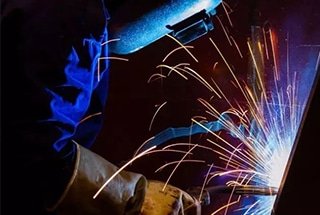
亜鉛メッキ鋼管を溶接する際の課題について考えたことはありますか?亜鉛メッキ鋼管を保護する亜鉛メッキは、溶接中に亀裂、気孔、スラグの混入などの問題を引き起こすこともあります。この記事では、このような課題に対処し、強靭で信頼性の高い溶接を実現するための、さまざまな溶接技術や溶接材料についてご紹介します。正しい方法と注意事項を理解することで、溶接亜鉛メッキ・パイプの品質と耐久性を向上させ、多くの産業用途に適したものにすることができます。亜鉛メッキ層の完全性を維持しながら、高品質の溶接を実現する方法をご覧ください。
亜鉛メッキ鋼板は、空気中で形成される酸化亜鉛の保護層が鋼鉄内部の構造を保持するため、様々な産業で広く使用されています。
亜鉛めっき層は耐食性に優れているが、 溶接中に亀裂、気孔、スラグの混入につながり、 溶接品質が劣ることが多い。
通常、低炭素鋼の上に厚さ約20μmの亜鉛層を塗布する。亜鉛の融点は419℃で、沸点は908℃前後である。溶接中、亜鉛は溶融して液体になり、溶接プールの表面に浮遊するか、溶接部の根元に沈殿する。 溶接継ぎ目.
亜鉛は鉄への溶解性が高いため、粒界に沿って 溶接金属に浸透し、「液体金属脆化」を引き起こす ことがある。同時に、亜鉛と鉄はFe3Zn10やFeZn10のよう な金属間脆性化合物を形成し、溶接金属の塑性 性を低下させ、引張応力下での割れにつながる。
溶接 隅肉溶接特にT字型ジョイントは割れやすい。
亜鉛メッキ鋼の溶接中、アーク熱の作用で溶接部の開先とエッジの亜鉛層が酸化、溶融、蒸発、揮発し、白煙と蒸気を放出する。
酸化により形成されるZnOの融点は約1800℃以上と高いため、以下のような場合、ZnOスラグの介在物につながる可能性がある。 溶接パラメータ は小さすぎる。
また、脱酸剤としての亜鉛の役割により、 FeO-MnOまたはFeO-MnO-SiO2のような 低融点酸化物スラグ化合物の生成も起こり得る。不適切な溶接規格と技術により、溶融領域が拡大し、亜鉛めっき層が損傷する可能性がある。
これは、長時間のアークや大きなスイングの作業中に特に起こりやすい。亜鉛が蒸発すると大量の白煙が発生し、人体に刺激や害を及ぼす可能性がある。
したがって 溶接方法 煙の発生が少ない素材を選ぶことが重要である。
亜鉛メッキ鋼板の溶接には、ガス溶接、手溶接、金属溶接など、さまざまな方法が使用される。 アーク溶接CO2ガスシールド溶接、サブマージアーク自動溶接、タングステンイナートガス溶接。
ガス溶接かつて亜鉛メッキ・パイプの溶接に一般的に使用 されていたガス溶接は、溶接部の欠陥や機械的性能 の低下につながる非集中入熱のため、現在ではほとんど 使用されていない。ガス溶接は、亜鉛メッキ層に大きな損傷を与える。
CO2ガスシールドウェルディングは次のような溶接に適している。 亜鉛メッキ鋼溶接.適切な溶接仕様と、保護ガスおよび溶接材料のマッチングにより、高品質の溶接継手を得ることができる。
しかし、この方法が工学的な実践で使われることはめったにない。
タングステン不活性ガス溶接は、アーク・エネル ギーが集中するため、亜鉛メッキ層への損傷が少 なく、良好な片面溶接両面形成継手を容易に 形成できる。
しかし、スピードが遅く、コストが高いため、魅力的な選択肢とは言えない。
マニュアル メタルアーク 溶接は、配管工事で最も一般的に使用される方法である。J421、J422、J423などの電極を正しく選択することで、溶接が可能になります、 チタン 酸化物タイプとチタンカルシウムタイプの電極を使用。
これらの電極は溶融速度が速いため、溶融速度が増 加する。スイングなしで操作した場合、溶接プールの端の亜鉛めっき層のみが損傷し、一般に溶融領域が拡大しないため、溶接金属への液体亜鉛の浸透が減少する。
正しい操作方法と 溶接材料その結果、欠陥のない良好な機械的性能が得られる。
タングステン・イナート・ガス溶接に比べ低コストで高速であるため、熟練した溶接工がいる場合は手動金属アーク溶接が採用される。
亜鉛メッキ鋼の溶接前準備は、一般的な低炭素鋼の場合と同じである。開先サイズと近くの亜鉛メッキ層には細心の注意を払う必要がある。
確実にするために 完全浸透開先寸法は適切であるべきで、一般に60~65°、一定の隙間、通常は1.5~2.5mmである。溶接部への亜鉛の浸透を抑えるため、溶接前に開先内部の亜鉛めっき層を洗浄することができる。
実作業では、集中制御のために鈍いエッジを残さない集中開先加工を採用し、2層の 溶接工程 は、不完全融合の可能性を減らすために使用される。
電極は亜鉛メッキ管の母材に応じて選択する。一般的な低炭素鋼の場合、作業性の良さからJ422がよく選ばれている。
溶接技術:
多層溶接の第1層を溶接する際には、亜鉛層を溶 かして気化させ、溶接部から蒸発させるようにす ると、溶接部に残る液体亜鉛の量を大幅に減らすこ とができる。
隅肉溶接を行う場合は、亜鉛層を溶かし、気化させ て第1層の溶接部から蒸発させるようにする。これは、まず電極の先端を5~7mmほど前進させ、亜鉛層を溶かした後、元の位置に戻って溶接を続けることで行う。
溶接後、速やかに溶接継ぎ目を清掃し、ジンク・リッチ・プライマーを塗布し、防錆対策を施す必要がある。
管理は、人員、材料、機械、方法、環境の5つの側面から実施される。
人的要因が溶接管理の焦点である:
したがって、溶接の前には、技術的に熟練し、溶接証明書を所持している溶接工が選ばれ、必要な技術訓練とブリーフィングを受けるべきである。パイプラインの溶接要員の安定性を確保するため、無作為の交代は許されない。
溶接材料の管理
購入材料が正規ルートからのもので、品質保証、適合証明書があり、工程要件を満たしていることを確認する。 溶接棒 溶接材料は工程に従って厳密に焼かなければならず、一度に発行される量は半日分を超えてはならない。
溶接機
溶接機は信頼性が高く、プロセス要件を満たしていなけれ ばならない。溶接機には、溶接プロセスが正しく実施され るよう、校正された電流計と電圧計がなければならない。溶接ケーブルは長すぎてはならず、長い場合は溶接パラメーターを調整する必要がある。
溶接プロセスの方法
亜鉛メッキ鋼管用の特別な作業方法の厳格な実施、 溶接前の溶接工程の開先検査、溶接工程のパラメーター と作業技術の管理、溶接後の外観品質検査、必要に応じて 溶接後の追加非破壊検査を確実に実施する。各接合部の溶接レベルと溶接材料の量を管理する。
溶接環境制御
溶接中の温度、湿度、風速が工程要件に適合し ていることを確認する。
建築における溶融亜鉛メッキパイプの溶接は、正しい溶接工程を採用し、仕様書に従って厳格に検査・検収し、溶接後は速やかに溶接部に防錆処理(リッチ亜鉛塗装)を行う。
オープンおよびクローズドシステムの空調建設プロセスにおいて、一定の実現可能性を持っており、建設速度を向上させ、パイプ接続の堅固性を向上させることができる。
従って、許容される建設条件下で、関連する保護・防錆措置を実施することを前提に、溶融亜鉛メッキ・パイプを溶接接合することができる。