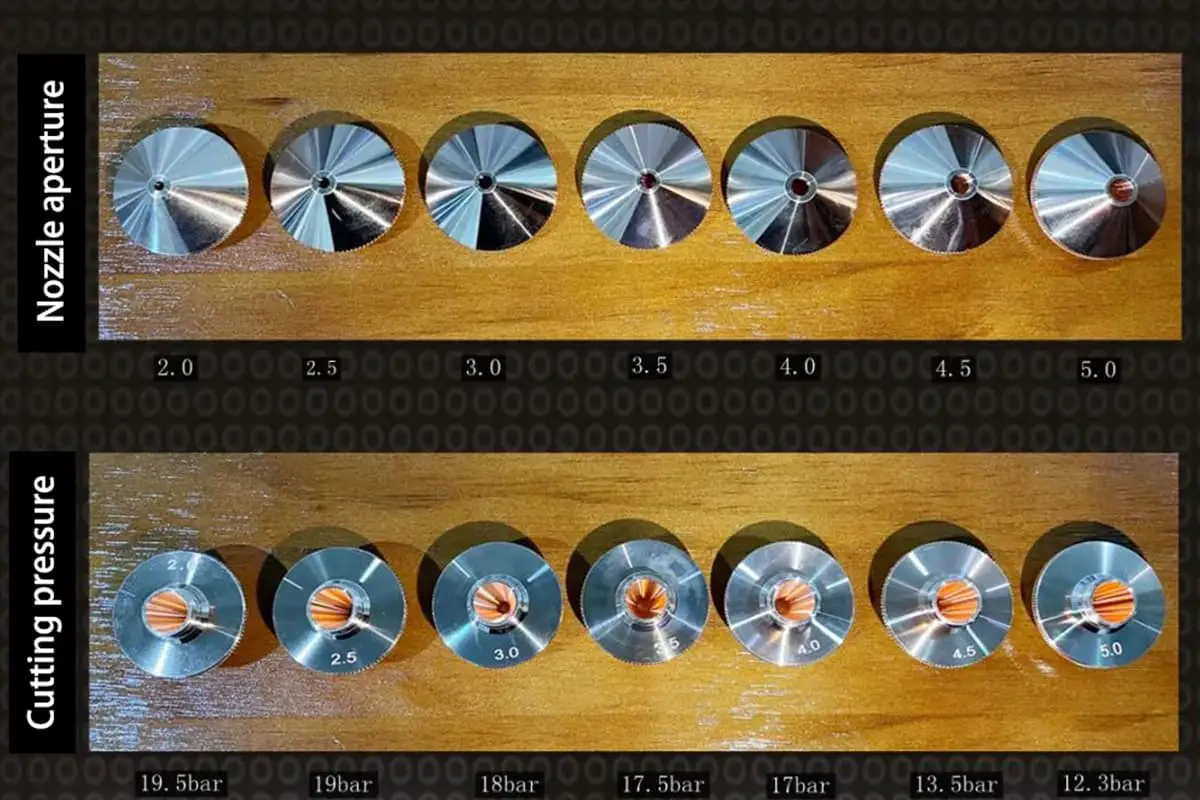
Why is laser cutting revolutionizing the shipbuilding industry? As shipbuilders face intense market competition and increased quality demands, laser cutting technology offers a solution with its high efficiency, precision, and environmental benefits. This article delves into how laser cutting is transforming shipbuilding by reducing costs, improving manufacturing quality, and enabling more precise and rapid construction. Learn how this technology is setting new standards in the industry and what future advancements might bring.
The shipbuilding industry is a significant player in metal welding and cutting, with its main processes being cutting and welding. Over the past few years, the industry has undergone a rapid expansion followed by a sudden contraction.
According to the Shipbuilding Industry Association, the market adjustment has resulted in some new developments in the industry. Despite the overall economic aggregate of the shipbuilding industry remaining unchanged, profits have decreased to some extent, but export orders have increased as the overall order has declined.
Additionally, the concentration of the shipbuilding industry has further increased, with the top ten companies now occupying over 53.4% of the market in China. With the intense market competition, decreased profits, and increasing quality requirements, the shipbuilding industry has placed a greater emphasis on manufacturing quality.
Laser cutting, being an efficient, green, high-quality, and high-precision technology, has become even more crucial in promoting the development and optimization of the shipbuilding industry. It plays a crucial role in reducing weight, re-manufacturing, reducing costs, reducing man-hours, saving energy, and protecting the environment in the shipbuilding industry.
Furthermore, the laser cutting process is an ideal method for preparing the ship’s front plate, aligning with the current trend of large-scale ship structures, precision manufacturing, and efficient construction.
Laser cutting is a common thermal cutting technique. It works by using a laser to produce a high-density laser beam, which is then focused by a group of laser lenses onto the workpiece. The beam repeatedly heats the material of the workpiece, causing it to rapidly melt, vaporize, and form holes.
As the cutting takes place, a high-speed air flow that is coaxial with the light beam removes the molten waste from the incision, completing the cutting and separation of the workpiece.
Laser cutting principle
Good Cutting Quality:
Laser cutting offers excellent cutting quality with its small laser spot and high energy density, resulting in fast cutting speed and a narrow, flat incision. The cut surface is smooth and attractive, with a surface roughness of only a few tens of micrometers. The dimensional accuracy of the cut parts can reach ± 0.05mm.
The workpiece undergoes minimal deformation and has a small heat-affected zone, making it highly adaptable and flexible. This allows for laser cutting to be used as the final processing step, eliminating the need for secondary processing and reducing processing costs.
High Cutting Efficiency:
Laser cutting is highly efficient due to its optical and transmission characteristics, which can be performed on a laser cutting machine with multiple numerical control operating tables. Additionally, cutting of multiple shapes and parts can be achieved by modifying the NC program, including 2D and 3D cutting.
Reduced Tool Costs:
Laser cutting is different from traditional cutting methods as the cutting torch does not come in contact with the workpiece, eliminating the need for tool changes and reducing tool wear. The laser can be adjusted to cut different thicknesses or shapes of parts simply by changing the laser output parameters.
Green and Environmentally Friendly:
Laser cutting is a green and environmentally friendly processing method with low noise, vibration, and no pollution. It is also a low-impact process that does not produce any waste.
Fast Cutting of Various Materials:
Laser cutting can be performed on a wide range of materials, including metals, non-metals, composite materials, and wood. The cutting speed is fast, with a 4000W laser cutting a 12mm thick low carbon steel with a 30° bevel at a speed of 2200mm per minute. A 6000W laser can cut an 8mm thick stainless steel with a 22.5° bevel at a speed of 1500mm per minute.
(1) Characteristics of Ship Cutting
The shipbuilding industry demands high precision in hull segmentation and transfer accuracy, and the frame transfer clearance must be kept within 1mm. In the past, plasma was commonly used to cut the ribs by shipbuilding companies, which required manual trimming during field assembly due to the set trimming allowances on the ribs to ensure the assembly gap. Poor cutting quality would result in increased residual oxide in the cutting slot, leading to increased assembly workload and prolonged assembly cycle, affecting the entire segmented construction cycle.
However, the use of a laser cutting machine to eliminate the assembly margin reduces the need for on-site trimming and minimizes labor and material waste. This leads to faster assembly of the structure and improved assembly quality.
(2) Advantages of Laser Cutting Technology in Shipbuilding
In recent years, precision and rapid shipbuilding have become the main trends in the shipbuilding industry, and laser cutting technology has developed rapidly, accounting for over 70% of the entire laser processing industry. The shipbuilding industry primarily uses steel plates as the main raw material, and laser cutting plates can replace some die-cutting methods that require complex large molds, significantly reducing production cycles and costs.
Presently, the cutting method of hull plate parts in the shipbuilding industry mainly involves flame cutting, plasma cutting, shear processing, and laser cutting. However, other cutting methods have several disadvantages compared to laser cutting. For instance, flame and plasma cutting have wide slits, low cutting accuracy, produce harmful gases, and cause significant environmental pollution.
In shipboard cutting, laser cutting has the advantage of high accuracy, minimal thermal deformation, reduced secondary processing (such as milling, drilling, etc.), transfer and grinding, especially for small circles, small holes, and curved surfaces. It can fully meet the hull sectional transfer accuracy requirements and control the frame assembly clearance within 1mm, but its practical cutting speed for steel is slower compared to plasma cutting.
The figure shows the relationship between cutting speed and cutting thickness of low carbon steel under different cutting methods and the cutting effect of low carbon steel under different cutting methods.
Relationship between cutting speed and cutting thickness of low carbon steel under different cutting modes
Cutting effect of low carbon steel under different cutting methods
In shipbuilding, laser cutting is used to ensure the assembly gap by setting a cutting margin on the ribs, which prevents plasma cutting. However, manual trimming leads to uneven cutting quality.
By using laser cutting, the quality of the cut is improved, resulting in a good verticality of the cut surface, no dross, a thin oxide layer, and a smooth surface. This eliminates the need for secondary processing and allows for direct welding.
Additionally, laser cutting minimizes thermal deformation, ensuring high accuracy in curve cutting. This reduces coordination man-hours and enables obstacle-free cutting of high-strength ship plates, reducing assembly workload, cycle time, material and labor costs.
Deviation of structural gaps in ships
(3) Application Status of Laser Cutting Technology in Shipbuilding
Presently, CO2 laser cutting technology is the most widespread and globally utilized manufacturing and processing technology in the shipbuilding industry.
However, the cutting speed of the commonly used 5-6kW CO2 laser falls short compared to plasma and fails to meet the current speed and efficiency requirements of the shipbuilding industry. Additionally, the high equipment and machinery maintenance costs, along with low returns, make it difficult for the shipbuilding industry to meet its needs.
Despite its limitations in shipbuilding applications, laser cutting technology has been gradually adopted in the field.
Additionally, there have been new advancements in related cutting and processing technologies.
The effect of 4 kW CO2 laser cutting
In recent years, several domestic shipyards with strong capabilities, such as Jiangnan Changxing Shipbuilding Base, have introduced the advanced “CO2 laser cutting machine” to the world.
However, the technology application of the laser cutting machine is more optimistic only in Japan. Its success or failure provides valuable experience for the domestic shipbuilding industry.
With the growth of domestic manufacturing, fiber lasers have also seen rapid development. The high power of fiber lasers, combined with their excellent beam quality, high electro-optical conversion efficiency, compact size, and the ability to be transmitted through optical fibers, provide greater working flexibility and are virtually maintenance-free with high reliability. This has challenged traditional CO2 laser cutting technology.
As the effectiveness of fiber laser cutting in thick plates continues to improve, many domestic cutting equipment manufacturers have entered or are preparing to enter the fiber laser market.
Universities, institutions, and scholars are also studying the cutting effect of fiber lasers. For instance, Jae Sung Shin has used a 6kW fiber laser to examine the cutting performance of high-speed fiber lasers on stainless steel plates. The maximum cutting speed achieved was 72mm per minute, and the study showed that the fiber laser was able to cut 60mm thick stainless steel plates with excellent cut shape and slit width.
Cutting speed for cutting 60mm thick stainless steel plate
Antti Salminen used a 5kW fiber laser to perform inert gas-assisted laser cutting on 10mm stainless steel plates and 4mm aluminum plates. The study investigated the effects of laser power, cutting speed, focus position, and auxiliary gas pressure on cutting performance and quality.
The maximum cutting speed was determined at different laser powers and the combination of various cutting parameters was studied to optimize cutting performance and achieve high-quality cuts.
For the laser power parameter set at 4kW and a cutting speed of 1m per minute, the figure shows the cutting effect on a 10mm thick stainless steel plate with 2MPa nitrogen.
10mm thick stainless steel plate with laser power of 4kw, cutting speed of lm / min, and nitrogen of 2MPa
The output power of a fiber laser on a 10mm thick stainless steel plate with a laser power of 4kW, cutting speed of 1m/min, and nitrogen pressure of 2MPa has reached 50kW. Currently, the development focus is still on 1-4kW lasers, with 10kW lasers being developed based on this.
Laser technology has been industrialized and has solved the cutting and welding problems in shipbuilding, aerospace, and automobile manufacturing.
The shipbuilding industry has fully utilized laser cutting technology, incorporating it with robots to form robot cutting systems. Since 2000, robot companies such as KUKA in Germany, ABB in Switzerland, and FANUC in Japan have developed a range of laser robots and laser cutting robots.
The integration of robotics and laser technology is the current mainstream trend in the shipbuilding industry and the entire manufacturing industry.
As previously mentioned, laser cutting technology has significant advantages in quality and has been widely adopted in industries such as automotive, sheet metal, and machinery.
Currently, large shipbuilding companies such as Jiangnan Shipyard and Wuhan Shipyard use laser cutting to process ship plates.
However, objectively speaking, laser cutting has not yet dominated the domestic shipbuilding industry due to the following reasons:
According to the current state of the industry, laser cutting technology is expected to be widely used in shipbuilding due to the decline in laser prices and the increase in the level of intelligence. The following are the main reasons for this:
(1) Cost-effectiveness
Cost reduction is a crucial issue in the shipbuilding industry. Currently, traditional processes involve multiple steps, including board entry, flame or plasma cutting, artificial deburring, artificial groove or trimming machine opening groove, and rocker, drill, etc. This process is complex and expensive. However, if laser cutting is used instead, the process can be simplified to board entry and laser cutting, which significantly reduces time, labor, and site costs.
(2) Flexibility and intelligence of laser equipment
In recent years, there has been a significant advancement in the intelligence level of domestic equipment. CNC and robot-based equipment have various modular and intelligent technologies. For example, Nantong COSCO Kawasaki’s intelligent production line can adapt to complex manufacturing systems. This adaptability is crucial for the segmented manufacturing, outdoor operations, and complex production environments of the shipbuilding industry.
The process plays a crucial role in determining the effectiveness of equipment. Therefore, technical personnel must monitor and control the mechanical cutting process in real-time to gather and analyze process information. The integration of multiple energy fields and processes can simplify the cutting process, improve the laser cutting effect, reduce the construction period and cost.
(3) Reduced equipment and maintenance costs
The rapid development of high-power fiber laser and semiconductor laser manufacturing technology and the improvement of corresponding processing technology have led to high-efficiency, energy-saving, and precise cutting characteristics. This meets the market demand and current development direction of laser manufacturing technology.
Fiber lasers and semiconductor lasers should be industrialized and commercialized, and corresponding equipment and control technologies should be developed and improved. The progress of equipment has further improved the integration and flexibility of the equipment.
For the special requirements of the cutting machine for ship stern plate work and the diversity of hull structure shapes, multi-degree-of-freedom optimization design of the laser cutting head, development of rotation control methods, and control systems are necessary. Attention should also be given to the application research of robots and machine vision detection systems in the laser field to achieve monitoring of cutting paths, high-precision cutting, and unmanned automatic operation to improve the quality and efficiency of operations.
Effective control of cutting quality can reduce production costs and safety risks.