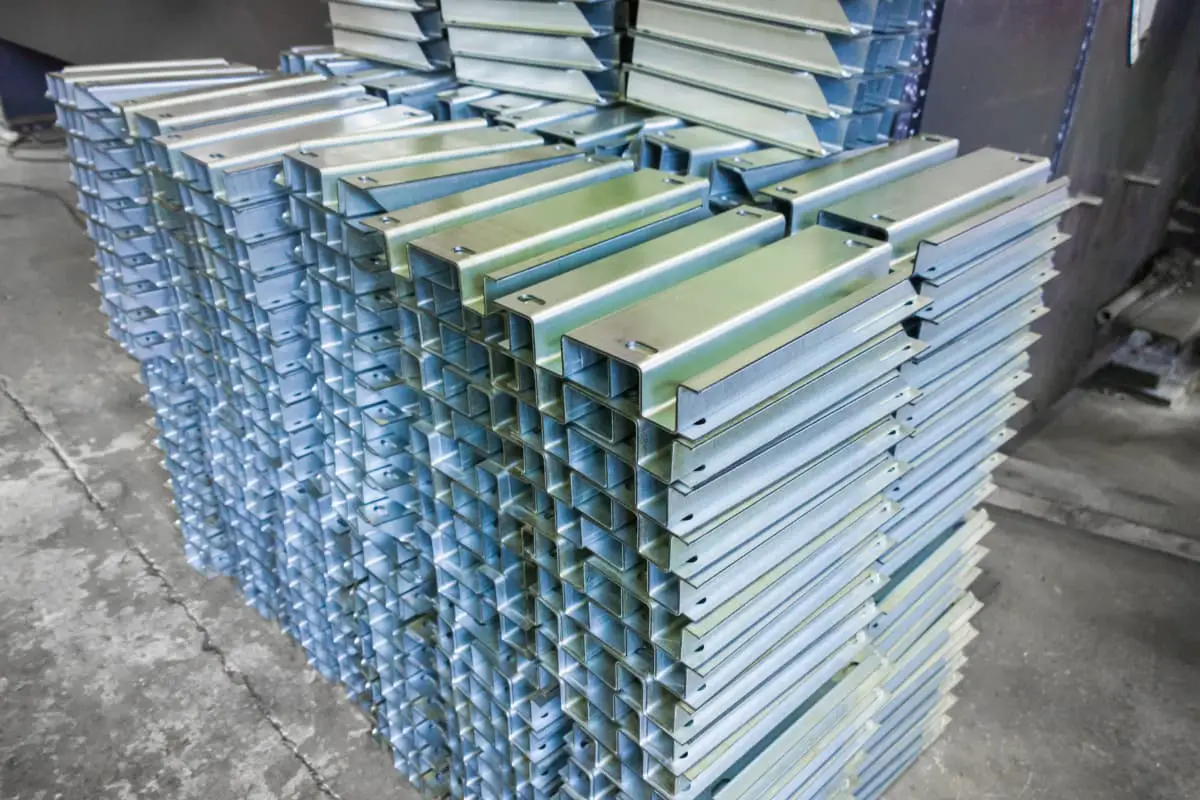
Avete mai pensato a come gli intricati processi che stanno dietro alla fabbricazione di lamiere metalliche diano forma ai nostri prodotti di tutti i giorni? Questo articolo approfondisce tecniche essenziali come la piegatura, la cesoiatura e la saldatura, scoprendo i metodi e i principi che garantiscono la qualità e l'efficienza della produzione. La comprensione di questi processi vi permetterà di capire come ottimizzare la produzione e ridurre gli errori, migliorando le vostre competenze tecniche e i risultati dei progetti. Esplorate l'affascinante mondo della fabbricazione di lamiere e scoprite come la padronanza di queste tecniche possa rivoluzionare il vostro approccio alla progettazione.
Le tecniche utilizzate per la fabbricazione di parti in lamiera hanno caratteristiche uniche.
Lo studio e la comprensione di queste tecniche possono migliorare le competenze dei tecnici nella fabbricazione della lamiera, portando alla progettazione di processi e piani di fabbricazione più ottimizzati.
Dati i limiti delle attrezzature esistenti e della struttura del prodotto, è importante ottimizzare la struttura dal punto di vista del processo. La responsabilità principale di un lamiera tecnologo è quello di sviluppare il metodo di processo più efficiente, tenendo conto dell'efficienza produttiva e della flessibilità del coordinamento.
Le parti in lamiera possiedono caratteristiche uniche, come lo spessore ridotto e la facilità di modellazione in varie forme.
Con l'uso di saldatura, assemblaggio e rivettatura, è possibile creare componenti multistrutturati.
Tuttavia, queste stesse caratteristiche possono anche provocare deformazioni durante la fabbricazione, come piegature, torsioni e deformazioni concave o convesse, che possono influire sulle dimensioni o sulla forma del componente e causare problemi di qualità.
Il processo di produzione di parti in lamiera ha una propria serie di principi che consentono di regolare con flessibilità la sequenza di fabbricazione in base alle attrezzature e alla manodopera disponibili. Selezionando il metodo più appropriato processo tecnologicoè possibile prevenire e risolvere efficacemente questo tipo di problemi.
Lo sviluppo di un percorso tecnologico deve tenere conto sia della forma del prodotto che delle attrezzature di lavorazione esistenti nell'azienda, per soddisfare i requisiti di qualità del prodotto e ottenere il massimo beneficio economico.
I principi generali per la creazione di una tecnica di fabbricazione sono i seguenti:
⑴ Soddisfare i requisiti di qualità del prodotto
⑵ La tecnica di fabbricazione è economicamente valida
⑶ Fornire l'ottimizzazione per i processi successivi
⑷ Lavorazione conveniente
Il personale tecnico deve considerare la qualità del prodotto sia dal punto di vista funzionale che estetico, oltre a conoscere le capacità di lavorazione delle apparecchiature.
Quando si prepara una tecnica, è importante considerare l'errore complessivo di integrazione della macchina, ottimizzare i metodi di lavorazione del prodotto per ridurre le difficoltà e stabilire un percorso tecnologico relativamente stabile per la produzione in lotti.
Il coordinamento dell'errore cumulativo è un riflesso completo della tolleranza cumulativa del prodotto ed è necessario assegnare le tolleranze corrispondenti durante l'analisi del processo per garantire che l'errore cumulativo rientri in un intervallo accettabile.
Ad esempio, l'armadio elettrico a corrente alternata è un prodotto tipico che richiede un'attenta considerazione del coordinamento degli errori cumulativi.
L'armadio di comando elettrico CA può essere trasformato in un armadio di montaggio o in un armadio di saldatura.
L'assemblaggio dell'armadio di montaggio è comune e consiste tipicamente in un telaio superiore, un telaio inferiore, un montante, una porta anteriore, una porta posteriore e una porta laterale (pannello).
Se questi componenti sono fabbricati bene, la qualità del mobile è garantita.
In genere, i clienti hanno determinati requisiti per le dimensioni complessive dell'armadio dopo l'assemblaggio, con la richiesta che l'errore di dimensione delle dimensioni diagonali X1 e X2, X3 e X4 sia inferiore a 2 mm.
In base alle condizioni di installazione, i clienti possono controllare la larghezza di L3, ma non vi sono requisiti rigorosi per l'altezza e lo spessore. Questo perché la progettazione del mobile da parte del cliente spesso utilizza la forma del corpo per determinare le dimensioni richieste, senza considerare lo spessore del film di rivestimento, il che può causare errori nelle dimensioni del mobile dopo la spruzzatura e l'assemblaggio.
Pertanto, è necessario regolare la quantità di spruzzi e coperture su ciascun componente per soddisfare la larghezza di L3, garantendo al contempo le dimensioni L1 e L2.
In genere, il telaio superiore, il telaio inferiore e la colonna vengono regolati in base ai requisiti, con regolazioni diverse per i vari gruppi.
La porta d'ingresso e la porta laterale vengono solitamente incastrate durante l'installazione nell'architrave superiore e inferiore della porta, causando uno scostamento negativo delle dimensioni di ingombro.
La tolleranza di rivestimento deve essere regolata di conseguenza in base al tipo di spruzzatura. Tenendo conto del gioco di montaggio e di altri fattori, la tolleranza di spruzzatura deve essere riadattata per controllare la deviazione delle dimensioni (per la tavola della porta, si deve lasciare una tolleranza dello strato di rivestimento da 0,5 a 1 mm dopo aver tenuto conto della deviazione negativa).
L'ottimizzazione del metodo di lavorazione comporta la regolazione della sequenza di lavorazione o il miglioramento del processo, che può essere dimostrato con un semplice esempio.
Se il pannello di una porta richiede un'espansione, la qualità e il tempo possono essere considerati nella lavorazione di un singolo pezzo.
Il processo di fabbricazione tipico è il seguente:
Taglio con cesoie → Punzonatura della forma e del foro interno → Piegatura con pressa piegatrice → Angoli di saldatura
Questo processo consente di risparmiare tempo e fatica, ma nella produzione di massa aumenta l'usura della macchina. utensile da taglio e aumenta notevolmente i costi di manutenzione della macchina. Inoltre, un piccolo errore di programmazione può causare danni irreparabili.
Poiché l'area sagomata di questo tipo di porta viene utilizzata per installare la maniglia, una soluzione comunemente adottata per la produzione in serie di questi pannelli porta è:
Taglio con cesoie (taglio separato per il tappo a tre ante) → Punzonatura del foro interno → Scantonatura degli angoli → Piegatura con pressa piegatrice → Saldatura degli angoli e del tappo a tre ante
Questo processo migliorato non solo consente di risparmiare sulle materie prime e sui costi di manutenzione delle apparecchiature, ma riduce anche in modo significativo il tasso di errore nella programmazione.
La stabilità della scelta del percorso di processo deve essere in linea con il lotto di produzione, poiché la scelta dei percorsi di processo può variare in base ai cambiamenti nella produzione. La fase di sviluppo si concentra sulla convalida della struttura complessiva del prodotto e sulla sua lavorazione tempestiva ed è meno sensibile a costo di fabbricazionementre la produzione in piccoli lotti si concentra sulla convalida del processo, sull'ottimizzazione delle singole strutture e sulla preparazione di una quantità moderata di stampi.
Per la produzione di piccoli lotti, il costo è la priorità assoluta e il processo viene ottimizzato il più possibile per risparmiare sui costi.
Ad esempio, si consideri il supporto angolare piccolo:
TecnicaⅠ: Taglio con cesoia → Piegatura con pressa piegatrice → Punzonatura e maschiatura per marcatura
TecnicaⅡ: Taglio con cesoie (gli articoli possono essere uniti) → Punzonatura del foro inferiore → Taglio in pezzi singoli → Piegatura con pressa piegatrice → Maschiatura
TecnicaⅢ: Realizzazione di uno stampo per la fabbricazione
Dopo aver confrontato queste tre strade tecnologiche, si può notare che tutte e tre le opzioni soddisfano efficacemente le esigenze dei clienti, ma ognuna ha i suoi punti di forza.
TecnicaⅠ
Richiede molta manodopera e richiede molto tempo (a causa della punzonatura e della battitura delle marcature), con conseguenti perdite di processo significative. È adatto solo per la produzione di singoli prodotti e non è raccomandato per la produzione in serie.
TecnicaⅡ
Utilizza più macchine utensili, è più veloce e può produrre più pezzi contemporaneamente. È adatto alla produzione di lotti medio-piccoli, ma il processo di taglio può causare piccoli spostamenti nei fori.
TecnicaⅢ
È adatto alla produzione di massa, in quanto si basa sull'utilizzo di uno stampo adatto, risparmiando tempo e fatica.
La scelta della tecnica di fabbricazione è strettamente legata all'impatto delle perdite di lavorazione e della produzione in lotti e deve essere effettuata sulla base di una considerazione completa di vari fattori. La scelta del piano di fabbricazione appropriato è particolarmente importante in considerazione delle diverse condizioni di produzione.
La tecnologia di lavorazione delle parti in lamiera è una questione complessa.
Questo post fornisce una breve panoramica dei principi di base per l'impostazione di una tecnica di fabbricazione di pezzi di lamiera generici, con l'obiettivo di identificare il metodo di base per l'impostazione di una tecnica di fabbricazione.
In conclusione, come ingegneri è importante adottare un approccio attento ai costi, considerare i costi in tutto il processo e considerare l'impostazione del processo da una prospettiva globale e completa.