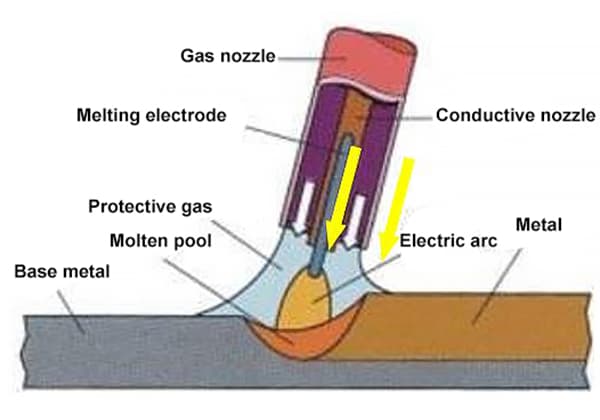
Ever wondered whether MIG or TIG welding is the better choice for your project? This article dives into the key differences, advantages, and applications of each welding method. From efficiency and cost to precision and versatility, discover how to choose the right technique for your specific needs. By the end, you’ll have a clear understanding of which welding process will ensure the best results for your work.
Tungsten Inert Gas (TIG) welding uses tungsten or tungsten alloy as the electrode material and protects the base metal and filler wire with an inert gas while melting them through the arc generated between the electrode and the base metal (workpiece). It is also known as Gas Tungsten Arc Welding (GTAW) or Tungsten Inert Gas Welding (TIG).
Shielded Arc Welding (SMAW) is a welding process that uses an electric arc to melt both the coated electrode and the base metal. The coated electrode is covered with a welding flux that melts when heated, providing several functions such as stabilizing the arc, forming slag, and deoxidizing and refining the weld.
Schematic diagram of manual arc welding with electrodes
The welding power source used for Shielded Arc Welding (SMAW) should be either an AC welding machine or a DC arc welding machine with descending characteristics.
Typically, an AC arc welding machine is used, but when more stability is needed in the arc, a DC arc welding machine may be used.
The main features of Shielded Arc Welding (SMAW) are:
Gas metal Arc Welding(GMAW)
What is MAG welding?
Metal Active Gas Welding (Active Gas)
What is MIG welding?
Metal Inert Gas Welding (Inert Gas)
Gas Metal Arc Welding (GMAW) is typically divided into two types based on the type of shielding gas used: MAG welding and MIG welding.
MAG welding uses CO2 or a mixture of CO2 and argon or oxygen (these are referred to as active gases). When only CO2 is used, it is referred to as CO2 arc welding, which is distinct from MIG welding.
In contrast, MIG welding uses inert gases such as argon or helium as the shielding gas.
The principle of Gas Metal Arc Welding (GMAW) is to generate an arc between the thin diameter consumable electrode (welding wire) and the base metal, while sealing the environment with shielding gas and melting the base metal and welding wire.
GMAW is widely used in various welding methods, including semi-automatic welding with a hand-held welding gun, robot welding, and automatic welding.
Schematic diagram of consumable electrode gas shielded welding
The features of CO2 welding are:
Characteristics of MAG welding:
In addition to the advantages of CO2 welding, it also has a clean and attractive weld seam, low spatter levels, ease of double-sided forming welding and full-penetration welding, and is ideal for high-speed welding.
Characteristics of pulsed MIG (GMAW) welding:
The MIG method is commonly used for aluminum welding and often employs pulse control. Pulse MIG welding can achieve minimal spatter through its spray transfer process. This results in a visually appealing weld and a flat weld height shape.
Compared to non-pulse MAG/MIG welding, pulse MIG welding can also use thicker wire to achieve spray transfer, improving wire feeding performance and reducing wire cost for thin plate welding.
In particular, MIG welding has advantages in automation and robotization when welding aluminum and alloys.
Principle of pulsed MIG (GMAW) welding:
In pulse MIG welding, the welding current alternates periodically between a pulse current (Ip) and a base current (Ib). This periodic alternation allows for droplet transfer across a wide range of welding current levels (as shown in the figure).
Tungsten Inert Gas (TIG) welding, also known as Gas Tungsten Arc Welding (GTAW), is a type of non-melting electrode gas shielded arc welding. It is characterized by its lack of sputtering and its ability to weld stainless steel, aluminum, iron, and other metals.
A non-consumable tungsten electrode is used and the weld is protected by an inert gas such as argon or helium. The arc is generated within the inert gas, and the base metal is melted by the arc’s heat for welding.
Due to the stability of the arc and the protection provided by the surrounding inert gas, there is minimal sputtering during TIG welding. Although filler material can be used, it is not necessary for the welding process.
The semi-automatic equipment for Tungsten Inert Gas (TIG) welding consists of a welding power supply, a welding torch, a liquefied gas cylinder, a gas flow regulator, and any necessary additional equipment, such as a water-cooled welding torch or wire welding materials.
It is important to note that the polarity of the current (positive or negative) must be selected based on the base metal, so the welding power source must be equipped with a device that allows for this selection.
Tungsten Inert Gas (TIG) welding is a welding method that involves melting and welding the base metal and any added filler material by creating an arc between the tungsten electrode and the base metal in an environment protected by an inert gas such as argon.
There are several variations of Tungsten Inert Gas (TIG) welding, which can be distinguished based on AC/DC classification, pulse, and welding wire.
DC TIG welding uses a DC arc welding power source and typically employs a negative electrode and positive base metal for welding stainless steel, titanium, copper, and copper alloys.
AC TIG welding, on the other hand, uses an AC arc welding power source and alternates the positive and negative polarities of the electrode and base metal. When the electrode is positive (EP polarity), it experiences significant overheating and consumes rapidly, which results in a cleaning effect that removes the oxide layer from the surface of the base metal. This cleaning effect is widely used in welding aluminum, magnesium, and other metals.
The choice between AC or DC for Tungsten Inert Gas (TIG) welding should be based on the type of base metal. Another variation of TIG welding is called “pulse TIG welding,” which alternates the welding current between pulse current and base current in a periodic manner.
During the use of pulse current, the base metal is melted, and during the use of base current, it is cooled. This periodic alternation allows for the formation of melting points and bead-like welds.
Classification according to output current waveform | ||
---|---|---|
Output current | Pulse | Frequency |
DC | with | Low frequency (0.5Hz to 20Hz) |
with | Medium frequency (20Hz to 500Hz) | |
with | High frequency (above 20KHz) | |
without | / | |
AC | with | Low frequency (0.5Hz to 20Hz) |
with | Medium frequency (20Hz to 500Hz) | |
without | / |
When using welding wire in Tungsten Inert Gas (TIG) welding, it can be divided into the “cold welding wire method” and the “hot welding wire method.
The cold welding wire method uses conventional welding materials. In contrast, the hot wire method heats the welding wire by applying current in advance, which results in a higher deposition rate per unit time. The hot wire method can deposit three times the amount of welding material compared to the cold wire method, making it useful for rapid welding in a short amount of time.
Although TIG welding provides high-quality welds, it can be time-consuming to achieve the necessary deposition amount. The hot wire method helps to overcome this limitation.
Classification according to the presence or absence of welding wires | |
---|---|
Welding stick | Welding wire mode |
Without | / |
With | Cold welding wire method |
Hot wire method |
The characteristics of Tungsten Inert Gas (TIG) welding, also known as Gas Tungsten Arc Welding (GTAW), include:
Metal Inert Gas (MIG) welding is a type of electric arc welding that uses an inert gas as a shield, similar to Tungsten Inert Gas (TIG) welding. However, MIG welding is a consumable electrode welding method that melts the discharge electrode.
It is commonly used for welding stainless steel and aluminum alloys and the shielding gas can vary depending on the welding material. The electrode is made of iron wire and is supplied in the form of a coil, which is installed in a welding wire supply device.
The electric motor drives a transfer roller to automatically feed the welding wire to the top of the welding torch. The welding wire is energized when it passes through a contact strip. An arc is generated between the welding wire and the base metal, allowing for welding while melting both the welding wire and the base metal. At the same time, shielding gas is supplied around the welding area through a nozzle to isolate the arc and molten materials from the atmosphere.
The semi-automatic equipment for Metal Inert Gas (MIG) welding consists of a welding power supply, a welding wire supply device, a welding torch, and a liquefied gas cylinder.
Since MIG welding is mostly used for aluminum welding, the welding wire supply device is equipped with a design that can stably supply soft aluminum wire (in 4-axis mode).
Metal Active Gas (MAG) welding can be classified based on the type of shielding gas and welding wire used.
Metal Inert Gas (MIG) welding can also be classified into AC/DC types and whether it is pulse welding.
Classification of MIG welding | ||
---|---|---|
DC | Without | Short circuit arc MIG welding |
Without | Spray MIG welding | |
Without | High current MIG welding | |
With | Pulse M1G welding | |
With | Low frequency overlapping pulse MIG method | |
AC | With | AC pulse MIG welding |
With | Low frequency overlapping AC pulse M1G welding | |
DC+AC | With | AC/DC Composite Pulse MIG Welding |
AC/DC Composite Pulse MIG Welding
Short circuit arc Metal Inert Gas (MIG) welding is a welding method that utilizes the short circuit transfer phenomenon. This method is ideal for welding thin plate materials, as it uses semi-automatic welding and generates lower heat transfer to the base metal.
Short circuit arc Metal Active Gas (MAG) welding is commonly used for welding medium-thick plates with complex structures, while pulse MIG welding is typically used for welding medium-thick plates with MIG welding.
Spray MIG welding
Spray Metal Inert Gas (MIG) welding is a welding method that sets the welding current above the critical current and increases the arc voltage. This method uses the spray transfer phenomenon to melt and atomize the welding material for bonding.
When welding aluminum without spatter, defects such as poor fusion may occur. In this case, the arc voltage can be slightly reduced and the welding can be performed in a small spray transfer state. However, with the popularity of pulse MIG welding, which can handle welding from thin plates to medium-thick plates, the use of spray MIG welding has become less common.
The high current Metal Inert Gas (MIG) welding method uses a coarse diameter welding wire (with a diameter of approximately 3.2 mm to 5.6 mm) for welding. The welding device consists of a welding torch with double shielding gas nozzles and a power supply with stable current characteristics and a rated output current of about 1000 A.
Traditional pulse MIG welding
The Direct Current (DC) and pulse Metal Inert Gas (MIG) welding method is also known as the traditional pulse MIG welding method. The basic principle is the same as pulse Metal Active Gas (MAG) welding. It is a welding method that alternates between a basic small current of the maintained arc and a pulse current above the critical current to ensure that the welding wire can be atomized even when the average current is lower than the critical current. This method can efficiently and effectively weld plates, including thin and thick plates.
Low frequency overlapping pulse welding
The Low Frequency Overlapping Pulse Welding Method is a development of pulse Metal Inert Gas (MIG) welding for high-value aluminum welding. It is used to produce a beautiful fish scale weld and is often used for welding thin aluminum plates on automobiles and motorcycles.