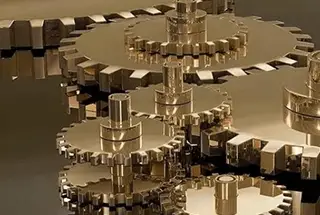
Heb je je ooit afgevraagd wat een vliegtuig veilig door de lucht laat zweven? Dit artikel verkent de fascinerende wereld van ruimtevaartmaterialen en onthult hoe ze extreme omstandigheden weerstaan en hoge prestaties garanderen. Ontdek de geheimen achter hun selectie en de ongelooflijke wetenschap die de moderne luchtvaart mogelijk maakt. Bereid je voor op het ontdekken van de cruciale factoren die onze vliegtuigen sterk, licht en betrouwbaar houden!
Lucht- en ruimtevaartmaterialen moeten bestand zijn tegen extreme mechanische spanningen, zoals hoge trek-, druk- en schuifkrachten en complexe dynamische belastingen. Deze materialen worden blootgesteld aan intense trillingen, cyclische vermoeidheid en impactkrachten tijdens het opstijgen, landen en manoeuvreren tijdens de vlucht. De snelle rotatie van turbinebladen, plotselinge atmosferische veranderingen en aerodynamische belastingen maken de mechanische eisen aan deze materialen nog hoger.
De thermische omgeving voor ruimtevaartmaterialen is al even uitdagend. Blootstelling aan hete motoruitlaatgassen en intense zonnestraling op grote hoogten creëert een omgeving met hoge temperaturen, vaak meer dan 1000°C in bepaalde onderdelen. Omgekeerd wordt bij supersonische en hypersonische snelheden aërodynamische verhitting een kritieke factor, met temperaturen die kunnen oplopen tot 2000°C of hoger bij voorranden en neuskegels.
Extreme temperaturen zijn niet beperkt tot hitte. Materialen moeten hun integriteit behouden bij cryogene temperaturen, die dalen tot ongeveer -60°C bij subsonische snelheden in de stratosfeer en dalen tot -80°C of lager in poolgebieden tijdens winteroperaties. Dit brede temperatuurbereik (-80°C tot +2000°C) vereist een uitzonderlijke thermische stabiliteit en weerstand tegen thermische schokken.
De chemische omgeving zorgt voor extra uitdagingen. Metalen onderdelen lopen het risico van spanningscorrosie en waterstofbrosheid, vooral in de aanwezigheid van stoom onder hoge temperatuur en hoge druk in motoren. Elastomeren, zoals afdichtingen en banden, moeten bestand zijn tegen scheuren door ozon en flexibel blijven bij extreme temperaturen. Brandstoffen, hydraulische vloeistoffen en ontdooimiddelen kunnen corrosie veroorzaken in metalen en degradatie of zwelling in polymeren en composieten.
Omgevingsfactoren versnellen de afbraak van materialen nog verder. Langdurige blootstelling aan UV-straling op grote hoogte kan leiden tot fotodegradatie in polymeren en composieten. Hypersonische vluchten onderwerpen materialen aan erosie door deeltjes met hoge snelheid en atomaire zuurstof in de bovenste atmosfeer. Bovendien moeten materialen bestand zijn tegen langdurige opslag in verschillende vochtigheidsgraden zonder hun prestaties of structurele integriteit aan te tasten.
Om aan deze veelzijdige uitdagingen te voldoen, vereisen ruimtevaartmaterialen een uitgekiende balans van eigenschappen, waaronder een hoge sterkte-gewichtsverhouding, uitstekende weerstand tegen vermoeiing, thermische stabiliteit, corrosiebestendigheid en stralingshardheid. Deze veeleisende werkomgeving stimuleert voortdurende innovatie in de materiaalkunde, waarbij de grenzen van legeringontwerp, composiettechniek en oppervlaktebehandelingen worden verlegd om de veiligheid en efficiëntie van ruimtevaartsystemen te garanderen.
Lucht- en ruimtevaartvoertuigen functioneren al lange tijd in de atmosfeer of de ruimte. Om hun hoge betrouwbaarheid, veiligheid en optimale vliegprestaties te garanderen, moeten ze worden ontworpen om effectief te functioneren in veeleisende omgevingen.
Om deze doelen te bereiken is het essentieel om de constructie te optimaliseren zodat deze voldoet aan aerodynamische, technologische en onderhoudseisen. Het vereist echter ook het gebruik van materialen met uitstekende eigenschappen en functies.
Tijdens het gebruik moeten constructieonderdelen verschillende soorten externe krachten aankunnen zonder het aanvaardbare vervormingsniveau te overschrijden of binnen een bepaalde tijd te breken.
Een van de ontwerpdoelen van luchtvaartconstructies is het minimaliseren van hun omvang en gewicht. In het verleden was de primaire focus gericht op de statische sterkte van de componenten, waarbij de plastische taaiheid vaak werd verwaarloosd of beperkt. Dit resulteerde in catastrofale ongelukken.
Belangrijkste structurele onderdelen van lijnvliegtuigen
Om de veiligheid van structurele onderdelen te garanderen en optimaal gebruik te maken van materiaalprestatiesHet ontwerp van constructiedelen voor de lucht- en ruimtevaart is verschoven van een "sterkte ontwerpprincipe" naar een "schadetolerantie ontwerpprincipe" en is geëvolueerd naar een "volledige levenscyclus ontwerpprincipe".
In de ontwerpfase wordt rekening gehouden met alle aspecten van de levenscyclus van een product en alle relevante factoren worden uitgebreid overwogen en geoptimaliseerd in de productontwerpfase.
Materialen moeten niet alleen een hoge specifieke sterkte en stijfheid hebben, maar ook een bepaalde breuk- en slagvastheid, weerstand tegen vermoeiing, weerstand tegen hoge en lage temperaturen, weerstand tegen corrosie, weerstand tegen veroudering en vormvastheid, evenals verbeterde prestatie-indicatoren.
Verschillende materiaalselectie criteria worden toegepast in verschillende belastingsgebieden, waarbij materialen worden gekozen op basis van de specifieke vereisten van elk onderdeel. Voor gebieden met een hoge belasting worden sterktecriteria gebruikt en worden materialen met een hoge sterkte gekozen. Voor gebieden met gemiddelde belasting worden stijfheidscriteria gebruikt en worden materialen met hoge elasticiteitsmoduli gekozen. In gebieden met lage belasting is dimensionale stabiliteit de belangrijkste overweging om ervoor te zorgen dat de onderdelen groter zijn dan de minimale kritische grootte.
Bij het selecteren en evalueren van constructiematerialen moeten geschikte testmethoden voor mechanische eigenschappen (trek, compressie, impact, vermoeidheid, impact bij lage temperatuur) worden geselecteerd op basis van de bedrijfsomstandigheden en spanningstoestanden. Er moet uitgebreid rekening worden gehouden met de sterkte, plasticiteit en taaiheid van het materiaal voor verschillende breukwijzen, waaronder ductiele breuk, brosse breuk, spanningsmoeheid, rekmoeheid en spanningscorrosie, waterstofbrosheid, verbrossing door neutronenstraling, enz.
Voor balken onder spanning moet de spanningsverdeling uniform zijn op zowel het oppervlak als de kern en het geselecteerde materiaal moet een uniforme structuur en prestatie hebben, met een goede hardbaarheid voor grote balken.
Voor staven die worden blootgesteld aan buig- en torsiebelastingen is er een groot spanningsverschil tussen het oppervlak en de kern en kunnen materialen met een lage hardbaarheid worden gebruikt.
Vermoeiingsgrens en kerfslaggevoeligheid zijn belangrijke evaluatiecriteria voor materiaalselectie voor componenten onder wisselende belastingen.
Voor onderdelen die worden blootgesteld aan corrosieve omgevingen, zijn factoren zoals corrosiebestendigheid, gevoeligheid voor waterstofbrosheid, neiging tot spanningscorrosie en corrosie vermoeiingssterkte zijn belangrijke beoordelingsindicatoren voor de materiaalselectie.
Er moet rekening worden gehouden met de stabiliteit van de structuur voor materialen die worden gebruikt voor toepassingen bij hoge temperaturen en er moet rekening worden gehouden met de prestaties bij lage temperaturen voor toepassingen bij lage temperaturen.
Gewichtsvermindering heeft praktische betekenis voor het verbeteren van de veiligheid van vliegtuigen, het vergroten van de nuttige lading en het uithoudingsvermogen, het verbeteren van de wendbaarheid en het bereik, en het verminderen van het brandstof- of drijfgasverbruik en de vliegkosten. Hoe hoger de snelheid van het vliegtuig, hoe belangrijker gewichtsvermindering wordt. Zo kan een gewichtsvermindering van een jachtvliegtuig met 15% leiden tot een vermindering van de taxiafstand met 15%, een toename van het bereik met 20% en een toename van het laadvermogen met 30%.
Voor wegwerpvliegtuigen voor de korte termijn, zoals raketten of lanceervoertuigen, is het noodzakelijk om gelijkwaardige functies te bereiken met een minimaal volume en een minimale massa, waarbij gestreefd wordt naar maximale materiaalprestaties en de kleinst mogelijke veiligheidsmarge wordt gekozen om absolute betrouwbaarheid te garanderen gedurende de hele levensduur.
Het verminderen van de structurele massa kan worden bereikt door de dichtheid te verminderen met 30%, wat meer is dan de sterkte met 50%.
Aluminiumlegeringen, titaniumlegeringen en composietmaterialen zijn de belangrijkste materialen die worden gebruikt in ruimtevaartstructuren vanwege hun hoge specifieke sterkte en stijfheid, die het laadvermogen, de wendbaarheid en het uithoudingsvermogen van vliegtuigen kunnen verbeteren en tegelijkertijd de vliegkosten kunnen verlagen.
Het gebruik van ultrasterk staal (met een treksterkte groter dan 1380 MPa) in de lucht- en ruimtevaarttechniek is beperkt tot minder dan 10%.
Voor moderne vliegtuigen, zoals supersonische gevechtsvliegtuigen, is de hoeveelheid ultrahoogsterkte staal stabiel op 5% ~ 10%, de treksterkte is 600 ~ 1850MPa, soms zo hoog als 1950mpa, en de breuktaaiheid KIc = 78 ~ 91MPa - m1 / 2.
Corrosiebestendig staal met hoge sterkte wordt meestal gebruikt voor de dragende structuur van de romp in omgevingen met actieve corrosie, terwijl koolstofvrij corrosiebestendig staal wordt gebruikt voor onderdelen in vliegtuigen die zijn uitgerust met waterstofmotoren die vloeibare waterstof en waterstofmedium gebruiken.
De belangrijkste structurele materialen die in de 21e eeuw in vliegtuigrompen worden gebruikt, zijn aluminiumlegeringen, waaronder de 2XXX-serie, 7XXXX-serie en aluminium-lithiumlegeringen. Het toevoegen van lithium aan aluminiumlegeringen kan de sterkte verbeteren en de dichtheid verminderen, waardoor de specifieke sterkte en stijfheid toenemen.
Aluminium-lithiumlegeringen zijn gebruikt in grote transportvliegtuigen, gevechtsvliegtuigen, strategische raketten, spaceshuttles en lanceervoertuigen, en worden gebruikt in onderdelen zoals kopschotten, lastdragende onderdelen, opslagtanks voor vloeibare waterstof en vloeibare zuurstof, pijpleidingen en laadadapters. Ze worden beschouwd als een veelbelovend materiaal voor de ontwikkeling van de ruimtevaart.
De derde en vierde generatie aluminium-lithiumlegeringen geven niet langer prioriteit aan een lage dichtheid en hebben betere algemene eigenschappen. Vergeleken met de derde generatie aluminium-lithiumlegeringen hebben de vierde generatie legeringen een hogere statische sterkte (vooral de vloeigrens) en breuktaaiheid, met behoud van gelijkwaardige scheurgroeisnelheid, vermoeiingsprestaties, corrosieprestaties en elasticiteitsmodulus.
Titaniumlegeringtitaanlegeringen hebben een hogere specifieke sterkte dan aluminiumlegeringen en worden gebruikt voor vliegtuigonderdelen zoals het frame, de geleiderail en beugel van de vleugelkleppen, de motorbasis, onderdelen van het landingsframe en verwarmingsonderdelen zoals de uitlaatkap en het brandscherm. Voor supersonische vliegtuigen met Mach-nummers groter dan 2,5 kan de oppervlaktetemperatuur 200 tot 350°C bereiken en kunnen titaniumlegeringen worden gebruikt als de huid.
De zeer zuivere titaanlegeringen met een hoge dichtheid, bereid door snelle stolling/poedermetallurgiemethoden, hebben een goede thermische stabiliteit en behouden hun sterkte bij 700°C, vergelijkbaar met hun sterkte bij kamertemperatuur. De ontwikkelde β-type titaanlegeringen met hoge sterkte en hoge taaiheid zijn door NASA geselecteerd als matrixmateriaal voor composietmaterialen van SiC/Ti die worden gebruikt in romp- en vleugelpanelen van vliegtuigen.
Het aandeel van titaanlegeringen in vliegtuigen neemt geleidelijk toe, waarbij 20% wordt gebruikt in rompen voor de burgerluchtvaart en 50% in rompen voor militaire vliegtuigen.
Metaalmatrixcomposieten, harsmatrixcomposieten met hoge temperatuur, keramische matrixcomposieten en koolstof/koolstofcomposieten spelen een steeds belangrijkere rol in de lucht- en ruimtevaartindustrie.
Koolstof/koolstofcomposietmaterialen combineren de vuurvaste eigenschappen van koolstof met de hoge sterkte en stijfheid van koolstofvezels. Ze hebben een uitstekende thermische stabiliteit en geleidbaarheid, evenals een hoge sterkte en taaiheid bij 2500°C met een dichtheid die slechts een vierde is van hogetemperatuurlegeringen.
Hybride composieten hebben veel aandacht gekregen, zoals het toevoegen van glasvezel aan koolstofvezelcomposieten om de impactprestaties te verbeteren of het toevoegen van koolstofvezel aan glasvezelversterkte kunststoffen om de stijfheid te verhogen.
Gelaagde composietmaterialen worden ook steeds vaker gebruikt in de ruimtevaart, zoals het 3% gebruik van GLARE, een nieuw laminaat, in de A380. Laminaat is een composietmateriaal dat wordt gemaakt door twee verschillende materialen onder druk op elkaar te stapelen.
Een laminaat bestaat meestal uit een bovenpaneel, bovenste lijmlaag, kernmateriaal, onderste lijmlaag en onderste paneel. De sterkte en stijfheid zijn hoger dan die van het afzonderlijke paneel of kernmateriaal. Het is gebruikt in transport- en gevechtsvliegtuigen.
Het GLARE laminaat wordt gevormd door het warm persen van meerdere dunne aluminium platen en unidirectionele glasvezels vooraf geïmpregneerd met epoxylijm onder druk of in een warmpers tank, zoals getoond in Figuur 1. De aluminiumplaten moet goed voorbehandeld worden om de hechting aan de vooraf geïmpregneerde vezellaag te vergemakkelijken.
Tabel 1 toont de soorten commercieel geproduceerde GLARE-laminaten die naar behoefte tot platen van verschillende dikte kunnen worden gemaakt. De vezels kunnen uit 2, 3, 4 of meer lagen bestaan en hun inhoud en richting kunnen voldoen aan de vereisten in de tabel. Elk type GLARE laminaat kan verschillende vormen hebben en kan worden aangepast om aan specifieke behoeften te voldoen.
Fig. 1 Schematisch diagram van schitterlaminaat
Tabel 1 soorten in de handel verkrijgbare glanslaminaten
Laminaat | Aluminium laag | Vezelige laag | Typische dichtheid / (g / cm 3) | ||
aluminium product | Dikte enkele laag / mm | oriëntatie | Dikte enkele laag / mm | ||
GLARE1 GLARE2 GLARE3 GLARE4 GLARE5 GLARE6 |
7475-T76 2024-T3 2024-T3 2024-T3 2024-T3 2024-T3 |
0.3~0.4 0.2~0.5 0.2~0.5 0.2~0.5 0.2~0.5 0.2~0.5 |
Eenrichtings Eenrichtings 0°/ 90° loodrecht 0°/ 90°/0° orthogonaal 0°/ 90°/90°/0° orthogonaal +45 ° / - 45 ° orthogonaal |
0.25 0.25 0.25 0.375 0.5 0.25 |
2.52 2.52 2.52 2.45 2.38 2.52 |
De verbindingstechnologie van GLARE laminaten pakt het probleem van de beperkte plaatbreedte aan. Zoals afbeelding 2 laat zien, is er een smalle naad tussen dezelfde laag aluminium platen, met verbindingen tussen verschillende lagen op verschillende posities. Deze naden kunnen worden verbonden met andere lagen aluminiumplaten door middel van vezellagen, waardoor wandplaten of de hele romphuid kunnen worden gemaakt met uitstekende weerstand tegen vermoeiing, corrosiebestendigheid en brandbestendigheid, waardoor er geen klinknagelgaten en de daaruit voortvloeiende spanningsconcentraties nodig zijn.
Om een veilige overdracht van de belasting te garanderen, kan bij de las een versterkende laag worden toegevoegd, zoals een laag metalen plaat of een laag glasvezel die vooraf met hars is geïmpregneerd.
Fig. 2 aansluitschema van glanslaminaat
Honingraat sandwich composietmaterialen bestaan uit een sandwichkern en een huid (paneel). De huid kan gemaakt zijn van aluminium of koolstof/epoxy composietmaterialen, terwijl de sandwichkern lijkt op een honingraat en bestaat uit een reeks zeshoekige, vierhoekige of anders gevormde cellen gemaakt van metaal, glasvezel of composietmaterialen. De bovenste en onderste oppervlakken van de sandwich zijn gelijmd of gesoldeerd aan de dunnere panelen.
Het kernmateriaal van aluminium honingraat sandwichcomposieten wordt gemaakt door aluminiumfolie op verschillende manieren te lijmen en honingraten van verschillende specificaties te vormen door uitrekken. De prestaties van het kernmateriaal worden voornamelijk bepaald door de dikte van de aluminiumfolie en de grootte van de cellen.
Deze materialen hebben een hoge specifieke sterkte en stijfheid, een goede slagvastheid, trillingsdemping, microgolftransmissie en een sterke ontwerpmogelijkheid. Vergeleken met geklonken constructies kan de structurele efficiëntie verhoogd worden met 15% tot 30%.
Honingraat sandwichstructuren kunnen worden gebruikt voor verschillende wandpanelen, zoals vleugeloppervlakken, cabineoppervlakken, cabinebekledingen, vloeren, motorkappen, geluiddemperplaten, warmte-isolatieplaten, satellietsteromhulsels, paraboloïde antennes, tankbodems voor raketstuwstof en nog veel meer. Maar honingraat sandwichstructuren zijn gevoelig voor corrosie in bepaalde omgevingen.
Bij een botsing zal de honingraatsandwich blijvend vervormen en loskomen van de huid.
Tabel 2 toont het percentage constructiematerialen dat wordt gebruikt in militaire vliegtuigen in de Verenigde Staten. De trend is dat het gebruik van composietmaterialen en titaniumlegeringen geleidelijk toeneemt, terwijl het gebruik van aluminiumlegeringen afneemt.
Tabel 2 percentage constructiematerialen voor Amerikaanse militaire vliegtuigen
Type | Staal | Alloy | Titaniumlegering | Gecombineerd materiaal |
F-16 | 5 | 8 | 2 | 3 |
F-18A/B | 15 | 50 | 12 | 9.5 |
F-18C/D | 16 | 50 | 13 | 10 |
F-18E/F | 14 | 31 | 21 | 23 |
F-22 | 5 | 16 | 41 | 24 |
F-35 | – | – | 27 | 36 |
F117 | 5 | 20 | 25 | 10 |
B-1 | 9 | 41 | 21 | 29 |
B2 | 6 | 19 | 26 | 38 |
C17 | 12.3 | 69.3 | 10.3 | 8.1 |
Tabel 3 toont de verdeling van materialen die worden gebruikt in typische mainline vliegtuigen. De B787 heeft 50% composietmaterialen en de A350 heeft 52% composietmaterialen. Het gebruik van composietmaterialen wordt een trend in de luchtvaartindustrie vanwege de mogelijkheid om gewicht te verminderen, schadebestendigheid te vergroten, corrosiebescherming te bieden en duurzaamheid te verbeteren.
Composietmaterialen hebben echter ook nadelen, zoals hoge kosten, beperkte slagvastheid, gebrek aan plasticiteit, verhoogde technische moeilijkheidsgraad, slechte onderhoudbaarheid en moeilijk te recyclen. Hierdoor is het gebruik van composietmaterialen in de A320neo en B737MAX niet toegenomen ten opzichte van de A320 en B737.
Tabel 3 aandeel van typische materialen voor mainline-vliegtuigen (%)
Type | Aluminiumlegering | Staal | Titaniumlegering | Gecombineerd materiaal | Andere |
B373 | 79 | 12 | 5 | 3 | 1 |
B747 | 79 | 13 | 4 | 3 | 1 |
B757 | 78 | 12 | 6 | 3 | 1 |
B767 | 80 | 14 | 2 | 3 | 1 |
B777 | 70 | 11 | 7 | 11 | 1 |
B787 | 20 | 10 | 15 | 50 | 5 |
A300 | 76 | 13 | 4 | 5 | 2 |
A310 | 74 | 8 | 5 | 6 | 7 |
A320 | 66 | 6 | 5 | 15 | 8 |
A330/A340 | 66 | 5 | 5 | 16 | 8 |
A380 | 61 | 5 | 5 | 22 | 7 |
A350 | 20 | 7 | 14 | 52 | 7 |
MD-82 | 74.5 | 12 | 6 | 7.5 | – |
MS-21 | 33 | 5 | 19 | 38 | 5 |
C919 | 63 | 8 | 8 | 21 | – |
De meeste cabinesecties van bemande ruimtevaartuigen zijn gemaakt van aluminiumlegeringen, titaniumlegeringen en composietmaterialen. De orbiters van het ruimteveer zijn bijvoorbeeld voornamelijk gemaakt van aluminiumlegeringen, terwijl de stuwkrachtstructuur die de hoofdmotor ondersteunt gemaakt is van een Qin-legering. Het hoofdframe van de middenromp is samengesteld uit een metaalmatrixcomposietmateriaal versterkt met een boriumvezelversterkte aluminiumlegering, en de deur van de laadruimte is gemaakt van een speciale papieren honingraat sandwichstructuur met grafietvezelversterkt epoxyharscomposietmateriaal als paneel.
Ablatieve materialen worden gebruikt voor de buitenkant van de raketkop, de terugkeercapsule van het ruimteschip en de binnenkant van de raketmotor. Onder invloed van warmtestroming kunnen deze materialen fysische en chemische veranderingen ondergaan, zoals ontbinding, smelten, verdamping, sublimatie en erosie. Dit resulteert in het massaconsumptie van het materiaaloppervlak, wat een grote hoeveelheid warmte wegneemt, waardoor de warmtestroom tijdens de terugkeer in de atmosfeer niet in het vliegtuig terechtkomt en de verbrandingskamer en de straalpijp van de raketmotor worden gekoeld.
Om de juiste temperatuur in de cabine te behouden, worden er stralingsbeschermende maatregelen genomen voor het terugkeergedeelte. De buitenhuid is gemaakt van een nikkelbasislegering of berylliumplaat die bestand is tegen hoge temperaturen, en de binnenstructuur is gemaakt van een hittebestendige legering. De buitenhuid en binnenstructuur zijn gevuld met materialen met goede thermische isolatie-eigenschappen, zoals kwartsvezel en glasvezelcomposietkeramiek.
Met de implementatie en voortdurende vooruitgang van ruimtevaartprojecten zoals bemande ruimtevluchten, verkenning van de maan, verkenning van de diepe ruimte, satellieten met hoge resolutie, hogesnelheidsvoertuigen, herbruikbare voertuigen en mobiele ruimtevoertuigen, worden nieuwe en veeleisendere eisen gesteld aan materialen, wat nieuwe mogelijkheden biedt en de ontwikkeling van nieuwe ruimtevaartmaterialen stimuleert.
Er zijn belangrijke doorbraken bereikt in de onafhankelijke garantie van belangrijke grondstoffen en technische toepassingen op het gebied van materialen.