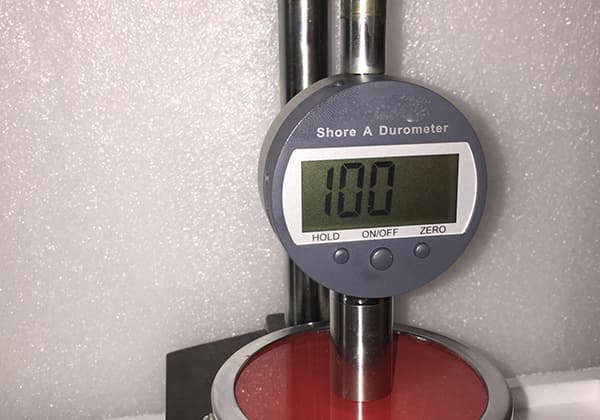
Heb je je ooit afgevraagd wat de kunst en wetenschap is achter de slanke metalen behuizingen van je favoriete gadgets? In deze blogpost duiken we in de fascinerende wereld van plaatbewerking. Als ervaren werktuigbouwkundig ingenieur deel ik mijn inzichten in de materialen, processen en ontwerpprincipes die vlakke metalen platen transformeren tot de complexe vormen waarin onze moderne elektronica is ondergebracht. Bereid je voor op het verkennen van de geavanceerde technieken en creatieve probleemoplossing die plaatbewerking tot een cruciaal onderdeel van productontwikkeling maken.
Plaatbewerking is een uitgebreid koudverwerkingsproces voor plaatmetaal (meestal minder dan 6 mm), inclusief scheren, blanking, buigen, lassenklinken, spuitgieten en oppervlaktebehandelingenz.
De opmerkelijke eigenschap is dat de dikte van hetzelfde onderdeel hetzelfde is.
Het fabricageproces van plaatmetaal, inclusief:
Plaatmaterialen zijn de meest gebruikte materialen in het structurele ontwerp van communicatieproducten.
Inzicht in de uitgebreide prestaties van materialen en de juiste materiaalselectie hebben een belangrijke invloed op productkosten, productprestaties, productkwaliteit en verwerkbaarheid.
1) Gebruik gewone metalen materialen om materiaalspecificaties te beperken en controleer zoveel mogelijk binnen het materiaalhandboek van het bedrijf;
2) Beperk in hetzelfde product de verscheidenheid aan materialen en de specificaties van de plaatdikte zoveel mogelijk;
3) Probeer onder het uitgangspunt van het waarborgen van de functie van de onderdelen goedkope materialen te gebruiken, het verbruik van materialen te verminderen en de materiaalkosten te verlagen;
4) Voor de kast en enkele grote stekkerdozen is het noodzakelijk om het gewicht van de hele machine te verminderen;
5) Naast het uitgangspunt om de functie van de onderdelen te garanderen, moet er ook rekening mee worden gehouden dat de stempelprestaties van het materiaal moeten voldoen aan de verwerkingseisen om de rationaliteit en kwaliteit van de verwerking van de producten te garanderen.
Stalen plaat
1) Koudgewalste staalplaat
Koudgewalst plaatstaal is de afkorting van koudgewalst koolstofstaal voor constructiedoeleinden.
Het wordt verder koudgewalst van een warmgewalst koolstofstaal voor constructiedoeleinden tot een staalplaat met een dikte van minder dan 4 mm.
Omdat de plaat bij normale temperatuur wordt gewalst, ontstaat er geen ijzeroxideschaal. Daarom is de oppervlaktekwaliteit van de koude plaat goed en is de maatnauwkeurigheid hoog.
Bovendien zijn de gloeiproces maakt dat het betere mechanische eigenschappen en procesprestaties heeft dan warmgewalst staal vellen.
Veelgebruikte kwaliteiten zijn staal met een laag koolstofgehalte 08F en 10#, die een goede kwaliteit hebben. blanking en buigeigenschappen.
2) Continu gegalvaniseerd zink koudgewalst plaatstaal
Continu gegalvaniseerde zink koudgewalste staalplaat, oftewel "elektrolytische plaat".
Verwijst naar het proces van het continu neerslaan van zink uit een waterige oplossing van zinkzout op een vooraf geprepareerde staalplaat om een gegalvaniseerde oppervlaktelaag te verkrijgen onder invloed van een elektrisch veld op een elektrolytische verzinklijn.
Vanwege de beperkingen van het proces is de coating dun.
3) Continu thermisch verzinkte staalplaat
Continu thermisch verzinkte staalplaat wordt aangeduid als verzinkte plaat of blik.
De koudgewalste continu thermisch verzinkte staalplaat en staalband met een dikte van 0,25 tot 2,5 mm worden eerst onderworpen aan een vlamverwarmde voorverwarmingsoven om restolie van het oppervlak af te branden.
Tegelijkertijd wordt er een ijzeroxidelaag gevormd op het oppervlak.
Daarna wordt het verhit tot 710~920 °C in een reductie-gloeioven met H2- en N2-menggassen om de ijzeroxidelaag te reduceren tot sponsijzer.
Nadat de oppervlaktegeactiveerde en gezuiverde strip is afgekoeld tot een temperatuur die iets hoger is dan die van het gesmolten zink, gaat hij de zinkpot in bij 450-460 °C.
De oppervlaktedikte van de zinklaag wordt geregeld met een luchtmes.
Pas ten slotte een passiveerbehandeling met chromaatoplossing toe om de weerstand tegen witte roest te verbeteren.
Vergeleken met het oppervlak van elektrolytisch verzinkte platen is de coating dikker en wordt deze voornamelijk gebruikt voor plaatdelen die een hoge corrosiebestendigheid vereisen.
4) Aluminium-zink plaat
De aluminium-zink legering coating van de aluminium-zink plaat is samengesteld uit 55% aluminium, 43,4% zink en 1,6% silicium bij 600 ° C.
Vormde een dichte quaternaire kristalbeschermende laag met uitstekende corrosieweerstand, de normale levensduur van tot 25 jaar, 3-6 keer langer dan een verzinkte plaat en vergelijkbaar met roestvrij staal.
De corrosieweerstand van de aluminium-zinkplaat is te danken aan de barrièrefunctie van aluminium en de opofferingsbescherming van zink.
Wanneer zink wordt opgeofferd voor het trimmen, krassen en schuren van de coating, vormt aluminium een onoplosbare oxidelaag die als barrière fungeert.
De bovenstaande 2), 3) en 4) staalplaten worden samen beklede staalplaten genoemd en worden veel gebruikt in communicatieapparatuur.
Na de gecoate staalplaat verwerkt is, kan het niet langer gegalvaniseerd of geverfd worden.
De incisie kan direct worden gebruikt zonder speciale behandeling en er kan een speciale fosfateringsbehandeling worden uitgevoerd om de roestbestendigheid van de incisie te verbeteren.
Uit de kostenanalyse blijkt dat de doorlopende elektrolytisch verzinkte staalplaat wordt gebruikt en dat het verwerkingsbedrijf de onderdelen niet naar de galvanisatie hoeft te sturen, wat tijd en transportkosten bespaart.
Bovendien worden de onderdelen niet gebeitst voor het spuiten, wat de verwerkingsefficiëntie verbetert.
5) Roestvrij staal plaat
Vanwege zijn sterke corrosiebestendigheid, goede elektrische geleidbaarheid, hoge sterkte, enz. wordt het veel gebruikt.
Maar we moeten ook kijken naar de tekortkomingen:
Aluminium en platen van aluminiumlegeringen
De veelgebruikte platen van aluminium en aluminiumlegeringen bestaan voornamelijk uit de volgende drie materialen:
Anti-roest aluminium 3A21, het oude merk LF21, is een AL-Mn legering. Het is het meest gebruikte roestwerende aluminium.
De sterkte van deze legering is niet hoog (alleen hoger dan industrieel zuiver aluminium) en kan niet warmtebehandeld en versterkt worden.
Daarom wordt de koudverwerkmethode vaak gebruikt om de mechanische eigenschappen te verbeteren en heeft het een hoge plasticiteit in de gegloeide toestand en de plasticiteit is goed in de half-koude uitharding.
Het heeft een lage plasticiteit, goede corrosiebestendigheid en goede lasbaarheid tijdens koudvervormen.
Anti-roest aluminium 5A02 is het oude merk LF2 serie AL-Mg anti-roest aluminium.
Vergeleken met 3A21, heeft 5A02 hogere sterkte, vooral hoog vermoeiingssterktehoge plasticiteit en corrosiebestendigheid.
De warmtebehandeling kan niet worden versterkt en de lasbaarheid door contactlassen en waterstofatoomlassen is goed en er is een neiging tot kristalscheuren tijdens het lassen. argon booglassenen de legering heeft de neiging om kristalscheuren te vormen tijdens koudvervormen.
De legering heeft een goede bewerkbaarheid in de koudhardende en half-koudhardende toestand, en de bewerkbaarheid is slecht in de gegloeide toestand, en het kan worden gepolijst.
Hard aluminium 2A06 is het oude LY6, een veelgebruikte soort hard aluminium.
Hard aluminium en superhard aluminium hebben een hogere sterkte en hardheid dan gewone aluminiumlegeringen en kan worden gebruikt als sommige plaatmaterialen.
De plasticiteit is echter slecht en het buigen kan niet worden uitgevoerd en het buigen kan scheuren of barsten veroorzaken in het buitenste afgeronde gedeelte.
Er zijn nieuwe normen voor de rang en status van aluminiumlegering. De standaardcode van de methode voor de weergave van de rang is GB/T16474-1996, de statuscode is GB/T16475-1996 en de vergelijkingstabel met de oude norm staat in Tabel 1-1 hieronder:
Tabel 1-1 Vergelijkingstabel van nieuw en oud aluminiumlegeringen
Rang | Staten | ||||||||
Nieuw | Oud | Nieuw | Oud | Nieuw | Oud | Nieuw | Oud | Nieuw | Oud |
1070A | L1 | 5A06 | LF6 | 2A80 | LD8 | 2A14 | LD10 | H12 | R |
1060 | L2 | 5A12 | LF12 | 2A90 | LD9 | 2A50 | LD5 | O | M |
1050A | L3 | 8A06 | L6 | 4A11 | LD11 | 6A02 | LD2 | T4 | CZ |
1035 | L4 | 3A21 | LF21 | 6063 | LD31 | 7A04 | LC4 | T5 | RCS |
1200 | L5 | 2A02 | LY2 | 6061 | LD30 | 7A09 | LC9 | T6 | CS |
5A02 | LF2 | 2A06 | LY6 | 2A11 | LY11 | ||||
5A03 | LF3 | 2A16 | LY16 | 2A12 | LY12 | ||||
5A05 | LF5 | 2A70 | LD7 | 2A13 | LY13 |
Platen van koper en koperlegeringen
Er zijn twee hoofdtypen veelgebruikte platen van koper en koperlegeringen: koper T2 en messing H62.
Koper T2 is het meest gebruikte pure koper. Het ziet er paars uit en wordt ook wel koper genoemd. Het heeft een hoog elektrisch en thermisch geleidingsvermogen, een goede corrosiebestendigheid en vervormbaarheid.
Maar de sterkte en hardheid zijn veel lager dan bij messing en de prijs is erg duur.
Het wordt voornamelijk gebruikt als corrosie-element voor geleidende, warmtegeleidende en consumptiegoederen. Het wordt over het algemeen gebruikt voor onderdelen van de stroomvoorziening die grote stromen moeten geleiden.
rass H62, een messing met een hoog zinkgehalte, heeft een hoge sterkte en een uitstekende koude en warme verwerkbaarheid en is gemakkelijk te gebruiken voor diverse vormen van pers die werkt en snijden.
Hoofdzakelijk gebruikt voor diverse dieptrekken en buigkracht delen, het geleidingsvermogen is niet zo goed als koper, maar het heeft een betere sterkte en hardheid, en de prijs is relatief matig.
Om te voldoen aan de eisen voor elektrische geleiding wordt zoveel mogelijk messing H62 gebruikt in plaats van koper, waardoor de materiaalkosten sterk kunnen worden verlaagd.
Bijvoorbeeld, stroomrails, de meeste van de huidige stroomrails zijn gemaakt van messing H62, die volledig bleek te voldoen.
Er zijn drie belangrijke soorten plaatwerk verwerking: ponsen en stansen, buigen en strekken.
Verschillende verwerkingstechnieken stellen verschillende eisen aan de plaat.
De selectie van plaatmetaal moet ook gebaseerd zijn op de algemene vorm en de verwerkingstechnologie van het product.
De invloed van materialen op blanking
Blanking vereist dat de plaat voldoende plastisch is om ervoor te zorgen dat de plaat niet barst bij het ponsen.
Zachte materialen (zoals zuiver aluminium, roestvast aluminium, messing, koper, staal met laag koolstofgehalte enz.) hebben goede ponsprestaties en na het ponsen kunnen onderdelen met een gladde dwarsdoorsnede en kleine helling worden verkregen;
Harde materialen (zoals hoog koolstofstaal) hebben een slechte kwaliteit na het ponsen en de ongelijkmatigheid van de doorsnede is groot, vooral bij dikke platen.
Bij brosse materialen is de kans op scheuren na het ponsen groot, vooral bij een kleine breedte.
Het effect van materialen op buigen
Platen die gebogen en gevormd moeten worden, moeten voldoende plastisch zijn en een lage vloeigrens hebben.
Een sterk plastische plaat die minder snel scheurt wanneer hij gebogen wordt.
Platen met een lagere rekgrens en elasticiteitsmodulus hebben minder springrug vervorming na het buigen en het is gemakkelijk om een nauwkeurige gebogen vorm te verkrijgen.
Kunststof materialen zoals laag koolstofstaal, messing en aluminium met een koolstofgehalte van <0,2% worden gemakkelijk gebogen en gevormd;
Meer brosse materialen, zoals fosforbrons (QSn6,5 ~ 2,5), verenstaal (65Mn), hard aluminium, superhard aluminium, etc., moeten een groot relatief buigradius (r / t) bij het buigen, anders kunnen er scheuren ontstaan tijdens het buigen.
Speciale aandacht moet worden besteed aan de keuze van de harde en zachte toestand van het materiaal, die een grote invloed heeft op de buigeigenschappen.
Bij veel brosse materialen kan de buiging ervoor zorgen dat de buitenste straal barst of zelfs breekt.
Er zijn ook stalen platen met een hoger koolstofgehalte.
Als je een harde toestand kiest, zal het buigen ook scheuren of zelfs breuk van de buitenste straal veroorzaken.
Deze moeten zoveel mogelijk worden vermeden.
Effect van materialen op de verwerking van tekeningen
Het uitrekken van het vel, vooral het dieptrekken, is moeilijk in de plaatbewerking proces.
Niet alleen moet de rekdiepte zo klein mogelijk zijn, ook moet de vorm zo eenvoudig mogelijk en glad zijn. Bovendien moet het materiaal een goede plasticiteit hebben.
Anders wordt het hele onderdeel gemakkelijk vervormd, gedeeltelijk gekreukeld of zelfs uitgetrokken bij het uitrekkende gedeelte.
De vloeigrens is laag en de richtingscoëfficiënt van de plaatdikte is groot.
Hoe kleiner de vloeiverhouding σs/σb van de plaat, hoe beter de ponsprestaties en hoe groter de limiet van de primaire vervorming.
Wanneer de richtingscoëfficiënt van de plaatdikte >1 is, is de vervorming in de breedterichting gemakkelijker dan de vervorming in de dikterichting.
Hoe groter de waarde van de rekstraal R, hoe kleiner de kans op verdunning en breuk tijdens het rekproces en hoe beter de trekeigenschappen.
Veel voorkomende trekeigenschappen zijn: zuiver aluminium plaat, 08Al, ST16, SPCD.
Materiaal invloed op stijfheid
Bij het ontwerp van plaatstalen constructies wordt vaak niet voldaan aan de stijfheid van plaatstalen constructiedelen.
Constructieontwerpers gebruiken vaak koolstofarm staal of roestvrij staal in plaats van koolstofarm staal, of vervangen de gewone aluminiumlegering door een harde aluminiumlegering met hoge sterkte en hardheid, en er wordt verwacht dat dit de stijfheid van het onderdeel zal verhogen.
Er is eigenlijk geen duidelijk effect.
Voor materialen van hetzelfde substraat kunnen de sterkte en hardheid van het materiaal sterk worden verbeterd door warmtebehandeling en legeren.
Maar de verandering in stijfheid is klein.
Om de stijfheid van het onderdeel te verbeteren, kan alleen door het materiaal en de vorm van het onderdeel te veranderen een bepaald effect worden bereikt.
Zie Tabel 1-2 voor de elasticiteitsmodulus en afschuifmodulus van verschillende materialen.
Tabel 1-2 Elastische modulus en afschuifmodulus van gewone materialen
Elastische modulus E | Schuifmodulus G | |
---|---|---|
Item | GPa | GPa |
Grijs gietijzer | 118~126 | 44.3 |
Nodulair gietijzer | 173 | |
Koolstofstaal, Nikkel-chroomstaal | 206 | 79.4 |
Gietstaal | 202 | |
Gewalst zuiver koper | 108 | 39.2 |
Koudgetrokken zuiver koper | 127 | 48 |
Gewalst fosforbrons | 113 | 41.2 |
Koudgetrokken messing | 89~97 | 34.3~36.3 |
Gewalst mangaanbrons | 108 | 39.2 |
Gewalst aluminium | 68 | 25.5~26.5 |
Aluminium draad eruit trekken | 69 | |
Gegoten aluminium brons | 103 | 11.1 |
Gegoten tinbrons | 103 | |
Harde aluminiumlegering | 70 | 26.5 |
Zink walsen | 82 | 31.4 |
Lood | 16 | 6.8 |
Glas | 55 | 1.96 |
Plexiglas | 2.35~29.4 | |
Rubber | 0.0078 | |
Bakeliet | 1.96~2.94 | 0.69~2.06 |
Fenol plastic | 3.95~8.83 | |
Celluloid | 1.71~1.89 | 0.69~0.98 |
Nylon 1010 | 1.07 | |
Hard tetrachloorethyleen | 3.14~3.92 | |
Polytetrachloorethyleen | 1.14~1.42 | |
Polyethyleen onder lage druk | 0.54~0.75 | |
Hogedruk polyethyleen | 0.147~0.24 | |
Beton | 13.73~39.2 | 4.9~15.69 |
Prestatievergelijking van veelgebruikte platen
Tabel 1-3 Vergelijking van de prestaties van verschillende veelgebruikte platen
Prijscoëfficiënt | Schootweerstand (mΩ) | CNC ponsen verwerkingsprestaties | Laserbewerking prestaties | Buigprestaties | Klinkmoer technologie | Persklinknageltechnologie | Oppervlaktecoating | Prestaties van incisiebescherming |
---|---|---|---|---|---|---|---|---|
1 | goed | goed | goed | goed | goed | Gemiddeld | Zeer goed | |
1.2 | 27 | goed | goed | goed | goed | goed | Gemiddeld | goed |
1.7 | 26 | goed | goed | goed | goed | goed | Gemiddeld | armste |
1.3 | 26 | goed | goed | goed | goed | goed | Gemiddeld | relatief slecht |
1.4 | 23 | goed | goed | goed | goed | goed | Gemiddeld | arme |
6.5 | 60 | arme | goed | gemiddelde | arme | zeer slecht | arme | goed |
2.9 | 46 | Gemiddeld | extreem arm | goed | goed | goed | Gemiddeld | goed |
3 | 46 | Gemiddeld | extreem arm | extreem arm | goed | goed | Gemiddeld | goed |
5.6 | goed | extreem arm | goed | goed | goed | Gemiddeld | goed | |
5 | goed | extreem arm | goed | goed | goed | Gemiddeld | goed |
Opmerking:
Doorboring en blanking door CNC ponsmachine
CNC ponsen en blanking gebruiken de single-chip microcomputer op de CNC ponsmachine om het bewerkingsprogramma (grootte, bewerkingspad, bewerkingsgereedschap, enz.) van het plaatwerkdeel van tevoren in te voeren, waardoor de CNC ponsmachine verschillende gereedschappen en een rijkdom aan NC-commando's gebruikt om een verscheidenheid aan bewerkingen uit te voeren, zoals ponsen, trimmen, vormen, enz.
CNC ponsen is over het algemeen niet in staat om te ponsen en blank te maken met te gecompliceerde vormen.
Kenmerken:
Het is in principe in staat om te voldoen aan de behoeften van monster blanking productie.
Aandachtsproblemen en -vereisten:
CNC ponsen is over het algemeen geschikt voor het ponsen van laag koolstofstaal, elektrolytische plaat, aluminium-zinkplaat, aluminiumplaat, koperplaat met T=3,5~4mm of minder, en roestvrijstalen plaat met T=3mm of minder.
De aanbevolen plaatdikte voor CNC ponsen is:
Het CNC ponsproces heeft een grote vervorming op de koperplaat, terwijl de verwerkings-PC en de PVC-plaat grote bramen en een lage precisie hebben.
Bij het ponsen moeten de diameter en breedte van het gebruikte gereedschap groter zijn dan de dikte van het materiaal. Een gereedschap met een diameter van Φ 1,5 kan bijvoorbeeld geen materiaal van 1,6 mm ponsen.
Materialen onder 0,6 mm worden over het algemeen niet verwerkt door NCT.
Roestvrijstalen materialen worden over het algemeen niet verwerkt door NCT. (Natuurlijk kan 0,6 ~ 1,5 mm materiaal worden verwerkt door NCT, maar de slijtage van het gereedschap is groot en de kans op uitval bij verwerking in het veld is veel groter dan bij andere GI-materialen).
Het doorboren en blank maken van andere vormen is zo eenvoudig en uniform mogelijk.
De grootte van de CNC pons moet genormaliseerd zijn, zoals ronde gaten, zeshoekige gaten en de minimale breedte van de procesgroef is 1,2 mm.
Doorboring en blanking door koud ponsmatrijs
Voor het ponsen en stansen van onderdelen met een grote capaciteit en kleine afmetingen worden speciaal ontworpen stempels voor plaatwerk gemaakt en gebruikt voor een hogere productie-efficiëntie.
Het bestaat meestal uit een pons en een matrijs.
De matrijs omvat over het algemeen: inperstype en ingelegd type.
De stempels zijn over het algemeen: rond type, kan worden vervangen; gecombineerd type; snel ladend en lossend type.
De meest voorkomende sterftes zijn:
Kenmerken:
Omdat de ponsen en afbramen met koude matrijs kan in principe worden voltooid door een stempelen, de efficiëntie is hoog, de consistentie is goed, en de kosten zijn laag.
Daarom voert het verwerkingsbedrijf voor structuurdelen met een jaarlijkse verwerkingscapaciteit van meer dan 5.000 stuks en met niet al te grote onderdelen over het algemeen een koudverwerkingsproces uit.
Bij het ontwerp van de constructie moet rekening worden gehouden met het ontwerp van de proceseigenschappen van de verwerking van de koude matrijs.
De onderdelen mogen bijvoorbeeld geen scherpe hoeken hebben (behalve voor gebruik). Ze moeten afgerond zijn om de kwaliteit en levensduur van de mal te verbeteren en het werkstuk mooi, veilig en duurzaam te maken.
Om aan de functionele eisen te voldoen, kan de structurele vorm van het onderdeel gecompliceerder worden ontworpen.
Doorprikken met de dichte perforator
De pons voor dichte gaten kan worden beschouwd als een soort numerieke controlepons. Voor onderdelen met een groot aantal dichte gaten kunnen de ponsefficiëntie en precisie verbeterd worden.
Een speciaal gemaakte ponsmatrijs kan een groot aantal dichte gaten ponsen om het werkstuk te bewerken.
Zoals: ventilatiesjabloon, inlaat- en uitlaatluchtschotten.
Zie Afbeelding 1-1.
Het gearceerde deel in de afbeelding is een dichte gatenvorm en het dichte gat van het onderdeel kan snel worden uitgestanst door de dichte gatenvorm. Vergeleken met één pons verbetert dit de efficiëntie aanzienlijk.
Problemen en vereisten voor ontwerpen van dichte gatenopstellingen
Bij het ontwerp van het dichte gat op het product moet er rekening mee worden gehouden dat de verwerkingskenmerken van de ponsmatrijs voor dichte gaten meerdere keren worden herhaald, zodat het volgende principe moet worden aangenomen bij het ontwerp van de opstelling van het dichte gat:
De mal met dichte gaten van Figuur 1-1a kan worden ontworpen zoals getoond in Figuur 1-4.
De mal met dichte gaten van Figuur 1-1 b kan alleen worden ontworpen zoals getoond in Figuur 1-5.
Probeer bij het ontwerpen van de opstelling van dichte gaten te ontwerpen volgens de bovenstaande eisen, en continu en een zekere regelmaat te hebben, wat handig is voor het openen van de gatenmal en het verlagen van de stempelkosten.
Anders kunnen slechts een paar ponsen of een aantal sets mallen worden gebruikt om de verwerking te voltooien.
Zoals getoond in Figuur 1-6,
Lasersnijden
Lasersnijden is een contactloze snijtechnologie die gebruikmaakt van elektronenontlading als energiebron om een laser scherpstellen lichtbundel als warmtebron met behulp van een reflecterende spiegelgroep. Deze lichtenergie met hoge dichtheid wordt gebruikt om plaatdelen te ponsen en blank te maken.
Kenmerken:
De kosten zijn echter hoog en tegelijkertijd wordt de steuntafel van het werkstuk beschadigd. Het snijoppervlak kan gemakkelijk een oxidelaag afzetten, wat moeilijk te hanteren is.
Over het algemeen alleen geschikt voor verwerking van enkele en kleine batches.
Let op: over het algemeen alleen gebruikt voor stalen platen.
Aluminium platen en koperen platen worden over het algemeen niet gebruikt omdat de warmteoverdracht van het materiaal te snel is, waardoor het rond de incisie smelt, wat de nauwkeurigheid en kwaliteit van de verwerking niet garandeert.
De lasersnijden Het snijvlak heeft een oxidelaag die er niet afgewassen kan worden en het snijvlak met speciale vereisten moet gepolijst worden;
Lasersnijden dichte gaten zijn meer vervormd, over het algemeen niet de laser gebruiken om dichte gaten te snijden.
Draad EDM
Draadsnijden is een bewerkingsmethode waarbij een werkstuk en een draad (molybdeendraad, koperdraad) elk als pool worden gebruikt en op een bepaalde afstand worden gehouden, en er een vonkbrug wordt gevormd wanneer de spanning hoog genoeg is, en het werkstuk elektrolytisch wordt geëtst. Het verwijderde materiaal wordt meegevoerd door de werkvloeistof.
Eigenschappen: hoge verwerkingsnauwkeurigheid, maar lage verwerkingssnelheid, hoge kosten, en zal de oppervlakte-eigenschappen van het materiaal veranderen.
Over het algemeen gebruikt voor het verwerken van mallen, niet voor het verwerken van productiedelen.
Sommige vierkante gaten van de profielpanelen hebben geen afgeronde hoeken die niet gefreesd kunnen worden, en omdat aluminiumlegeringen niet met laser gesneden kunnen worden, als er geen ponsruimte is, kunnen ze alleen met draadvonkmachine geponst worden.
De snelheid is erg laag, het rendement is erg laag en het is niet geschikt voor massaproductie. Het ontwerp moet deze situatie vermijden.
Vergelijking van de drie veelgebruikte blanking en piercmethoden
Tabel 1-4 Vergelijking van drie gangbare verwerkingskenmerken voor ponsen en blanking
Opmerking: De volgende gegevens zijn gegevens voor koudgewalste stalen platen.
Laser | Snijden | Punch | |
---|---|---|---|
Bewerkbaar materiaal | staalplaat | Stalen plaat, koperen plaat, aluminium plaat | Stalen plaat, koperen plaat, aluminium plaat |
Bewerkbare materiaaldikte | 1mm ~ 8mm | 0,6 mm ~ 3 mm | over het algemeen <4mm |
Verwerking minimale grootte (normale koudgewalste staalplaat) | Minimale spleet 0,2 mm | Ponsgat Ø≧t | Ponsgat Ø≧t |
Minimale cirkel 0,7 mm | Vierkant gat kleine rand W≧t | Vierkant gat kleine rand W≧t | |
Groefbreedte lang W≧t | Groefbreedte lang W≧2t | ||
Minimale afstand tussen gat en gat, gat en rand | ≧t | ≧t | ≧1t |
Bij voorkeur is de afstand tussen de gaten en de gaten, de gaten en de randen | ≧1.5t | ≧1.5t | ≧1.5t |
Algemene bewerkingsnauwkeurigheid | ±0,1 mm | ±0,1 mm | ±0,1 mm |
Verwerkingsbereik | 2000X1350 | 2000X1350 | |
Uiterlijk effect | Gladde buitenrand, een laagje aanslag op het snijvlak | Grote ruwe randen met bramen | een kleine hoeveelheid ruwe randen |
Curve-effect | Soepele, veranderlijke vorm | Grote bramen en regelmatige vormen; | Soepele, veranderlijke vorm |
Verwerkingssnelheid | De buitenste cirkel snel uitsnijden | Snel dichte gaten perforeren | snelste |
Tekst verwerken | Ets, ondieper, onbeperkte grootte | Gestempelde holle tekst met diepere symbolen; de grootte wordt beperkt door de mal | Gestempelde holle tekst met diepere symbolen; de grootte wordt beperkt door de mal |
Het vormen van | niet kunnen | Hol, tegenboring, kleine rek, enz. | Kan complexere vormen maken |
Verwerkingskosten | Hoger | Laag | Laag |
Ttechnisch ontwerp van de arrangement
Bij de productie van grote volumes en middelgrote volumes vormen de materiaalkosten van onderdelen een groot deel.
Het volledige en effectieve gebruik van materialen is een belangrijke economische indicator voor de plaatwerkproductie.
Daarom moet de constructief ontwerper, op voorwaarde dat de ontwerpeisen niet worden beïnvloed, streven naar de plaatsingsmethode zonder of met minder afval.
Zoals getoond in Figuur 1-7 is er geen afvalregeling.
Sommige onderdelen hebben een licht gewijzigde vorm, wat veel materiaal kan besparen.
Zoals te zien is in Figuur 1-8, wordt in Figuur 2 minder materiaal gebruikt dan in Figuur 1.
Verwerkbaarheid van blanking onderdelen
Om de CNC ponsmachine de buitenradius te laten verwerken, is een speciaal extern gereedschap nodig. Om het gereedschap voor de buitenste cirkel te verkleinen, is de standaardhoekafronding van deze handleiding zoals weergegeven in Figuur 1-9:
1) 90 graden rechte hoek afrondingsreeks, de straal is r2.0, r3.0, r5.0, r10
2) De afgeschuinde hoekradius van 135 graden is gelijk aan R5,0
Om ronde gaten te gebruiken, wordt de voorkeur gegeven aan ponsen.
De ronde gaten moeten gekozen worden volgens de serie ronde gaten die in de handleiding van de plaatmetaalmal staat.
Dit kan het aantal gereedschappen voor ronde gaten verminderen en de tijd voor het verwisselen van messen bij CNC-ponsen verkorten.
Door de beperkingen van de ponssterkte kan de opening niet te klein zijn. De minimale opening is gerelateerd aan de materiaaldikte.
De minimale diameter van het gat mag niet kleiner zijn dan de waarde in Tabel 1-5 hieronder.
Tabel 1-5 Minimumafmetingen voor ponsen met een gewone pons
De minimale diameter of minimale randlengte van de pons (t is de materiaaldikte) | |||
---|---|---|---|
Materiaal | Rond gat D (D is diameter) | Vierkant gat L(L is randlengte) | Taillegat, rechthoekig gat a(a is de minimale randlengte) |
Staal met hoog en gemiddeld koolstofgehalte | ≥1.3t | ≥1.2t | ≥1t |
Laag koolstofstaal en messing | ≥1t | ≥0.8t | ≥0.8t |
Aluminium, zink | ≥0.8t | ≥0.6t | ≥0.6t |
Doek bakeliet laminaat | ≥0.4t | ≥0.35t | ≥0.3t |
De afstand tussen de gaten en tussen het gat en de rand mag niet te klein zijn. De waarde wordt getoond in Figuur 1-10:
De precisie tussen het gat en de vorm, het gat en het gat verwerkt door de samengestelde mal is gemakkelijk te waarborgen tijdens de stempelproces van de mal.
Bovendien is de verwerkingsefficiëntie hoog en zijn de onderhoudskosten van de schimmel geschikt voor onderhoud.
Gezien de bovenstaande redenen, de afstand tussen het gat en het gat, als de afstand tussen het gat en de vorm kan voldoen aan de minimale wanddikte eis van de samengestelde mal, het proces is beter, zoals weergegeven in figuur 1-11:
Tabel 1-6 Minimumafmeting van de rand van de samengestelde matrijsafronding
t (<0.8 ) | t (0.8~1.59) | t (1.59~3.18) | t (>3.2) | |
---|---|---|---|---|
D1 | 3 mm | 2t | ||
D2 | 3 mm | 2t | ||
D3 | 1,6 mm | 2t | 2.5t | |
D4 | 1,6 mm | 2t | 2.5t |
Zoals getoond in Figuur 1-12, eerst doorboren en dan buigen. Om ervoor te zorgen dat het gat niet wordt vervormd, moet de minimumafstand tussen het gat en de flens X≥2t+R
Bij het ponsen van gaten op dieptrekonderdelen, zie Afbeelding 1-13, moeten de gatenwand en de rechte wand van de onderdelen op een bepaalde afstand worden gehouden om de vorm en positienauwkeurigheid van de gaten en de sterkte van de mal te garanderen, dat wil zeggen dat de afstanden a1 en a2 aan de volgende eisen moeten voldoen:
In de formule is R1, R2 de hoekradius en t de dikte.
Verwerkingsnauwkeurigheid van blanking onderdelen
Tabel 1-7 Tolerantietabel van de hartafstand van het gat (Eenheid: mm)
Gewone ponsnauwkeurigheid | Geavanceerde ponsnauwkeurigheid | |||||
---|---|---|---|---|---|---|
Nominale maat L | Nominale maat L | |||||
Dikte | <50 | 50~150 | 150~300 | <50 | 50~150 | 150~300 |
<1 | ±0.1 | ±0.15 | ±0.20 | ±0.03 | ±0.05 | ±0.08 |
1~2 | ±0.12 | ±0.20 | ±0.30 | ±0.04 | ±0.06 | ±0.10 |
2~4 | ±0.15 | ±0.25 | ±0.35 | ±0.06 | ±0.08 | ±0.12 |
4~6 | ±0.20 | ±0.30 | ±0.40 | ±0.08 | ±0.10 | ±0.15 |
Opmerking: Alle gaten moeten één keer worden uitgestanst bij gebruik van de waarden in deze tabel.
Selectieprincipe van de ontwerpgrootte van het stempelende onderdeel
1) De dimensionale ontwerpreferentie van het gestempelde onderdeel ligt zo dicht mogelijk bij de gefabriceerde positioneringsreferentie, zodat de fabricagefout van de dimensie kan worden vermeden.
2) De referentie voor de gatgrootte van het stansdeel moet zo ver mogelijk van het begin tot het einde van het stansproces worden gekozen en mag niet worden geassocieerd met het deel dat deelneemt aan de vervorming.
3) Voor onderdelen die in meerdere stappen gedispergeerd en gestanst worden op verschillende matrijzen, moet zoveel mogelijk dezelfde positioneringsreferentie gebruikt worden.
Tabel 1-8 Tolerantietabel van hart gat en rand afstand
Dikte | Maten b | |||
---|---|---|---|---|
≤50 | 50<b≤120 | 120<b≤220 | 220<b≤360 | |
<2 | ±0.2 | ±0.3 | ±0.5 | ±0.7 |
≥2~4 | ±0.3 | ±0.5 | ±0.6 | ±0.8 |
>4 | ±0.4 | ±0.5 | ±0.8 | ±1.0 |
Opmerking: Deze tafel is geschikt voor perforeren na blanking.
Secundair snijden
Secundair snijden wordt ook wel secundair blanking of extra snijden genoemd (zeer slecht proces, moet worden vermeden bij het ontwerpen).
Het secundaire snijden is dat het uitrekken een vervorming van het materiaal veroorzaakt. Als de buigvervorming groot is, wordt de blanking groter. Eerst vormen, dan gaten of contouren snijden om het gereserveerde materiaal te verwijderen en de volledige juiste structuurgrootte te verkrijgen.
Toepassing: als de spannok zich dicht bij de rand bevindt, moet er een extra snede worden uitgevoerd.
Neem de tegenboring als voorbeeld, zoals getoond in Figuur 1-16.
U kunt lees dit bericht om elk detail te leren over het buigen van plaatmetaal.
Veel voorkomende vormen van geklonken moeren zijn zelfklemmende standoff, zelfklemmende moer, ankernagelmoer, treknagelmoer en zwevende klinknagelmoer.
Selfen-beknellende impasse
Drukklinken betekent dat in de klinkprocesOnder de externe druk vervormt het klinknagelgedeelte het basismateriaal plastisch en wordt het samengeperst in de geprefabriceerde groef die speciaal is ontworpen in de geklonken schroef- en moerstructuur, waardoor de betrouwbare verbinding van de twee delen wordt gerealiseerd.
Er zijn twee soorten niet-standaard moeren voor klinken, de ene is een zelfklemmende standaard en de andere is een zelfklemmende moer.
De verbinding met het substraat wordt gemaakt met behulp van een dergelijke geklonken vorm.
Dergelijke klinkvormen vereisen meestal dat het geklonken onderdeel een grotere hardheid heeft dan de hardheid van het substraat.
Gewoon laag koolstofstaal, aluminiumlegeringsplaat en koperplaat zijn geschikt voor het krimpen van de zelfborgende standoff.
Voor roestvrijstalen en koolstofstalen platen is vanwege het harde materiaal een speciale klinkmoerkolom met hoge sterkte nodig, die niet alleen duur is, maar ook moeilijk te krimpen, en de krimp is niet betrouwbaar en valt er gemakkelijk af na het krimpen.
Om de betrouwbaarheid te garanderen, moeten fabrikanten vaak lassen toevoegen aan de zijkant van de moerkolom, wat niet goed is in het proces.
Daarom zijn de plaatdelen met de klinkmoerzuil en de klinkmoer niet zo roestvrij mogelijk.
Dit geldt ook voor klinknagelschroeven en klinkmoeren, die niet geschikt zijn voor gebruik op roestvrijstalen platen.
Het krimpproces van de klinkmoerzuil wordt getoond in Figuur 1-41:
Selfenklem klinkmoer
Het krimpproces van de klinknagelschroef wordt getoond in Figuur 1-42:
Aklinkmoer
Verankeren betekent dat tijdens het klinken een deel van het materiaal van de geklonken schroef of moer plastisch wordt vervormd onder invloed van een externe kracht en dat er een nauwe verbinding wordt gevormd met het basismateriaal, waardoor een betrouwbare verbinding tussen de twee delen ontstaat.
De veelgebruikte ZRS wordt met het substraat verbonden door dit type klinknagel.
Het klinkproces is relatief eenvoudig en de verbindingssterkte is laag en wordt meestal gebruikt om de hoogte van het bevestigingsmiddel te beperken en een klein koppel te weerstaan. Zoals getoond in Figuur 1-43:
Trek klinkmoer
Treknagelen betekent dat het klinknagelelement plastisch wordt vervormd onder invloed van externe spanning tijdens het klinkproces.
De positie van de vervorming is meestal in een speciaal ontworpen onderdeel en het substraat wordt vastgeklemd door het vervormingsgedeelte om een betrouwbare verbinding te krijgen.
De veelgebruikte klinkmoeren worden met het substraat verbonden door dit type klinknagel.
Het klinken gebeurt met een speciaal klinknagelpistool, dat vaak wordt gebruikt op plaatsen waar de installatieruimte klein is en het niet mogelijk is om universeel klinkgereedschap te gebruiken, zoals bij gesloten pijpen. Zoals getoond in Figuur 1-44:
Fklinkmoer
Sommige klinkmoeren op de plaatmetalen structuur, omdat de algehele chassisstructuur complex is, is de accumulatiefout van de structuur te groot, zodat de relatieve positiefout van deze klinkmoeren groot is, wat de montage van andere onderdelen bemoeilijkt.
Dit is een goede verbetering na het gebruik van een geklonken zwevende moer op de positie van de corresponderende klinkmoer.
Zoals getoond in Figuur 1-45: (Let op: er moet voldoende ruimte zijn in de klinknagelpositie)
Anker rivet moer of zelfborgende klinkmoer aan de zijkant afstand
De ankerklinkmoer of de zelfklemmende klinknagelmoer worden samen met de plaat geklonken door de plaat samen te drukken.
Als de ankerklinking of zelfklemmende klinknagel te dicht bij de rand zit, kan dit onderdeel gemakkelijk vervormen.
Als er geen speciale vereisten zijn, moet de minimumafstand tussen de middellijn van de geklonken bevestiging en de rand van de plaat groter zijn dan L, zie Figuur 1-46.
Anders moeten er speciale klemmen worden gebruikt om te voorkomen dat de randen van de plaat worden vervormd door kracht.
Factoren die de kwaliteit van het klinken beïnvloeden
Er zijn veel factoren die de kwaliteit van het klinken beïnvloeden. Samengevat zijn dat voornamelijk de volgende: de prestaties van het substraat, de grootte van het bodemgat en de klinkmethode.
1) Substraateigenschappen.
Als de hardheid van het substraat geschikt is, is de klinkkwaliteit goed en is de kracht van het klinknagelelement goed.
2) Grootte bodemgat.
De grootte van het onderste gat heeft een directe invloed op de kwaliteit van de klinknagel, als de opening groot is, dan is de opening tussen het substraat en de klinknagel groot.
Voor het klinken mag er niet genoeg vervorming zijn om de groef op het klinkstuk te vullen, zodat de schuifkracht onvoldoende is, wat direct van invloed is op de drukweerstand van de klinkmoer (nagel).
Voor de klinknagelschroef is het onderste gat te groot en wordt de drukkracht die wordt gegenereerd door de plastische vervorming tijdens het klinken klein, wat een directe invloed heeft op de drukweerstand en de torsieweerstand van de klinknagelschroef (vrouwelijk).
Hetzelfde geldt voor de klinknagel, het onderste gat is te groot, zodat de effectieve wrijving tussen de twee stukken na plastische vervorming wordt verminderd, wat de kwaliteit van de klinknagel beïnvloedt.
De grootte van het onderste gat is klein en hoewel de kracht van de klinknagel tot op zekere hoogte kan worden verhoogd, zal de uiterlijke kwaliteit van de klinknagel waarschijnlijk slecht zijn.
De klinkkracht is groot, de installatie is onhandig en de vervorming van de bodemplaat wordt gemakkelijk veroorzaakt, wat de productie-efficiëntie van het klinkwerk en de kwaliteit van het klinken beïnvloedt.
3) Klinkmethode.
Het is geïntroduceerd in de vorige paragraaf. Klinkbouten en -moeren moeten veel aandacht besteden aan de omstandigheden tijdens het gebruik. Verschillende situaties en verschillende krachtvereisten vereisen verschillende types.
Als deze niet correct wordt gebruikt, zal het krachtbereik van de geklonken schroeven en moeren afnemen, waardoor de verbinding zal bezwijken.
Hier zijn een paar voorbeelden om het juiste gebruik van de normale situatie te illustreren.
1) Installeer geen stalen of roestvrijstalen klinkbevestigingen voordat de aluminium plaat geanodiseerd of oppervlaktebehandeld is.
2) Als er te veel geklonken wordt op dezelfde rechte lijn, is er geen plaats voor het geëxtrudeerde materiaal om te vloeien, waardoor er grote spanning ontstaat en het werkstuk in een gebogen vorm wordt gebogen.
3) Probeer ervoor te zorgen dat het oppervlak van de plank bedekt is voordat je de geklonken bevestigingen aanbrengt.
4) M5, M6, M8, M10 moeren worden meestal gelast. Te grote moeren vereisen over het algemeen een hoge sterkte. Booglassen gebruikt worden. Onder M4 (inclusief M4) moet de ankerklinkmoer worden gebruikt. Als deze is gegalvaniseerd, kan de klinkmoer met elektrolytisch verzinken worden gebruikt.
5) Wanneer je de moer aan de gebogen kant vastklinkt, moet je opletten om de kwaliteit van de geklonken moer te garanderen: 1.
De afstand van de rand van het klinkgat tot de zijkant van de bocht moet groter zijn dan de vervormingszone van het gebogen onderdeel. 2.
De afstand L van het middelpunt van de geklonken moer tot de binnenkant van de gebogen zijde moet groter zijn dan de som van de buitenste cilindrische straal van de geklonken moer en de binnenste straal van de bocht. Dat wil zeggen, L>D/2+r.
De projectielas moer (puntlasmoer) wordt veel gebruikt bij het ontwerpen van plaatwerkonderdelen.
In veel ontwerpen is de grootte van het voorgat echter niet in overeenstemming met de norm en kan het niet nauwkeurig worden geplaatst.
Het constructietype en de afmetingen zijn zoals aangegeven in Figuur 1-47 en Figuur 1-48. De aanbevolen waarden voor de gatdiameter D0 en de dikte H voor het lassen van de staalplaat voor het lassen zijn zoals gespecificeerd in Tabel 1-17.
Tabel 1-17 Afmetingen van gelaste zeskantmoeren en openingsdikte van bijbehorende staalplaat (mm)
Schroefdraadmaat (D of D×P) | M4 | M5 | M6 | M8 | M10 | M12 | M16 | |
---|---|---|---|---|---|---|---|---|
─ | ─ | ─ | M8×1 | M10×1 | M12×1. 5 | M16×1. 5 | ||
─ | ─ | ─ | ─ | (M10×1.25) | (M12×1. 25) | ─ | ||
e | min | 9.83 | 10.95 | 12.02 | 15.38 | 18.74 | 20.91 | 26.51 |
dy | max | 5.97 | 6.96 | 7.96 | 10.45 | 12.45 | 14.75 | 18.735 |
min | 5.885 | 6.87 | 7.87 | 10.34 | 12.34 | 14.64 | 18.605 | |
h1 | max | 0.65 | 0.7 | 0.75 | 0.9 | 1.15 | 1.4 | 1.8 |
min | 0.55 | 0.6 | 0.6 | 0.75 | 0.95 | 1.2 | 1.6 | |
h2 | max | 0.35 | 0.4 | 0.4 | 0.5 | 0.65 | 0.8 | 1 |
min | 0.25 | 0.3 | 0.3 | 0.35 | 0.5 | 0.6 | 0.8 | |
m | max | 3.5 | 4 | 5 | 6.5 | 8 | 10 | 13 |
min | 3.2 | 3.7 | 4.7 | 6.14 | 7.64 | 9.64 | 12.3 | |
D0 | max | 6.075 | 7.09 | 8.09 | 10.61 | 12.61 | 14.91 | 18.93 |
min | 6 | 7 | 8 | 10.5 | 12.5 | 14.8 | 18.8 | |
H | max | 3 | 3.5 | 4 | 4.5 | 5 | 5 | 6 |
min | 0.75 | 0.9 | 0.9 | 1 | 1.25 | 1.5 | 2 |
Opmerking: Gebruik de specificaties tussen haakjes zo min mogelijk.
Gangbare grove draadboring
Diameter schroefdraad M | Dikte t | Binnendiameter D1 | Buitendiameter D2 | Hoogte h | Diameter voorpons D0 | Straal |
---|---|---|---|---|---|---|
M2.5 | 0.6 | 2.1 | 2.8 | 1.2 | 1.4 | 0.3 |
0.8 | 2.8 | 1.44 | 1.5 | 0.4 | ||
1 | 2.9 | 1.8 | 1.2 | 0.5 | ||
1.2 | 2.9 | 1.92 | 1.3 | 0.6 | ||
M3 | 1 | 2.55 | 3.5 | 2 | 1.4 | 0.5 |
1.2 | 3.5 | 2.16 | 1.5 | 0.6 | ||
1.5 | 3.5 | 2.4 | 1.7 | 0.75 | ||
M4 | 1 | 3.35 | 4.46 | 2 | 2.3 | 0.5 |
1.2 | 4.5 | 2.16 | 2.3 | 0.6 | ||
1.5 | 4.65 | 2.7 | 1.8 | 0.75 | ||
2 | 4.56 | 3.2 | 2.4 | 1 | ||
M5 | 1.2 | 4.25 | 5.6 | 2.4 | 3 | 0.6 |
1.5 | 5.75 | 3 | 2.5 | 0.75 | ||
2 | 5.75 | 3.6 | 2.7 | 1 | ||
2.5 | 5.75 | 4 | 3.1 | 1.25 |
De minimale afstand van de tik tot de buigrand
Tabel 1-19 Afstand tussen het tapcentrum en de buigrand Vergelijkingstabel H-waarde
Dikte/draaddiameter | 1 | 1.2 | 1.5 | 2 |
---|---|---|---|---|
M3 | 6.2 | 6.6 | - | - |
M4 | 7.7 | 8 | - | |
M5 | - | 7.6 | 8.4 | - |
Tabel 1-20 Vergelijking van de klinknagelmoer, zelfborgende moer, treknagelen en tappen
Verbindingsmethode / functie | Anker klinkmoer | zelfborgende klinkmoer | popnagelen | felsen en tappen |
---|---|---|---|---|
Verwerkbaarheid | het is goed | goed | goed | gemiddelde |
Vereisten voor plaatwerk | Roestvrijstalen klinknagels, vallen er gemakkelijk af | Het klinken van roestvrij staal is zeer slecht, gebruik speciale klinkmoeren en heb puntlassen | geen | Dunne plaat en koper, aluminium zacht materiaal gemakkelijk uit te glijden |
Precisie | goed | goed | goed | gemiddelde |
Duurzaamheid | goed | goed | goed | Koper en aluminium zachte materialen zijn slecht, andere materiaaldraden hebben 3 tot 4 gespen of meer |
Kosten | hoog | hoog | gemiddelde | laag |
kwaliteit | goed | goed | goed | gemiddelde |
Het uitrekken van de plaat wordt getoond in Figuur 1-50.
Overwegingen bij het uitrekken van plaatwerk:
In de vorm en afmeting van het bolle plaatwerk zijn verschillende seriegroottes gespecificeerd in de handleiding voor plaatwerkmallen. Er is een bijbehorend Vormmodel in de Intralink-bibliotheek.
Het ontwerp moet worden gekozen volgens de maat die in de handleiding staat, en de vormmal in de bibliotheek wordt direct gebruikt.
Beperk de grootte van de convexe steek en convexe marge
Tabel 1-21 Grensafmetingen van de convexe steek en de convexe marge
Schema | L | B | D |
---|---|---|---|
![]() | 6.5 | 10 | 6 |
8.5 | 13 | 7.5 | |
10.5 | 15 | 9 | |
13 | 18 | 11 | |
15 | 22 | 13 | |
18 | 26 | 16 | |
24 | 34 | 20 | |
31 | 44 | 26 | |
36 | 51 | 30 | |
43 | 60 | 35 | |
48 | 68 | 40 | |
55 | 78 | 45 |
Zoals getoond in 1-52 kan een 0,3 inch reliëfdruk op plaatmetaal worden gebruikt als sticker voor een label of iets dergelijks om de betrouwbaarheid van het label te verbeteren.
Bij zo'n halfronde holte is de vervorming veel kleiner dan de normale uitrekking, maar er is nog steeds een zekere vervorming voor een afdekplaat met een groot oppervlak en een bodemplaat die niet gebogen is of een kleine buighoogte heeft.
Alternatieve methode: In het labelbereik kunnen twee haakse lijnen worden geponst om de vervorming te verbeteren.
De betrouwbaarheid van de labelbevestiging neemt echter af.
Deze methode kan ook worden gebruikt voor bewerkingen zoals productcodering, productiedatum, versie en zelfs patroon.
Door de ribben op de plaatvormige metalen delen te drukken, zie Afbeelding 1-53, wordt de structurele stijfheid vergroot.
Zoals getoond in Figuur 1-54,
De boren Klinken is een klinkmethode tussen plaatmetaal, voornamelijk gebruikt voor het verbinden van gecoate stalen platen of roestvrij stalen platen.
Een van de delen is geponst en het andere deel is geponst en geboeid om er een niet-verwijderbare connector van te maken.
Voordelen: de flens is afgestemd op het rechte gat en heeft zelf een positioneringsfunctie. De klinksterkte is hoog en de klinkefficiëntie door de mal is ook hoog.
De specifieke manier wordt getoond in Figuur 1-55:
Tabel 1-22 Afmetingen voor klinken boren
Parameter | Dikte T (mm) | Flens hoogte H(mm) | Buiten-ø flens D (mm) | |||||||||||
---|---|---|---|---|---|---|---|---|---|---|---|---|---|---|
Nee. | 3 | 3.8 | 4 | 4.8 | 5 | 6 | ||||||||
Bijbehorend recht gat binnendia. d en voorboorgat d0 | ||||||||||||||
d | d0 | d | d0 | d | d0 | d | d0 | d | d0 | d | d0 | |||
1 | 0.5 | 1.2 | 2.4 | 1.5 | 3.2 | 2.4 | 3.4 | 2.6 | 4.2 | 3.4 | ||||
2 | 0.8 | 2 | 2.3 | 0.7 | 3.1 | 1.8 | 3.3 | 2.1 | 4.1 | 2.9 | 4.3 | 3.2 | ||
3 | 1 | 2.4 | 3.2 | 1.8 | 4 | 2.7 | 4.2 | 2.9 | 5.2 | 4 | ||||
4 | 1.2 | 2.7 | 3 | 1.2 | 3.8 | 2.3 | 4 | 2.5 | 5 | 3.6 | ||||
5 | 1.5 | 3.2 | 2.8 | 1 | 3.6 | 1.7 | 3.8 | 2 | 4.8 | 3.2 |
Opmerking: Met het algemene principe H=T+T'+(0,3~0,4)
D = D'-0,3;
D-d=0,8T
Wanneer T≧0,8 mm is, is de wanddikte van het flensgat 0,4 T.
Als T<0,8 mm is, is de wanddikte van de flens meestal 0,3 mm. H is meestal 0,46±0,12
In de plaatmetaal klinkmethode is er ook een klinkmethode die Tox klinken is.
Het principe is dat twee stapels bij elkaar worden geplaatst, zoals getoond in Figuur 1-56.
Stempelen en tekenen met behulp van een mal, voornamelijk gebruikt voor de verbinding van gecoate stalen platen of roestvrij stalen platen.
Het heeft de voordelen van energiebesparing, milieubescherming en hoge efficiëntie.
In het verleden werd het chassis van de communicatie-industrie meer geklonken, maar de kwaliteitscontrole van massaproductie was moeilijk. Het is minder toegepast en wordt niet aanbevolen.
De structurele afmetingen van de tegenboring van de schroef worden geselecteerd zoals weergegeven in de volgende tabel.
Als de verzonken kop van de verzonken schroef te dun is, is het moeilijk om tegelijkertijd de via d2 en de tegenboring D te garanderen en moet de via d2 bij voorkeur worden gegarandeerd.
De verzonken kop en doorvoer voor verzonken schroeven: (Gekozen plaatdikte t is bij voorkeur groter dan h)
Tabel 1-23 Afmetingen van schroefgat
![]() | d1 | M2 | M2.5 | M3 | M4 | M5 |
---|---|---|---|---|---|---|
d2 | Φ2.2 | Φ2.8 | Φ3.5 | Φ4.5 | Φ5.5 | |
D | Φ4.0 | Φ5.0 | Φ6.0 | Φ8.0 | Φ9.5 | |
h | 1.2 | 1.5 | 1.65 | 2.7 | 2.7 | |
Voorkeur min. dikte | 1.2 | 1.5 | 1.5 | 2 | 2 | |
α | 90° |
Tabel 1-24 Afmetingen van tegenboringen voor verzonken klinknagels
![]() | d1 | Φ2 | Φ2.5 | Φ3 | Φ4 | Φ5 |
---|---|---|---|---|---|---|
d2 | Φ2.2 | Φ2.7 | Φ3.3 | Φ4.3 | Φ5.3 | |
D | Φ4.0 | Φ5.0 | Φ5.5 | Φ7.0 | Φ9.0 | |
h | 1 | 1.1 | 1.2 | 1.6 | 2 | |
α | 120° |
De verbinding van plaatmetaal wordt voltooid met verzonken M3-schroeven.
Als de dikte van het vergulde gat 1 mm is, is het problematisch volgens de conventionele methode.
In het werkelijke ontwerp komen echter een groot aantal van dergelijke problemen voor.
De klinknagelmoer wordt hieronder gebruikt en de diameter van de tegenboring is 6 mm, waardoor de verbinding effectief kan worden voltooid, zoals te zien is in de afbeelding.
Dit formaat wordt gebruikt in een groot aantal inzetbakjes.
Het is belangrijk om op te merken dat dit type verbinding vereist dat de onderste moer ankerklinkmoeren zijn.
De zelfborgende klinkmoer en de tap kunnen de verbinding niet voltooien.
Om dergelijke afmetingen te standaardiseren, moet d/D als volgt zijn:
Tabel 1-25 Unificatie van dunne plaat tegenboring
Plaatdikte | 1 | 1.2 | 1.5 |
---|---|---|---|
M3 | 4/6 | 3.6/6.0 | 3.5/6 |
M4 | - | - | 5.8/8.8 |
Als oprichter van MachineMFG heb ik meer dan tien jaar van mijn carrière gewijd aan de metaalbewerkingsindustrie. Door mijn uitgebreide ervaring ben ik een expert geworden op het gebied van plaatbewerking, verspaning, werktuigbouwkunde en gereedschapsmachines voor metalen. Ik denk, lees en schrijf voortdurend over deze onderwerpen en streef er voortdurend naar om voorop te blijven lopen in mijn vakgebied. Laat mijn kennis en expertise een aanwinst zijn voor uw bedrijf.