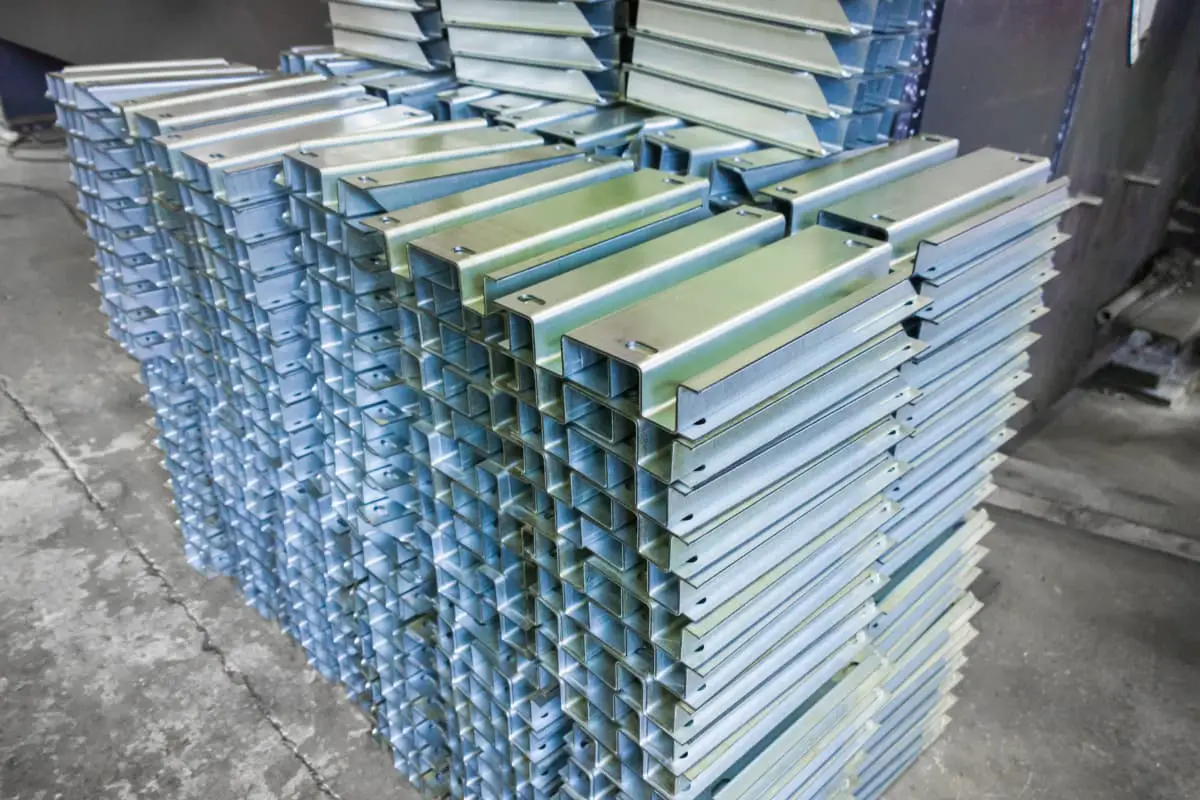
板金加工において、安全で耐久性のある接合部を確保するにはどうすればよいだろうか?この記事では、TOXリベッティング、溶接、釘リベッティングを含む様々な接合と締結技術について説明します。それぞれの方法の長所と短所、実用的な応用、そしてそれらが金属構造物の強度と完全性にどのように貢献するかを発見するでしょう。どの技術があなたの特定の製作ニーズに最も適しているかを理解するために、飛び込んでみてください。
接続にはさまざまな種類があり、接続後に取り外しが可能かどうかで、取り外し可能な接続と取り外し不可能な接続に分けられる。
この章では主に、TOXリベッティング、溶接、パンチング・リベッティング、ネイル・リベッティングを含む、取外し不可能な接続について述べる。
1.定義
単純な凸型を使用することで、接続部品は凹型に押し込まれます。さらに圧力をかけると、凹型内の材料が外側に流れ出し、バリのない滑らかな円形の接続部ができる。
コーティングや塗装層がある板材であっても、耐食性には影響しない。なぜなら、コーティングや塗装層も材料とともに変形し、流動するからである。
下図に示すように、材料は両側に向かって絞り込まれ、凹型側のプレートに入り、TOX接続点が形成される:
2.接続方法:
TOXリベッティングは、同じまたは異なる材料と厚さの2層以上の板を接続するために使用することができます。
同じ条件下で、TOXシングルポイントの静的接続強度は50%-70%である。 スポット溶接ダブルポイントの強度はスポット溶接と同じである。
3.異なるリベットポイントの接続範囲:(単位mm)
リベット径 | 12 | 10 | 8 | 6 | 5 | 4 | 3 |
接続材料の厚さの範囲 | 4~11 | 1.75~7 | 1.6~6.0 | 1.0~3.0 | 0.9~2.5 | 0.6~2.0 | 0.5~1.5 |
端からTOXリベット中心までの最短距離 | 10 | 8 | 7 | 6 | 6 | 5 | 4 |
注:TOXリベットの直径は接続強度と密接な関係がある。直径が大きいほど、接続は強くなる。
4.TOXリベットの欠陥:
(1) 位置決めのために位置決め治具や金型ブロックに頼る。
(2) 連結材料の最小幅は、TOX金型の直径に影響される。
5.TOX金型の利点:
特殊な装置に使用されるだけでなく、通常の装置にも適しています。 パンチプレスそのため、リベッティングの範囲はTOXが要求する範囲よりもはるかに広い。
コーティングや塗装が施された板材の場合、接続部の保護層は損傷せず、元の防錆特性は維持される。
6.TOXリベット成形の模式図:
その本質とは 溶接工程 とは、適切な物理的・化学的プロセスを用いて、分離した2つの表面の金属原子を格子間距離(0.3~0.5nm)に近づけ、金属結合を形成することで、2つの金属を1つにつなぎ、溶接の目的を達成することである。
製造工程では、タングステン不活性ガスが使用される。 アーク溶接 (TIG)、金属不活性ガス・アーク溶接(MIG)、スポット 溶接が最も一般的な溶接方法である。これら3つの溶接法について簡単に紹介する:
A.タングステンイナートガスアーク溶接
TIG溶接は 溶接工程 電極とアークゾーン、溶融金属がすべてアルゴンガスで保護され、空気から隔離されている。
電極はタングステンまたはタングステン合金棒でできており、アーク燃焼中に溶けることがなく、安定した溶接ができる。
ヘリウムガスを使用する場合 シールドガスヘリウムアーク溶接と呼ばれる。
TIG溶接 は、航空機製造、原子力、化学工学、繊維などの産業で広く使用されている。
酸化しやすい非鉄金属とその合金、ステンレス鋼、高温合金の溶接に適している、 チタン やチタン合金、モリブデン、ニオブ、ジルコニウムのような溶けにくい反応性金属がある。
しかし、タングステン電極の通電容量には限界があり、アーク出力も制限されるため、溶接深さが浅くなり、溶接強度が低下する。 溶接速度厚さ6mm以下のワークの溶接にのみ適している。
B.金属不活性ガスアーク溶接
MIG溶接は、ガス溶接としても知られている。 メタル・アーク 溶接(GMAW)は、電極として溶接ワイヤーを使用し、電極とアークゾーンはアルゴンなどの不活性ガスで保護される。
シールド・ガスにAr-O2、Ar-CO2、Ar-CO2-O2を使用する場合は、メタル・アクティブ・ガス(MAG)溶接と呼ばれる。
MIG溶接はほとんどの金属を溶接でき、特にアルミニウムとその合金、銅とその合金、ステンレス鋼などの溶接に適している。
電極に溶接ワイヤを使用するため、高密度の電流を流すことができ、溶融深さが大きく、充填速度が速い。
厚いアルミ板や銅板の溶接に適しており、溶接変形はTIG溶接より小さい。
MIG溶接は、直流逆接続を使用することもでき、アルミニウムとその合金を溶接する際に良好なカソード・スパッタリング効果を発揮する。
さらに、アルミニウムとその合金を溶接する場合、サブソニック・アーク固有の自己調整効果は、MIG溶接でより顕著になる。
C.スポット溶接
スポット溶接は、電極と被加工物の接触により発生する抵抗熱で、接合部の接触面とその周囲を溶かし、凝固させて溶接点を形成する溶接法である。
アルミニウムと鉄、アルミニウムと銅、ステンレス鋼と鋳鉄の混合溶接に使用できるが、スポット溶接は難しい。 アルミニウム溶接 とアルミニウムだ。
D. ろう付け
ろう付けは、母材よりも融点の低い金属フィラーを使用して、2つ以上の金属片を接合する方法である。
フィラーメタルは溶融し、毛細管現象によって母材を濡らし、凝固時に強固な接合部を形成する。
ろう付けには加熱と、溶融したろう材が空気に触れないようにする保護が必要である。
ろう付けには、炎ろう付け、誘導ろう付け、抵抗炉ろう付け、塩浴ろう付けなど、熱源や保護条件の違いによっていくつかの種類がある。
既存の溶接設備は大きく3つのタイプに分けられる: スポット溶接機手動溶接機(MIG & TIG)、溶接ロボット(MIG & TIG)。
A.スポット溶接機:
固定式C型スポット溶接機:
Qilong 100KVA AC IC同期制御スポット溶接機
パナソニック100KVA交流マイコン制御二次電流補償スポット溶接機(日本技術、パナソニック唐山製)
以上 スポット溶接機 亜鉛メッキ鋼板、冷延鋼板、ステンレス鋼板、馬口鉄、熱延鋼板の溶接が可能で、板厚範囲は0.3mm~6mm。
吊り下げ式スポット溶接機:
Quanxingブランドの48KVA吊りスポット溶接機(台湾で生産)は、2枚のプレートのラップジョイントのために0.2〜3ミリメートルの板厚範囲を溶接することができます。
蓄電式スポット溶接機:
Pengyuwei 4500J のコンデンサーの貯蔵のタイプ点溶接機械は、アルミニウムおよびアルミニウムを溶接できます 合金板 厚さは0.4mmから3.0mmである。
B.MIG 手動溶接機:
OTC350P直流パルスMIG溶接機とアメリカンフライマットMIG350A溶接機があり、板厚0.8mm以上の軟鋼、アルミ、銅の溶接が可能です。 アルミニウム合金 厚さ2mm以上のもの。
C.TIG 手動溶接機:
板厚0.4mm以上の軟鋼、板厚1.0mm以上のアルミ・アルミ合金の溶接が可能な日立HITACHI AC/DC兼用パルスTIG溶接機。
D.MIG溶接ロボット:
スウェーデンのABB社のMIG溶接ロボットと日本のYAKAWA社のMOTOMAN WF200MIG溶接ロボットがあり、亜鉛メッキ鋼板、冷延鋼板、ステンレス鋼板、馬口鉄、熱延鋼板、板厚0.8mm以上の溶接が可能です。
E.TIG溶接ロボット:
スウェーデンABB社製TIGノンフィラー溶接ロボットがあり、亜鉛メッキ鋼板、冷延鋼板、ステンレス鋼板、馬口鉄、厚さ0.4mm以上の熱延鋼板を溶接できる。
溶接記号 および溶接方法コードは、溶接構造図に使用される標準化された記号またはコードであり、一種のエンジニアリング言語を構成している。
中国の溶接記号と溶接方法コードは国家標準GB324-88「溶接記号表現方法」とGB5185-85「図面上の溶接と関連プロセスの表現コード」で定義されている。
これらの規格は、基本的に国際規格ISO2553-84「溶接記号の表現方法」およびISO4063-78「溶接および関連プロセスの図上表現」と一致している。
したがって、両者は同じ意味で使うことができる。
I.溶接記号
GB324-88「溶接記号の表現方法」規格では、溶接記号は溶融溶接と溶接の両方に適用されると規定している。 抵抗溶接.
この規格はまた、図面を簡素化するため、図面上の溶接部の表現には一般的に溶接記号を使用すべきであるが、技術的な図面手法も使用できると規定している。
国家規格で定められた溶接記号には、基本記号、補助記号、溶接寸法記号がある。
溶接記号は一般に基本記号と基準線で構成され、必要に応じて補助記号や溶接寸法記号などを追加することができる。
基本記号は溶接部の断面形状を表す。GB324-88規格に規定されている13の基本記号を表1-3に示す。
溶接補助記号は溶接部の表面形状を表す。GB324-88規格に規定されている3つの補助記号を表1-4に示す。
溶接の付加記号は、溶接の特定の特徴を補足するために使用される。GB324-88規格で規定されている追加記号を表1-5に示す。
溶接サイズ記号は、開先と溶接部の特徴的な寸法を表します。GB324-88規格に規定された16のサイズ記号を表1-6に示す。
表1-3:基本的な溶接記号。
シリアル番号 | 名称 | 概略図 | シンボル |
1 | エッジ溶接 (エッジの完全融合) | ![]() | ![]() |
2 | I字型溶接 | ![]() | ![]() |
3 | V字溶接 | ![]() | ![]() |
4 | 片側V字溶接 | ![]() | ![]() |
5 | 鈍いエッジのV字型溶接 | ![]() | ![]() |
6 | 鈍いエッジの片側V字溶接 | ![]() | ![]() |
7 | 鈍いエッジのU字型溶接 | ![]() | ![]() |
8 | 鈍いエッジのJ型溶接 | ![]() | ![]() |
9 | シーム溶接 | ![]() | ![]() |
10 | コーナー溶接 | ![]() | ![]() |
11 | プラグ溶接またはスロット溶接 | ![]() | ![]() |
12 | スポット溶接 | ![]() | ![]() |
13 | 突き合わせ溶接 | ![]() | ![]() |
表1-4:溶接補助記号
シリアル番号 | 名称 | 模式図 | シンボル | インストラクション |
1 | フラットシンボル | ![]() | ![]() | フラットな溶接面(一般に機械加工によって達成される) |
2 | コンケーブ・シンボル | ![]() | ![]() | 凹状の溶接面 |
3 | 凸記号 | ![]() | ![]() | 凸状溶接面 |
表1-5:補足溶接記号
シリアル番号 | 名称 | 模式図 | シンボル | インストラクション |
1 | バッキング・バー・シンボル | ![]() | ![]() | ルートがバッキング・バーになっている溶接部を示す。 |
2 | ステッチ溶接記号 | ![]() | ![]() | 3面の溶接を示す |
3 | 円周溶接記号 | ![]() | ![]() | 被加工物の外周の溶接を示す。 |
4 | オンサイト・シンボル | ![]() | 現場またはフィールドで行われた溶接を示す。 | |
5 | テール・シンボル "は | ![]() | マーキング溶接プロセス方法などについては、GB5185の内容を参照できる。 |
表1-6:溶接寸法記号
シリアル番号 | 名称 | 模式図 | シリアル番号 | 名称 | 模式図 |
d | ワークの厚さ | ![]() | aa | ベベル角 | ![]() |
b | ルート・ギャップ | ![]() | l | ウェルド・レングス "は | ![]() |
p | ブラント・エッジ | ![]() | n | 溶接セグメント番号 | ![]() |
c | 溶接幅 | ![]() | e | 溶接間隔 | ![]() |
d | フュージョン直径 | ![]() | K | 溶接脚サイズ | ![]() |
S | 有効スロート厚 | ![]() | H | 溝の深さ | ![]() |
N | 同一溶接部の数量記号 | ![]() | h | 補強の高さ | ![]() |
R | ルート半径 | ![]() | b | 溝面の開先角度 | ![]() |
2.溶接方法コード
溶接方法の表示と説明を簡素化するため、金属溶接や_溶接などのさまざまな溶接方法は、国家標準GB5185-85で指定されたアラビア数字で表すことができます。
表1-7は、国家標準GB5185-85に規定されている一般的な溶接方法のコードを示している。
表1-7:一般的に使用される主な溶接方法のコード。
溶接方法名 | 溶接方法コード | 溶接方法名 | 溶接方法コード |
アーク溶接 | 1 | 圧接 | 4 |
被覆アーク溶接(SMAW) | 111 | 摩擦圧接 | 42 |
サブマージアーク溶接(SAW) | 12 | 拡散溶接 | 45 |
ガス タングステンアーク溶接 (タングステンイナートガス(TIG)溶接としても知られる。 | 131 | その他の溶接方法 | 7 |
不活性ガス・シールドによるガス・メタル・ アーク溶接(GMAW)、別名メタル・イナート・ ガス(MIG)溶接 | 135 | エレクトロスラグ溶接 (ESW) | 72 |
非不活性ガス・シールドによるガス・メタル・ アーク溶接(GMAW)、別名メタル・アクティブ・ ガス(MAG)溶接 | 141 | エレクトロガス溶接(EGW) | 73 |
プラズマアーク 溶接(PAW) | 15 | レーザー溶接 | 751 |
抵抗溶接 | 2 | 電子ビーム溶接 | 76 |
スポット溶接 | 21 | スタッド溶接 | 78 |
シーム溶接 | 22 | 硬ロウ付け | |
フラッシュ溶接 | 24 | 硬ろう付け | 9 |
抵抗突合せ溶接 | 25 | ソフトソルダリング | 91 |
ガス溶接 | 3 | ろう付け。 | 94 |
酸素燃料溶接。 | 311 | – | – |
3.図面上の溶接記号の配置
3.1 基本要件
図面に溶接部を表現する完全な方法には、基本記号、補助記号、補助記号だけでなく、参照線、一部の寸法記号、データも含まれる。
溶接記号と溶接方法コードは、参照線と関連仕様によって正確に表現されなければならない。
基準線は一般に、矢尻のついた矢線と、2本の基準線(実線と破線)の2つの部分からなる。
3.2 アローとジョイントの関係
下図は、関節の矢印側と非矢印側の意味の一例である:
矢印の位置:
通常、溶接部に対する矢線の位置には特別な要件はないが、V字型、単一V字型、J字型の溶接部を示す場合、矢線はワークの溝のある側を指すべきである。必要であれば、矢線は一度曲げてもよい。
3.4 ベースラインの位置づけ
ベースラインの破線は、ベースラインの実線の上側または下側に引くことができる。ベースラインは一般に図面の下辺と平行であるべきだが、特別な条件下では下辺と垂直にすることもできる。
3.5 ベースラインに対する基本記号の位置:
溶接部と矢線が同じ側にある場合は、実線側に溶接部の基本記号を記す。
例えば、次の図のように:
溶接部が接合部の矢印のない側にある場合は、溶接部の基本記号をベースラインの破線側に記す。
対称溶接部や両面溶接部に印を付ける場合、破線を入れる必要はない。
4.溶接サイズ記号とその注釈位置:
4.1 溶接サイズ記号とデータのマーキングの原則を下図に示す:
溶接部の断面サイズは、基本記号の左側に記されている。
溶接部の長さ方向の寸法は、基本記号の右側に記されている。
基本記号の上側または下側には、溝角度、溝面角度、ルートギャップなどのサイズが記されている。
同じ溶接の数を示す記号が最後尾に記されている。
区別しにくいサイズデータが多い場合は、データの前に対応するサイズ記号を付加することもできる。
矢印の方向が変わっても、上記の原則は変わらない。
4.2 寸法記号の説明:
溶接の位置を決定する寸法は、溶接記号には記 載されていないが、パターンに記されている。
基本記号の右側に注釈や説明がない場合は、溶接がワークの全長にわたって連続していることを意味する。
基本記号の左側に注釈や説明がない場合は、突合せ溶接部が完全に貫通していなければならないことを意味する。
開先があるプラグ溶接やスロット溶接の場 合は、穴の底の寸法を示す必要がある。
1. ドローイングを理解する
製造工程では、工程設計担当者が図面を受け取ると、まずワークの構造を理解することから始まる。
その上で、溶接箇所、溶接方法、研磨の有無、その他特別な要求事項など、顧客が求める溶接内容を把握する。
顧客の意図を理解することは非常に重要であり、それによって後に採用するプロセスの流れが決まる。
2. 溶接方法の決定:
一般に、顧客の図面には、はんだ付けかスポット溶接か、溶接シームの長さ、断面の大きさなど、溶接方法と要求事項がすでに明記されている。
ただし、ハンダ付けからスポット溶接に変更した方が良いと思われる場合など、溶接方法の変更をお客様に確認させていただく場合もあります。
3. を決定する。 溶接ジョイント:
最も一般的な溶接継手は、自己溶接時にワークの両側が垂直に交差する場合である。下の図1に示すとおりである:
ほとんどの場合、顧客は次のようなことを考慮していない。 溶接性また、接合部は必ずしも実際の溶接要件を満たしているとは限らない。
そのため、90度直角継手のような溶接では、一般に調整が必要となる。
図2および図3に示すように、図2は薄い材料(2.0未満)のTIG溶接に最も適しており、図3は厚い材料のMIG溶接に適している。
エッジの巻き方については、実際の状況に応じて決定すればよいが、一般的には、以下のように考える。 曲げ角度そして、長い方を使って短い方を包むのがベストである。
4.溶接の位置決め:
2つ以上のワークを溶接する場合、互いの位置を決定できる関係が必要であり、これが位置決め問題である。
ワーク自体が位置決め構造を持っているかどうかによって、自己位置決めと固定具位置決めに分けられる。
以下では、これら2種類のポジショニングについて別々に説明する:
(1) セルフポジショニング:
一方のワークピースには、ある突起や留保された段差が作られ、他方のワークピースには、対応する凹部や穴が作られ、ワークピース間の位置決めを実現する。
現在、最も一般的に使用されているのは、ハーフシャー-凹ピット位置決めと、テノン-角溝位置決めの2種類である。
ハーフシアー-コンケーブ・ピット・ポジショニングの典型的な構造を下図に示す。
要求が高くない場合(ワークの溶接面が見えない場合など)は、凹ピットをスルーホールに加工することができるが、ワークが外部に露出している場合はスルーホールにすることは厳禁である。
この方法のもう一つの代替構造は、円形のハーフシアと凹型のピットを長方形にすることだが、これは推奨されない。
ハーフシャーとコンケーブピットの加工は、一般的にNCTで行われる。ハーフシャーは上向き、下向きどちらの仕様も金型がある。
フロント・コンケーブ・ピット専用の工具はないが、コンビネーション・ツールを使うことで加工できる。
直径3.1の逆凹ピットには専用の金型があるが、直径2.4の逆凹ピットには現在金型がなく、加工できない。
ハーフシア-凹ピットの位置決めを利用する方法には、ハーフシア構造の採用により、ハーフシア効果が厚板(T2.0以上)には不向きであること、ハーフシアの突出部が円弧状であり、制限機能を果たせないことなどの制約がある。
また、凹ピットは素材を強制的に絞り込むことで形成されるため、比較的柔らかい素材(AL、CRS、GIなど)にしか適用できず、硬い素材(SPHC、SUSなど)には不可能である。
要約すると、この方法は、GI、CRS、AL の2.0mm 以下の範囲の素材に適している。 板金.
テノンと角溝の位置関係を下図に示す:
このような位置決め方法を用いる場合、まず位置決め溝の仕様を決定する必要がある。
NCT切削を使用する場合は、NCT工具を使用して角穴を1パスで加工できると考えた方がよい。
もし レーザー切断 を使用する場合は、実際の状況に応じてサイズを決定することができます。一般的には、溝穴はテノンより0.1mm大きく、テノンの突出部分は位置決め溝の板厚を超えないようにします。
スロットは必ずしも長方形の穴(クローズドタイプ)である必要はなく、特定の状況に応じてオープンタイプにすることもできる。
(2) 2つのセルフポジショニング方式の適用範囲:
上記の2つの位置決め方法を比較すると、2つのワークの溶接面が互いに平行である場合、ハーフシアと凹ピットの位置決め方法が優れていることがわかる。
2つのワークの溶接面が互いに垂直な場合は、テノンと角溝の位置決め方法が適している。
(3) フィクスチャーの位置決め:
自己位置決めが図面の要件を満たせない場合、または高い位置決め要件が必要な場合は、特別な位置決め装置が必要です。 締め付け 固定化が必要であり、関連部門(オートメーションの研究開発など)との協力が必要である。
5.スポット溶接のプロセス要件:
(1) スポット溶接の総厚み:
スポット溶接の総厚みは8mmを超えてはならず、溶接スポットの大きさは一般に2T+3(2Tは2つの溶接部分の厚みを表す)である。
上部電極は中空で、冷却水によって冷却されるため、電極を無制限に小さくすることはできず、最小直径は一般に3~4mmである。
(2) 溶接スポットのパンチングとバーリング:
スポット溶接のワークピースは、互いに接触している面の一方に溶接スポットを打ち抜き、バリ取りをしなければならない。 溶接強度.
通常、バリの大きさはΦ1.5~2.5mm、高さは約0.3mmです。溶接するワークの片方に小さな突起を加工することで、溶接工程を改善することができます。
下図に示すように、溶接中に溶接ヘッドが突起を押して通電すると、小さな突起が溶けて接続が強固になり、信頼性が高まる。
(3) 2つの溶接部間の距離:
被溶接物の厚みが増すと、2つの溶接部間の距離も長くなる。
この距離が小さすぎると、ワークが過熱して変形しやすくなり、逆に大きすぎると、接合部の強度が不足し、2つのワークの間に亀裂が入る可能性がある。
一般に、2つの溶接部の間隔は35mmを超えないようにする(2mm以下の材料の場合)。
(4) 溶接ワーク間のギャップ:
スポット溶接の前に、2つのワーク間のギャップは通常0.8mmを超えないようにする。
ワークピースを曲げてからスポット溶接する場合、溶接部の位置と高さが非常に重要になる。
これらの配置が適切でないと、スポット溶接の位置がずれたり変形したりして、誤差が大きくなる可能性がある。
(5) スポット溶接による表面損傷:
スポット溶接箇所にはバリができやすく、研磨と防錆処理が必要である。
必要な場合は、スポット溶接部に銀塗料を塗ることができる。スポット溶接部を塗装する必要がある場合は、塗装前に研磨する必要がある。
(6) 亜鉛メッキ鋼板のスポット溶接:
亜鉛メッキ鋼板は主に亜鉛メッキ鋼板、鉛メッキ鋼板、アルミメッキ鋼板、錫メッキ鋼板などを含む。
生産現場では、亜鉛メッキ鋼板や亜鉛メッキ部品のスポット溶接が一般的です。
亜鉛層の厚さは一般的に20μm以下。
通常の鋼板のスポット溶接に比べ、亜鉛めっきの存在は溶接部の電流密度を低下させるだけでなく、電流場の分布を不安定にする。
また、電流を増加させると、電極の加工端面におけるCu-Zn合金の形成がさらに促進され、電極の消耗と被覆の損傷が加速される。
同時に、低融点亜鉛皮膜は、その結晶化過程でクラックや気孔を発生させる。 フュージョンゾーン.
そのため、亜鉛めっき鋼板のスポット溶接に適した仕様範囲は狭く、継手強度のばらつきが大きく、溶接性が悪い。
(7) スポット溶接の干渉処理範囲:
以下は、溶接機によるスポット溶接の模式図であり、2000年10月16日にスポット溶接グループから提供された加工範囲を示すデータである。
1.定義
穴押出しリベッティングは、打ち抜き穴と皿穴のある2つの部品を、リベッティング・ダイを使って分離不可能な接合部を形成するプロセスである。
利点パンチングとカウンターシンキングは2つの部品に固有の位置決めを提供する。穴押出しリベッティングは高い接合強度と専用工具の使用による高い効率をもたらす。
皿リベットジョイント データシート
シリアル番号 | 材料の厚さT(mm) | カウンターシンク高さH(mm) | カウンターシンク外径D(mm) | |||||||||||
3.0 | 3.8 | 4.0 | 4.8 | 5.0 | 6.0 | |||||||||
カウンターシンク内径dと下穴d0に対応する | ||||||||||||||
d | d0 | d | d0 | d | d0 | d | d0 | d | d0 | d | d0 | |||
1 | 0.5 | 1.2 | 2.4 | 1.5 | 3.2 | 2.4 | 3.4 | 2.6 | 4.2 | 3.4 | / | / | / | / |
2 | 0.8 | 2.0 | 2.3 | 0.7 | 3.1 | 1.8 | 3.3 | 2.1 | 4.1 | 2.9 | 4.3 | 3.2 | / | / |
3 | 1.0 | 2.4 | / | / | / | / | 3.2 | 1.8 | 4.0 | 2.7 | 4.2 | 2.9 | 5.2 | 4.0 |
4 | 1.2 | 2.7 | / | / | / | / | 3.0 | 1.2 | 3.8 | 2.3 | 4.0 | 2.5 | 5.0 | 3.6 |
5 | 1.5 | 3.2 | / | / | / | / | 2.8 | 1.0 | 3.6 | 1.7 | 3.8 | 2.0 | 4.8 | 3.2 |
注:皿リベットの一般原理はH=T+T'+(0.3~0.4)、D=D'-0.3、D-d=0.8Tである。T≧0.8mmの時、皿壁の厚さは0.4Tである。T<0.8mmの場合、カウンターシンクの肉厚は通常0.3mmです。H'は通常0.46±0.12とする。
1.分類:
プル・リベットは、平頭と丸頭(傘頭とも呼ばれる)の2種類に分けられる。
平頭プルリベットの場合、リベット頭部と接触する側は皿穴がなければならない。丸頭プルリベットでは、接触面は平らである。
2.定義:
リベット・ガンを使ってリベットのマンドレルを貫通穴のある2つの部品に通し、壊れるまで引っ張る。
3.プルリベットジョイントのパラメータ:
リベットのカテゴリー | リベットの公称直径D | 鋼板をリベットで固定する穴の直径 D1 | 長さL | M | ヘッド径 H | 頭の高さ P | 厚さ 鋼板 リベット用 | 極限強度(N) | |||
傘型 | フラットヘッド | 皿 | 剪断抵抗付きフラットヘッド | せん断抵抗 | 引張強度抵抗 | ||||||
アルミブラインドリベット | 2.4 | 2.5 | 5.7 7.3 8.9 | 1.42 | 4.8 | 0.7 | 0.8 | 1.0~3.2 3.2~4.8 4.8~6.4 | 1.6~3.2 3.2~4.8 4.8~6.4 | 490 | 735 |
3.0 | 3.1 | 6.3 8.0 9.8 | 1.83 | 6.0 | 0.9 | 1.0 | 1.0~3.2 3.2~4.8 4.8~6.4 | 1.6~3.2 3.2~4.8 4.8~6.4 | 735 | 1180 | |
3.2 | 3.3 | 6.3 8.0 9.8 | 1.83 | 6.4 | 0.9 | 1.1 | 1.6~3.2 3.2~4.8 4.8~6.4 | 1.6~3.2 3.2~4.8 4.8~6.4 | 930 | 1420 | |
4.0 | 4.1 | 6.9 8.6 10.4 | 2.28 | 8.0 | 1.2 | 1.4 | 1.2~3.2 3.2~4.8 4.8~6.4 | 1.6~3.2 3.2~4.8 4.8~6.4 | 1470 | 2210 | |
アルミ製プルリベット | 4.8 | 4.9 | 7.5 9.3 11.1 | 2.64 | 9.6 | 1.4 | 1.6 | 1.6~3.2 3.2~4.8 4.8~6.4 | 2.3~3.2 3.2~4.8 4.8~6.4 | 2260 | 3240 |
スチール製プルリベット | 3.2 | 3.3 | 6.4 9.5 | 1.93 | 9.5 | 1.0 | 1.0~3.2 3.2~6.4 | 1270 | 1770 | ||
4.0 | 4.1 | 10.2 | 2.41 | 11.9 | 1.25 | 3.2~6.4 | 2060 | 2940 | |||
4.8 | 4.9 | 10.8 | 2.90 | 15.9 | 1.9 | 3.2~6.4 | 2750 | 3920 |
注: 部品のリベット用貫通穴の直径は、通常リベットの呼び径Dより0.2~0.3mm大きい。リベット穴の中心から端までの距離は、最良のリベット接合強度のためには、リベット穴の大きさの2倍以上であるべきである。距離が小さすぎると、強度が大幅に低下する。
4. リベット形状の図:
注:
(1) 平頭プル・リベットは主に、突出したファスナーを接続することが許されない厳しい条件の表面に使用される。プル・リベットの平らな頭部は、頭部が表面から突出しないようにファスナーの皿穴に埋め込まれる。
(2)プル・リベットの色は、顧客の要求を満たすために、黒化処理又は他の処理によって組立工作物と一致させることができる。例えば、プル・リベットの頭部は、塗装されたワークピースへのリベッティングを可能にするために塗装することができる。
5.最も一般的に使用されるプルリベットについては、3B010-01
これは前述のオープン・エンド・フラット・ヘッド・プル・リベットである。リベットの外径Dは0.125インチで、3.175mmです。対応する皿穴はΦ6.5XΦ3.5X120°で、それと一致する貫通穴はΦ3.4です。