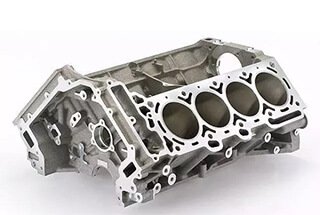
Pernahkah Anda bertanya-tanya, bagaimana komponen logam yang rumit dibuat dengan presisi tinggi? Masuki dunia die casting, di mana logam cair bertekanan tinggi disuntikkan ke dalam cetakan yang tahan lama, menciptakan segala sesuatu mulai dari suku cadang mobil hingga gadget yang rumit. Proses ini, yang dikenal dengan efisiensi dan akurasinya, memungkinkan produksi massal komponen logam berukuran kecil hingga menengah. Dalam artikel ini, temukan langkah-langkah penting, manfaat, dan inovasi dalam die casting, dan pelajari bagaimana teknik yang menarik ini membentuk benda-benda sehari-hari dengan detail dan konsistensi yang luar biasa.
Die casting adalah logam proses pengecoranyang ditandai dengan memberikan tekanan tinggi pada logam yang meleleh dengan menggunakan rongga bagian dalam cetakan.
Cetakan biasanya terbuat dari paduan dengan kekuatan yang lebih tinggi, yang agak mirip dengan cetakan injeksi.
Sebagian besar die casting bebas dari besi, seperti seng, tembaga, aluminium, magnesium, timbal, timah, paduan timah, dan paduannya.
Tergantung pada jenis dadu-casting, mesin die-casting ruang dingin atau mesin die-casting ruang panas perlu digunakan.
Biaya peralatan pengecoran dan cetakan tinggi, sehingga proses die casting umumnya hanya digunakan untuk produksi massal produk dalam jumlah besar.
Memproduksi komponen die-casting relatif mudah, yang umumnya hanya memerlukan empat langkah utama, dan kenaikan biaya tunggal sangat rendah.
Die casting sangat cocok untuk memproduksi sejumlah besar coran berukuran kecil dan menengah, sehingga die casting adalah salah satu yang paling banyak digunakan berbagai proses pengecoran.
Dibandingkan dengan teknologi pengecoran lainnya, permukaan die casting lebih halus dan memiliki konsistensi dimensi yang lebih tinggi.
Berdasarkan proses die-casting tradisional, lahirlah beberapa proses yang lebih baik, termasuk proses die-casting tanpa lubang yang mengurangi cacat pengecoran dan menghilangkan lubang udara.
Hal ini terutama digunakan untuk proses injeksi langsung dalam memproses seng, yang dapat mengurangi limbah dan meningkatkan hasil.
Ada juga teknologi die-casting baru seperti teknologi die-casting berkecepatan tinggi dan padat serta die-casting semi-padat yang ditemukan oleh dinamika umum.
Die casting adalah sejenis metode pengecoran presisi yang menggunakan tekanan tinggi untuk melelehkan logam secara paksa ke dalam cetakan logam yang kompleks.
Pada tahun 1964, Asosiasi Pengecoran Die Jepang mendefinisikan die casting sebagai "metode pengecoran dengan menekan paduan cair ke dalam cetakan pengecoran presisi pada suhu tinggi dan menghasilkan permukaan pengecoran yang presisi dan sangat baik dalam jumlah besar dalam waktu singkat".
Die casting disebut die casting di Amerika Serikat, pressure die casting di Inggris, dan istilah Jepang, die casting, paling dikenal oleh operator domestik biasa.
Coran yang dihasilkan oleh metode die casting disebut die casting.
Kekuatan tarik material ini hampir dua kali lipat lebih tinggi daripada paduan cor biasa, yang memiliki signifikansi lebih positif untuk velg mobil paduan aluminium, rangka, dan komponen lain yang diharapkan dapat diproduksi dengan bahan yang lebih kuat dan tahan benturan.
Pada tahun 1838, untuk membuat cetakan cetak tipe bergerak, orang menemukan peralatan die-casting. Paten pertama yang terkait dengan die casting dikeluarkan pada tahun 1849.
Ini adalah mesin manual kecil yang digunakan untuk memproduksi jenis pencetakan.
Pada tahun 1885 Otto Mergenthaler menemukan mesin penyusunan huruf Linotype, yang dapat mencetak seluruh baris teks ke dalam satu jenis huruf.
Ini membawa inovasi yang belum pernah terjadi sebelumnya ke dunia pencetakan.
Setelah industrialisasi industri percetakan berskala besar, jenis cetak tangan tradisional telah digantikan oleh die casting.
Sekitar tahun 1900, pengenalan penyusunan huruf ke pasar semakin meningkatkan teknologi otomasi industri percetakan, sehingga terkadang lebih dari sepuluh mesin cetak dapat dilihat di koran.
Dengan pertumbuhan produk konsumen yang terus menerus, penemuan Otto telah mendapatkan lebih banyak aplikasi.
Orang dapat menggunakan die-casting untuk memproduksi suku cadang dan produk dalam jumlah besar.
Pada tahun 1966, General Dynamics menemukan cetakan presisi proses pengecoranyang kadang-kadang disebut die casting pukulan ganda.
Proses die casting tradisional terutama terdiri dari empat langkah, atau die casting bertekanan tinggi.
Keempat langkah ini meliputi persiapan cetakan, pengisian, injeksi, dan Desanding, yang juga merupakan dasar dari berbagai proses die casting yang lebih baik.
Dalam proses persiapan, pelumas perlu disemprotkan ke dalam rongga cetakan.
Selain membantu mengontrol suhu cetakan, pelumas juga dapat membantu demoulding pengecoran.
Kemudian cetakan dapat ditutup dan logam cair dapat diinjeksikan ke dalam cetakan dengan tekanan tinggi, yaitu sekitar 10 hingga 175 MPa.
Setelah logam cair terisi, tekanan akan dipertahankan hingga pengecoran mengeras.
Kemudian, batang pendorong akan mendorong semua coran keluar.
Karena mungkin ada beberapa rongga dalam cetakan, mungkin ada beberapa coran dalam setiap proses pengecoran.
Dalam proses desanding, residu perlu dipisahkan, termasuk gerbang pembuatan cetakan, runner, gerbang dan flash.
Proses ini biasanya diselesaikan dengan mengekstrusi casting dengan cetakan pemangkasan khusus.
Metode pengamplasan lainnya termasuk menggergaji dan menggerinda.
Jika gerbangnya rapuh, Anda bisa langsung memukul pengecorannya, yang bisa menghemat tenaga.
Port pencetakan berlebih dapat digunakan kembali setelah peleburan. Hasil yang biasa adalah sekitar 67%.
Injeksi tekanan tinggi menghasilkan pengisian cetakan yang sangat cepat, sehingga logam cair dapat mengisi seluruh cetakan sebelum ada bagian yang mengeras.
Dengan cara ini, bahkan bagian berdinding tipis yang sulit untuk diisi, bisa terhindar dari diskontinuitas permukaan.
Namun demikian, hal ini juga akan menyebabkan retensi udara, karena sulit untuk keluar ketika mengisi cetakan dengan cepat.
Masalah ini bisa dikurangi dengan menempatkan lubang pembuangan pada garis perpisahan, tetapi bahkan proses yang sangat presisi pun akan meninggalkan pori-pori di bagian tengah casting.
Sebagian besar die casting dapat menyelesaikan beberapa struktur yang tidak dapat diselesaikan dengan pengecoran melalui proses sekunder, seperti pengeboran dan pemolesan.
Cacat dapat diperiksa setelah pasir jatuh. Cacat yang paling umum termasuk Stagnasi (penuangan yang tidak cukup) dan bekas luka dingin.
Cacat ini dapat disebabkan oleh suhu cetakan atau logam cair yang tidak mencukupi, logam yang bercampur dengan kotoran, ventilasi yang terlalu sedikit, pelumas yang terlalu banyak, dll. Cacat lainnya termasuk pori-pori, rongga penyusutan, retakan panas dan tanda aliran.
Tanda aliran adalah tanda yang tertinggal pada permukaan coran karena cacat gerbang, sudut tajam, atau pelumas yang berlebihan.
Pelumas berbahan dasar air, yang disebut emulsi, adalah jenis pelumas yang paling sering digunakan untuk alasan kesehatan, lingkungan, dan keselamatan.
Tidak seperti pelumas pelarut, jika mineral di dalam air dihilangkan dengan proses yang tepat, mereka tidak akan meninggalkan produk sampingan dalam coran.
Jika proses pengolahan air tidak tepat, mineral di dalam air akan menyebabkan cacat permukaan pengecoran dan diskontinuitas.
Pada dasarnya ada empat jenis pelumas berbahan dasar air: air yang dicampur dengan oli, oli yang dicampur dengan air, semi sintetis, dan sintetis.
Air yang dicampur dengan oli adalah pelumas terbaik, karena ketika menggunakan pelumas, air akan mendinginkan permukaan cetakan melalui penguapan sambil menyimpan oli, yang dapat membantu proses demoulding.
Pada umumnya, proporsi pelumas tersebut adalah 30 bagian air dicampur dengan 1 bagian minyak. Dalam kasus yang ekstrem, rasio ini bisa mencapai 100:1.
Minyak yang dapat digunakan sebagai pelumas termasuk minyak berat, lemak hewani, lemak nabati, dan lemak sintetis.
Oli residu yang berat memiliki viskositas tinggi pada suhu kamar, tetapi akan menjadi film pada suhu tinggi dalam proses die casting.
Viskositas dan sifat termal losion dapat dikontrol dengan menambahkan zat lain ke dalam pelumas.
Bahan-bahan ini termasuk grafit, aluminium dan mika. Bahan kimia tambahan lainnya dapat menghindari debu dan oksidasi.
Pengemulsi dapat ditambahkan ke pelumas berbasis air, sehingga pelumas berbasis minyak dapat ditambahkan ke air, termasuk sabun, alkohol, dan etilena oksida.
Untuk waktu yang lama, pelumas berbasis pelarut yang umum digunakan adalah solar dan bensin.
Mereka bagus untuk pengecoran yang akan keluar, tetapi ledakan kecil akan terjadi selama setiap proses die casting, yang mengarah pada akumulasi elemen karbon pada dinding rongga.
Pelumas berbasis pelarut lebih seragam daripada pelumas berbasis air.
Mesin die casting dapat dibagi menjadi dua jenis: mesin die casting ruang panas dan mesin die casting ruang dingin.
Perbedaannya adalah seberapa besar kekuatan yang dapat mereka tahan. Kisaran tekanan tipikal adalah antara 400 dan 4000 ton.
Pengecoran die casting ruang panas
Pengecoran die casting ruang panas, kadang-kadang juga dikenal sebagai leher angsa mati pengecoran, memiliki cairan cair dan logam semi cair di dalam kolam logamnya, yang mengisi cetakan di bawah tekanan.
Pada awal siklus, piston mesin berada dalam kondisi berkontraksi, dan kemudian logam cair dapat mengisi leher angsa.
Piston pneumatik atau hidrolik menekan logam dan mengisinya ke dalam cetakan.
Keuntungan dari sistem ini termasuk kecepatan sirkulasi yang tinggi (sekitar 15 siklus dapat diselesaikan per menit), otomatisasi yang mudah, dan proses peleburan logam yang nyaman.
Kerugiannya antara lain adalah tidak mungkin untuk membuat logam cor dengan titik leleh yang tinggi, dan juga tidak mungkin untuk aluminium cor matikarena aluminium akan mengeluarkan besi dari kolam peleburan.
Oleh karena itu, secara umum, mesin die casting ruang panas digunakan untuk paduan seng, timah, dan timah.
Selain itu, die casting ruang panas sulit digunakan untuk pengecoran coran besar, dan biasanya proses ini digunakan untuk pengecoran coran kecil.
Pengecoran die casting ruang dingin
Cold chamber die casting dapat digunakan untuk logam yang tidak dapat digunakan dalam proses hot chamber die casting, termasuk aluminium, magnesium, tembaga, dan paduan seng dengan kandungan aluminium yang tinggi.
Dalam proses ini, logam perlu dilebur dalam wadah tersendiri terlebih dulu.
Sejumlah logam cair kemudian ditransfer ke ruang injeksi yang tidak dipanaskan atau nosel injeksi.
Logam-logam ini diinjeksikan ke dalam cetakan dengan tekanan hidrolik atau mekanis.
Karena logam cair perlu dipindahkan ke dalam ruang dingin, kerugian terbesar dari proses ini adalah waktu siklusnya yang sangat lama.
Ada mesin die-casting ruang dingin vertikal dan horizontal.
Mesin die-casting vertikal biasanya merupakan mesin kecil, sedangkan mesin die-casting horizontal memiliki berbagai model.
Die-casting die terdiri dari dua bagian, yaitu bagian penutup dan bagian yang bergerak, dan bagian tempat keduanya digabungkan, disebut garis perpisahan.
Pada die casting ruang panas, bagian penutup memiliki gerbang, sedangkan pada die casting ruang dingin, ini adalah port injeksi.
Logam cair dapat masuk ke dalam cetakan dari sini, dan bentuk bagian ini cocok dengan nosel injeksi di die casting ruang panas atau ruang injeksi di die casting ruang dingin.
Bagian yang dapat digerakkan biasanya mencakup batang dorong dan pelari.
Pelari adalah saluran antara gerbang dan rongga cetakan, tempat logam cair memasuki rongga cetakan.
Bagian penutup biasanya dihubungkan ke pelat penekan tetap atau pelat penekan depan, sedangkan bagian yang dapat digerakkan dihubungkan ke pelat penekan yang dapat digerakkan.
Rongga dibagi menjadi dua sisipan rongga, yang merupakan komponen independen yang secara relatif mudah dilepas atau dipasang dari cetakan dengan baut.
Cetakannya didesain secara khusus. Ketika cetakan dibuka, casting akan tetap berada di bagian yang bergerak.
Dengan cara ini, batang pendorong dari bagian yang dapat digerakkan akan mendorong keluar casting. Batang dorong biasanya digerakkan oleh pelat penekan. Ini akan secara akurat menggerakkan semua batang dorong pada saat yang sama dengan kekuatan yang sama, untuk memastikan bahwa casting tidak rusak.
Setelah pengecoran didorong keluar, pelat penekan menyusut untuk menarik kembali semua batang dorong untuk mempersiapkan pengecoran cetakan berikutnya.
Karena pengecoran masih dalam kondisi suhu tinggi saat demoulding, hanya jika jumlah batang dorong cukup, tekanan rata-rata pada setiap batang dorong dapat menjadi cukup kecil untuk menghindari kerusakan pada pengecoran.
Namun demikian, push rod masih akan meninggalkan jejak, sehingga harus dirancang dengan hati-hati agar posisi push rod tidak terlalu berdampak pada pengoperasian casting.
Bagian lain dalam cetakan termasuk pelat geser inti dan sejenisnya.
Core digunakan untuk membuat lubang atau bukaan pada coran. Mereka juga dapat digunakan untuk meningkatkan detail coran.
Ada tiga jenis core: tetap, dapat digerakkan dan longgar.
Arah inti tetap sejajar dengan arah pengecoran keluar dari cetakan. Mereka dipasang atau dihubungkan secara permanen ke cetakan.
Inti yang dapat digerakkan dapat diatur ke segala arah kecuali arah penarikan keluar.
Setelah pengecoran dipadatkan, sebelum membuka cetakan, inti yang dapat digerakkan harus dikeluarkan dari rongga cetakan dengan menggunakan alat pemisah.
Geser sangat dekat dengan inti yang dapat digerakkan, dan perbedaan terbesarnya yaitu, slider dapat digunakan untuk membuat permukaan cekung.
Penggunaan core dan slider dalam die casting dapat meningkatkan biaya secara signifikan.
Loose core, juga dikenal sebagai takeout block, dapat digunakan untuk membuat permukaan yang kompleks, seperti lubang berulir.
Sebelum memulai setiap siklus, Anda perlu memasang slider secara manual dan akhirnya mendorongnya keluar dengan casting.
Kemudian keluarkan inti yang lepas.
Loose core adalah core yang paling mahal karena pembuatannya membutuhkan banyak tenaga kerja, dan akan meningkatkan waktu siklus.
Saluran keluar biasanya tipis dan panjang (sekitar 0,13 mm), sehingga logam cair dapat didinginkan dengan cepat untuk mengurangi limbah.
Dalam proses die casting, tidak perlu menggunakan riser, karena tekanan logam cair sangat tinggi, yang dapat memastikan bahwa logam cair mengalir ke dalam cetakan dari gerbang.
Karena suhu, karakteristik material yang paling penting untuk cetakan adalah ketahanan getaran termal dan fleksibilitas.
Karakteristik lainnya termasuk kemampuan pengerasan, kemampuan mesin, ketahanan retak termal, kemampuan laskegunaan (terutama untuk cetakan besar) dan biaya.
Umur die secara langsung bergantung pada suhu logam cair dan waktu setiap siklus.
Cetakan yang digunakan untuk die casting biasanya terbuat dari baja perkakas yang keras. Karena besi tuang tidak dapat menahan tekanan internal yang besar, cetakannya mahal, yang juga menyebabkan biaya pembukaan yang tinggi.
Logam yang dicetak pada suhu yang lebih tinggi perlu menggunakan bahan yang lebih keras baja paduan.
Utama cacat pada die casting termasuk keausan dan erosi.
Cacat lainnya termasuk retak termal dan kelelahan termal.
Ketika permukaan cetakan memiliki cacat karena perubahan suhu yang terlalu besar, maka akan terjadi retakan panas.
Setelah terlalu sering digunakan, cacat pada permukaan cetakan akan menghasilkan kelelahan termal.
Luas penampang minimum yang sesuai dan sudut rancangan minimum berbagai bahan tercantum dalam tabel berikut ini, dan penampang yang paling tebal harus kurang dari 13mm.
Logam | Luas penampang minimum | Sudut rancangan minimum |
paduan aluminium | 0,89mm (0,035 inci) | 1:100(0.6°) |
Kuningan dan perunggu | 1,27mm (0,050 inci) | 1:80(0.7°) |
Paduan magnesium | 1,27mm (0,050 inci) | 1:100(0.6°) |
Kirsite | 0,63mm (0,025 inci) | 1:200(0.3°) |
Logam yang digunakan untuk die casting terutama meliputi seng, tembaga, aluminium, magnesium, timah, timah, dan paduan timah.
Meskipun besi tuang tekan jarang digunakan, namun juga dapat digunakan.
Logam die-casting khusus termasuk ZAMAK, paduan seng aluminium dan standar Asosiasi Aluminium Amerika: Magnesium AA380, AA384, aa386, AA390 dan AZ91D.
Karakteristik berbagai logam selama die casting adalah sebagai berikut:
Seng:
Logam termudah untuk die cast. Sangat ekonomis untuk membuat komponen kecil, mudah dilapisi, kekuatan tekan dan plastisitas tinggi, dan umur pengecoran yang panjang.
Aluminium:
Ringan, kompleks dalam pembuatan dan coran berdinding tipis, dengan stabilitas dimensi yang tinggi, ketahanan korosi yang kuat, kinerja mekanik yang baik, konduktivitas termal dan konduktivitas yang tinggi, dan kekuatan yang masih tinggi pada suhu tinggi.
Magnesium:
Mudah dikerjakan dengan mesin, rasio kekuatan dan berat yang tinggi, paling ringan dari logam die-casting yang umum digunakan.
Tembaga:
Memiliki kekerasan yang tinggi dan ketahanan korosi yang kuat. Ini memiliki kinerja mekanis, ketahanan abrasi dan kekuatan terbaik dalam logam die-casting yang umum.
Timbal dan timah:
Kepadatan tinggi, akurasi dimensi tinggi, dapat digunakan sebagai bagian anti-korosi khusus.
Untuk alasan kesehatan masyarakat, paduan ini tidak dapat digunakan sebagai peralatan pemrosesan dan penyimpanan makanan.
Paduan timbal, timah dan antimon (kadang-kadang dengan sedikit tembaga) dapat digunakan untuk membuat tipe manual dan bronzing dalam pencetakan relief.
Batas massa atas untuk die casting yang menggunakan aluminium, tembaga, magnesium, dan seng masing-masing adalah 70 pon (32 kg), 10 pon (4,5 kg), 44 pon (20 kg), dan 75 pon (34 kg).
Keuntungan dari pengecoran
Keunggulan die casting termasuk akurasi dimensi yang sangat baik.
Pada umumnya, hal ini bergantung pada bahan casting. Nilai tipikal yaitu, kesalahannya 0,1 mm untuk ukuran 2,5 cm pertama, dan kesalahan meningkat 0,002 mm untuk setiap kenaikan 1 cm.
Dibandingkan dengan proses pengecoran lainnya, permukaan pengecorannya halus, dan radius fillet sekitar 1-2,5 mikron.
Pengecoran dengan ketebalan dinding sekitar 0,75 mm dapat diproduksi relatif terhadap metode pengecoran kotak pasir atau cetakan permanen.
Ini dapat secara langsung mencetak struktur internal, seperti selongsong kawat, elemen pemanas, dan permukaan bantalan berkekuatan tinggi.
Keunggulan lainnya termasuk dapat mengurangi atau menghindari pemesinan sekunder, kecepatan produksi yang cepat, kekuatan tarik pengecoran hingga 415 MPa, dan dapat mengecor logam dengan fluiditas tinggi.
Kerugian dari pengecoran
Kerugian terbesar dari die casting adalah biaya tinggi.
Peralatan pengecoran, cetakan, dan komponen terkait cetakan mahal dibandingkan dengan metode pengecoran lainnya.
Oleh karena itu, akan lebih ekonomis untuk menghasilkan produk dalam jumlah besar saat membuat die casting.
Kerugian lainnya termasuk: proses ini hanya dapat diterapkan pada logam dengan fluiditas tinggi, dan massa pengecoran harus antara 30g dan 10kg.
Pada die casting normal, selalu ada pori-pori pada batch terakhir coran.
Oleh karena itu, tidak ada perlakuan panas atau pengelasan yang dapat dilakukan, karena gas dalam celah akan mengembang di bawah aksi panas, sehingga mengakibatkan cacat mikro di dalam dan pengelupasan permukaan.
Pengecoran bertekanan, singkatnya disebut die casting, adalah metode pengecoran di mana cairan paduan cair dituangkan ke dalam ruang bertekanan untuk mengisi rongga cetakan baja dengan kecepatan tinggi, dan cairan paduan dipadatkan di bawah tekanan untuk membentuk pengecoran.
Karakteristik utama die casting yang berbeda dari metode pengecoran lainnya adalah tekanan tinggi dan kecepatan tinggi.
(1) Logam cair mengisi rongga cetakan di bawah tekanan, dan mengkristal serta mengeras di bawah tekanan yang lebih tinggi. Tekanan yang umum adalah 15-100mpa.
② Cairan logam mengisi rongga cetakan dengan kecepatan tinggi, biasanya 10-50 m/s, dan terkadang lebih dari 80 m/s (kecepatan linier rongga cetakan yang dimasukkan melalui pintu masuk - kecepatan pintu masuk).
Oleh karena itu, waktu pengisian cairan logam sangat singkat, sekitar 0,01-0,2 detik (tergantung pada ukuran casting).
Die casting adalah metode pengecoran presisi. Toleransi dimensi dari komponen die-casting yang dicetak dengan die casting sangat kecil dan akurasi permukaannya sangat tinggi.
Dalam kebanyakan kasus, komponen die-casting dapat dirakit dan diaplikasikan tanpa diputar, dan komponen berulir dapat langsung dilemparkan.
Dari suku cadang kamera biasa, suku cadang mesin tik, suku cadang kalkulator elektronik, dekorasi dan suku cadang kecil lainnya, serta suku cadang kendaraan yang rumit seperti mobil, lokomotif, dan pesawat terbang, sebagian besar dibuat dengan die casting.
Damage
Selama produksi die-casting, cetakan berulang kali mengalami pendinginan dan pemanasan, dan permukaan pembentuk serta bagian dalamnya berubah bentuk, yang menyebabkan tekanan termal siklik berulang, mengakibatkan kerusakan sekunder pada struktur dan hilangnya ketangguhan, yang mengarah pada munculnya retakan mikro dan terus meluas.
Setelah retakan meluas, logam cair akan masuk ke dalam, dan tekanan mekanis yang berulang-ulang akan mempercepat pertumbuhan retakan.
Oleh karena itu, di satu sisi, die harus dipanaskan sepenuhnya pada awal die casting.
Selain itu, dalam proses die produksi pengecorancetakan harus disimpan dalam kisaran suhu kerja tertentu untuk menghindari kegagalan retak dini.
Pada saat yang sama, perlu dipastikan bahwa penyebab internal tidak terjadi sebelum cetakan dimasukkan ke dalam produksi dan selama produksi.
Karena dalam produksi aktual, sebagian besar kegagalan cetakan disebabkan oleh panas kelelahan retak kegagalan.
Fragmentasi
Di bawah aksi gaya injeksi, cetakan akan memulai retakan pada bagian terlemah, terutama bila tanda juru tulis atau tanda pemesinan listrik pada permukaan cetakan cetakan tidak dipoles, atau bila sudut-sudut cetakan terlihat jelas, retakan halus akan muncul terlebih dahulu.
Apabila terdapat fase getas atau butiran kasar pada batas butir, maka akan mudah retak.
Namun, ketika terjadi fraktur getas, retakan tumbuh dengan cepat, yang merupakan faktor yang sangat berbahaya untuk kegagalan fraktur pada die.
Untuk alasan ini, di satu sisi, semua goresan dan bekas pemesinan listrik pada permukaan cetakan harus dipoles, meskipun dalam sistem penuangan.
Selain itu, diperlukan bahwa bahan mati yang digunakan memiliki kekuatan tinggi, plastisitas yang baik, ketangguhan benturan yang baik, dan ketangguhan patah.
Corosi
Seperti disebutkan di atas, paduan die-casting yang umum digunakan meliputi paduan seng, paduan aluminium, paduan magnesium dan paduan tembaga, serta die-casting aluminium murni.
Zn, Al dan Mg relatif aktif elemen logamyang memiliki afinitas yang baik dengan bahan cetakan, terutama Al yang mudah menggigit cetakan.
Ketika kekerasan cetakan tinggi, ketahanan korosi lebih baik, tetapi jika ada titik-titik lunak pada permukaan cetakan, ketahanan korosi tidak baik.
Ada banyak faktor yang menyebabkan kegagalan cetakan, termasuk faktor eksternal (seperti suhu pengecoran, apakah cetakan dipanaskan terlebih dahulu, berapa banyak lapisan zat air yang disemprotkan, apakah tonase mesin die-casting cocok, apakah tekanan die-casting terlalu tinggi, kecepatan gerbang bagian dalam terlalu cepat, pembukaan air pendingin tidak disinkronkan dengan produksi die-casting, jenis dan komposisi bahan pengecoran Fe, ukuran dan bentuk pengecoran, ketebalan dinding, jenis pelapis, dll.).
Ada juga penyebab internal (misalnya, kualitas metalurgi bahan cetakan itu sendiri, proses penempaan blanko, rasionalitas struktur cetakan desain, rasionalitas desain sistem gating, tekanan internal yang dihasilkan selama pemesinan mesin cetakan (pemesinan listrik), proses perlakuan panas cetakan, termasuk berbagai akurasi pencocokan dan persyaratan kebersihan).
Jika terjadi kegagalan awal pada cetakan, maka perlu dicari tahu penyebab internal atau eksternal untuk perbaikan di masa mendatang.
Namun, dalam produksi aktual, korosi hanya bersifat lokal pada cetakan, misalnya, bagian yang langsung dicuci oleh gerbang (inti dan rongga) rentan terhadap korosi, dan bagian dengan kekerasan lunak rentan terhadap pelekatan paduan aluminium.
Menuangkan luapan
Persyaratan untuk sariawan cetakan pada mesin die casting horizontal ruang dingin:
(1) Diameter bagian dalam ruang tekanan harus dipilih sesuai dengan tekanan spesifik yang diperlukan dan kepenuhan ruang tekanan.
Pada saat yang sama, deviasi diameter bagian dalam selongsong gerbang harus diperbesar secara tepat oleh beberapa kabel dibandingkan dengan deviasi diameter bagian dalam ruang tekanan, untuk menghindari masalah kemacetan pukulan atau keausan serius yang disebabkan oleh sumbu yang berbeda dari selongsong gerbang dan diameter bagian dalam ruang tekanan, dan ketebalan dinding selongsong gerbang tidak boleh terlalu tipis.
Panjang selongsong sariawan umumnya harus lebih kecil dari ujung pengiriman pukulan injeksi, sehingga cat dapat dikeluarkan dari ruang tekanan.
② Lubang bagian dalam ruang tekanan dan selongsong sariawan harus digerinda halus setelah perlakuan panas, dan kemudian digerinda di sepanjang arah sumbu.
The kekasaran permukaan harus ≤ Ra0,2 μ m.
③ Pengalih terhubung dengan rongga yang membentuk lapisan.
Kedalaman cekungnya sama dengan kedalaman runner, diameternya disesuaikan dengan diameter bagian dalam selongsong sariawan, dan memiliki kemiringan 5 ° di sepanjang arah demoulding.
Ketika sariawan jenis pengantar lapisan digunakan, volume panjang efektif ruang tekanan diperpendek, dan kepenuhan ruang tekanan dapat ditingkatkan.
Persyaratan cetakan
(1) Pintu masuk pelari cetakan horizontal dingin umumnya harus ditempatkan pada posisi di atas 1/3 dari diameter dalam bagian atas ruang tekanan, untuk mencegah cairan logam di ruang tekanan memasuki pelari sebelum waktunya dan mulai mengeras terlebih dahulu di bawah aksi gravitasi.
② Luas penampang runner harus dikurangi secara bertahap dari sariawan ke pintu masuk.
Untuk memperluas penampang melintang, tekanan negatif akan terjadi ketika logam cair mengalir, yang mudah menyedot gas pada permukaan perpisahan, dan meningkatkan bungkus eddy dalam aliran logam cair.
Pada umumnya, bagian pada saluran keluar lebih kecil 10-30% daripada saluran masuk.
③ Pelari harus memiliki panjang dan kedalaman tertentu.
Tujuan mempertahankan panjang tertentu adalah untuk menstabilkan dan memandu aliran.
Jika kedalamannya tidak cukup, suhu logam cair akan turun dengan cepat;
Jika kedalamannya terlalu dalam, kondensasi akan menjadi terlalu lambat, yang tidak hanya akan mempengaruhi produktivitas tetapi juga meningkatkan jumlah bahan daur ulang.
④ Luas penampang runner harus lebih besar daripada luas penampang pintu masuk untuk memastikan kecepatan penuangan logam ke dalam cetakan.
Luas penampang runner utama harus lebih besar daripada luas penampang setiap runner cabang.
⑤ Kedua sisi bagian bawah runner harus dibulatkan untuk menghindari keretakan dini, dan kedua sisinya dapat dibuat dengan kemiringan sekitar 5 °.
Kekasaran permukaan pelari ≤ Ra0,4 μ m.
Ingate
(1) Permukaan perpisahan tidak boleh ditutup segera setelah logam cair memasuki cetakan, dan alur luapan serta alur pembuangan tidak boleh langsung mengenai inti.
Arah aliran logam cair setelah memasuki cetakan harus diisi dari dinding tebal ke dinding tipis di sepanjang rusuk dan sirip tuang sebanyak mungkin.
② Apabila memilih posisi pintu masuk, aliran logam cair harus sependek mungkin.
Ketika multi strand ingate digunakan, perlu untuk mencegah beberapa helai logam cair menyatu dan saling bertumbukan setelah injeksi, yang akan menyebabkan inklusi arus eddy, inklusi oksidasi, dan cacat lainnya.
③ Gerbang bagian dalam dari bagian berdinding tipis harus lebih kecil secara tepat daripada bagian yang tebal untuk memastikan kecepatan pengisian yang diperlukan.
Pengaturan gerbang bagian dalam harus mudah dipotong, dan badan pengecoran tidak boleh rusak (memakan daging).
Tangki luapan
(1) Alur luapan harus mudah dilepas dari casting dan sebisa mungkin tidak merusak badan casting.
② Apabila menetapkan slot pembuangan pada slot luapan, perhatikan posisi port luapan untuk menghindari pemblokiran slot pembuangan terlalu dini dan membuat slot pembuangan menjadi tidak efektif.
③ Tidak diperbolehkan untuk mengatur beberapa port luapan atau port luapan yang sangat lebar dan tebal pada tangki luapan yang sama, untuk mencegah cairan dingin, terak, gas, cat, dll. Dalam logam cair kembali ke rongga cetakan dari tangki luapan dan menyebabkan cacat pengecoran.
Dengan alasan untuk memenuhi fungsi produk, desain die casting yang wajar, menyederhanakan struktur die casting, mengurangi biaya die casting, mengurangi cacat die casting, dan meningkatkan kualitas komponen die casting.
Karena proses pencetakan injeksi berasal dari proses pengecoran, panduan desain die casting sangat mirip dengan panduan desain komponen plastik dalam beberapa aspek.
Untuk desain detail komponen die-casting, silakan merujuk ke buku "panduan desain produk untuk manufaktur dan perakitan" yang diterbitkan oleh Mesin Cina Tekan.
Fillet
(termasuk sudut) gambar pengecoran sering kali menunjukkan persyaratan seperti fillet yang tidak bertanda R2.
Kita tidak boleh mengabaikan peran fillet yang tidak bertanda ini ketika membuka cetakan, dan tidak boleh membuat sudut yang jelas atau fillet yang terlalu kecil.
Fillet pengecoran dapat membuat cairan logam terisi dengan lancar, membuat gas dalam rongga keluar secara berurutan, mengurangi konsentrasi tegangan, dan memperpanjang masa pakai cetakan. (tidak mudah bagi pengecoran untuk mengalami keretakan atau berbagai cacat karena pengisian yang tidak tepat).
Contohnya, terdapat banyak sudut yang bersih pada cetakan panci minyak standar.
Secara relatif, cetakan panci minyak saudara paling baik dibuka saat ini, dan ada juga banyak panci minyak yang berat.
Kemiringan demoulding
Dilarang memiliki ceruk samping buatan ke arah demoulding (biasanya coran terjebak dalam cetakan selama uji coba cetakan, dan ceruk lokal disebabkan oleh pengeboran, pahatan keras, dll. Ketika cetakan ditangani dengan metode yang salah).
Kekasaran
Bagian cetakan dan sistem penuangan harus dipoles dengan hati-hati sesuai kebutuhan, dan harus dipoles di sepanjang arah demoulding.
Karena seluruh proses logam cair memasuki sistem penuangan dari ruang tekanan dan mengisi rongga hanya membutuhkan waktu 0,01-0,2 detik.
Untuk mengurangi hambatan aliran logam cair dan meminimalkan kehilangan tekanan, maka diperlukan permukaan akhir yang tinggi.
Pada saat yang sama, kondisi pemanasan dan erosi dari sistem penuangan relatif buruk, dan semakin buruk hasil akhirnya, semakin mudah cetakan rusak.
5. Kekerasan bagian cetakan cetakan: paduan aluminium: sekitar HRC46 °, tembaga: sekitar HRC38 °.
Selama pemrosesan, cetakan harus mencoba menyisakan kelonggaran perbaikan, membuat batas atas ukuran, dan menghindari pengelasan.
Fluiditas mengacu ke kemampuan cairan paduan untuk mengisi cetakan.
Fluiditas menentukan apakah paduan dapat menghasilkan coran yang rumit.
Paduan eutektik memiliki fluiditas terbaik dalam paduan aluminium.
Ada banyak faktor yang memengaruhi fluiditas, terutama komposisi, suhu dan partikel padat oksida logam, senyawa logam, dan polutan lain dalam cairan paduan, tetapi faktor fundamental eksternal adalah suhu penuangan dan tekanan penuangan (umumnya dikenal sebagai kepala penuangan).
Dalam produksi aktual, ketika paduan telah ditentukan, selain memperkuat proses peleburan (pemurnian dan pembuangan terak), juga perlu untuk meningkatkan proses pengecoran (permeabilitas cetakan pasir, knalpot cetakan logam dan suhu), dan meningkatkan suhu penuangan tanpa mempengaruhi kualitas pengecoran untuk memastikan fluiditas paduan.
Tindakan pencegahan untuk kondisi pembentukan die casting:
Mesin die casting, paduan die casting, dan die casting adalah tiga elemen utama produksi die casting, yang tidak ada yang tidak dapat dipisahkan.
Yang disebut proses die-casting adalah menggunakan ketiga elemen ini secara organik dan komprehensif, sehingga menghasilkan coran yang memenuhi syarat dengan tampilan yang baik, kualitas internal dan dimensi sesuai dengan persyaratan gambar atau perjanjian secara stabil, berirama dan efisien, dan bahkan coran berkualitas tinggi.
Suhu leleh bahan, suhu cetakan dan suhu leleh selama injeksi;
Terakhir, kondisi produk die-casting harus diperbaiki untuk mendapatkan produk yang sempurna.
Prinsip pemilihan suhu kerja die casting die:
1) Suhu cetakan terlalu rendah, struktur internal pengecoran longgar, dan sulit untuk mengeluarkan udara, yang membuatnya sulit untuk dibentuk;
2) Suhu cetakan terlalu tinggi, dan struktur internal pengecoran padat, tetapi pengecoran mudah "dilas" ke rongga cetakan, dan sulit untuk melepaskan pengecoran setelah menempel pada cetakan.
Pada saat yang sama, suhu yang terlalu tinggi akan memperluas cetakan itu sendiri dan memengaruhi akurasi dimensi pengecoran.
3) Suhu cetakan harus dipilih dalam kisaran yang sesuai. Umumnya, setelah pengujian sesuai, kontrol suhu konstan bagus.
Tindakan pencegahan untuk kondisi pembentukan die casting dapat dirangkum dalam dua aspek berikut:
*Suhu leleh material, suhu cetakan, dan suhu leleh selama injeksi;
Inti dari pengecoran tekanan (disingkat die casting) adalah membuat logam cair atau semi cair mengisi rongga cetakan die casting dengan kecepatan tinggi di bawah aksi tekanan tinggi, dan untuk membentuk dan memadatkan pengecoran di bawah tekanan.
Cetakan die casting bertekanan tinggi dan pengisian berkecepatan tinggi adalah dua karakteristik utama die casting. Tekanan spesifik injeksi yang umum digunakan adalah dari beberapa ribu hingga puluhan ribu kPa, dan bahkan setinggi 2 × 105kPa.
Kecepatan pengisian sekitar 10 ~ 50m / s, dan bahkan lebih dari 100m / s dalam beberapa kasus.
Waktu pengisian sangat singkat, umumnya dalam kisaran 0,01 ~ 0,2 detik.
Dibandingkan dengan metode pengecoran lainnya, die casting memiliki tiga keunggulan sebagai berikut:
1. Kualitas produk yang baik
Akurasi dimensi coran sangat tinggi, umumnya setara dengan grade 6-7, atau bahkan hingga grade 4;
Permukaan akhir yang bagus, umumnya setara dengan kelas 5 ~ 8;
The kekuatan dan kekerasan lebih tinggi, dan kekuatannya umumnya 25-30% lebih tinggi daripada pengecoran pasir, tetapi perpanjangannya berkurang sekitar 70%;
Ukuran yang stabil dan dapat dipertukarkan dengan baik;
Ini dapat membuat coran berdinding tipis dan coran yang rumit.
Sebagai contoh, ketebalan dinding minimum saat ini dari coran die casting paduan seng dapat mencapai 0,3 mm;
Pengecoran paduan aluminium bisa mencapai 0,5mm;
Diameter lubang cor minimum adalah 0,7 mm;
Pitch minimum adalah 0,75mm.
2. Efisiensi produksi yang tinggi
Alat berat ini memiliki produktivitas yang tinggi.
Misalnya, mesin die casting udara dingin horisontal J Ⅲ 3 domestik dapat melemparkan rata-rata 600-700 kali per delapan jam, dan mesin die casting ruang panas kecil dapat melemparkan rata-rata 3000-7000 kali per delapan jam;
Umur panjang cetakan die-casting, sepasang cetakan die-casting, paduan jam die-casting, umur pemakaian bisa mencapai ratusan ribu kali, bahkan jutaan kali;
Sangat mudah untuk mewujudkan mekanisasi dan otomatisasi.
3. Efek ekonomi yang sangat baik
Karena komponen die-casting memiliki keunggulan ukuran yang akurat dan permukaan yang halus.
Umumnya, tidak lagi dikerjakan dengan mesin dan digunakan secara langsung, atau volume pemrosesannya sangat kecil, sehingga tidak hanya meningkatkan tingkat pemanfaatan logam, tetapi juga mengurangi sejumlah besar peralatan pemrosesan dan jam kerja;
Harga coran itu mudah;
Bahan logam atau non-logam lainnya dapat digunakan dengan die casting gabungan.
Menghemat waktu perakitan dan logam.
Meskipun die casting memiliki banyak keunggulan, namun juga memiliki beberapa kelemahan yang perlu dipecahkan.
Sebagai contoh:
1). Karena kecepatan pengisian logam cair yang tinggi di rongga cetakan dan kondisi aliran yang tidak stabil selama pengecoran, metode pengecoran umum mudah untuk menghasilkan lubang udara pada coran, yang tidak dapat diberi perlakuan panas;
2) Sulit untuk melakukan die cast coran dengan cekung yang rumit;
3) Paduan titik leleh tinggi (seperti tembaga, logam besi), umur die-casting die yang rendah;
4) Tidak cocok untuk produksi batch kecil.
Alasan utamanya adalah bahwa biaya pembuatan cetakan die-casting tinggi, efisiensi produksi mesin die-casting tinggi, dan produksi batch kecil tidak ekonomis.
Die casting adalah salah satu yang paling canggih pembentukan logam metode.
Ini adalah cara yang efektif untuk mencapai lebih sedikit chip dan tanpa chip. Metode ini digunakan secara luas dan berkembang dengan cepat.
Ukuran dan berat casting tergantung pada kekuatan mesin die casting.
Karena meningkatnya kekuatan mesin die casting, bentuk dan ukuran casting bisa dari beberapa milimeter hingga 1-2m;
Beratnya bisa berkisar dari beberapa gram hingga puluhan kilogram.
Coran aluminium dengan diameter 2 m dan berat 50 kg dapat dicetak di luar negeri.
Die casting tidak lagi terbatas pada industri mobil dan industri instrumen, tetapi secara bertahap telah berkembang ke sektor industri lain, seperti mesin pertanian, industri peralatan mesinindustri elektronik, industri pertahanan nasional, komputer, peralatan medis, jam tangan, kamera, perangkat keras harian dan puluhan industri lainnya, khususnya: suku cadang mobil, aksesori furnitur, aksesori kamar mandi (saniter), suku cadang penerangan, mainan, alat cukur, penjepit dasi, suku cadang listrik dan elektronik, gesper ikat pinggang, kotak arloji, ornamen logam, kunci, ritsleting, dll.
Dalam aspek teknologi die-casting, teknologi baru seperti die-casting vakum, die-casting beroksigen, die-casting berkecepatan tinggi dan padat, serta penerapan inti yang dapat larut telah muncul.
Ini akan memainkan peran yang sangat baik dalam mempromosikan industri die casting China.
Produksi coran die-casting perlu mengandalkan mesin dan peralatan die-casting. Mesin die-casting adalah dasar dari produksi die-casting.
Tingkat teknis peralatan die-casting menentukan kualitas dan tingkat coran die-casting.
Oleh karena itu, untuk mendorong perkembangan industri die-casting, kita harus memprioritaskan pengembangan peralatan die-casting.
Tiongkok adalah negara besar dalam hal pengecoran die-casting, tetapi tingkat teknologi produksi dan peralatan industrinya masih perlu ditingkatkan.
Rencana lima tahun ke-12 China dengan jelas menunjukkan bahwa tugas utama pengembangan industri pengecoran adalah memberikan prioritas pada pengembangan peralatan teknis utama, termasuk "unit pengecoran mesin pengecoran bertonase besar", dengan tujuan memberikan dukungan peralatan untuk peningkatan teknologi perusahaan pengecoran.
Pengembangan teknologi dan peralatan die-casting akan membantu meningkatkan tingkat mesin dan peralatan die-casting, sehingga dapat meningkatkan kualitas dan tingkat teknis pengecoran dan mempromosikan pengembangan industri pengecoran.