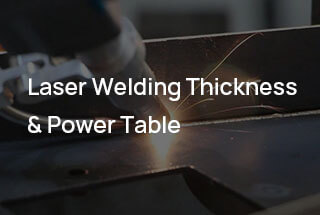
Have you ever thought about how welding has evolved to meet the demands of modern industries? Laser welding, a groundbreaking technology, has revolutionized manufacturing with its precision and efficiency. From its origins in the 1960s to its widespread adoption today, laser welding stands out for its speed, flexibility, and quality. In this article, you’ll discover the fascinating history of laser welding, its key advancements, and its critical role in industries like automotive and aerospace. Dive in to explore how this technology shapes the future of manufacturing.
Welding, as a method for achieving permanent material connections, is widely used in sectors including mechanical manufacturing, petrochemicals, bridges, ships, construction, power engineering, transportation vehicles, and aerospace.
It has become an indispensable processing technology in the mechanical manufacturing industry.
Moreover, with the development of the national economy, its application field will continue to expand.
The laser, a major invention of mankind since the 20th century following atomic energy, computers, and semiconductors, has high energy density, accuracy, and adaptability.
As a new means of cutting and welding applied to industrial production, it has great development potential. Laser welding fully demonstrates its advanced, fast, and flexible processing characteristics in industrial production.
It is not only a technical guarantee for the development of new industrial products, but also an indispensable technical means for high-quality, low-cost production.
LASER, an acronym composed of the first letter of each word in “Light Amplification by Stimulated Emission of Radiation”.
The principle of the laser was discovered by the famous American physicist Albert Einstein as early as 1916, but it was not until 1960 that the laser was successfully manufactured for the first time.
The laser was born in the context of theoretical preparation and urgent need for production practice.
As soon as it came out, it achieved extraordinarily rapid development. The development of lasers not only gave new life to the ancient science and technology of optics, but also led to the emergence of an entire new industry.
Lasers enable people to effectively use unprecedented advanced methods and means to achieve unprecedented benefits and results, thereby promoting the development of productivity.
Since lasers offer exceptional advantages, they have been applied in the welding field since the 1970s.
Currently, laser welding research accounts for about 20% of the total in welding methodology, second only to gas shield welding.
Lasers for welding require high power density (104-105W/cm2), fundamental mode power density distribution, and good beam quality. The most commonly used lasers for welding include the following:
(1) CO2 Gas Laser
This is a type of gas laser that uses CO2 as the working material. It has the benefits of a simple structure, low cost, user-friendliness, uniform working medium, good beam quality, and the ability to operate continuously and stably for an extended period.
At present, it is the most diverse and widely used type of laser. The helium-neon laser is the most common variant.
(2) Nd:YAG Laser, Disc YAG Laser;
These are types of solid-state lasers that use yttrium aluminum garnet crystals as a matrix. The chemical formula for yttrium aluminum garnet is Y3Al5O12, commonly abbreviated as YAG.
(3) Fiber Laser;
CO2 Laser | Lamp-pumped Nd:YAG | Laser Pumping Nd:YAG | Fiber Laser (Laser Pumping) | Disc-Type Laser (Laser Pumping) | Semiconductor Laser | |
Laser Medium | Mixed Gas | Crystal Rod | Crystal Rod | Fiber Optic (ytterbium) | Crystal Thin Disc | Semiconductor Array |
Wavelength nm | 10,600 | 1,060 | 1,060 | 1,070 | 1,030 | 800-960 |
Light Beam Transmission | Lens | Fiber optic | Fiber Optic | Fiber Optic | Fiber Optic | Lens |
Output Power KW | 20 | 4 | 6 | 10 | 4 | 6 |
Beam Quality mm. mrad | 25 | 12 | 12 | 5 | 2.5 | 80 |
Energy Efficiency % | 10 | 3 | 10 | 20 | 20 | 35 |
Employing lasers in welding robots represents a significant aspect of laser welding. With attributes such as multi-degree freedom, flexible programming, high automation, and adaptability, welding robots are a crucial part of welding assembly lines.
Mounting lasers on welding robots enhances the welding quality and broadens the scope of use, thereby making them increasingly pivotal in shipbuilding and automotive production lines.
Figure 4 illustrates a schematic representation of a CO2 laser welding robot in action.
The welding of metallic materials with a laser essentially involves a complex interaction between the laser and opaque substances.
This process, at a microscopic level, is a quantum one, and macroscopically, it manifests as reflection, absorption, melting, and vaporization phenomena.
Laser welding can be executed using a continuous or pulsed laser beam, and the principles of laser welding can be divided into heat conduction welding and deep penetration laser welding.
For power densities less than 104-105 W/cm2, it is heat conduction welding, which results in shallow melt depth and slower welding speeds.
For power densities greater than 105-107 W/cm2, the metal surface under the heating effect forms a “keyhole”, resulting in deep penetration welding, characterized by fast welding speeds and a high depth-to-width ratio.
During the interaction between the laser and the workpiece, a self-oscillation effect may occur, leading to periodic changes in the weld pool, small holes in the weld pool, and metal flow phenomena.
The frequency of this oscillation is related to the parameters of the laser beam, the thermo-physical properties of the metal, and the dynamic characteristics of the metal vapor.
The periodic changes in the weld pool can generate two unique phenomena in the weld seam: One is the formation of gas-filled pores, which due to periodic changes, and as the metal from the pool flows from front to back around it, combined with the disturbance caused by metal evaporation, can potentially bisect the small hole, leaving the vapor in the weld seam and forming a pore after solidification.
The other is the periodic change in the melt depth at the root of the weld seam, which is related to the periodic changes in the small hole.
Significant factors affecting the quality of laser welding include power density, pulse waveform, defocus amount, welding speed, and supplementary blowing. Their organic coordination determines the final welding quality.
Compared to other traditional welding processes, laser welding has many advantages. One of its primary benefits is the ability to concentrate the laser beam on a very narrow area, thereby generating a high-energy-density heat source.
Subsequently, this concentrated heat source swiftly sweeps across the welding seam. In this respect, laser welding can be compared to electron beam welding.
Simultaneously, the tight concentration of the laser beam, the effective heat transfer to the workpiece, and the narrow heat-affected zone present challenges in joint assembly.
A tiny assembly deviation can lead to significant changes in welding conditions, and even narrow gaps (≤0.1mm) can cause defects in laser radiation coupling and a decrease in thermal efficiency.
To address the issues of high joint assembly precision and gap requirements in laser welding, as well as common defects such as porosity, cracking, undercutting, and high equipment investment with low energy conversion rate, one of the recent trends in laser welding is the use of composite laser technology.
For instance, the combined laser+arc welding method integrates the advantages of laser welding, such as a large depth-to-width ratio of the weld, small heat-affected zone, fast welding speed, low line energy in welding, small welding deformation, small diameter of the focused light spot, and high energy density, with the benefits of arc welding, such as low equipment investment, gap insensitivity, and metal filling capability.
This combination has achieved increased laser absorption rate, increased melting depth, and arc stabilization. Besides laser+arc, laser composite technology has also developed other comprehensive techniques like laser-HF welding, laser compression welding, and laser brazing, expanding the application range and usage effects of laser welding, and promoting the further development of laser welding technology.
The advancement of the automotive industry has set higher standards for vehicle body quality.
Laser welding and cutting techniques not only outperform traditional manufacturing methods in terms of processing quality, but also significantly improve production efficiency.
As illustrated in Figure 7, laser welding and cutting technologies will undoubtedly play a critical role in the field of automobile manufacturing in the 21st century.
The entire process of laser welding in automobile manufacturing mainly includes three types: laser butt welding of unequal-thickness plates; laser assembly welding of body assemblies and subassemblies; and laser welding of automotive parts.
Butt welding was initially a technique adopted by Honda Motor Company in Japan in the 1960s to utilize scrap metal for the inner plates of the vehicle body. From the mid-1980s, laser butt welding as a new technology received widespread attention in Europe, America, and Japan.
Laser butt welding, in body design and manufacturing, combines plates of different thicknesses, materials, and properties into a whole through laser cutting and assembly technology, then formed into particular body components through stamping.
The deep penetration laser welding technology, with its high welding speed and excellent connection quality, has greatly enhanced the application of laser welding technology in body manufacturing.
The use of laser welding technology in automobile bodies significantly improves the rigidity, strength, and sealing of the car; reduces body weight and achieves energy-saving goals; enhances assembly precision, increasing body rigidity by 30%, thereby improving safety; reduces stamping and assembly costs in the process of automobile body manufacturing, reduces the number of body parts and improves the degree of body integration; makes the entire body stronger and safer, and also reduces noise and vibration during vehicle operation, improving ride comfort.
The use of laser welding in place of traditional welding for automotive parts results in almost no deformation at the welding site, faster welding speed, and eliminates the need for post-weld heat treatment.
At present, laser welding is widely used in the manufacture of various automobile parts, including transmission gears, valve push rods, door hinges, drive shafts, steering shafts, engine exhaust pipes, clutches, turbocharger wheel axles, and chassis, becoming a standard process in automotive parts manufacturing.
With the development of laser welding technology to this day, its trend to gradually replace traditional welding methods such as arc welding and resistance welding is irreversible.
In the 21st century, laser welding technology will play a crucial role in the field of material connection.