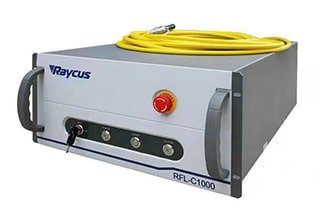
Heb je je ooit afgevraagd hoe een laser door metaal kan snijden als een heet mes door boter? In dit fascinerende artikel verkennen we de wetenschap achter de fiberlasersnijtechnologie. Onze deskundige werktuigbouwkundig ingenieur leidt je door de fundamentele concepten en laat zien hoe deze geavanceerde technologie een revolutie teweegbrengt in de productie. Bereid je voor op een duik in de wereld van lasersnijden en ontdek het immense potentieel!
"De laser snijdt door ijzer alsof het modder is", deze uitspraak is niet overdreven.
Laten we de laser in meer detail bekijken.
Wat is een laser?
Een laser is een type versterkt licht dat wordt geproduceerd door middel van gestimuleerde straling.
De belangrijkste functies zijn:
Wanneer de laserstraal op het oppervlak van het werkstuk wordt gericht, wordt de lichtenergie geabsorbeerd en omgezet in warmte-energie.
Dit zorgt ervoor dat de temperatuur op het bestralingspunt snel stijgt, smelt en verdampt en een kleine put vormt.
Het metaal rondom de put smelt door thermische diffusie. De damp in de kleine put zet snel uit, waardoor een micro-explosie ontstaat. Het gesmolten materiaal wordt met hoge snelheid uitgestoten en genereert een zeer gerichte anti-schokgolf.
Dit resulteert in de vorming van een gat met een grote bovenkant en een kleine onderkant op het te bewerken oppervlak.
Vergelijking van gewoon licht en laser:
De generatie van laser
Laser opwekkend gas
Lasergeneratiegas is anders dan snijgas.
Samenstelling van het lasergas:
De proportionele relatie tussen de drie bovengenoemde gassen is:
N2CO2:Hij = 1:4:5
Fiber lasersnijden is een hete snijmethode die gebruik maakt van een gefocuste laserstraal met een hoog vermogen als belangrijkste hittebron. Dit zorgt ervoor dat de bestraalde materialen snel smelten, verdampen, ableren of een ontstekingspunt bereiken.
Tegelijkertijd helpt het gebruik van een snelle luchtstroom die coaxiaal is met de laserstraal om het gesmolten materiaal weg te blazen, waardoor het werkstuk kan worden gesneden.
In de afgelopen jaren is de technologie achter krachtige fiberlasergeneratoren volwassen geworden en verbeterd, wat heeft geleid tot een steeds breder scala aan toepassingen.
De fiber lasersnijmachine is een populaire focus geworden van industrieel onderzoek en ontwikkeling.
In de wereld van dunne plaat snijdenVezellasergeneratoren vervangen om verschillende redenen geleidelijk de traditionele CO2 lasers en YAG lasers:
(1) Lagere kosten:
De foto-elektrische omzettingsefficiëntie van fiber lasers is ongeveer 30%, terwijl de foto-elektrische omzettingsefficiëntie van CO2 lasers 6-10% is en de foto-elektrische omzettingsefficiëntie van YAG lasers slechts 3% is. Bovendien hebben fiberlasergeneratoren geen kwetsbare onderdelen, dus er zijn geen kosten verbonden aan laattijdig onderhoud.
(2) Compact en flexibel ontwerp:
Fiber lasers zijn klein, licht van gewicht en bieden een flexibele en beweegbare werkpositie.
(3) Verbeterde snijkwaliteit:
Het gebruik van een flexibel lichtgeleidingssysteem in vezellasers en een constante straaloverdrachtsafstand voorkomt slechte snijkwaliteit veroorzaakt door veranderingen in het lichtpad lengte van CO2-lasergeneratoren.
Dit zorgt voor een consistente snijkwaliteit over de hele snijbreedte, waardoor het ideaal is voor grootformaat laserverwerkingssystemen.
(4) Kostenbesparingen:
De straal van een fiberlaser beweegt langs een optische vezel, waardoor er geen extern gereflecteerd lichtpadsysteem nodig is, wat de kosten van reflectielenzen en orgaanschilden uitspaart.
Er zijn ook geen externe optische padaanpassingen nodig, wat het risico op vervuiling van het lichtpad door vuil vermindert en het gewicht van bewegende onderdelen vermindert.
(5) Verbeterde prestaties bij het snijden van metaal:
De golflengte van een fiberlaser is 1,06 μm, die gemakkelijker geabsorbeerd wordt door metalen materialen in vergelijking met de golflengte van CO2 (10,6 μm).
Dit is vooral gunstig voor snijden van plaatwerkmet snijsnelheden die 2 tot 4 keer hoger liggen dan bij CO2.
Vezellasers hebben ook een beter snijeffect voor hoogreflecterende materialen zoals aluminiumlegeringenkoper en koperlegeringen.
Zie ook:
(1) lens
(2) de laserstraal
(3) luchtstroom
(4) de lijn
(5) gesmolten materiaal
(6) snijoppervlak
(7) mondstuk
(8) snijrichting
A: Lege hoogte
B: Punthoogte
C: Snijhoogte
T: Plaatdikte
De eerste lasersnijmachine ter wereld werd uitgevonden in de jaren 1970. In de afgelopen dertig jaar is de toepassing van lasersnijmachines voortdurend uitgebreid en is de technologie voortdurend verbeterd.
Veel bedrijven produceren nu verschillende soorten lasers snijmachines om aan de marktvraag te voldoen, waaronder 2D-plaatlasersnijmachines, 3D-ruimte laserbochtsnijmachines en pijplasersnijmachines.
Enkele van de topbedrijven op het gebied van lasersnijmachines zijn: Trumpf (Duitsland), Prima (Italië), Bystronic (Zwitserland), Amada (Japan), MAZAK (Japan), NTC (Japan) en HGLaserLab (Australië).
Een lijst van de top lasersnijmachine fabrikanten wereldwijd beschikbaar ter referentie.
Fiberlasersnijapparatuur kan effectief roestvrij staal snijden dat minder dan 4 mm dik is. Als er zuurstof wordt toegevoegd, kan het zelfs roestvrij staal tot 8 tot 10 mm dik snijden met een laserstraal.
Bij gebruik van zuurstof vormt zich echter een dunne oxidelaag op het snijoppervlak. De maximale snijdikte kan worden verhoogd tot 16 mm, maar de maattolerantie van het gesneden onderdeel wordt groter.
Hoewel fiberlasersnijapparatuur duur is, is het nog steeds economisch haalbaar voor grote productieruns vanwege de lagere kosten voor verdere verwerking.
Omdat er geen gereedschapskosten zijn, is lasersnijapparatuur ook geschikt voor kleine series onderdelen die voorheen niet te bewerken waren.
Fiberlasersnijapparatuur maakt meestal gebruik van een CNC-systeem (Computerized Numberical Control). Met deze technologie kunnen snijgegevens worden ontvangen van een CAD-werkstation (Computer Aided Design).
Zie ook:
Het adaptieve optische systeem, een kernonderdeel van moderne lasersnijmachines, past de kromming van de focuslens dynamisch aan door middel van nauwkeurige hydraulische drukregeling. Deze aanpassing verandert de divergentiehoek van de laserstraal, waardoor een nauwkeurig afgestelde verticale positionering van het brandpunt mogelijk wordt.
Bovendien compenseert dit geavanceerde systeem focale verschuivingen die optreden door verschillende spotdiameters in verschillende werkposities van de machine. Deze automatische aanpassing zorgt voor een consistente snijkwaliteit en precisie, ongeacht de positie van het werkstuk of de locatie van de snijkop binnen het werkbereik.
De adaptieve optiek optimaliseert niet alleen de focus van de bundel voor verschillende materiaaldiktes, maar handhaaft ook de snijprestaties tijdens hogesnelheidsbewerkingen, waarbij snelle versnellingen en vertragingen de eigenschappen van de bundel kunnen beïnvloeden. Deze technologie verbetert de snijefficiëntie aanzienlijk, vermindert variaties in de kerfbreedte en verbetert de algehele productkwaliteit, met name bij complexe contoursnijtoepassingen en toepassingen met hoge precisie.
De fiberlasersnijkop is een kritisch onderdeel in moderne lasersnijsystemen, ontworpen om de krachtige laserstraal te focussen en nauwkeurig op het werkstuk te richten. De kop bestaat uit verschillende belangrijke elementen die samenwerken om optimale snijprestaties te bereiken:
In praktische toepassingen varieert de hoogte van de focus met het materiaal en de snijmachine.
Selectie focuspositie
Bij het lasersnijden heeft de positie van de laserfocus een grote invloed op de kwaliteit van de oppervlakteafwerking van de gesneden onderdelen.
Als je bijvoorbeeld koolstofstaal snijdt, moet je je richten op het bovenste oppervlak van de plaat. snijden van roestvrij staalBij het snijden van een aluminiumlegering moet de focus ongeveer halverwege de dikte van de plaat liggen; bij het snijden van een aluminiumlegering moet de focus dicht bij het onderste oppervlak van de plaat liggen.
In het geval van het snijden van een roestvast stalen monster van 2 mm, zoals te zien is in de afbeelding hieronder, moet de focuspositie ongeveer 0,8 tot 1,2 mm onder het oppervlak van de plaat liggen.
Fig. Voorbeeld lasersnijden
Tijdens het snijproces kan het ongelijke oppervlak van het materiaal veranderingen veroorzaken in de focuspositie van de laser, waardoor de snijkwaliteit beïnvloed wordt.
Om dit probleem aan te pakken, wordt een zeer gevoelige capacitieve sensor op de snijkop geplaatst om real-time feedback te geven over de afstand tussen het mondstuk en het paneel aan de CNC-systeem.
Op basis van deze feedback wordt de hoogte van de snijkop in realtime aangepast via een transmissiemechanisme, waardoor een gesloten regelcircuit met een hoge dynamische respons ontstaat dat defecten helpt voorkomen die worden veroorzaakt door veranderingen in de focuspositie tijdens het snijden. plaat snijden.
Het laservermogen is een kritische parameter die een significante invloed heeft op de snijdikte, snelheid, kerfbreedte en algehele kwaliteit bij lasersnijden. Over het algemeen maakt een hoger laservermogen het mogelijk om dikkere materialen te snijden met hogere snelheden. De relatie tussen deze variabelen is echter genuanceerder en vereist zorgvuldige optimalisatie.
Voor elke combinatie van materiaaldikte en snijsnelheid bestaat er een optimaal laservermogensbereik dat de oppervlakteruwheid minimaliseert en de snijkwaliteit maximaliseert. Afwijken van dit optimale bereik leidt tot verhoogde oppervlakteruwheid, verminderde verwerkingsefficiëntie en hogere operationele kosten. Overmatig vermogen kan leiden tot verbranding of problemen met de warmte-beïnvloede zone (HAZ), terwijl onvoldoende vermogen kan resulteren in onvolledige sneden of verhoogde drossvorming.
Het is belangrijk om te weten dat wanneer het laservermogen en de druk van het hulpgas constant worden gehouden, de snijsnelheid en kerfbreedte een niet-lineair omgekeerd evenredig verband vertonen. Als de snijsnelheid toeneemt, neemt de kerfbreedte af en omgekeerd. Deze relatie is essentieel voor een nauwkeurige dimensionale controle van lasergesneden onderdelen.
De correlatie tussen snijsnelheid en oppervlakteruwheid van de snijkant volgt een parabolische curve. Beginnend bij nul, vermindert het verhogen van de snijsnelheid aanvankelijk de oppervlakteruwheid. Deze verbetering gaat door tot een optimale snelheid wordt bereikt waarbij de oppervlakteruwheid wordt geminimaliseerd. Voorbij dit punt leiden verdere snelheidsverhogingen tot onvolledige snedes en een verslechterende oppervlaktekwaliteit.
Moderne CNC lasersnijsystemen maken gebruik van adaptieve besturingsalgoritmes om het laservermogen dynamisch aan te passen op basis van de snijsnelheid en de geometrie. Bijvoorbeeld bij het snijden van kleine radii of scherpe hoeken waarbij de snijsnelheid moet worden verminderd, vermindert het systeem automatisch het laservermogen om een optimale energie-input te behouden en oververhitting of een te grote kerfbreedte te voorkomen.
Deze adaptieve vermogensregeling is vooral cruciaal voor het bereiken van hoge precisie en uitstekende randkwaliteit in complexe werkstukken met verschillende vormgroottes. Het zorgt voor een consistente snijkwaliteit in rechte secties, bochten en ingewikkelde details zonder handmatige tussenkomst.
Het begrijpen en optimaliseren van deze onderling gerelateerde parameters - laservermogen, snijsnelheid, materiaaldikte en assisterende gasdynamica - is essentieel voor het bereiken van hoogwaardige, kosteneffectieve lasersnijbewerkingen in een breed scala aan materialen en toepassingen.
Zie ook:
Voel je je als beginner op het gebied van lasersnijden vaak overweldigd tijdens het proces? Het kan verwarrend zijn om te experimenteren met verschillende platen, gassen, luchtdrukken en vermogens en toch niet de gewenste resultaten te behalen.
Heb je je afgevraagd hoe je het juiste hulpgas moet kiezen en welke factoren van invloed zijn op de snijkwaliteit? Welk hulpgas moet worden gebruikt voor verschillende materialen? Hoe wordt de druk van het hulpgas geregeld en wat zijn de vereisten voor de zuiverheid ervan?
Het is belangrijk om de rol van het hulpgas bij het lasersnijden te begrijpen. Het wordt gebruikt om de slak weg te blazen in de snijkantHet oppervlak van het bewerkte materiaal afkoelen om de warmte-beïnvloede zone te verkleinen, de beschermende lens afkoelen om contaminatie te voorkomen en in sommige gevallen het basismetaal beschermen.
Typen en eigenschappen hulpgas
De hulpgassen die vaak worden gebruikt in lasersnijden zijn stikstof, zuurstof en lucht.
Hulpgas is cruciaal bij het lasersnijden omdat het helpt om het gesmolten en verdampte materiaal van de snede te verwijderen en ook de rook wegblaast die tijdens het snijproces ontstaat, waardoor het snijproces minder hinder ondervindt.
De druk- en debietvereisten voor het hulpgas variëren afhankelijk van de dikte en het soort materiaal dat wordt gesneden.
Bij het snijden van koolstofstaal wordt meestal zuurstof gebruikt. Het doel van het gebruik van zuurstof bij het snijden van koolstofstaal is om het gesmolten materiaal te doen ontbranden en te verwijderen.
Ondervind je als beginnende lasersnijder vaak moeilijkheden tijdens het lasersnijden? Ondanks het uitproberen van verschillende platen, gassen, luchtdrukken en vermogens, ben je misschien nog steeds niet zeker van de optimale combinatie.
Om het beste hulpgas te kiezen, is het essentieel om de rol ervan te begrijpen en de factoren die de snijkwaliteit beïnvloeden, zoals druk en debiet en de zuiverheid van het gas.
Voor het snijden van koolstofarme staalplaten wordt meestal zuurstof gebruikt. De rol van zuurstof in het snijproces is het aanwakkeren en verwijderen van het gesmolten materiaal.
De zuiverheid van zuurstof moet hoger zijn dan 99,5%, waarbij een hogere zuiverheid resulteert in een helderder snijoppervlak.
Onzuiverheden zoals water kunnen echter een aanzienlijke invloed hebben op de snijkwaliteit van de plaat. Als de zuurstofzuiverheid niet hoog genoeg is of als de onderdelen hogere eisen stellen aan de oppervlaktekwaliteit, kan het nodig zijn om de zuiverheid te verbeteren door zuurstofdroging of andere methoden.
Stikstof wordt meestal gebruikt voor het snijden van roestvrij staal en aluminiumlegering materialen. De rol van stikstof is het elimineren van oxidatie en het verwijderen van de smelt.
De stikstofdruk neemt toe met de dikte van de plaat.
Voor het snijden van roestvrij staal moet de zuiverheid van stikstof hoger zijn dan 99,999%. Stikstof met een lage zuiverheid kan leiden tot vergeling van het snijoppervlak en verminderde helderheid.
Een monster in de lasersnijfiguur werd gesneden met hoogzuivere (99,99%) vloeibare stikstof, met een gasdruk van 0,8 tot 1,0 MPa.
Standaard voor zuiverheid hulpgas
Het gebruik van bijpassende hulpgassen is vereist voor laserbewerking van verschillende materialen.
Onzuiverheden in het hulpgas kunnen nadelige effecten hebben op de lens, wat resulteert in schommelingen in snijvermogen en ongelijkmatigheden op de snijvlakken voor en achter.
Hulpgasdruk standaard
De hoeveelheid luchtdruk die kan worden gebruikt voor verschillende soorten hulpgassen verschilt. Op basis van de eigenschappen van het gas, zoals ontvlambaarheid en verbranding, heeft de ervaring geleerd dat het hulpgas kan voorkomen dat er slak terugkomt tijdens het snijproces, waardoor de interne lens van de machine wordt beschermd. laserkop.
Met andere woorden, hoe hoger de gasdruk, hoe meer rook en stof er kan worden weggeblazen bij dezelfde verwerkingskracht, hetzelfde materiaal en dezelfde plaatdikte.
Daarom resulteert een hogere luchtdrukwaarde in een snellere lasersnijsnelheidDaarom wordt stikstof gebruikt voor het snijden van dunne platen.
Hieruit kan worden geconcludeerd dat de algemene regel voor de snijsnelheid van dunne platen is: Zuurstof < Lucht < Stikstof. Deze regel kan worden gebruikt als uitgangspunt voor de selectie van hulpgassen door beginnende gebruikers.
Opmerking: De bovenstaande algemene regel is niet van toepassing op het lasersnijden van dikke platen. Het type snijgas dat wordt gebruikt, moet worden gekozen op basis van de individuele plaatkenmerken.
Na het lezen hiervan zou je een basiskennis moeten hebben van de kenmerken van de drie hulpgassen. Laten we ze eens nader bekijken.
Zuurstof
Zuurstof wordt voornamelijk gebruikt voor het snijden van koolstofstaal. De reactiewarmte van zuurstof wordt gebruikt om de snijefficiëntie te verhogen, maar de resulterende oxidelaag verhoogt de spectrale absorptiefactor van de straal van het reflecterende materiaal.
Hierdoor ziet het uiteinde van de spleet er zwart of donkergeel uit.
Zuurstof wordt voornamelijk gebruikt voor het snijden van walsstaal, gerold staal voor lasconstructies, koolstofstaal voor mechanische constructies, hoogspanningsplaten, gereedschapsplaten, roestvrij staal, gegalvaniseerde staalplaten, koper, koperlegeringen, enz.
De zuiverheidsvereiste voor zuurstof is over het algemeen 99,95% of hoger. De belangrijkste functie is helpen bij het verbranden en wegblazen van de gesneden smelt.
De vereiste druk en stroomsnelheid zijn verschillend en worden bepaald door de grootte van het mondstukmodel en de dikte van het snijmateriaal. Over het algemeen is de vereiste druk 0,3-1Mpa en het debiet varieert op basis van de dikte van het materiaal. snijmateriaal.
Als je bijvoorbeeld 22 mm koolstofstaal snijdt, moet het debiet 10 m3/u zijn, inclusief de zuurstofbescherming van de dubbele spuitmond.
Nstikstof
Sommige metalen vereisen het gebruik van stikstof om oxidatie tijdens het snijden te voorkomen en om de kwaliteit van het snijoppervlak te behouden. Dit resulteert in een witachtig eindvlak van de spleet en een hoge weerstand tegen lassen, smeren en corrosie.
De belangrijkste materialen die gesneden kunnen worden met stikstof zijn roestvrij staal, plaatstaal, messing, aluminium en aluminiumlegeringen. Het doel van het gebruik van stikstof is om oxidatie te voorkomen en de smelt af te blazen.
Voor hoogwaardig snijden is een hoge zuiverheid stikstof nodig (99,999% is vaak vereist voor roestvrij staal met een dikte van 8 mm of meer). De vereiste druk is relatief hoog, meestal rond 1,5 MPa. Voor dikker roestvrij staal (12 mm of meer, tot 25 mm) kan een druk van 2 MPa of hoger nodig zijn.
De stroomsnelheid van stikstof varieert afhankelijk van het type mondstuk dat wordt gebruikt, maar is over het algemeen vrij hoog. Voor het snijden van 12 mm roestvast staal is bijvoorbeeld een stroomsnelheid van 150 m3/h, terwijl voor het snijden van 3 mm roestvast staal slechts 50 m3/h.
Air
Het gebruik van lucht als hulpgas bij laserbewerking is kosteneffectief omdat het direct uit een luchtcompressor kan worden gehaald. Hoewel het 20% zuurstof bevat, is de snijefficiëntie laag in vergelijking met zuurstof en vergelijkbaar met stikstof.
Er kan een spoor van oxidelaag verschijnen op het snijvlak, maar dit kan ook helpen voorkomen dat de coating eraf valt. Het uiteinde van de snede ziet er gelig uit.
Voornamelijk gebruikt voor het snijden van materialen zoals aluminium, roestvrij koper, messing, gegalvaniseerde stalen platen en niet-metalen. Echter, wanneer producten van hoge kwaliteit nodig zijn, is lucht niet geschikt voor aluminium snijdenaluminiumlegering en roestvrij staal omdat dit het basismateriaal oxideert.
De keuze van het hulpgas hangt af van de snijkosten en de vereisten voor het product. Bij het snijden van roestvast staal voor producten van lage kwaliteit die verder bewerkt zullen worden, kan bijvoorbeeld lucht gebruikt worden om de kosten te drukken.
Aan de andere kant, als het gesneden product het eindproduct is, moet een beschermend gas zoals stikstof worden gebruikt, zoals bij ambachtelijke producten.
Daarom moet het hulpgas worden gekozen op basis van de kenmerken van het product in het snijproces.
Zie ook:
Door een laserstraal met hoge energiedichtheid te gebruiken om het werkstuk te verhitten, stijgt de temperatuur snel en bereikt deze in zeer korte tijd het kookpunt van het materiaal, waardoor het materiaal verdampt en stoom vormt.
Deze snel bewegende stoom maakt een insnijding in het materiaal terwijl het ook verdampt.
De verdampingswarmte van materialen is meestal hoog, waardoor een grote hoeveelheid vermogen en een hoge vermogensdichtheid nodig zijn voor laserverdamping.
Deze techniek wordt gebruikt voor het snijden van dunne metalen materialen en niet-metaalachtige materialen zoals papier, stof, hout, plastic en rubber.
Tijdens het verdampingsproces voert de stoom het gesmolten materiaal en de brokstukken mee, waardoor er een gat ontstaat.
Ongeveer 40% van het materiaal wordt opgelost in stoom, terwijl 60% tijdens het verdampingsproces in de vorm van druppels door de stroom wordt uitgestoten.
Wanneer de vermogensdichtheid van de inkomende laserstraal een bepaalde drempel overschrijdt, begint het materiaal op het bestralingspunt van de straal te verdampen en vormt het een gat. Het gat absorbeert alle inkomende stralingsenergie en gedraagt zich als een zwart lichaam.
De gaten worden omgeven door wanden van gesmolten metaal en de extra luchtstroom, langs de as van de straal, voert het gesmolten materiaal rond het gat weg.
Terwijl het werkstuk beweegt, wordt het gat horizontaal gesynchroniseerd, waardoor een snede in de snijrichting wordt gevormd. De laserstraal blijft langs de rand van de naad stralen, waardoor het smeltmateriaal continu of periodiek door de scheuren wordt weggeblazen.
Bij lasersmeltsnijden hoeft het metaal niet volledig te worden verdampt en wordt slechts 1/10 van de energie gebruikt die nodig is voor verdamping.
Deze methode wordt voornamelijk gebruikt voor het snijden van niet-oxideerbare materialen of actieve metalen zoals roestvrij staal, titanium, aluminium en legeringen.
Het principe van laserzuurstofsnijden is vergelijkbaar met dat van autogeensnijden. Het gebruikt de laser als voorverwarmingsbron en gebruikt zuurstof en andere actieve gassen als snijgas.
Aan de ene kant reageert het gas met het metaal dat gesneden wordt en veroorzaakt het een oxidatiereactie, waarbij een aanzienlijke hoeveelheid warmte vrijkomt.
Aan de andere kant worden het gesmolten oxide en het gesmolten metaal uit het reactiegebied gedreven, waardoor er een snede in het metaal ontstaat.
Door de grote hoeveelheid warmte die wordt gegenereerd tijdens de oxidatiereactie, heeft laser zuurstof snijden slechts de helft van de energie nodig die nodig is voor smeltsnijden en heeft het een snellere snijsnelheid vergeleken met laser verdampingssnijden en smeltsnijden.
Deze methode wordt voornamelijk gebruikt voor het snijden van koolstofstaal, titaniumstaal, warmtebehandeld staal en andere gemakkelijk geoxideerde metalen materialen.
Het proces van zuurstof snijden met een laser kan als volgt worden beschreven:
Voor brosse materialen die gevoelig zijn voor hitteschade staat snijden door middel van laserstraalverwarming met hoge snelheid en controle bekend als gecontroleerd breuksnijden.
Het belangrijkste aspect van dit snijproces is dat de laserstraal een klein gebied van het brosse materiaal verhit, wat leidt tot een grote thermische gradiënt en aanzienlijke mechanische vervorming in het gebied, waardoor het materiaal barst.
Zolang de verwarmingsgradiënt in balans blijft, kan de laserstraal de scheuren in elke gewenste richting sturen.
Het is belangrijk om te weten dat dit type snijden niet geschikt is voor het snijden van scherpe hoeken. Het is ook een uitdaging om succes te boeken bij het snijden van een grote en gesloten vorm.
De snijsnelheid van gecontroleerd breukzagen is snel en vereist geen buitensporig vermogen, anders zal het oppervlak van het werkstuk smelten en de snijrand breken.
De belangrijkste controleparameters zijn het laservermogen en de spotgrootte.
Lasersnijden geclassificeerd door snijgas:
Vlammend snijden | Smelten snijden | |
---|---|---|
Snijgas | Zuurstof | Stikstof |
Kenmerken | Grote snijdikte | Snijgedeelte zonder oxidelaag |
Snelle snijsnelheid | Minder snijbramen | |
Heeft geoxideerde laag | Gas afsnijden is duur | |
Snijgedeelte met een sleeplijn achteraan | Langzaam snijden snelheid | |
Een deel van het materiaal heeft zuurstof nodig om deel te nemen aan de punctie | ||
Toepasselijk materiaal | Koolstofstaal | Roestvrij staal, aluminium, verzinkte plaat |
Vergeleken met andere thermische snijmethoden onderscheidt lasersnijden zich door de hoge snijsnelheid en superieure kwaliteit.
Specifiek kunnen de volgende aspecten worden samengevat:
Lasersnijden biedt een betere snijkwaliteit dankzij de kleine laserspot, hoge energiedichtheid en hoge snijsnelheid.
De laserstraal wordt op een klein punt gericht, wat resulteert in een hoge vermogensdichtheid in het brandpunt.
De warmte-input van de straal is aanzienlijk hoger dan de warmte die gereflecteerd, doorgelaten of verspreid wordt door het materiaal.
Dit leidt tot snelle verhitting en verdamping van het materiaal, waardoor een porie ontstaat door verdamping.
Door de relatieve lineaire beweging van de straal en het materiaal wordt het gat continu gevormd tot een smalle spleet.
De snijkant wordt zeer weinig beïnvloed door de hitte en er is geen vervorming van het werkstuk.
Tijdens het snijproces wordt het hulpgas toegevoegd dat geschikt is voor het te snijden materiaal.
Wanneer het staal wordt gesneden, wordt zuurstof gebruikt als hulpgas en gesmolten metaal om exotherm chemisch reactieoxidatiemateriaal te produceren, terwijl het helpt om de slak in de spleet weg te blazen.
Bij het snijden van kunststoffen zoals polypropyleen wordt perslucht gebruikt.
Bij het snijden van brandbare materialen zoals katoen en papier wordt inert gas gebruikt.
Het hulpgas dat het mondstuk binnenkomt, kan ook de focuslens koelen en voorkomen dat stof de lenszitting binnendringt om de lens te vervuilen en oververhitting van de lens te veroorzaken.
De meeste organische en anorganische materialen kunnen met een laser worden gesneden.
De zware metaalverwerkende industrie, die veel betekent voor het industriële productiesysteem, veel metalen materialen, ongeacht hoe hard het is, kunnen worden gesneden zonder vervorming.
Natuurlijk zijn materialen met een hoge reflectie, zoals goud, zilver, koper en aluminium, ook goede warmtegeleiders, dus lasersnijden is moeilijk en kan niet eens worden gesneden.
Lasersnijden zonder bramen en rimpels. Het is in hoge precisie, beter dan plasmasnijden.
Voor veel mechanische en elektrische verwerkende industrie, als gevolg van moderne lasersnijsysteem bestuurd door de microcomputer programma kan gemakkelijk snijden werkstukken in verschillende vormen en maten, is het vaak de voorkeur dan blankingVormgevingsproces;
Hoewel de verwerkingssnelheid nog steeds lager is dan die van de stempel, heeft het geen schimmelverbruik, hoeft de schimmel niet gerepareerd te worden en bespaart ook de tijd van het vervangen van de schimmel, waardoor de verwerkingskosten worden bespaard en de productiekosten worden verlaagd. Daarom is het over het algemeen veel economischer.
De lasersnijsnede is smal, de spleten zijn parallel en loodrecht op het oppervlak en de maatnauwkeurigheid van de snijdelen kan ±0,05 mm bereiken.
Het snijoppervlak is glad en mooi, de oppervlakteruwheid is slechts enkele tientallen micrometers en zelfs lasersnijden kan als laatste proces worden gebruikt. Er is geen machinale bewerking nodig en de onderdelen kunnen direct worden gebruikt.
Na het lasersnijden is de breedte van de warmte-beïnvloede zone klein, de prestaties van het materiaal in de buurt van de spleet zijn bijna onaangetast en de vervorming van het werkstuk is klein, de snijprecisie is hoog, de geometrie van de spleet is goed en de vorm van de spleetdoorsnede is relatief regelmatig rechthoekig.
De vergelijking van lasersnijden, autogeensnijden en plasmasnijden wordt getoond in Tabel 1.
Het snijmateriaal is laag koolstofstaal met een dikte van 6,2 mm.
Tabel 1 lasersnijden vs. autogeensnijden vs. plasmasnijden
Snijmethoden | Sleufbreedte /mm | Warmte beïnvloede zone Breedte /mm | Spleetvorm | Snijsnelheid | Uitrusting Kosten |
---|---|---|---|---|---|
Lasersnijden | 0.2-0.3 | 0.04-0.06 | Parallel | Snel | Hoog |
Autogeen snijden | 0.9-1.2 | 0.6-1.2 | Relatief parallel | Langzaam | Laag |
Plasmasnijden | 3.0-4.0 | 0.5-1.0 | Wig & Kantelen | Snel | Medium |
Vanwege de transmissiekenmerken hebben lasersnijmachines meestal meerdere werktafels met numerieke besturing, waardoor volledige numerieke besturing van het snijproces mogelijk is.
Tijdens het gebruik kunnen verschillende vormen van onderdelen worden gesneden door eenvoudigweg het numerieke besturingsprogramma te wijzigen. Dit maakt zowel tweedimensionaal als driedimensionaal snijden mogelijk.
Een laag koolstof van 2 mm snijden staalplaat met een 1200W fiberlasersnijmachine kan resulteren in een snijsnelheid van 600cm/min.
Bij het snijden van een 5 mm polypropyleen harsplaat kan de snijsnelheid 1200 cm/min bereiken.
Het materiaal hoeft tijdens het lasersnijden niet vastgeklemd of gefixeerd te worden, wat tijd bespaart bij het voorbereiden van de opspanning en het laden en ontladen.
De laserstraal wordt gericht om een sterk geconcentreerd energiepunt te creëren, wat verschillende belangrijke voordelen heeft voor snijtoepassingen.
Ten eerste kan de laserstraal worden omgezet in intense thermische energie in een zeer klein gebied, wat resulteert in:
(1) een smalle, recht afgesneden spleet;
(2) een minimale thermische impactzone in de buurt van de snijrand;
(3) minimale lokale vervorming.
Ten tweede werkt de laserstraal zonder fysiek contact met het werkstuk. snijtangmet de voordelen van:
(1) geen mechanische vervorming van het werkstuk;
(2) geen slijtage of breuk van gereedschap;
(3) de mogelijkheid om elk materiaal te snijden, ongeacht de hardheid.
Tot slot is de laserstraal zeer controleerbaar en flexibel, wat leidt tot:
(1) eenvoudige integratie met automatiseringsapparatuur, waardoor het snijproces eenvoudig te automatiseren is;
(2) onbeperkte mogelijkheid om zaagsneden op hetzelfde werkstuk te herhalen;
(3) de mogelijkheid om het materiaalgebruik te optimaliseren door met behulp van een computer de sneden op de hele plaat te rangschikken.
Materialen die gesneden kunnen worden met een lasersnijmachine zijn onder andere metaalmatrixcomposieten, leer, hout en vezels.
Elk materiaal vertoont echter verschillende niveaus van aanpasbaarheid aan lasersnijden vanwege de unieke thermofysische eigenschappen en absorptiesnelheden van laserlicht.
De lasersnijprestaties van verschillende materialen met een CO2 laserbron worden geïllustreerd in de volgende tabel.
Materialen | Vermogen om laserlicht te absorberen | Snijprestaties | ||
---|---|---|---|---|
Metaal | Au, Ag, Cu, Al | Laag absorptie van laser licht | Over het algemeen is het moeilijker te bewerken en kunnen Cu en Al platen van 1-2mm met de laser gesneden worden. | |
W,Mo,Cr,Ti | Grote absorptie van laserlicht | Bij verwerking op lage snelheid kan de dunne plaat worden gesneden en moeten metalen zoals enkel Ti en Zr lucht gebruiken als hulpgas. | ||
Fe,Ni,Pb,Sn | Gemakkelijker te verwerken | |||
Niet-metaal | Organisch materiaal | Acryl, polyethyleen, polypropyleen, polyester, PTFE | Doordringen tot gloeilamplicht | De meeste materialen kunnen worden gesneden met een laser met een klein vermogen. Omdat deze materialen brandbaar zijn, wordt het snijoppervlak gemakkelijk verkoold. Acrylzuur en polytetrafluorethyleen worden niet gemakkelijk verkoold. Over het algemeen kan stikstof of droge lucht worden gebruikt als hulpgas. |
Leer, hout, doek, rubber, papier, glas, epoxy, fenol plastic | Kan niet doordringen tot gloeilamplicht | |||
Anorganisch materiaal | Glas, glasvezel | Grote thermische uitzetting | Glas, keramiek, porselein, enz. zijn gevoelig voor barsten tijdens of na de verwerking, en kwartsglas met een dikte van minder dan 2 mm heeft goede snij-eigenschappen. | |
Keramiek, kwartsglas, asbest, mica, porselein | Kleine thermische uitzetting |
Vergeleken met andere traditionele bewerkingsmethoden is lasersnijden veelzijdiger.
Ten eerste kunnen andere thermische snijmethoden niet in zo'n klein gebied snijden als de laserstraal dat kan, wat leidt tot bredere sneden, grotere warmte-beïnvloede zones en aanzienlijke vervorming.
Ten tweede kunnen lasers niet-metalen materialen snijden, wat niet mogelijk is met andere hete snijmethodes.
Snijden met behulp van zuurstof leidt tot betere resultaten voor het materiaal.
Wanneer zuurstof als bewerkingsgas wordt gebruikt, treedt er een lichte oxidatie op aan de snijrand. Voor platen met een dikte tot 4 mm kan hogedruksnijden met stikstof worden uitgevoerd, waardoor er geen oxidatie van de snijrand optreedt.
Voor platen met een dikte van meer dan 10 mm kan het gebruik van een speciale plaat in combinatie met de laser en het aanbrengen van olie op het oppervlak van het werkstuk de snijkwaliteit verbeteren.
Zuurstof kan worden gebruikt als oxidatie aan de snijkant acceptabel is. Het gebruik van stikstof resulteert in een niet-geoxideerde snijrand zonder bramen die geen verdere bewerking nodig hebben.
Het aanbrengen van een oliefilm op het oppervlak van de plaat kan het piercingeffect verbeteren zonder dat dit ten koste gaat van de verwerkingskwaliteit.
Aluminium kan, ondanks de hoge reflectiviteit en thermische geleidbaarheid, gesneden worden met een dikte van minder dan 6 mm, afhankelijk van het type legering en het vermogen van de lasergenerator.
Bij het snijden met zuurstof is het snijoppervlak ruw en hard. Stikstof zorgt voor een glad snijoppervlak.
Zuiver aluminium is moeilijk te snijden vanwege de hoge zuiverheidsgraad.
Alleen als het systeem is uitgerust met een "reflecterende absorptie" kan het aluminium worden afgesneden, want zonder deze wordt de optische component beschadigd door reflectie.
Titaanplaten worden gesneden met argon en stikstof als bewerkingsgassen. De andere parameters voor het snijden zijn die voor nikkel-chroomstaal.
Zowel messing als koper hebben een hoog reflectievermogen en een uitstekend warmtegeleidingsvermogen. Messing platen met een dikte van 1 mm kunnen gesneden worden met stikstof als bewerkingsgas.
Koperplaten met een dikte van minder dan 2 mm kunnen worden gesneden met zuurstof als bewerkingsgas.
Het is echter essentieel om een "reflecterende absorptie" op het systeem te installeren, anders zal de reflectie schade veroorzaken aan de optische componenten.
Vergeleken met andere thermische snijmethoden onderscheidt lasersnijden zich door de hoge snijsnelheid en de hoge kwaliteit van de sneden. Enkele van de belangrijkste voordelen zijn
Uitstekende snijkwaliteit:
Lasersnijden heeft een smalle incisiebreedte (meestal 0,1-0,5 mm), een hoge precisie (met een gat centrum afstand fout van 0,1-0,4 mm en een fout in de profielgrootte van 0,1-0,5 mm) en een gladde oppervlakteruwheid (met een Ra-waarde van 12,5-25 µm). Gesneden naden hebben meestal geen extra bewerking nodig voor het lassen.
Snelle snijsnelheid:
Een 2KW lasersnijder kan bijvoorbeeld door 8 mm dik koolstofstaal snijden met een snelheid van 1,6 m/min en door 2 mm dik roestvast staal met een snelheid van 3,5 m/min, met minimale thermische invloed en vervorming.
Schoon, veilig en milieuvriendelijk:
Lasersnijden verbetert de werkomgeving voor operators, omdat het schoon en veilig is en geen vervuiling veroorzaakt.
Zie ook:
Het kan als volgt worden samengevat:
(1) Goede snijkwaliteit.
Door de kleine laserlichtspot en hoge energiedichtheid kan lasersnijden een betere snijkwaliteit bereiken.
(1) De lasersnijsneden zijn smal, met snijkanten die parallel en loodrecht op het oppervlak staan en de nauwkeurigheid van de gesneden onderdelen kan oplopen tot + 0,05 mm.
(2) Het snijoppervlak is schoon en glad, met een oppervlakteruwheid van slechts enkele tientallen microns. In sommige gevallen kan lasersnijden zelfs gebruikt worden als laatste stap, zodat de onderdelen direct gebruikt kunnen worden zonder verdere bewerking.
(3) Na het lasersnijden is het door warmte beïnvloede gebied erg klein en de eigenschappen van het materiaal in de buurt van de snede zijn grotendeels onaangetast. Bovendien is er minimale vervorming van het werkstuk, wat resulteert in een hoge snijprecisie en een regelmatige rechthoekige vorm in de dwarsdoorsnede van de snede.
(2) Hoog snijrendement.
Vanwege de kenmerken van laser transmissie, lasersnijmachines hebben meestal meerdere CNC-werkstations, waardoor het hele snijproces alleen met CNC kan worden uitgevoerd.
In de praktijk kunnen onderdelen met verschillende vormen worden gesneden door eenvoudigweg het NC-programma te wijzigen, en zowel 2D als 3D snijden is mogelijk.
(3) Snelle snijsnelheid.
De snijsnelheid voor 2mm zacht staal met een 1200W lasersnijder kan 600cm/min bereiken, terwijl voor een 5mm polypropyleen hars plaat de snijsnelheid 1200cm/min kan bereiken.
Het materiaal hoeft tijdens het lasersnijden niet te worden vastgeklemd, wat niet alleen gereedschap bespaart, maar ook de tijd verkort die nodig is voor het laden en ontladen van materialen.
(4) Contactloos snijden.
Bij lasersnijden komt de snijbrander niet in contact met het werkstuk en is er geen slijtage van het gereedschap. Er is geen vervanging van de "snijder" nodig voor het bewerken van onderdelen met verschillende vormen.
De enige verandering die nodig is, zijn de outputparameters van de laser. Bovendien is het lasersnijproces geluidsarm, trillingsarm en levert het geen vervuiling op.
(5) Talrijke variëteiten aan snijmaterialen.
Vergeleken met autogeen en plasmasnijden kan lasersnijden een grotere verscheidenheid aan materialen snijden, waaronder metalen, niet-metalen, metaalgebaseerde en niet-metaal matrix composieten, leer, hout en vezels.
De geschiktheid van lasersnijden voor deze materialen varieert echter door hun verschillende thermische en fysische eigenschappen en hun verschillende laserabsorptiesnelheden.
Door beperkingen in het laservermogen en de grootte van de apparatuur zijn lasersnijders beperkt in hun mogelijkheden om dikkere plaat- en buismaterialen te snijden.
Naarmate de dikte van het werkstuk toeneemt, neemt de snijsnelheid aanzienlijk af.
Bovendien is lasersnijapparatuur duur, wat resulteert in een hoge initiële investering.
Lasersnijtechnologie heeft een revolutie teweeggebracht in de metaalbewerking en biedt een uiterst nauwkeurig alternatief voor conventionele snijmethoden. Met zijn superieure snijsnelheid en uitzonderlijke randkwaliteit is lasersnijden onmisbaar geworden in moderne productieprocessen.
In de afgelopen jaren heeft de komst van fiberlasersnijmachines de efficiëntie en veelzijdigheid van lasersnijbewerkingen verder verbeterd. Deze systemen bieden een betere straalkwaliteit, hoger vermogen en minder onderhoud in vergelijking met hun CO2 tegenhangers.
Het beoordelen van de kwaliteit van een lasersnijmachine is cruciaal om optimale prestaties en productkwaliteit te garanderen. De snijkwaliteit van de machine dient als een primaire indicator voor de algehele capaciteiten. Op basis van uitgebreide industriële ervaring en best practices hebben we negen belangrijke criteria geïdentificeerd die klanten kunnen gebruiken om lasersnijders effectief te evalueren. Deze benchmarks bieden een uitgebreid kader voor het beoordelen van machineprestaties, randkwaliteit en algemene snijprecisie.
Zie ook:
Hardware Factoren
Parameter Factoren
Door deze hardware en parameterfactoren systematisch te optimaliseren, kunt u de kwaliteit van het lasersnijden aanzienlijk verbeteren en schonere sneden, een betere randafwerking en een hogere algemene precisie in metaalbewerkingsprocessen bereiken.
De meeste lasersnijmachines worden aangestuurd door CNC-programma's of geïntegreerd in snijrobots. Als hoogwaardige bewerkingsmethode kan lasersnijden een breed scala aan materialen snijden, waaronder het 2D- of 3D-snijden van dunne materialen. metalen platen.
In de auto-industrie wordt lasersnijtechnologie veel gebruikt voor het snijden van complexe carrosserieplaten en diverse gebogen onderdelen, zoals dakramen.
Volkswagen AG gebruikt bijvoorbeeld een 500W laser om deze onderdelen te snijden. In de luchtvaartindustrie wordt lasersnijtechnologie voornamelijk gebruikt voor het snijden van speciale luchtvaartmaterialen zoals titaniumlegeringen, aluminiumlegeringen, nikkellegeringen, chroomlegeringen, roestvrij staal, ceriumoxide, composietmaterialen, kunststoffen, keramiek en kwarts.
Onderdelen voor de lucht- en ruimtevaart die met lasersnijden worden bewerkt, zijn onder andere vlampijpen voor motoren, dunwandige titaniumlegeringen en vliegtuigframes, titaniumlegering huiden, lange vleugelstijlen, staartvlakken, hoofdrotors van helikopters en keramische warmte-isolatietegels voor spaceshuttles.
Lasersnijden wordt ook veel gebruikt in de niet-metalen materialenindustrie. Het kan zowel harde en brosse materialen snijden, zoals siliciumnitride, keramiek en kwarts, als flexibele materialen, zoals stof, papier, plastic vellen en rubber.
Lasersnijden kan bijvoorbeeld worden gebruikt in de kledingindustrie om 10% tot 12% materiaal te besparen en de efficiëntie met meer dan drie keer te verhogen.
Producten die geschikt zijn voor lasersnijden kunnen over het algemeen worden ingedeeld in drie categorieën:
Recente ontwikkelingen in lasersnijtechnologie zijn onder andere:
Zie ook:
Hieronder vindt u antwoorden op een aantal veelgestelde vragen:
Fiber lasersnijders zijn zeer veelzijdig en kunnen een breed scala aan materialen met hoge precisie en efficiëntie snijden. Tot deze materialen behoren voornamelijk verschillende metalen en sommige kunststoffen.
Voor metalen blinken fiberlasersnijders uit in het snijden van roestvrij staal tot 19 mm dik, koolstofstaal tot 15 mm dik en gegalvaniseerd staal tot 13 mm dik. Ze kunnen ook aluminium en aluminiumlegeringen aan tot 10 mm, koper en koperlegeringen tot 5 mm, titanium tot 7,6 mm en nikkellegeringen tot 10 mm. Het gebruik van hulpgassen zoals stikstof, zuurstof of argon helpt het snijproces te beheersen, vooral bij reflecterende metalen zoals aluminium en koper.
Op het gebied van kunststoffen kunnen fiberlasersnijders materialen zoals acryl (PMMA), polyoxymethyleen (POM), polypropyleen, polyethyleen, nylon en ABS (Acrylonitril Butadieen Styreen) effectief snijden. Voor elk type kunststof is zorgvuldig energiebeheer nodig om problemen als smelten, kromtrekken of het vrijkomen van schadelijke dampen te voorkomen, zodat het snijden soepel verloopt.
Bepaalde materialen zijn ongeschikt voor fiberlasersnijden, waaronder glas, polyvinylchloride (PVC), polycarbonaat, piepschuim en glasvezel of gecoate koolstofvezel, vanwege problemen zoals slechte absorptie van de golflengte, vrijkomen van giftige dampen en brandbaarheid.
Over het algemeen bieden fiber lasersnijders een hoge precisie, hoge verwerkingssnelheden, een lage warmte-beïnvloede zone en verminderde slijtage van het gereedschap, waardoor ze zeer efficiënt zijn voor het snijden van een verscheidenheid aan metalen en sommige kunststof materialen.
Dankzij een aantal belangrijke factoren is fiberlasersnijden zeer nauwkeurig in vergelijking met andere snijmethoden. Fiberlasersnijmachines kunnen extreem nauwe toleranties bereiken, vaak rond de ±0,076 mm (±0,003 inch) of zelfs zo nauwkeurig als ±0,0005 inch (±0,013 mm) onder optimale omstandigheden. Deze precisie is grotendeels te danken aan de kleine bundelvlek van fiberlasers, die wel 10-30 micron kan zijn. Dit resulteert in smallere sleuven en kleinere warmte-beïnvloede zones, waardoor de nauwkeurigheid en kwaliteit van de sneden verbetert.
In vergelijking met andere lasersnijtechnologieën presteren fiberlasers qua precisie beter dan YAG- en CO2-lasers. YAG-lasers bieden doorgaans een procesnauwkeurigheid van ongeveer ±0,05 mm, terwijl CO2-lasers een nauwkeurigheid van ongeveer ±0,1 mm hebben. De superieure straalkwaliteit van fiber lasers, die de diffractielimiet benadert, draagt bij aan gladdere en preciezere sneden die niet geëvenaard worden door YAG- of CO2-lasers.
In tegenstelling tot traditionele snijmethoden zoals plasmasnijden of mechanisch gereedschap, springt fiberlasersnijden er aanzienlijk uit. Plasmasnijden heeft bijvoorbeeld over het algemeen een tolerantie van ±0,020 inch, wat minder nauwkeurig is dan fiberlasersnijden. De precisie van fiberlasers wordt verder verbeterd door het gebruik van optische lenzen om de laserstraal te geleiden, computergestuurde systemen die vaak geïntegreerd zijn met CAD-software en de consistente, intense energiebundel die fiberlasers produceren.
Fiber lasers zijn bijzonder effectief voor het snijden van dunne tot middel dikke metalen platen (tot 8 mm) met hoge snelheid en nauwkeurigheid. Ze zijn vooral favoriet in industrieën die veeleisende normen vereisen, zoals de ruimtevaart, elektronica en autoproductie, vanwege hun vermogen om ingewikkelde ontwerpen en fijne details met hoge precisie te verwerken. Over het algemeen staat fiberlasersnijden bekend om zijn superieure precisie en is het een voorkeurskeuze voor toepassingen waarbij nauwkeurigheid en kwaliteit van cruciaal belang zijn.
Fiber lasersnijden biedt een aantal belangrijke voordelen ten opzichte van traditionele snijmethoden. Een van de belangrijkste voordelen is de hoge precisie en nauwkeurigheid, die extreem fijne en gedetailleerde sneden met nauwe toleranties mogelijk maakt, waardoor het ideaal is voor ingewikkelde ontwerpen en complexe geometrieën. Deze precisie zorgt ook voor minimale materiaalverspilling en een afwerking van hoge kwaliteit, waardoor er minder extra bewerkingen nodig zijn.
In termen van snelheid en efficiëntie werken fiberlasersnijders veel sneller dan traditionele methoden, waardoor de productiviteit aanzienlijk toeneemt en de productietijden korter worden. Deze hoge snelheid is vooral duidelijk bij het snijden van dunne materialen, waar fiberlasers andere snijtechnologieën met een aanzienlijke marge kunnen overtreffen.
Energie-efficiëntie is een ander belangrijk voordeel. Fiber lasers zetten een hoger percentage elektrische energie om in laserlicht, wat resulteert in een lager stroomverbruik en lagere operationele kosten. Deze energie-efficiëntie vertaalt zich ook in een kleinere ecologische voetafdruk, waardoor fiberlasersnijden een duurzamere optie is.
Fiber lasersnijmachines staan ook bekend om hun veelzijdigheid, ze snijden effectief een breed scala aan materialen, waaronder sterk reflecterende metalen zoals aluminium, koper en messing, wat een uitdaging kan zijn voor andere lasertypes. Deze veelzijdigheid maakt ze geschikt voor verschillende industriële toepassingen.
De onderhouds- en operationele kosten zijn lager bij fiberlasers vanwege hun solid-state ontwerp, dat minder bewegende onderdelen en verbruiksartikelen vereist. Dit leidt tot minder stilstand en lagere onderhoudskosten, waardoor de kosteneffectiviteit nog verder toeneemt.
Het compacte ontwerp van fiberlasersnijmachines bespaart kostbaar vloeroppervlak in productieomgevingen, waardoor ze een ideale keuze zijn voor faciliteiten met beperkte ruimte. Bovendien zorgt de stabiele en geavanceerde technologie die in fiberlasers wordt gebruikt voor consistente prestaties en betrouwbaarheid.
Over het algemeen biedt fiberlasersnijden superieure precisie, snelheid, energie-efficiëntie, veelzijdigheid en lagere operationele kosten, waardoor het een voordelige keuze is ten opzichte van traditionele snijmethoden voor veel industriële toepassingen.
De kosten van fiber lasersnijmachines zijn over het algemeen hoger in vergelijking met andere soorten lasersnijmachines vanwege hun geavanceerde technologie en superieure mogelijkheden. Fiber lasersnijmachines, geoptimaliseerd voor het snijden van metalen met hoge precisie en snelheid, variëren meestal van $20.000 tot $500.000. Deze prijsvariatie wordt beïnvloed door factoren zoals het uitgangsvermogen (variërend van 500W tot meer dan 20W). Deze prijsvariatie wordt beïnvloed door factoren zoals vermogen (variërend van 500W tot meer dan 20kW), grootte van het snijbed en specifieke kenmerken die zijn afgestemd op industriële toepassingen.
CO2 lasersnijmachines daarentegen, die vaker gebruikt worden voor niet-metalen materialen zoals hout, acryl en stof, hebben een lagere prijsklasse van ongeveer $8.000 tot $50.000. Instapmodellen CO2 lasersnijmachines zijn te vinden voor minder dan $5.000, terwijl topmodellen oplopen tot $50.000. CO2-machines op instapniveau zijn te vinden voor minder dan $5.000, terwijl high-end modellen tot $50.000 gaan.
Diode lasersnijders, geschikt voor zowel beginners als gevorderden, zijn betaalbaarder met prijzen van $5.000 tot $20.000. Nd: YAG lasersnijders, bekend om hun veelzijdigheid in het snijden van verschillende materialen waaronder metalen en kunststoffen, hebben een prijsbereik tussen $40.000 en $300.000.
Als we kijken naar de bedrijfs- en onderhoudskosten, dan bieden fiberlasermachines over het algemeen lagere bedrijfskosten in vergelijking met CO2 lasers. Een 4kW fiberlasersysteem heeft bijvoorbeeld gemiddelde kosten van $6,24 per uur, vergeleken met $12,73 per uur voor een 4kW CO2 lasersnijder. Bovendien hebben fiberlasers meestal minder onderhoud nodig omdat er minder bewegende onderdelen zijn, waardoor de kosten op lange termijn nog lager uitvallen.
Over het algemeen hebben fiberlasersnijmachines een hogere initiële investering, maar hun efficiëntie, precisie en lagere bedrijfskosten kunnen een aanzienlijke waarde op lange termijn bieden, vooral voor bedrijven die zich richten op het snijden van metalen.
De nieuwste trends in fiberlasersnijtechnologie worden gekenmerkt door aanzienlijke vooruitgang in vermogen, precisie, automatisering en duurzaamheid. Fiberlasers met een hoog vermogen, die kunnen werken tot 80 kW, zorgen voor hogere snijsnelheden en de verwerking van dikkere materialen met uitzonderlijke nauwkeurigheid, waardoor ze ideaal zijn voor veeleisende industrieën zoals lucht- en ruimtevaart en zware productie. De straalvormingstechnologie is ook verbeterd, waardoor de laserstraal op kleinere diameters wordt gericht om warmte-beïnvloede zones en materiaalvervorming te minimaliseren, wat resulteert in schonere sneden.
Adaptieve optiek is een andere trend, die real-time aanpassingen aan de laserstraal mogelijk maakt voor variaties in materiaaldikte en omgevingscondities, waardoor de nauwkeurigheid en snelheid van het snijden verbetert. Automatisering en integratie komen steeds vaker voor, met slimme softwarepakketten en dynamische snijalgoritmen die workflows stroomlijnen en prestaties optimaliseren. De integratie van robotica verhoogt de productiviteit en verlaagt de arbeidskosten door laadsystemen en productieprocessen te automatiseren.
Kunstmatige intelligentie en machine learning staan op het punt een revolutie teweeg te brengen in het fiberlasersnijden door machines in staat te stellen instellingen te optimaliseren op basis van historische gegevens en de meest efficiënte snijpaden te voorspellen. Deze technologie belooft afval te verminderen en de output te verhogen. De veelzijdigheid van fiberlasers neemt ook toe, met de mogelijkheid om een verscheidenheid aan hightech materialen te snijden, zoals composieten en legeringen, wat cruciaal is voor geavanceerde productiesectoren.
Duurzaamheid is een groeiend aandachtspunt, met energie-efficiënte machines die minder energie verbruiken met behoud van hoge prestaties, in lijn met milieudoelstellingen. De markt voor lasersnijmachines zal naar verwachting aanzienlijk groeien, gedreven door de toepassing van fiberlasertechnologie en de vraag naar precisie-engineeringoplossingen. Over het geheel genomen benadrukken deze trends de voortdurende evolutie van fiberlasersnijtechnologie naar meer efficiëntie, aanpassingsvermogen en verantwoordelijkheid voor het milieu.