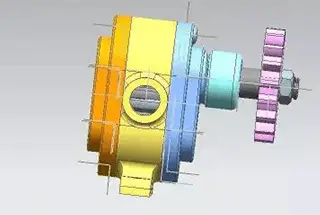
Have you ever wondered how mechanical structures transform ideas into tangible designs? Mechanical structure design turns abstract principles into detailed schematics, ensuring every part is optimized for functionality, strength, and manufacturability. This guide delves into essential design principles, material selection, and inter-component relationships, offering insights to improve your engineering projects. Discover how strategic design can enhance precision, durability, and efficiency, making your mechanical systems more reliable and effective.
The objective of mechanical structure design is, based on the overall design concept, to solidify the initial design principle into a detailed schematic that fulfills the required functions.
The design process transforms abstract working principles into specific components or parts, which involves determining the material, shape, size, tolerance, heat treatment method, and surface treatment of the structural members.
Moreover, it’s crucial to consider their manufacturing process, strength, rigidity, precision, and interrelationships with other components. Although the direct output of structural design is technical drawings, the task isn’t as simple as mechanical drafting.
Blueprints merely express the design scheme in engineering language; applying various techniques in mechanism design to materialize the design concept is the fundamental content of structural design.
The function of a mechanical structure is primarily achieved through the geometric shape of its components and the relative positional relationship between them. The geometric shape of a component is constituted by its surfaces.
Typically, a component comprises multiple surfaces, some of which directly contact the surfaces of other components. These contacting surfaces are referred to as functional surfaces. The areas connecting these functional surfaces are called connection surfaces.
The functional surfaces of a component are crucial in determining its mechanical function. The design of these functional surfaces is at the core of component structural design.
The primary geometric parameters used to describe functional surfaces include their geometric shape, size, number of surfaces, position, sequence, etc. Various structural solutions can be achieved to realize the same technical function through different designs of the functional surfaces.
In any machine or mechanical system, no component exists in isolation.
Therefore, in addition to studying the function and related characteristics of each component during structural design, it is also necessary to explore the interrelationships among the components.
The interrelationships between components can be classified into two categories: direct and indirect relationships.
Two parts with a direct assembly relationship are deemed directly related, whereas those without are considered indirectly related. Indirect relationships can be further divided into positional and motion-related classes.
Positional relationships refer to the requirement for two components to maintain certain spatial arrangements.
For example, in a speed reducer, the center distance between two adjacent transmission shafts must maintain specific precision, and the two shaft axes must be parallel to ensure the normal meshing of gears.
Motion-related relationships refer to the movement trajectory of one component being associated with another. For example, the movement trajectory of a lathe tool carrier must be parallel to the spindle’s centerline, which is guaranteed by the parallelism between the bed rail and the spindle axis.
Therefore, the spindle and rail are positionally related, while the tool carrier and spindle are motion-related.
Most components have two or more directly related components. Thus, each part usually has two or more locations structurally related to other components.
During structural design, the structures of directly related parts must be considered simultaneously to reasonably select heat treatment methods, shapes, sizes, precision, and surfaces of materials.
Additionally, requirements for indirect relationships, such as dimension chain and precision calculations, must also be considered.
Generally, the more directly related parts a component has, the more complex its structure becomes. Conversely, the higher the number of indirectly related parts, the higher the precision required.
Various materials can be chosen in part design, each with unique properties. Different materials correspond to different manufacturing processes.
The design process requires not only selecting appropriate materials based on functional requirements but also determining the appropriate manufacturing process based on material type.
Furthermore, the structure must be determined according to the requirements of the manufacturing process.
Only through proper structural design can the chosen material be utilized to its fullest advantage.
For designers to correctly select materials for parts, they must fully understand the mechanical properties, machinability, and cost-effectiveness of the relevant materials.
In structural design, different design principles should be adhered to based on the characteristics of the chosen materials and their corresponding manufacturing processes.
Mechanical products are utilized across various industries, with the specifics and requirements of structural design varying significantly.
However, the fundamental requirements for structural design are universal. The following outlines the requirements for mechanical structure design at three distinct levels.
Effort is put into the materialization of technical aspects to meet the primary mechanical requirements.
Elements such as the implementation of working principles, reliability of operation, processes, materials, and assembly are addressed.
Balancing various demands and constraints to enhance product quality and cost-effectiveness exemplifies modern engineering design.
Specific areas include operability, aesthetics, safety, cost, and environmental conservation. In contemporary designs, quality design holds significant importance and often dictates competitive strength.
The design approach solely focused on satisfying primary technical functions has become outdated.
Modern mechanical design’s core lies in harmonizing various demands, striking a balance and making appropriate trade-offs under the premise of fulfilling primary functions to improve product quality.
Structural design variables are systematically used to construct an optimized design space. Creative design thinking methods and other scientific methods are employed for selection and innovation.
The end result of mechanical design is to express a determined structural form in drawings. The final product is manufactured according to these designs through machining and assembly processes.
Therefore, the design of mechanical structures should meet various requirements as a product, including functionality, reliability, processability, economic efficiency, and aesthetic form.
Additionally, it should improve the force-bearing capacity of parts, enhancing their strength, rigidity, precision, and lifespan.
Mechanical structure design, thus, is a comprehensive technical task. Unreasonable or erroneous structural designs can lead to unexpected component failures, prevent machines from achieving required precision, and cause considerable inconvenience during assembly and maintenance.
The following structural design principles should be considered in the process of mechanical structure design.
The primary purpose of product design is to meet predetermined functional requirements.
Therefore, the design principle of achieving expected functionality is the first consideration in structural design. To meet these functional requirements, the following points must be adhered to:
(1) Explicit Functionality:
Structural design should determine the parameters, dimensions, and shape of the structure based on its function within the machine and its interconnection with other components.
The main functions of components include bearing loads, transmitting motion and power, and ensuring or maintaining the relative position or motion trajectory among related parts or components. The designed structure should meet its functional requirements as considered from the whole machine perspective.
(2) Functional Allocation:
During product design, it is often necessary to reasonably delegate tasks based on specific circumstances, i.e., decomposing one function into several sub-functions.
Each sub-function must be supported by a defined structure, and there should be a reasonable and coordinated connection between different structural parts to achieve the overall function.
Multiple structural components sharing one function can ease the burden on individual parts, thereby extending their service life.
For instance, the structure of a V-belt cross-section is an example of task distribution.
A fiber cord is used to withstand tension; a rubber filler layer absorbs the stretching and compression during belt bending; a fabric layer interacts with the pulley groove to generate the friction needed for transmission.
Another example is when friction generated by bolt pre-tightening alone is relied upon to withstand lateral loads, which can result in oversized bolts. This issue can be resolved by adding shear-resistant components, such as pins, sleeves, and keys, to share the lateral load.
(3) Functional Concentration: To simplify the structure of mechanical products, reduce manufacturing costs, and facilitate installation, a single part or component can be assigned multiple functions in some circumstances.
Although functional concentration can make the shape of parts more complex, it should be moderated to avoid increasing machining difficulty and inadvertently raising manufacturing costs. The design should be determined based on the specific situation.
(1) Equal strength criterion:
Changes in the cross-sectional dimensions of parts should be adapted to changes in internal stress, so that the strength of each section is equal.
The structure designed according to the principle of equal strength can make full use of materials, thereby reducing weight and cost. Design of cantilever brackets, stepped shafts, etc.
(2) Reasonable force flow structure:
In order to visually demonstrate the state of how force is transmitted in mechanical components, the force is regarded as flowing like water in the component, and these force lines converge into force flow.
The flow of this force plays an important role in structural design considerations. The force flow in the component will not be interrupted, and no force line will suddenly disappear. It must be transmitted from one place to another.
Another characteristic of force flow is that it tends to propagate along the shortest route, resulting in a dense force flow near the shortest route and forming a high stress zone.
The force flow in other parts is sparse, and there is even no force flow passing through. From a stress perspective, the material is not fully utilized.
Therefore, in order to improve the stiffness of the component, the shape of the component is designed according to the shortest force flow path as much as possible, reducing the load-bearing area, and thus reducing the accumulated deformation, increasing the stiffness of the entire component and making full use of the material.
(3) Minimize stress concentration in structures:
When the direction of force flow abruptly changes, the force becomes overly concentrated at the turn, leading to stress concentration.
Measures should be implemented in the design to ensure a gradual change in force direction. Stress concentration is a significant factor affecting the fatigue strength of components.
In structural design, efforts should be made to avoid or minimize stress concentration, such as by increasing transition radii, adopting stress relief structures, and so on.
(4) Establish load balanced structures:
During machine operation, some unnecessary forces, such as inertial forces and helical gear axial forces, are often generated.
These forces not only increase the load on parts like shafts and bearings, reducing their precision and lifespan, but also decrease the transmission efficiency of the machine. Load balancing refers to structural measures that partly or wholly balance these unnecessary forces to mitigate or eliminate their adverse effects.
These structural measures mainly involve the use of balancing components and symmetrical arrangement.
To ensure that components function normally throughout their lifecycle, it is essential to provide them with sufficient rigidity.
The primary purpose of mechanical component structural design is to ensure functionality, enabling the product to meet the required performance. However, the rationality of the design directly affects the production cost and quality of the components.
Therefore, it is crucial in structural design to strive for good manufacturability of the component mechanisms. Good manufacturability means the structure of the component is easy to manufacture.
Every manufacturing method has its limitations, which may result in high production costs or compromised quality.
Therefore, it’s important for designers to be familiar with the characteristics of various manufacturing methods, so as to maximize their strengths and minimize their weaknesses during design.
In actual production, the manufacturability of component structures is constrained by numerous factors. For example, the size of the production batch may affect the method of creating the workpiece blanks; the conditions of the production equipment may limit the size of the workpieces.
Additionally, factors like molding, precision, heat treatment, cost, etc., could potentially restrict the manufacturability of the component structure.
Therefore, these factors should be thoroughly considered in the structural design for their impact on manufacturability.
Assembly is a crucial step in the product manufacturing process, and the structure of the components directly influences the quality and cost of assembly. The structural design guidelines for assembly are briefly described as follows:
(1) Rational division of assembly units:
The entire machine should be dissected into several independently assembled units (parts or components) to achieve parallel and specialized assembly operations, shorten assembly cycles, and facilitate step-by-step technical inspections and repairs.
(2) Ensure correct installation of components:
This includes accurate positioning of parts, avoiding double mating, and preventing assembly errors.
(3) Facilitate assembly and disassembly of components:
The structural design should ensure enough assembly space, such as wrench space; avoid overly long mating to prevent increasing assembly difficulty and potential damage to mating surfaces, as seen in some stepped shaft designs; to facilitate the disassembly of parts, positions for placing disassembly tools should be provided, like in the case of bearing removal.
(1) The configuration of a product should be arranged based on factors such as its failure rate, complexity of repair, size, weight, and installation characteristics.
Any parts that require maintenance should be easily accessible. High-failure-rate components and emergency switches that require frequent maintenance should be provided with optimal accessibility.
(2) Products, particularly consumable parts, frequently disassembled components, and additional equipment, should be easy to assemble and disassemble.
The path for parts to move in and out during disassembly and assembly should ideally be a straight line or a gentle curve.
(3) Maintenance points of the product, such as inspection points and test points, should be located in easily accessible locations.
(4) Products that require maintenance and disassembly should have adequate operational space around them.
(5) During maintenance, operators should generally be able to view the internal operations. Besides accommodating the hand or arm of the maintenance personnel, the passage should also leave an appropriate gap for observation.
The design of a product should not only satisfy its functional needs but also consider its aesthetic value, making it appealing to users. Simply put, a product should be both useful and attractive. Psychologically, 60% of human decisions are based on first impressions.
Given that technical products are commodities in a buyer’s market, designing an appealing exterior is a crucial design requirement. Moreover, aesthetically pleasing products can help operators reduce errors caused by fatigue.
Design aesthetics encompass three aspects: form, color, and surface treatment.
When considering form, attention should be paid to harmonious size proportions, simple and unified shapes, and the enhancement and embellishment provided by colors and patterns.
Monochrome is only suitable for small components. Large, particularly moving parts, will appear monotonous and flat if only one color is used. A small addition of a contrasting color can enliven the overall color scheme.
In multi-color situations, there should be a dominant base color, with the corresponding color known as the contrast color.
However, the number of different colors on a single product should not be excessive, as too many colors can give an impression of superficiality.
Comfortable colors are generally located in the range from light yellow and yellow-green to brown. This trend is towards warmer colors, with bright yellow and green often appearing uncomfortable; strong gray tones can seem oppressive.
Warm colors such as yellow, orange-yellow, and red should be used for cold environments, while cool colors like light blue should be used for hot environments.
All colors should be muted. In addition, a specific color configuration can make the product appear safe and sturdy.
Areas with minimal shape changes and larger surfaces should be configured in light colors, while components with moving, active contours should be configured in dark colors. Dark colors should be placed at the lower part of the machinery, and light colors at the top.
Design should simplify both the product and the maintenance tasks:
(1) During design, a cost-benefit analysis should be performed on product functionalities.
Merge similar or identical functionalities, remove unnecessary ones to simplify both the product and the maintenance tasks.
(2) The design should aim for simplicity in structure while meeting the specified functional requirements.
The number of hierarchical layers and components should be minimized, and the shape of the parts simplified as much as possible.
(3) Products should be designed with easy-to-use yet reliable adjustment mechanisms to troubleshoot common issues caused by wear or drift.
For parts that are expensive and prone to localized wear, design them as adjustable or removable assemblies for easy partial replacement or repair. Avoid or minimize the need for iterative adjustments due to interconnected parts.
(4) Components should be arranged logically to reduce the number of connectors and fixtures, making inspection, part replacement, and other maintenance tasks simpler and more convenient.
As much as possible, the design should allow for the repair of any component without the need to disassemble, move, or minimally disassemble or move other parts. This approach lowers the skill level and workload required of maintenance personnel.