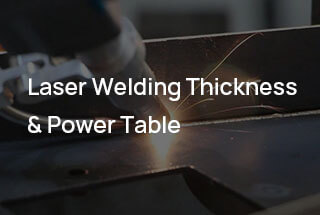
Heb je je ooit afgevraagd hoe moderne technologie een revolutie teweeg kan brengen in traditioneel lassen? Dit artikel verkent de fascinerende wereld van laserlassen en belicht de voordelen, uitdagingen en toepassingen in industrieën van lucht- en ruimtevaart tot de auto-industrie. Leer hoe deze geavanceerde technologie het lassen van aluminiumlegeringen transformeert en nauwkeurigheid en efficiëntie biedt zoals nooit tevoren.
Laserlassen biedt aanzienlijke voordelen ten opzichte van traditionele lasmethoden, zoals minimale warmte-inbreng, verminderde thermische invloed, hoge aspectratio's en geautomatiseerde procesbesturing. Deze voordelen resulteren in een betere laskwaliteit, een hogere productiviteit en een grotere precisie in metaalverbindingstoepassingen.
Aluminiumlegeringen zijn geliefd in verschillende industrieën vanwege hun uitzonderlijke eigenschappen, zoals lage dichtheid, hoge sterkte-gewichtsverhouding, uitstekende corrosiebestendigheid en superieure vervormbaarheid. Deze eigenschappen maken aluminiumlegeringen ideaal voor toepassingen in de productie van containers, machines, elektrische apparatuur, onderdelen voor de chemische industrie en ruimtevaartstructuren.
De vervanging van staal door aluminiumlegeringen in gelaste constructies kan leiden tot aanzienlijke verbeteringen in de algemene structurele prestaties en gewichtsvermindering. Echter, aluminium vormt een unieke uitdaging bij het lassen vanwege de hoge thermische geleidbaarheid, het lage ionisatiepotentiaal en de neiging om een hardnekkig aluminiumoxide (Al2O3) laag op het oppervlak. Deze oxidelaag kan de versmelting belemmeren en bijdragen aan lasdefecten zoals onvoldoende versmelting, poreusheid, insluitsels en warmscheuren, waardoor de mechanische integriteit van de lasverbinding in gevaar kan komen.
Vergeleken met conventionele booglastechnieken zoals Gas Tungsten Arc Welding (GTAW) of Gas Metal Arc Welding (GMAW), biedt laserlassen een aantal duidelijke voordelen. Deze omvatten smallere lasnaden, geminimaliseerde warmte-beïnvloede zones, minder overlapvereisten voor de lasnaad, nauwkeurige controle over de lasparameters en verbeterde automatiseringsmogelijkheden. Deze eigenschappen dragen bij aan een betere laskwaliteit, minder vervorming en een hogere productie-efficiëntie.
Momenteel wordt laserlastechnologie op grote schaal toegepast bij het verbinden van dunwandige elektronische componenten, structurele onderdelen en ruimtevaartcomponenten. Het toekomstige traject van onderzoek naar laserlassen is gericht op de ontwikkeling en implementatie van vezellasers met een hoog vermogen, met name in het bereik van 10 kW, voor diep penetratielassen van grote en dikke materialen. Deze vooruitgang zal de mogelijkheden van laserlassen uitbreiden naar meer uitdagende toepassingen in de zware industrie en grootschalige productie.
Prestaties/type | Kooldioxydelaser | NdYAG laser | YbYAG Dac-laser | Vezellaser |
---|---|---|---|---|
Golflengte / um | 10.6 | 1.06 | 1.06 | 1-2 |
Elektrisch conversierendement/% | 12-15 | 2-6 | 20 | 8-10 |
Vermogensdichtheid/(MW/cm-2) | 10 | 10 | 100 | 100 |
Maximaal vermogen/kW) | 50 | 6 | 15 | 50 |
Straalvermogen | Optische lens | Optische vezel | Optische vezel | Optische vezel |
Metaalabsorptie/% | 8 | 20 | 20 | 20 |
Onderhoudscyclus/uur | 1000 | 1000 | 1ooo | 20000 |
Laserhelderheid (103W/mm2steradian) (4kW/h) | — | 7.5 (brandpuntsafstand:200; Vezeldiameter: 0,6 mm) | 134.2 (brandpuntsafstand:200; Vezeldiameter: 0,2 mm) | 264.4 (brandpuntsafstand:160; Vezeldiameter: 0,1 mm) |
CO2-gaslaslaser
De CO2 laser gebruikt koolstofdioxidegas als actief medium en zendt uit bij een golflengte van 10,6 μm. Deze lasers worden op basis van hun excitatiestructuur onderverdeeld in kruisstroom- en axiaalstroomtypes. Hoewel CO2 lasers met kruisstroom indrukwekkende outputvermogens tot 150 kW hebben bereikt, is hun straalkwaliteit suboptimaal voor precisielastoepassingen. Daarentegen bieden axiale CO2 lasers een superieure straalkwaliteit, waardoor ze geschikt zijn voor het lassen van sterk reflecterende materialen zoals aluminiumlegeringen. De langere golflengte van CO2 lasers kan echter leiden tot verhoogde warmte beïnvloede zones en potentiële thermische vervorming in dunne materialen.
YAG vaste-stoflaser
Vastestoflasers maken gebruik van kristallijne of glazen materialen als actief medium. Gangbare types zijn robijn, neodymiumglas en neodymium-gedoopt yttriumaluminiumgranaat (Nd:YAG). Deze lasers zenden doorgaans uit bij een golflengte van 1,06 μm. YAG lasers bieden verschillende voordelen ten opzichte van CO2 lasers voor het lassen van metaal: hogere absorptie door metalen oppervlakken, minder plasma afschermingseffecten en compatibiliteit met glasvezeltransport. Deze fiberoptische mogelijkheid maakt flexibele laswerkzaamheden en een betere toegankelijkheid tot complexe geometrieën mogelijk. De kortere golflengte maakt ook kleinere brandpunten mogelijk, waardoor de vermogensdichtheid en lassnelheid kunnen toenemen. Deze eigenschappen hebben ervoor gezorgd dat YAG-lasers in veel industrieën de eerste keuze zijn voor het structurele lassen van aluminiumlegeringen.
YLR fiberlaser
YLR vezellasers zijn na 2002 ontwikkeld en betekenen een aanzienlijke vooruitgang in de lasertechnologie. Deze lasers gebruiken optische vezels die gedoteerd zijn met zeldzame aardionen als versterkingsmedium en zenden meestal uit rond 1,08 μm. De revolutionaire dubbel beklede vezelstructuur van deze lasers verbetert de pompefficiëntie en het uitgangsvermogen aanzienlijk in vergelijking met traditionele vezellasers. YLR fiber lasers bieden vele voordelen ten opzichte van YAG systemen, waaronder:
Deze eigenschappen maken YLR fiber lasers steeds populairder voor het zeer nauwkeurig lassen van aluminiumlegeringen, vooral in de ruimtevaart en de automobielindustrie waar laskwaliteit en procesbetrouwbaarheid van cruciaal belang zijn.
Aluminium en aluminiumlegeringen worden ingedeeld in zeven primaire series:
Op basis van hun verwerkingseigenschappen worden aluminiumlegeringen ingedeeld in twee hoofdcategorieën: smeedbare aluminiumlegeringen en gegoten aluminiumlegeringen. Smeedlegeringen worden verder onderverdeeld in niet-warmtebehandelbare legeringen en warmtebehandelbare legeringen.
De lasbaarheid van aluminiumlegeringen varieert aanzienlijk tussen verschillende series:
Niet-warmtebehandelbare legeringen (1000, 3000 en 5000 series) vertonen over het algemeen een goede lasbaarheid. De 4000 serie legeringen vertonen een lage gevoeligheid voor warmscheuren.
Echter, 5000 serie legeringen met een magnesiumgehalte van meer dan 2% worden gevoelig voor scheuren. Hoewel een hoger magnesiumgehalte de lasprestaties verbetert, heeft het een nadelige invloed op de vervormbaarheid en corrosiebestendigheid van de legering.
Warmtebehandelbare legeringen (2000, 6000 en 7000 series) vormen een grotere uitdaging bij het lassen. Ze zijn gevoeliger voor warmscheuren, vertonen een slechte lasparelvorming en ondervinden een aanzienlijke vermindering in sterkte door het oplossen van verhardingsprecipitaten in de warmte-beïnvloede zone (HAZ).
Om lasverbindingen van hoge kwaliteit in aluminiumlegeringen te krijgen, is het cruciaal om de juiste lastechnieken toe te passen, geschikte lasprocessen te kiezen en compatibele toevoegmaterialen te gebruiken. Voorbereiding van het lasoppervlak is essentieel en bestaat meestal uit:
Om het oppervlak schoon te houden, moet er binnen 24 uur na de voorbereiding gelast worden. Daarnaast wordt aanbevolen om lasprocedurekwalificatietests uit te voeren om de parameters te optimaliseren voor specifieke legeringcombinaties en verbindingsconfiguraties.
Sinds de jaren '90 hebben significante ontwikkelingen in lasertechnologie, met name de ontwikkeling van lasers met hoog vermogen en hoge helderheid, het laserlassen naar nieuwe hoogten gestuwd op het gebied van integratie, intelligentie, flexibiliteit en veelzijdigheid. Deze ontwikkeling heeft geleid tot een toegenomen interesse in het toepassen van laserlassen op constructies van aluminiumlegeringen in verschillende industrieën wereldwijd.
In de automobielsector hebben verschillende Chinese fabrikanten al laserlastechnologie toegepast in hun nieuwste modellen. Aangezien het vermogen om dikke platen van aluminiumlegeringen te laserlassen steeds beter wordt, is deze technologie klaar voor toekomstige toepassing in gepantserde voertuigstructuren, wat potentiële voordelen biedt op het gebied van sterkte-gewichtsverhouding en productie-efficiëntie.
Het streven naar lichtgewicht productie heeft laserlassen van sandwichstructuren van aluminiumlegeringen tot een belangrijk onderzoeksgebied gemaakt voor de scheepsbouw en de hogesnelheidsspoorwegindustrie. Deze composietstructuren bieden een optimale balans tussen sterkte, gewichtsvermindering en thermisch beheer, wat cruciaal is voor het verbeteren van de prestaties en energie-efficiëntie in scheeps- en spoorwegtoepassingen.
Aluminiumlegeringen blijven van cruciaal belang in luchtvaartconstructies, waardoor technologisch geavanceerde landen zoals Japan, de Verenigde Staten, het Verenigd Koninkrijk en Duitsland intensief onderzoek doen naar laserlastechnieken. De focus is verschoven naar fiber laserlassen en laser-boog hybride lassen, met name voor het verbinden van dikke platen en het lassen van ongelijksoortige metalen, omdat deze methoden een superieure laskwaliteit, diepere inbranding en minder warmte-beïnvloede zones bieden.
De evolutie van de fiberlasertechnologie heeft ervoor gezorgd dat fiberlaserlassen en laser-boog hybride lassen een vooraanstaande rol spelen bij het verbinden van aluminiumlegeringen in de geavanceerde luchtvaartindustrie. Deze technieken blinken uit in precisie, snelheid en de mogelijkheid om complexe geometrieën te lassen, waardoor ze ideaal zijn voor ruimtevaarttoepassingen. Een goed voorbeeld is het Amerikaanse NALI-project (National Aerospace Leadership Initiative), dat geavanceerd onderzoek uitvoert naar fiberlaser- en laserbooghybride lassen voor verbrandingskamerstructuren in zowel commerciële vliegtuigen als motoren van Joint Strike Fighter (JSF).
Dit voortdurende onderzoek en de toepassing van geavanceerde laserlastechnieken voor aluminiumlegeringen zorgen voor innovaties op het gebied van structureel ontwerp, productieprocessen en materiaalprestaties in verschillende hightechindustrieën, waardoor de weg wordt vrijgemaakt voor lichtere, sterkere en efficiëntere producten in de auto-, defensie-, scheepvaart-, spoorweg- en ruimtevaartsector.
Laserlassen van aluminiumlegeringen biedt aanzienlijke voordelen ten opzichte van conventionele fusielastechnieken, zoals een zeer gerichte warmte-inbreng, superieure lasdiepte-breedteverhoudingen en minimale structurele vervorming. Dit geavanceerde proces brengt echter ook unieke uitdagingen met zich mee:
Concluderend, hoewel laserlassen overtuigende voordelen biedt voor het verbinden van aluminiumlegeringen, vereist het realiseren van het volledige potentieel het aanpakken van deze inherente uitdagingen. De primaire focus bij het bevorderen van deze technologie ligt in het ontwikkelen van strategieën om lasdefecten te verminderen, de eigenschappen van de verbinding te verbeteren en de processtabiliteit te verhogen door nauwkeurige controle van de lasparameters, innovatieve verbindingsontwerpen en mogelijk de integratie van real-time bewakings- en adaptieve regelsystemen.
Laserlassen maakt gebruik van de laser als een lichtbron met hoge dichtheid die een snelle verwarming en onmiddellijke stolling biedt, met een aspectratio van wel 12:1. Echter, door de hoge reflectiviteit en goede thermische geleidbaarheid van aluminiumlegeringen, evenals het afschermingseffect van plasma, zullen er waarschijnlijk defecten optreden tijdens het lasproces.
De twee belangrijkste defecten zijn poriën en thermische scheuren. De uitdaging bij het laserlassen van aluminiumlegeringen is het effectief verbeteren van de absorptie van laserlicht door het materiaal vanwege de sterke reflectie.
De laserlasproces voor aluminiumlegeringen is complexer en het is cruciaal om deze te verbeteren en te verfijnen vanwege de eigenschappen van de aluminiumlegering zelf.
Hoe hoger de absorptiesnelheid van het materiaal van de laser, of hoe lager de warmteoverdrachtscoëfficiënt en temperatuurgeleidingscoëfficiënt, hoe gemakkelijker de laserenergie wordt geabsorbeerd door het oppervlak van het materiaal, wat leidt tot een snelle stijging van de oppervlaktetemperatuur en het smelten of verdampen van het materiaal.
Tabel 1 toont de reflectie van verschillende metalen op lasers met verschillende golflengten.
Tabel 1 De reflectie van metalen op lasers van verschillende golflengten bij kamertemperatuur (%)
λ/μm | Ag | Al | Cu | Cr | Ni | Staal |
---|---|---|---|---|---|---|
0.7 | 95 | 77 | 82 | 56 | 68 | 58 |
1.06 | 97 | 80 | 91 | 58 | 75 | 63 |
10.6 | 99 | 98 | 98 | 93 | 95 | 93 |
De reflectie van verschillende metalen neemt af naarmate de golflengte korter wordt, waarbij de reflectiviteit van Ag, Al en Cu voor laserlicht kan oplopen tot 90% of meer. Dit verhoogt de moeilijkheidsgraad van laserbewerking.
Bij kamertemperatuur is de absorptiesnelheid van CO2 lasers door aluminiumlegeringen is erg laag: 98% van de laserenergie wordt gereflecteerd door het oppervlak van de aluminiumlegering. De reflectiviteit van Nd:YAG lasers is ook tot 80%.
Het is duidelijk dat aluminiumlegeringen een hoge reflectiviteit hebben voor laserlicht en een lage absorptiesnelheid, vanwege hun hoge dichtheid aan vrije elektronen. De sterke trilling van elektromagnetische lichtgolven resulteert in de generatie van sterke gereflecteerde golven en zwakkere uitgezonden golven. De gereflecteerde golven worden niet gemakkelijk geabsorbeerd door het oppervlak van de aluminiumlegering, wat leidt tot de hoge reflectiviteit voor lasers bij kamertemperatuur.
In de laserlasproceswanneer de laserenergiedichtheid groter is dan 3,5 * 106W/cm2worden ionen gegenereerd. Deze lasmethode wordt uitgevoerd door middel van diep penetratielassen en is gebaseerd op het "kleine gaatjes" effect. De aanwezigheid van "kleine gaatjes" verhoogt de absorptiesnelheid van het materiaal door de laser aanzienlijk en resulteert in een goed laseffect door het lasmetaal te smelten met een hoge energiedichtheid.
De grootste uitdaging bij het laserlassen van aluminiumlegeringen is het induceren en behouden van de stabiliteit van kleine gaatjes, wat te wijten is aan zowel de materiaaleigenschappen van aluminiumlegeringen en de optische eigenschappen van de laserstraal. Zoals eerder vermeld, reflecteert aluminium 80% energie bij kamertemperatuur en heeft het een goede thermische geleidbaarheid, waardoor een grote drempelwaarde voor de laserenergiedichtheid nodig is om "kleine gaatjes" te produceren.
Zodra het ingangsvermogen deze waarde overschrijdt, wordt de overdracht van laserenergie in het materiaal niet langer beperkt door warmtegeleiding en wordt het lassen uitgevoerd door middel van diepe penetratie. De laserstraling veroorzaakt een sterke verdamping van het basismetaal en vormt een verdampingsgroef. De laserstraal dringt door deze groef in het materiaal, waardoor zowel de lasdiepte als het rendement sterk toenemen.
Voor sterk reflecterende materialen, zoals aluminiumlegeringen en koperlegeringen, is een grote vermogensdichtheid vereist tijdens het lassen. Dit stelt bepaalde eisen aan de keuze van lasmodellen en collimatie- en focuslenzen.
Verfijning versterken, vaste oplossing versterken en verouderingsneerslag versterken zijn drie verschillende manieren om aluminiumlegeringen te versterken. Ondanks deze mechanismen zorgt de grote hoeveelheid verdamping van legeringselementen met een laag smeltpunt, zoals Mg en Zn, tijdens het laserlassen ervoor dat de las zinkt en vermindert zijn hardheid en sterkte.
Tijdens het snelle stolproces resulteert de transformatie van de fijnkorrelige versterkte structuur in een as-gietstructuur in een afname van de hardheid en sterkte. Bovendien vermindert de aanwezigheid van scheuren en poriën in de las de treksterkte.
Concluderend kan worden gesteld dat verweking van de verbinding een andere uitdaging is bij het laserlassen van aluminiumlegeringen.
Er zijn twee primaire soorten poriën in het laserlasproces van aluminiumlegeringen: waterstofgasporiën en instortporiën.
(1) Waterstofporiën: Aluminiumlegeringen vormen bij hoge temperaturen een oxidelaag op hun oppervlak, die gemakkelijk vocht uit de omgeving absorbeert. Bij verhitting door een laser valt water uiteen in waterstof en de oplosbaarheid van waterstof in vloeibaar aluminium is ongeveer 20 keer groter dan in vast aluminium. Tijdens het snelle stollen van de legering neemt de oplosbaarheid van waterstof drastisch af wanneer het verandert van vloeibaar aluminium naar een vaste toestand. Als het teveel aan waterstof in het vloeibare aluminium niet gelijkmatig stijgt en overloopt, zal het waterstofporiën vormen. Deze poriën zijn over het algemeen regelmatig van vorm en groter dan dendrieten en de stolpatronen van dendrieten zijn te zien op het binnenoppervlak.
(2) Instorting van het sleutelgat: Het lasgat is in evenwicht met zijn eigen zwaartekracht en atmosferische druk. Als dit evenwicht eenmaal is verstoord, kan het vloeibare metaal in het smeltbad niet op tijd overvloeien en vullen, wat resulteert in onregelmatige gaten. Uit onderzoek is gebleken dat het magnesiumgehalte van de binnenwand van het gat ongeveer 4 keer zo hoog is als dat van de omgeving van de lasnaad. Omdat de koelsnelheid van laserlassen te snel is, is het probleem van waterstofgasporiën ernstiger en zijn er meer gaten veroorzaakt door het instorten van kleine gaten bij laserlassen.
Aluminiumlegering is een veel voorkomende eutectische legering die gevoelig is voor hete scheuren tijdens het lassen, inclusief laskristallisatiescheuren en HAZ (Heat Affected Zone) liquefactiescheuren. In het algemeen verschijnen kristallisatiescheuren in de laszone terwijl liquefactiescheuren in de buurt van de lasnaad verschijnen. Van de aluminiumlegeringen zijn de 6000 serie Al-Mg-Si legeringen bijzonder gevoelig voor scheuren.
Het basismetaal wordt onderworpen aan snelle verwarming en koeling, wat kan leiden tot het instantane stollings- en kristallisatieproces. De grote mate van onderkoeling tijdens dit proces zorgt ervoor dat de kristalkorrels loodrecht op het midden van de las groeien, waardoor eutectische verbindingen met een laag smeltpunt worden gevormd, zoals Al-Si of Mg-Si, Al-Mg2Si en andere. Dit verzwakt de bindingskracht van het kristalvlak, waardoor het vatbaarder wordt voor kristalscheuren onder thermische spanning.
In de aluminium lassen van legeringen proces worden elementen met een laag kookpunt, zoals Mg, Zn, Mn en Si, gemakkelijk verdampt en verbrand. Hoe lager de lassnelheid, hoe ernstiger de verbranding, waardoor de chemische samenstelling van het lasmetaal verandert. Door de segregatie van de componenten in de laszone treden eutectische segregatie en smelten van de korrelgrens op, wat leidt tot vloeibaarheidsscheuren op de korrelgrens onder spanning, waardoor de prestaties van de lasverbinding afnemen.
Om succesvol laserlassen van aluminiumlegeringen te bereiken en de eerder genoemde problemen aan te pakken, worden vaak verschillende benaderingen gebruikt.
Een van de belangrijkste factoren die het verlies van elementen met een laag smeltpunt in aluminiumlegeringen tijdens het lassen beïnvloedt, is de druk van het gas dat uit het mondstuk komt. Om dit probleem te verminderen kan de diameter van het mondstuk worden verkleind en kunnen de gasdruk en het debiet worden verhoogd. Dit zal het verbrandingsverlies van elementen zoals Mg en Zn tijdens het lasproces verminderen en ook de penetratie verhogen.
Er zijn twee blaasmethoden beschikbaar: direct blazen en zijdelings blazen. Daarnaast is het mogelijk om tegelijkertijd naar boven en naar beneden te blazen. De keuze van de blaasmethode moet worden bepaald op basis van de specifieke omstandigheden tijdens het lassen.
Aluminiumlegering reageert sterk op laserenergie. Goede voorbereiding van het oppervlak van de aluminiumlegering, zoals anodische oxidatie, elektrolytisch polijstenzandstralen enz. kan de energieabsorptie van de straal op het oppervlak sterk verbeteren.
Onderzoek heeft aangetoond dat het verwijderen van de oxidelaag van aluminiumlegeringen de neiging tot kristallisatiescheuren vergroot. Om beschadiging van het oppervlak van de aluminiumlegering te voorkomen en tegelijkertijd het laserlasproces te vereenvoudigen, kan de oppervlaktetemperatuur van het werkstuk voor het lassen worden verhoogd, waardoor het materiaal de laser beter absorbeert.
Laserlassen wordt onderverdeeld in twee categorieën: gepulseerde lasers en continue lasers. Gepulseerde lasers met een golflengte van 1064 nm hebben een sterk geconcentreerde laserstraal en de pulsenergie is groter dan die van continue lasers. De energie van gepulseerde lasers is over het algemeen echter beperkt, waardoor ze geschikter zijn voor het lassen van dunwandige materialen.
Lassen met pulsmodus
Bij het uitvoeren van laserlassen is het belangrijk om de juiste lasgolfvorm te kiezen. Gangbare pulsvormen zijn blokgolf, piekgolf en dubbele piekgolf. Pulsgolven duren meestal milliseconden. Tijdens een laserpuls verandert het reflectievermogen van het metaal dramatisch. Aluminiumlegeringen hebben een hoge reflectiviteit voor licht, wat betekent dat 60-98% van de laserenergie die het materiaaloppervlak raakt, verloren kan gaan door reflectie. Deze reflectiviteit verandert met de oppervlaktetemperatuur.
Scherpe golf en dubbele piekgolf zijn de beste opties voor het lassen van aluminiumlegeringen, omdat de stijgende fase van de golfvorm meer energie levert om de aluminiumlegering te smelten. Als er eenmaal een "klein gat" in het werkstuk is gevormd, neemt de absorptiesnelheid van het vloeibare metaal naar de laser snel toe bij diep penetratielassen. Op dit punt is het belangrijk om de laserenergie snel te verminderen en het lassen uit te voeren op een laag vermogen om spatten te voorkomen.
Het vertragende deel van de lasgolfvorm heeft een langere pulsbreedte, wat de vorming van poriën en scheuren effectief vermindert. Deze golfvorm zorgt ervoor dat de las herhaaldelijk wordt gesmolten en gestold, waardoor het smeltbad minder snel stolt. De golfvorm kan naar behoefte worden aangepast bij het lassen van verschillende soorten monsters.
Figuur 1 Impulsgolfvorm van het lassen van aluminiumlegering
De juiste hoeveelheid selecteren defocus kan ook de vorming van poriën minimaliseren. De verandering in defocus heeft een significante invloed op de vorming van het lasoppervlak en de inbranding. Negatieve defocus kan de penetratie verhogen, terwijl positieve defocus bij pulslassen het lasoppervlak gladder en visueel aantrekkelijker kan maken.
Vanwege de hoge reflectie van aluminiumlegeringen op laserenergie, wordt de laskop meestal onder een hoek geplaatst om te voorkomen dat de laserstraal verticaal wordt gereflecteerd en de laserstraal beschadigt. laserfocus lens. De diameter van de soldeerverbinding en het effectieve bindingsoppervlak nemen toe naarmate de kantelhoek van de laser toeneemt. De grootste soldeerverbinding en het grootste effectieve bindingsoppervlak worden bereikt bij een kantelhoek van de laser van 40°. De laspuntpenetratie en effectieve laspuntpenetratie nemen echter af met de toename van de kantelhoek van de laser en bij meer dan 60° neemt de effectieve laspuntpenetratie af met de toename van de kantelhoek van de laser. laspenetratie afneemt tot nul. Door de laskop onder een bepaalde hoek te kantelen, kunnen de inbranddiepte en de breedte van de lasnaad toenemen.
Daarnaast is het belangrijk op te merken dat hoe hoger de lassnelheid, hoe groter het risico op scheurvorming. Dit komt doordat een hoge lassnelheid leidt tot een grote mate van onderkoeling, waardoor de korrels in de laszone worden verfijnd en er een groot aantal "balkkristallen" in dezelfde richting groeit, waardoor de kans op scheurvorming op het kristalvlak tussen deze balkkristallen toeneemt. Als de lassnelheid te hoog is, zal de inbranddiepte van de las relatief ondiep zijn.
Lassen met continue modus
Traditioneel laserlassen kan leiden tot verbrossing of scheuren. Daarentegen heeft continu laserlassen niet hetzelfde plotselinge koel- en verwarmingsproces als puls laserlassen, wat leidt tot minder scheuren tijdens het lasproces. Bovendien resulteert fiber laserlassen van de meeste aluminiumlegeringen in een verbeterde taaiheid na het lassen en vermindert het de kans op brosheid.
Gepulseerd laserlassen is geschikt voor het lassen van industrieel zuiver aluminium, met weinig risico op scheuren na het lassen. Sommige industrieën vereisen echter het polijsten van het oppervlak na het lassen, en gepulst laserlassen kan deuken veroorzaken en de vereiste hoeveelheid polijsten verhogen, wat leidt tot een langere verwerkingstijd en hogere productiekosten. Continue lasers kunnen deze problemen oplossen.
Zoals getoond in afbeelding 2 toont de vergelijking van de lasnaad van de batterijshell na pulslaserlassen en continu laserlassen de voordelen van continu laserlassen aan. De impulssoldeerverbindingen zijn ongelijkmatig en hebben ondergesneden en ingedeukte oppervlakken, met veel spatten en een lagere sterkte na het lassen. Daarentegen resulteert continu laserlassen in een glad en uniform lasnaad oppervlak, vrij van defecten en spatten, zonder scheuren in de lasnaad.
Figuur 2 Impuls en continu lassen van Al-Mn legering
Boogkraters komen vaak voor tijdens argon booglassenen hetzelfde kan gebeuren tijdens het laserlassen. Om het verschijnen van kleine kraters te minimaliseren, kan een langzame stijging en langzame daling worden ingesteld in de golfvorm tijdens het lassen en kan de lassnelheid indien nodig worden verhoogd.
Continu laserlassen heeft talloze voordelen bij het lassen van aluminiumlegeringen. Vergeleken met traditioneel lasmethodencontinu laserlassen is efficiënter en maakt draadvulling overbodig. In vergelijking met puls laserlassen, elimineert continu laserlassen defecten zoals scheuren, poriën en spatten en zorgt ervoor dat de aluminiumlegering goede mechanische eigenschappen heeft na het lassen. Bovendien ontstaan er geen deuken na het lassen en is er minder polijst- en slijpwerk nodig, waardoor op productiekosten wordt bespaard.
Het is echter belangrijk op te merken dat continue lasers een relatief kleine spotgrootte hebben, zodat de montagenauwkeurigheid van het werkstuk hoog moet zijn.
Het voorkomen van thermische scheuren is een kritieke technologie voor het laserlassen van aluminiumlegeringen, vooral voor de 6000 serie legeringen die zeer gevoelig zijn voor scheuren. Als het gehalte ω(Mg2Si) 1% bereikt, is de kans op warmscheuren groot. Om het risico op scheuren te verminderen, kunnen geschikte legeringselementen worden toegevoegd om de chemische samenstelling van het smeltbad aan te passen, zoals het toevoegen van Al-Si of Al-Mg-Si poeder.
Bovendien kan draadtoevoer het laseffect verbeteren en een uniforme lasnaad met verbeterde hardheid produceren. De introductie van vulmateriaal verhoogt het gehalte aan Mg en Si in de dendriet in de fusiezonewat leidt tot een toename van de sterkte van de verbinding door het versterkende effect van de β" vaste oplossing.
Gewoonlijk worden 6063 en 6082 aluminiumlegeringen gevuld met Al-5Si en Al-7Si lasdraden, terwijl 6013 en 6056 platen worden gelast met CO2 en Nd: YAG lasers, respectievelijk, en gevuld met Al-12Si lasdraden.
Streven naar stabiliteit en kwaliteit bij het laserlassen van aluminiumlegeringen.
De huidige onderzoeksfocus bij het laserlassen van aluminiumlegeringen is het gebruik van een samengesteld proces dat de hoge energiedichtheid van laserstralen combineert met het bredere verwarmingsbereik van vlambogen, waarbij gebruik wordt gemaakt van de sterke punten van beide warmtebronnen en hun kenmerken van hoge energiedichtheid en stabiele vlambogen worden verbeterd.
Voor materialen met een hoge reflectiviteit, zoals aluminiumlegeringen, kan hybride laserlassen het materiaaloppervlak voorverwarmen of smelten met behulp van boog-energie, waardoor de absorptie van laserenergie door de aluminiumlegering aanzienlijk wordt verbeterd.
Shida et al. gebruikten met succes een 10 kW CO2 laser in combinatie met TIG en MIG bogen om aluminium lassen legeringen. De introductie van bogen verbeterde het gebruik van laserenergie en verhoogde de laspenetratie met 5-20%. Het resultaat was een glad, goed gevormd lasoppervlak.
Laserhybride lassen vergroot de grootte van het smeltbad en wijzigt de materiaalstroomcondities in de gesmolten toestand door de koppeling van laserstralen en bogen, wat gunstig is voor het elimineren van poriën.
Het elimineren van luchtgaten bij het lassen van aluminiumlegeringen kan ook worden bereikt door dubbelstraallassen. Een 6 kW continue fiberlaser werd gebruikt voor dubbelstraallassen. stomplassen van aluminiumlegering 5052 en de effecten van parallel en serieel lassen met twee bundels en verschillende lassnelheden op de naadmorfologie en -structuur werden bestudeerd. Uit het onderzoek bleek dat parallel lassen met twee bundels resulteerde in grote gaten in de lassen, terwijl serieel lassen van aluminiumlegeringen een goede lasvorming zonder poriën opleverde.
Onder invloed van lasers met hoog vermogen zijn de belangrijkste defecten bij laserdiep penetratielassen van aluminiumlegeringen porositeit, oppervlakteverzakking en ondersnijding. Oppervlakteverzakking en ondersnijding kunnen worden verbeterd door laserdraadvullassen of laserbooghybridelassen. Het onder controle houden van porositeitsdefecten is echter een uitdaging.
Onderzoek heeft aangetoond dat er twee soorten karakteristieke poriën zijn bij laserdiep penetratielassen van aluminiumlegeringen. Het ene type is metallurgische porositeit, veroorzaakt door materiaalvervuiling of luchtinsijpeling tijdens het lasproces, vergelijkbaar met boogfusielassen. Het andere type is procesporositeit, die wordt veroorzaakt door de onstabiele fluctuatie van kleine gaatjes die inherent is aan het laserdiep penetratielassen.
Tijdens het laserdiep penetratielassen loopt het kleine gat vaak achter op de straalbeweging door de viscositeit van het vloeibare metaal en fluctueren de diameter en diepte onder invloed van plasma/metaaldamp. Als de straal beweegt en het gesmolten metaal stroomt, wordt onvolledig diep penetratielassen gesloten door de stroming van het gesmolten metaal, waardoor er bellen verschijnen aan het uiteinde van het kleine gat. Bij diep penetratielassen met volledige penetratie verschijnen er belletjes in de taille van het kleine gat in het midden.
Deze bellen migreren en rollen met de stroom vloeibaar metaal mee, ontsnappen uit het smeltbadoppervlak of worden teruggeduwd in het kleine gat. Als de bellen door het smeltbad worden gestold en door het metaalfront worden gevangen, worden het lasporiën.
Metallurgische poriën kunnen worden beheerst door oppervlaktebehandeling vóór het lassen en de juiste gasbescherming tijdens het lasproces. De sleutel tot het beheersen van procesporiën is het waarborgen van stabiliteit tijdens het laser dieptedoorsteeklasproces.
Volgens onderzoek naar binnenlandse laserlastechnologie vereist het beheersen van luchtgaten in laserdiep penetratielassen van aluminiumlegeringen aandacht voor alle schakels, inclusief vóór het lassen, het lasproces en de behandeling na het lassen. Dit kan worden bereikt door middel van de volgende nieuwe processen en technologieën.
Voorlasbehandelingsmethode
De oppervlaktebehandeling vóór het lassen is een effectieve methode om metallurgische poriën te controleren bij het laserlassen van aluminiumlegeringen. Gangbare methoden voor oppervlaktebehandeling zijn fysieke mechanische reiniging en chemische reiniging. Onlangs heeft laserimpactreiniging ook zijn intrede gedaan, wat de automatisering van laserlassen verder verbetert.
Parameterstabiliteit optimalisatieregeling
De procesparameters van het laserlassen van aluminiumlegeringen omvatten doorgaans laservermogen, defocus, lassnelheid en de samenstelling en stroom van gasbescherming. Deze parameters hebben niet alleen invloed op het beschermende effect van het lasgebied, maar ook op de stabiliteit van het laserproces voor diep doordringen, wat weer invloed heeft op lasporositeit.
Bij het laserdiep penetratielassen van aluminiumlegering platen is gebleken dat de stabiliteit van de penetratie van kleine gaatjes de stabiliteit van het smeltbad beïnvloedt, wat vervolgens de lasvorming beïnvloedt en resulteert in porositeitsdefecten. Bovendien is de stabiliteit van het laserdiep penetratielassen gerelateerd aan de afstemming van laser vermogensdichtheid en lineaire energie.
Daarom is het bepalen van redelijke procesparameters voor stabiele lasvorming een effectieve methode om de porositeit van het laserlassen van aluminiumlegeringen te beheersen. Onderzoeksresultaten over stabiele lasvormingskenmerken bij volledige inbranding hebben aangetoond dat de verhouding tussen de breedte van de lasrug en de breedte van het lasoppervlak (verhouding lasrugbreedte) kan worden gebruikt om de lasvorming en stabiliteit van aluminiumlegering platen te evalueren.
Door de dichtheid van het laservermogen en de energie van de laserstraal tijdens het laserlassen van dunne platen goed op elkaar af te stemmen, kan een bepaalde verhouding van lasrugbreedte worden gegarandeerd, waardoor de poreusheid van de las effectief wordt beheerst.
Dubbel puntlaserlassen
Dubbel puntlaserlassen verwijst naar een lasproces waarbij twee gerichte laserstralen tegelijkertijd op hetzelfde lasbad werken. Bij laserdiep penetratielassen is een van de belangrijkste oorzaken van lasporositeit het sluiten van gas in het kleine gat in het smeltbad.
Door dubbel puntlaserlassen te gebruiken, wordt de opening van het kleine gat vergroot door de invloed van twee lichtbronnen, waardoor het gemakkelijker wordt voor de inwendige metaaldamp om te ontsnappen en de stabiliteit van het kleine gat wordt verbeterd, waardoor de poreusheid van de las wordt verminderd.
Onderzoeken naar laserlassen van A356, AA5083, 2024 en 5A90 aluminiumlegeringen hebben aangetoond dat dubbel puntlaserlassen de poreusheid van de las aanzienlijk kan verminderen.
Hybride laserbooglassen
Laserbooghybride lassen is een lasmethode waarbij zowel de laser als de boog hetzelfde smeltbad beïnvloeden. Meestal is de laser de primaire warmtebron en de interactie tussen laser en boog verbetert de penetratie en lassnelheid van laserlassen terwijl de nauwkeurigheid van de lasassemblage afneemt.
Het gebruik van lasdraad helpt bij het beheersen van de microstructuur en eigenschappen van de lasverbindingen en het neveneffect van de boog verbetert de stabiliteit van lasergaten, wat bijdraagt aan het verminderen van lasporositeit.
In het proces van laserbooghybride lassen beïnvloedt de boog de metaaldamp/plasmawolk die door het laserproces wordt gegenereerd, wat de absorptie van laserenergie en de stabiliteit van kleine gaten bevordert.
Onderzoek naar laserbooghybride lassen van aluminiumlegeringen heeft bevestigd dat het effectief is in het verminderen van lasporositeit.
Fiber laserlassen
Het sleutelgateffect bij laserdiep penetratielassen ontstaat door de sterke verdamping van metaal onder invloed van de laser. De kracht van de verdamping van metaal is nauw verbonden met de vermogensdichtheid van de laser en de kwaliteit van de straal en beïnvloedt zowel de penetratie van het laserlassen als de stabiliteit van de sleutelgaten.
Seiji et al. bestudeerden SUS304 roestvast staal hoog vermogen fiber laser en toonden aan dat:
Tijdens het lassen met hoge snelheid wordt het smeltbad langer, wordt het spatten beheerst, zijn de schommelingen in kleine gaatjes stabiel en zijn er geen luchtbellen aan het uiteinde van het kleine gaatje. Wanneer een fiberlaser wordt gebruikt voor hogesnelheids lassen van titanium legeringen en aluminiumlegeringen kan ook een las zonder poriën worden gemaakt.
Onderzoek naar schermgas besturingstechnologie voor fiber laserlassen van titaniumlegeringen door Allen et al. shoe vind je dat:
Door de positie van de beschermgas voor lassenis het mogelijk om gasbetrokkenheid te voorkomen, de sluitingstijd van het kleine gat te verkorten, het kleine gat te stabiliseren en het stollingsgedrag van het smeltbad te veranderen, waardoor de poreusheid van de las wordt verminderd.
Gepulseerd laserlassen
Vergeleken met continu laserlassen kan de pulsmodus van de laseruitvoer de periodieke en constante stroom van het smeltbad verbeteren, wat helpt bij het loslaten van bellen en de poreusheid van de las vermindert.
T.Y. Kuo en S.L. Jeng onderzochten de invloed van het uitgangsvermogen van de YAG-laser op de porositeit en eigenschappen van lassen gemaakt van SUS 304L roestvast staal en Inconel 690 superlegering.
De resultaten geven aan dat voor het laserlassen met vierkante-golfpuls, als het basisvermogen toeneemt tot 1700 W, de lasporositeit afneemt met de toename van de pulsamplitude ΔP. De porositeit van het roestvast staal neemt af van 2,1% tot 0,5% en die van de superlegering neemt af van 7,1% tot 0,5%.
Technologie voor composietbehandeling na het lassen
Ondanks een strikte oppervlaktebehandeling vóór het lassen en een stabiel lasproces is poreusheid in praktische technische toepassingen nog steeds een veel voorkomend probleem bij het laserlassen van aluminiumlegeringen.
Daarom zijn methoden voor behandeling na het lassen om porositeit te elimineren van cruciaal belang.
Momenteel wordt vooral gemodificeerd lassen gebruikt.
Eén zo'n methode om inwendige en krimpporositeit in aluminium te elimineren gietstukken van legeringen is de hete isostatische perstechnologie.
Door dit te combineren met een warmtebehandeling na het laserlassen van aluminiumlegeringen, ontstaat een samengesteld proces van heet isostatisch persen en warmtebehandeling van componenten voor het laserlassen van aluminiumlegeringen. Dit elimineert niet alleen lasporositeit, maar verbetert ook de prestaties van de lasverbinding.
De toepassing van hoogvermogen laserlassen in aluminiumlegeringen brengt nog steeds veel uitdagingen met zich mee vanwege de unieke eigenschappen.
Een van de belangrijkste uitdagingen is het beheersen van lasporositeitsdefecten en het verbeteren van laskwaliteit.
Om de stabiliteit van het lasproces te verbeteren en porositeit bij het laserlassen van aluminiumlegeringen onder controle te houden, is een allesomvattende aanpak nodig die rekening houdt met alle aspecten, van voor het lassen tot het lasproces en de behandeling na het lassen.
Om deze uitdaging aan te gaan, zijn er verschillende nieuwe technologieën en processen ontwikkeld, waaronder laserreiniging vóór het lassen, optimalisatie van lasprocesparameters door middel van terugdringerbreedteverhoudingsregeling, laserlassen met dubbele laserstraal, laser-boog hybride lassen, pulslaserlassen en laserlassen met dubbele laserstraal. optische vezellaser lassen.