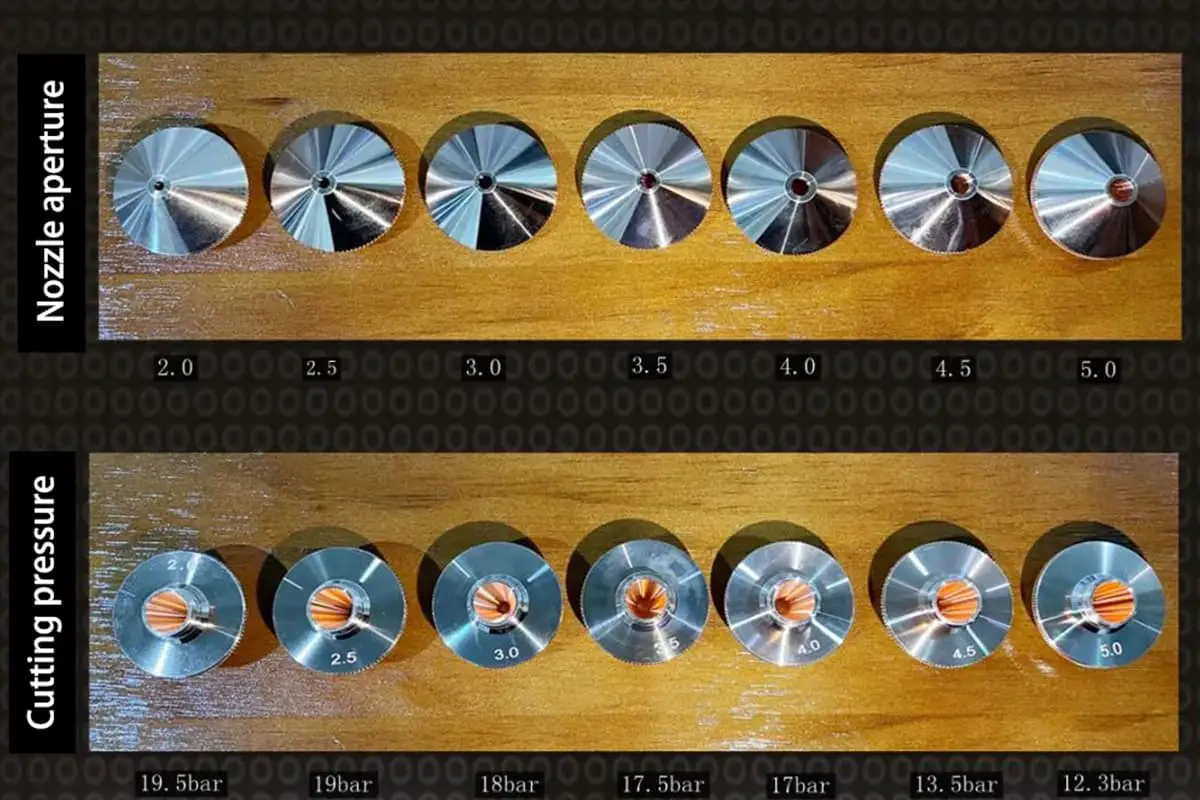
バターを切り裂くように楽に金属を切断することを想像してみてください。これがレーザー穿孔の威力です。この記事では、パルス穿孔とブラスト穿孔の2つの主なタイプについて説明します。その原理と用途を理解することで、これらの技術を活用し、プロジェクトの精度と効率を高めることができます。これらの方法が金属加工工程をどのように変えることができるかを知る準備はできましたか?続きをお読みください。
レーザー切断では、レーザービームを使って切断する材料を加熱、溶融、気化させる。溶けた材料は高圧ガスで吹き飛ばされ、穴が開けられ、ビームは材料に沿って移動し続け、連続的な切断シームが形成される。
ほとんどの熱切断技術では、板の端から切断を開始できる一部のケースを除き、切断を開始する前に板に小さな穴を開ける必要がある。そして、この小さな穴から切断を進める。
レーザー穿孔の基本原理は、一定のエネルギーを持つレーザービームを金属板の表面に照射すると、その一部が反射し、残りのエネルギーが金属に吸収されるというものである。これにより金属が溶け、溶融池が形成される。
金属表面からの溶融金属の吸収率が高まり、より多くのエネルギーを吸収し、溶融プロセスを加速することができる。
エネルギーと空気圧を適切に制御することで、溶融金属を溶融池から取り出し、金属が貫通するまで連続的に深くすることができる。
実際の用途では、穿孔は通常、パルス穿孔とブラスト穿孔の2つの方法に分けられる。
パルス穿孔の原理は、ピークパワーが高く、デューティサイクルの低いパルスレーザーを使用して、切断する板に照射し、少量の材料を溶融または気化させ、連続ビートと補助ガスの共同作用によって穴から排出し、板を段階的に貫通させることである。
レーザーの照射時間が断続的で、平均使用エネルギーが比較的小さいため、加工材料が吸収する熱量が少ない。その結果、ミシン目周辺の余熱や残渣が少なく、貫通穴も小さく規則的で、初期切断への影響が少ない。
レーザービームが被加工物に照射されると、まず被加工物の表面が加熱される(Aの図)。徐々に加熱が深まると、穿孔が発生する(Bの図)。CD) 貫通するまで(Eに示すように)。
穿孔プロセス全体は、貫通が達成されるまで、段階的に徐々に達成される。したがって、この方法の穿孔時間は比較的長い。しかし、得られる穴は小さく、周囲への熱影響も少ない。
ブラスト穿孔の原理は、あるエネルギーの連続波レーザー光線を対象物に照射することで、対象物が相当量のエネルギーを吸収して溶融し、ピットが形成される。その後、補助ガスの助けを借りて溶融物を除去し、穴を形成することで、迅速な貫通という目的を達成します。
しかし、連続的にレーザーを照射するため、ブラスト穿孔の穴径は比較的大きく、飛散も激しい。そのため、高い精度が要求される切断用途には不向きである。
焦点位置を材料表面より高く設定し、素早く加熱するために穿孔の開口部を大きくする。
この穿孔方法では、被加工材の表面に噴霧される溶融金属がかなりの量になるが、穿孔時間を大幅に短縮することができる。
2つの穿孔方法の実際の効果を下図に示す。
ほとんどの場合、パルス穿孔の品質はブラスト穿孔よりも優れている。