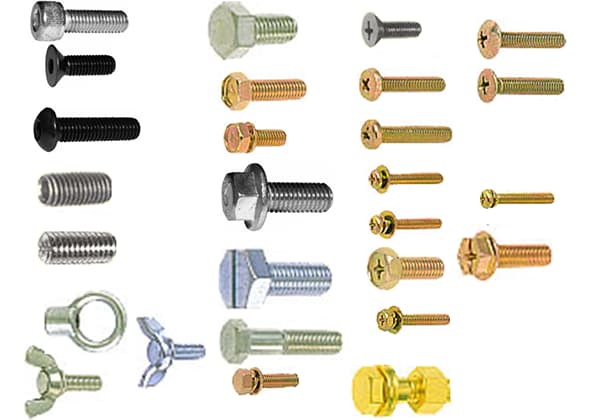
Ever wondered why your electric motor sometimes struggles to start smoothly? High starting currents can cause significant stress on your electrical system, leading to potential failures and inefficiencies. This article explores five practical methods to reduce the starting current of electric motors, including direct start, series resistance start, autotransformer start-up, star-delta reduced voltage start-up, and variable frequency drive start-up. Discover how these techniques can enhance your motor’s performance and longevity while protecting your electrical infrastructure.
Direct start is the method where the stator winding of the motor is directly connected to the power supply and started at the rated voltage. This procedure is characterized by high starting torque and short start time.
It is the simplest, most economical, and most reliable way to start. The full-voltage start draws a large current without a significant increase in starting torque. It is convenient and quick to start but requires a larger grid capacity and load. This method is mainly suitable for starting motors below 1W.
Series resistance start is a method of reducing voltage during the start process. A resistance is serially connected in the stator winding circuit during startup. As the starting current passes through, a voltage drop occurs across the resistance, reducing the voltage applied to the stator winding, thereby achieving the purpose of reducing the starting current.
Utilizing the multiple taps of an autotransformer for voltage reduction can both accommodate the start-up needs of different loads and achieve larger start-up torque. It’s a commonly used method for starting larger capacity motors.
Its greatest advantage is the substantial start-up torque. When the winding tap is at 80%, the start-up torque can reach 64% of that during direct start-up, and the start-up torque can be adjusted via the tap.
For a squirrel-cage asynchronous motor with a delta-connected stator winding under normal operation, if the stator winding is star-connected during start-up and switched back to delta after start-up, the start-up current can be reduced, mitigating its impact on the power grid. This method is known as star-delta reduced voltage start-up, or simply star-delta start-up.
With the star-delta start-up, the start-up current is only one-third of that during direct start-up with a delta connection. During star-delta start-up, the start-up current is only 2-2.3 times the original. This means that with star-delta start-up, the start-up torque also drops to one-third of that during direct start-up with a delta connection.
It is suitable for no-load or light-load start-up situations. Compared to any other voltage reduction starters, it has the simplest structure and is the most cost-effective.
Besides, the star-delta start-up method has another advantage: when the load is light, the motor can operate under a star connection. At this time, the rated torque can match the load, which can enhance the motor’s efficiency and save power consumption.
The variable frequency drive is the most technologically advanced, comprehensive, and effective motor control device in the modern motor control field. It adjusts the motor’s speed and torque by altering the frequency of the power grid.
Due to its reliance on power electronics and microcomputer technology, it is costly and requires a high skill level from maintenance technicians.
Therefore, it is mainly used in areas that require speed control and high standards for speed control.