernes ont adopté des capacités d'usinage multi-axes, comportant généralement cinq axes de mouvement ou plus. L'usinage multi-axes permet une plus grande flexibilité dans l'usinage de formes et de géométries complexes sans qu'il soit nécessaire de repositionner la pièce à usiner. Cette avancée améliore la précision et réduit la nécessité de configurer plusieurs machines, ce qui permet de gagner du temps et d'améliorer la productivité globale. Par exemple, un tour CNC à cinq axes peut usiner des pièces qui nécessiteraient autrement plusieurs configurations différentes sur une machine à trois axes.
En outre, les progrès récents dans les technologies d'outillage ont encore amélioré les capacités des tours à commande numérique. Des outils de coupe, des revêtements et des matériaux de haute performance ont été mis au point pour résister aux exigences des processus d'usinage modernes. Les systèmes d'outillage à changement rapide sont devenus courants, ce qui permet de changer rapidement d'outil et de minimiser les temps d'arrêt dus à l'usure de l'outil. Ces progrès contribuent à rendre le processus d'usinage CNC plus efficace en maximisant la productivité et en préservant la durée de vie des outils.
L'intégration de l'automatisation est devenue une caractéristique essentielle des tours CNC modernes. Les chargeurs et déchargeurs robotisés automatisent les tâches de manutention, réduisant les interventions manuelles et augmentant la productivité. Les systèmes automatisés permettent aux tours CNC de fonctionner en continu, ce qui minimise les temps d'arrêt et contribue à un environnement de fabrication plus sûr et plus cohérent. Par exemple, des entreprises ont signalé des augmentations de productivité allant jusqu'à 30% et des économies de coûts de 20% grâce à l'automatisation.
En outre, l'intégration de la connectivité de l'internet des objets (IoT) dans les tours CNC a ouvert l'ère de l'industrie 4.0. Les tours compatibles avec l'IoT peuvent surveiller les performances de la machine en temps réel, collecter et analyser des données, et mettre en œuvre des procédures de maintenance prédictive. Cette connectivité permet de détecter et de corriger rapidement les défauts potentiels, de réduire les temps d'arrêt et d'améliorer l'efficacité globale de l'équipement. La connectivité IoT a transformé les tours CNC en machines hautement intelligentes et réactives, capables d'auto-optimisation et de surveillance en temps réel.
Les centres de tournage modernes sont conçus pour être plus efficaces sur le plan énergétique, en intégrant des caractéristiques qui réduisent la consommation d'énergie et la chaleur perdue. L'accent mis sur l'efficacité énergétique permet non seulement de réduire les coûts d'exploitation, mais a également un impact positif sur l'environnement. Les fabricants accordent de plus en plus d'importance aux pratiques durables, et le développement de tours CNC à haut rendement énergétique va dans le sens de ces objectifs. Par exemple, les tours CNC à haut rendement énergétique peuvent réduire la consommation d'électricité jusqu'à 20%, ce qui contribue à réduire l'empreinte carbone.
L'avenir des tours devrait être marqué par de nouvelles avancées dans la technologie CNC, telles que les commandes numériques de nouvelle génération, l'intégration de la réalité virtuelle et l'amélioration de la programmation et de l'automatisation de la CNC. L'intégration de technologies telles que l'impression 3D et le contrôle des mouvements de précision continuera à améliorer la qualité et la rapidité des processus d'usinage. Grâce à ces innovations, les tours resteront à la pointe de la technologie de fabrication, ce qui permettra d'améliorer encore la productivité et la précision.
Les tours ont contribué à façonner la fabrication moderne, en offrant de nombreux avantages et en ayant un impact profond sur diverses industries.
Les tours sont réputés pour leur polyvalence, car ils sont capables d'effectuer toute une série d'opérations telles que le tournage, le dressage, le filetage, le tronçonnage, le chanfreinage, le moletage, le perçage, l'alésage et l'alésage. Ce large éventail de capacités fait des tours des outils essentiels dans de nombreux secteurs, notamment le tournage du bois, le travail des métaux, le repoussage des métaux, la pulvérisation thermique et le travail du verre. La capacité à manipuler divers matériaux et à produire des formes complexes et des composants précis a renforcé le rôle du tour dans les petits ateliers artisanaux comme dans les grandes usines de fabrication industrielle. Par exemple, dans l'industrie automobile, les tours sont utilisés pour fabriquer des pièces de moteur de haute précision, tandis que dans l'aérospatiale, ils sont essentiels pour créer des composants complexes avec des tolérances serrées.
L'introduction de la technologie CNC (Computer Numerical Control) a révolutionné les opérations de tournage en améliorant considérablement la productivité et la précision. La technologie CNC permet le contrôle automatisé des outils d'usinage par le biais d'une programmation informatique. Les opérateurs entrent des instructions détaillées dans l'ordinateur de la machine, qui commande ensuite avec précision le tour pour exécuter des tâches complexes. Cette avancée est particulièrement cruciale dans les secteurs qui exigent une grande précision, tels que l'aérospatiale, l'automobile et l'électronique. Par exemple, les tours à commande numérique peuvent produire des composants de haute qualité rapidement et avec une intervention manuelle minimale, ce qui réduit les erreurs humaines et garantit une précision constante. L'automatisation offerte par les tours à commande numérique permet de produire des pièces complexes avec des tolérances serrées, ce qui serait difficile à réaliser avec des méthodes manuelles.
Les tours contribuent à l'efficacité économique en permettant d'économiser du temps et de l'argent. Les tours automatisés réduisent les coûts de main-d'œuvre en minimisant le besoin d'opérateurs hautement qualifiés et en diminuant le temps total d'usinage. Cette efficacité se traduit par une rentabilité accrue pour les entreprises de fabrication. En outre, la précision et la répétabilité des tours à commande numérique réduisent le gaspillage de matériaux, ce qui contribue encore à la réduction des coûts. Par exemple, une étude a révélé que les fabricants utilisant des tours à commande numérique ont enregistré une réduction de 30% des déchets de matériaux. La capacité de produire des pièces en grandes quantités sans compromettre la qualité favorise également la production de masse et la normalisation, qui sont essentielles pour les pratiques de fabrication modernes.
Le tour est souvent appelé la "mère des machines-outils" en raison de son rôle fondamental dans le développement d'autres machines-outils. Son invention et ses améliorations constantes ont été à l'origine de progrès technologiques dans le domaine de la fabrication. La capacité de créer des pièces précises et complexes a facilité la production de machines et d'équipements essentiels pour diverses industries, notamment la construction, les transports et les appareils médicaux. Par exemple, la précision requise dans les dispositifs médicaux tels que les prothèses et les implants est possible grâce aux progrès de la technologie des tours. L'impact du tour s'étend au-delà de la fabrication, influençant le progrès technologique et l'industrialisation à l'échelle mondiale.
L'évolution du tour a été parallèle aux progrès technologiques importants. Des premiers tours à main aux machines CNC sophistiquées d'aujourd'hui, chaque innovation a contribué au domaine plus large de l'ingénierie et de la technologie de fabrication. L'intégration de l'IdO (Internet des objets) et des techniques de fabrication intelligente dans les tours modernes illustre cette progression. Les tours équipés de l'IdO peuvent surveiller les performances en temps réel, mettre en œuvre une maintenance prédictive et optimiser les opérations, améliorant ainsi la productivité et réduisant les temps d'arrêt. Par exemple, les capteurs IoT peuvent détecter l'usure des composants et alerter les opérateurs pour qu'ils effectuent la maintenance avant qu'une panne ne se produise.
Les tours modernes sont conçus avec des dispositifs de sécurité améliorés et des technologies à haut rendement énergétique. Les mécanismes de sécurité tels que les arrêts automatiques, les protections et la surveillance en temps réel réduisent le risque d'accident et rendent le lieu de travail plus sûr pour les opérateurs. Les conceptions à haut rendement énergétique réduisent la consommation d'énergie et minimisent la chaleur perdue, ce qui va dans le sens des pratiques de fabrication durable. Ces avancées contribuent non seulement à rendre l'environnement de travail plus sûr, mais aussi à soutenir l'évolution de l'industrie vers une production respectueuse de l'environnement. Par exemple, les tours CNC à haut rendement énergétique peuvent réduire la consommation d'énergie jusqu'à 20%, ce qui contribue à réduire les coûts d'exploitation et l'empreinte carbone.
Les avantages et l'impact des tours sont vastes : ils améliorent la polyvalence, la productivité, l'efficacité économique et contribuent aux progrès industriels et technologiques. L'évolution continue du tour garantit sa pertinence et son rôle indispensable dans la fabrication moderne et au-delà.
Vous trouverez ci-dessous les réponses à certaines questions fréquemment posées :
Le premier tour a été inventé vers 1300 avant J.-C. dans l'Égypte ancienne. Ces premiers tours étaient des appareils simples qui nécessitaient l'intervention de deux personnes : l'une pour tourner la pièce à l'aide d'une broche enroulée autour d'une corde et l'autre pour la façonner à l'aide d'un outil tranchant. Cette innovation a marqué le début de la longue histoire du tour, dont les améliorations et les innovations se sont succédé au fil des siècles, notamment à l'époque romaine, au Moyen Âge, à la révolution industrielle et à l'avènement de l'automatisation moderne.
Les Romains ont apporté des améliorations significatives au tour en introduisant l'archet de tournage, qui permettait un fonctionnement plus facile et plus efficace. Cette innovation a permis à un seul opérateur de gérer le tour, contrairement aux modèles précédents qui nécessitaient deux personnes, l'une pour créer le mouvement de rotation en tirant sur une corde et l'autre pour tenir l'outil de coupe. Bien que le tour à archet présente certaines limites en termes de précision et de force de rotation, il marque un progrès considérable en rendant la machine plus pratique et plus accessible pour les artisans individuels. Ces améliorations ont jeté les bases d'autres perfectionnements, comme l'utilisation ultérieure de pédales et de perches à ressort, qui ont amélioré l'efficacité et la précision du tour au cours des siècles suivants.
Au cours de la révolution industrielle, le tour a connu d'importantes avancées qui ont grandement amélioré sa fonctionnalité et son efficacité. L'une des principales évolutions a été l'introduction de sources d'énergie mécanisées, telles que les machines à vapeur et les roues hydrauliques, qui ont remplacé l'énergie manuelle ou animale. Cette mécanisation a permis aux tours de fonctionner plus rapidement et plus régulièrement.
L'amélioration de la précision et de l'automatisation a constitué un autre progrès majeur. Des innovations telles que le support coulissant, développé par des ingénieurs comme Andrey Nartov et Henry Maudslay, ont permis de générer des surfaces cylindriques et coniques précises sans manipulation manuelle de l'outil. La conception de Maudslay, qui consiste à fixer l'outil de coupe sur des rails coulissants, garantit des coupes régulières et des tailles de filets de vis standardisées, ce qui est crucial pour la production de masse.
En outre, les tours sont passés du travail du bois à celui du métal au cours de cette période. Cette évolution a permis d'accroître la précision et l'efficacité de la coupe et du façonnage des pièces métalliques, ce qui a constitué une amélioration significative par rapport aux méthodes manuelles.
Le concept de production de masse et de pièces interchangeables, défendu par Eli Whitney, a également été rendu possible grâce à la précision et à la standardisation offertes par les tours à métaux. Cela a révolutionné les processus de fabrication, en particulier dans des industries telles que les armes à feu, les textiles et les transports, en permettant la production de composants identiques à grande échelle.
Dans l'ensemble, les progrès de la technologie des tours au cours de la révolution industrielle ont jeté les bases des innovations futures, notamment le développement de la technologie de la commande numérique par ordinateur (CNC) dans les années 1950. Ces améliorations ont rendu les tours plus puissants, plus polyvalents et plus efficaces, contribuant grandement aux progrès industriels de l'époque.
La technologie CNC (Computer Numerical Control) a profondément transformé les tours en automatisant et en améliorant leur précision, leur efficacité et leur polyvalence. Avant la CNC, les opérations de tournage étaient manuelles ou contrôlées mécaniquement, ce qui les rendait laborieuses et sujettes à l'erreur humaine. L'introduction de la technologie CNC au milieu du XXe siècle a révolutionné ces machines en leur permettant de suivre des instructions précises à partir de programmes informatiques générés par des logiciels de CAO (conception assistée par ordinateur) et de FAO (fabrication assistée par ordinateur). Cela a permis aux tours CNC de réaliser des opérations d'usinage extrêmement précises et reproductibles, essentielles pour les industries exigeant des tolérances serrées, telles que l'aérospatiale, l'équipement médical et l'automobile.
La technologie CNC a également introduit des capacités multi-axes, élargissant la gamme d'opérations que les tours peuvent effectuer. Par exemple, les tours CNC à 3 axes gèrent des conceptions plus complexes, les tours à 4 axes permettent de réaliser des contournages complexes et des usinages multi-processus, et les tours à 5 axes permettent d'approcher l'outil dans pratiquement toutes les directions, ce qui est essentiel pour produire des géométries complexes. Certains tours CNC comportent même six axes ou plus, offrant une flexibilité et une précision inégalées.
L'automatisation offerte par la technologie CNC renforce considérablement l'efficacité et la productivité, permettant un fonctionnement continu avec des temps d'arrêt minimes et des coûts de main-d'œuvre réduits. Les tours à commande numérique peuvent travailler avec différents matériaux, notamment les métaux, les plastiques, les céramiques et les composites, ce qui les rend très polyvalents. En outre, l'automatisation améliore la sécurité sur le lieu de travail en minimisant les interventions manuelles et en réduisant l'exposition aux risques. L'usinage CNC favorise également le développement durable grâce à l'utilisation efficace des matériaux et à la réduction des déchets.
En résumé, la technologie CNC a transformé les tours en outils hautement automatisés, précis et polyvalents, révolutionnant l'industrie manufacturière en améliorant la productivité, la sécurité et la capacité à produire des pièces complexes avec une grande précision.
Le tour est considéré comme la "mère des machines-outils" en raison de son rôle fondamental dans l'histoire et le développement des machines-outils. Issu des civilisations anciennes, le principe de base du tour, qui consiste à faire tourner une pièce contre un outil de coupe, a jeté les bases de l'usinage moderne. Tout au long de l'histoire, des innovations importantes, telles que l'ajout d'un arc rotatif par les Romains et le tour à pédale au Moyen-Âge, ont amélioré son efficacité et sa fonctionnalité.
Au cours de la révolution industrielle, le tour est devenu essentiel pour la production de masse de pièces, ce qui a conduit à la mise au point de machines plus sophistiquées, notamment des tours hydrauliques actionnés par des machines à vapeur. Cette période a vu l'évolution du tour vers un outil plus précis et plus polyvalent, essentiel à la création de pièces pour d'autres machines.
La capacité du tour à effectuer diverses opérations, telles que le tournage, le perçage et le découpage, en a fait un outil indispensable dans différentes industries. Sa polyvalence et son adaptabilité lui ont permis de rester d'actualité, depuis l'invention du tour à glissière entièrement métallique par Jacques de Vaucanson au XVIIIe siècle jusqu'aux tours modernes à commande numérique d'aujourd'hui.
En résumé, l'importance historique du tour, son rôle dans la révolution industrielle, sa conception fondatrice pour d'autres machines-outils et les progrès constants en matière de précision et d'automatisation en font la "mère des machines-outils".
Les tours modernes, qui ont considérablement évolué par rapport à leurs homologues historiques, se déclinent en différents types en fonction de leur conception, de leur fonctionnalité et de leur application. Le tour à moteur, également connu sous le nom de tour central, est le type le plus courant et le plus polyvalent. Il est entraîné par un moteur électrique et utilisé pour un large éventail d'opérations de tournage telles que le découpage, le ponçage, le moletage et le perçage sur divers matériaux tels que les métaux, les plastiques et le bois. Les tours d'établi sont plus petits et conçus pour le travail de précision sur de petites pièces, ce qui les rend idéaux pour la bijouterie et l'horlogerie en raison de leur taille compacte et de leur capacité à effectuer des tâches détaillées.
Les tours à tourelle se caractérisent par une tourelle rotative qui contient plusieurs outils de coupe, ce qui permet des changements d'outils efficaces et rapides et les rend adaptés à la production de masse. Les tours CNC (Computer Numerical Control) sont contrôlés par ordinateur et offrent des processus d'usinage très précis, ce qui les rend parfaits pour les conceptions complexes et la fabrication en grandes quantités dans des industries telles que l'aérospatiale et l'automobile.
Les tours rapides fonctionnent à grande vitesse et sont principalement utilisés pour les opérations de finition et de polissage, tandis que les tours verticaux, dont la broche est orientée verticalement, traitent des pièces lourdes et de grande taille et sont couramment utilisés dans les industries lourdes pour l'usinage de composants tels que les disques de turbine. Les tours pour salles d'usinage sont des machines de haute précision conçues pour les pièces maîtresses et les outils de faible production, connues pour leur rigidité et leur précision.
Les tours spéciaux sont conçus sur mesure pour des tâches spécifiques et sont souvent utilisés pour des opérations lourdes pour lesquelles les tours standard sont inadéquats. Les tours automatiques, conçus pour la production en grande série, peuvent effectuer diverses opérations automatiquement, améliorant ainsi la productivité et l'efficacité. Chaque type de tour moderne a été développé pour répondre à des besoins d'usinage spécifiques, du travail de précision à la production à grande échelle, et continue à jouer un rôle essentiel dans de nombreuses industries.