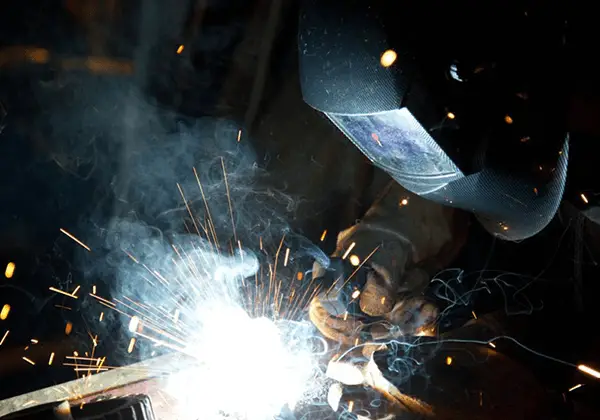
Immaginate di costruire un ponte o un grattacielo per poi vederlo crollare a causa di difetti inavvertiti nella saldatura. La resistenza alla fatica delle strutture saldate è un fattore critico per garantire la durata e la sicurezza di tali costruzioni. Questo articolo approfondisce le cause dei cedimenti per fatica, compresi gli effetti della resistenza al carico statico, della concentrazione delle sollecitazioni e dei difetti di saldatura. Grazie alla comprensione di questi fattori, gli ingegneri possono progettare e produrre strutture saldate più affidabili, evitando guasti catastrofici e prolungando la durata di vita di infrastrutture vitali.
Le cause della rottura per fatica delle strutture saldate comprendono diversi fattori critici:
Mentre i giunti saldati presentano in genere una capacità di carico statico paragonabile a quella del metallo di base, le loro prestazioni sotto carico ciclico sono significativamente compromesse. La resistenza alla fatica è fortemente influenzata dalla configurazione del giunto e dalla progettazione strutturale complessiva. Di conseguenza, spesso si verificano cedimenti prematuri nelle connessioni saldate, compromettendo l'integrità dell'intera struttura.
Storicamente, la progettazione delle strutture di saldatura ha dato priorità alla resistenza al carico statico, trascurando considerazioni cruciali sulla fatica. Questa dimenticanza, unita all'assenza di standard completi per la progettazione a fatica, ha portato a progetti di giunti non ottimali, oggi riconosciuti come inadeguati per carichi ciclici a lungo termine.
Esiste una carenza di conoscenze tra i progettisti e i tecnici di ingegneria riguardo alle caratteristiche uniche di resistenza alla fatica delle strutture saldate. Questa carenza si traduce spesso nell'applicazione inappropriata dei criteri di progettazione a fatica e delle forme strutturali delle strutture metalliche non saldate, senza affrontare le sfide specifiche poste dai giunti saldati.
④ La proliferazione delle strutture saldate, unita alle tendenze del settore che favoriscono l'economicità e la riduzione del peso, ha portato a un aumento dei carichi di progetto. Questa spinta all'ottimizzazione, se da un lato è vantaggiosa per gli scenari statici, dall'altro spesso aggrava i problemi legati alla fatica, spingendo i materiali verso i loro limiti di resistenza.
Con il crescente utilizzo di strutture saldate in applicazioni ad alta velocità e con carichi pesanti, si è intensificata la richiesta di capacità di carico dinamico. Tuttavia, la ricerca sulla resistenza alla fatica delle strutture saldate non ha tenuto il passo con l'evoluzione dei requisiti, creando una lacuna critica nella progettazione e nella previsione delle prestazioni.
Le concentrazioni di tensione intrinseche ai punti di saldatura e alle radici, insieme ai potenziali difetti di saldatura come la mancanza di fusione o la porosità, fungono da siti di innesco per le cricche da fatica. Queste discontinuità microstrutturali e geometriche riducono significativamente la durata a fatica dei componenti saldati rispetto alle loro controparti non saldate.
Le tensioni residue introdotte durante il processo di saldatura, in particolare le tensioni residue di trazione in prossimità della zona di saldatura, possono ridurre sostanzialmente la resistenza effettiva alla fatica della struttura, facilitando l'innesco e la propagazione di cricche sotto carico ciclico.
Nello studio dei materiali in ferro e acciaio, i ricercatori cercano di ottenere un'elevata resistenza specifica, ovvero la capacità di sostenere carichi pesanti pur essendo leggeri. Ciò consente alle strutture di avere una maggiore capacità portante a parità di peso o di avere la stessa capacità pur essendo più leggere. Di conseguenza, è stato sviluppato l'acciaio ad alta resistenza, che vanta un'elevata resistenza alla fatica.
La resistenza alla fatica dei metalli comuni aumenta con l'aumentare della resistenza al carico statico. Tuttavia, questo non vale per le strutture saldate. La resistenza alla fatica dei giunti saldati ha una correlazione limitata con la resistenza statica del metallo di base, del metallo saldato, della microstruttura e delle proprietà della zona termicamente alterata e della corrispondenza di resistenza del metallo saldato.
In altre parole, a parità di dettagli del giunto saldato, la resistenza alla fatica degli acciai ad alta resistenza e degli acciai a basso tenore di carbonio è la stessa, e presentano la stessa curva S-N. Questo vale per vari tipi di giunti, come giunti di testa, giunti d'angolo e travi saldate.
Maddox ha condotto uno studio sulla crescita delle cricche da fatica di acciaio al carbonio-manganese con un punto di snervamento compreso tra 386 e 636 MPa, e sul metallo saldato e le zone termicamente interessate saldate con sei diversi elettrodi.
I risultati indicano che le proprietà meccaniche del materiale hanno un certo impatto sul tasso di crescita delle cricche, ma l'effetto non è significativo.
Nella progettazione di strutture saldate sottoposte a carichi alternati, la scelta dell'acciaio ad alta resistenza non è significativa per soddisfare i requisiti ingegneristici. L'acciaio ad alta resistenza è necessario per il metallo di base del giunto saldato solo quando il rapporto di sollecitazione è superiore a +0,5 e la condizione di resistenza statica gioca un ruolo dominante.
La ragione di questi risultati è la presenza di difetti di cuneo di scoria simili a sottosquadri lungo la linea di fusione in corrispondenza del cordone di saldatura, con uno spessore compreso tra 0,075 mm e 0,5 mm e un raggio di punta inferiore a 0,015 mm. Questi difetti appuntiti sono l'origine di cricche da fatica, equivalenti allo stadio di formazione della cricca da fatica.
Pertanto, la vita a fatica del giunto sotto una certa ampiezza di sollecitazione è determinata principalmente dalla fase di propagazione della cricca da fatica. Questi difetti determinano lo stesso tipo di giunti saldati per tutti gli acciai che hanno la stessa resistenza alla fatica, indipendentemente dalla resistenza statica del metallo di base e dei materiali di saldatura.
2.2.1 Influenza del tipo di giunto
I giunti saldati comprendono giunti di testa, giunti a croce, giunti a T e giunti di sovrapposizione. Questi giunti sono suscettibili di concentrazione delle sollecitazioni a causa dell'interferenza della linea di trasmissione della forza.
L'interferenza della linea di stress dei giunti di testa è minima, con conseguente bassa concentrazione di stress e maggiore resistenza alla fatica rispetto ad altri giunti. Tuttavia, gli esperimenti hanno dimostrato che la resistenza alla fatica dei giunti di testa può variare notevolmente, a causa di vari fattori come la dimensione del campione, la forma della scanalatura, il metodo di saldatura, il tipo di elettrodo, la posizione di saldatura, la forma della saldatura, la lavorazione della saldatura post-saldatura e il trattamento termico post-saldatura.
L'uso di una piastra di supporto permanente in un giunto di testa può causare una significativa concentrazione di tensioni sulla piastra di supporto e ridurre la resistenza a fatica del giunto. Le cricche a fatica in questo tipo di giunto si verificano in corrispondenza della giunzione tra la saldatura e la piastra di supporto, piuttosto che in corrispondenza della punta della saldatura, e la resistenza a fatica è generalmente pari a quella di un giunto di testa con la forma peggiore senza piastra di supporto.
I giunti trasversali e i giunti a T sono ampiamente utilizzati nelle strutture saldate.
In questi giunti portanti, l'evidente cambiamento di sezione nel passaggio dalla saldatura al metallo base determina un fattore di concentrazione delle sollecitazioni più elevato rispetto al giunto di testa, con conseguente minore resistenza a fatica per i giunti a croce e a T rispetto ai giunti di testa.
Per i giunti non smussati collegati da saldature a filetto e giunti scanalati con saldature a penetrazione locale, le fratture per fatica possono verificarsi in due anelli deboli, cioè la giunzione tra il metallo di base e la punta della saldatura o la saldatura, quando la saldatura trasmette le sollecitazioni di lavoro. Per i giunti trasversali con scanalature a penetrazione, le fratture si verificano generalmente solo sulla punta della saldatura, non sulla saldatura.
La resistenza alla fatica dei giunti a T e dei giunti a croce, in cui la saldatura non sopporta le sollecitazioni di lavoro, dipende principalmente dalla concentrazione delle sollecitazioni alla giunzione tra la saldatura e la piastra principale sollecitata. I giunti a T hanno una resistenza alla fatica più elevata, mentre i giunti a croce hanno una resistenza alla fatica inferiore.
Il miglioramento della resistenza alla fatica dei giunti a T o a croce può essere ottenuto utilizzando la saldatura a scanalatura e lavorando la transizione della saldatura per creare una transizione liscia. Questa misura può migliorare notevolmente la resistenza alla fatica.
La resistenza alla fatica dei giunti di testa è molto bassa a causa della grave distorsione della linea di forza. L'utilizzo di un giunto di testa cosiddetto "rinforzato" con piastra di copertura è estremamente irragionevole.
L'uso di una piastra di copertura in un giunto di testa indebolisce significativamente la sua elevata resistenza alla fatica a causa di una maggiore concentrazione delle sollecitazioni.
Nei giunti di copertura portanti, le cricche da fatica possono verificarsi nel metallo di base o nella saldatura. Inoltre, modificando la larghezza della lamiera di copertura o la lunghezza della saldatura, si altera la distribuzione delle sollecitazioni nel metallo di base, influenzando la resistenza a fatica del giunto. La resistenza a fatica del giunto aumenta con l'aumentare del rapporto tra la lunghezza della saldatura e la larghezza della lamiera di copertura, in quanto tende a determinare una distribuzione più uniforme delle sollecitazioni nel metallo di base.
2.2.2 Influenza della forma della saldatura
Indipendentemente dalla forma del giunto, essi sono collegati da due tipi di saldature: saldature di testa e saldature di testa. saldature a filetto.
La forma delle saldature influisce sul fattore di concentrazione delle sollecitazioni, determinando variazioni significative nella resistenza alla fatica.
La forma della saldatura di testa ha il maggiore impatto sulla resistenza a fatica del giunto.
(1) Influenza dell'angolo di transizione
Yamaguchi et al. hanno stabilito la relazione tra la resistenza alla fatica e l'angolo di transizione (angolo ottuso esterno) tra il metallo base e il metallo saldato.
Nelle prove, la larghezza (W) e l'altezza (H) della saldatura sono cambiate, ma il rapporto H/W è rimasto costante, il che significa che l'angolo incluso è rimasto invariato. I risultati hanno mostrato che anche la resistenza alla fatica è rimasta invariata.
Tuttavia, quando la larghezza della saldatura è rimasta costante e l'altezza è cambiata, si è riscontrato che un aumento dell'altezza ha comportato una diminuzione della resistenza a fatica del giunto. Ciò è chiaramente dovuto alla diminuzione dell'angolo incluso esterno.
(2) Influenza del raggio di transizione della saldatura
I risultati della ricerca di Sander et al. indicano che anche il raggio di transizione della saldatura influisce significativamente sulla resistenza alla fatica del giunto. All'aumentare del raggio di transizione (mentre l'angolo di transizione rimane invariato), aumenta la resistenza alla fatica.
Anche la forma della saldatura di raccordo ha un impatto significativo sulla resistenza a fatica del giunto. Quando il rapporto tra lo spessore calcolato (a) di una singola saldatura e lo spessore della piastra (b) è inferiore a 0,6-0,7, generalmente si rompe nella saldatura. Quando a/b > 0,7, generalmente si rompe dal metallo base.
L'aumento delle dimensioni della saldatura non può modificare la resistenza di un'altra sezione debole, cioè il metallo di base all'estremità del cordone di saldatura, e quindi la resistenza alla fatica non può essere superata nel migliore dei casi.
Soete e Van Crombrugge hanno condotto prove su piastre di 15 mm di spessore saldate con diverse saldature a filetto sotto carico di fatica assiale.
I risultati hanno mostrato che quando il cordone di saldatura era di 13 mm, si verificavano fratture nel metallo di base o in corrispondenza del cordone di saldatura. Se il cordone di saldatura era inferiore a questo valore, si verificavano fratture da fatica nella saldatura. Quando la dimensione del cordone era di 18 mm, si verificavano fratture nel metallo di base.
Sulla base di questi risultati, hanno proposto un limite per le dimensioni del cordone di saldatura: S = 0,85B, dove S è la dimensione del cordone di saldatura e B è lo spessore della piastra.
Anche se la dimensione del cordone di saldatura ha raggiunto lo spessore della piastra (15 mm), si sono comunque verificate fratture nella saldatura, il che conferma i risultati teorici.
2.2.3 influenza di difetti di saldatura
Esistono numerosi tipi di tipi di difetti in corrispondenza del cordone di saldatura, che portano alla formazione precoce di cricche da fatica e a una significativa diminuzione della resistenza a fatica del metallo base (fino a 80%).
I difetti di saldatura possono essere generalmente suddivisi in due categorie:
I difetti planari (come cricche e mancanza di fusione) e volumetrici (come pori e inclusioni di scorie) hanno diversi gradi di influenza.
Inoltre, l'impatto di difetti di saldatura sulla resistenza a fatica dei giunti dipende dal tipo, dalla direzione e dalla posizione dei difetti.
1) Crepa
Crepe nella saldaturaCome le cricche fredde e calde, oltre alla microstruttura fragile, sono fonti significative di concentrazione delle tensioni e possono ridurre significativamente la resistenza alla fatica di strutture o giunti.
Studi precedenti hanno dimostrato che in un campione di giunto di testa in acciaio a basso tenore di carbonio con una larghezza di 60 mm e uno spessore di 12,7 mm, in presenza di cricche di 25 mm di lunghezza e 5,2 mm di profondità nella saldatura (che occupano circa 10% dell'area della sezione trasversale del campione), la resistenza a fatica sotto carico alternato si riduce da 55% a 65% dopo 2 milioni di cicli.
2) Penetrazione incompleta
È importante notare che la penetrazione incompleta non è sempre considerata un difetto, in quanto può essere intenzionalmente progettata per alcuni giunti, come gli ugelli dei recipienti a pressione.
I difetti di penetrazione incompleta possono essere superficiali (saldatura su un solo lato) o interni (saldatura su due lati) e possono essere locali o complessivi. Essi indeboliscono principalmente la sezione trasversale e causano la concentrazione delle tensioni.
I test hanno dimostrato che, rispetto ai risultati senza tali difetti, la resistenza alla fatica si riduce di 25%, il che significa che l'impatto non è così grave come quello delle cricche.
3) Fusione incompleta
Nonostante sia un problema importante, la ricerca su questo argomento è stata limitata a causa delle difficoltà di preparazione dei campioni.
Tuttavia, è chiaro che la mancanza di fusione è un tipo di difetto planare che non può essere ignorato. Spesso viene trattata come una forma di penetrazione incompleta.
4) Sottotaglio
I parametri principali che descrivono il sottosquadro sono la lunghezza (L), la profondità (h) e la larghezza (W).
Attualmente, il parametro principale che influenza la resistenza alla fatica è la profondità del sottosquadro (h), che può essere valutata in base alla profondità (h) o al rapporto tra la profondità e lo spessore della piastra (h/B).
5) Stomi
Harrison ha analizzato e riassunto i risultati dei test precedenti relativi ai difetti volumetrici.
La diminuzione della resistenza alla fatica è dovuta principalmente alla riduzione della sezione trasversale causata dai pori. Esiste una relazione lineare tra di essi.
Tuttavia, alcuni studi dimostrano che quando la superficie del campione viene lavorata e i pori si trovano sulla superficie o appena sotto di essa, l'impatto negativo dei pori aumenta. Essi agiscono come fonte di concentrazione delle sollecitazioni e diventano il punto di partenza delle cricche da fatica.
Ciò suggerisce che la posizione dei pori ha un impatto maggiore sulla resistenza alla fatica del giunto rispetto alla loro dimensione, e i pori situati sulla superficie o sotto di essa hanno l'effetto negativo più significativo.
6) Inclusione di scorie
La ricerca condotta da IIW ha dimostrato che, tra i difetti volumetrici, l'inclusione di scorie ha un impatto maggiore sulla resistenza alla fatica dei giunti rispetto alla porosità.
L'impatto dei difetti di saldatura sulla resistenza alla fatica dei giunti non dipende solo dalle dimensioni del difetto, ma è anche influenzato da vari altri fattori, come i difetti superficiali che hanno un impatto maggiore rispetto ai difetti interni e i difetti planari perpendicolari alla direzione della forza che hanno un impatto maggiore rispetto alle altre direzioni.
L'influenza dei difetti situati in aree di tensione residua di trazione è maggiore rispetto a quelli in aree di tensione residua di compressione, e i difetti situati in aree di concentrazione delle tensioni, come le cricche del cordone di saldatura, hanno un impatto maggiore rispetto agli stessi difetti in campi di tensione uniformi.
Saldatura sollecitazione residua è una caratteristica delle strutture saldate che viene ampiamente studiata per il suo impatto sulla resistenza alla fatica di queste strutture. Sono stati condotti numerosi studi sperimentali per esaminare questo problema.
Le prove di fatica vengono spesso eseguite confrontando campioni con sollecitazione residua di saldatura a quelli che sono stati sottoposti a trattamento termico per rimuovere le tensioni residue. Questo perché la generazione di tensioni residue di saldatura è spesso accompagnata da modifiche delle proprietà del materiale derivanti dal trattamento termico. ciclo termico di saldaturae il trattamento termico non solo elimina le tensioni residue, ma ripristina anche parzialmente o completamente le proprietà del materiale.
Tuttavia, a causa della variabilità dei risultati dei test, esistono interpretazioni diverse dei risultati e delle valutazioni dell'impatto delle tensioni residue di saldatura. Ciò si evince esaminando le prime e recenti ricerche condotte da vari soggetti.
Ad esempio, diversi ricercatori sono giunti a conclusioni diverse da prove di 2×106 cicli su giunti di testa con rinforzo.
È stato riscontrato che la resistenza alla fatica di un campione dopo il trattamento termico per alleviare le tensioni era superiore di 12,5% rispetto allo stesso campione allo stato saldato. Tuttavia, alcuni studi hanno rilevato che la resistenza alla fatica dei campioni saldati e trattati termicamente era la stessa, con poche differenze. In altri risultati, la resistenza alla fatica è aumentata dopo il trattamento termico per rimuovere le tensioni residue, ma l'aumento è stato molto inferiore a 12,5%.
Risultati simili sono stati riscontrati nelle prove di campioni di giunzione di testa con rettifica superficiale. Alcune prove hanno mostrato che la resistenza alla fatica poteva essere aumentata di 17% dopo il trattamento termico, mentre altre non hanno mostrato alcun miglioramento.
La questione è stata per qualche tempo fonte di confusione. Tuttavia, una serie di prove a carico alternato condotte da studiosi dell'ex Unione Sovietica ha contribuito a chiarire il problema. Particolarmente degna di nota è la ricerca di Trufyakov sull'effetto delle tensioni residue di saldatura sulla resistenza a fatica del giunto in presenza di diverse caratteristiche del ciclo di sollecitazione.
Le prove sono state eseguite con acciaio strutturale ordinario basso legato 14Mn2 e prevedevano una saldatura di testa trasversale sul campione, con un cordone di saldatura longitudinale sovrapposto su entrambi i lati.
Un gruppo di campioni è stato sottoposto a trattamento termico per eliminare le tensioni residue dopo la saldatura, mentre l'altro gruppo non è stato trattato. La prova di confronto della resistenza alla fatica è stata condotta utilizzando tre coefficienti caratteristici dei cicli di sollecitazione, r = -1, 0, e +0,3.
Sotto carico alternato (r = -1), la resistenza a fatica del campione con sollecitazione residua eliminata era vicina a 130 MPa, mentre il campione senza eliminazione aveva una resistenza a fatica di soli 75 MPa.
Sotto carico pulsante (r = 0), la resistenza alla fatica di entrambi i gruppi di campioni era la stessa, a 185 MPa.
Quando r = 0,3, la resistenza a fatica del campione con tensioni residue eliminate dal trattamento termico era di 260 MPa, leggermente inferiore a quella del campione senza trattamento termico, che aveva una resistenza a fatica di 270 MPa.
Le ragioni principali di questo fenomeno sono:
Quando il valore di r è alto, ad esempio sotto carico pulsante (r = 0), la resistenza alla fatica è elevata e la tensione residua viene rilasciata rapidamente sotto l'influenza di un'elevata sollecitazione di trazione, riducendo l'impatto della tensione residua sulla resistenza alla fatica. Quando r aumenta a 0,3, la sollecitazione residua diminuisce ulteriormente sotto carico, senza alcun effetto sulla resistenza alla fatica.
Il trattamento termico non solo elimina le tensioni residue, ma ammorbidisce anche il materiale, determinando una diminuzione della resistenza alla fatica dopo il trattamento.
Questa prova dimostra l'influenza delle tensioni residue e dei cambiamenti del materiale causati dal ciclo termico di saldatura sulla resistenza alla fatica. Indica inoltre che l'impatto delle sollecitazioni residue di saldatura sulla resistenza alla fatica di un giunto è legato alle caratteristiche del ciclo di sollecitazione del carico di fatica. Quando il valore caratteristico del ciclo è basso, l'impatto è relativamente alto.
In precedenza è stato osservato che, a causa delle tensioni residue che raggiungono le resa del materiale in una saldatura strutturale, in un giunto con un ciclo di sollecitazione ad ampiezza costante, il ciclo di sollecitazione effettivo in prossimità della saldatura scenderà al di sotto del punto di snervamento del materiale, indipendentemente dalle caratteristiche del ciclo originale.
Ad esempio, il ciclo di sollecitazione nominale dovrebbe essere compreso tra +S1 e -S2, con un intervallo di sollecitazione di S1 + S2. Tuttavia, il ciclo di sollecitazione effettivo nel giunto sarà compreso tra sy (ampiezza della sollecitazione al punto di snervamento) e SY-(S1 + S2).
Questo è un fattore cruciale da considerare quando si studia la resistenza alla fatica dei giunti saldati, tanto che alcuni codici di progettazione sostituiscono la caratteristica ciclica r con il campo di sollecitazione.
Inoltre, anche le dimensioni del provino, la modalità di carico, il rapporto dei cicli di sollecitazione e lo spettro di carico hanno un impatto significativo sulla resistenza alla fatica.
L'innesco della cricca da fatica nei giunti saldati avviene tipicamente in corrispondenza della radice e della punta della saldatura. Se il rischio di innesco della cricca di fatica alla radice della saldatura è controllato, i punti più vulnerabili dei giunti saldati si concentrano sulla punta della saldatura.
Esistono diversi modi per migliorare la resistenza alla fatica dei giunti saldati:
① Ridurre o eliminare i difetti di saldatura, in particolare le aperture;
② Migliorare la geometria del cordone di saldatura e ridurre il fattore di concentrazione delle sollecitazioni;
③ Regolare il campo di sollecitazione residua di saldatura per produrre un campo di sollecitazione residua di compressione. Questi metodi di miglioramento possono essere suddivisi in due categorie, come illustrato nella Tabella 1.
Ottimizzazione del processo di saldatura non solo migliora la resistenza alla fatica della struttura saldata, ma ne aumenta anche la resistenza al carico statico e le proprietà metallurgiche dei giunti saldati. Esiste una vasta quantità di dati su questo argomento, che non verranno ripetuti in questa sede.
Tabella 1 metodi di miglioramento della resistenza alla fatica delle strutture saldate
Metodo di miglioramento della resistenza alla fatica delle strutture saldate | Ottimizzazione del processo di saldatura | Geometria locale | Controllo qualità | Controllo dei difetti di saldatura | 1 | |
Miglioramento della geometria | 2 | |||||
Processo tecnologico | Sequenza di saldatura | 3 | ||||
Sollecitazione residua (<0) | Trattamento metallurgico del cordone di saldatura | 4 | ||||
Modellazione del cordone di saldatura | Geometria del puntale di saldatura | 5 | ||||
Stato dell'oro e del metallo | 6 | |||||
Miglioramento della saldatura | Geometria locale | Lavorazione meccanica | Rettifica della punta della saldatura | 7 | ||
Impatto dell'acqua | 8 | |||||
Rifusione locale | Riparazione TG | 9 | ||||
Riparazione al plasma | 10 | |||||
Sollecitazione residua | Metodo di rilascio dello stress | Trattamento termico | 11 | |||
Trattamento meccanico | 12 | |||||
Riscaldamento locale | 13 | |||||
Metodo meccanico | Contatto meccanico | Scatto pallinatura | 14 | |||
Martellamento | 15 | |||||
Impatto ultrasonico | 16 | |||||
saldatura | Timbratura | 17 | ||||
Compressione locale | 18 |
I metodi principali per migliorare la resistenza alla fatica dei giunti saldati sono discussi in dettaglio in tre parti, con particolare attenzione ai metodi di processo.
1) Preparazione TIG
Gli studi hanno dimostrato che la riparazione TIG può migliorare significativamente la resistenza alla fatica dei giunti saldati, sia a livello nazionale che internazionale. Il processo prevede l'utilizzo di Saldatura TIG per rifondere la sezione di transizione del giunto saldato, creando una transizione omogenea tra la saldatura e il metallo di base. In questo modo si riduce la concentrazione delle tensioni e si eliminano i piccoli non metallico inclusioni di scorie, con conseguente miglioramento della resistenza a fatica del giunto.
Durante il processo di riparazione, la pistola di saldatura viene solitamente posizionata a 0,5-1,5 mm di distanza dalla punta di saldatura e l'area rifusa deve essere mantenuta pulita. L'aggiunta di una leggera smerigliatura preventiva migliorerà i risultati.
È fondamentale gestire correttamente il processo di riarco se si verifica un'estinzione dell'arco durante la rifusione, poiché ciò influisce sulla qualità del cordone di saldatura rifuso. La posizione migliore per il riarco è generalmente 6 mm davanti al cratere del cordone di saldatura.
Recentemente, l'International Welding Society ha collaborato con gli istituti di ricerca sulla saldatura di diversi Paesi europei e del Giappone per condurre uno studio unificato sull'efficacia dei metodi per migliorare la resistenza alla fatica dei giunti. I campioni sono stati preparati dal British Welding Research Institute.
Lo studio ha confermato che la resistenza nominale a fatica del giunto dopo 2×106 è aumentata di 58% in seguito al trattamento con questo metodo. Questo valore nominale di 211MPa di resistenza alla fatica corrisponde a un valore caratteristico (indice K) di 144MPa. Supera il più alto valore FAT nella resistenza alla fatica dei dettagli del giunto stabilito dall'International Welding Society.
2) Lavorazione
La lavorazione della superficie della saldatura può ridurre notevolmente la concentrazione delle tensioni e migliorare la resistenza alla fatica del giunto di testa. Se la saldatura è priva di difetti, la sua resistenza a fatica può persino superare quella del metallo di base. Tuttavia, la lavorazione è un processo costoso e dovrebbe essere eseguita solo quando i benefici giustificano il costo.
Nel caso di saldature con difetti significativi e senza saldatura di fondo, la concentrazione delle sollecitazioni in corrispondenza del difetto o della radice della saldatura è molto più grave che in superficie, rendendo inutile la lavorazione. Se non c'è un difetto di penetrazione, le cricche da fatica non inizieranno in corrispondenza dell'armatura e della punta della saldatura, ma si trasferiranno alla radice della saldatura. In questi casi, la lavorazione può effettivamente ridurre la resistenza a fatica del giunto.
Anche la rettifica del solo cordone di saldatura, anziché dell'intero metallo saldato, può migliorare la resistenza a fatica del giunto. Le ricerche hanno dimostrato che in questo scenario il punto di innesco della cricca si trasferisce dalla punta della saldatura al difetto di saldatura.
Le prove di resistenza a fatica condotte da Makorov dell'ex Unione Sovietica su acciai ad alta resistenza (resistenza a trazione σb = 1080MPa) hanno mostrato che la resistenza a fatica delle saldature di testa trasversali sotto carico alternato era di ± 150MPa dopo 2×106 cicli come saldato. La lavorazione della saldatura e la rimozione del rinforzo hanno aumentato la resistenza alla fatica a ± 275MPa, equivalente alla resistenza alla fatica del metallo base. La rettifica locale sulla punta della saldatura di testa ha portato a una resistenza a fatica di ± 245MPa, equivalente a 83% dell'effetto della lavorazione e a un miglioramento di 65% rispetto allo stato saldato.
È importante notare che per garantire il miglioramento desiderato della resistenza alla fatica è necessario utilizzare una tecnica adeguata sia nella lavorazione che nella rettifica.
3) Rettifica con mola
La rettifica con una mola può non essere efficace come la lavorazione meccanica, ma è comunque un metodo utile per migliorare la resistenza alla fatica dei giunti saldati. L'International Welding Society raccomanda di utilizzare una mola ad alta velocità, elettrica o idraulica, con una velocità compresa tra 15.000 e 40.000 giri al minuto, in materiale di tungsteno al carbonio. Il diametro della mola deve garantire che la profondità e il raggio di rettifica siano pari o superiori a 1/4 dello spessore della piastra.
Una recente ricerca dell'International Welding Society ha rilevato che la resistenza nominale alla fatica del campione dopo 2 cicli è aumentata di 45% in seguito alla rettifica. Il valore nominale di 199 MPa di resistenza alla fatica corrisponde a un valore caratteristico (135 MPa), superiore al più alto valore FAT della resistenza alla fatica dei dettagli del giunto stabilito dalla International Welding Society.
È importante notare che la direzione di rettifica deve essere allineata con la direzione della linea di sollecitazione. Una rettifica in direzione diversa può lasciare un intaglio perpendicolare alla linea di sollecitazione, agendo di fatto come fonte di concentrazione delle sollecitazioni e riducendo la resistenza a fatica del giunto.
4) Metodo dell'elettrodo speciale
Questo metodo prevede lo sviluppo di un nuovo tipo di elettrodo. Il suo metallo liquido e la sua scoria liquida hanno un'elevata bagnabilità, che migliora il raggio di transizione della saldatura, riduce l'angolo in punta di saldatura, riduce la concentrazione di tensioni in punta di saldatura e migliora la resistenza alla fatica del giunto saldato.
Come la riparazione con saldatura TIG, ha una forte preferenza per alcune posizioni di saldatura, in particolare per la saldatura piana e a filetto, mentre i suoi vantaggi sono significativamente ridotti per le saldature verticali, orizzontali e a filo. saldatura aerea.
1) Metodo del pre-carico
Quando si applica un carico di trazione a un provino contenente una concentrazione di tensioni fino a quando si verifica lo snervamento in corrispondenza dell'intaglio, con conseguente deformazione plastica da trazione, dopo lo scarico si genererà una sollecitazione di compressione nel sito della deformazione plastica da trazione vicino all'intaglio caricato. La sollecitazione di trazione al di sotto del punto di snervamento sarà bilanciata in altre sezioni del campione.
Nelle successive prove di fatica, il campo di sollecitazione del provino sottoposto a questo trattamento differirà da quello del provino originale senza precarico e sarà significativamente ridotto. Ciò può migliorare la resistenza a fatica dei giunti saldati.
Le ricerche dimostrano che è necessario eseguire una prova di precarico prima di mettere in funzione grandi strutture saldate, come ponti e recipienti a pressione. Questo migliorerà le loro prestazioni a fatica.
2) Riscaldamento locale
Il riscaldamento locale può regolare il campo di tensioni residue nella saldatura, generando tensioni residue di compressione nei punti di concentrazione delle tensioni, che possono migliorare la resistenza alla fatica del giunto. Attualmente, questo metodo è applicabile solo a saldature discontinue longitudinali o a giunti con piastre irrigidite longitudinalmente.
Per le piastre di filetto monofaccia, la posizione di riscaldamento è in genere a circa 1/3 della larghezza della piastra dalla saldatura. Per le piastre di filetto bifacciali, la posizione di riscaldamento è al centro della piastra. Questo genera una tensione di compressione nella saldatura, aumentando la resistenza alla fatica del giunto.
Diversi ricercatori hanno ottenuto risultati diversi utilizzando questo metodo. Per le piastre a soffietto su un solo lato, la resistenza alla fatica è aumentata di 145-150%, mentre per le piastre a soffietto su due lati la resistenza alla fatica è aumentata di 70-187%.
La posizione del riscaldamento locale ha un impatto significativo sulla resistenza a fatica del giunto. Il riscaldamento a punti all'estremità della saldatura provoca tensioni residue di compressione in corrispondenza dell'intaglio e aumenta la resistenza alla fatica di 53%. Tuttavia, il riscaldamento a punti al centro del campione all'estremità della saldatura, con la stessa distanza dall'estremità della saldatura, ha lo stesso effetto metallografico, ma produce una tensione residua di trazione, con la stessa resistenza alla fatica del provino non trattato.
3) Metodo di estrusione
Il meccanismo di estrusione locale è simile al metodo di riscaldamento puntuale, in quanto migliora la resistenza alla fatica del giunto generando tensioni residue di compressione. Tuttavia, il suo punto d'azione è diverso e la posizione di estrusione deve essere quella in cui si desidera una sollecitazione residua di compressione.
Il metodo di estrusione ha un effetto più significativo sui campioni di acciaio ad alta resistenza rispetto a quelli di acciaio a basso tenore di carbonio.
4) Metodo di Gurnnert
Gunnert ha proposto un metodo per ottenere risultati soddisfacenti a causa della difficoltà di determinare con precisione la posizione e la temperatura di riscaldamento nel metodo di riscaldamento locale. La chiave di questo metodo consiste nel riscaldare direttamente l'intaglio, anziché l'area circostante, a una temperatura che può provocare una deformazione plastica ma che è inferiore alla temperatura di trasformazione di fase di 55°C o 550°C, per poi raffreddarla rapidamente.
Il raffreddamento tardivo del metallo sotto la superficie e del metallo circostante non raffreddato provoca un ritiro e genera una tensione di compressione sulla superficie raffreddata. Questa sollecitazione di compressione può aumentare la resistenza a fatica dell'elemento.
È importante notare che il processo di riscaldamento deve essere lento per riscaldare lo strato inferiore. Gunnert consiglia un tempo di riscaldamento di 3 minuti, mentre Harrison raccomanda 5 minuti.
Ohta è riuscito a prevenire le cricche da fatica nei tubi di testa utilizzando questo metodo. L'esterno della tubazione è stato riscaldato per induzione e l'interno è stato raffreddato facendo circolare l'acqua, generando una tensione di compressione nella tubazione e impedendo efficacemente la formazione di cricche da fatica. Dopo il trattamento, il tasso di crescita delle cricche da fatica del tubo saldato di testa è stato notevolmente ridotto e ha raggiunto lo stesso tasso di crescita delle cricche del metallo di base.
1) Metodo di martellatura
La martellatura è un metodo di lavorazione a freddo che crea una tensione di compressione sulla superficie del cordone di saldatura di un giunto. L'efficacia di questo metodo dipende dalla deformazione plastica sulla superficie del cordone di saldatura.
Inoltre, la martellatura può ridurre la nitidezza dell'intaglio e quindi la concentrazione delle tensioni, con un significativo miglioramento della resistenza a fatica del giunto. L'International Welding Society raccomanda una pressione di martellamento di 5-6 Pa.
La parte superiore della testa del martello deve essere solida con un diametro di 8-12 mm e si consiglia di utilizzare quattro colpi per garantire una profondità di martellamento di 0,6 mm.
Una ricerca dell'International Welding Society mostra che per i giunti a T non portanti, la martellatura aumenta la resistenza alla fatica di 54% sotto 2×106 cicli.
2) Pallinatura
La pallinatura è un'altra forma di martellatura ed è un tipo di lavorazione a impatto. L'efficacia della pallinatura dipende dal diametro di pallinatura. Il diametro non deve essere troppo grande per risolvere piccoli difetti, ma nemmeno troppo piccolo per ottenere un certo livello di indurimento a freddo. In genere, la pallinatura può colpire la superficie a una profondità di pochi millesimi di millimetro.
Le ricerche dimostrano che la pallinatura può migliorare notevolmente la resistenza alla fatica dei giunti in acciaio ad alta resistenza e ha un effetto particolarmente forte su saldatura ad arco di argon materiali in acciaio ad alta resistenza, superando anche la riparazione TIG. L'uso della pallinatura può anche migliorare l'impatto della riparazione per fusione TIG.
Negli ultimi anni, l'impatto ultrasonico è stato sviluppato come mezzo per migliorare la resistenza alla fatica di giunti e strutture saldate. Il suo meccanismo è simile a quello della martellatura e della pallinatura.
Tuttavia, l'impatto a ultrasuoni presenta vantaggi quali leggerezza, buon controllo, flessibilità e praticità d'uso, rumore minimo, elevata efficienza, minori restrizioni nell'applicazione, basso costo ed efficienza energetica. È adatto a tutti i tipi di giunti ed è un metodo efficace per migliorare le prestazioni a fatica dei giunti saldati dopo la saldatura.
Sono stati condotti studi utilizzando il trattamento d'urto a ultrasuoni su giunti di testa e giunti d'angolo longitudinali non portanti di vari acciai strutturali tipicamente saldati. Sono state quindi condotte prove di fatica comparative sia sui giunti saldati che su quelli trattati con l'impatto. I risultati, riportati nella Tabella 2, indicano che la resistenza a fatica dei giunti saldati è aumentata di 50-170% dopo il trattamento a ultrasuoni.
Tabella 2 Confronto tra la resistenza alla fatica prima e dopo il trattamento d'urto a ultrasuoni
Materiale e forma del giunto | Resistenza alla fatica Ds / MPa | Aumento di grado(%) | |
---|---|---|---|
Come saldato | Stato trattato con shock | ||
Q235B (R= 0,1) - giunto di testa | 152 | 230 | 51 |
SS800 (R= 0,05) - giunto di testa | 306 | 101 | |
16Mn (R= 0,1) - giunto di testa | 285 | 88 | |
Q235B (R=0,1) - giunto angolare longitudinale | 104 | 200 | 92 |
SS800 (R=0,05) - giunto angolare longitudinale | 279 | 168 | |
16Mn (R=0,1) - giunto angolare longitudinale | 212 | 104 |
4.2.1 Principio e sviluppo del miglioramento della resistenza alla fatica dei giunti saldati
Le sollecitazioni di compressione possono aumentare la resistenza alla fatica dei giunti saldati, come ampiamente discusso in letteratura. Tuttavia, la sfida risiede nel modo in cui introdurre facilmente le sollecitazioni di compressione nei giunti saldati.
È noto che la composizione chimica, il contenuto di lega e la velocità di raffreddamento possono determinare diverse trasformazioni microstrutturali durante il processo di raffreddamento dei materiali in ferro e acciaio. Queste trasformazioni strutturali sono accompagnate da un'espansione volumetrica, che può creare tensioni da trasformazione di fase quando viene trattenuta, portando a tensioni di compressione.
Per il metallo saldato, questo riduce la tensione residua di trazione e persino la tensione residua di compressione, migliorando così le proprietà meccaniche dei giunti saldati.
L'elettrodo di saldatura a bassa temperatura di trasformazione (LTTE) è un nuovo prodotto materiale di saldatura che utilizza le sollecitazioni di trasformazione di fase per produrre sollecitazioni di compressione nei giunti saldati e migliorarne la resistenza alla fatica.
Già negli anni Sessanta, gli esperti di saldatura dell'ex Unione Sovietica proposero il metodo della bassa trasformazione di fase saldatura a punti per migliorare la resistenza alla fatica delle strutture saldate, anche se all'epoca non si usava il termine "nastro di saldatura a punti a bassa trasformazione di fase", ma ci si riferiva semplicemente a un elettrodo speciale.
Il rivestimento composizione del metallo è costituito principalmente da 3-4% Mn per ridurre la temperatura di trasformazione di fase e ottenere la trasformazione di fase metallurgica. La letteratura suggerisce che la resistenza alla fatica dei campioni di piccole dimensioni dopo l'affilatura con questi elettrodi speciali è 75% superiore a quella senza affilatura.
Recentemente, lo sviluppo di acciai a bassissimo tenore di carbonio e l'uso di Cr e Ni per abbassare la temperatura di trasformazione martensitica del metallo depositato nei materiali di saldatura ha portato a rapidi progressi nella saldatura a punti a bassa trasformazione.
Sia il Giappone che la Cina hanno condotto ricerche approfondite in questo settore, sebbene siano ancora in fase di laboratorio.
4.2.2 Effetto dell'elettrodo LTTE sul miglioramento della resistenza alla fatica
La Scuola dei Materiali dell'Università di Tianjin ha progettato e ottimizzato l'elettrodo di saldatura a bassa temperatura di trasformazione (LTTE) e ha condotto prove di fatica e test di prestazione di processo su vari giunti saldati.
(1) Metodo LTTE
L'elettrodo di saldatura a bassa temperatura di trasformazione (LTTE) e l'elettrodo ordinario E5015 sono stati utilizzati per saldare il giunto di testa trasversale, il giunto trasversale non portante, il giunto di raccordo longitudinale circonferenziale, il giunto parallelo longitudinale. giunto di saldatura a filettoe longitudinale, rispettivamente. È stata eseguita una prova comparativa di fatica.
I risultati indicano che la resistenza alla fatica della giunzione LTTE del punto di cambiamento di fase bacchetta per saldatura è stato di 11%, 23%, 42%, 46% e 59% superiore a quello dell'elettrodo ordinario E5015. La vita a fatica è aumentata da diverse volte a centinaia di volte.
Tabella 3 Effetto di miglioramento della resistenza alla fatica di diversi tipi di giunti saldati
Tipo di elettrodo | Giunto trasversale di testa | Giunto trasversale non portante | Giunto di saldatura a filetto longitudinale circonferenziale | Giunto di saldatura a filetto parallelo longitudinale | Giunto di testa longitudinale |
---|---|---|---|---|---|
Bacchetta per saldatura E5015 | 176.9 | 202.1 | 167.0 | 182.7 | 179.4 |
Elettrodo LTTE | 157.8 | 164.8 | 118.3 | 124.9 | 113.0 |
Grado di miglioramento | 11% | 23% | 41% | 47% | 58% |
Concentrazione di stress | K1 mite | Medio K2 | Forte K3 | Particolarmente forte N4 | Particolarmente forte K4 |
Grado di restrizione | Piccolo grande |
Poiché l'elettrodo di saldatura a bassa temperatura di trasformazione (LTTE) crea una tensione di compressione residua dovuta all'espansione di volume della trasformazione martensitica a una temperatura inferiore, l'entità della tensione di compressione residua è strettamente legata al vincolo del giunto saldato.
Più il giunto saldato è vincolato, maggiore è la tensione residua di compressione e più significativo è il miglioramento della resistenza alla fatica.
(2) Metodo di apprettatura LTTE per la saldatura a punti a bassa trasformazione di fase
Tuttavia, l'aggiunta di ulteriori elementi in lega ai materiali di saldatura per ottenere la trasformazione martensitica a una normale velocità di raffreddamento e a una bassa temperatura aumenta significativamente il costo dell'elettrodo di saldatura a bassa temperatura di trasformazione (LTTE). Se tutte le saldature di una struttura saldata sono realizzate con materiali di saldatura a bassa trasformazione di fase, anche il costo complessivo della struttura sarà significativamente più alto, rendendola economicamente non fattibile.
È noto che il frattura da fatica nei giunti saldati si verifica solitamente in corrispondenza del cordone di saldatura. Se la tensione residua di compressione viene generata in corrispondenza della punta della saldatura, è possibile migliorare la resistenza alla fatica del giunto saldato senza utilizzare tutte le strisce di saldatura a punti a basso cambiamento di fase, riducendo il costo dei materiali.
Con questa idea in mente, l'Università di Tianjin ha proposto il metodo di apprettatura dell'elettrodo di saldatura a bassa temperatura di trasformazione (LTTE) per migliorare la resistenza alla fatica dei giunti saldati, sulla base di risultati sperimentali. La resistenza alla fatica dei giunti saldati con elettrodo LTTE e di quelli con elettrodo ordinario è stata confrontata utilizzando due tipi di giunti trasversali non portanti e giunti di saldatura a filetto longitudinale circonferenziale. La resistenza alla fatica dei primi è risultata rispettivamente di 19,9% e 41,7% superiore a quella dei secondi, dimostrando la fattibilità e la praticità dell'idea.
Questa ricerca preliminare fornisce un'applicazione più ragionevole dell'elettrodo di saldatura a bassa temperatura di trasformazione (LTTE) nella pratica ingegneristica.
Allo stesso tempo, il giunto di apprettatura dell'elettrodo di saldatura a bassa temperatura di trasformazione (LTTE) può anche riflettere la sua applicazione nelle saldature di copertura e nei cordoni di saldatura vicino alla punta.
4.2.3 Advantaggi e svantaggi della striscia di saldatura a punti a basso cambiamento di fase
Vantaggio:
(1) Il metodo dell'elettrodo di saldatura a bassa temperatura di trasformazione (LTTE) viene eseguito durante il processo di saldatura, eliminando la necessità di una lavorazione post-saldatura.
(2) Il metodo LTTE non richiede particolari competenze operative e quindi è semplice e comodo da usare.
(3) Utilizzando un elettrodo di saldatura a bassa temperatura di trasformazione (LTTE), è possibile migliorare la resistenza alla fatica dei giunti saldati. Poiché non è influenzato dagli effetti termici dei cordoni di saldatura successivi, è adatto a migliorare la resistenza alla fatica di saldature nascoste, saldature coperte, saldature posteriori di saldature su un solo lato e altre saldature che non possono essere lavorate dopo la saldatura.
(4) L'elettrodo LTTE può essere utilizzato anche per riparare le cricche da fatica nelle strutture saldate.
Svantaggi:
L'aggiunta di altri elementi di lega ai materiali di saldatura aumenta il costo degli elettrodi di saldatura a bassa temperatura di trasformazione (LTTE), ma questo può essere compensato dall'uso di ravvivature LTTE e di altri metodi.
In conclusione, i requisiti di capacità di carico dinamico delle strutture saldate sono aumentati con l'utilizzo di queste ultime per carichi pesanti e ad alta velocità. Di conseguenza, lo sviluppo e l'utilizzo di nuove tecnologie per migliorare le prestazioni a fatica dei giunti saldati è fondamentale per una più ampia applicazione delle strutture saldate.
Sia la tecnologia dell'impatto ultrasonico che l'uso di elettrodi di saldatura a bassa temperatura di trasformazione (LTTE) per migliorare la resistenza alla fatica dei giunti saldati sono importanti direzioni di ricerca nel campo del miglioramento delle prestazioni a fatica e del processo delle strutture saldate.