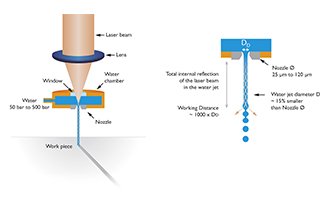
比類のない精度と効率で、複雑な高強度ステンレス鋼部品を製造することを想像してみてください。指向性エネルギー蒸着 (DED) や選択的レーザー溶融 (SLM) などの高度な技術を採用した 316L ステンレス鋼のレーザー積層造形は、業界に革命をもたらしている。この記事では、これらの最先端技術の方法、利点、課題を掘り下げ、製造プロセスへの影響と材料工学の将来についての洞察を提供します。この技術革新がどのように製品の耐久性と性能を向上させ、産業加工の新時代を約束するかを探る。
レーザー積層造形技術は、複雑な形状の部品を迅速に造形できるという利点があり、近年広く注目されている。
本稿では、DED(Directed Energy Deposition)とSLM(Selective Laser Melting)という2つのレーザー積層造形技術を紹介し、316Lステンレス鋼のレーザー積層造形について、一般的な欠陥、構造・組織、機械的特性の観点から研究の進展をまとめた。
316Lステンレス鋼のレーザー積層造形における既存の問題を分析し、その発展の展望を展望している。
レーザー積層造形には、指向性エネルギー堆積法(DED)と選択的レーザー溶融法(SLM)という2つの技術がある。
どちらも高エネルギーのレーザービームを熱源として使用し、金属粉末を局所的に溶かして溶融プールを形成する。レーザービームが遠ざかると、溶融プールは速やかに凝固する。しかし、DEDとSLM技術の動作原理は異なる。
DEDは、ニアネットシェイプ・レーザー・エンジニアリング、レーザー金属蒸着、ラピッドレーザー成形とも呼ばれ、典型的な同軸粉末伝送レーザー積層造形技術である。
パウダードラム内の金属粉末は、搬送パイプと特別に設計されたノズルから溶融プールに入る。レーザービームはコンピューター制御のもと、所定の軌道に沿って移動し、金属粉末を溶かして薄い層を形成する。
その後、蒸着ヘッドが上方に移動し、次の層を蒸着し続け、目的の部品ができるまで層ごとにこのプロセスを繰り返す。
を直接提供する。 フォーミングメタル 部品だけでなく、DED技術は、コーティングの準備、損傷した部品の修理、機能的に等級分けされた材料の準備にも使用できる。SLMは代表的な粉末床レーザー積層造形技術である。
金属粉末はノズルから噴射されるのではなく、あらかじめ粉末層上に均一に散布されている。レーザービームは、所定の経路に従ってパウダーベッドを選択的に溶融する。
1つの層が形成された後、粉末層は一定距離下方に移動し、再度粉末化され、選択的に溶融され、所望の部品が製造されるまで層ごとにこのプロセスを繰り返す。
の酸化を避ける。 316Lステンレス鋼 部品は、DEDとSLMの両方の成形工程を不活性ガス保護下で実施する必要がある。
Directed Energy Deposition(DED)とSelective Laser Melting(SLM)は、動作原理が異なるだけでなく、プロセスパラメーターも大きく異なる。DEDのレーザービーム径は通常600~1300μmであるのに対し、SLMのそれはかなり小さく、通常15~80μmである。
現在、レーザー積層造形に使用される316Lステンレス鋼粉末は、アトマイズによって調製されることが多い。
DEDとSLMのビーム径を考慮すると、DEDの316Lステンレス鋼粉末の粒径は通常45~180μmであり、SLMの粒径は通常5~63μmである。
DEDプロセスでは レーザー出力 (P)は200~720Wに達するが、走査速度(v)は10mm-s以下であることが多い。-1.
その結果、線エネルギー密度(EL=P/v)は非常に高く、1ミリメートルあたり数十ジュールから数百ジュールにもなる。線エネルギー密度が高いほどレーザーの浸透力が強くなるため、DEDの層厚は通常254~500μmに設定され、走査間隔は通常350~500μmに設定される。
対照的に、SLMではレーザー出力が低く(60~380W)、走査速度が速い(30~7000mm/s)ことが多い。-1)であるため、線エネルギー密度は非常に低く、通常は0.01~0.5J-mmである。-1.
融着欠陥が生じないようにするためには、SLMの走査間隔と層厚の両方を十分に小さくする必要があり、通常はそれぞれ20~300μmと10~60μmである。
DEDの形成中、温度勾配と冷却速度は最大10℃に達する。2 から103Kミリ-1 および103 から104K-s-1それぞれ
SLMでは線エネルギー密度が低いため、メルトプール内の温度勾配はさらに大きくなり、最大で10℃にもなる。3 から105K-mm-1に達する。4 から107K-s-1.
従来の冶金技術に比べ、レーザー積層造形技術には大きな利点がある。
しかし、プロセス・パラメーターの選 択を誤ると、気孔、融着不足、亀裂など、成形 過程で様々な欠陥が発生する可能性がある。これらの欠陥は、316Lステンレ ス鋼の機械的特性を著しく低下させる。
したがって、レーザー積層造形では、このような欠陥をいかに低減または除去するかが重要な課題となる。
気孔と融合不足は、316Lステンレス鋼のレーザー積層造形で最も一般的な2つの欠陥である。気孔は一般的に球状に見え、主に316Lステンレス鋼粉末中のガスに起因する。
粉末内の気孔は、メルトプールの急速な凝固中に完全には排出されず、部品内に残る。不活性ガスもメルトプールに巻き込まれ、気孔を形成することがある。
さらに、レーザー積層造形プロセスでは、部品の表面が最も高温になる。熱は内側に伝導し、広く浅いメルトプールを形成する。
しかし、レーザー出力が極めて高いか、レーザー走査速度が極めて低い場合、すなわちレーザー線エネルギー密度が極めて高い場合、溶融池形成は熱伝導モードから深い溶融モードに切り替わり、狭く深い溶融池チャネルが形成される。
この流路は非常に不安定で、溶融池の底に気孔を形成しやすい。一般に、メルトプールの幅と深さの比がある臨界値を下回ると、深部溶解モードが引き起こされると考えられている。
レーザー積層造形で316Lステンレス鋼の気孔率を制御するには、316Lステンレス鋼粉末のガス含有量を厳密に制御し、プロセスパラメーターを最適化して、深い溶融モードによる気孔の発生を避ける必要がある。
気孔の形成メカニズムとは対照的に、融解不足欠陥は一般的に、レーザーエネルギー密度が不十分なために融解深さが不十分となり、その結果、層間に不規則な形状の大きな空隙が生じることに起因する。この種の欠陥は一般に、層厚を薄くすることで解決できる。
バリフィケーションは、316Lステンレス鋼のレーザー積層造形における一般的な欠陥の1つである。この現象は、溶融金属液滴が連続的な溶融ラインを形成できず、代わりに形成された部品上に液滴状の表面が形成されることを指し、球状化の累積効果は部品の精度を著しく低下させます。
この影響は、成形キャビティ内の過剰な酸素含有量に起因することが多く、その結果、金属液滴の表面が酸化し、融着が妨げられる。従って、成形工程中の成形キャビティ内の酸素含有量を厳密に管理することが極めて重要である。
316Lステンレス鋼は積層造形に適した金属の1つであるが、316Lステンレス鋼のレーザー積層造形で割れ欠陥が発生したという報告がある。
熱割れ(または凝固割れ)は、割れの重要なメカニズムのひとつで、溶融プールの急速凝固の後期に発生することが多い。
この時点では、固相の割合が大きく、溶融池はセル状の部分構造で占められており、セル状の部分構造の境界には液相の膜がある。
この構造の強度は極めて低いため、引張応力下でクラックが発生しやすく、この時、クラック部分を埋めるように液体が流れ込むことは難しく、最終的には粒界熱クラックが形成される。
316Lステンレス鋼のレーザー積層造形における一般的な欠陥とその形成メカニズムを表1に示す。
表1: 316Lステンレス鋼のレーザー積層造形における一般的な欠陥とその形成メカニズム。
欠陥名 | 結成のメカニズム |
毛穴 | 粉末の中に気孔がある。 シールドガス プロセスパラメーターの不適切な選択は、過剰なレーザーエネルギー密度をもたらし、深い溶融モードを引き起こす。 |
不完全融合 | レーザーのエネルギー密度が不十分で、融合の深さが不十分。 |
スフェロイド化 | 酸素が過剰に含まれていると、金属液滴が合流して連続した溶融ラインを形成することができない。 |
クラッキング | 凝固後期には、セルラー下部構造境界の液相膜が引張応力で割れる。 |
高い温度勾配と冷却速度のために、凝固は レーザー加工 アディティブ・マニュファクチャリングは、急速な焼き入れ効果を示す。
このようにして調製された316Lステンレス鋼は、極めて非平衡な構造を示し、従来の 鋳造法 は達成できない。
通常、柱状の結晶構造を形成し、図1に描かれているように、柱状の結晶粒の中に多数の小さな細胞状の部分構造を持つ。
凝固プロセス(鋳造、溶接、レーザー積層造形などを含む)では、固液界面の最前線における液相の温度勾配Gと凝固フロントの成長速度Vが、結晶粒の形態とサイズ、内部下部構造を決定する。
G/Vが小さいほど、等軸粒構造が形成されやすく、逆に柱状粒構造が形成されやすい。温度勾配と成長速度はメルトプール全体で異なる。
一般的に、メルトプールの底部は温度勾配が大きく成長速度が小さいため柱状結晶の形成が促進され、メルトプールの上部は温度勾配が小さく成長速度が速いため等軸晶の形成が促進される。
レーザー積層造形法では、層ごとの堆積法を用いる。十分な層間結合を確保するため、前の層の材料の一部が再溶融される。そのため、メルトプールの上部にある等軸結晶構造は存在しないことが多く、メルトプールの下部にある柱状結晶はエピタキシャル成長によって層ごとに伸びる。
さらに、鋳造されたままの316Lステンレス鋼の樹枝状構造とは異なり、レーザー積層造形のメルトプールは凝固中に極めて速く冷却されるため、二次デンドライトの形成と成長が制限される。
そのため、レーザー積層造形中の316Lステンレス鋼メルトプールの固液界面は、通常、細胞成長によって進行する。
凝固中、DED成形された316Lステンレス鋼は通常、一次凝固を形成する。 オーステナイト 構造と、細胞下部構造の細胞壁上では、クロムやモリブデンなどのフェライト安定化元素の偏析が顕著であり、その結果、少量のフェライトの形成が促進される。
DEDと比較すると、SLMは冷却が速く、元素偏析の影響は大幅に低減されるが、一般的に安定したフェライトを形成するには不十分であるため、SLMで形成された316Lステンレス鋼は通常、単相を示す。 オーステナイト 構造で、フェライトの形成はない。
セル状部分構造のセル壁には、クロムやモリブデンなどのフェライト安定化元素が偏析していることに加え、隣接するセル状部分構造間のわずかな方位差により、セル壁には多数の転位が集積している一方、セル状部分構造内部の転位密度は比較的低く、典型的な転位セルを形成している。
さらに、レーザー積層造形によって316Lステンレス鋼に特定の結晶学的テクスチャーが形成される。プロセス全体を通して、熱流動方向は溶融プール内で変化するが、全体としては形成方向と反対である。
レーザー積層造形によって形成された316Lステンレ ス鋼の組織は、主に面心立方構造のオーステナイトから 成っている。
方向は立方晶の最速成長方向であるため、316Lステンレス鋼は、レーザー積層造形中に形成方向に沿って繊維状のテクスチャを形成するのが一般的である。レーザー走査戦略などのプロセスパラメーターを調整することで、テクスチャーの形成を効果的に制御できます。
について 降伏強度 レーザー積層造形法で製造された316Lステン レス鋼の降伏強度は300~600MPa、引張強度は 400~800MPaであり、従来の方法で製造された 316Lステンレス鋼の降伏強度(200~300MPa)および引張 強度(500~600MPa)よりも大幅に高い。
レーザー添加法で製造された316Lステンレス鋼の超高強度降伏強度は、微細粒(サイズ約0.2mm)、セル状部分構造(直径1μm未満)、高密度小角粒界(最大41%)、転位ネットワーク(数百ナノメートル規模)、析出相(サイズ10~150nm)、局所的元素偏析(範囲1nm未満)などのマルチスケール構造組織に起因する。
このマルチスケール不均一組織は、316Lステンレス鋼の降伏後の安定した連続加工硬化にも寄与している。
さらに、従来のプロセスで作製された316Lステンレス鋼と同様に、レーザー積層造形316Lステンレス鋼も、引張塑性変形プロセス中の変形を補助するナノツインの形成による動的ホールペッチ効果を示し、加工硬化効果を高めるのに役立つため、高い引張強度と超高破断後伸びを達成することができる。
レーザー積層造形316Lステンレス鋼の破断後伸び率は、材料内部の気孔率と密接に関連している。
レーザー積層造形で形成された316Lステンレ ス鋼は、一般的に柱状結晶構造を示し、特定の 結晶テクスチャーを形成するため、形成されたステンレ ス鋼の引張特性は異方性となる。スキャニング戦略を調整することで、結晶学的テクスチャを効果的に減少させ、降伏強度を等方性にすることができる。
しかし、柱状結晶構造は、レーザー積層造形で形成された316Lステンレス鋼の引張プロセスにおいて、異なる方向の加工硬化のレベルを変化させ、その結果、異なる方向の引張強さと破断後の伸びに大きな違いが生じる。
さらに、従来の316Lステンレ ス鋼製造工程では、塑性変形中にマルテンサイト相変態を引き 起こす可能性があるが、レーザー積層造形316Lステンレ ス鋼の塑性変形に関する現在の研究では、変形誘起 マルテンサイト相変態は見つかっていない。
レーザー積層造形で形成された316Lステンレス鋼の疲労性能は、微細構造、内部欠陥などさまざまな要因に影響される、 表面粗さそしてローディングの方向。
レーザー積層造形で形成された316Lステンレス鋼の構造内の微細なセル下部構造は、転位すべりおよびき裂の核形成を著しく阻害し、316Lステンレス鋼の疲労性能を大幅に向上させる。
レーザー積層造形後、316Lステンレス鋼部品には通常、加工後の熱処理が必要であり、その間に316Lステンレス鋼の微細構造が変化し、疲労性能に影響を与える可能性がある。
研究によると、ストレス解消の後に アニール 470℃では、レーザー積層造形316Lステンレス鋼のセル下部構造は大きく変化しないため、低温応力除去焼鈍は疲労強度に大きな影響を与えない。
しかし、熱処理温度が十分に高い場合、レーザー積層造形316Lステンレス鋼のセル下部構造に影響を与え、疲労性能に影響を与える可能性がある。
レーザー積層造形によって形成された316Lステンレ ス鋼の疲労性能は、内部欠陥と表面粗さによって 著しく劣化する。研究によると、内部欠陥(ボイドや未溶融粉末など)や粗い表面は、316Lステンレス鋼の局所的な応力集中につながる。
このような応力集中部位は、疲労き裂の核発生の初期部位となる傾向があり、その結果、疲労き裂の発生が促進される。 疲労故障.さらに、負荷方向は、レーザー積層造形によって形成された316Lステンレス鋼の疲労性能に著しく影響する。
レーザー成形された316Lステンレ ス鋼の疲労強度は、荷重方向が成形方向と直角の場 合に最も高く、平行の場合は低く、45度の角度で は最も低くなる。
しかし、レーザー成形された316Lステンレス鋼の疲労き裂進展メカニズムに関する現在の研究は、まだ始まったばかりであり、多くのメカニズムが不明なままであるか、矛盾していることさえある。
316Lステンレス鋼は、その卓越した機械的特性と耐食性を併せ持ち、最も広く使用されている鋼のひとつです。 ステンレス素材.従来の鋳造方法では、結晶粒が粗く強度の低い316Lステンレス鋼が製造されていた。
熱機械加工は、結晶粒を著しく微細化し、高密度の転位を導入することで、316Lステンレス鋼の強度を向上させる。
しかし、この手順は複雑で、通常は単純な形状の部品に使用される。
層ごとの堆積と急速な凝固を特徴とするレーザー積層造形技術は、複雑な部品の迅速な成形を可能にし、従来の冶金的手法にはない、小さな結晶粒、内部のセル状部分構造、高密度の小角粒界、高密度の転位などのユニークな組織的特徴を与える。
316Lステンレス鋼のレーザー積層造形では、従来の冶金的手法で作製された316Lステンレス鋼と比較して、優れた強度と塑性が得られる。
しかし、レーザー積層造形技術は、研究と応用の初期段階にある。今後の研究では、レーザー積層造形によって成形された316Lステンレス鋼の微細構造と機械的挙動をさらに探求するとともに、プロセス・パラメーターが構造と性能に及ぼす影響を深く調査する必要がある。
製造工程を正確に管理することで、広範な産業への応用をより技術的にサポートすることができる。
さらに、レーザー積層造形によって成形された316Lステンレス鋼の性能の異方性を改善するために結晶組織を制御すること、および疲労亀裂の伝播パターンを解明することは、今後の不可欠な研究分野である。