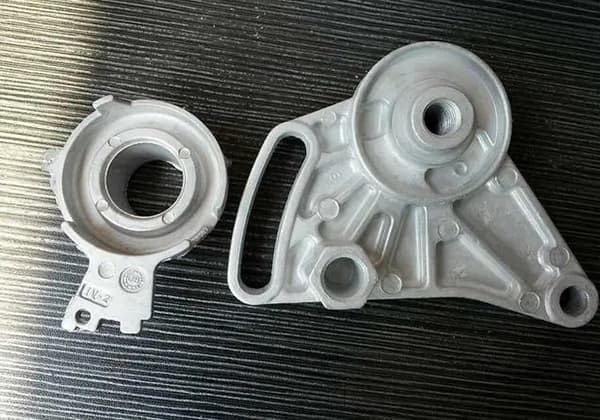
Mengapa beberapa coran gagal sementara yang lain unggul? Jawabannya terletak pada sifat-sifat pengecoran paduan. Artikel ini mengeksplorasi bagaimana faktor-faktor seperti fluiditas, penyusutan, kemampuan oksidasi, dan penyerapan gas memengaruhi kualitas dan kinerja komponen yang dicor. Dengan memahami sifat-sifat ini, Anda akan mendapatkan wawasan untuk memilih material yang tepat dan merancang proses yang memastikan pengecoran berkualitas tinggi. Selami untuk mempelajari bagaimana menguasai elemen-elemen ini dapat meningkatkan proyek pengecoran Anda dan mencegah cacat umum.
Konsep Kinerja Pengecoran Paduan: Performa pengecoran mengacu pada kemampuan suatu paduan untuk dicor dan menghasilkan coran berkualitas tinggi.
Indikator Kinerja Pengecoran Paduan: Kemampuan mengisi (fluiditas), penyusutan, oksidabilitas, segregasi, dan penyerapan gas, dll.
Kualitas kinerja pengecoran paduan secara signifikan berdampak pada proses pengecoran, kualitas pengecoran, dan desain struktur pengecoran.
Oleh karena itu, ketika memilih material untuk komponen casting, material dengan performa casting yang baik harus lebih diutamakan sekaligus memastikan performa operasional.
Namun, dalam produksi aktual, untuk memastikan kinerja operasional, paduan dengan kinerja pengecoran yang lebih buruk sering digunakan.
Dalam kasus ini, perhatian lebih harus diberikan pada desain struktur pengecoran dan sesuai proses pengecoran harus disediakan untuk menghasilkan coran berkualitas tinggi. Oleh karena itu, diperlukan pemahaman yang komprehensif mengenai kinerja pengecoran suatu paduan.
Definisi: Kemampuan paduan cair untuk mengisi cetakan dan menghasilkan pengecoran dengan dimensi yang benar dan kontur yang jelas disebut kemampuan pengisian paduan cair.
Proses pengisian paduan cair adalah tahap pertama pembentukan casting. Tahap ini melibatkan serangkaian perubahan fisik dan kimia, seperti aliran paduan cair dan pertukaran panas antara paduan cair dan cetakan, serta kristalisasi paduan.
Oleh karena itu, kemampuan pengisian tidak hanya bergantung pada kemampuan mengalir dari paduan itu sendiri, tetapi juga dipengaruhi oleh kondisi eksternal seperti sifat cetakan, kondisi penuangan, dan struktur pengecoran.
Dampak pada Kualitas Pengecoran: Jika kemampuan pengisian paduan cair kuat, maka akan lebih mudah untuk mendapatkan coran berdinding tipis dan kompleks. Hal ini menghasilkan lebih sedikit cacat seperti kontur yang tidak jelas, penuangan yang tidak cukup, dan cold shut.
Ini juga memfasilitasi kenaikan dan pengeluaran gas dan non-logam inklusi pada logam cair, mengurangi cacat seperti pori-pori dan inklusi terak. Selain itu, hal ini dapat meningkatkan kemampuan pengumpanan, sehingga mengurangi kecenderungan penyusutan dan porositas.
(1) Fluiditas Paduan
Definisi:
Fluiditas mengacu pada kemampuan paduan cair untuk mengalir. Ini adalah sifat yang melekat pada paduan, tergantung pada jenis paduan, karakteristik kristalisasi, dan sifat fisik lainnya (misalnya, semakin kecil viskositas dan semakin besar kapasitas panas, semakin kecil konduktivitas termal dan semakin besar panas laten kristalisasi, dan semakin kecil tegangan permukaan, semakin baik fluiditasnya).
Metode Pengukuran:
Untuk membandingkan fluiditas paduan yang berbeda, metode pengecoran sampel spiral standar sering digunakan. Panjang sampel fluiditas yang diperoleh di bawah cetakan yang sama (umumnya menggunakan cetakan pasir) dan kondisi pengecoran (seperti suhu penuangan yang sama atau suhu panas berlebih yang sama) dapat mewakili fluiditas paduan yang diuji.
Di antara paduan pengecoran yang umum, besi cor abu-abu dan kuningan silikon memiliki fluiditas terbaik, sedangkan baja tuang memiliki fluiditas terburuk. Untuk paduan yang sama, sampel fluiditas juga dapat digunakan untuk mempelajari dampak berbagai faktor proses pengecoran terhadap kemampuan pengisiannya.
Panjang sampel fluiditas yang diperoleh adalah hasil kali antara waktu dan kecepatan aliran logam cair dari awal penuangan hingga aliran berhenti. Oleh karena itu, faktor apa pun yang memengaruhi kedua faktor ini akan memengaruhi fluiditas (atau kemampuan pengisian).
Komposisi kimiawi paduan menentukan karakteristik kristalisasi, dan karakteristik kristalisasi mendominasi dampak pada fluiditas. Paduan dengan komponen eutektik (seperti paduan besi-karbon dengan fraksi massa karbon 4,3%) membeku pada suhu konstan, permukaan bagian dalam lapisan pemadatan relatif halus, dan hambatan aliran ke logam cair berikutnya kecil.
Selain itu, suhu pemadatan paduan komponen eutektik rendah, yang mudah untuk mendapatkan tingkat panas berlebih yang lebih besar, sehingga fluiditasnya bagus. Selain paduan eutektik dan logam murni, paduan komponen lainnya membeku dalam kisaran suhu tertentu, dan ada zona dua fase cairan dan padat di bagian pengecoran.
Kristal dendritik yang terbentuk pertama kali menciptakan hambatan aliran yang lebih besar untuk logam cair berikutnya, sehingga fluiditasnya menurun. Semakin jauh komposisi paduan menyimpang dari komponen eutektik, semakin besar kisaran suhu pemadatan, dan semakin buruk fluiditasnya. Oleh karena itu, paduan yang dekat dengan komposisi eutektik sering digunakan sebagai bahan pengecoran.
(2) Properti Cetakan
(1) Koefisien penyimpanan panas dari cetakan menunjukkan kemampuan cetakan untuk menyerap dan menyimpan panas dari logam cair.
Semakin besar konduktivitas termal, kapasitas panas spesifik, dan kepadatan bahan cetakan, semakin kuat kemampuan penyimpanan panasnya, semakin kuat kemampuan pendinginan pada logam cair, semakin pendek waktu bagi logam cair untuk mempertahankan aliran, dan semakin buruk kemampuan pengisiannya.
Sebagai contoh, pengecoran cetakan logam lebih mungkin menghasilkan cacat seperti penuangan yang tidak memadai dan penutupan dingin daripada pengecoran cetakan pasir.
② Pemanasan awal suhu cetakan dapat mengurangi perbedaan suhu antara cetakan dan logam cair, mengurangi intensitas pertukaran panas, dan dengan demikian meningkatkan kemampuan pengisian logam cair.
Misalnya, ketika melakukan pengecoran coran paduan aluminium dengan cetakan logam, menaikkan suhu cetakan dari 340°C ke 520°C akan meningkatkan panjang sampel spiral dari 525mm ke 950mm di bawah suhu penuangan yang sama (760°C). Oleh karena itu, pemanasan awal cetakan merupakan salah satu langkah proses yang diperlukan dalam pengecoran cetakan logam.
③ Gas dalam cetakan memiliki kemampuan tertentu untuk mengeluarkan gas, yang dapat membentuk lapisan gas antara logam cair dan cetakan, mengurangi hambatan aliran dan memudahkan pengisian. Tetapi jika emisi gas terlalu besar dan knalpot cetakan tidak lancar, tekanan balik gas yang dihasilkan di rongga cetakan akan menghalangi aliran logam cair.
Oleh karena itu, untuk meningkatkan permeabilitas pasir cetakan (inti), perlu dan sering diterapkan untuk membuka lubang ventilasi pada cetakan.
(3) Kondisi Penuangan
① Suhu Penuangan
Suhu penuangan memiliki dampak yang menentukan pada kemampuan pengisian logam cair. Meningkatkan suhu penuangan menurunkan viskositas paduan dan memperpanjang waktu agar tetap dapat mengalir, sehingga meningkatkan kemampuan pengisian; sebaliknya, kemampuan pengisian akan menurun.
Untuk coran berdinding tipis atau paduan dengan fluiditas yang buruk, meningkatkan suhu penuangan untuk meningkatkan kemampuan pengisian sering digunakan dan relatif nyaman dalam produksi.
Namun, ketika suhu penuangan meningkat, penyerapan gas dan oksidasi paduan menjadi serius, penyusutan total meningkat, dan cacat seperti lubang sembur, lubang susut, dan adhesi pasir dengan mudah terjadi, dan struktur kristal pengecoran menjadi kasar.
Oleh karena itu, pada prinsipnya, suhu penuangan harus dikurangi sebanyak mungkin sekaligus memastikan fluiditas yang memadai.
② Tekanan Pengisian
Semakin besar tekanan pada logam cair pada arah aliran, semakin besar laju aliran dan semakin baik kemampuan pengisiannya. Oleh karena itu, metode seperti meningkatkan ketinggian sariawan atau menerapkan tekanan buatan (seperti pengecoran tekananpengecoran tekanan rendah, dll.) sering digunakan untuk meningkatkan kemampuan pengisian paduan cair.
(4) Struktur Pengecoran
Jika ketebalan dinding pengecoran terlalu kecil, ketebalan dinding berubah tajam atau ada permukaan horizontal yang lebih besar, maka akan menyulitkan pengisian cairan paduan. Oleh karena itu, saat mendesain struktur pengecoran, dinding
ketebalan pengecoran harus lebih besar dari nilai minimum yang diijinkan; beberapa pengecoran perlu mendesain saluran aliran; dan rusuk harus dipasang pada permukaan datar yang besar. Hal ini tidak hanya memfasilitasi pengisian cairan paduan yang lancar tetapi juga mencegah terjadinya cacat inklusi pasir.
Pemisahan
Istilah ini mengacu pada distribusi komposisi kimia yang tidak merata dalam coran. Segregasi dapat membuat sifat coran menjadi tidak merata, dan dalam kasus yang parah, dapat menyebabkan produk cacat.
Pemisahan dapat dibagi menjadi dua kategori: Pemisahan mikro dan Pemisahan makro.
Segregasi mikro:
Segregasi intragranular (juga dikenal sebagai segregasi dendritik) - Ini adalah fenomena di mana bagian yang berbeda dari butiran yang sama memiliki komposisi kimia yang berbeda-beda. Untuk paduan yang membentuk larutan padat, hanya pada kondisi pendinginan yang sangat lambat, atom dapat berdifusi secara memadai untuk mendapatkan butiran yang homogen secara kimiawi selama proses kristalisasi.
Di bawah kondisi pengecoran yang sesungguhnya, laju pemadatan paduan lebih cepat, dan atom-atom tidak memiliki cukup waktu untuk berdifusi sepenuhnya. Akibatnya, butiran yang tumbuh secara dendritik, pasti memiliki komposisi kimia yang tidak merata.
Untuk menghilangkan segregasi intragranular, pengecoran dapat dipanaskan kembali ke suhu tinggi dan ditahan dalam waktu yang lama untuk memungkinkan difusi atom yang cukup. Metode perlakuan panas ini dikenal sebagai anil difusi.
Pemisahan makro:
Pemisahan Densitas (sebelumnya dikenal sebagai pemisahan gravitasi) - Ini adalah fenomena di mana bagian atas dan bawah casting memiliki komposisi kimia yang tidak merata. Ketika kepadatan elemen paduan berbeda secara signifikan, elemen dengan kepadatan yang lebih rendah cenderung terakumulasi di bagian atas setelah pengecoran mengeras sepenuhnya, sedangkan elemen dengan kepadatan yang lebih tinggi cenderung terakumulasi di bagian bawah.
Untuk mencegah pemisahan densitas, logam cair harus diaduk secara menyeluruh atau didinginkan dengan cepat selama penuangan untuk mencegah pemisahan elemen dengan densitas yang berbeda.
Ada banyak jenis pemisahan makro, termasuk pemisahan positif, pemisahan negatif, pemisahan berbentuk V, dan pemisahan pita, di samping pemisahan densitas.
Penyerapan gas dari paduan - Istilah ini mengacu pada sifat paduan untuk menyerap gas selama peleburan dan penuangan.
Penyerapan gas pada paduan meningkat seiring dengan suhu. Gas jauh lebih mudah larut dalam paduan cair daripada dalam keadaan padat. Semakin tinggi panas super paduan, semakin banyak gas yang dikandungnya. Keberadaan gas dalam coran memiliki tiga bentuk: larutan padat, senyawa, dan porositas.
Berdasarkan sumber gas dalam paduan, porositas dapat dibagi ke dalam tiga kategori:
a. Porositas eksudasi
Ketika gas yang terlarut dalam cairan paduan memancar selama proses pemadatan karena penurunan kelarutan gas, dan tidak dapat dikeluarkan tepat waktu, porositas yang terbentuk dalam coran disebut porositas eksudasi.
Porositas eksudasi paling sering terjadi pada paduan aluminiumdengan diameter yang sering kali kurang dari 1mm. Hal ini tidak hanya memengaruhi sifat mekanis paduan, tetapi juga sangat memengaruhi kekedapan udara pada pengecoran.
b. Porositas invasif
Porositas invasif mengacu pada pori-pori yang dibentuk oleh gas yang berkumpul pada lapisan permukaan cetakan pasir yang menyerang cairan paduan.
c. Porositas reaktif
Porositas reaktif mengacu pada pori-pori yang terbentuk pada coran oleh gas yang dihasilkan melalui reaksi kimia antara paduan cair yang dituangkan ke dalam cetakan dengan kelembaban, karat, dll. pada material cetakan, penyangga inti, pendingin, atau terak.
Porositas reaktif hadir dalam berbagai jenis dan bentuk. Sebagai contoh, pori-pori yang tercipta dari reaksi kimia antara cairan paduan dan antarmuka cetakan pasir biasanya terdistribusi 1-2 mm di bawah permukaan pengecoran. Setelah permukaan dikerjakan atau dibersihkan, banyak lubang kecil yang terlihat, sehingga disebut pori-pori di bawah permukaan.
Pori-pori mengganggu kontinuitas paduan, mengurangi area penahan beban yang efektif, dan menyebabkan konsentrasi tegangan di sekitar pori-pori, sehingga mengurangi sifat mekanik coran, terutama ketangguhan impak dan kekuatan kelelahan. Pori-pori yang tersebar juga dapat mendorong pembentukan mikroporositas, mengurangi kekedapan udara pada casting.
a. Mengurangi emisi gas dari pasir cetakan (pasir inti) dan meningkatkan kapasitas pembuangan cetakan.
b. Mengontrol suhu cairan paduan, mengurangi panas berlebih yang tidak perlu, dan mengurangi kandungan gas asli cairan paduan.
c. Berikan tekanan untuk memadatkan paduan dan mencegah keluarnya gas. Perubahan tekanan secara langsung memengaruhi eksudasi gas. Sebagai contoh, jika paduan aluminium cair dikristalisasi dalam ruang bertekanan 405-608 kPa (4-6 atmosfer), pengecoran bebas pori dapat diperoleh.
d. Selama peleburan dan penuangan, cobalah untuk mengurangi kemungkinan kontak cairan paduan dengan gas. Misalnya, gunakan penutup untuk melindungi permukaan cairan paduan atau gunakan teknologi peleburan vakum.
e. Menghilangkan gas pada cairan paduan. Misalnya, memasukkan gas klorin ke dalam cairan paduan aluminium. Kapan tidak terlarut gelembung gas klorin naik, atom hidrogen yang dilarutkan dalam cairan paduan aluminium terus berdifusi ke dalam gelembung gas klorin dan dikeluarkan dari cairan paduan.
f. Permukaan pendingin, penyangga inti, dll. tidak boleh berkarat atau berminyak, dan harus dijaga agar tetap kering, dll.
(1) Definisi Pemadatan dan Penyusutan
Pemadatan adalah proses transisi suatu zat dari bentuk cair ke bentuk padat.
Penyusutan mengacu pada pengurangan volume yang terjadi pada coran selama proses pemadatan dan pendinginan.
(2) Dampak pada Kualitas Pengecoran
Jika pemadatan dan penyusutan tidak dikontrol dengan baik selama proses pendinginan logam cair yang dituangkan ke dalam cetakan, maka pengecoran dapat menimbulkan cacat seperti rongga penyusutan, porositas penyusutan, tekanan pengecoran, deformasi, dan retakan.
(1) Metode Pemadatan Pengecoran
Selama pemadatan, ada tiga area yang biasanya ada pada penampang pengecoran: area fase padat, area pemadatan, dan area fase cair. Koeksistensi fase cair dan padat di area solidifikasi secara signifikan memengaruhi kualitas pengecoran.
"Metode solidifikasi" pengecoran dikategorikan berdasarkan luasnya area solidifikasi ini, ke dalam tiga jenis berikut ini:
(1) Pemadatan lapis demi lapis
Logam murni atau paduan eutektik membeku tanpa fase cair dan padat yang berdampingan di area pemadatan, seperti yang ditunjukkan pada Gambar 2(a). Dengan demikian, batas yang jelas (bagian depan pemadatan) memisahkan lapisan padat luar dan lapisan cair dalam pada penampang melintang.
Saat suhu turun, lapisan padat menebal, dan lapisan cair berkurang sampai bagian depan pemadatan mencapai bagian tengah. Metode pemadatan ini disebut pemadatan lapis demi lapis.
② Pemadatan seperti pasta
Jika kisaran suhu kristalisasi suatu paduan luas, dan kurva distribusi suhu di dalam pengecoran relatif datar, tidak akan ada lapisan padat pada permukaan pengecoran selama periode pemadatan tertentu.
Sebaliknya, area pemadatan di mana fase cair dan padat hidup berdampingan meluas ke seluruh penampang, seperti yang ditunjukkan pada Gambar 1(C). Metode pemadatan ini mirip dengan pemadatan semen, yang pada awalnya berbentuk seperti pasta sebelum dipadatkan, dan oleh karena itu disebut pemadatan seperti pasta.
③ Pemadatan Menengah
Mayoritas paduan mengeras menggunakan metode di antara kedua metode di atas, yang disebut sebagai pemadatan menengah.
Hubungan antara Pemadatan Pengecoran dan Cacat Pengecoran:
Secara umum, pemadatan lapis demi lapis memfasilitasi pengisian paduan dan kompensasi penyusutan, mencegah rongga penyusutan dan porositas. Mencapai coran struktural yang padat dapat menjadi tantangan selama pemadatan seperti pasta.
(2) Faktor Utama yang Mempengaruhi Metode Pemadatan Pengecoran
(1) Kisaran Suhu Kristalisasi Paduan
Kisaran suhu kristalisasi yang lebih kecil dari suatu paduan menghasilkan area pemadatan yang lebih sempit dan kecenderungan ke arah pemadatan lapis demi lapis. Sebagai contoh, selama pengecoran pasir, baja karbon rendah membeku lapis demi lapis, sedangkan baja karbon tinggi, dengan rentang suhu kristalisasi yang luas, membeku seperti pasta.
② Gradien Suhu dari Penampang Pengecoran
Dengan kisaran suhu kristalisasi tertentu dari suatu paduan, lebar area pemadatan bergantung pada gradien suhu penampang pengecoran, seperti yang ditunjukkan pada Gambar 2 (T1 → T2). Jika gradien temperatur pengecoran meningkat, maka area pemadatan yang sesuai akan menyempit.
Gradien suhu pengecoran terutama bergantung pada:
a. Properti Paduan: Semakin rendah suhu pemadatan suatu paduan, semakin tinggi konduktivitas termalnya, dan semakin besar panas laten kristalisasinya, semakin baik kemampuannya untuk menyamakan suhu internal, sehingga menghasilkan gradien suhu yang lebih kecil (seperti pada sebagian besar paduan aluminium).
b. Kapasitas Retensi Panas dari Cetakan: Koefisien retensi panas yang lebih tinggi dari cetakan meningkatkan kemampuan pendinginan yang cepat, yang mengarah ke gradien suhu pengecoran yang lebih besar.
c. Suhu Penuangan: Suhu penuangan yang lebih tinggi memasukkan lebih banyak panas ke dalam cetakan, mengurangi gradien suhu pengecoran.
d. Ketebalan Dinding Pengecoran: Dinding pengecoran yang lebih tebal menghasilkan gradien suhu yang lebih kecil.
Dari diskusi di atas, dapat disimpulkan bahwa paduan yang cenderung ke arah pemadatan lapis demi lapis (seperti besi tuang kelabu, paduan aluminium-silikon, dll.) lebih cocok untuk pengecoran dan harus digunakan jika memungkinkan.
Ketika paduan yang cenderung ke arah pemadatan seperti pasta (seperti perunggu timah, paduan tembaga aluminium, besi ulet, dll.) harus digunakan, langkah-langkah proses yang tepat (misalnya, pengecoran cetakan logam) harus dipertimbangkan untuk mengurangi area pemadatannya.
(1) Prinsip dan Proses Penyusutan Paduan
Struktur paduan cair terdiri atas gugusan atom dan "rongga". Atom-atom di dalam gugus tersusun secara teratur, tetapi jarak antar atom lebih besar daripada dalam keadaan padat. Ketika paduan cair dituangkan ke dalam cetakan, suhu terus turun, kekosongan berkurang, jarak atom memendek, dan volume cairan paduan berkurang.
Sewaktu cairan paduan membeku, rongga-rongga menghilang, dan jarak atom semakin memendek. Selama proses pendinginan ke suhu kamar setelah pemadatan, jarak atom terus berkurang.
Penyusutan paduan dari suhu penuangan ke suhu kamar mengalami tiga tahap berikut ini:
①Penyusutan Cairan
Ini adalah penyusutan paduan dari suhu penuangan ke awal pemadatan (suhu garis liquidus), sementara paduan dalam keadaan cair. Hal ini mengakibatkan penurunan level cairan di dalam rongga cetakan.
② Penyusutan Pemadatan
Ini adalah penyusutan paduan dari awal pemadatan hingga akhir pemadatan. Umumnya, penyusutan solidifikasi masih bermanifestasi sebagai penurunan level cairan.
Penyusutan Kondisi Padat
Ini adalah penyusutan paduan dari akhir pemadatan ke suhu kamar, ketika paduan dalam keadaan padat. Penyusutan pada tahap ini ditandai dengan penurunan dimensi linier dari pengecoran.
Penyusutan cairan dan pemadatan dari suatu paduan adalah penyebab utama rongga penyusutan dan porositas dalam pengecoran, sedangkan penyusutan solid-state adalah penyebab mendasar dari tegangan pengecoran, deformasi, dan retak, dan secara langsung mempengaruhi akurasi dimensi pengecoran.
(2) Faktor Utama yang Mempengaruhi Penyusutan Paduan
①Komposisi Kimia Paduan
Paduan yang berbeda memiliki tingkat penyusutan yang berbeda. Di antara paduan yang umum digunakan, baja tuang memiliki tingkat penyusutan tertinggi, sedangkan besi tuang kelabu memiliki tingkat penyusutan terendah. Alasan besi tuang kelabu memiliki tingkat penyusutan yang sangat kecil adalah karena sebagian besar karbon di dalamnya terdapat dalam bentuk grafit, yang memiliki volume spesifik yang besar. Pemuaian volume yang dihasilkan oleh pengendapan grafit selama proses kristalisasi mengimbangi sebagian penyusutan paduan.
Tabel 1 Tingkat penyusutan dari berbagai paduan
Jenis paduan | Fraksi massa karbon | Suhu penuangan /℃ | Penyusutan cairan | Penyusutan koagulasi | Penyusutan keadaan padat | Total penyusutan volume |
Baja karbon tuang | 0.35% | 1610 | 1.6% | 3% | 7.8% | 12.46% |
Besi cor putih | 3.00% | 1400 | 2.4% | 4.2% | 5.4~6.3% | 12-12.9% |
Besi tuang abu-abu | 3.50% | 1400 | 3.5% | 0.1% | 3.3~4.2% | 6.9~7.8% |
② Suhu Penuangan
Semakin tinggi suhu penuangan, semakin besar penyusutan cairan paduan.
Kondisi Cetakan dan Struktur Pengecoran
Penyusutan aktual dari pengecoran berbeda dengan penyusutan bebas dari paduan. Hal ini terhalang oleh cetakan dan inti; dan, karena pengecoran memiliki struktur yang rumit dan ketebalan dinding yang tidak rata, kendala bersama dari berbagai bagian selama pendinginan juga menghambat penyusutan.
Porositas dan penyusutan didefinisikan sebagai lubang yang terbentuk pada bagian akhir yang dipadatkan dari pengecoran jika penyusutan cairan dan penyusutan pemadatan paduan tidak dikompensasi oleh paduan cairan. Rongga yang lebih besar dan terkonsentrasi disebut sebagai porositas, sedangkan rongga yang kecil dan tersebar disebut sebagai penyusutan.
Bahaya - Porositas dan penyusutan mengurangi area penahan beban efektif dari pengecoran, menyebabkan konsentrasi tegangan dan dengan demikian mengurangi sifat mekanis. Untuk komponen yang membutuhkan kedap udara, porositas dan penyusutan dapat menyebabkan kebocoran dan secara serius memengaruhi kedap udara. Oleh karena itu, porositas dan penyusutan merupakan salah satu cacat pengecoran yang utama.
① Proses pembentukan porositas
Ketika paduan cair dituangkan ke dalam cetakan silinder, suhu paduan cair secara bertahap menurun karena efek pendinginan cetakan. Penyusutan cairannya terus berlanjut, tetapi apabila sariawan tidak dipadatkan, rongga cetakan selalu terisi (lihat Gambar 3(a)).
Saat suhu turun, permukaan pengecoran pertama-tama membeku menjadi cangkang keras, sekaligus menutup sariawan (lihat Gambar 3(b)). Setelah pendinginan lebih lanjut, logam cair di dalam cangkang terus menyusut, mengkompensasi penyusutan pemadatan yang terjadi ketika cangkang terbentuk.
Karena penyusutan cairan dan penyusutan pemadatan jauh lebih besar daripada penyusutan padat cangkang, level cairan turun dan terlepas dari bagian atas cangkang (lihat Gambar 3(c)). Hal ini terus berlanjut, dengan cangkang yang menebal dan level cairan yang turun.
Setelah logam benar-benar dipadatkan, porositas berbentuk lancip terbentuk di bagian atas pengecoran (lihat Gambar 3(d)). Ketika pengecoran terus mendingin hingga mencapai suhu kamar, volumenya sedikit menyusut, mengurangi volume porositas (lihat Gambar 3(e)). Jika riser dipasang di bagian atas pengecoran, porositas akan berpindah ke riser.
② Lokasi porositas
Umumnya, hal ini muncul di area pengecoran yang terakhir dipadatkan, seperti bagian atas atau tengah pengecoran, di dekat sariawan, atau di mana dinding pengecoran lebih tebal.
③ Pembentukan penyusutan
Hal ini disebabkan oleh kompensasi yang tidak mencukupi untuk penyusutan pada area pemadatan terakhir dari pengecoran, atau karena paduan membeku dalam keadaan seperti pasta dan area cairan kecil yang dipisahkan oleh kristal dendritik tidak menerima kompensasi penyusutan.
Penyusutan dibagi menjadi penyusutan makro dan penyusutan mikro. Penyusutan makro adalah lubang-lubang kecil yang terlihat dengan mata telanjang atau di bawah kaca pembesar, sering kali terdistribusi pada sumbu tengah pengecoran atau di bawah porositas (Gambar 4). Penyusutan mikro adalah lubang-lubang kecil yang terdistribusi di antara butiran, hanya dapat dilihat di bawah mikroskop.
Jenis penyusutan ini lebih luas, kadang-kadang menutupi seluruh bagian. Penyusutan mikro sulit untuk dihindari sepenuhnya, dan biasanya tidak diperlakukan sebagai cacat untuk coran umum. Untuk coran dengan persyaratan kedap udara, sifat mekanik, sifat fisik, atau sifat kimia yang tinggi, upaya harus dilakukan untuk menguranginya.
Paduan pengecoran yang berbeda memiliki kecenderungan yang berbeda untuk membentuk porositas dan penyusutan. Paduan pemadatan berlapis (logam murni, paduan eutektik, atau paduan dengan kisaran suhu kristalisasi yang sempit) memiliki kecenderungan porositas yang tinggi dan kecenderungan penyusutan yang rendah.
Paduan pemadatan yang pucat, meskipun tidak terlalu rentan terhadap porositas, namun sangat rentan terhadap penyusutan. Karena beberapa langkah proses dapat mengontrol mode pemadatan pengecoran, porositas dan penyusutan dapat saling dikonversi dalam kisaran tertentu.
① Menerapkan "Pemantapan Arah"
Untuk mencegah rongga penyusutan dan porositas, pengecoran harus dipadatkan sesuai dengan prinsip "pemadatan terarah". Prinsip ini mengacu pada penggunaan berbagai langkah teknis untuk menetapkan gradien suhu yang meningkat dari bagian pengecoran yang terjauh dari gerbang ke gerbang itu sendiri.
Pemadatan dimulai dari bagian terjauh dari gerbang, secara bertahap berkembang menuju gerbang secara berurutan, dengan gerbang itu sendiri menjadi yang terakhir untuk dipadatkan. Proses ini memfasilitasi penyusutan solidifikasi yang efektif, memindahkan rongga penyusutan ke gerbang dan menghasilkan coran yang lebih padat.
Oleh karena itu, gerbang harus ditempatkan pada bagian yang paling tebal dan paling tinggi dari pengecoran, dengan ukuran yang cukup besar. Jika memungkinkan, sariawan harus ditempatkan di gerbang, sehingga logam cair dapat mengalir terlebih dahulu melalui gerbang.
Pada saat yang sama, pendingin dapat ditempatkan pada beberapa bagian pengecoran yang sangat tebal (seperti yang ditunjukkan pada Gambar 5) untuk mempercepat pendinginan dan memaksimalkan efek penyusutan solidifikasi gerbang.
Kelemahan dari pemadatan terarah adalah perbedaan suhu yang signifikan di seluruh pengecoran, yang menyebabkan tekanan termal yang substansial dan potensi deformasi atau keretakan pada pengecoran.
Selain itu, penyertaan gerbang meningkatkan konsumsi logam dan biaya pembersihan. Pemadatan terarah biasanya digunakan untuk paduan dengan tingkat penyusutan yang tinggi dan rentang suhu pemadatan yang sempit (seperti baja tuang, besi tuang yang dapat ditempa, dan kuningan), serta pengecoran dengan perbedaan yang signifikan pada ketebalan dinding dan persyaratan yang tinggi untuk kekedapan udara.
② Kompensasi Tekanan
Ini melibatkan penempatan cetakan dalam ruang tekanan. Setelah pengecoran, ruang tekanan dengan cepat ditutup sehingga pengecoran mengeras di bawah tekanan, menghilangkan porositas dan rongga penyusutan. Metode ini juga dikenal sebagai "pengecoran panci bertekanan."
③ Menggunakan Teknologi Impregnasi untuk Mencegah Kebocoran Akibat Rongga Penyusutan dan Porositas
Hal ini melibatkan penyusupan zat peresapan seperti gel ke dalam rongga-rongga pengecoran, kemudian mengeraskan zat peresapan dan mengintegrasikannya dengan dinding rongga pengecoran untuk mencapai anti bocor.
Penentuan Lokasi Rongga Susut dan Porositas
Untuk mencegah rongga penyusutan dan porositas, sangat penting untuk secara akurat menilai lokasinya dalam pengecoran saat mengembangkan proses pengecoran, sehingga tindakan teknis yang diperlukan dapat diambil. Lokasi rongga penyusutan dan porositas umumnya ditentukan dengan menggunakan metode garis isotermal atau metode lingkaran bertulis.
① Metode Garis Isotermal
Metode ini melibatkan penghubungan titik-titik pada casting yang mencapai suhu pemadatan secara bersamaan untuk membentuk garis isotermal berdasarkan kondisi pembuangan panas dari berbagai bagian casting. Hal ini dilakukan lapis demi lapis hingga garis isotermal pada penampang tersempit saling bersentuhan.
Dengan cara ini, bagian pemadatan terakhir dari pengecoran, yaitu lokasi rongga penyusutan dan porositas, dapat ditentukan. Gambar 6(a) menunjukkan posisi rongga penyusutan yang ditentukan dengan metode garis isotermal, dan Gambar 6(b) menunjukkan posisi rongga penyusutan yang sebenarnya pada pengecoran, yang pada dasarnya konsisten.
Metode Lingkaran Bertuliskan
Metode ini sering digunakan untuk menentukan lokasi rongga penyusutan pada dinding yang berpotongan pada pengecoran, seperti yang ditunjukkan pada Gambar 7(a). Pada bagian dengan diameter lingkaran bertuliskan terbesar (disebut sebagai "titik panas"), di mana lebih banyak logam terakumulasi, pemadatan biasanya terjadi paling akhir, yang dengan mudah menyebabkan rongga penyusutan dan porositas (Gambar 7(b)).
Definisi:
Tegangan yang disebabkan oleh penyusutan solid-state yang terhambat pada pengecoran disebut sebagai tegangan pengecoran. Tegangan pengecoran dapat dibagi menjadi tiga jenis:
Tekanan Mekanis:
Jenis tegangan ini bersifat sementara, yang diakibatkan oleh hambatan mekanis dari penyusutan pengecoran. Segera setelah halangan mekanis dihilangkan, tegangan menghilang. Penyebab halangan mekanis termasuk kekuatan suhu tinggi dari pasir cetak (inti), kemampuan kolaps yang buruk, dan halangan oleh tali pengikat kotak pasir dan cetakan inti.
Tekanan Panas:
Ini stres internalyang dikenal sebagai tegangan termal, dihasilkan karena kecepatan pendinginan yang berbeda-beda dari berbagai bagian pengecoran, menyebabkan penyusutan yang tidak konsisten dalam periode yang sama, dan terdapat kendala di antara bagian-bagian ini. Tekanan termal ini tetap ada bahkan setelah pengecoran mendingin hingga mencapai suhu kamar, oleh karena itu disebut juga tegangan sisa.
Stres perubahan fase:
Perubahan volume yang disebabkan oleh perubahan fasa pada paduan di bawah kondisi elastis dapat menciptakan tegangan perubahan fasa. Jika bagian yang berbeda dari pengecoran mendingin dengan kecepatan yang berbeda, perubahan fasa tidak terjadi secara bersamaan, yang menyebabkan tegangan ini.
Tegangan pengecoran adalah jumlah aljabar dari tegangan termal, tegangan mekanis, dan tegangan perubahan fase. Tergantung pada situasinya, ketiga tegangan ini dapat saling tumpang tindih atau saling meniadakan. Adanya tegangan pengecoran dapat menimbulkan serangkaian efek yang merugikan, seperti menyebabkan deformasi dan retakan pada pengecoran, mengurangi daya dukung beban, dan mempengaruhi akurasi pemesinan.
① Aspek teknologi:
a. Pengecoran harus dipadatkan sesuai dengan prinsip "pemadatan simultan". Untuk mencapai hal ini, sistem gating harus ditempatkan di area dinding tipis dan dinginkan di area dinding tebal. Hal ini memastikan bahwa perbedaan suhu di antara berbagai bagian pengecoran diminimalkan dan pemadatan simultan terjadi, sehingga mengurangi tekanan termal ke tingkat terendah. Perlu dicatat bahwa area tengah pengecoran sering menunjukkan porositas penyusutan dan pemadatan yang tidak memadai saat ini.
b. Dengan meningkatkan kemampuan pelipatan cetakan dan inti, membuang pasir dan mengemas kotak sedini mungkin untuk menghilangkan rintangan mekanis, dan secara perlahan mendinginkan pengecoran di lubang pengawetan panas juga dapat mengurangi tekanan pengecoran.
② Desain struktural:
Upayakan struktur yang sederhana dengan ketebalan dinding yang seragam dan transisi bertahap dari dinding tipis ke dinding tebal, untuk mengurangi perbedaan suhu dan memungkinkan setiap bagian menyusut dengan lebih leluasa.
③ Tekanan termal pada coran dapat dihilangkan dengan menggunakan metode seperti penuaan alami dan penuaan buatan.
① Deformasi:
Coran yang mengalami tegangan berada dalam kondisi tidak stabil dan secara spontan mengurangi tegangan melalui deformasi untuk mencapai kondisi stabil. Jelaslah bahwa hanya jika bagian yang diregangkan secara elastis berkontraksi dan bagian yang dikompresi secara elastis memanjang, maka tegangan pada pengecoran berpotensi berkurang atau dihilangkan.
Arah deformasi coran berbentuk T ditunjukkan oleh garis putus-putus pada Gambar 9(a). Hal ini karena setelah coran berbentuk T mendingin, dinding tebal berada di bawah tegangan dan dinding tipis berada di bawah kompresi, mirip dengan dua pegas dengan panjang yang berbeda (Gambar 9(b)). Pegas yang lebih pendek di atas diregangkan dan pegas yang lebih panjang di bawah dikompresi untuk mempertahankan panjang yang sama (Gambar 9(c)).
Namun demikian, kombinasi pegas ini tidak stabil dan berusaha untuk mengembalikan keadaan keseimbangan semula. Oleh karena itu, deformasi tekukan yang mirip dengan situasi di atas muncul (Gambar 9(d)).
Bahaya, Penanggulangan:
Langkah mendasar untuk mencegah deformasi pengecoran adalah dengan mengurangi tegangan pengecoran internal. Misalnya, selama fase desain, upayakan agar ketebalan dinding pengecoran seragam. Saat melakukan proses pengecoran, cobalah untuk mendinginkan semua bagian pengecoran secara bersamaan, dan tingkatkan daya runtuh pasir cetakan (inti).
Ketika membuat pola, metode deformasi terbalik dapat digunakan, yaitu pola dibuat dalam bentuk yang berlawanan dengan deformasi pengecoran terlebih dahulu untuk mengkompensasi deformasi pengecoran. Basis alat mesin yang ditunjukkan pada Gambar 10 memiliki deformasi lentur karena rel yang tebal dan dinding samping yang tipis setelah pengecoran. Jika pola dibuat dengan kelengkungan berlawanan yang diwakili oleh garis berujung ganda, maka rel akan lurus setelah pengecoran.
Perlu diperhatikan bahwa setelah pengecoran mengalami deformasi, seringkali hanya dapat mengurangi tetapi tidak dapat sepenuhnya menghilangkan tegangan pengecoran. Setelah pemesinan, ketidakseimbangan tegangan pada bagian tersebut menyebabkan deformasi lebih lanjut, sehingga mempengaruhi akurasi pemesinan. Oleh karena itu, untuk pengecoran yang penting, anil pelepas tegangan harus dilakukan sebelum pemesinan.
② Retak:
Ketika tegangan pengecoran melebihi batas kekuatan material pada saat itu, retakan dapat terjadi pada pengecoran.
Retak dapat dibagi menjadi retak panas dan retakan dingin.
Ini terbentuk pada suhu tinggi dan merupakan salah satu cacat pengecoran yang paling umum dalam produksi coran baja, besi tuang yang dapat dilebur, dan beberapa coran paduan ringan. Ciri-cirinya adalah: bentuk retakan berliku-liku dan tidak beraturan, permukaan retakan tampak teroksidasi (permukaan retakan pengecoran baja tampak hampir hitam, sedangkan paduan aluminium berwarna abu-abu tua), dan retakan melewati batas butir. Retakan panas sering muncul di bagian coran yang dipadatkan terakhir atau di permukaan di mana konsentrasi tegangan cenderung terjadi.
Retak Dingin:
Ini terbentuk pada suhu rendah. Paduan dengan plastisitas yang buruk, kerapuhan yang tinggi, dan konduktivitas termal yang rendah, seperti besi tuang putih, baja karbon tinggidan beberapa baja paduan, rentan terhadap retak dingin. Ciri-cirinya adalah: bentuk retakan berupa garis lurus kontinu atau kurva halus, sering kali melewati butiran. Permukaan retakan bersih, dengan kilau logam atau sedikit warna oksidasi. Retak dingin sering terjadi pada bagian tarik dari pengecoran, terutama pada area konsentrasi tegangan, seperti sudut tajam internal, rongga penyusutan, dan dekat inklusi non-logam.
Bahaya, Penanggulangan:
Faktor-faktor yang mengurangi tekanan pengecoran atau mengurangi kerapuhan paduan (seperti mengurangi kandungan sulfur dan fosfor dalam baja) memiliki efek positif dalam mencegah keretakan.