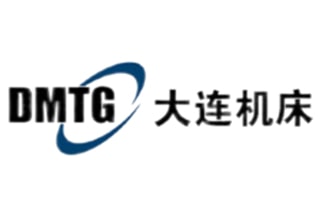
ただの粉が、なぜ地球上で最も強靭な素材のひとつに生まれ変わるのか?この記事では、最初の粉末冶金から最終的なコーティングまで、ブレードの複雑な製造工程を探ります。最後には、混合、プレス、焼結、研磨、刃先処理など、この重要な道具を作る各工程を理解できるだろう。ブレード製造の世界に飛び込み、その強度と耐久性を保証する精度と技術を発見してください。
今日、粉末冶金は大きな進歩を遂げ、世界で最も強靭な素材であるダイヤモンドの硬度に近づいている。
パウダーはありそうもない候補のように思えるかもしれないが、世界で最も硬い素材のひとつがパウダーから作られているというのは驚きだ。
私たちは、最初の粉末から最終的なブレードに至るまで、超硬合金ブレード製造の謎を解明することができます。
酸化タングステンは炭素と混合され、特殊な炉で処理されて炭化タングステンを生成する。 超硬合金.
炭化タングステンは、超硬合金の主成分を形成する非常に硬く脆い材料である。
コバルトは、超硬合金とタングステンカーバイドを組み合わせた場合の超硬合金の特性にとって重要な元素である。
コバルトの量が多いほど、超硬合金の靭性は向上する。逆にコバルトが少ないと硬くなり、耐摩耗性が高くなる。
異なるコンポーネントの重量比は、最高精度で綿密に測定されている。
420kgの原材料のバッチは、誤差が20g以下でなければならない。
混合は精密な冶金作業である。
最後に、この混合物を大きなボールミルで細かく繊細な粉末にする。
粉末混合物は適切な流動性を得るために噴霧乾燥を受けなければならない。
粉砕後の粉末の粒径は0.5~2.0マイクロメートルに達する。
まず、刃物の基本的な形状とサイズは、金型と高度に自動化されたCNC制御のプレス機による打ち抜きによって得られる。
プレス後のブレードは本物の超硬ブレードに似ているかもしれないが、その硬度はまだ要求される基準にはほど遠い。
その後、ロボットがプレスされたブレードを耐熱素材でできたディスクに移し替える。
刃を硬化させるため、1500℃で15時間の熱処理が施される。
焼結プロセスでは、コバルトと炭化タングステンの粒子が溶けて結合する。焼結炉のプロセスには2つの重要なステップがあります。第一に、ブレードは明らかに収縮し、正確な収縮のみが正しい公差を得ることを保証します。第二に、粉末混合物は 新素材 これは超硬合金として知られている。
期待通りの硬さになったとはいえ、納品までにはさらなる加工が必要だ。次の工程に進む前に、三次元測定機を使って刃物のサイズを入念にチェックする。
超硬チップの正確な形状を確保できるのは、ダイヤモンド研削だけです。
ブレードは幾何学的な角度に従って研磨される。
ほとんどのグラインダーには、さまざまな段階で刃をチェックし、測定するための測定コントロールが内蔵されている。
機械加工に必要な最大限の耐摩耗性を達成するために、刃先は正しい形状になるように処理される。
これらのブレードは、炭化ケイ素のコーティングが施された特殊なブラシで磨くことができる。
処理方法にかかわらず、最終的な結果を確認することは不可欠である。
全ブレードの約90%から95%に何らかのコーティングが施されている。
ブレードの表面に異物がないことを確認することは、異物がコーティングに付着して工具の性能に影響を与えるのを防ぐために非常に重要です。
ブレードのコーティング方法には2種類ある:化学蒸着法(CVD)と物理蒸着法(PVD)です。適切なコーティング方法の選択は、ブレードの材質と加工方法によって異なります。
コーティングの厚さはブレードの用途によって決まり、コーティングの質はブレードの耐久性と寿命に不可欠です。
技術的なノウハウは、次のような数種類の薄いコーティングを施すことである。 チタン 超硬合金の表面には、炭化物、酸化アルミニウム、窒化チタンなどがあります。これらのコーティングは、ブレードの寿命と耐久性を大幅に向上させることができます。
CVD法を用いる場合、ブレードは炉に入れられ、塩化物ガスと酸化物ガス、それにメタンと水素の混合ガスにさらされる。温度が1000℃に達すると、これらのガスが互いに反応し、超硬合金ブレードの表面に厚さわずか1000分の数ミリの均質な皮膜が形成される。
コーティングされたブレードの中には、表面が金色に輝くものもあり、より価値が高い。その耐久性はコーティングされていない刃物の5倍である。
PVDは、400℃でブレードに溶射する方法である。
自動検査に合格した後、レーザーで刃の素材に印をつけ、梱包する。
さらに、ブレードの箱には製品情報、シリアル番号、日付が記載されます。これは、優れた品質とサービスが期待できることをユーザーに約束するものです。
梱包後、ブレードは顧客に配送される。