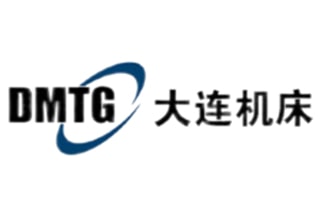
How can simple powder transform into one of the toughest materials on Earth? This article explores the intricate process of making blades, from the initial powder metallurgy to the final coating. By the end, you’ll understand each step in crafting these essential tools, including mixing, pressing, sintering, grinding, and edge treatment. Dive into the world of blade production and discover the precision and technology that ensure their strength and durability.
Today, powder metallurgy has made significant progress and has come close to the hardness of the world’s toughest material, diamond.
Powder may seem like an unlikely candidate, but it is surprising to know that one of the hardest materials in the world is made from it.
We can uncover the mystery of cemented carbide blade production, from the initial powder to the final blade.
Tungsten oxide is mixed with carbon and processed in a special furnace to produce tungsten carbide, which serves as the primary raw material for all cemented carbide.
Tungsten carbide is an exceptionally hard and brittle material that forms the main component of cemented carbide.
Cobalt is a critical element for the properties of cemented carbide when combined with tungsten carbide.
The greater the amount of cobalt, the better the toughness of cemented carbide. Conversely, less cobalt makes it harder and more wear-resistant.
The weight ratio of different components is meticulously measured with the highest accuracy.
A batch of 420 kg raw materials must have an error margin of no more than 20 grams.
Mixing is a precise metallurgical operation.
Finally, the mixture is ground into a fine and delicate powder in a large ball mill.
The powder mixture must undergo spray drying to achieve the appropriate fluidity.
After grinding, the particle size of the powder reaches 0.5-2.0 micrometers.
To begin with, the basic shape and size of the blade are obtained through punching with a die and a highly automatic CNC-controlled press.
Although the blade may appear similar to a real cemented carbide blade after pressing, its hardness is still far from the required standard.
Subsequently, a robot transfers the pressed blade to a disc that is made of heat-resistant material.
To harden the blade, it undergoes a heat treatment at 1500℃ for 15 hours.
During the sintering process, the cobalt and tungsten carbide particles are melted and bonded together. There are two crucial steps involved in the sintering furnace process. First, the blade undergoes obvious shrinkage, and only accurate shrinkage can ensure obtaining the correct tolerance. Second, the powder mixture transforms into a new material with metallic properties, which is known as cemented carbide.
Although the blade has reached the expected hardness, it still needs further processing before it can be delivered. Before proceeding with the next production step, we carefully check the blade’s size using a coordinate measuring machine.
Only diamond grinding can ensure the carbide inserts have an accurate shape.
The blade is ground according to its geometric angle.
Most grinders come with built-in measuring controls to check and measure the blades at various stages.
In order to achieve the maximum wear resistance required for machining, the cutting edge is treated to obtain the correct shape.
These blades can be brushed with a special brush that has a silicon carbide coating.
Regardless of the processing method used, it is essential to check the final result.
Approximately 90% to 95% of all blades have some sort of coating.
It is crucial to ensure that there are no foreign particles on the blade’s surface to prevent them from adhering to the coating and affecting the tool’s performance.
There are two types of coating methods for blades: Chemical Vapor Deposition (CVD) and Physical Vapor Deposition (PVD). The selection of the appropriate coating method depends on the material and processing of the blade.
The thickness of the coating is determined by the blade’s application, and the coating quality is essential for the durability and lifespan of the blade.
The technical know-how is to apply several thin coatings, such as titanium carbide, aluminum oxide, and titanium nitride, on the surface of cemented carbide. These coatings can significantly enhance the blade’s service life and durability.
If the CVD method is used, the blade is placed in a furnace and exposed to a mixture of chloride and oxide gases, along with methane and hydrogen. When the temperature reaches 1000℃, these gases react with each other and deposit a homogeneous coating only a few thousandths of a millimeter thick onto the surface of the cemented carbide blade.
Some coated blades have a golden surface and are more valuable. Their durability is five times higher than that of uncoated blades.
PVD is a method used to spray the blade at 400℃.
After the blade passes the automatic inspection, we will proceed to mark the material on the blade using a laser, and then pack it.
Additionally, the blade box will be labeled with product information, a serial number, and the date. This serves as a promise to our users that they can expect excellent quality and service.
After packaging, the blades can be delivered to customers.