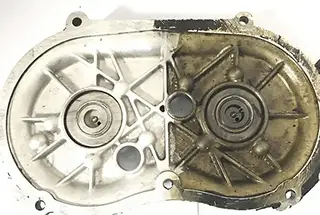
What makes metal-laser interaction so fascinating? It’s the interplay between light and metal’s charged particles that results in varying levels of reflection, absorption, and transmission. This article dives into the science behind metal-laser absorption, exploring factors such as laser wavelength, material properties, temperature, and surface conditions. Readers will learn how these elements influence energy transfer during laser processing and gain insights into optimizing laser usage for better efficiency and precision.
The reflection, absorption, and transmission of light on the material surface are essentially the result of the interaction between the electromagnetic field of light waves and the charged particles in the material. Metals have a high density of free electrons, which are forced to vibrate by the electromagnetic field of light waves, producing secondary electromagnetic waves (sub-waves).
The interference among these sub-waves and between the sub-waves and the incident waves results in strong reflected waves and relatively weak transmitted waves, which are absorbed by a thin layer of metal surface. Therefore, the metal surface often has a high reflection ratio to the laser. Especially for low-frequency infrared light, its photon energy is low, mainly affecting free electrons in the metal, reflecting strongly.
For higher-frequency visible light and ultraviolet light with larger photon energy, they can affect bound electrons in the metal. The action of bound electrons will reduce the reflectivity of metal, increase its transmissibility, and enhance the absorption of the laser by the metal.
Due to the high density of free electrons, the transmitted wave is absorbed within a very thin surface layer of metal. Measurements from ultraviolet light with a wavelength of 0.25μm to infrared light with a wavelength of 10.6μm show that the penetration depth of light in various metals is only 0.01~0.1μm.
As explained above, the penetration depth equals the reciprocal of the linear absorption coefficient, so the linear absorption coefficient of metal to light waves is large, between 105~106 cm-1.
After absorbing the laser, the material converts light energy into heat energy by exciting the resonance of charged particles and collisions between particles. The entire process is completed in a very short time. The overall energy relaxation time for metals is typically 10-13s. For general laser processing, it is believed that the conversion of absorbed laser into heat energy is instantaneously completed.
In that instant, the heat is confined to the laser irradiation area of the material. Subsequent heat conduction transfers the heat from high temperature areas to lower temperature ones.
The absorption of laser by metal is related to a series of factors such as laser wavelength, material properties, temperature, surface condition, and polarization characteristics.
Generally speaking, the longer the laser wavelength, the higher the reflection ratio, and the lower the absorption ratio.
Figure 1-2 shows the relationship between the reflection ratio R of commonly used metals at room temperature and the wavelength. In the infrared region, the absorption ratio A is approximately proportional to (ρ/λ)1/2, where ρ is the resistivity of the material and λ is the wavelength. As the wavelength increases, the absorption ratio A decreases, and the reflection ratio R increases.
The absorption ratio A of various metals at different laser wavelengths at 20℃ is shown in Table 1-1.
As can be seen from Table 1-1, at room temperature, the absorption ratio of the 10.6μm wavelength infrared laser on the metal surface is almost an order of magnitude smaller than that of visible light (the laser wavelengths in the table are 500nm and 700nm), and the absorption ratio of the 1.06μm YAG infrared laser is significantly larger than that of the CO2 laser.
Table 1-1: Absorption Ratios of Various Metals at Different Laser Wavelengths at 20℃
Materials | Argon Ion | Ruby | YAG | CO2 |
Wavelength | 500nm | 700nm | 1.06μm | 10.6μm |
Aluminum | 0.09 | 0.11 | 0.08 | 0.019 |
Copper | 0.56 | 0.17 | 0.1 | 0.015 |
Gold | 0.58 | 0.07 | — | 0.017 |
Iridium | 0.36 | 0.3 | 0.22 | — |
Iron | 0.68 | 0.64 | — | 0.035 |
Lead | 0.38 | 0.35 | 0.16 | 0.045 |
Molybdenum | 0.48 | 0.48 | 0.4 | 0.027 |
Nickel | 0.4 | 0.32 | 0.26 | 0.03 |
Niobium | 0.58 | 0.5 | 0.32 | 0.036 |
Platinum | 0.21 | 0.15 | 0.11 | 0.036 |
Nickel | 0.47 | 0.44 | 0.28 | — |
Silver | 0.05 | 0.04 | 0.04 | 0.014 |
Tantalum | 0.65 | 0.5 | 0.18 | 0.044 |
Tin | 0.2 | 0.18 | 0.19 | 0.034 |
Titanium | 0.48 | 0.45 | 0.42 | 0.08 |
Tungsten | 0.55 | 0.5 | 0.41 | 0.026 |
Zinc | — | — | 0.16 | 0.027 |
As shown in Figure 1-2, in the visible light region and its adjacent areas, different metals exhibit complex variations in reflectance. However, in the infrared range where λ>2μm, the order of reflectance for metals is: Silver > Copper > Aluminum > Nickel > Carbon Steel, which indicates that the better the material’s conductivity, the higher its reflectance to infrared radiation.
This rule can be explained by the mechanism of how these metals absorb laser: in this infrared band, the photon energy is low and can only couple with the free electrons in the metal. The lower the resistivity of the metal, the greater the density of free electrons. The forced vibration of free electrons produces stronger reflected waves, resulting in a higher reflectance ratio.
Calculations show that there is an approximate relationship between the absorption ratio and the metal resistivity as follows:
In the formula:
A represents the absorption ratio of the metal to the laser;
ρ is the resistivity of the metal material at the time of measurement (Ω·cm);
λ is the wavelength of the laser (cm).
This relationship has been confirmed by tests on different polished metal surfaces.
The resistivity of the metal increases with the rise in temperature, which shows that:
In the equation:
ρ20 is the resistivity of the metal material at 20℃ (Ω·cm);
γ is the temperature coefficient of resistance (℃-1);
T is the temperature (℃).
By substituting equation (1-14) into equation (1-13), we can calculate the absorption ratio at different temperatures, which is given by:
As can be seen from equation (1-15), the absorption ratio increases with the rise in temperature. This relationship is not only applicable to solid metals, but also valid for liquid metals.
Table 1-2 lists the resistivity p20 and temperature coefficient of resistance γ for various metals at 20℃. Figure 1-3 shows the change in the absorption ratio of several metals to a 10.6μm wavelength infrared laser with temperature, calculated according to equation (1-15).
It is noted that although the temperature coefficient of resistance for low-carbon steel is not significantly different compared to aluminum and copper, its resistivity at 20℃ is much larger, making its absorption ratio not only larger in absolute value but also increases faster with temperature. However, overall, the polished surfaces of most solid metal materials have a low absorption ratio to a 10.6μm wavelength laser, none exceeding 11%.
Table 1-2: Resistivity ρ20 and Temperature Coefficient of Resistance γ for Various Metals at 20℃.
Materials | ρ20(Ω ·cm) | γ(℃-1) | Materials | ρ20(Ω·cm) | γ(℃-1) |
Aluminum | 2. 82 ×10-6 | 3. 6 ×10-3 | Nickel | 7.24 ×10-6 | S. 4 ×10-3 |
Brass | 8.00×10-6 | 1.5 ×10-3 | Platinum | 1. 05 ×10-5 | 3. 7 ×10-3 |
Bronze | 8. 00 ×10-6 | 3. 5 ×10-3 | Silver | 1. 62 ×10-6 | 3.6 ×10-3 |
Copper-Nickel Alloy | 4. 90 ×10-5 | 1.0×10-5 | Alloy Steel | 1. 50 ×10-5 | 1.5×10-3 |
Copper | 1. 72 ×10-5 | 4. 0 ×10-3 | Low Carbon Steel | 1.50 ×10-5 | 3.3×10-3 |
Gold | 2. 42 ×10-6 | 3. 6×10-3 | Structural Steel | 1. 20 × 10-5 | 3. 2 ×10-3 |
Invar | 7. 80 ×10-5 | 2. 0 ×10-3 | Tantalum | 1.55×10-5 | 3.1×10-3 |
Iron | 9.80 ×10-6 | 5. 0 ×10-3 | Tin | 1. 14 × 10-6 | 4. 0 ×10-3 |
Manganese | 4. 40 ×10-6 | 1.0×10-5 | Cadmium | 5.50 ×10-5 | 5.2×10-3 |
Molybdenum | 5. 60 ×10-6 | 4. 7 ×10-3 | Zinc | 5. 92 ×10-5 | 3.5 ×10-3 |
Nichrome Alloy | 1. 00 ×10-4 | 4. 0×10-4 |
The roughness of the metal surface, the state of the oxide film, and the presence of special surface coatings can significantly affect the absorption ratio of infrared lasers.
The absorption ratios in Table 1-1 were measured using smooth metal surfaces in a vacuum. However, the actual laser-heated metal surfaces, due to oxidation and contamination, have much larger absorption ratios for infrared lasers than the values in the table. The impact of surface condition on the absorption ratio of visible light is relatively small.
Table 1-3 shows the effect of the surface condition of aluminum and its alloys on the absorption ratio of CO2 lasers.
Table 1-3: Impact of the surface condition of aluminum and its alloys on the absorption ratio of CO2 lasers[6](%).
Materials | Original Surface | Electropolishing | Sandblasting | Anodizing |
Pure Aluminum | 7 | 5 | 20 | 22 |
5456 Aluminum Alloy | 5~11 | 4 | 22 | 27 |
The oxide film formed on metal materials at high temperatures significantly increases the absorption ratio. Figure 1-4 shows the relationship between the absorption ratio of a 10.6μm wavelength infrared laser on the surface of 304 stainless steel oxidized in air for 1 minute and the oxidation temperature; Figure 1-5 shows the relationship between the absorption ratio of a molybdenum surface and the same laser with the oxidation temperature and time.
Since the thickness of the oxide film is a function of the oxidation temperature and time, the absorption ratio of the laser is also affected by the oxidation temperature and time. The absorption ratio of metal materials to a 10.6μm wavelength CO2 laser increases significantly with temperature, due to two factors: increased resistivity and surface high-temperature oxidation.
Phosphates, zirconia, titanium oxide, silica, as well as carbon black, graphite, etc., are substances with high absorption ratios to CO2 lasers. Surface coatings mainly composed of these substances can significantly increase the absorption ratio of metals to infrared lasers, which has become an important measure that must be taken during laser surface heat treatment.
However, for laser welding, the increase in phosphorus, oxygen, and carbon is very harmful. They can reduce the plasticity and toughness of the weld seam, and their use should be carefully considered.
Once the incident laser is not perpendicular to the material surface, the reflection ratio and absorption ratio are related to the polarization state of the incident laser. This issue has been discussed in section 1.1.1.