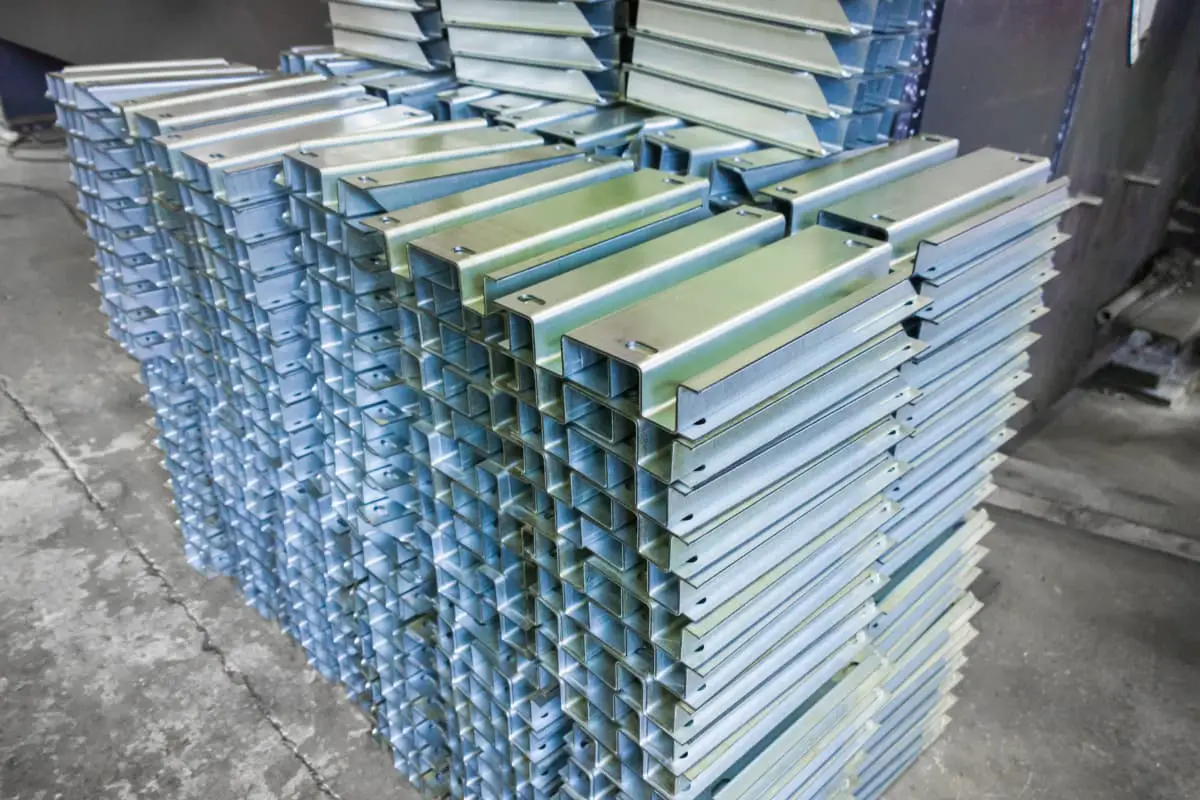
身近な機器の複雑な部品がどのように作られているのか、不思議に思ったことはないだろうか。この記事では、板金製品の製造工程を解明し、最初の図面設計から最終梱包、納品までの道のりを詳しく説明します。レーザー加工、CNCスタンピング、曲げ加工、溶接、コーティングなど、生の金属板を精密で機能的な部品へと変化させる重要な工程を理解することができます。この重要な製造工程について理解を深めてください!
当社の一般的な板金加工は6つの主な工程から成り、以下にその詳細を説明する:
1.図面デザイン
一般顧客は図面またはサンプルを提供し、それを同社のエンジニアリング・チームが分析・設計する。このプロセスにより、加工内訳図と組立図の両方が作成される。これらは、製造部門に提出され、加工される。
2. レーザー加工
について レーザー切断 本機は、炭素鋼、ステンレス鋼、その他さまざまな材料の切断が可能です。その結果、エッジの美しい、滑らかで整然とした正確な切断が可能になります。この方法は、特に曲面形状のワークに有利で、従来のCNCプレス加工に比べ、なくてはならない加工技術です。
3. CNC 足踏み
について CNCタレット パンチは主に、通常2.5mm以下の薄い材料厚の製品に使用される。この方法は次のような場合に適している。 板金 複数の穴が必要な部品や、加工に特殊な金型を使用する必要がある部品。部品の数量が多い場合、CNCプレス加工は他の方法よりもコスト面で有利です。
4.曲げ
ワークの大半が切断後に曲げ加工を必要とする場合、 プレスブレーキ 曲げ加工を完成させるために必要です。CNCプレスブレーキが好まれるのは、より速いだけでなく、より正確だからです。
5. 溶接 成形
一般的に ブランキング処理このような場合、ワークピースを組み立てて成形する必要がある。組立方法には様々なものがあり、中にはネジやリベットなどの非溶接工程を用いるものもある。ほとんどのメカニカル・シェル・シート・メタルでは、溶接成形が使用され、同社は通常、以下の方法を採用している。 アルゴンアーク溶接タッチ溶接、炭酸ガス溶接がある。溶接後、ワークピースを研磨して強度を確保し、外観を向上させる。
6.静電粉体塗装
静電粉体塗装の主な対象は炭素鋼部品です。このプロセスには、油分や錆の除去、表面洗浄、リン酸塩処理、静電粉体塗装、高温ベーキングなど、いくつかの工程が含まれます。その結果、数年間錆のない美しい表面が保たれ、費用対効果も高くなります。
対照的に、液体塗装は異なるプロセスで、一般的に大きなワークピースに使用され、輸送のオプションがない場合、より便利で費用対効果が高い。液体塗装は通常、プライマーの塗布と塗料の塗布の2段階に分けられます。
7.梱包と配送
梱包前に100%検査を実施し、検査データを提供する。納品条件や梱包方法については、現地でお客様担当者に確認していただき、お客様確認のための記録を作成します。
(1) ノンモールド加工
の技術 板金加工パンチング、レーザー切断、シャーリング、折り畳み、リベッティングなどの機械が含まれ、一般的にサンプルや小ロットの生産に使用され、コストが高くなる。
(2) 金型加工
固定金型の使用 板金加工 ブランキング金型と成形金型があり、主に大量生産で安価に利用される。
1.ブランキング
シートメタルのブランキングは、パンチングやレーザー切断など、いくつかの方法で行うことができる、 剪断機ダイ・ブランキングなど。現在、CNC打ち抜き加工が最も一般的に使用されている。レーザー切断は加工コストが高いため、主に試作段階で利用され、型抜きは大量生産によく使われる。
ここでは、CNCパンチを使用したシートメタルのブランキングに焦点を当てる。CNCパンチはタレットパンチとも呼ばれ、ブランキング、パンチング、穴あけ、バープレスなど様々な加工が可能です。その加工精度は+/-0.1mmに達する。
次の表は、CNCパンチングで加工できる板金の厚さを示しています:
(1)パンチングは小さなサイズを必要とする。
パンチングに必要な小さなサイズは、穴の形状、材料の機械的特性、材料の厚さなどの要因によって決まる(下図参照)。
材料 | ホールド径 b | 長方形の穴 短辺幅 b |
---|---|---|
高炭素鋼 | 1.3t | 1.0t |
低炭素鋼、真鍮 | 1.0t | 0.7t |
アルミニウム | 0.8t | 0.5t |
(2) 穴と穴の間の距離と穴の端と端の間の距離。
パンチングエッジと部品の形状との間のわずかな距離は、部品の形状と穴の両方によって制限されます。パンチングエッジが部品の輪郭エッジと平行でない場合、最小距離は材料の厚さT未満であってはなりません。平行である場合、最小距離は1.5T未満であってはなりません(下図に示すように)。
(3)ドローイングの穴のガイドライン。
絞り穴をあける場合、絞り穴とエッジ間の最短距離は3Tとする。2つの絞り穴間の最短距離は6Tとし、絞り穴と内側の曲げエッジ間の安全な最短距離は3T+Rとする(ここで、Tは板金厚、Rは 曲げ半径).
(4)絞り曲げおよび深絞り部品の間隔要件。
曲げ加工や深絞り加工を行う場合、穴の壁と直線の壁との間に一定の距離を保つ必要がある(下図参照)。
2.成形
板金成形には主に以下のものが含まれる。 板金曲げ そしてストレッチ。
(1) 板金曲げ
曲げ順のガイドライン:
曲げ加工の順序は、内側から外側へ曲げる、小さいものから大きいものへ曲げる、特殊な形状を先に曲げ、次に一般的な形状を曲げる、前の工程が後の工程を妨げないようにする、といった原則に従うべきである。
曲げ部品の小さな曲げ半径:
材料が曲げられると、フィレットの外側の層は伸びを経験し、内側の層は圧縮を経験する。内側の曲げ半径(R)が小さくなるにつれて、引張応力と圧縮応力が増加します。外側のフィレットの引張応力が材料の極限強度を超えると、亀裂や破壊が発生する可能性があります。したがって、曲げ部品の設計では、曲げ半径を過度に小さくすることは避けるべきである。
同社が使用する一般的な材料の最小曲げ半径を下表に示す:
曲げ部品の最小曲げ半径の表:
この曲げ半径は、その内半径を意味する。 曲げ部分tは材料の肉厚である。
(2) シートメタル・ストレッチ
板金延伸は、主に複数のパンチまたは単一のパンチを使用することによって達成され、様々な延伸パンチまたはダイを必要とする。延伸部品の形状はできるだけ単純で対称的であるべきであり、1回の作業で可能な限り延伸する必要がある。複数回の延伸加工が必要な場合は、表面に延伸加工の跡が残っても構わない。延伸側壁は、組立要件を満たす限り、ある程度の傾きを持たせることができる。
(3) その他 成形方法:
補強リブ - シートメタル部品に補強リブを付けることで、構造的な剛性を高める。
補強リブの構造とサイズの選択:
ルーバー - ルーバーは、さまざまな筐体やケーシングの換気や放熱のために一般的に使用されます。
③ ホールフランジング (ストレッチホール) - ストレッチホールとしても知られるホールフランジングは、ねじ山を作ったり、開口部の剛性を高めるために使用される。
3.溶接
をデザインする。 板金溶接 構造物では、溶接部や接合部は左右対称に配置 し、収束、凝集、重なりの発生を避けるべきである。二次溶接部や接合部は中断してもよいが、主 溶接部や接合部は接続すべきである。
板金加工で使用される一般的な溶接方法には、電気アーク溶接と 抵抗溶接.
(1) アーク溶接
溶接のために板金間に十分なスペースを設け、溶接ギャップは0.5~0.8mmとし、溶接部は均一でなければならない。
(2) 抵抗溶接
溶接面は、しわやスプリングバックのない滑らかなものでなければならない。以下は抵抗の寸法である。 スポット溶接.
厚さ t(mm) | はんだ接合部直径 d (mm) | 最短距離 はんだ接合部から端までの長さ (mm) | 最小幅 溶接端 (mm) |
---|---|---|---|
0.6-0.79 | 5.0-6.0 | 5 | 10 |
0.8-1.39 | 5.5-6.5 | 5-6 | 10-12 |
1.4-1.99 | 6.0-7.0 | 7-9 | 14-18 |
2.0-2.49 | 6.5-7.5 | 9-10 | 18-20 |
4. 板金接続方法
ここでは主に、加工段階における板金同士の接合方法として、リベット接合、溶接(既述)、穴あけリベット接合、トックスリベット接合について紹介する。
(1) リベッティング
リベッティングは、プル・リベットとして知られる一種のリベットを用いて2枚の板を接合する方法である。一般的なリベットの形状を下図に示す:
(2) プルアウト・リベット:
一方は抜き穴で、もう一方はザグリ穴である。
利点穴自体が位置決め機能を提供する。リベッティング強度が高く、ダイを通してのリベッティング効率も高い。
(3) トックス・リベット:
接続された部品は、単純なパンチを通してダイに押し込まれる。さらに圧力をかけると、ダイの中の材料が外側に流れ出し、丸い接続点ができます。 鋭角 やバリが除去され、耐食性が維持されます。鋼板表面のコーティングや溶射皮膜も一緒に変形・流動し、本来の防錆・防食性を保持します。
下図に示すように、材料は両側へ押し出され、ダイ側近くのパネルに入り込み、Tox接続ドットを形成する:
5.表面処理
シートメタルの表面処理は、防錆と装飾の両方の目的を果たす。一般的な表面処理には、粉末溶射、電気亜鉛メッキ、溶融亜鉛メッキ、表面酸化、表面絞り、シルクスクリーン印刷などがある。表面処理を行う前に、板金表面の油汚れ、錆、溶接スラグを除去することが重要である。
(1) 粉体塗装:シートメタルの表面塗装には、液体塗装と粉体塗装の2つの選択肢がある。後者の方が一般的である。粉体塗装は、シートメタルの表面に様々な色の塗料を静電吸着させ、高温で焼き付けることで、外観と防錆性能を向上させます。
(2) 電気亜鉛メッキと溶融亜鉛メッキ:シートメタルの表面に亜鉛めっきを施すことは、一般的な防錆処理方法であり、外観も良くなる。電気亜鉛めっきと溶融亜鉛めっきの2つの形態がある。電気亜鉛メッキは薄い亜鉛コーティングで明るく平らな外観を作り出しますが、溶融亜鉛メッキは亜鉛-鉄合金層を形成する厚い亜鉛コーティングとなり、電気亜鉛メッキよりも強い耐食性を提供します。
(3) 表面酸化:このセクションでは、アルミニウムの表面陽極酸化と アルミニウム合金.表面アルマイト処理は、様々な色を作り出し、保護と装飾の両方の効果を提供することができます。また、陽極酸化皮膜を表面に形成することで、高硬度、耐摩耗性、電気的絶縁性、熱絶縁性に優れています。
(4) 表面伸線:素材は伸線機の上下のローラーの間に置かれ、ローラーには研磨ベルトが取り付けられている。その後、素材は研磨ベルトを通過し、表面に痕跡ができる。痕跡の厚さは使用する研磨ベルトの種類によって異なり、この処理の主な目的は材料の外観を向上させることである。この表面処理方法は、通常アルミニウムにのみ適用される。
(5) シルクスクリーン印刷:素材へのスクリーン印刷は、フラットスクリーン印刷とパッド印刷に分けられる。フラットスクリーン印刷は平らな面に使用され、パッド印刷は深い穴のある面に使用される。シルクスクリーン印刷にはシルクインプレッションが必要である。