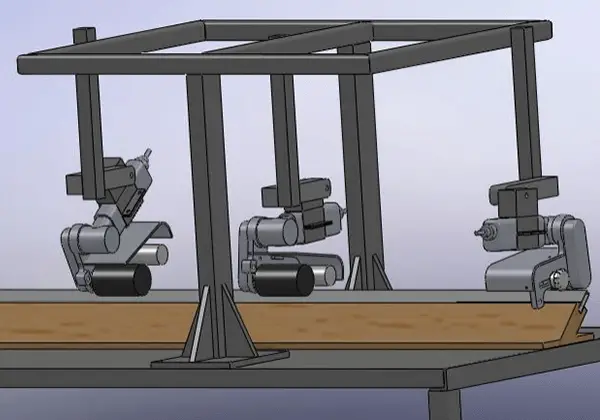
완벽한 금속 마감 처리를 위한 방법이 궁금한 적이 있나요? 이 글에서는 기계식부터 초음파 방식까지 다양한 폴리싱 기법에 대해 자세히 알아보고 그 적용 분야와 이점에 대해 설명합니다. 각 기법의 작동 방식과 프로젝트에 적합한 기법을 선택하여 최적의 표면 품질과 효율성을 보장하는 방법을 배울 수 있습니다. 거울과 같은 광택을 구현하는 비결과 이를 가능하게 하는 과학에 대해 알아보세요.
현재 일반적으로 사용되는 폴리싱 방법은 다음과 같습니다:
기계적 연마는 연마 후 돌출부를 제거하여 매끄러운 표면을 얻기 위해 재료 표면의 절단 및 소성 변형에 의존합니다. 일반적으로 오일스톤, 양모 휠, 사포 등을 사용하며 주로 수작업으로 이루어집니다.
회전하는 본체 표면과 같은 특수 부품은 턴테이블 및 기타 보조 도구를 사용할 수 있습니다. 높은 표면 품질 요구 사항의 경우 초정밀 연삭 및 연마 방법을 채택할 수 있습니다.
초정밀 연삭 및 연마에는 특수 제작된 연삭 공구를 사용합니다. 연마제가 포함된 연삭 및 연마 유체에서 고속 회전 운동을 위해 공작물 표면을 단단히 누릅니다. 이 기술은 다음을 달성할 수 있습니다. 표면 거칠기 Ra0.008μm로 모든 연마 방법 중 가장 높습니다. 광학 렌즈 몰드는 종종 이 방법을 사용합니다.
화학 연마는 표면의 미세한 돌출부를 화학 매체에 우선적으로 용해시켜 매끄러운 표면을 얻을 수 있습니다. 이 방법의 가장 큰 장점은 복잡한 장비가 필요하지 않고 복잡한 모양의 공작물을 연마할 수 있으며 동시에 많은 공작물을 연마할 수 있어 효율성이 높다는 점입니다.
화학적 연마의 핵심 문제는 연마액의 준비입니다. 화학적 연마로 얻은 표면 거칠기는 일반적으로 수 10μm입니다.
의 기본 원칙 전해 연마 은 재료 표면의 작은 돌출부를 선택적으로 용해하여 표면을 매끄럽게 만드는 화학적 연마와 동일합니다. 화학적 연마와 비교하여 음극 반응의 영향을 제거할 수 있고 더 나은 결과를 얻을 수 있습니다.
전기 화학 폴리싱 프로세스 는 두 단계로 나뉩니다:
(1) 매크로 레벨링: 용해 생성물이 전해질로 확산되고 재료 표면의 기하학적 거칠기가 Ra>1μm로 감소합니다.
(2) 마이크로 레벨링: 양극 편광은 Ra <1μm로 표면 밝기를 증가시킵니다.
초음파 연마에서는 연마재 현탁액에 공작물을 넣고 초음파 필드에 넣습니다. 초음파의 진동 작용으로 연마재가 공작물 표면을 연마하고 연마합니다.
초음파 가공 은 낮은 매크로 힘을 가하기 때문에 공작물의 변형을 일으키지 않습니다. 그러나 툴링의 제작과 설치는 어려울 수 있습니다. 초음파 가공은 화학적 또는 전기 화학적 방법과 결합할 수 있습니다.
용액 부식 및 전기 분해를 기반으로 초음파 진동을 적용하여 용액을 교반하여 공작물 표면의 용해 생성물이 분리되어 표면 근처의 균일한 부식 또는 전해질을 유지할 수 있도록 합니다. 액체에서 초음파의 캐비테이션 효과는 또한 부식 과정을 억제하여 표면을 밝게 하는 데 도움이 됩니다.
유체 연마는 액체의 고속 흐름과 운반된 연마 입자를 사용하여 공작물 표면을 연마합니다. 일반적인 방법으로는 연마제 분사 가공, 액체 분사 가공 및 유체 동력 연삭이 있습니다.
유체 동력 연삭은 유압에 의해 구동되어 연마 입자를 운반하는 액체 매체가 공작물 표면을 빠르게 앞뒤로 흐르게 합니다. 매체는 주로 저압에서 흐름 특성이 좋은 특수 화합물(고분자 유사 물질)을 연마재와 혼합하여 사용합니다. 연마재는 실리콘 카바이드 분말로 만들 수 있습니다.
자기 연마 연마는 자기 연마재를 사용하여 자기장의 작용으로 연마 브러시를 형성하여 공작물을 연마하는 방식입니다. 이 방법은 높은 가공 효율, 우수한 품질, 제어하기 쉬운 가공 조건 및 좋은 작업 조건을 가지고 있습니다.
적절한 연마재를 사용하면 표면 거칠기가 Ra0.1μm에 도달할 수 있습니다.
플라스틱 금형 가공에서 필요한 연마는 다른 산업에서 필요한 표면 연마와는 크게 다릅니다. 엄밀히 말하면 금형 연마는 거울 표면 처리라고 해야 합니다.
이를 위해서는 연마 자체에 대한 높은 기준이 필요할 뿐만 아니라 표면 평탄도, 부드러움 및 기하학적 정확도에 대한 높은 기준도 요구됩니다. 표면 연마는 일반적으로 밝은 표면만 있으면 됩니다.
미러 표면 처리 기준은 4단계로 나뉩니다: AO=Ra0.008μm, A1=Ra0.016μm, A3=Ra0.032μm, A4=Ra0.063μm. 전해 연마 및 유체 연마와 같은 방법은 부품의 기하학적 정확도를 정밀하게 제어하기 어렵고 화학 연마, 초음파 연마 및 자기 연마 연마와 같은 방법의 표면 품질이 요구 사항을 충족 할 수 없기 때문입니다, 기계적 연마 는 주로 정밀 금형의 거울 표면 처리에 사용됩니다.
고품질 연마 효과를 얻으려면 오일스톤, 사포, 다이아몬드 연마 페이스트와 같은 고품질 연마 도구와 보조 품목을 갖추는 것이 중요합니다.
연마 절차의 선택은 기계 가공, 스파크 가공, 연마 등과 같은 이전 가공 후 표면 상태에 따라 달라집니다.
기계적 연마의 일반적인 절차는 다음과 같습니다:
(1) 거친 연마
밀링, 스파크 가공, 연삭 등의 작업 후 표면은 35000-40000rpm의 회전식 표면 연마기 또는 초음파 연마기를 사용하여 연마할 수 있습니다.
일반적인 방법으로는 직경 Φ3mm의 휠과 WA#400을 사용하여 흰색 스파크 층을 제거하는 방법이 있습니다. 그 다음에는 손으로 오일스톤을 연마하고 스트립 오일스톤과 등유를 윤활유 또는 냉각수로 사용합니다.
일반적인 사용 순서는 #180~#240~#320~#400~#600~#800~#1000입니다. 많은 금형 제조업체는 시간을 절약하기 위해 #400부터 시작하는 것을 선택합니다.
세미 미세 연마는 주로 사포와 등유를 사용합니다. 샌드페이퍼 그릿의 순서는 다음과 같습니다: #400 ~ #600 ~ #800 ~ #1000 ~ #1200 ~ #1500.
실제로 #1500 사포는 경화된 금형강(52HRC 이상)에만 적합하며, 사전 경화된 강철 부품에 표면 화상을 일으킬 수 있으므로 사전 경화된 강철에는 적합하지 않습니다.
미세 연마는 주로 다이아몬드 연마 페이스트를 사용합니다. 다이아몬드 연마 분말 또는 연마 페이스트가 혼합된 연마 천 휠을 연마에 사용하는 경우 일반적인 연마 순서는 9μm(#1800) ~ 6μm(#3000) ~ 3μm(#8000) 순입니다.
9μm 다이아몬드 연마 페이스트와 연마 천 휠을 사용하여 #1200 및 #1500 사포에 남은 털이 많은 연마 자국을 제거할 수 있습니다. 그런 다음 접착 펠트와 다이아몬드 연마 페이스트를 사용하여 1μm(#14000) ~ 1/2μm(#60000) ~ 1/4μm(#100000) 순서로 연마합니다.
1μm(1μm 포함) 이상의 정밀도가 요구되는 연마 공정은 금형 가공 작업장의 깨끗한 연마실에서 수행할 수 있습니다. 보다 정밀한 연마를 위해서는 절대적으로 깨끗한 공간이 필요합니다. 먼지, 연기, 비듬, 침방울은 몇 시간 동안의 작업 끝에 얻은 고정밀 연마 표면을 망칠 수 있습니다.
사포로 연마할 때는 다음 사항에 유의해야 합니다:
(1) 사포로 연마할 때는 부드러운 나무 또는 대나무 막대기를 사용해야 합니다. 원형 또는 구형 표면을 연마할 때 부드러운 나무 막대기를 사용하면 원형 및 구형 표면의 곡률을 더 잘 맞출 수 있습니다.
반면 벚나무와 같이 단단한 나무는 평평한 표면을 연마하는 데 더 적합합니다. 나무 막대기의 끝은 강철 부품의 표면 모양에 맞게 다듬어야 나무(또는 대나무) 막대기의 날카로운 모서리가 강철 부품의 표면을 긁는 것을 방지할 수 있습니다.
(2) 다른 종류의 사포로 전환할 때는 연마 방향을 45°~90°로 변경해야 합니다. 이렇게하면 연마 후 이전 유형의 사포가 남긴 줄무늬 그림자를 구분할 수 있습니다. 다른 종류의 사포로 변경하기 전에 100% 순면을 사용하여 알코올과 같은 세척 용액으로 연마 표면을 조심스럽게 닦아야 합니다.
표면에 작은 자갈 조각만 남아 있어도 이후 연마 공정 전체를 망칠 수 있기 때문입니다. 이 청소 과정은 사포 연마에서 다이아몬드 연마 페이스트 연마로 전환할 때도 똑같이 중요합니다. 연마 프로세스를 계속하기 전에 모든 입자와 등유를 완전히 청소해야 합니다.
(3) 공작물 표면의 긁힘과 화상을 방지하기 위해 #1200 및 #1500 사포로 연마할 때는 특별한 주의를 기울여야 합니다. 따라서 가벼운 하중을 가하고 표면에 2단계 연마 방법을 사용해야 합니다. 연마에 사용되는 사포의 종류에 따라 두 가지 방향으로 45°~90° 회전하면서 두 번 연마해야 합니다.
다이아몬드 연마 및 연마 시 주의해야 할 사항은 다음과 같습니다:
(1) 이러한 유형의 연마는 가능한 한 가벼운 압력으로 수행해야 하며, 특히 미리 경화된 강철 부품을 연마하고 미세 연삭 페이스트를 사용할 때는 더욱 그렇습니다. #8000 연마 페이스트로 연마할 때 일반적으로 사용되는 하중은 100~200g/cm2이지만 이 하중을 정밀하게 유지하기가 어렵습니다. 이를 쉽게하기 위해 구리 조각을 추가하는 등 나무 막대기에 얇고 좁은 손잡이를 만들거나 대나무 막대기의 일부를 잘라내어 더 유연하게 만들 수 있습니다. 이렇게 하면 연마 압력을 제어하여 금형 표면의 압력이 너무 높지 않도록 할 수 있습니다.
(2) 연마에 다이아몬드 연삭을 사용할 때는 작업 표면이 깨끗해야 할 뿐만 아니라 작업자의 손도 조심스럽게 청소해야 합니다.
(3) 각 연마 세션은 너무 길어서는 안 되며, 짧을수록 좋습니다. 연마 과정이 너무 길면 "오렌지 껍질"과 "파임"이 발생할 수 있습니다.
(4) 고품질의 연마 효과를 얻으려면 열을 쉽게 발생시키는 연마 방법과 도구를 피해야 합니다. 예를 들어 휠 연마는 열을 발생시켜 '오렌지 껍질'을 쉽게 유발할 수 있습니다.
(5) 연마 공정이 중지되면 공작물 표면의 청결을 유지하고 모든 연마재와 윤활유를 조심스럽게 제거하는 것이 매우 중요합니다. 그 후 표면에 금형 방청 코팅을 뿌려야 합니다.
기계 연마는 주로 수작업으로 이루어지기 때문에 현재의 연마 기술이 연마 품질에 영향을 미치는 주요 요인입니다. 또한 금형 재료, 연마 전 표면 상태, 열처리 공정과도 관련이 있습니다.
고품질의 강철은 좋은 연마 품질을 얻기 위한 전제 조건입니다. 강철의 표면 경도가 고르지 않거나 특성이 다르면 연마에 어려움이 발생하는 경우가 많습니다. 강철의 다양한 내포물과 기공은 연마에 도움이 되지 않습니다.
3.1 다양한 경도가 연마 공정에 미치는 영향
경도가 증가하면 연마가 더 어려워지지만 연마 후 거칠기는 감소합니다. 경도가 증가하면 거칠기를 낮추는 데 필요한 연마 시간도 그에 따라 증가합니다. 동시에 경도가 증가함에 따라 과도하게 연마할 가능성도 감소합니다.
3.2 공작물 표면 상태가 연마 공정에 미치는 영향
열로 인해 강철의 표면층이 손상될 수 있습니다, 내부 스트레스또는 기계 가공을 절단하는 파쇄 과정 중 다른 요인에 의해 영향을 받을 수 있습니다. 부적절한 절단 매개 변수는 연마 효과에 영향을 미칩니다. 스파크 가공 후 표면은 일반 기계 가공 또는 열처리 후 표면보다 연마하기가 더 어렵습니다.
따라서 스파크 가공이 끝나기 전에 정밀 스파크 드레싱을 적용해야 하며, 그렇지 않으면 표면에 경화된 얇은 층이 형성됩니다. 정밀 스파크 드레싱을 잘못 선택하면 열에 영향을 받는 층의 깊이가 최대 0.4mm에 달할 수 있습니다. 경화된 얇은 층의 경도는 기본 경도보다 높으므로 제거해야 합니다.
따라서 거친 연삭 공정을 추가하고 손상된 표면층을 철저히 제거하고 평균 거친 금속 표면을 만들고 연마 공정을위한 좋은 기초를 제공하는 것이 가장 좋습니다.
화학적 연마는 연마 요구 사항이 높지 않고 가열해야 하는 경우에 사용됩니다. 현재 기술로 위의 세 가지 유형의 연마를 사용할 수있는 경우 화학 연마의 효과가 좋지 않고 전체 비용이 높기 때문에 화학 연마를 사용하지 마십시오.