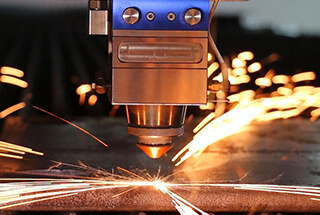
Have you ever considered the importance of a laser cutting head’s protective lens? This tiny component, often overlooked, shields the laser system from dust and damage, ensuring precise cuts and preventing costly repairs. In this article, discover how to select the right lens to maintain your machine’s efficiency and longevity. Learn about the critical factors to consider and avoid common pitfalls that can lead to significant performance issues and expenses. Dive in to enhance your laser cutting process with expert insights and practical tips.
The lower protective lens is an essential consumable accessory for laser equipment, with a very high replacement frequency. It acts as a “double-sided fence” in the external light path of the laser.
Its primary functions are to withstand the harsh external processing environment, prevent the invasion of dust and splashes, and resist the high-power laser transmitted in the internal forward direction.
Due to its crucial role, it is often the first component to be affected even when there is a problem in the gas path, leading to huge consumption.
Customers frequently inquire about how to select the appropriate protective lens. To address these inquiries, we have interviewed the R&D and after-sales engineers of Raycus to provide answers to your concerns.
There is a significant difference between lower protective lenses. These lenses not only protect the cleanliness of the internal light path of the cutting head but also require high-power laser bearing capacity and high laser transmission.
To meet these demanding conditions, the substrate, processing, coating, and packaging requirements for the lower protective lens are stringent.
Generally speaking, the original lower protective lens of the cutting head is expensive, which has made third-party lower protective lenses quite popular. However, not every third-party manufacturer has the production capacity to manufacture this type of consumable.
In recent years, as the price war for fiber lasers has heated up, the price of laser accessories has decreased significantly. Nevertheless, blindly pursuing lower prices and ignoring quality will not lead to positive outcomes.
The unqualified lower protective lens absorbs light and heats up rapidly, causing a significant drift in focus and resulting in poor cutting.
Furthermore, excessive heating may cause the lower protective lens to break down, and even lead to reverse breakdown of the cutting head’s focusing and alignment.
Damage to high-value components can result in maintenance costs as high as 20%-50% of the price of a new cutting head, resulting in significant losses.
Lower protective lens breakdown
The coating that does not meet the required standards has poor light transmittance. As a result, there is insufficient transmission and strong reflection, causing the return light from the lower protective lens to reverse through the collimating lens and focusing lens of the cutting head. This light then converges near the end cap of the output head, leading to the burning of the protective window of the output head.
The protective window cover and protective end cap of cutting head are burned
The situation becomes more serious when the end cap of the output head is burnt. The forward laser cannot be transmitted and gets trapped in the output head, leading to the destruction of the metal structure of the output head. This, in turn, causes water leakage, slag spraying, and other related issues.
In such cases, irreversible damage is likely to occur to the cutting head.
Cutting head shell burned
In general, small and medium-sized end customers have relatively low demand for consumables and weak bargaining power. They can purchase consumables through equipment suppliers. However, caution should be exercised when buying from informal channels or when prices are significantly different.
Large terminal or integrator customers, on the other hand, have high demand and strong bargaining power and quality inspection abilities. They can purchase from integrators, consumable manufacturers or first-class agents.
When purchasing protective lenses, it is important to consider the following points:
There are four types of protective lenses that should not be used.
The first type is the protective lens with a film coating and quartz substrate exposed. This type of protective lens can be recognized with the naked eye.
Lower protective lens coating stripping
The second type is the protective lens with poor coating quality. Although the appearance of this protective lens may seem fine, testing shows that some areas of the coating have low transmittance and high reflection.
This type of protective lens cannot be detected by the naked eye or microscope and can only be measured accurately with professional instruments.
Poor coating quality of lower protective lens
The third type is a protective lens with foreign matter or bubbles between the film and substrate. This type of protective lens is intended for use under high power, but has a short service life and is prone to burning.
Bubbles or foreign matters at the bottom of the film
The fourth type is the protective lens with poor finish, which has a short service life.
Poor finish of lower protective lens
Identifying system instability and risks resulting from abnormal protection is a pressing requirement in today’s competitive market. While most high-power cutting heads currently have protective lens temperature and scattered light monitoring, some cutting head monitoring indirectly deduces the current temperature, resulting in low accuracy and low sensitivity response.
Sensor packaging position and abnormal points that can be monitored
Based on the situation mentioned above, Raycus has recently implemented a new return light monitoring system in their medium and high-power lasers.
The primary return light monitoring sensor is enclosed near the end cap of the output optical cable, creating an almost coaxial monitoring arrangement. This enables prompt detection of any return light generated due to damage to the optical components in the cutting head.
Model of laser power section and output optical cable with return light monitoring
Assuming that the water cooling system is functioning normally, the Raycus laser return visit optical monitoring system will quickly trigger an alarm signal if it detects any of the following three conditions:
For instance, the Raycus 20kW model has been equipped with return light monitoring since 2019, successfully preventing the following issues:
Currently, the quality of protective lenses available on the market varies widely. We recommend carefully reviewing the above information and purchasing protective lenses through legitimate channels.