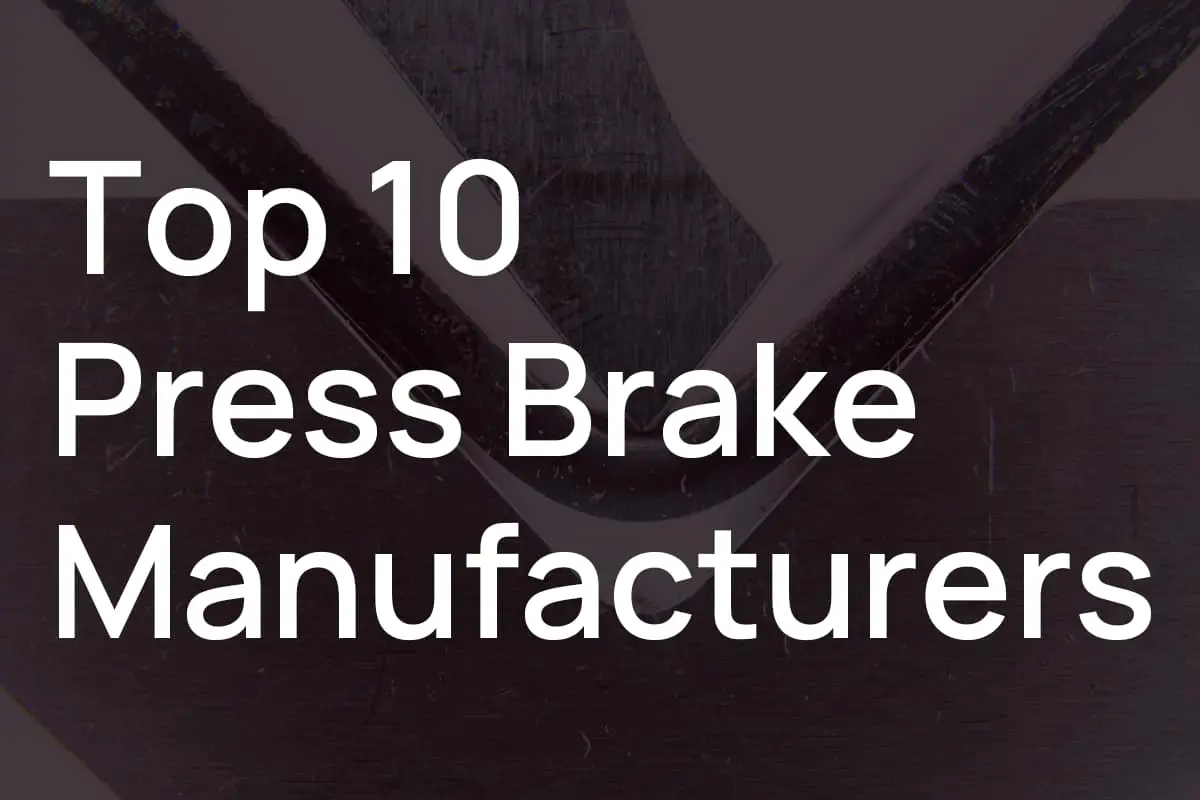
얇은 금속판을 어떻게 하면 튼튼하고 매끄러운 모서리를 가진 부품으로 만들 수 있을까요? 해답은 헤밍 벤딩이라는 매력적인 공정에 있습니다. 이 기사에서는 평평한 바닥 다이부터 유압식 헤밍 테이블까지, 각각 다른 재료와 용도에 적합한 네 가지 효과적인 기술을 살펴봅니다. 독자들은 이러한 방법을 통해 금속 제품의 강도와 안전성을 향상시킬 뿐만 아니라 미적 매력도 향상시키는 방법을 배울 수 있습니다. 귀사의 제조 요구 사항에 가장 적합한 헤밍 벤딩 솔루션을 찾아보세요.
헤밍(평평하게 만들기) 벤딩은 그림 1과 같이 일반적으로 공작물의 가장자리를 평행한 가장자리 또는 둥근 가장자리로 구부리는 빈번한 벤딩 작업 방법입니다.
그림 1 헤밍 및 벤딩의 개략도
헤밍 및 벤딩의 목적은 다음을 제거하는 것입니다. 날카로운 모서리를 사용하여 공작물의 강도를 높이고 외관을 개선할 수 있습니다.
굽힘을 평평하게 만드는 과정에는 일반적으로 두 단계가 포함됩니다:
(1) 공작물을 30°로 미리 구부린 다음 그림 2와 같이 공작물을 평평하게 펴서 구부립니다.
그림 2 헤밍 및 벤딩 단계
올바른 평탄화 절곡 솔루션을 선택하려면 먼저 공작물의 재질과 두께, 평탄화 절곡 빈도를 고려해야 합니다.
(2) 헤밍 다이를 헤밍이 필요하지 않은 일반 굽힘에도 사용할 수 있다는 점에 유의하세요.
밑단에는 두 가지 유형이 있습니다:
오른쪽의 차트는 위에서 설명한 두 가지 헤밍 유형을 생성하는 데 필요한 힘을 보여줍니다.
판금 제작의 다양한 굽힘 조건과 재료 요구 사항을 수용하도록 설계된 네 가지 기본 헤밍 벤딩 솔루션이 있습니다:
(1) 평평한 바닥 밑단 다이: 이 전통적인 솔루션은 직선 밑단을 만들기 위한 간단하고 비용 효율적인 접근 방식을 제공합니다. 더 얇은 게이지 소재와 대량 생산이 필요한 애플리케이션에 이상적입니다. 평평한 표면은 밑단 전체에 일관된 압력 분포를 보장합니다.
(2) U자형 헤밍 다이: 향상된 안정성과 정밀도를 위해 설계된 이 다이는 헤밍 공정 중에 공작물을 받쳐주는 U자형 채널이 특징입니다. 두꺼운 소재나 더 엄격한 공차가 필요한 부품에 특히 효과적입니다. U자형 채널은 소재의 스프링백을 방지하고 보다 균일한 밑단 마감 처리를 보장합니다.
(3) 스프링형 헤밍 다이: 이 고급 솔루션은 스프링이 장착된 구성 요소를 통합하여 헤밍 작업 중에 적응형 압력을 제공합니다. 스프링이 이러한 차이를 보정하기 때문에 두께가 다양하거나 약간의 불규칙성이 있는 소재에 적합합니다. 이 다이 유형은 복잡한 형상에서 일관된 헴 품질이 중요한 자동차 패널 생산에 자주 사용됩니다.
(4) 유압식 헤밍 테이블: 최고 수준의 제어력과 다용도성을 제공하는 유압식 헤밍 테이블은 유체 압력을 사용하여 정밀하고 조절 가능한 헤밍 힘을 생성합니다. 이 솔루션은 대형 패널, 복잡한 모양 또는 잦은 조정이 필요한 애플리케이션에 이상적입니다. 유압 시스템을 통해 압력과 속도를 미세 조정할 수 있으므로 작업자는 다양한 재료와 형상에 맞게 헤밍 프로세스를 최적화할 수 있습니다.
이러한 헤밍 솔루션은 각각 고유한 장점을 제공하며 재료 특성, 부품 형상, 생산량 및 품질 요구 사항과 같은 요소에 따라 선택이 달라집니다. 현대의 제조업에서는 다양한 제품 라인에서 최적의 결과를 얻기 위해 이러한 기술을 조합하여 사용하는 경우가 많습니다.
관련: V자 및 U자 굽힘력 계산기
그림 3 네 가지 헤밍 및 벤딩 솔루션
평평한 바닥 헤밍 다이는 그림 4에 표시된 것처럼 두 세트의 다이, 즉 상하 표준 다이와 상하 평평한 바닥 다이를 함께 사용하여 헤밍 및 굽힘을 수행합니다.
그림 4 평평한 바닥 헤밍 다이의 개략도
이 공정은 표준 다이를 사용하여 공작물을 30°로 미리 구부리는 것으로 시작됩니다.
다음으로 공작물을 평평한 바닥 다이에서 평평하게 구부립니다.
평평한 바닥 헤밍 다이에는 두 단계가 필요하기 때문에 벤딩 프로세스주로 헤밍과 굽힘이 빈번하지 않고 비용 효율성이 높은 작업 조건에 적합합니다.
그러나 헤밍 중에 약간의 횡력이 발생하고 평평한 카본의 최대 두께는 다음과 같습니다. 강판 는 2mm로 제한됩니다.
납작하게 구부릴 때 제한된 두께를 해결하기 위해 볼 타입의 이동식 플랫 바닥을 사용했습니다. 낮은 주사위 가 혁신적으로 도입되었습니다. 그림 5에서 볼 수 있듯이 평평한 탄소강판 또는 스테인리스 강판의 최대 두께는 이제 4mm에 달할 수 있습니다.
그림 5 볼 타입 이동식 하부 다이의 개략도
그림 6에 표시된 것처럼 U자형 헤밍 다이 세트를 사용하여 사전 굽힘 및 평탄화에 사용할 수 있습니다.
그림 6 U자형 헤밍 다이의 개략도
U자형 헤밍 다이의 장점은 다용도로 사용할 수 있다는 것입니다. 헤밍 및 벤딩에 필요하지 않은 경우 표준 헤밍 다이에 활용할 수 있습니다. 에어 벤딩높은 활용도와 비용 효율성을 제공합니다.
납작한 탄소강판의 최대 두께는 1.5mm이고 납작한 스테인리스 강판의 최대 두께는 1mm입니다. 평평하게 만들 수 있는 최소 플랜지 크기는 약 14mm입니다.
스프링 헤밍 다이는 28° 표준 상부 다이와 30° 헤밍 하부 다이로 구성됩니다. 하단 다이의 헤밍 인서트는 다음에 의해 지원됩니다. 봄.
헤밍 공정 중에 미리 구부러진 공작물은 헤밍 인서트와 헤밍 하부 다이의 가이드 인서트 사이에 배치됩니다. 헤밍 인서트는 상부 다이의 하강을 따라가며 미리 구부러진 공작물이 평평해질 때까지 아래로 누릅니다.
스프링 헤밍 다이가 탄소강판에서 평평하게 만들 수 있는 최대 두께는 2mm입니다.
다른 헤밍 솔루션과 마찬가지로 스프링 헤밍 다이는 표준 헤밍 다이에도 사용할 수 있습니다. 에어 벤딩 헤밍 굽힘에 사용하지 않는 경우.
그림 7 스프링 헤밍 다이의 개략도
유압식 헤밍 테이블(그림 8 참조)은 스프링 헤밍 다이와 유사하게 작동하지만 스프링 대신 유압 실린더를 사용하여 헤밍 인서트의 리프트를 제어합니다.
그림 8 유압 헤밍 작업대의 개략도
오일 압력은 100bar로 더 두껍고 무거운 공작물을 구부릴 수 있습니다. 유압 헤밍 테이블의 사용 수명을 더욱 늘리기 위해 경화 헤밍 인서트를 추가할 수 있습니다.
표준 하부 다이를 유압 헤밍 작업대에 배치할 수 있으며 필요에 따라 최대 40mm까지 V 개구부를 선택할 수 있습니다. 하부 다이를 수동 또는 자동으로 고정하여 보다 효율적으로 다이를 교체할 수 있습니다.
유압 헤밍 테이블은 최대 3mm 두께의 탄소강판을 평평하게 만들 수 있습니다. 스프링 헤밍 다이 또는 유압 헤밍 테이블은 고정 장치 또는 기계식 보정 테이블에 고정할 수 있습니다.
유압 헤밍 테이블은 벤딩 머신의 하부 빔에 직접 설치할 수도 있어 개방 높이와 유연성을 높일 수 있습니다.
결론적으로, 네 가지 헤밍 및 벤딩 솔루션은 각각 고유한 장점이 있습니다. 헤밍 및 벤딩 적용 시나리오에 따라 적절한 솔루션을 선택할 수 있습니다.