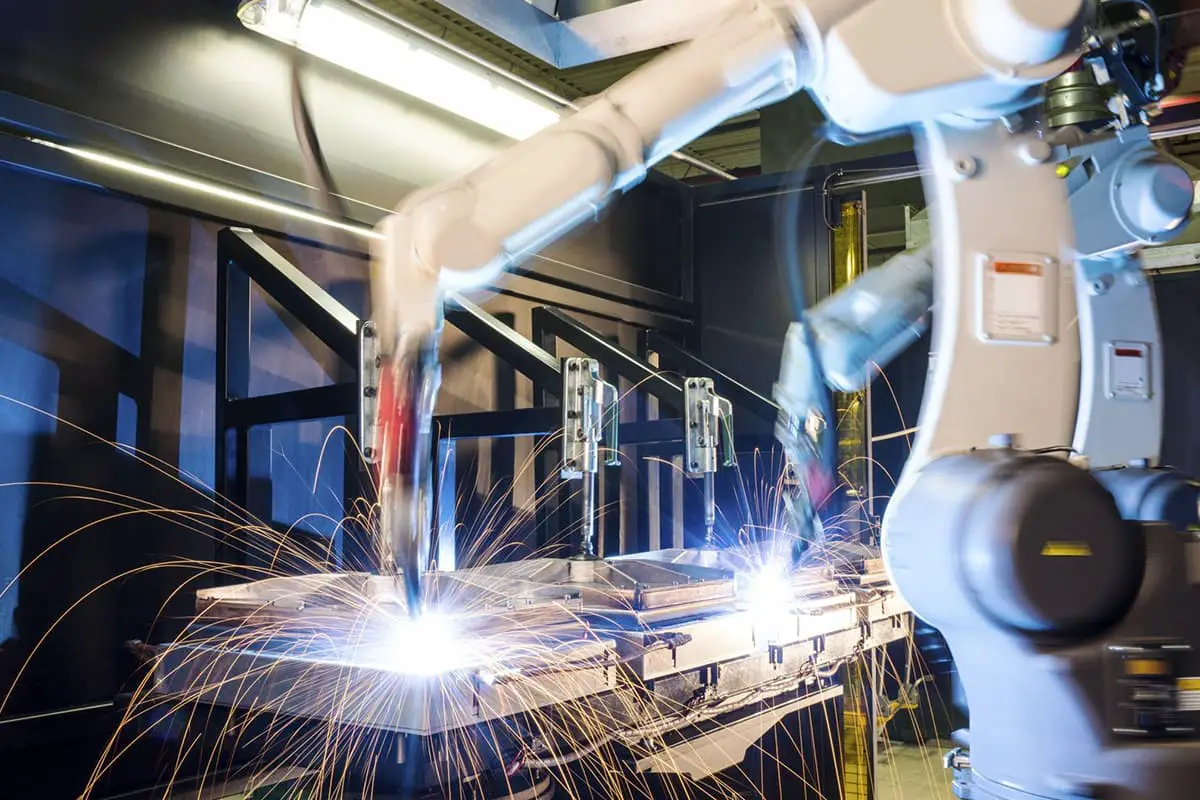
Pernahkah Anda bertanya-tanya bagaimana kualitas pengelasan berdampak pada keandalan produk elektronik? Dalam pengelasan, bahkan cacat kecil pun dapat menyebabkan kegagalan yang signifikan. Artikel ini membahas standar utama dan metode pemeriksaan untuk memastikan kualitas pengelasan, yang mencakup aspek-aspek seperti integritas listrik dan mekanik, penampilan, dan teknik pemeriksaan. Pada akhirnya, Anda akan memahami cara mengidentifikasi dan mencegah cacat pengelasan yang umum terjadi, sehingga dapat memastikan rakitan elektronik yang kuat dan andal. Selami dan temukan bagaimana menguasai standar ini dapat melindungi produk Anda dari kerusakan yang merugikan.
Pengelasan adalah proses teknologi yang signifikan dalam perakitan produk elektronik dan merupakan tahap yang sangat penting dalam pembuatannya.
Pengelasan digunakan secara luas dalam eksperimen, penyesuaian, dan produksi produk elektronik dan merupakan beban kerja yang substansial. Kualitas pengelasan secara langsung memengaruhi kualitas produk.
Sebagian besar kegagalan pada produk elektronik, selain masalah komponen, sebagian besar disebabkan oleh kualitas pengelasan. Oleh karena itu, menguasai keterampilan pengoperasian pengelasan yang mahir sangat penting untuk kualitas produk.
Persyaratan kualitas untuk titik pengelasan harus mencakup kontak listrik yang baik, kontak mekanis yang kokoh, dan penampilan yang estetis.
Aspek yang paling penting dalam memastikan kualitas titik pengelasan adalah menghindari sambungan solder dingin.
Pengelasan adalah cara utama untuk mewujudkan koneksi listrik secara fisik dalam sirkuit elektronik. Sambungan solder tidak dicapai dengan tekanan, tetapi dengan membentuk lapisan paduan padat selama proses proses pengelasan untuk mencapai tujuan sambungan listrik.
Jika solder hanya ditumpuk pada permukaan bagian yang dilas, atau hanya sebagian kecil saja yang membentuk lapisan paduan, mungkin akan sulit untuk mendeteksi masalah apa pun pada titik pengelasan selama pengujian dan pengoperasian awal.
Titik pengelasan semacam itu dapat melewatkan arus dalam jangka pendek, tetapi dengan perubahan kondisi dan berlalunya waktu, lapisan kontak teroksidasi, terpisah, dan menciptakan sirkuit yang terputus-putus atau tidak berfungsi.
Mengamati bagian luar titik pengelasan mungkin masih tampak baik-baik saja, yang merupakan masalah utama selama penggunaan instrumen elektronik dan masalah yang harus ditanggapi secara serius selama pembuatan produk.
Pengelasan tidak hanya berfungsi untuk sambungan listrik, tetapi juga memperbaiki komponen dan memastikan sambungan mekanis. Untuk memastikan bahwa bagian yang dilas tidak jatuh atau kendor ketika terkena getaran atau benturan, titik pengelasan harus memiliki kekuatan mekanis yang memadai.
Pada umumnya, hal ini dapat dicapai dengan menekuk terminal utama komponen yang akan dilas, kemudian melakukan pengelasan.
Paduan timah-timah, yang digunakan sebagai bahan solder, memiliki kekuatan yang relatif rendah, dengan kekuatan tarik bahan solder timah-timah yang umum digunakan sekitar 3-4,7kg/cm2, hanya 10% baja biasa.
Untuk meningkatkan kekuatan, diperlukan area sambungan yang memadai. Jika ini adalah sambungan solder dingin dengan solder yang hanya ditumpuk di atas bantalan solder, sambungan ini tidak akan memiliki kekuatan apa pun.
Titik pengelasan yang baik memerlukan jumlah solder yang sesuai, memiliki kilau logam, tidak memiliki paku atau jembatan, dan tidak merusak lapisan insulasi kawat atau komponen yang berdekatan. Penampilan yang baik mencerminkan kualitas pengelasan.
Catatan: Kehadiran kilau logam mengindikasikan kesesuaian suhu pengelasan dan pembentukan lapisan paduan, yang tidak hanya merupakan persyaratan untuk penampilan estetika.
Penampakan titik las yang khas digambarkan dalam Gambar 1, dengan karakteristik umum berikut ini:
Selain inspeksi visual (atau menggunakan kaca pembesar atau mikroskop) untuk memeriksa apakah titik las memenuhi standar di atas, inspeksi kualitas pengelasan juga mencakup hal-hal berikut: lasan yang hilang; solder runcing; korsleting yang disebabkan oleh solder di antara kabel (misalnya, "menjembatani"); kerusakan pada isolasi kawat dan komponen; pembentukan kawat; percikan solder.
Selama pemeriksaan, selain pemeriksaan visual, metode seperti sentuhan, pemeriksaan dengan pinset, dan penarikan kabel digunakan untuk memeriksa cacat seperti kerusakan kabel dan pengelupasan pad.
Inspeksi visual melibatkan pemeriksaan kualitas pengelasan dari perspektif eksternal untuk mengidentifikasi cacat pada titik las.
Isi utama inspeksi visual meliputi:
1. Apakah ada lasan yang hilang, yaitu titik lasan yang seharusnya disolder ternyata tidak ada.
2. Kilauan titik las.
3. Apakah ada solder yang cukup pada titik pengelasan.
4. Apakah ada fluks sisa di sekitar titik las.
5. Apakah ada pengelasan yang terus menerus dan apakah bantalannya terlepas.
6. Apakah titik las mengalami keretakan.
7. Apakah titik las tidak rata; apakah ada fenomena runcing pada titik las.
Gambar 2 menunjukkan bentuk titik las yang benar. Pada gambar tersebut, (a) adalah bentuk titik las yang disisipkan lurus, dan (b) adalah bentuk titik las yang setengah bengkok.
Pemeriksaan sentuh terutama mengacu pada apakah ada komponen yang longgar atau tidak dilas dengan aman ketika disentuh.
Menggunakan pinset untuk memegang kabel komponen dan menariknya secara perlahan untuk melihat apakah ada kelonggaran. Apakah solder di bagian atas terlepas ketika titik las digoyangkan.
Setelah pemeriksaan eksternal selesai dan pemasangan kabel dipastikan benar, pemeriksaan penyalaan dapat dilakukan, yang merupakan kunci untuk menguji performa sirkuit.
Jika pemeriksaan eksternal tidak dilakukan dengan ketat, pemeriksaan penyalaan tidak hanya akan menjadi lebih sulit, tetapi juga dapat merusak peralatan dan menyebabkan kecelakaan keselamatan.
Misalnya, jika sambungan catu daya tidak disolder dengan baik, maka perangkat tidak dapat dihidupkan selama pemeriksaan penyalaan, sehingga tidak memungkinkan untuk dilakukan pengecekan.
Inspeksi Penyalaan dan Analisis Akar Masalah
Inspeksi Elektrifikasi
(1) Kegagalan komponen
(2) Konduktivitas listrik yang buruk
Inspeksi penyalaan dapat mengungkapkan banyak cacat kecil, seperti penghubung sirkuit yang tidak terlihat secara kasat mata. Namun demikian, sulit untuk mendeteksi masalah potensial seperti penyolderan kering internal.
Oleh karena itu, solusi mendasar terletak pada peningkatan tingkat keterampilan operasi pengelasan, daripada menyerahkan tugas tersebut pada proses inspeksi.
Hubungan antara potensi kesalahan yang mungkin terjadi selama pemeriksaan penyalaan dan cacat pengelasan diilustrasikan pada Gambar 3 sebagai referensi.
Ada banyak penyebab cacat pengelasan. Dengan bahan tertentu (solder dan fluks) dan alat (besi solder, jig), metode yang digunakan dan rasa tanggung jawab operator menjadi faktor penentu.
Cacat umum yang terlihat pada pemosisian komponen PCBA dan sambungan solder ditunjukkan pada Tabel 1 dan 2.
Tabel-tabel ini mencantumkan tampilan, karakteristik, dan bahaya cacat sambungan solder yang umum terjadi, beserta analisis penyebabnya.
Tabel 1: Analisis Cacat Sambungan Solder yang Umum
Cacat titik pengelasan | Karakteristik Desain | Bahaya | Analisis Akar Masalah |
Pengelasan Salah![]() | Terdapat garis hitam yang berbeda antara solder dan timah komponen atau kertas tembaga, dengan solder yang surut ke arah batas. | Tidak dapat berfungsi dengan baik. | 1. 1. Kabel komponen tidak dibersihkan dengan benar, tidak dikalengkan dengan baik, atau solder telah teroksidasi. 2. Papan sirkuit cetak tidak dibersihkan secara menyeluruh, dan kualitas fluks yang digunakan di bawah standar. |
Korsleting solder![]() | Penyolderan yang berlebihan telah menyebabkan korsleting karena solder menjembatani antara titik-titik yang berdekatan. | Korsleting listrik. | 1. 1. teknik pengelasan tidak benar. 2. Ada kelebihan solder. |
Menjembatani![]() | Kabel yang berdekatan terhubung. | Korsleting listrik. | 1. Kabel komponen dibiarkan terlalu lama setelah pemotongan. 2. Sisa kabel komponen belum dibersihkan. |
Pengelasan gerakan gores![]() | Terdapat retakan, kasar seperti roti yang remuk, dengan celah pada sambungannya. | Kekuatannya rendah, tidak berfungsi atau hanya sesekali beroperasi. | Apabila solder masih basah dan mengalami pergerakan. |
Solder tidak mencukupi![]() | Area pengelasan kurang dari 75% pad, dan solder belum membentuk permukaan berlapis yang halus. | Kekuatan mekanis yang tidak memadai. | 1. Aliran solder yang buruk atau penarikan kawat las yang terlalu dini. 2. Fluks tidak mencukupi. 3. Durasi pengelasan terlalu singkat. |
Solder yang berlebihan![]() | Permukaan solder berbentuk cembung. | Membuang-buang solder berpotensi menyembunyikan cacat. | Penarikan kawat tertunda. |
Terlalu panas![]() | Titik lasan tampak putih, tidak berkilau metalik, dengan permukaan yang agak kasar. | Bantalan solder mudah terkelupas, sehingga kekuatannya berkurang. | Daya besi solder berlebihan, sehingga mengakibatkan waktu pemanasan yang lama. |
Penyolderan dingin![]() | Permukaannya tampak seperti butiran seperti tahu, dan kadang-kadang, mungkin ada retakan. | Kekuatannya rendah, dan konduktivitasnya buruk. | Aduk benda kerja sebelum solder mengeras. |
Tidak ada sumbu![]() | Apabila sudut kontak melebihi 90 derajat, solder tidak dapat menyebar atau menutupi, mirip dengan tetesan minyak yang menempel pada permukaan yang lembap. | Kekuatannya rendah, dan konduktivitasnya buruk. | Permukaan logam yang disolder tidak simetris, dan begitu juga dengan sumber panas itu sendiri. |
Kelonggaran![]() | Ujung kabel atau komponen dapat bergeser. | Konduktivitas yang buruk atau tidak ada konduktivitas. | 1. Kabel bergerak sebelum solder mengeras, sehingga menyebabkan celah. 2. 2. Timbal tidak diolah (pembasahan yang buruk atau tidak ada pembasahan). |
Menarik ke suatu titik![]() | Munculnya ujung tombak. | Penampilannya di bawah standar, yang dapat dengan mudah menyebabkan terjadinya bridging. | Besi solder yang tidak bersih, atau yang dilepas sebelum waktunya sebelum tempat penyolderan mencapai titik leleh solder, dapat mengakibatkan melekatnya solder dan pembentukan berikutnya saat ditarik. |
Lubang Jarum![]() | Inspeksi visual atau kaca pembesar berdaya rendah dapat menyingkapkan lubang pada kertas tembaga. | Kekuatan yang tidak mencukupi dapat menyebabkan titik-titik las rentan terhadap korosi. | Kontaminasi bahan penyolderan, bahan komponen, dan lingkungan. |
Delaminasi foil tembaga![]() | Kertas tembaga terkelupas dari papan sirkuit tercetak. | Papan sirkuit telah rusak. | Durasi pengelasan terlalu lama. |
Tabel 2: Analisis Standar dan Cacat Sambungan Solder SMT untuk Komponen yang Dipasang di Permukaan.
Proyek | Diagram | Poin-poin Penting | Alat Inspeksi | Kriteria Penilaian: |
1. Posisi komponen. | ![]() | Amplitudo 'W' dari elektroda sambungan mencakup lebih dari separuh permukaan konduksi. Penting: Inspeksi visual harus digunakan untuk mengidentifikasi pergeseran posisi komponen, bukan melalui verifikasi dengan tester. Sebagai gantinya, gunakan kaca pembesar untuk pengamatan langsung. | Kaliper | Lebih dari setengah |
2. Posisi komponen. | ![]() | Lebih dari separuh panjang E elektroda sambungan tertutupi permukaan konduksi. Perhatian: Inspeksi visual harus digunakan untuk menentukan offset posisi komponen, bukan dikonfirmasi dengan penguji dan diperiksa dengan kaca pembesar. | Kaliper | Lebih dari setengah |
3. Posisi komponen. | ![]() | Dari segi kemiringan bagian sambungan, cukup untuk mencakup lebih dari separuh amplitudo W elektroda sambungan pada permukaan konduktif. Catatan: Andalkan inspeksi visual untuk ketidaksesuaian posisi komponen, dan hindari menggunakan tester untuk konfirmasi; sebaliknya, gunakan kaca pembesar untuk pengamatan langsung. | Kaliper | Lebih dari setengah |
4. Jumlah solder. | ![]() 1/2F | Elektroda disolder dengan timah, yang luasnya melebihi setengah tinggi F dan setengah lebar W. | Kaliper | Lebih dari setengah |
5. Jumlah solder. | ![]() | Solder komponen sambungan ke arah yang lebih panjang, dari permukaan ujung elektroda sambungan, dengan ketebalan solder lebih dari 0,5 mm. Sebagai contoh, G. | Kaliper | Di atas 0.5mm |
6. Jumlah solder. | ![]() | Ketinggian solder harus kurang dari 0,3 mm di atas permukaan komponen sambungan. | Indikator Dial | Di bawah 0.3mm |
7. Jumlah solder. | ![]() | Penyolderan pada bagian sambungan tidak dapat tumpang tindih, seperti dalam bentuk "I". | Inspeksi Visual | Tidak dapat ditumpuk di atas |
8. Perlekatan bagian tersebut. | ![]() Produk Berkualitas | Tidak ada perekat antara elektroda komponen sambungan dan papan sirkuit tercetak. | Inspeksi Visual | Tidak boleh berada di bawah elektroda |
![]() Produk Berkualitas | ||||
9. Perlekatan bagian tersebut. | ![]() Produk yang cacat | Tidak ada perekat antara elektroda komponen sambungan dan papan sirkuit tercetak. | Inspeksi Visual | Tidak boleh berada di bawah elektroda |
10. Perlekatan bagian tersebut. | ![]() Tidak boleh mengandung bahan pengikat apa pun. | Perekat tidak boleh digunakan pada bagian elektroda komponen sambungan. | Inspeksi Visual | Tidak dapat menjadi perekat |
11. Posisi komponen. | ![]() Jangan Sentuh G | Posisi komponen sambungan tidak boleh diimbangi atau dimiringkan untuk menyentuh konduktor yang berdekatan. Untuk aspek yang tidak dapat ditentukan secara visual, gunakan instrumen pengujian. | Inspeksi Visual | Tidak dapat melakukan kontak |
12. Jumlah solder. | ![]() Solder meluap | Solder tidak boleh meluap melebihi lebar permukaan konduktif. | Inspeksi Visual | Tidak bisa meluap |
13. Posisi bagian tersebut. | ![]() | Lebih dari separuh lebar J kaki komponen IC berada di atas permukaan konduksi. | Kaliper | Lebih dari setengah |
14. Posisi bagian tersebut. | ![]() | Lebih dari setengah panjang, K, dari kaki komponen IC membuat kontak di atas permukaan konduksi. | Kaliper | Lebih dari setengah |
15. Posisi komponen. | ![]() | Perpindahan posisi komponen relatif terhadap konduktor yang berdekatan harus ≥0,2 mm; komponen tidak boleh bersentuhan dengan konduktor yang berdekatan. | Inspeksi Visual | Tidak dapat melakukan kontak |
16. Kaki tidak stabil. | ![]() | Untuk benda yang ujung ujungnya terangkat, pengangkatan harus kurang dari 0,5 mm. | Kaliper | Di bawah 0.5mm |
17. Kaki tidak stabil. | ![]() | Untuk benda yang alasnya terangkat, pengangkatan pada alasnya harus kurang dari 0,5 mm. | Pengukur 0,5 mm | Di bawah 0.5mm |
18. Kaki tidak stabil. | ![]() | Untuk benda yang seluruh kakinya dinaikkan, elevasi harus kurang dari 0,5mm. | Pengukur 0,5 mm | Di bawah 0.5mm |
19. Kaki tidak stabil. | ![]() | Ketinggian solder dari permukaan papan cetak ke puncak solder kurang dari 1mm. | Kaliper | Di bawah 1mm |
20. Kaki tidak stabil. | ![]() | Ketinggian solder yang terpasang pada kaki komponen kurang dari 0,5 mm. | Kaliper | Di bawah 0.5mm |