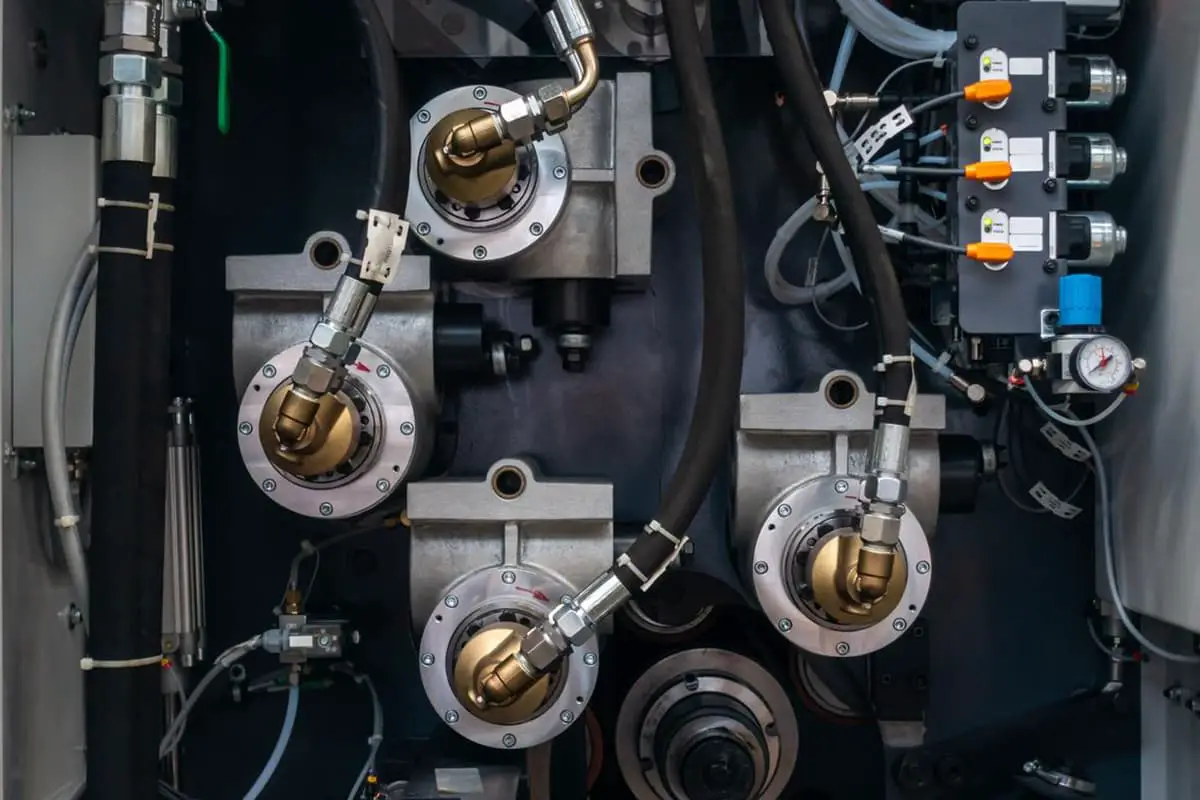
Ever wondered why your hydraulic system is so noisy? This article breaks down the primary sources of hydraulic system noise, such as hydraulic pumps and control valves, and offers practical methods to reduce or eliminate these disturbances. By understanding the causes—like pressure fluctuations, cavitation, and mechanical vibrations—you’ll learn effective strategies to ensure your machinery runs smoothly and quietly. Dive in to uncover the secrets to a quieter, more efficient hydraulic system.
In mechanical processing, the hydraulic system’s noise and vibration can have a direct impact on the accuracy of the processed workpiece.
Noise refers to a vibration wave produced by a specific sound source.
There are numerous causes of noise in hydraulic systems, including voltage fluctuations, mechanical systems, changes in load and flow, cavitation caused by air entering, and trapped oil and fluids.
Variations in power grid voltage, changes in load, pressure fluctuations, and flow pulsations can all contribute to noise and vibration in hydraulic pumps.
Fluctuations in the power grid voltage will result in flow pulsations in the hydraulic pump, leading to fluctuations in the pump outlet and pipeline pressure, resulting in fluid noise caused by changes in flow and pressure.
The accumulation of pressure in trapped areas in the oil system can also generate fluid noise in the hydraulic pump. For example, when the cylinder block of a slanting axial piston pump reaches the top dead center during rotation, the sudden increase in suction pressure to discharge pressure when the liquid pressure in the piston cavity connects to the oil discharge cavity creates a large pressure shock.
Similar pressure shocks occur when the cylinder block is located at the bottom dead center. These pressure shocks are the main source of noise in the hydraulic pump.
To minimize the noise produced by the hydraulic pump, the capacity of the power grid must be sufficient.
When choosing a hydraulic pump, it is important to prioritize low speed while ensuring the necessary power and flow.
An alternative solution is to select a compound pump, which increases the sensitivity of the relief valve and incorporates an unloading circuit to reduce noise.
The control valve’s cavitation creates fluid noise as the oil flow through the valve body generates air flow, resulting in a high flow velocity at the regulator orifice.
As the flow rate changes, the pressure changes as well. When the pressure drops below atmospheric pressure, the air dissolved in the oil separates, producing a large number of air bubbles and causing high-frequency noise.
Additionally, vortices generated by uneven oil flow velocities or interruption of oil flow in the jet state can also cause noise.
To resolve this type of noise, the back pressure on the downstream side of the regulator orifice must be increased to exceed the air separation pressure.
Using multi-stage decompression can prevent cavitation. In general, the ratio of upstream pressure to downstream pressure at the control valve’s orifice should be between 3 to 6.
The pressure fluctuations of the hydraulic pump can cause resonance in the valve, leading to increased noise. The throttle valve, in particular, with its small throttling opening and high flow velocity, is prone to generating vortices.
At times, the valve core may press against the valve seat, causing significant vibration.
In such cases, the throttle valve can be replaced by a smaller control valve or the throttle orifice can be made larger.
When a directional control valve is opened or closed, it can cause vibration and noise due to hydraulic shock. For example, when a solenoid directional control valve is rapidly switched, it creates hydraulic shock that causes violent fluctuations in pipe pressure, which spreads throughout the pipeline. When these fluctuations reach hydraulic pumps and cylinders, it results in vibration and noise in these components.
To minimize this type of vibration and noise, the hydraulic shock must be reduced through proper valve and pipeline settings.
Suction in a hydraulic pump refers to the direct intake of air by the pump or the presence of air in the sucked oil.
This phenomenon not only degrades the oil quality, increases noise, and affects the volumetric efficiency of the hydraulic pump, which is unacceptable in a hydraulic system.
The primary cause of this phenomenon is improper fuel tank and suction pipe settings. To prevent suction, the following measures should be taken:
Errors in the design, manufacture, and installation of a hydraulic system can result in vibration and noise from its components during operation.
To eliminate or reduce this noise, attenuators and isolation techniques can be used: