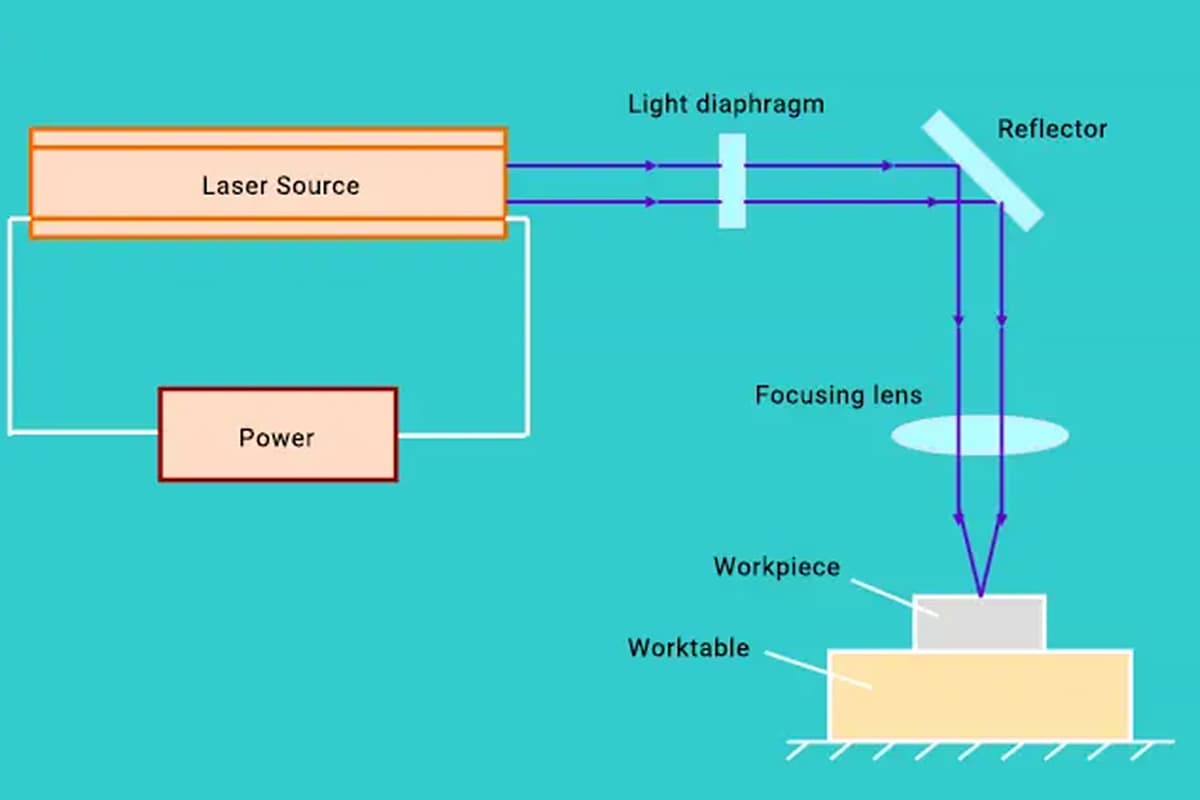
急速に進化する金属切断の世界では、レーザーとプラズマの戦いが繰り広げられている。技術の進歩に伴い、状況は変化し、長年の思い込みが覆される。業界を再構築する最先端の開発を探求し、超高出力レーザーの台頭が金属切断の方法にどのような革命をもたらしているのかを発見しましょう。金属加工の2つの巨頭の魅力的な比較に飛び込む準備をしよう。
レーザー切断技術の進化は、金属加工の風景を大きく変えた。歴史的に、レーザー切断は10mm以下の薄板加工を支配し、プラズマ切断はその優れた速度により30~50mmの厚さの範囲では明確な優位性を保っていた。しかし、マルチキロワットレーザーの出現、特に60kWシステムの広範な採用により、レーザー切断能力は中厚板用途に劇的に拡大した。
この技術的飛躍はプラズマ切断市場の著しい衰退を促し、多くの応用場面でレーザーシステムが徐々にプラズマに取って代わっている。レーザー切断の急速な台頭は、高出力ファイバーレーザー技術の成熟と、効率的で高精度な厚板加工を必要とする鉄鋼建設、造船、航空宇宙、原子力などの産業からの需要の急増という2つの主な要因に起因している。
マルチキロワットレーザーに対する業界の熱意は容赦なく、レーザー分野に急速に浸透している。しかし、この傾向には否定的な意見もないわけではなく、特に最近導入された60kWレーザー切断機については、業界の専門家の間でかなりの議論が巻き起こっている。
当初の懐疑的な見方とは裏腹に、60kWレーザー切断システムに対する市場の需要は、6カ月以内という極めて短い期間で供給可能量を上回った。特筆すべきは、鉄鋼建設セクターがこの超高出力レーザー切断機を強く好み、プラズマ切断システムに取って代わるために繰り返し投資していることである。この傾向は、以前の疑問と矛盾するように見え、金属切断工程における超高出力レーザーの変革の可能性を強調している。
これらの先進的なレーザーシステムの影響は、従来のプロセスの置き換えをはるかに超え、アプリケーションシナリオに新たな可能性を提供し、金属加工の風景を根本的に変えています。この技術が進化を続けるにつれて、さまざまな産業分野にわたる厚板加工のさらなる効率化と能力の解放が約束される。
プラズマ切断からレーザー技術への置き換えが加速している。
レーザー切断が普及する以前から、プラズマ切断は金属加工において最も成熟したプロセスであった。高温プラズマアークの熱を利用して切断部の金属を局所的に溶かし、高速プラズマの勢いを利用して溶けた金属を排出し、切断部を形成する。プラズマ切断は、リーズナブルな品質とコストで知られていた。当時、プラズマ切断は切断速度が速く、滑らかであったため、薄板や中板の分野でまだ広く使われていた。 カーフ.
しかし、レーザー切断の出現により、プラズマ切断に一定の影響を与えるようになった。薄板切断の領域では、キロワットレベルのファイバーレーザーは、品質と効率の面でプラズマ切断よりも絶対的な優位性を持っている。その高精度、狭い切り口、最小限の熱影響部、バリのないエッジ、速い切断速度により、この分野ではファイバーレーザーが好ましい選択肢となっている。対照的に、プラズマ切断の欠点はますます明らかになってきている。
レーザー切断の影響に対抗するため、装置メーカーは切断面の粗さや垂直度の低さといった問題に対処するため、より洗練されたプラズマ切断機を開発してきた。ノズルの開口サイズを小さくすることで、高度に圧縮されたアークを作り出し、電流密度を大幅に高めて、より高い切断精度と表面仕上げを達成する。とはいえ、薄板領域でのプラズマ切断は、加工効率、精度、環境への配慮の点で、レーザー切断にはまだ太刀打ちできない。
加工材料の厚みが増すにつれて、キロワットレベルのレーザー切断も課題に直面した。30~50mmの中厚板セグメントでは、レーザー切断の切断速度は、この領域でその地位を維持している精密プラズマ切断機の切断速度を大幅に下回った。
2020年までに、10キロワット級レーザー切断技術の出現は、金属加工に新たな息吹を吹き込み、伝統産業の変革とアップグレードを助けた。当時、レーザー切断は10キロワット時代に突入し、プラズマに対する第2ラウンドの挑戦を開始し、広大なプラズマ切断市場を激しく争った。
厚さ20mmまでの炭素鋼/ステンレス鋼の場合、20kWのレーザー切断システムは300Aのプラズマ切断機の効率を上回る。しかし、レーザー切断の初期購入コストはプラズマ切断よりもかなり高く、ユーザーは2つの選択肢の間で揺れ動くことになる。全面的な買い替えを検討するには、まだ時期尚早だった。
2022年までに、30kWレーザー技術の普及はプラズマ切断の支配的地位を揺るがし始め、特に中厚板市場に影響を与える。
2023年、国産の超高出力ファイバーレーザー技術の急速な進歩により、60kWのレーザーが登場し、切断厚さの限界を真に突破し、再びプラズマ切断に挑戦した。
切断効率と品質の点で、60kWレーザー切断は今やプラズマ切断に完全に取って代わる能力を持つ。現在、レーザー切断とプラズマ切断は、総合的な経済効果の点で互角であり、それぞれが市場の半分を占めている。超高出力レーザー切断は、極めて幅広い応用の可能性を示している。
近年、レーザー切断アプリケーションは、川下産業における需要の進化と高出力レーザーシステムのコスト低下により、急激な成長を遂げている。この急成長は特に精密製造分野で顕著であり、この技術の能力はますます厳しくなる生産要件に合致している。
プラズマ切断は、厚い材料では依然として有効な選択肢ですが、厚さ6mm以下の板金加工、特に高い切断精度が要求される用途では、限界に直面しています。プラズマ切断時に発生する高熱は、熱歪みやエッジの変形を引き起こし、薄いワークピースの寸法安定性を損なう可能性があります。
逆に、レーザー切断は幅広い材料に適した方法として登場し、明確なプロセス上の利点を示している。その精度と汎用性は、高融点材料、耐熱合金、超硬合金を扱う場合に特に有益です。集光されたレーザービームは、熱影響部を最小限に抑え、よりきれいな切断と材料の歪みの低減を実現します。さらに、レーザー切断は半導体材料、非金属基板、高度な複合材料の加工に優れており、比類のない精度とエッジ品質を提供します。多様な材料を高精度で扱うこの技術は、航空宇宙部品からマイクロエレクトロニクスに至るまで、現代の製造工程の要として位置づけられている。
ファイバーレーザー切断 | プラズマ切断 | |
原則 | A高パワー密度レーザー ビームを使用して材料の表面を走査し、数千度から数万度の温度まで急速に加熱する。 これにより材料は溶融または気化し、溶融または気化した材料は高圧ガスでスリットから除去される。 | 酸素または窒素を作動ガスとして、高温・高速のプラズマアークが熱源となり、切断される金属を局部的に溶かす。 溶けた金属は高速気流によって除去され、狭いスリットが形成される。 |
素材 | 金属材料、特殊金属材料、非金属材料 | 炭素鋼、ステンレス鋼、アルミニウム、銅、鋳鉄、その他の金属材料 |
切断厚さ | 中厚板 | 中薄板 |
切断精度 | 仕上げ加工(0.2mm以内) | 粗加工(1mm以内) |
スリット幅 | 非常に小さい(0.2~0.3mm) | 小さい |
熱影響部 | 非常に小さい(幅0.1mm) | 小さい |
プレートの変形 | 非常に小さい | 小さい |
一部のパンチ機能をレーザー切断に置き換える場合、以下のことが必要になる場合がある。 プレスブレーキ購入 その後の曲げ工程を完了させる。
これは、次のような場合に顧客がよく考慮することである。 レーザー切断機の購入.
項目 | ファイバーレーザー切断 | プラズマ切断 | ファイバーレーザーの利点 |
測位精度 | 0.14mm | 0.4mm | 高精度 |
断面垂直度 | 0.2mm(40mm) | 5mm(40mm) | 仕上げ不要 |
スリット幅 | 0.2-1.5mm | 2-5mm | 材料の節約 |
予約エッジと共通エッジ | 3-4mm | 10mm | 材料の節約 |
熱影響部 | 0.1-0.4mm | 0.5-2.0mm | 小さな変形 |
セクションの質 | スラグの垂れ下がりが少ない。 | ノーマル | 研削不要 |
切断速度(20mm以内) | 非常に速い | ノーマル | 高い生産効率 |
小さな穴を開ける | 直径深さ比: 10-20% | 穴を開けられない | セーブ ボーリング マシンとトランスファー |
面取り | 面取り | 一般的には | セービング面取り機 |
職場環境 | クリーン | 家中に煙が充満 | 健康と環境保護 |
高出力レーザーの普及により、レーザー切断装置は厚さの限界を超えることができるようになった。
以前は、高出力レーザーの販売量は非常に少なく、レーザー切断の適用は長い間、厚さによって制限されていた。
伝統的に、 フレームカット 厚板や極厚板を低精度で加工するのに適しており、50mm以上の厚板では明らかに速度面で有利である。
一方、プラズマ切断は、30~50mmの範囲では速度面で明らかに有利だが、極薄板(2mm未満)には適さない。
一方、キロワットレベルのレーザーを主に使用するレーザー切断は、10mm以下の板ではスピードと精度の面で明らかに有利である。
近年、高出力レーザーの普及に伴い、レーザー切断装置は中厚物切断に徐々に浸透している。 プレートカット 市場だ。
20kWレーザー切断機の限界切断厚みと最適切断厚み(mm)が含まれています。
パワーの増大は、切断厚さの増大と装置の効率化につながる。
統計によると、20kWレーザー切断機は軟鋼で50mm、ステンレス鋼で40mmの最適切断厚を達成している。
鋼板は一般に、厚さによって薄板(4mm未満)、中板(4~20mm)、厚板(20~60mm)、極厚板(60mm以上)に分類される。
切断出力は10000ワットで、レーザー切断装置は中板やほとんどの厚板を切断できるようになり、中板の分野にも用途が広がった。
さらに、高出力レーザーは切断効率の向上にもつながる。
例えば、30000ワットのレーザー切断機で50mmの軟鋼を切断した場合の切断効率は次のようになる。 鋼板 は20000ワット機と比較して88%増加させることができる。
こちらも参照のこと:
プラズマ切断を上回る高出力ファイバーレーザー切断の利点
厚さ | 15kW (m/分) | 20kW (m/分) | 30kW (m/分) | 効率改善 (20kWを超える30kW) |
8 | 11 | 15 | 22 | 47% |
10 | 8 | 11 | 17 | 55% |
14 | 5 | 6 | 7.5 | 25% |
20 | 1.5 | 2.5 | 4.5 | 80% |
30 | 0.9 | 1.2 | 1.6 | 33% |
40 | 0.35 | 0.6 | 1 | 67% |
50 | 0.2 | 0.4 | 0.75 | 88% |
中厚の分野では プレートカットレーザー切断のコストは、プラズマ切断よりも大幅に低い。
プラズマ切断は厚板分野で使われる主な方法の一つだが、レーザー切断の方がコストが安い理由は2つある:
例えば、厚さ30mmの炭素鋼板を切断する場合、12kWレーザー切断、20kWレーザー切断、300Aプラズマ切断の1m当たりの操業コストは、それぞれ3.05元/m、1.32元/m、3.13元/mである。
20kWのレーザー切断方式は、300Aのプラズマ切断方式と比較して57.8%の運転コストを削減し、大きなコスト優位性を提供する。
レーザー切断とプラズマ切断のコスト比較
コスト項目 | レーザー切断(12KW) | レーザー切断(20kW) | プラズマ切断(300A) |
設備の脆弱部分(元/時間) | 5 | 5 | 70 (電極、ノズル、ボルテックスリングなど)。 |
酸素消費量 (元/時間) | 60 | 80 | 80 |
設備の脆弱部分(元/時間) | 10(板厚20mm以上) | 10(板厚20mm以上) | 12 |
ハンドリング(1名)+ポリッシング (2名) | 0 | 0 | 60 |
固定費 (元/時間) | 0 | 0 | 60 |
ドリル/ポジショニング/トランスファー (3名+備品) | 65(75) | 85(95) | 282 |
切削速度 (14mm炭素鋼) | 4m/分 | 6m/分 | 3.4m/分 |
メーター当たりの営業費用 | 65 / 60 / 4m = 0.27元/m | 85 / 60 / 6m = 0.24元/m | 282 / 60 / 3.4m = 1.38元/m |
切削速度 (30mm炭素鋼) | 0.41m/分 | 1.2m/分 | 1.5m/分 |
メーター当たりの営業費用 | 75 / 60 / 0.41m = 3.05元/m | 95 / 60 / 1.2m = 1.32元/m | 282 / 60 / 1.5m = 3.13元/m |
これまでの経験から、レーザー切断機とプラズマ切断機の比較は次のようになる:
レーザー切断機はワークピースにダメージを与えないが、プラズマ切断機は、特に切断プロセス中にプラズマ切断機のトーチやノズルに問題が発生した場合、プレートに多少のダメージを与える可能性がある。
レーザービームは微小な点に集光されるため、レーザー切断機の切断溝は狭くなる。一方、プラズマ切断機の切断溝はやや広い。
レーザー切断機は切断速度が速く、プラズマ切断機と比較して毎分最大10メートルの速度を出せるものもある。
レーザー切断機で作られる切断面は滑らかでバリがないため、高品質の切断ができる。
また、非接触の切断プロセスでもある。
熱の影響を受ける領域が最小限に抑えられ、ワークピースの熱変形がほとんどないため、二次加工の必要がなく、エッジの折り返しを防ぐことができる。
しかし、レーザー切断機では板厚に制限があり、加工コストも高くなる。
一方、プラズマ切断機は6mmから40mmまでの幅広い鋼板を切断でき、機種やパワーもさまざまだ。
レーザー切断機に比べて加工コストが低く、オペレーターのスキルも少なくて済む。
レーザー切断機は位置決め精度0.05mm、再位置決め精度0.02mmと高精度だが、厳しい作業環境が要求される。
一方、プラズマ切断機はレーザー切断機ほどの精度はないものの、作業環境や機動性の要求が低く、切断能力も幅広い。
これらの利点により、レーザー切断機は複雑な形状や高い精度が要求される部品の切断に適している。
しかし、切断可能な板厚は限られており、通常は8mm以下の板厚の切断にしか使用されない。
プラズマ切断の欠点は、厚板、特に20mm以上の板を切断するのが難しいことである。
このような厚板を切断するには、より高いプラズマ出力が必要となり、装置のコストが高くなる。
1.レーザー切断とプラズマ切断の比較表
レーザー切断(CO2レーザー4kW) | プラズマ切断(O2プラズマ230A) | ||
---|---|---|---|
カット可能な素材 | 金属: 炭素鋼, 低 合金鋼ステンレス鋼、高合金鋼、アルミニウム、銅合金など; 非金属:セラミックス、プラスチック、ゴム、木材、皮革、布、紙、フィルムなど | 炭素鋼、低合金鋼、ステンレス鋼などの高合金鋼。 その他の非金属高粘度材料(ゴム、フィルムなど)、脆性材料(セラミックス、ガラスなど)は処理できない。 | |
最大切断厚さ | 25mm(軟鋼) | 150mm(ss, ms) | |
切削速度 (mm/min) | 厚さ < 1 | >10,000 | カットできない |
2 | 7,000 | カットできない | |
6 | 3,000 | 3,700 | |
12 | 1,800 | 2,700 | |
25 | 500 | 1,200 | |
50 | カットできない | 250 | |
> 100 | カットできない | - | |
スロット幅 | 狭い | 非常に広い | |
16mmマイルドで0.6mm前後 鋼材切断 | 16mm軟鋼切断で0.5mm前後 | ||
カッティングサイズ 精度(変形をカット) | 非常に良い | ノーマル | |
誤差 ±0.15mm | 誤差0.5~1mm | ||
メリット | 高精度加工が可能。 | ポータブル | |
熱変形はほとんどない。 | 低コストで高速カットオフ | ||
デメリット | 穴あけに要する時間は、板厚が厚くなるにつれて大幅に増加する。 加工表面の品質は、素材表面の状態に左右される。 の変動 素材構成 は切断面の品質に影響を与える可能性がある。 | 電極とノズルの寿命は短く、1日に2回の交換が必要。 カットの幅が広く、変形が大きい。 ノズルや電極の消耗により、切断幅や形状が変化することがあります。 切断時に大きな音がする。 大量の粉塵が発生する。 穴径が大きい(φ12mm~φ16mm)。 磁気を帯びた材料を切るのは難しい。 |
2.レーザー切断とプラズマ切断の切断溝比較
3.酸素プラズマの消耗品寿命。
切断方法 | 電極の種類 | 電極の加工。 | 電極寿命 | ノズル寿命 |
---|---|---|---|---|
酸素プラズマ切断。 | Sタイプ | 初期開発 | 60分 | 45分 |
Fタイプ | 修正版を挿入する | 120分 | 60分 | |
LLタイプ | 特殊金属の挿入。 | 180分 | 60分 | |
水添加式酸素プラズマ切断 | Fタイプに似ている | 修正版を挿入する | 120分 | 150分 |
アーク開閉1サイクル、耐久試験1分間寿命比較(遮断電流値:250A)
4板厚とコストの関係。
5様々な切断方法の切開幅と切断精度。
6様々な切断方法の切断条件。
高温を利用した加工法 プラズマアーク 酸素または窒素を作動ガスとして使用し、金属部品の切り込みを溶かして蒸発させる熱。
その後、高速プラズマ流の勢いを利用して溶融金属を除去し、溝状の継ぎ目を形成する。
こちらも参照のこと:
レーザー装置で生成されたレーザーは、一連のミラーを透過し、集光レンズによって被加工物の表面に集光され、被加工物上のホットスポットを溶融または蒸発させ、スリットを形成する。
同時に、補助ガスが切断工程で利用され、スリットからスラグを除去し、最終的に加工の目的を達成する。
こちらも参照のこと:
プラズマ切断は、幅広い金属材料に適した汎用性の高いプロセスであり、特に中厚板の切断に優れています。その利点は、切断速度が速いこと、切り口幅が狭いこと、熱影響部(HAZ)が最小であること、加工物の歪みが少ないこと、費用対効果が高いことなどである。このプロセスは、高温プラズマアークを利用して材料を溶融・排出し、導電性金属の効率的な切断を可能にする。
しかし、プラズマ切断には限界がある。プラズマ切断では通常、切断端に0.5~1.5度のわずかな開先角が生じるため、精密な用途では二次加工が必要になる場合がある。さらに、高温プラズマは切断面に局所的な硬化を引き起こし、重要な部分の材料特性に影響を与える可能性がある。
レーザー切断は逆に、薄板から中厚板向けに最適化されており、材料適合性において卓越した汎用性を誇っている。金属、非金属、セラミック、複合材料、さらにはガラスのような特殊な材料も効果的に加工できる。高度に集光された強力なレーザービームは、局所的な溶融、気化、化学反応による正確な材料除去を可能にします。
レーザービームの固有の特性である高い指向性、明るさ、出力密度は、レーザー切断の多くの利点に変換されます。これには、非常に速い切断速度、優れた加工精度(多くの場合±0.1mm以内)、非常に狭い切り口幅(薄い材料では0.1mm程度)が含まれる。得られるカットエッジは一般的に高品質であるため、後加工は最小限または全く必要なく、生産ワークフローが合理化される。
材料切断の用途で2つの技術を比較すると、レーザー切断はより幅広い材料に対応でき、特に薄板加工に有利である。高精度、複雑な形状、最小限の入熱を必要とする場面で優れている。また、レーザーシステムは、非接触の性質と精密な制御により、自動化された生産ラインに容易に組み込むことができる。
しかし、コスト・ベネフィット分析では、特に厚い材料や超高精度が重要でない場合など、多くの産業シーンでプラズマ切断が有利である。プラズマシステムは一般的に初期投資コストが低く、運転経費が削減され、中厚板部品の大規模生産では費用対効果が高くなります。
プラズマ切断とレーザー切断のどちらを選択するかは、最終的には特定の用途要件、材料の種類と厚さ、生産量、予算の制約によって決まる。多くの先進的な製造施設では、多様なプロジェクトや材料において切断能力を最適化するために、両方の技術を採用しています。
従来の切断方法と比較して、レーザー切断機にはいくつかの特筆すべき利点がある:
しかし、レーザー切断にはデメリットもある:
プラズマ切断にも長所と短所がある:
メリット:
中厚板の切断では、プラズマ切断はレーザー切断や火炎切断よりもはるかに高い切断速度を達成することができる。
さらに、レーザー切断に比べて設備への初期投資が少なく、メンテナンスコストも大幅に低い。
デメリット:
プラズマ切断の欠点は以下の通り:
貧しい 矩 その結果、刃先が著しく斜めになる。
切削スラグが多く発生するため、研削による除去が必要となり、人件費が増加する。
切断時に有害な粉塵やアーク光が発生する。しかし、水中プラズマ切断はこの問題を軽減することができる。
長期的には切断ノズルの消費量が多く、コスト高につながる。
この記事では、レーザー切断とプラズマ切断技術の包括的な概要を提供し、その原理、機能、板金加工における応用について検討した。
このような最先端の方法を探求することで、それぞれの長所と限界をより深く理解していただくことを目的としています。この知識は、現代の金属加工プロセスにおいて、十分な情報に基づいた意思決定を行うために極めて重要です。
プラズマ切断とレーザー切断のどちらを選択するかは、最終的には以下のような複雑な要因の相互作用にかかっている:
どの技術がお客様の製造ニーズに最も適しているか、まだご不明な場合は、経験豊富な冶金学者と加工スペシャリストで構成される当社のチームにご相談ください。当社の専門家が、お客様独自の生産環境、予算の制約、品質基準を考慮しながら、お客様の業務に最も有利な決定を下せるよう、オーダーメイドのガイダンスを提供いたします。