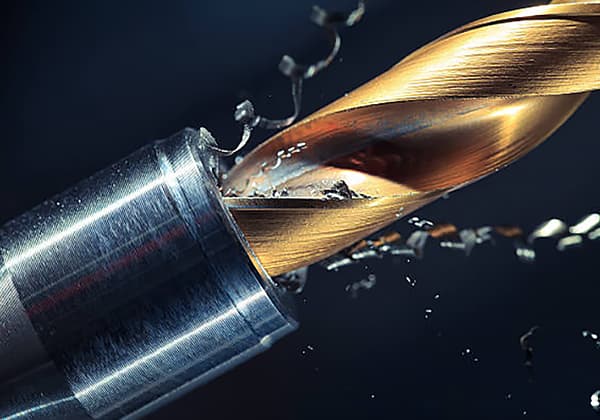
Choosing the right twist drill can be a daunting task. Are you overwhelmed by the options of materials, coatings, and geometries? This guide breaks down the key factors to consider when selecting a twist drill for your specific needs. Learn how different materials like high-speed steel, cobalt, and carbide, as well as coatings and geometric features, affect performance and durability. Equip yourself with the knowledge to make informed decisions and enhance your machining efficiency. Dive into the essentials and master the art of twist drill selection.
Overview
For drilling, there are three basic criteria to consider when selecting a drill: material, coating, and geometric features.
The materials used for drilling can be broadly categorized into three categories: high-speed steel, cobalt high-speed steel, and solid carbide.
High-speed steel has been a popular choice for cutting tools since 1910 and has been in use for over a century. It is currently the most commonly used and economically priced material for cutting tools. These drills can be utilized both in hand drills and in more stable setups such as drilling machines. Additionally, high-speed steel tools can be sharpened multiple times, which is another reason for its enduring popularity. Due to its low cost, high-speed steel is not only used for creating drill bits, but also for making lathe tools.
It boasts superior hardness and red hardness compared to high-speed steel. The elevated hardness results in improved wear resistance, but it also reduces some of the toughness. Similarly to high-speed steels, they can be re-sharpened to extend their lifespan.
Carbide is a composite material comprised of a metal matrix, with tungsten carbide serving as the matrix and other materials acting as the binding agent. The production of carbide involves a complex series of processes, including sintering by hot isostatic pressing.
In terms of hardness, red hardness, wear resistance, etc., carbide outperforms high-speed steel. However, the cost of carbide tools is significantly higher than that of high-speed steel.
Despite the cost, carbide offers benefits in terms of tool life and machining speed when compared to other tool materials. To maintain the quality of carbide tools during repeated grinding, it is necessary to use professional grinding tools.
Coatings can be roughly divided into the following 5 types according to the scope of use:
Uncoated tools are the most cost-effective option and are typically used for machining softer materials such as aluminum alloys and mild steel.
Oxidized coatings offer improved lubrication compared to uncoated tools, as well as enhanced resistance to oxidation and heat. This type of coating can extend the service life of the tool by over 50%.
Titanium nitride is the most commonly used coating material. However, it is not suitable for machining materials with high hardness and high processing temperatures.
Titanium carbonitride is an advancement of titanium nitride and offers improved temperature resistance and wear resistance. It is typically purple or blue in color. This coating has been utilized in Haas workshops for machining cast iron components.
Titanium nitride coating is highly resistant to high temperatures, making it suitable for use in high-temperature cutting environments, such as the processing of high-temperature alloys and steel and stainless steel. However, it is important to note that chemical reactions may occur when processing aluminum-containing materials as the coating contains aluminum elements. To avoid these reactions, it is best to avoid processing materials that contain aluminum.
In general, using cobalt-containing diamond with titanium carbonitride or titanium nitride coatings is a more cost-effective solution.
Geometric features can be divided into the following 3 parts:
The term “double diameter” refers to the ratio of length to diameter. The rigidity of a drill bit improves as the diameter becomes smaller. To increase the span life of the tool and improve rigidity during machining, it’s best to choose a drill bit with a chip length that’s appropriate for chip removal and the shortest possible overhang length. Insufficient blade length can lead to damage to the drill.
The 118° drill point angle is a commonly used angle in machining and is typically used for softer metals like mild steel and aluminum. This angle design typically lacks the self-centering feature, meaning it’s necessary to drill a center hole first.
On the other hand, the 135° drill point angle usually has a self-centering function, eliminating the need to drill a center hole separately, thus saving time.
For most materials, a 30° helix angle is a suitable option. However, for applications that require improved chip removal and enhanced cutting edge strength, a drill with a smaller helix angle may be preferred. When machining difficult materials, such as stainless steel, a drill with a larger helix angle may be more suitable to better transfer torque.