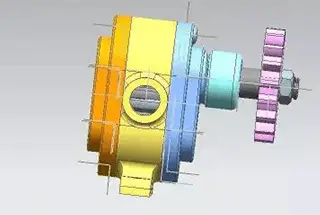
Pertanyaan seperti apa yang dapat membantu Anda meraih kesuksesan dalam wawancara teknik mesin? Artikel ini membahas 20 pertanyaan teratas yang menguji berbagai aspek teknik mesin, mulai dari sistem transmisi hingga ilmu material. Pembaca akan mempelajari tidak hanya pertanyaan apa yang diharapkan tetapi juga jenis jawaban yang menunjukkan kedalaman pengetahuan dan keahlian praktis. Baik Anda sedang mempersiapkan wawancara pertama atau ingin menyempurnakan jawaban Anda, panduan ini menawarkan wawasan yang berharga untuk meningkatkan kepercayaan diri dan kesiapan Anda.
Setelah bekerja beberapa lama, tidak dapat dihindari untuk melakukan wawancara untuk karyawan baru. Hari ini, saya ingin berbagi beberapa pertanyaan yang biasanya saya tanyakan saat mewawancarai insinyur mesin. Setiap orang dapat merefleksikan pertanyaan-pertanyaan ini dan mempertimbangkan apakah pertanyaan-pertanyaan tersebut mewakili kemampuan dan level Anda.
Pertanyaan seperti apa yang akan ditanyakan dalam wawancara teknik mesin?
Pertama, saya akan menanyakan aspek apa yang mereka kuasai, kemudian melanjutkan dengan mengajukan pertanyaan dari kategori berikut: transmisi, struktur, lembaran logam, komponen poros, komponen pelat, dan pengetahuan tentang pemilihan material (berbagai jenis baja, aluminium, paduan, dan logam lainnya, serta non-logam bahan seperti plastik), perlakuan panas pada komponen, pelapisan listrik, pengecatan, dan perawatan permukaan lainnya.
Untuk transmisi, pertanyaan akan berfokus pada beberapa aspek: transmisi roda gigi, penggerak rantai, roda sabuk, sabuk sinkron drive.
Rantai dimensi memainkan peran penting dalam proses manufaktur dan perakitan yang presisi. Rantai ini mewakili serangkaian dimensi yang saling berhubungan yang membentuk lingkaran tertutup, diatur dalam urutan tertentu untuk mencapai toleransi dan kecocokan yang diinginkan. Setiap dimensi individu dalam rantai ini disebut sebagai link.
Dalam rantai dimensi, dimensi kritis yang secara tidak langsung memastikan keakuratan keseluruhan proses perakitan atau pemesinan dikenal sebagai mata rantai penutup. Tautan ini biasanya merupakan persyaratan fungsional atau spesifikasi desain yang harus dipenuhi. Dimensi lainnya yang berkontribusi untuk mencapai link penutup disebut link konstituen.
Contoh praktis dari aplikasi rantai dimensi dapat ditemukan dalam perakitan bantalan rol silinder ke dalam rumah:
Dengan menganalisis rantai dimensi, para insinyur dapat:
Pendekatan ini memungkinkan produsen untuk:
Logam besi terutama mencakup baja dan besi tuang, dengan baja yang dikategorikan lebih lanjut ke dalam baja karbon dan baja paduan. Klasifikasi ini didasarkan pada komposisi dan sifat logam.
Baja karbon, kategori dasar, dibagi lagi menjadi tiga kelas berdasarkan kandungan pengotornya, terutama sulfur (S) dan fosfor (P):
Baja karbon berkualitas tinggi dibedakan dengan kontrol ketat terhadap pengotornya, khususnya menjaga tingkat sulfur dan fosfor masing-masing pada atau di bawah 0,040%. Kandungan pengotor yang rendah ini secara signifikan meningkatkan sifat mekanis baja, termasuk peningkatan kekuatan, keuletan, dan kemampuan las.
Komposisi terkontrol dari baja karbon berkualitas tinggi menawarkan beberapa keuntungan:
Karakteristik ini menjadikan baja karbon berkualitas tinggi sebagai pilihan yang sangat baik untuk aplikasi yang membutuhkan toleransi yang tepat, rasio kekuatan-terhadap-berat yang tinggi, dan kinerja yang andal dalam berbagai kondisi pembebanan. Aplikasi yang umum meliputi komponen otomotif, suku cadang mesin presisi, dan elemen struktural berkinerja tinggi.
Penting untuk diperhatikan bahwa meskipun ambang batas ≤0,040% untuk S dan P merupakan pedoman umum, standar spesifik dapat sedikit berbeda tergantung pada grade dan aplikasi baja yang diinginkan.
Tegangan pengelasan, yang juga dikenal sebagai tegangan sisa, dapat dikurangi melalui berbagai metode, masing-masing dengan aplikasi dan efektivitas yang spesifik:
1. Perlakuan Panas:
2. Metode Mekanis:
3. Pereda Stres Getaran (VSR):
4. Penuaan Alami:
5. Teknik Pengelasan Terkendali:
6. Perawatan Kriogenik:
Metode perlakuan panas yang umum digunakan untuk logam antara lain adalah anil, normalisasi, pendinginan, temper, dan pengerasan casing. Masing-masing proses ini memiliki tujuan khusus dalam mengubah sifat mekanik dan struktur mikro logam.
Tempering adalah proses perlakuan panas kritis yang biasanya dilakukan setelah pendinginan. Proses ini melibatkan pemanasan ulang logam yang telah dipadamkan ke suhu di bawah suhu kritis yang lebih rendah, biasanya antara 150°C hingga 650°C (302°F hingga 1202°F), menahannya pada suhu tersebut untuk waktu tertentu, dan kemudian mendinginkannya, biasanya di udara. Tujuan utama tempering adalah:
Tempering suhu tinggi, yang dilakukan pada kisaran 500-650°C (932-1202°F), sangat efektif untuk baja. Proses ini memungkinkan terjadinya pelepasan tegangan yang signifikan dan perubahan mikrostruktur, sehingga menghasilkan kombinasi yang baik antara kekuatan, keuletan, dan ketangguhan. Temperatur dan durasi temper yang tepat bergantung pada komposisi paduan spesifik dan sifat akhir yang diinginkan.
Penting untuk dicatat bahwa parameter tempering harus dikontrol dengan hati-hati, karena secara signifikan mempengaruhi sifat mekanik akhir logam. Hubungan waktu-suhu dalam temper sangat penting, dan fasilitas perlakuan panas modern sering kali menggunakan proses yang dikontrol komputer secara tepat untuk memastikan hasil yang konsisten.
Mode kegagalan utama transmisi roda gigi tertutup berbeda secara signifikan antara roda gigi permukaan gigi lunak dan keras, sehingga memerlukan pendekatan yang berbeda untuk desain dan verifikasi:
Untuk transmisi roda gigi permukaan gigi lunak tertutup:
Modus kegagalan yang paling dominan adalah pitting fatigue pada permukaan gigi. Hal ini terjadi karena kontak tekanan tinggi yang berulang-ulang antara gigi roda gigi yang dikawinkan, menyebabkan retakan mikroskopis pada permukaan dan di bawah permukaan yang pada akhirnya menyebabkan pelepasan material. Proses desain harus diprioritaskan:
Untuk transmisi roda gigi permukaan gigi keras tertutup:
Modus kegagalan utama bergeser ke fraktur kelelahan akar gigi. Hal ini terjadi karena tekanan lentur siklik pada akar gigi, yang pada akhirnya menyebabkan inisiasi dan perambatan retak. Proses desain harus fokus pada:
Prinsip-prinsip verifikasi desain:
Gearbox, juga dikenal sebagai transmisi, berfungsi sebagai komponen mekanis penting yang mengubah kecepatan dan torsi yang ditransmisikan dari penggerak utama (seperti mesin atau motor listrik) ke mesin atau mekanisme yang digerakkan. Fungsi utamanya meliputi:
Gearbox tersedia dalam berbagai jenis dan konfigurasi, termasuk:
Saya paling akrab dengan proses penggulungan pelat tebal sedang dalam produksi baja. Proses manufaktur yang canggih ini mengubah billet tuang kontinu menjadi pelat baja berkualitas tinggi melalui serangkaian operasi yang dikontrol dengan tepat. Alur produksi biasanya terdiri dari tahap-tahap utama berikut ini:
Proses ini memanfaatkan otomatisasi canggih, sistem kontrol kualitas waktu nyata, dan analisis data untuk memastikan produksi pelat tebal menengah berkualitas tinggi yang konsisten yang memenuhi persyaratan ketat beragam aplikasi industri.
Dalam skenario yang paling ekstrem, silinder hidraulik yang mengalami guncangan eksternal yang kuat dapat mengalami kegagalan yang sangat parah, yang berpotensi menyebabkan:
1. Lepasnya silinder: Gaya yang kuat dapat menyebabkan silinder terlepas dari dudukannya, yang mengakibatkan hilangnya fungsi dan menimbulkan risiko keselamatan yang signifikan.
2. Pipa minyak pecah: Saluran hidraulik bertekanan tinggi dapat meledak atau pecah, sehingga menyebabkan hilangnya cairan hidraulik dan tekanan sistem dengan cepat. Hal ini dapat menyebabkan kebocoran oli, kontaminasi lingkungan, dan potensi bahaya kebakaran jika fluida bersentuhan dengan permukaan yang panas.
3. Deformasi struktural: Bodi silinder, batang piston, atau komponen internal dapat mengalami deformasi, pembengkokan, atau patah yang parah. Hal ini dapat mengakibatkan:
4. Kerusakan komponen internal: Gaya kejut dapat menyebabkan kerusakan pada komponen internal seperti:
5. Lonjakan tekanan: Guncangan tiba-tiba dapat menciptakan lonjakan tekanan di dalam sistem, yang berpotensi melebihi nilai tekanan silinder dan menyebabkan kerusakan tambahan pada komponen hidraulik lainnya.
6. Kerusakan sekunder: Kegagalan silinder hidraulik dapat menyebabkan kerusakan tambahan pada mesin atau struktur yang terhubung, yang berpotensi menyebabkan reaksi berantai kegagalan pada sistem yang lebih luas.
Untuk mengurangi risiko ini, sistem peredam guncangan yang tepat, desain pemasangan yang kuat, dan inspeksi rutin sangat penting untuk sistem hidraulik yang beroperasi di lingkungan dengan guncangan tinggi. Selain itu, menggabungkan fitur keselamatan seperti katup pelepas tekanan dan mendesain dengan faktor keselamatan yang tepat dapat membantu mencegah kegagalan besar dalam skenario ekstrem.
Untuk komponen yang mengalami beban lentur dan torsi gabungan, kriteria luluh von Mises (juga dikenal sebagai teori energi distorsi atau teori kekuatan ketiga) adalah yang paling tepat. Teori ini memberikan penilaian yang komprehensif terhadap kondisi tegangan pada material, dengan mempertimbangkan interaksi antara tegangan normal dan tegangan geser.
Prosedurnya meliputi:
Pendekatan ini memperhitungkan kondisi tegangan multi-aksial dan memberikan prediksi yang lebih akurat terhadap kegagalan material dalam kondisi pembebanan yang kompleks dibandingkan dengan menggunakan komponen tegangan individual saja. Pendekatan ini sangat berguna untuk material ulet dan diadopsi secara luas dalam praktik perekayasaan karena keandalan dan kemudahan aplikasinya.
Perkembangan pemesinan mekanis modern ditandai dengan evolusi multifaset menuju sistem manufaktur yang canggih. Perkembangan ini didorong oleh beberapa tren utama:
Kandungan karbon dalam baja 45# biasanya berkisar antara 0.42% hingga 0.50%. Baja karbon sedang ini, juga dikenal sebagai C45 dalam beberapa standar internasional, biasanya disebut sebagai baja 45 dalam sistem standar GB (Guobiao) Cina. Angka "45" dalam penunjukannya secara langsung menunjukkan perkiraan kandungan karbonnya sebesar 0,45%.
Kelas baja serbaguna ini, kadang-kadang disebut "baja oli" karena kesesuaiannya untuk pendinginan oli, menawarkan keseimbangan yang baik antara kekuatan, kekerasan, dan keuletan. Baja ini banyak digunakan dalam berbagai aplikasi teknik, terutama untuk komponen yang membutuhkan kekuatan dan ketahanan aus yang moderat.
Di pasaran, baja 45# terutama tersedia sebagai produk canai panas, yang cocok untuk berbagai macam aplikasi. Spesifikasi canai dingin juga tersedia, biasanya dengan ketebalan mulai dari 1,0 hingga 4,0 mm. Proses pengerolan dingin memberikan hasil akhir permukaan yang lebih baik dan toleransi dimensi yang lebih ketat, sehingga ideal untuk aplikasi yang membutuhkan kemampuan mesin atau kualitas permukaan yang lebih baik.
Cacat pengecoran dapat secara signifikan memengaruhi kualitas, kinerja, dan keandalan komponen logam. Cacat yang paling umum ditemui dalam proses pengecoran logam meliputi:
Cutting fluid memainkan peran penting dalam proses pemotongan logam, melayani beberapa fungsi penting yang secara signifikan meningkatkan kinerja pemesinan dan umur pahat. Tujuan utama cairan pemotongan meliputi:
Desain digital mencakup integrasi komprehensif teknologi canggih di seluruh siklus hidup produk, mulai dari konseptualisasi hingga produksi dan seterusnya. Desain digital memanfaatkan alat komputasi dan metodologi yang kuat untuk merevolusi proses desain tradisional.
Contohnya, dalam konteks fabrikasi logam, desain digital mungkin melibatkan:
Informatisasi di bidang manufaktur mencakup integrasi dan pemanfaatan teknologi informasi digital, cerdas, dan berjejaring yang komprehensif untuk mengubah paradigma industri tradisional. Revolusi ini menjangkau berbagai domain:
Transformasi digital ini memungkinkan produsen untuk:
Bantalan gelinding menawarkan operasi presisi tinggi dan dapat mengakomodasi beban radial dan aksial secara bersamaan. Mereka membutuhkan lebih sedikit pelumas, lebih mudah dipasang, dan menunjukkan koefisien gesekan yang lebih rendah dibandingkan dengan bantalan geser. Desain standar, serial, dan universal mereka memfasilitasi penggunaan yang mudah, pemeliharaan, dan efektivitas biaya, menghilangkan kebutuhan akan logam non-besi yang mahal yang sering dibutuhkan pada bantalan geser.
Namun, bantalan gelinding sangat rentan terhadap kontaminasi dari partikel asing seperti serpihan logam. Mereka umumnya memiliki masa pakai yang lebih pendek daripada bantalan geser dan kapasitas penahan beban yang lebih rendah dibandingkan dengan ukurannya, menghasilkan dimensi radial yang lebih besar.
Bantalan geser unggul dalam aplikasi yang menuntut kapasitas beban tinggi, ukuran ringkas, dan integritas struktural. Mereka biasanya digunakan pada bantalan poros engkol mesin pembakaran internal dan bantalan rolling mill. Bantalan ini menawarkan karakteristik redaman yang unggul, menjadikannya ideal untuk aplikasi presisi dengan persyaratan getaran dan kebisingan yang ketat.
Pemilihan antara bantalan gelinding dan geser tergantung pada kriteria aplikasi tertentu:
Dalam praktiknya, solusi hibrida yang menggabungkan kedua jenis bantalan terkadang digunakan untuk meningkatkan kekuatan masing-masing. Misalnya, dalam gearbox industri besar, bantalan gelinding dapat digunakan untuk poros berkecepatan tinggi, sementara bantalan geser mendukung komponen yang lebih lambat dan lebih banyak beban.
CNC adalah singkatan dari Computer Numerical Control. Ini mengacu pada proses manufaktur di mana perangkat lunak komputer yang telah diprogram sebelumnya menentukan pergerakan perkakas dan mesin pabrik. Sistem CNC mengotomatiskan kontrol peralatan mesin melalui penggunaan perangkat lunak yang tertanam dalam komputer mikro yang terpasang pada alat tersebut. Teknologi ini memungkinkan kontrol yang tepat terhadap berbagai parameter seperti laju pemakanan, koordinasi, lokasi, dan kecepatan, sehingga memungkinkan operasi pemesinan yang sangat akurat dan dapat diulang.
Teknologi CNC banyak digunakan dalam manufaktur modern untuk berbagai aplikasi, termasuk:
Penggunaan mesin CNC telah merevolusi industri manufaktur dengan meningkatkan presisi, efisiensi, dan konsistensi dalam proses produksi, sekaligus mengurangi kesalahan manusia dan biaya tenaga kerja.
Motor DC menggunakan medan magnet stasioner dengan konduktor yang berputar, sedangkan motor AC menggunakan medan magnet yang berputar dengan konduktor yang tidak bergerak. Perbedaan mendasar dalam desain ini mengarah pada karakteristik operasional dan aplikasi yang berbeda.
Kontrol kecepatan adalah pembeda utama. Motor DC unggul dalam aspek ini, menawarkan penyesuaian kecepatan yang tepat dengan memvariasikan tegangan atau arus input. Hal ini membuatnya ideal untuk aplikasi yang membutuhkan kontrol kecepatan yang baik, seperti pada robotika atau kendaraan listrik. Motor AC, sebaliknya, biasanya menyesuaikan kecepatan dengan mengubah frekuensi arus bolak-balik, sering kali melalui penggerak frekuensi variabel (VFD).
Karakteristik torsi juga berbeda secara signifikan. Motor DC umumnya memberikan torsi awal yang lebih tinggi dan rasio torsi-ke-kecepatan yang lebih baik, terutama pada kecepatan rendah. Hal ini membuatnya lebih unggul untuk aplikasi yang membutuhkan torsi tinggi pada RPM rendah, seperti pada sistem konveyor atau traksi listrik. Motor AC, terutama jenis induksi, cenderung memiliki torsi awal yang lebih rendah tetapi dapat mempertahankan torsi yang konsisten pada rentang kecepatan yang lebih luas.
Persyaratan perawatan bervariasi di antara keduanya. Motor DC, dengan komutator dan rakitan sikatnya, biasanya membutuhkan perawatan yang lebih sering karena keausan sikat dan degradasi komutator. Motor AC, terutama desain tanpa sikat, umumnya menawarkan kebutuhan perawatan yang lebih rendah dan keandalan yang lebih tinggi dari waktu ke waktu.
Efisiensi dan kepadatan daya juga berbeda. Motor AC modern, terutama yang menggunakan magnet permanen, sering kali mencapai efisiensi dan kepadatan daya yang lebih tinggi dibandingkan dengan motor DC yang setara. Hal ini telah menyebabkan peningkatan penggunaan motor AC dalam aplikasi industri dan kendaraan listrik di mana efisiensi energi sangat penting.
Pertimbangan biaya berperan dalam pemilihan motor. Motor DC sering kali lebih sederhana dan lebih murah untuk aplikasi berdaya rendah. Namun, untuk penggunaan industri berdaya tinggi, motor AC sering kali terbukti lebih hemat biaya karena ketangguhannya dan persyaratan perawatan yang lebih rendah.
Pilihan antara motor DC dan AC pada akhirnya bergantung pada persyaratan aplikasi spesifik, termasuk presisi kontrol kecepatan, kebutuhan torsi, tujuan efisiensi, kemampuan pemeliharaan, dan pertimbangan desain sistem secara keseluruhan.
Pada bahan logam, deformasi elastis mengacu pada perubahan bentuk yang dapat dibalik yang terjadi ketika gaya eksternal diterapkan dalam batas elastisitas bahan. Setelah tegangan yang diberikan dihilangkan, logam akan kembali ke dimensi aslinya tanpa perubahan permanen pada struktur kristalnya. Perilaku ini diatur oleh Hukum Hooke, di mana tegangan sebanding dengan regangan hingga titik luluh.
Sebaliknya, deformasi plastis adalah perubahan bentuk yang tidak dapat dipulihkan yang terjadi ketika tegangan yang diberikan melebihi kekuatan luluh material. Deformasi permanen ini ditandai dengan pemutusan dan pembentukan kembali ikatan atom, yang menghasilkan penataan ulang struktur kristal logam. Tidak seperti deformasi elastis, deformasi plastis tetap ada bahkan setelah gaya yang diberikan dihilangkan.
Dalam aplikasi teknik, deformasi plastis sering dianggap sebagai bentuk kegagalan struktural, terutama pada komponen penahan beban. Hal ini dapat menyebabkan perubahan sifat material, penurunan kinerja, dan potensi bahaya keselamatan. Oleh karena itu, tujuan utama dalam desain struktural adalah untuk memastikan bahwa tegangan kerja tetap berada di bawah kekuatan luluh material, sehingga mencegah deformasi plastis dalam kondisi operasi normal.
Namun, penting untuk dicatat bahwa deformasi plastis yang terkendali dapat menguntungkan dalam proses manufaktur tertentu, seperti operasi pembentukan logam (misalnya, penempaan, pencetakan, atau ekstrusi), di mana deformasi tersebut sengaja diinduksi untuk mencapai bentuk dan sifat yang diinginkan. Memahami transisi dari perilaku elastis ke plastis sangat penting untuk mengoptimalkan pemilihan material, desain komponen, dan proses manufaktur dalam industri pengerjaan logam.
Peredam, juga dikenal sebagai peredam kecepatan atau gearbox, berfungsi untuk memodifikasi kecepatan rotasi dan torsi yang ditransmisikan dari penggerak utama (seperti motor listrik atau mesin) ke mesin atau peralatan yang digerakkan. Fungsi utamanya meliputi:
Peredam tersedia dalam berbagai konfigurasi:
1. Jenis Mekanis:
2. Jenis Hidrodinamika:
3. Opsi Rasio Kecepatan:
Pemilihan jenis dan konfigurasi peredam yang tepat tergantung pada faktor-faktor seperti kebutuhan daya, rentang kecepatan, kondisi lingkungan, dan kebutuhan aplikasi tertentu.