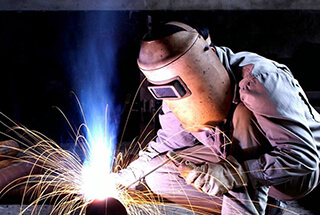
Pernahkah Anda bertanya-tanya mengapa beberapa logam mengelas dengan mulus sementara yang lain retak dan patah? Artikel ini mengeksplorasi dunia pengelasan yang menarik, dengan fokus pada baja karbon dan berbagai bentuknya. Pelajari bagaimana kandungan karbon, kotoran, dan metode pengelasan memengaruhi kekuatan dan daya tahan sambungan las. Bersiaplah untuk mengungkap rahasia pengelasan yang sukses!
Kemampuan las mengacu pada kemampuan material untuk dilas menjadi komponen yang memenuhi persyaratan desain yang ditentukan dalam kondisi konstruksi yang ditentukan dan untuk memenuhi persyaratan layanan yang telah ditentukan.
Kemampuan las dipengaruhi oleh empat faktor: material, metode pengelasan, jenis komponen, dan persyaratan penggunaan.
Paduan Besi-Karbon adalah paduan biner yang terdiri dari besi dan karbon. Ini adalah jenis material berbasis besi yang paling banyak digunakan. Baja karbon dan besi tuang adalah bahan dari paduan besi-karbon. Paduan dengan karbon kurang dari 0,0218% dikenal sebagai besi murni industri. Paduan besi-karbon dengan karbon kurang dari 2,11% disebut sebagai baja.
Paduan dengan karbon lebih dari 2.11% dikenal sebagai besi tuang. Selain karbon, baja karbon dan besi tuang mengandung pengotor seperti silikon, mangan, belerang, fosfor, nitrogen, hidrogen, dan oksigen; pengotor ini dapat mempengaruhi sifat baja.
1. Klasifikasi Baja Karbon
(1) Berdasarkan Kandungan Karbon
(2) Berdasarkan Kualitas Baja
(3) Berdasarkan Penggunaan Baja
(4) Berdasarkan Tingkat Deoksidasi Baja:
Metode Penunjukan
Q235-AF
Q235-AF menandakan baja struktural karbon dengan titik leleh ≥235MPa, yang termasuk dalam baja didih kelas A.
Nilai kualitas adalah sebagai berikut:
Sifat-sifat baja karbon terutama ditentukan oleh kandungan karbonnya. Korelasi antara kandungan karbon, kemampuan lasserta struktur dan kinerja baja karbon dapat dilihat pada Gambar 2-1 dan Tabel 2-1.
Tabel 2-1: Kemampuan Las dari Berbagai Jenis Baja Karbon
Nama | Kandungan Karbon | Kekerasan Khas | Penggunaan Khas | Kemampuan las |
Baja Karbon Rendah | ≤0,15% | HRB | Pelat khusus dan lembaran tipis berprofil, strip, dan kabel las | Luar biasa |
0.15%~0.25% | 30-35HRB | Profil, pelat, dan batang struktural | Bagus. | |
Baja Karbon Sedang | 0.25%~0.60% | 42-46HRC | Suku cadang dan peralatan mekanis | Rata-rata (biasanya membutuhkan pemanasan awal, direkomendasikan metode pengelasan hidrogen rendah) |
Baja Karbon Tinggi | > 0,60%-1,00 | 55HRC | Mata air, cetakan | Buruk (membutuhkan metode pengelasan hidrogen rendah, pemanasan awal, dan pemanasan akhir) |
Meskipun kekuatan baja karbon relatif rendah, baja ini mudah dilebur, memiliki kemampuan proses yang sangat baik, dan tidak mahal. Ini membanggakan keunggulan kemampuan menempakemampuan las, dan kinerja pemotongan. Baja karbon biasanya dipasok ke pasar dalam berbagai bentuk dan ukuran, seperti baja bulat, baja persegi, I-beam baja, dan tulangan.
Baja karbon rendah, dengan kandungan karbon serendah 0,25% atau kurang, dan kandungan M dan Si yang minimal, memiliki kecenderungan pengerasan yang rendah, menjadikannya jenis baja yang paling mudah dilas. Selain C, M, dan Si, pengotor seperti S, P, O, N pada baja karbon dapat mempengaruhi sifat mekaniknya, retak dingin pada sambungan las, retak panas, dan sensitivitas terhadap kerapuhan akibat usia. Sifat mekanik baja karbon rendah yang umum adalah seperti yang ditunjukkan pada Tabel 2-2.
Tabel 2-2 Sifat Mekanis Baja Karbon Rendah
Kelas | Tingkat | Uji Tarik (Tidak Kurang dari) | Uji Dampak | Uji Lentur Dingin 180°, B = 2a | ||||
Titik Hasil /MPa | Kekuatan Tarik /MPa | Tingkat Perpanjangan | Suhu /℃ | Energi Penyerapan Dampak Charpy V-Notch (Longitudinal) / J≥ | ||||
Diameter Inti Lentur d | ||||||||
Spesimen Longitudinal | Spesimen Melintang | |||||||
Q195 | – | 195 | 315-430 | 33 | – | – | 0 | 0.5a |
Q215 | A | 215 | 335-410 | 31 | – | – | 0.5a | a |
B | 20 | 27 | ||||||
Q235 | A | 235 | 370-500 | 26 | – | – | a | 1.5a |
B | 20 | 27 | ||||||
– | 0 | |||||||
D | -20 | |||||||
Q275 | A | 275 | 410-540 | 22 | – | – | 1.5a | 2a |
B | 20 | 27 | ||||||
C | 0 | |||||||
D | -20 | |||||||
Q245R | – | 245 | 400-520 | 25 | 0 | 31 | 1.5a | |
(20g, 20R) |
Aplikasi:
Umumnya, tidak ada perlakuan panas yang dilakukan setelah pembentukan. Sebagian besar digunakan secara langsung dalam keadaan canai panas.
Baja karbon dan baja paduan rendah dikategorikan berdasarkan komposisi kimianya ke dalam tiga kelompok: baja karbon, baja paduan rendah, dan baja paduandengan baja karbon (umumnya disebut sebagai baja karbon) yang paling banyak digunakan.
Selain karbon, yang merupakan elemen paduan utama dalam baja karbon, ada juga silikon (Si <0,5%), mangan (Mn <0,8%), dan pengotor yang tidak dapat dihindari seperti belerang dan fosfor.
Baja paduan rendah berasal dari baja karbon, dan satu atau lebih elemen paduan sengaja ditambahkan untuk mendapatkan sifat tertentu. Misalnya, baja 16Mn.
Klasifikasi dan Penggunaan Baja Paduan:
Total kandungan elemen paduan:
1. Analisis Kemampuan Las Baja Karbon Rendah
Kemampuan las baja karbon memburuk dengan meningkatnya kandungan karbon. Saat memilih bahan pengelasantidak hanya harus sesuai dengan material induk dalam komposisi dan sifat, tetapi elemen berbahaya seperti sulfur dan fosfor harus dihindari agar tidak masuk ke dalam logam las.
Kapan pengelasan baja karbon dengan kandungan karbon lebih tinggi dari 0,25%, sumber hidrogen harus diminimalkan.
Alasan mekanis terjadinya retakan saat mengelas baja karbon adalah tegangan pembatas struktural dan tegangan termal yang tidak merata. Langkah-langkah teknologi yang berbeda harus diambil tergantung pada kandungan karbon.
Untuk baja karbon rendah, perhatian khusus harus diberikan untuk mencegah retakan yang disebabkan oleh tegangan pembatas struktural dan tegangan termal yang tidak merata. Selain mencegah retakan yang disebabkan oleh tekanan ini, baja karbon tinggi terutama harus menghindari retakan yang disebabkan oleh pengerasan.
Kemampuan las baja karbon terutama bergantung pada kerentanannya terhadap retak dingin, retak panas, dan ketangguhan sambungan. Kandungan karbon baja dan logam yang diendapkan memiliki dampak paling signifikan terhadap keretakan dingin baja karbon.
Setara dengan karbon: CE = C + Mn/6 + Si/24
Untuk baja karbon, kandungan silikonnya relatif rendah, tidak melebihi 0,5%. Terkadang, dampaknya dapat diabaikan. Ketika nilai Carbon Equivalent (CE) meningkat, kecenderungan retak dingin meningkat, dan kemampuan las memburuk. Biasanya, ketika nilai CE melebihi 0,40%, sensitivitas terhadap retak dingin meningkat.
Kecenderungan pengerasan las dan zona yang terpengaruh panas, serta kerentanannya terhadap retak dingin, tidak hanya terkait dengan komposisi, tetapi dampak struktur terhadap kinerja bahkan lebih signifikan. Dengan komposisi tertentu, struktur bergantung pada laju pendinginan, yang dapat ditentukan melalui struktur SHCCT (Simulated Heat Affected Zone Continuous Cooling Transformation). Gambar 2-2 menyajikan diagram SHCCT baja Q235 (A3).
Mengontrol laju pendinginan area pengelasan adalah metode penting untuk mengubah jenis struktur dan kekerasan zona pengelasansehingga mengurangi terjadinya retak dingin.
Saat ketebalan lasan meningkat, atau ketika suhu lingkungan lebih rendah selama pengelasan, atau energi kawat las lebih kecil, pembuangan panas semakin cepat, dan kecepatan pendinginan sambungan las meningkat, yang pada gilirannya meningkatkan kecenderungan retak dingin.
Sambungan T dan sambungan pangkuan memiliki area pembuangan panas yang lebih besar dibandingkan dengan sambungan butt, sehingga mempercepat laju pendinginan di zona pengelasan dan membuatnya rentan terhadap pembentukan struktur yang mengeras.
Pemanasan awal, menaikkan suhu di antara jalur atau lapisan pengelasan, atau tindakan pasca-pemanasan juga dapat mengurangi kecepatan pendinginan selama pengelasan.
Pengerasan baja karbon terutama disebabkan oleh pembentukan struktur martensit. Martensit adalah larutan jenuh karbon dalam α-Fε, dan kekerasannya terkait dengan kandungan karbon dalam baja dan jumlah martensit yang terbentuk. Jumlah martensit dipengaruhi oleh laju pendinginan; kecepatan pendinginan yang sangat cepat dapat menghasilkan martensit 100%, sehingga mencapai kekerasan tertinggi.
Hidrogen dan Tingkat Pengekangan
Hidrogen di area pengelasan terutama berasal dari bahan las dan kelembapan di zona pengelasan. Hidrogen terlarut dalam lasan dapat dikurangi dengan menggunakan bahan las rendah hidrogen, meningkatkan suhu pengeringan bahan las, mengurangi kadar air dalam gas pelindungatau menurunkan kelembapan di area pengelasan.
Peningkatan ketebalan pelat baja atau kekakuan struktur akan meningkatkan tingkat pengekangan, sehingga meningkatkan sensitivitas terhadap retak yang disebabkan oleh hidrogen.
Tiga pemicu utama sensitivitas retak dingin adalah struktur yang dikeraskan, hidrogen, dan tegangan pengekangan. Ketika komposisi baja tetap, semakin tinggi proporsi struktur yang dikeraskan, semakin rendah kandungan hidrogen kritis yang diperlukan untuk menyebabkan retak dingin, dan semakin rendah tegangan pengekangan yang diperlukan, sehingga meningkatkan kecenderungan retak dingin.
Ketika struktur dan kandungan hidrogen tetap, semakin besar tingkat pengekangan, semakin tinggi sensitivitas terhadap retak dingin. Oleh karena itu, dalam kecenderungan baja karbon terhadap retak dingin, ketiga faktor struktur yang diperkeras, hidrogen, dan tegangan pengekangan saling mendorong satu sama lain dan saling bergantung.
Retak Panas
Kerentanan retak panas berkaitan erat dengan pengotor seperti sulfur (S) dan fosfor (P) di dalam baja. Selama pengelasan baja karbon dengan kandungan S dan P yang tinggi, senyawa S dan P dengan titik leleh rendah berkumpul pada batas butir di zona yang terpengaruh panas, menyebabkan retakan likuidasi di dekat garis fusi zona yang terpengaruh panas.
Untuk pelat baja yang lebih tebal, sulfida yang terdistribusi di sepanjang zona pemisahan yang berbeda dapat menyebabkan retak sobek laminar pada sambungan T dan lainnya. Ketika tingkat pengenceran bahan dasar tinggi, lebih banyak S dan P yang masuk ke dalam jahitan lasyang dapat dengan mudah menyebabkan retak panas pada lapisan las.
Untuk menghindari hal ini, desain sambungan atau operasi proses harus mencegah agar lapisan las tidak memiliki bentuk yang sempit dan dalam. Rendah karbon busur baja Lapisan las biasanya memiliki ketahanan yang lebih tinggi terhadap retak panas.
Robekan Laminar
Baja yang mendidih memiliki kandungan oksigen yang lebih tinggi dan pita pemisahan yang terlihat di tengah ketebalan pelat, yang dapat menyebabkan keretakan dan porositas selama pengelasan. Ada kecenderungan tertentu untuk terjadinya robekan laminar pada pengelasan pelat tebal, dan juga menunjukkan tingkat sensitivitas penuaan yang tinggi. Suhu transisi getas dari sambungan las juga berada di sisi yang lebih tinggi.
Oleh karena itu, baja didih biasanya tidak digunakan dalam struktur manufaktur yang mengalami beban dinamis atau beroperasi pada suhu rendah.
Perubahan Performa Zona yang Terpengaruh Panas Selama Pengelasan
Perubahan utama adalah pada keuletan sambungan, yang bergantung pada komposisi baja, kondisi perlakuan panas bahan dasar sebelum pengelasan, dan panas pengelasan proses. Baja karbon terutama dikirim dalam keadaan canai panas, tetapi untuk beberapa baja struktural karbon berkualitas tinggi dan baja struktural karbon untuk tujuan khusus, status pengiriman juga dapat dikontrol dengan penggulungan, normalisasi, normalisasi + temper, atau pendinginan + temper.
Selama proses pendinginan baja, deformasi besar diterapkan pada suhu yang lebih rendah sebelum austenit terurai, yang meningkatkan laju nukleasi fasa ferit. Butiran yang dihasilkan secara signifikan disempurnakan, sehingga secara drastis meningkatkan kekuatan dan keuletannya.
Tertentu metode pengelasan memiliki sumber panas yang tersebar atau energi linier yang terlalu tinggi, seperti pengelasan gas dan pengelasan electroslag. Metode ini menyebabkan butiran di zona butiran kasar pada area yang terpengaruh panas las menjadi lebih besar, sehingga mengurangi ketangguhan benturan pada sambungan. Akibatnya, perlakuan panas pasca las sering kali diperlukan untuk struktur yang signifikan.
Kesimpulannya, baja karbon rendah memiliki kandungan karbon yang rendah dan sangat rendah elemen paduan konten. Oleh karena itu, dengan menggunakan metode pengelasan konvensional, tidak akan ada struktur yang mengeras atau retakan dingin di dalam sambungan. Selama bahan pengelasan dipilih dengan benar, memuaskan sambungan las dapat dicapai.
2. Metode Pengelasan
Tidak ada persyaratan khusus untuk memilih metode pengelasan untuk baja karbon rendah. Pemilihan dapat dilakukan berdasarkan variabel seperti ketebalan material, struktur produkpersyaratan kinerja, dan kondisi produksi.
Logam berpelindung pengelasan busur, CO2 pengelasan berpelindung gas, dan pengelasan busur terendam adalah metode pengelasan yang umum digunakan.
3. Analisis Kemampuan Las Baja Karbon Sedang
Retak Dingin
Baja karbon sedang memiliki karbon yang lebih tinggi daripada baja karbon rendah. Jika kandungan karbon melebihi 0.25%, maka kemampuan pengerasan baja akan meningkat. Selama pengelasan, jika kecepatan pendinginan cepat (seperti yang ditunjukkan pada diagram CCT baja 45 pada Gambar 2-3, kecepatan pendinginan melebihi titik nilai kritis c), a struktur martensit akan terbentuk di zona yang terpengaruh panas.
Struktur martensitik baja karbon sedang lebih rapuh, dan di bawah pengaruh tekanan pengelasan, rentan terhadap retak dingin dan patah getas. Zona yang terpengaruh panas dari baja karbon sedang lebih cenderung membentuk struktur martensitik yang mengeras setelah pengelasan. Struktur ini lebih sensitif terhadap hidrogen, dan tegangan kritis yang dibutuhkan untuk retak dingin lebih rendah.
Oleh karena itu, disarankan untuk menggunakan elektroda hidrogen rendah dan meningkatkan suhu pemanasan awal secara tepat untuk mengurangi tegangan sisa.
Retak Panas
Ketika fraksi massa karbon dalam baja melebihi 0.25%, pemisahan karbon itu sendiri dan peningkatan unsur-unsur lain seperti sulfur (S) dan fosfor (P) menjadi sangat menonjol. Hal ini terutama terjadi ketika kandungan S dan P dalam material induk dikontrol di dekat batas atas dari nilai yang memenuhi syarat yang disyaratkan oleh standar. Sulfida dengan titik leleh rendah dapat menyebabkan peningkatan kecenderungan terjadinya retak panas, terutama pada lubang busur.
Oleh karena itu, dalam pengelasan baja karbon, kontrol yang ketat terhadap fraksi massa sulfur adalah suatu keharusan.
Pori-pori
Karena kandungan karbon yang lebih tinggi dibandingkan dengan baja karbon rendah, jumlah karbon yang masuk ke dalam weld pool meningkat. Hal ini berpotensi menyebabkan terbentuknya pori-pori CO selama reaksi metalurgi pengelasan, sehingga meningkatkan sensitivitas terhadap pembentukan pori-pori pada lapisan las.
Saat mengelas baja mendidih, sangat penting untuk memastikan bahwa bahan las yang dipilih mengandung deoxidizer yang memadai untuk mencegah terbentuknya pori-pori pada lapisan las.
Perubahan Performa Zona yang Terpengaruh Panas dalam Pengelasan
Zona yang terpengaruh panas dalam pengelasan mengalami perubahan akibat munculnya struktur yang mengeras, sehingga meningkatkan kekuatan, kerapuhan, dan pengerasan, serta kerentanan yang lebih tinggi terhadap keretakan dingin. Karbon dari logam induk yang meleleh masuk ke dalam kolam las, yang menyebabkan peningkatan kandungan karbon pada logam las. Performa bervariasi di antara jalur las karena perbedaan tingkat pengenceran.
Ketika kandungan karbon dalam baja karbon sedang meningkat, kemampuan lasnya akan menurun. Masalah utama yang dihadapi selama pengelasan adalah retak panas, retak dingin, porositas, dan patah getas, dan terkadang terjadi penurunan kekuatan pada zona yang terpengaruh panas. Semakin banyak kotoran dalam baja dan semakin besar kekakuan struktural, semakin parah masalah ini.
Ketika pekerjaan perbaikan pengelasan dilakukan pada coran baja karbon sedang, tindakan pencegahan harus dilakukan untuk mencegah retak dingin selama pengelasan atau retak karena tegangan sisa yang berlebihan di area yang diperbaiki.
4. Metode Pengelasan
Biasanya, pengelasan elektroda tongkat atau metode pengelasan berpelindung gas CO2 digunakan. Saat menambahkan permukaan tahan aus atau tahan korosi pada baja karbon sedang, atau memperbaiki permukaan aus yang lebih besar pada baja karbon sedang, pengelasan busur terendam juga dapat digunakan.
5. Analisis Kemampuan Las Baja Karbon Tinggi
Kemampuan Las yang Buruk
Baja karbon tinggi, yang meliputi baja karbon struktural, baja karbon tuang, dan baja perkakas karbon, mengandung lebih dari 0,6% karbon. Kemampuan las material ini cukup buruk, dan pengelasan dapat menghasilkan martensit karbon tinggi yang keras dan rapuh. Mereka memiliki kecenderungan tinggi untuk mengeras dan retak. Mengingat kemampuan lasnya yang buruk dan kekerasannya yang tinggi, ini jenis baja biasanya digunakan pada komponen atau suku cadang yang membutuhkan kekerasan dan ketahanan aus yang tinggi, bukan pada pembuatan struktur yang dilas.
Metode pengelasan: Pengelasan busur logam berpelindung dan pengelasan gas biasanya digunakan untuk pengelasan perbaikan.
Baja tahan karat mengacu pada jenis baja yang tidak mudah berkarat di atmosfer; baja ini lebih tahan terhadap korosi dalam kondisi asam, basa, dan garam tertentu. Karena ketahanan korosi, sifat mampu bentuk, dan ketangguhannya yang sangat baik pada rentang suhu yang luas, baja tahan karat banyak digunakan dalam petrokimia, energi nuklir, industri ringan, tekstil, makanan, dan peralatan rumah tangga.
1. Klasifikasi Baja Tahan Karat
(1) Baja Tahan Karat Austenitik
Baja tahan karat austenitik dibedakan berdasarkan sifat non-magnetisnya, kinerja suhu rendah yang baik, kemampuan bentuk, dan kemampuan las.
Baja tahan karat feritik dicirikan oleh daya tarik yang kuat, mudah dibentuk, tahan karat, dan tahan lubang.
(3) Baja Tahan Karat Martensitik
Baja tahan karat martensitik dikenal dengan kualitasnya yang tinggi kekuatan dan kekerasanmeskipun ketahanan korosinya sedikit lebih rendah daripada baja tahan karat austenitik dan feritik.
(4) Baja Tahan Karat Dupleks
Baja tahan karat dupleks menunjukkan tinggi kekuatan luluhtahan terhadap korosi sumuran dan korosi tegangan, serta mudah dibentuk dan dilas.
(5) Baja Tahan Karat Pengerasan Curah Hujan
Baja tahan karat pengerasan presipitasi memiliki kandungan kromium sekitar 17%, dan ditambah dengan unsur-unsur seperti nikel dan molibdenum, baja ini tidak hanya memiliki sifat tahan karat yang memadai tetapi juga menunjukkan ketahanan korosi yang sebanding dengan baja tahan karat austenitik.
2. Peran Elemen Paduan
Besi: Ini adalah elemen logam dasar dalam baja tahan karat.
Kromium: Merupakan elemen pembentuk ferit utama. Ketika dikombinasikan dengan oksigen, kromium membentuk lapisan pasif Cr2O3 yang tahan korosi, menjadikannya elemen penting untuk menjaga ketahanan korosi baja tahan karat.
Karbon: Karbon adalah elemen pembentuk austenit yang kuat yang secara khusus dapat meningkatkan kekuatan baja. Namun, karbon juga dapat mempengaruhi ketahanan terhadap korosi.
Nikel: Ini adalah elemen pembentuk austenit utama. Nikel dapat memperlambat korosi baja dan pembesaran butiran selama pemanasan.
Molibdenum: Ini adalah elemen yang membentuk karbida. Karbida yang dibentuknya sangat stabil, mencegah pertumbuhan butir selama austenit memanaskan dan mengurangi sensitivitas panas berlebih pada baja.
Niobium, Titanium: Ini adalah elemen pembentuk karbida yang kuat yang meningkatkan ketahanan baja terhadap korosi antar butir.
Nitrogen: Nitrogen adalah elemen pembentuk austenit yang kuat yang secara signifikan meningkatkan kekuatan baja.
Fosfor, Belerang: Ini berbahaya elemen dalam baja tahan karat mempengaruhi ketahanan korosi dan sifat stamping.
3. Fisik Umum Sifat-sifat Baja Tahan Karat
(1) Konduksi Panas: Laju perpindahan panas baja tahan karat relatif lambat.
(2) Ekspansi Termal: Dibandingkan dengan baja karbon, koefisien muai panjang baja kelas 304 lebih besar.
(3) Hambatan Listrik: Pada umumnya, hambatan listrik paduan lebih tinggi daripada logam murni, dan hal yang sama berlaku untuk baja tahan karat.
(4) Sifat Magnetik Baja Tahan Karat
Tabel 3: Sifat Magnetik dari Berbagai Bahan
Bahan | Sifat Magnetik | Permeabilitas Magnetik: μ (H = 50e) |
SUS430 | Magnet yang kuat | – |
Besi | Magnet yang kuat | – |
Ni | Magnet yang kuat | – |
SUS304 | Non-Magnetik (menunjukkan daya tarik selama pekerjaan dingin) | 1.5 (Pemrosesan 65%) |
SUS301 | Non-Magnetik (menunjukkan daya tarik selama pekerjaan dingin) | 14.8 (Pemrosesan 55%) |
SUS305 | Non-Magnetik | – |
1. Kemampuan Las Baja Tahan Karat
Hambatan listrik baja tahan karat secara signifikan lebih tinggi daripada baja karbon rendah. Selama pengelasan, kedua batang las dan material induk di area pengelasan rentan terhadap pemanasan dan peleburan. Hal ini dapat menyebabkan material dasar di sekitarnya menjadi terlalu panas, sehingga mengakibatkan deformasi yang tidak merata di area pengelasan dan butiran kasar.
Baja tahan karat memiliki koefisien muai panjang yang tinggi dan koefisien konduktivitas termal yang rendah, sehingga menyulitkan panas untuk menghilang. Selama pengelasan, kedalaman penetrasi tinggi, dan pemanasan dari pengelasan menyebabkan struktur mengembang. Selama pendinginan, terjadi deformasi penyusutan yang signifikan dan tegangan tarik, yang dapat dengan mudah menyebabkan keretakan termal.
Zona yang terpengaruh panas (HAZ) dalam pengelasan dapat dengan mudah menyebabkan korosi intergranular. Hal ini karena, di dalam HAZ, logam dasar menjadi terkuras kromiumnya pada kisaran suhu sensitisasi (450°C hingga 850°C), sehingga sulit untuk dipasivasi.
Akibatnya, ketahanan korosinya menurun secara signifikan, dan karenanya, lebih disukai terkorosi di lingkungan korosif yang sesuai, memperluas batas butir baja. Pada titik ini, plastisitas dan kekuatan area yang terkorosi telah sangat terganggu, yang menyebabkan retakan dan patah getas selama pembengkokan dingin, dan a non-logam suara ketika bagian yang terkorosi menyentuh tanah.
Baja tahan karat adalah jenis baja yang relatif tahan korosi, tetapi tidak sepenuhnya tahan karat. Hingga saat ini, belum ditemukan baja yang tidak berkarat dalam kondisi apa pun. Oleh karena itu, jenis baja tertentu didesain untuk digunakan dalam lingkungan tertentu.
Ketahanan korosi baja meningkat seiring dengan kandungan kromium. Ketika kandungan kromium mencapai atau melebihi 12%, ketahanan korosi baja berubah secara dramatis, bergeser dari rentan berkarat menjadi tahan karat, dan dari tidak tahan korosi menjadi tahan korosi. Oleh karena itu, baja tahan karat biasanya disebut sebagai paduan berbasis besi dengan kandungan kromium lebih dari 12%.
Kemampuan baja untuk mempertahankan stabilitas kimiawi (ketahanan terhadap korosi dan kerak) pada suhu tinggi disebut sebagai stabilitas termal; sifat baja untuk memiliki kekuatan yang cukup pada suhu tinggi disebut sebagai kekuatan termal. Baja yang memiliki stabilitas termal dan kekuatan termal dikenal sebagai baja tahan panas.
1. Klasifikasi Baja Tahan Panas
(1) Pada baja tahan panas pearlitic, elemen paduan utamanya adalah kromium, molibdenum, dan vanadium, dengan kandungan gabungan biasanya kurang dari 5%. Jenis ini juga disebut sebagai baja tahan panas paduan rendah.
(2) Baja tahan panas martensitik tidak hanya menampilkan kekuatan suhu tinggi tetapi juga menunjukkan ketahanan korosi yang luar biasa. Baja 1Cr13 dan 2Cr13 dapat berfungsi sebagai baja tahan panas dan juga baja tahan karat.
(3) Baja Tahan Panas Feritik
Jenis baja ini memiliki ketahanan yang sangat baik terhadap oksidasi dan korosi suhu tinggi, tetapi memiliki kekuatan panas yang buruk dan rentan terhadap kerapuhan.
(4) Baja Tahan Panas Austenitik
Baja jenis ini tidak hanya memiliki kekuatan panas yang tinggi, tetapi juga menunjukkan plastisitas, ketangguhan, dan sifat pengelasan yang sangat baik. Karena struktur austenitik fase tunggal, baja ini juga memiliki ketahanan korosi yang unggul.
1. Kemampuan Las Baja Tahan Panas Pearlitic
Elemen utama dalam baja tahan panas pearlitic adalah karbon, dan mengandung sejumlah kromium dan molibdenum. Beberapa varietas juga mengandung elemen seperti vanadium, tungsten, silikon, titaniumdan boron. Kehadiran elemen paduan ini membuat lapisan las dan zona yang terpengaruh panas rentan terhadap pengerasan.
Setelah pengelasan, pendinginan di udara dapat dengan mudah menghasilkan martensit yang keras dan rapuh, yang tidak hanya memengaruhi sifat mekanis sambungan las tetapi juga menghasilkan stres internal. Dikombinasikan dengan konsentrasi tinggi hidrogen yang menyebar, lapisan las dan zona yang terpengaruh panas rentan terhadap retak dingin.
Selain itu, karena baja tahan panas pearlitic mengandung karbida yang kuat seperti niobium, molibdenum, dan kromium, dan biasanya digunakan pada suhu tinggi, maka baja ini rentan terhadap retak akibat pemanasan ulang.
2. Kemampuan Las Baja Tahan Panas Martensitik
Baja tahan panas martensitik terutama mencakup baja kromium tinggi dengan komposisi sederhana, seperti Cr13 dan 2Cr13, serta baja yang menambahkan elemen paduan seperti Mo, V, W, Nb, dll., berdasarkan Chromium 12. Jenis baja ini cenderung mengalami pendinginan udara, yang menghasilkan kemampuan las yang buruk. Setelah pengelasan, mereka sering membentuk martensit dengan kekerasan tinggi dan sejumlah kecil struktur bainitik, yang menyebabkan keretakan dingin.
3. Kemampuan Las Baja Tahan Panas Feritik
Sebagian besar baja tahan panas feritik terdiri dari baja kromium tinggi dengan w(Cr)>17% dan sebagian baja tipe Cr13. Jenis baja ini tidak mengalami transformasi fasa α→Y selama pengelasan, sehingga tidak menunjukkan kecenderungan untuk mengeras. Namun, butiran di dekat garis fusi akan membesar dengan cepat, yang menyebabkan kerapuhan sambungan las.
Semakin tinggi kandungan kromium, dan semakin lama waktu tinggal pada suhu tinggi, maka kerapuhannya akan semakin parah. Kerapuhan ini tidak dapat disempurnakan melalui perlakuan panas, sehingga rentan terhadap keretakan ketika mengelas struktur yang kaku.
4. Kemampuan Las Baja Tahan Panas Austenitik
Baja tahan panas austenitik memiliki struktur mikro austenitik sebagai matriksnya. Jenis baja ini mengandung sejumlah besar nikel, mangan, dan nitrogen, yang merupakan elemen pembentuk austenit. Baja ini memiliki kekuatan suhu tinggi yang sangat baik dan stabilitas struktural di atas 600 ℃, dikombinasikan dengan kinerja pengelasan yang baik. Oleh karena itu, ini adalah jenis baja tahan panas yang paling banyak digunakan dalam aplikasi mulai dari 600 hingga 1200 ℃.