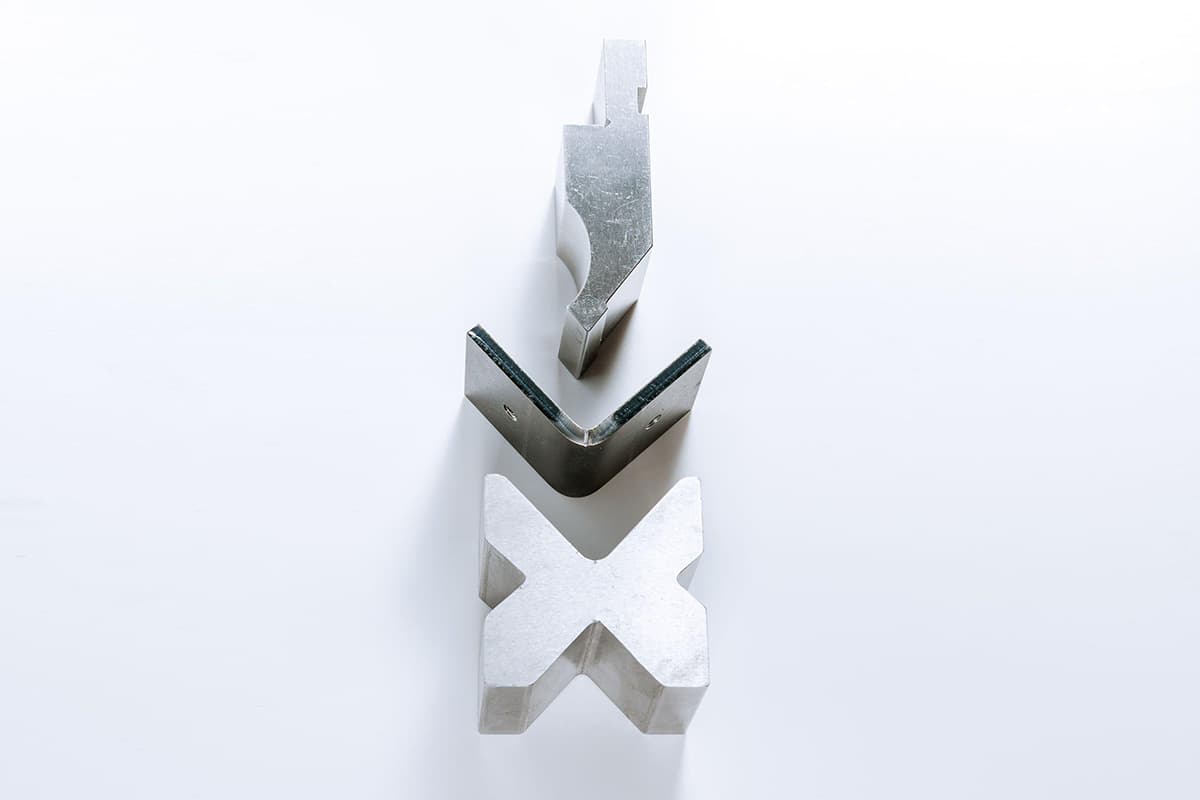
このブログでは、魅力的なエアベンディングの世界と、それを可能にするフォースチャートについてご紹介します。この重要なプロセスの背後にある科学を掘り下げ、私たちが毎日使っている製品がどのように形作られているのかを発見しましょう。すべての曲げ加工に施された工夫と精度に驚嘆することでしょう。
当社の空気曲げ力チャートは、世界中の様々な業界のお客様の経験データに基づいており、軟鋼やステンレス鋼を曲げる際に、異なるV開口部に対応する最小曲げ圧力、最小フランジ長、および曲げ半径を簡単に決定するための権威あるガイドを提供します。
このチャートを使えば、時間を節約し、効率を上げることができる。 曲げ加工.
さらに プレスブレーキ トン数計算機は、特定のシートメタル製品に必要な曲げ力の計算をお手伝いします。
私たちは、最適なV開口部を選択することの重要性を理解しており、金属厚とV開口部幅の最適な関係をチャートで示しています。
トン数要件
エアー・ベンディングは 成形シート パンチとダイの組み合わせで低い成形トン数により プレスブレーキ 成形部品の製造能力が低い。
下図は、指定された材料の引張強さが60,000 PSIの場合の材料厚さとダイ開口部の関係を詳しく示しています。北米のほとんどの軟鋼の引張強度は60,000 PSIを超えるため、より高いトン数が必要になる場合があることに留意されたい。
注:
上の表は、引張特性60,000 PSIの軟鋼をエアベンドする場合の適切なトン数を示しています。北米のほとんどの製鋼所では、降伏強さ44,000 PSI、引張強さ80,000 PSIまでの典型的な機械的特性を持つ、より硬い金属を生産していることに注意しなければなりません。これらの金属を成形するのに必要なトン数は、かなり高くなり、プレスブレーキの選択において考慮しなければなりません。
ダイと素材の厚さ比
業界の標準的なダイ・オープニング・サイズは、1/2 "未満の場合は材料厚の8倍、1/2 "以上の場合は材料厚の10倍である。
熱処理された状態の材料については、成形された形状に亀裂が入るのを防ぐため、材料データシートによってはダイの開口部を大きく指定する場合がある。
ゲージシート材や軽板材の場合、パンチ半径は通常、板厚に等しい。厚板の場合、パンチ半径は、成形される板の特性にもよりますが、通常、材料厚の1.5倍から3倍です。
エア曲げ力チャートは、さまざまな板金の曲げ加工に対応する標準下型V幅と必要曲げ力を記録したもので、業界の一般的な仕様となっている。
しかし、当初はそのような指定はなかった。
それぞれ プレスブレーキメーカー は、自分たちの経験に基づいてVワイドを使うことを決めた。
このときアマダは、世界のさまざまな業界のお客様の経験データを収集・整理し、最終的に次のような曲げ加工の権威ある曲げ力表を作成しました。
この曲げ力チャートによって、最小曲げ圧力、最小フランジ長、最小曲げ荷重を簡単に決定することができます。 曲げ半径 軟鋼とステンレスの曲げ加工では、Vの開きが異なる。
読みやすく、印刷しやすくするために 空気曲げ力チャートのPDFファイルをダウンロードする.
を使用することもできます。 プレスブレーキのトン数計算機 を使用して、シートメタル製品に必要な曲げ力を計算してください。
エア曲げは、プレスブレーキを使って金属を希望する形状や角度に成形する板金加工で使用される方法です。他の曲げ技術とは異なり、エア曲げでは、金属を金型の底に完全に押し付けないため、柔軟性と精度が向上します。この工程では、金属と金型の間に「エアスペース」と呼ばれる隙間ができるため、曲げ角度のコントロールがしやすくなり、曲げすぎや材料の変形のリスクを減らすことができます。
エアベンディングで使用される主な工具は、パンチとダイである。パンチは金属板を押さえる上側の工具で、ダイは金属を曲げるV字型またはU字型の空洞を持つ下側の工具です。例えば、自動車用のブラケットを製造する場合、V字型のダイを使用して、特定の取り付け要件に適合する正確な角度を作ることができる。パンチとダイの選択は、金属の種類、厚さ、必要な曲げ角度などの要因によって決まる。
エア曲げの特徴は、金属とダイの底の間にエアギャップがあることです。パンチは金属を完全にダイに押し込む前に停止するため、パンチの下降深さを変えることで曲げ角度を調整することができます。このエアギャップは、金属の完全性を維持し、不要な変形を防ぐのに役立ちます。航空宇宙部品など、厳しい公差が要求される場面では、エアギャップの制御が要求仕様を達成する上で極めて重要です。
これらのステップを説明する視覚教材を加えることで、理解度を高めることができます。例えば、金属板の位置合わせ、パンチの下降、曲げの結果などを図で示すことで、工程を明確にすることができます。
エア曲げは、底曲げやコイニングなどの他の曲げ方法と比べ、いくつかの利点がある。
放送から以下の情報を得ることができる。 曲げ力 金属厚と曲げ内径のデータが既知であれば、上の表を参照:
V字型開口部というのは、その横の距離のことである。 下型 の口があり、板金厚に応じて適切な金型のV開きを選択する必要があります。上記のエア曲げチャートは、板厚とV開口幅の最適な関係を示しています。
しかし、フランジの長さ、内側の曲げ半径、プレスブレーキのトン数、金型の能力など、他の要因もV幅の選択に影響する。
材料の厚さ (t)mm | 0.5-2.5 | 3.0-8.0 | 9.0-10.0 | ≥12.0 |
Vワイド | 6xt | 8xt | 10xt | 12xt |
板金加工における空気曲げは、金属が金型に完全に接触することなく金属板に曲げを作るために使用される技術です。この工程では、パンチとV字型またはU字型のダイを備えたプレスブレーキが使用されます。パンチはシートメタルを押し下げ、ダイの中に押し込みますが、底に到達する前に停止し、金属とダイの間に隙間を残します。この隙間(エアギャップ)により、金属がダイの形状に完全に適合することなく、さまざまな曲げ角度を柔軟に実現することができます。
エアベンディングに関わる主要なコンポーネントには、曲げの形状とサイズを決定するパンチとダイ、さまざまな角度と半径に必要な柔軟性を提供するエアギャップが含まれます。工程は、金属板の種類、厚さ、必要な曲げ角度に応じてパンチとダイをセットアップすることから始まります。その後、シートはダイの上に置かれ、パンチと位置合わせされます。パンチが下降すると、ダイ内で金属が曲げられ、エアギャップを作るために底の手前で止まります。
エア曲げには、同じ金型セットアップでさまざまな曲げ角度を柔軟に製造できる、生産時間が短縮できる、金型コストが削減できる、曲げ工程をより適切に制御できる、などの利点があります。しかし、底面曲げに比べて精度が劣ることや、曲げ後に金属が部分的に元の形状に戻るスプリングバックの可能性など、いくつかの欠点もあります。このスプリングバックは、オーバーベンディングや適応成形技術を使用することで管理することができる。
全体として、エアー曲げは、高い精度が要求されない生産工程や、頻繁に金型を交換することなく様々な曲げ角度の部品を作るのに適した、多用途で効率的な方法である。
金属加工における空気曲げに必要な曲げ力を計算するには、材料特性、曲げの形状、使用する工具など、いくつかの重要な要素を考慮する必要があります。曲げ力 ( F ) は、次の式で計算できます:
どこでだ:
例えば、引張強さ45kg/mm²、厚さ2mm、曲げ長さ100mmの軟鋼を曲げる場合、金型開口部6mmで計算すると、次のようになります:
さらに考慮すべき点として、内部半径と最小曲げ半径がある。内 半 径 は 、次 式 を 用 い て 推 定 す る こ と が で き る :
正確な計算、特に異なる材料での計算については、以下のことを考慮されたい:
ここで、( TS_{text{baseline}} ) は、軟鋼の場合60,000 PSIであることが多い。最小曲げ半径は、曲げによって亀裂が生じないことを保証するもので、次のように計算される:
エア曲げ力チャートや計算機を使用すると、一般的な材料や金型開口部に対して事前に計算された値が提供されるため、プロセスが簡素化されます。これらのツールにより、ユーザーは特定のパラメータを入力し、必要な曲げ力を直接得ることができ、安全で正確な金属加工作業を保証します。
特に空気曲げ力表を使用する場合、空気曲げにおける最小曲げフランジ長にはいくつかの要因が影響する。
一般的に、フランジの長さは材料の厚さの少なくとも4倍必要である。例えば、厚さ2mmのシートの場合、フランジ長は最低8mmが必要となる。
第二に、ダイのV字開口部によって決まる曲げ半径も、フランジの長さに影響する。曲げ半径が大きいほど、適切な曲げを確保するためにフランジ長を長くする必要があります。
第三に、金型開口部と金型形状が最小曲げ寸法を課す。フランジの長さは、成形後にダイの上端に達するのに十分でなければならない。
さらに、Kファクター自体はフランジ長を直接決定するものではないが、曲げ代を計算するためには不可欠であり、これは全体のフラットパターンに影響し、結果としてフランジ長にも影響する。
フランジの許容最小高さを決定するために使用される一般的な式は以下の通りである:
さらに、曲げ部からの最小穴距離は、フランジ長さとは直接関係しないが、変形を防ぐために重要であり、間接的にフランジ設計に影響する。
最後に、曲げ角度の公差+/-1度や一貫した曲げ半径など、業界のガイドラインや公差を遵守することで、均一性を維持し、曲げ加工を成功させるための適切なフランジ長を確保することができます。
これらの要素を考慮することで、設計者や製造者は、曲げ可能なフランジの最小長さを正確に決定することができ、一貫した板金加工を成功に導くことができます。
空気曲げ加工におけるダイス開度(V)は、曲げ加工のいくつかの重要な側面を決定する上で重要な役割を果たします。まず、曲げ半径の内側に直接影響し、Vダイの開口部が大きいほど曲げ半径が大きくなります。60KSI冷延鋼板やステンレス鋼のような材料では、ダイ開口幅の16-20%程度が一般的です。
8の法則」として知られる一般的なガイドラインでは、Vダイの開口部は材料厚さの8倍が望ましいとされていますが、これは特定の条件によって6倍から12倍の間で変化します。ダイスの開口部の大きさは、材料内の応力分布にも影響します。ダイスの開口部が小さいと、曲げ半径がきつくなり、外層部の引張応力と内層部の圧縮応力が増加し、材料の強度を超える応力がかかると、材料の変形や割れにつながる可能性があります。
スプリングバックとは、曲げ加工後に材料が部分的に元の形状に戻る傾向のことで、Vダイの開口部にも影響されます。通常、ダイスの開きが大きいとスプリングバックが大きくなり、所望の角度を得るために曲げ過ぎが必要になります。さらに、ダイス開口部は曲げ加工に必要なトン数や力にも影響し、厚い材料や小さな半径ではより大きな力が必要になります。
最後に、曲げ加工の精度と生産性は、Vダイの開き具合に影響される。Vダイを使用するエア曲げ加工は、一般に、底付け加工やコイニング加工よりも精度が劣るが、工具交換の回数が少なく、調整可能な工具でさまざまなプロファイルを作成できるため、生産性と柔軟性が高い。
エアベンディングはさまざまな素材に使用できるが、その適性は素材ごとの特性に左右される。アルミニウム、ステンレス鋼、炭素鋼、銅、一部のプラスチックなどの材料に有効です。例えば、アルミニウムは非常に可鍛性で成形しやすいため、空気による曲げ加工に適している。ステンレス鋼も適していますが、スプリングバックの度合いが高く、曲げ工程の調整が必要になります。炭素鋼も同様にエア曲げ加工が可能ですが、厚みや結晶粒の向きのばらつきを考慮する必要があります。
しかし、考慮すべき限界もある。エア曲げは一般的に、コイニングのような他の曲げ方法よりも少ない力で曲げられるが、精度が劣ることがある。希望の曲げ角度と半径を得るには、金型とダイスの開口部の選択が重要です。材料の厚みのばらつきは曲げ角度に大きな影響を与え、スプリングバックは材料によって異なる一般的な問題です。さらに、結晶粒方向に垂直に曲げることで、亀裂や変形のリスクを減らすことができます。
結論として、エアー曲げ加工は汎用性が高く、さまざまな材料に対応できますが、万能ではありません。エア曲げの成功は、材料の慎重な選択、適切な金型、材料の特性の十分な理解にかかっている。高い精度や厳しい公差が要求される用途には、他の方法が適しているかもしれません。
プレスブレーキ機でエアベンディング作業を行う場合、オペレーターの安全と装置の完全性を確保するために、いくつかの重要な安全予防措置を講じる必要があります。第一に、作業者は常に安全ゴーグル、手袋、作業靴などの適切な個人用保護具(PPE)を着用し、鋭利な金属エッジやその他の危険から怪我を防ぐ必要があります。
マシンを始動させる前に、徹底的に点検することが不可欠である。電気接続、作動油のレベルをチェックし、亀裂や破損などの損傷がないか点検する。油圧システムを含む装置の定期的なメンテナンスは、事故を防ぐために極めて重要である。オペレーターは、取扱説明書を読んで理解し、機械の機能や原理を熟知する必要がある。
事故のリスクを減らすため、作業エリアには不要な人員や機器を置かないようにする。安全な作業には、曲げ機械と平行にシートメタルを適切に配置することが重要です。不適切な配置は、シートが作業者に当たって怪我をする原因になります。
ガードレールを使用して屈曲作業エリアを隔離し、安全状態の目視管理を実施することを推奨する。ライトカーテンやAOPD(Active Optoelectronic Protective Devices:能動型光電子保護装置)のような最新の保護装置は、作業者が危険地帯に近づきすぎるのを防ぎ、必要に応じて機械を停止させることができる。
機械を初めて使用する前に、定期的なリスクアセスメントを実施し、できれば経験豊富なエンジニアがオペレーターのトレーニングを行うことが不可欠である。機器に保護アース(PE)が接続されていることを確認し、濡れた手で電気機器に触れないようにするなどの電気安全対策が重要である。
その他の注意事項としては、材料をあまり高く積み上げない、作業面を清潔に保つ、濡れた金属板は滑りやすいので取り扱いに注意する、などがある。使用前に機械が十分に潤滑されていることを確認することも、ロールや材料の損傷を防ぐことができる。
これらの安全注意事項に従うことで、オペレーターはエアベンディング作業に伴うリスクを大幅に軽減し、安全で効率的な作業環境を維持することができる。