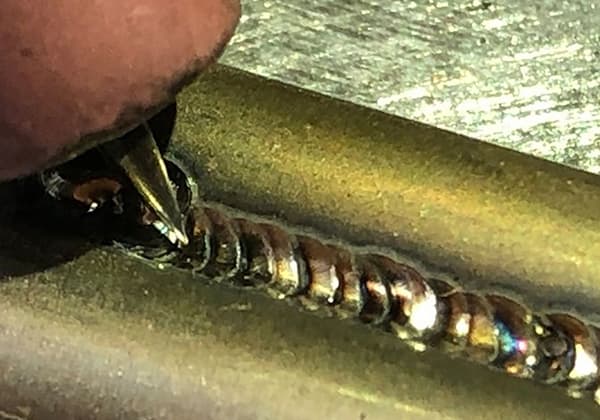
Stel je voor dat je twee heel verschillende metalen naadloos met elkaar kunt laten versmelten. Dit artikel onthult zeven effectieve methoden voor het lassen van messing en roodkoper, metalen die bekend staan om hun unieke eigenschappen en uitdagingen. Van gaslassen tot argonbooglassen, ontdek de technieken, gereedschappen en tips die nodig zijn om perfecte lassen te maken. Aan het eind zult u begrijpen hoe u deze metalen met vertrouwen kunt verwerken, zodat u verzekerd bent van sterke verbindingen van hoge kwaliteit in uw projecten. Duik in de wereld van het lassen en verbeter je vaardigheden met deze essentiële inzichten.
Messing
Messing is een veelzijdige koper-zinklegering die bekend staat om zijn opvallende gouden tint. Standaard messing bestaat voornamelijk uit koper en zink, terwijl speciale messing elementen bevat zoals lood, tin, mangaan, nikkel, ijzer en silicium om specifieke eigenschappen te verbeteren.
Het kopergehalte in messing ligt meestal tussen 62% en 68%, wat resulteert in een smeltpunt tussen 934°C en 967°C (1713°F tot 1773°F). Deze samenstelling zorgt voor een uitstekende slijtvastheid en gunstige mechanische eigenschappen, waardoor messing een ideaal materiaal is voor de fabricage van drukvaten en andere veeleisende toepassingen.
Speciaal messing heeft een superieure sterkte, hardheid en weerstand tegen chemische corrosie in vergelijking met standaardlegeringen. Deze verbeterde eigenschappen maken ze bijzonder geschikt voor de productie van naadloze buizen die worden gebruikt in kritieke toepassingen zoals warmtewisselaars, condensors, cryogene pijpleidingen en onderzeese transportsystemen.
De veelzijdigheid van messing gaat verder dan pijpleidingtoepassingen. De uitstekende vervormbaarheid en bewerkbaarheid maken het een optimale keuze voor de productie van plaatwerk, staven, precisiegietwerk en ingewikkelde onderdelen. Het hoge kopergehalte draagt bij aan de uitzonderlijke plasticiteit van messing, waardoor complexe vervormingen mogelijk zijn die vaak nodig zijn bij de productie van drukapparatuur.
Bovendien biedt messing extra voordelen zoals antimicrobiële eigenschappen, elektrische geleiding en akoestische eigenschappen, waardoor het gebruik in verschillende industrieën toeneemt. Moderne legeringstechnieken en warmtebehandelingen maken op maat gemaakte messingsamenstellingen mogelijk om te voldoen aan specifieke prestatie-eisen, waardoor het gebruik in geavanceerde technische toepassingen mogelijk blijft.
Rood koper
Rood koper, ook wel industrieel zuiver koper of elektrolytisch taai pek (ETP) koper genoemd, is een zeer zuivere koperlegering die bestaat uit ten minste 99,90% koper. De kenmerkende rood-oranje kleur is het resultaat van het hoge kopergehalte en de vorming van een dunne oxidelaag op het oppervlak bij blootstelling aan lucht.
Met een smeltpunt van 1084,62 °C (1984,32 °F) behoudt rood koper een uitstekende thermische stabiliteit zonder fasetransformaties te ondergaan. De dichtheid is ongeveer 8,94 g/cm³ bij 20°C, waardoor het aanzienlijk dichter is dan veel gangbare constructiematerialen. Ter vergelijking: het is ongeveer 4,9 keer dichter dan magnesium (1,738 g/cm³) en ongeveer 14% zwaarder dan zacht staal (7,85 g/cm³).
Het oppervlak van roodkoper vormt gemakkelijk een beschermende oxidelaag wanneer het wordt blootgesteld aan zuurstof, wat resulteert in het karakteristieke roodoranje uiterlijk. Deze natuurlijke patina, die voornamelijk bestaat uit koper(I)oxide (Cu2O), draagt niet alleen bij aan de esthetische aantrekkingskracht, maar biedt ook enige weerstand tegen corrosie. Het zuurstofgehalte in roodkoper varieert meestal van 0,02% tot 0,04% per gewicht, wat opzettelijk wordt gehandhaafd om bepaalde mechanische en elektrische eigenschappen te verbeteren, zoals verbeterde taaiheid en elektrische geleiding.
De methoden voor het lassen van messing zijn onder andere gaslassen, booglassen met koolstof, booglassen met de hand en argon booglassen.
Gaslassen blijft de voorkeursmethode voor het verbinden van messing onderdelen vanwege de lagere vlamtemperatuur in vergelijking met elektrische lasprocessen. Deze eigenschap vermindert de vervluchtiging van zink aanzienlijk, een belangrijk punt van zorg bij het werken met messinglegeringen.
De keuze van het juiste toevoegmateriaal is cruciaal voor succesvol lassen met messinggas. Veel gebruikte lasdraden zijn de kwaliteiten 221, 222 en 224. Deze legeringen zijn speciaal samengesteld met elementen als silicium (0,15-0,5%), tin (0,5-1%) en ijzer (0,1-0,5%). Deze additieven dienen meerdere doelen:
Twee soorten vloeimiddel zijn essentieel voor het lassen met messinggas:
Het op de juiste manier aanbrengen van vloeimiddelen is essentieel voor:
Wanneer het correct wordt uitgevoerd, kan autogeen lassen van messing hoogwaardige, corrosiebestendige verbindingen produceren met uitstekende mechanische eigenschappen en minimale vervorming.
Handmatig booglassen van messing vereist specifieke technieken en overwegingen vanwege de unieke eigenschappen van het materiaal. Naast in de handel verkrijgbare elektroden zoals koper 227 en koper 237, kunnen op maat gemaakte elektroden effectief worden gebruikt voor het lassen van messing. Voor optimale resultaten wordt aanbevolen om een gelijkstroomvoeding met rechte polariteit te gebruiken - waarbij de positieve elektrode op het werkstuk wordt aangesloten en de negatieve elektrode op de lasdraad.
Vóór het lassen is een grondige voorbereiding van het oppervlak van cruciaal belang. Het werkstukoppervlak moet zorgvuldig worden gereinigd om alle oxiden, verontreinigingen of organische resten te verwijderen die de integriteit van de las in gevaar kunnen brengen. Voor een goede laspenetratie en samensmelting moet de groefhoek precies tussen 60 en 70 graden zijn.
Het voorverwarmen van het werkstuk tot een temperatuurbereik van 150 tot 250°C is essentieel om thermische schokken te beperken en het risico op barsten te verminderen. Dit voorverwarmingsproces helpt ook om de koelsnelheid te verlagen, waardoor de interne spanningen in het lasstuk geminimaliseerd worden.
Tijdens het lasproces is het van cruciaal belang om een korte booglengte aan te houden om de warmte-inbreng onder controle te houden en zinkverdamping te minimaliseren, een veel voorkomend probleem bij het lassen van messing. De lastechniek moet gebruik maken van een lineaire beweging zonder transversale of oscillerende bewegingen. Een relatief hoge lassnelheid wordt aanbevolen om overmatige warmteaccumulatie te voorkomen en een optimale vloeibaarheid van het smeltbad te behouden.
Voor messing lassen die blootgesteld worden aan corrosieve omgevingen, zoals zeewater of ammoniakrijke atmosferen, is een warmtebehandeling na het lassen noodzakelijk. Gloeien van het gelaste onderdeel na het lassen helpt om restspanningen te verlichten, de microstructuur te homogeniseren en de algehele corrosiebestendigheid van de verbinding te verbeteren.
Het is vermeldenswaard dat goede ventilatie en persoonlijke beschermingsmiddelen essentieel zijn tijdens het lassen van messing om de risico's van blootstelling aan zinkdampen te beperken. Daarnaast kan het controleren en regelen van de interpasstemperatuur de laskwaliteit en mechanische eigenschappen verder verbeteren.
Voor handmatig TIG-lassen van messing worden vaak gespecialiseerde toevoegmaterialen gebruikt zoals AWS A5.7 ERCuSi-A (draad 221), ERCuSn-A (draad 222) en ERCuAl-A1 (draad 224). Deze legeringen zijn ontworpen om de samenstelling en mechanische eigenschappen van verschillende messingkwaliteiten te evenaren. Als alternatief kan autogeen lassen of het gebruik van toevoegmateriaal met een samenstelling identiek aan het basismetaal worden gebruikt voor optimale metallurgische compatibiliteit.
Bij dit proces kan zowel gelijkstroomelektrodepositief (DCEP) als wisselstroom (AC) worden toegepast. AC-lassen heeft vaak de voorkeur omdat het de vervluchtiging van zink minimaliseert in vergelijking met DCEP, waardoor porositeit wordt verminderd en de samenstelling van de legering behouden blijft. De balans tussen positieve en negatieve halfcycli van de elektrode bij AC-lassen kan worden aangepast om de reinigingswerking en warmte-inbreng te optimaliseren.
Voorverwarmen is over het algemeen niet nodig bij messing TIG-lassen vanwege het goede warmtegeleidingsvermogen van de legering. Maar voor componenten met aanzienlijke diktevariaties (meestal meer dan 4:1) of voor grote, complexe samenstellingen kan voorverwarmen tot 150-200°C nodig zijn om thermische schokken te voorkomen en een gelijkmatige warmteverdeling te garanderen.
Om een optimale laskwaliteit te bereiken, is het van cruciaal belang om een hoge verplaatsingssnelheid te handhaven en toch voor voldoende inbranding te zorgen. Deze aanpak minimaliseert de warmte-beïnvloede zone (HAZ) en vermindert het risico op ontzinking in zinkrijke messinglegeringen. Een juiste stroom beschermgas (meestal zuiver argon bij 10-15 L/min) is essentieel om het smeltbad te beschermen tegen atmosferische verontreiniging.
Warmtebehandeling na het lassen wordt aanbevolen om restspanningen te verminderen en de mechanische eigenschappen van het laswerk te verbeteren. Gloeien bij 300-400°C gedurende 1-2 uur, gevolgd door langzaam afkoelen, verlicht effectief de lasspanning, verbetert de vervormbaarheid en vermindert het risico op spanningscorrosie tijdens het gebruik. Voor kritische toepassingen kan oplossingsgloeien bij hogere temperaturen (650-750°C) worden overwogen om de microstructuur volledig te homogeniseren, gevolgd door snel afschrikken en eventueel verouderen.
Booglassen van messing vereist een zorgvuldige selectie van toevoegmaterialen en lastechnieken om een optimale verbindingskwaliteit te garanderen en zinkverlies te minimaliseren. De keuze van lasdraad hangt af van de samenstelling van het basismetaal, met opties als draad 221 (hoog kopergehalte), draad 222 (uitgebalanceerde koper-zink verhouding) en draad 224 (hoger zinkgehalte). Voor gespecialiseerde toepassingen kunnen op maat gemaakte messing lasdraden worden samengesteld om te voldoen aan specifieke legeringseisen.
Om het lasbad te beschermen en de boogstabiliteit te verbeteren, wordt gasflux 301 aanbevolen. Deze flux helpt oxidatie onder controle te houden, poreusheid te verminderen en het uiterlijk van de lasnaad te verbeteren.
Kort booglassen is de voorkeurstechniek voor het lassen van messing koolstof. Deze methode minimaliseert de warmte-inbreng, waardoor er minder zinkverdamping en verbrandingsverlies optreedt, wat kritisch is bij het lassen van messinglegeringen. De lagere warmte-inbreng helpt ook om vervorming onder controle te houden en de mechanische eigenschappen van het basismetaal te behouden.
Om het lasproces verder te optimaliseren:
Door deze parameters zorgvuldig te regelen, kunnen hoogwaardige messing lassen met minimaal zinkverlies en optimale mechanische eigenschappen worden bereikt met het koolstofbooglasproces.
Roodkoper, ook bekend als industrieel zuiver koper of zuurstofvrij koper (OFC), kan worden verbonden met verschillende lastechnieken, die elk geschikt zijn voor specifieke toepassingen en productieschalen. Voor kleine tot middelgrote componenten worden vaak gaslassen en handmatige boogprocessen gebruikt, terwijl geautomatiseerde methoden de voorkeur hebben voor grotere structuren of productie in grote volumes.
Stootverbindingen zijn de voorkeursmethode voor het lassen van roodkoper, omdat ze optimale sterkte en minimale vervorming bieden. Schootverbindingen en T-verbindingen worden alleen gebruikt als dit noodzakelijk is vanwege specifieke ontwerpeisen of toegankelijkheid. Voor het autogeen lassen van roodkoper zijn er twee primaire opties voor vulmaterialen:
Een neutrale vlam, gekenmerkt door een evenwichtige verhouding tussen zuurstof en acetyleen, is cruciaal voor het autogeen lassen van rood koper. Dit vlamtype handhaaft een temperatuur van ongeveer 3200°C (5792°F) en voorkomt zowel oxidatie als koolstofimpregnatie van het smeltbad. Een juiste afstelling van de vlam is essentieel, omdat een oxiderende vlam kan leiden tot porositeit en verminderde sterkte van de lasverbinding, terwijl een carburerende vlam broosheid in de las kan veroorzaken.
Bij het uitvoeren van autogeen lassen op roodkoper is het belangrijk om het werkstuk voor te verwarmen tot ongeveer 300-500°C (572-932°F) om thermische gradiënten te verminderen en het risico op barsten te minimaliseren. Daarnaast zijn het schoonhouden van de verbindingsoppervlakken en het onder controle houden van de warmte-inbreng kritieke factoren voor het bereiken van lassen van hoge kwaliteit in dit zeer warmtegeleidende materiaal.
Bij handmatig booglassen van roodkoper worden ERCu- of ECu-lasstaven (bijvoorbeeld koper 107) gebruikt met een bijpassend basismetaal van roodkoper (T2, T3). Vóór het lassen is een grondige reiniging van de verbindingsranden van cruciaal belang om oxiden en verontreinigingen te verwijderen en een optimale laskwaliteit te garanderen.
Voor werkstukken met een dikte van meer dan 4 mm is voorverwarmen essentieel om thermische schokken te voorkomen en het risico op barsten te verminderen. De aanbevolen voorverwarmingstemperatuur is 400 tot 500°C, die gecontroleerd moet worden met een gekalibreerde pyrometer. Lassen moet worden uitgevoerd met een DC omgekeerde polariteit (DCEP) stroombron om de boogstabiliteit en penetratie te verbeteren.
Houd tijdens het lasproces een korte booglengte aan om de warmte-inbreng en oxidatie te minimaliseren. De elektrode moet in een rechte lijn gemanipuleerd worden zonder zijdelingse beweging. Een lichte heen en weer gaande beweging kan de controle over het lasbad en de inbranding verbeteren. Gebruik voor lange lassen de back-step lastechniek om de warmteverdeling te regelen en vervorming te verminderen.
De lassnelheid moet worden geoptimaliseerd om een balans te vinden tussen warmte-inbreng en laskwaliteit. Snellere snelheden geven over het algemeen betere resultaten bij koperlassen, omdat ze de warmte-beïnvloede zone (HAZ) beperken en het risico op porositeit verminderen.
Bij meerlaags lassen is grondige reiniging tussen de lagen essentieel. Verwijder alle slak en oxiden tussen de lagen met een roestvast stalen draadborstel om insluitingen te voorkomen en een goede samensmelting te garanderen.
Voldoende ventilatie is van het grootste belang bij het lassen van koper om blootstelling aan potentieel schadelijke dampen te voorkomen. Gebruik plaatselijke afzuiging of draag de juiste ademhalingsbescherming om het risico op kopervergiftiging te beperken.
Een nabehandeling omvat spanningsontlasting door middel van penen. Sla zachtjes op de las terwijl deze nog heet is om drukspanning op te wekken. Dit kan krimpspanningen tegengaan en de mechanische eigenschappen van de las verbeteren. Wees echter voorzichtig om overmatige vervorming of barsten te voorkomen.
Overweeg voor kritieke toepassingen warmtebehandeling na het lassen (PWHT) om de restspanningen verder te verlichten en de microstructuur van de las en HAZ te optimaliseren.
Gerelateerde lectuur: Hoe kies je de juiste lasstaaf?
Bij handmatig TIG-lassen van roodkoper worden gespecialiseerde lasdraden gebruikt zoals ER Cu (draad 201), ERCu-A1 (draad 202) en T2 roodkoperdraad. Voor het lassen is het cruciaal om de laskanten en de oppervlakken van de lasdraad zorgvuldig te reinigen om oxidelagen, olie en andere verontreinigingen te verwijderen. Deze voorbereiding voorkomt defecten zoals porositeit en slakinsluitsels, die de integriteit van de las in gevaar kunnen brengen. Reinigen kan mechanisch (bijv. draadborstelen, slijpen) of chemisch (bijv. zuurbeitsen).
De voorbereiding van de verbinding varieert met de materiaaldikte. Voor diktes onder 3 mm volstaat een vierkante stootvoeg. Platen met een dikte van 3-10 mm vereisen een enkele V-groef met een hoek van 60-70°. Voor diktes van meer dan 10 mm wordt een X-groef (dubbele V) met een hoek van 60-70° aanbevolen. Scherpe randen verdienen de voorkeur boven stompe randen om volledige indringing te garanderen. De wortelspleet voor stootvoegen moet nauwkeurig gecontroleerd worden, variërend van 0,5 tot 1,5 mm, in overeenstemming met de plaatdikte en de geometrie van de groeven om de versmelting te optimaliseren en vervorming te minimaliseren.
Bij het TIG-lassen van roodkoper wordt meestal gebruik gemaakt van DCEP-polariteit (Direct Current Electrode Positive), waarbij de wolfraamelektrode op de positieve pool wordt aangesloten. Deze configuratie bevordert de verwijdering van oxide en verbetert de vloeibaarheid van het smeltbad. Om poreusheid te verminderen en een betrouwbare hechting te garanderen, met name bij de laswortel, is het essentieel om:
De voorverwarmingstemperatuur moet zorgvuldig geregeld worden: 150-300°C voor diktes van minder dan 3 mm en 350-500°C voor dikkere secties. Overmatig voorverwarmen moet vermeden worden omdat het de mechanische eigenschappen van de lasverbinding kan aantasten door overmatige korrelgroei en mogelijke precipitatieharding in bepaalde koperlegeringen.
Het lasproces moet worden uitgevoerd met nauwkeurige controle van de warmte-inbreng, met een korte booglengte en een lichte achterwaartse toortshoek om de penetratie te verbeteren en oxidatie te verminderen. Warmtebehandeling na het lassen kan nodig zijn voor dikke secties om restspanningen te verlichten en de mechanische eigenschappen te optimaliseren.
Booglassen met koolstof is een haalbare techniek voor het verbinden van roodkoperen onderdelen. Dit proces maakt gebruik van koolstof- of grafietelektroden als primaire warmtebron, waarbij de samenstelling van de lasdraad overeenkomt met die van gaslassen. De methode is veelzijdig en maakt zowel lassen als snijden van het basismetaal mogelijk.
Voor optimale resultaten wordt een speciale flux zoals gasflux 301 aanbevolen. Deze flux helpt bij het afschermen van het lasbad tegen atmosferische verontreiniging, verbetert de vloei-eigenschappen en verbetert de algehele laskwaliteit. De keuze tussen koolstof- en grafietelektroden hangt af van de specifieke toepassingsvereisten, waarbij grafiet over het algemeen een betere boogstabiliteit en een lager verontreinigingsrisico biedt.
Bij het lassen van roodkoper met deze methode is het cruciaal om rekening te houden met de hoge thermische geleidbaarheid van het materiaal. Het voorverwarmen van het werkstuk en het handhaven van de juiste tussentemperaturen kunnen warmtegerelateerde defecten helpen voorkomen en zorgen voor een gelijkmatige inbranding. Daarnaast is het beheersen van de warmte-inbreng essentieel om vervorming te minimaliseren en de gewenste eigenschappen van het koper te behouden.
Tijdens het lasproces is goede ventilatie nodig vanwege de mogelijke rookontwikkeling. Operators moeten zich ook bewust zijn van de specifieke uitdagingen die gepaard gaan met het lassen van koper, zoals de neiging van koper om gassen te absorberen als het gesmolten is, wat kan leiden tot poreusheid als er niet goed mee wordt omgegaan.
Tijdens de installatie van apparatuur moest een bedrijf zes koperen buizen (model T2) lassen met afmetingen van Φ 180 mm×10 mm. Voor deze taak werd met succes handmatig wolfraam inert gas gelast. Het lasproces verliep als volgt:
1. Voorbereiding voor het lassen
1.1 De gebruikte lasapparatuur was een WSE-350 AC/DC TIG-lassen machine met DC positieve polariteit. De gekozen lasmateriaal was koperen lasdraad (draad 201) met een diameter van 3 mm. De zuiverheid van het argongas was ≥99,96%.
1.2 De vellingkanten waren uitgelijnd zonder openingen ertussen.
1.3 Het lasgebied van de koperen buis en de koperdraad werden vrijgehouden van olie, oxidatielagen, vocht en andere verontreinigingen en vertoonden een metaalglans.
1.4 Lasparameters: Er werd een cerium wolfraamelektrode van Φ3mm gebruikt, samen met een mondstuk van Φ14mm. De lasstroom werd ingesteld tussen 160~180A en de argongasstroom was 15L/min.
1.5 Voorverwarmen: Vanwege de hoge thermische geleidbaarheid en thermische uitzettingscoëfficiënt van koper en de brosheid van koper bij verhitting, werden de schuine kant van de koperen buis en het 60 mm gebied aan weerszijden voorverwarmd voor het lassen. Dit voorverwarmen werd uitgevoerd met een oxy-acetyleen vlam, waarmee een temperatuur van ongeveer 500℃ werd bereikt. De temperatuur werd gemeten met een puntcontactthermometer.
1.6 Twee delen van de buis werden gehecht gelast (waarbij de omtrek van de buis in drie gelijke delen werd verdeeld, waarvan er twee gehecht werden gelast en één het beginpunt van de las was). De hechtlassen hadden een vereiste lengte ≥10 mm en een geschikte lashoogte van 3 mm.
2. Lasprocedure
Het lasproces werd in twee lagen uitgevoerd: een aanloop en een afloop. Alle lassen werden uitgevoerd in de roterende laspositie, specifiek tussen 10 en 11:30 op een wijzerplaat, met een willekeurige opwaartse rotatie tijdens het lassen.
2.1 Wortelronde: De root-run werd uitgevoerd met een linkse lastechniek. Tijdens het lassen werden maatregelen genomen om de vorming van gaszakken, slakinsluitsels, lasspatten en onvolledige inbranding te voorkomen. De hoek tussen de lasdraad en het buisoppervlak werd zo klein mogelijk gehouden om de effectiviteit van de argon afscherming te verbeteren, zoals te zien is in figuur 7.
Zorg voor een soepele beweging van het laspistool en een goede regeling van de temperatuur van het smeltbad. Deze mag niet te hoog of te laag zijn om het lasproces soepel te laten verlopen. Het is cruciaal om de stroom van het gesmolten koper in het smeltbad nauwlettend in de gaten te houden en de timing van smelten en inbranding te beheersen.
Wanneer het gesmolten metaal in het smeltbad licht begint te zinken, duidt dit op penetratie (met een goede basiswortelvorming).
Gebruik een "onderbroken" draadaanvoermethode voor het inbrengen van de lasdraad, dat wil zeggen dat de koperen lasdraad afwisselend vooruit en achteruit gaat. De draad moet "snel" aanvoeren en "netjes" terugtrekken, waarbij deze toestand gehandhaafd blijft terwijl er gelijkmatig naar voren wordt gelast. Als de lassnelheid iets te laag is of de inbranding ongelijkmatig, kan onvolledige inbranding of doorbranding optreden, met lasknobbeltjes als gevolg. De boogslag, verbinding en bedieningsmethode zijn hetzelfde als de eerder genoemde argonbooglasmethode.
2.2 Lassen van de deklaag: Het laspistool zwenkt naar links en rechts en de lasdraad wordt aangevoerd met de beweging van het laspistool. Wanneer de boog naar beide kanten van de groef beweegt, pauzeer dan even en voeg lasdraad toe om de groef te vullen en 1,5~2mm boven het buisoppervlak uit te komen. Het laspistool en de lasdraad moeten goed samenwerken en gelijkmatig zwenken om de consistentie van de vorm van het smeltbad te controleren en een las van uitstekende kwaliteit van binnen en buiten te produceren.
1) Tijdens het lassen is "wolfraam aanraken" (d.w.z. dat de wolfraamelektrode in contact komt met de lasdraad of het smeltbad) ten strengste verboden. Als er tijdens het lassen "wolfraamcontact" optreedt, zal er een grote hoeveelheid metaalstof en dampen in het smeltbad terechtkomen, wat resulteert in talrijke honingraatvormige poriën of scheuren in de las. Als er "tungsten touching" optreedt, stop dan met lassen, behandel het door schoon te slijpen en vervang de wolfraamelektrode of slijp de wolfraamtip opnieuw tot het metaal vrij is van kopervlekken.
2) Zorg ervoor dat de overlappende lijnen goed contact maken en voorkom krassen op het buisoppervlak.
3) Nadat de las enigszins is afgekoeld, draait u de pijp en stoot u hem stevig aan.
4) Controleer de temperatuur van de tussenlaag. Als het lassen moeilijk gaat, duidt dit op een te lage temperatuur. Verwarm opnieuw tot boven de 500℃ voordat je opnieuw gaat lassen om onvolledige versmelting of slechte versmelting te voorkomen.
5) Zorg voor een goede samensmelting, een iets hogere lassnelheid en geschikte draadtoevoer. Besteed aandacht aan het gelijktijdig smelten van het basismetaal en de lasdraad om samen te smelten om onvolledige smelting of slechte smeltfouten te voorkomen.
6) Bij het doven van de lasboog mag het laspistool niet onmiddellijk worden opgetild. Blijf de post-flow schermgas functie om het lasbad te beschermen om de vorming van poriën te voorkomen.
Als er na inspectie geen defecten zijn zoals poriën, scheuren of slakinsluitsels, verwarm het lasgebied van de gelaste pijpverbinding dan opnieuw tot 600~700℃ en blus het vervolgens af met kraanwater om de plasticiteit van het lasgebied te verhogen.
De waterstop in het koelbad van de hoogoven bestaat uit aan elkaar gelaste δ=2 mm dunne paarse koperen platen. Lassen is een uitdaging vanwege de uitstekende thermische geleidbaarheid van koper.
Ofwel is de temperatuur onvoldoende om een smeltbad te vormen, wat resulteert in ongesmolten of slecht gesmolten metaal in de las, ofwel is de temperatuur te hoog, waardoor een groot deel van de laszone smelt, wat resulteert in lasdefecten zoals doorbranden of lasklonten. Het lassen van dunne paarse koperplaten is een nogal "lastig" probleem.
Het probleem kan effectief worden opgelost door gebruik te maken van "messing hardsolderen"Lasmethode. De voorbereidingen voor het lassen en het lasproces zijn als volgt:
1) Ontsmet 60 mm aan elke kant van de lasnaad en gebruik een staalborstel om het te polijsten zodat de metallic glans zichtbaar wordt.
2) De werkstukken worden gekoppeld zonder groef en de koppelspleet moet minder dan 1 mm zijn.
3) Gebruik Ф3mm silicium messing lasdraad (draad 224) met lasstroom 301.
4) Nivelleer het te lassen gebied (de onderlegger is gemaakt van vlakke staalplaatdie dikker moet zijn om thermische vervorming te voorkomen).
5) Voorverwarmen. Twee lassers gebruiken middelzware lastoortsen en neutrale vlammen om het lasgebied gelijktijdig te verwarmen tot een temperatuur van 500~600℃. Eén persoon last en de ander blijft de laslocatie verwarmen om een stabiele voortgang van het lasproces te garanderen.
6) Het voorverwarmlasapparaat gebruikt een neutrale vlam en het lasapparaat gebruikt een licht oxiderende vlam.
7) Puntlassen en het formele lassen moet continu worden uitgevoerd, met een puntlasafstand van 60~80mm. Het puntlaspunt moet kleiner zijn.
8) Let goed op de temperatuurveranderingen in het lasgebied tijdens het verwarmen en lassen om te voorkomen dat de temperatuur te hoog of te laag is. Over het algemeen wordt dit visueel beoordeeld aan de hand van donkerrood (550~600℃).
9) De beweging van het lasmondstuk moet stabiel zijn en met een gelijkmatige snelheid vooruit bewegen. De kern van de vlam (witte punt) moet zich 5 ~ 8 mm boven het smeltbad bevinden. De omtrek van de vlam moet altijd het smeltbad bedekken om contact met lucht te voorkomen. Zorg ervoor dat de messingvloeistof zich op natuurlijke en soepele wijze naar beide kanten van de las verspreidt en in de spleet doordringt.
10) Om de kristallijne structuur van de lasnaad dichter te maken en de sterkte en taaiheid te verbeteren, tik je na het lassen met een kleine hamer op de lasnaad.
11) Voer na het lassen een lekdichtheidstest uit.