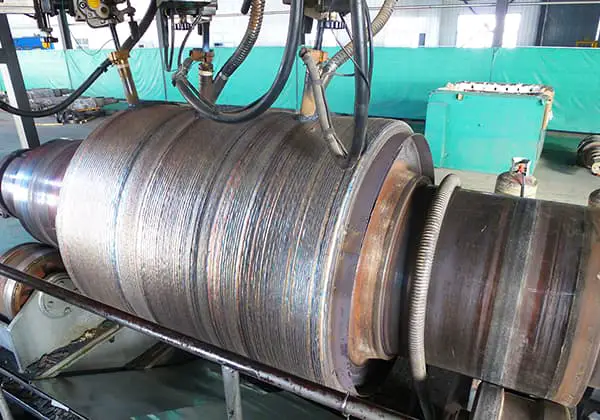
Wat als je de levensduur van kritieke machineonderdelen zou kunnen verlengen door hun oppervlakken te versterken tegen slijtage en corrosie? Dit artikel gaat in op sproeilassen, een geavanceerde techniek die precies dat doet. U zult ontdekken hoe sproeilassen werkt, wat de voordelen zijn ten opzichte van traditionele methoden en welke soorten materialen het meest geschikt zijn voor dit proces. Aan het eind zult u begrijpen hoe deze technologie de duurzaamheid en prestaties in verschillende industriële toepassingen kan verbeteren.
Bij sproeilassen wordt een voorverwarmde zelfoplosbare poedercoating van legeringen verhit tot een temperatuur van 1000-1300℃, smelten de deeltjes, drijven de slak naar het coatingoppervlak en worden de boride en silicide in de coating gedispergeerd. Dit proces zorgt voor een goede combinatie tussen de deeltjes en het substraatoppervlak.
De uiteindelijke afzetting vormt een dichte metaalkristalstructuur en creëert een metallurgische bindingslaag van ongeveer 0,05-0,1 mm met de matrix. Deze bindingslaag heeft een sterkte van ongeveer 400MPa, een uitstekende slagvastheid, slijtvastheid en corrosiebestendigheid en ziet er spiegelend uit.
Vergeleken met sproeicoating biedt sproeilascoating aanzienlijke voordelen. Maar door de hoge temperatuur die de matrix bereikt tijdens het omsmelten, tot 900℃, kan er een grotere thermische vervorming optreden, wat leidt tot bepaalde beperkingen in het toepassingsgebied van sproeilassen.
Onderdelen en materialen die geschikt zijn voor sproeilassen zijn over het algemeen:
Kwetsbare onderdelen die een hoge oppervlaktehardheid en goede slijtvastheid onder schokbelasting vereisen, zoals schuurbladen, brekertandplaten, graafmachinetanden, enz.
② Grote kwetsbare onderdelen met eenvoudige geometrieën, zoals assen, plunjers, schuiven, hydraulische cilindersen glijplaten.
③ Materialen met inbegrip van koolstofstaal met een laag koolstofgehalte, koolstofstaal met een gemiddeld koolstofgehalte (minder dan 0,4% koolstof), constructiestaal met minder dan 3% mangaan, molybdeen en vanadium, nikkel chroom roestvrij staalgietijzer en andere soortgelijke materialen.
Het zelfvloeiende legeringspoeder is samengesteld uit nikkel, kobalt en ijzer als basismaterialen. De juiste hoeveelheden boor en silicium worden toegevoegd om te dienen als desoxidatiemiddelen en slakvormers, lasstroomen om het smeltpunt van de legering te verlagen. Dit type legering is geschikt om de coating om te smelten met een acetyleen-zuurstofvlam.
Er zijn veel soorten zelfvloeiende legeringspoeders beschikbaar. Op nikkel gebaseerde legeringspoeders hebben een sterke corrosiebestendigheid, oxidatiebestendigheid tot 650°C en een sterke slijtvastheid.
Poeder op basis van kobaltlegering wordt gekenmerkt door een uitstekende rode hardheid, waardoor het goed bestand is tegen slijtage en corrosie tot 700 °C.
Poeder op basis van ijzerlegeringen heeft een superieure abrasieve slijtvastheid in vergelijking met de andere twee soorten.
Het proces van sproeilassen lijkt in wezen op dat van spuiten. Bij sproeilassen wordt echter een extra omsmeltingsproces uitgevoerd tijdens de poederspuitprocedure.
Spuitlassen bestaat uit twee types: éénstapsspuitlassen en tweestapsspuitlassen.
Voordat je aan het proces begint, moet je de volgende punten in overweging nemen:
① Het carboneren of nitreren laag op het oppervlak van het werkstuk moet tijdens de voorbehandeling worden verwijderd.
De voorverwarmingstemperatuur van het werkstuk moet 200-300℃ zijn voor gewoon koolstofstaal en 350-400℃ voor hittebestendig austenitisch staal. Voor het voorverwarmen moet een neutrale of zwakke koolstofvlam worden gebruikt.
Het is belangrijk op te merken dat de dikte van de gespoten laag na het hersmelten met ongeveer 25% afneemt. Daarom moet met deze factor rekening worden gehouden bij het meten van de laagdikte in warme toestand na het spuiten.
Spuitlassen in één stap.
Bij de eenstapsmethode wordt afwisselend gespoten en gesmolten met hetzelfde spuitpistool.
Er zijn middelgrote en kleine spuitlaspistolen beschikbaar.
Voor je begint, verwarm je het werkstuk voor en breng je een beschermlaag van 0,2 mm aan, die het oppervlak goed afsluit om oxidatie te voorkomen.
Begin te spuiten en te smelten vanaf één uiteinde, waarbij je een afstand van 10-30 mm houdt.
Verwarm de beschermlaag gedeeltelijk achter elkaar tot het smelten nat begint te worden zonder te vloeien. Herhaal het proces, spuiten en smelten van het poeder, totdat de vooraf bepaalde dikte is bereikt en het oppervlak een "spiegel" reflectie vertoont. Breid dan verder uit tot het volledige oppervlak bedekt is met de spuit- en laslaag.
Herhaal het proces als de dikte onvoldoende is.
De methode in één stap is geschikt voor kleine onderdelen of kleine oppervlakken waarvoor sproeilassen nodig is.
Tweestaps sproeilasmethode.
Bij de tweestapsmethode wordt eerst de spuitlaag aangebracht en vervolgens omgesmolten.
Spuitpistolen met hoog vermogen, zoals SpH-E-spuitpistolen en laspistolen, worden gebruikt om het poeder van de legering volledig te smelten in de vlam en een afzettingslaag van plastische vervorming te creëren op het oppervlak van het werkstuk.
Poeder op ijzerbasis moet worden gespoten met een zwakke koolstofvlam, terwijl neutrale of zwakke koolstofvlammen moeten worden gebruikt voor poeder op nikkelbasis en kobaltbasis.
Elke laag poeder spuiten moet minder dan 0,2 mm dik, en herhaaldelijk spuiten moet de gewenste omsmelten dikte van over het algemeen 0,5-0,6 mm te bereiken.
Als er een dikke spuitlaslaag nodig is en één keer omsmelten niet genoeg is, kan er meerdere keren worden gespoten en omgesmolten.
Omsmelten is het belangrijkste proces in de tweestapsmethode en moet onmiddellijk na het spuiten worden uitgevoerd.
Gebruik een krachtige zachte vlam of een neutrale vlam of een zwakke carbonisatievlam.
De spuitafstand moet ongeveer 20-30 mm zijn en de hoek tussen de vlam en het oppervlak moet 60°-75° zijn.
Beginnend op ongeveer 30 mm afstand van de coating moet de hersmeltsnelheid goed worden geregeld en de coating moet worden verwarmd tot een "spiegel" reflectie van de coating verschijnt voordat het volgende deel wordt hersmolten.
Tijdens het hersmelten moet oversmelten (d.w.z. barsten in het spiegeloppervlak), het vloeien van de coating of oxidatie van het oppervlak door een te lange lokale verhittingstijd worden voorkomen.
Tijdens het omsmelten van meerdere lagen moet de vorige laag worden afgekoeld tot ongeveer 700 ℃ en moet de oppervlakteslak worden verwijderd voordat er secundair wordt gespoten.
Omsmelten mag niet meer dan drie keer gebeuren.
Koeling van het werkstuk.
Werkstukken van middelgroot en laag koolstofstaal, werkstukken van laag gelegeerd staal en dunne laslaag ijzeren gietstukken met eenvoudige vormen kunnen op natuurlijke wijze worden gekoeld in de lucht.
Echter, voor ijzeren gietstukken met een dikke laslaag en complexe vorm, gietstukken van gelegeerd staal met een hoog gehalte aan mangaan, koper en vanadium, en onderdelen met een hoge hardheid, moeten worden begraven in kalkputten voor langzame afkoeling.
De combinatie van de spuitlaag en spuitlaslaag met het basismetaal verschilt.
Bij het verhitten van met nikkel bekleed aluminium met een sproeiende vlamstraal treedt een exotherme chemische reactie op en roestverwijdering door zandstralen bereikt Sa3, RZ>50 μm. Het koolstofstalen oppervlak vormt een mechanische hechtlaag met een micrometallurgische hechtende onderlaag en een werkende laag, die ook een "ankerhaak"-effect produceert. De hechting tussen de sproeilaslaag en het substraat is daarentegen puur een metallurgische hechtlaag.
Verschillende spuitmaterialen vereisen het gebruik van zelf smeltbaar legeringspoeder voor spuitlassen, terwijl voor spuiten poeder met een lage zelf smeltbaarheid nodig is, dat niet noodzakelijk zelf smeltbaar legeringspoeder is.
Verschillende zelfsmeltbare legeringspoeders kunnen worden gebruikt voor zowel sproeilassen als spuiten, maar het sproeipoeder heeft geen zelfsmeltbaarheid. Daarom kan het alleen worden gebruikt voor sproeien en niet voor het sproeien. lasproces.
Het werkstuk wordt anders verhit tijdens het spuiten en sproeilassen en ook de voorverwarmingstemperatuur voor het spuiten verschilt. Daardoor zijn de microstructuur en de eigenschappen van het werkstuk na het spuiten ook verschillend.
De dichtheid van de coating verschilt ook, aangezien de spuitlaslaag dicht is, terwijl de spuitcoating een paar poriën heeft.
Bovendien is de belastbaarheid verschillend. In het algemeen is de sproeicoating bestand tegen contact met grote oppervlakken en wordt deze meestal gebruikt op gesmeerde werkoppervlakken, pasvlakken en andere werkomstandigheden met minder spanning. De sproeilascoating is echter bestand tegen grote stootkracht, extrusiespanning of contactspanning.
(1) De oppervlaktebelasting op werkstukken gemaakt van diverse koolstofstalen en lage gelegeerd staal is aanzienlijk, vooral onder schokbelastingen.
Voor werkstukken met een hechtsterkte tussen coating en substraat van 350-450N/mm2spuitlashardheid HRC150 ≤ 65, bekledingsdikte variërend van 0,3 tot enkele millimeters, en oppervlakteruwheid van de sproeilaslaag na het slijpen tot Ra0,4-0,1 μm boven.
(2) Bij gebruik in een corrosief medium moet de coating compact en vrij van poriën zijn.
(3) Het originele ontwerp van het werkstukoppervlak keurt afschrikken, carboneren, nitreren, hard verchromenen andere processen waarbij het oppervlak een hoge hardheid moet hebben.
(4) De werkomgeving van het werkstuk is slecht, zoals sterk schurende slijtage, erosieslijtage, cavitatie, enz.
(5) De oxyacetyleen vlam legering poeder spray lasproces is geschikt voor oppervlakteversterking of reparatie van diverse koolstofstalen en laaggelegeerde stalen onderdelen, maar sommige eigenschappen van de onderdelenmaterialen moeten worden opgemerkt.
Als de lineaire uitzettingscoëfficiënt van het basismateriaal sterk verschilt van die van de legeringsspuitlaslaag, d.w.z. minder dan 12 × 10-6/℃ of groter dan 12 × 10-6/℃, moet dit proces voorzichtig worden toegepast om scheuren te voorkomen.
Als de inhoud van elementen met een hoge affiniteit voor zuurstof in het basismetaal meer dan 3%, zoals wolfraam en molybdeen, de totale inhoud van aluminium, magnesium, kobalt, titanium, molybdeen en andere elementen is meer dan 0,5%, of het zwavelgehalte in staal is meer, zal het ook problemen om spuiten lassen.
Dit komt doordat deze materialen een dichte en stabiele oxidelaag genereren onder invloed van zuurstof, waardoor het bevochtigingseffect van de gesmolten legering op de basis wordt geblokkeerd.
Tijdens het hersmelten rolt de vloeibare legering naar beneden als kralen, zoals "zweetparels".
Daarom moet bij het gebruik van het sproeilasproces aandacht worden besteed aan de aanpasbaarheid van dit proces aan het gespoten basismateriaal.
(6) Metalen materialen die zonder speciale behandeling kunnen worden verspoten:
① Koolstof constructiestaal met een koolstofgehalte ≤ 0,25%.
② Gelegeerd constructiestaal met een totaal gehalte aan Mh, Mo, V, Cr en Ni <3%.
③ 18-8 roestvrij staal, nikkel roestvrij staal, grijs gietstaal, smeedbaar ijzer, nodulair ijzer, koolstofarm puur ijzer, rood koper.
(7) Metalen materialen die na het sproeilassen bij 250-375 ℃ langzaam moeten afkoelen, moeten worden voorverwarmd:
① Koolstofhoudend constructiestaal met een koolstofgehalte >0,4%;
② Mangaan, molybdeen, vanadium gelegeerd constructiestaal met een totaal nikkelgehalte >3%;
③ Gelegeerd constructiestaal met chroomgehalte ≤ 2%;
(8) Metalen materialen die isothermisch gloeien na het sproeilassen:
① Martensitisch roestvrij staal met chroomgehalte ≥ 13%;
② Nikkel-molybdeen gelegeerd constructiestaal met koolstofgehalte ≥ 0,4%.
Na het bepalen van het sproeilasproces moet de keuze voor een eenstaps of tweestaps sproeilasproces worden gebaseerd op de volgende voorwaarden:
(1) Als het werkstuk plaatselijk gerepareerd moet worden en de positie van het sproeilassen geen grote warmte-inbreng kan verdragen, gebruik dan het eenstaps sproeilasproces. Zo kunnen bijvoorbeeld plaatselijke littekens op diverse geleiders van bewerkingsmachines met dit proces worden gerepareerd.
(2) Als het oppervlak van het werkstuk complex of onregelmatig is, zoals tandwielen, tandwieloppervlakken, schroeftransporteurs, etc., gebruik dan het éénstaps sproeilasproces.
(3) Voor grote werkstukken die moeilijk in hun geheel te verhitten zijn, zoals wielen van locomotieven en trams, moet het éénstaps sproeilasproces worden gebruikt.
(4) Gebruik voor algemene asonderdelen die kunnen draaien op de bewerkingsmachine het tweestapsspuitlasproces.
(5) De hardheid van de coating moet zo dicht mogelijk bij de oppervlaktehardheid van het originele ontwerp liggen. Als de oppervlaktehardheid van het originele ontwerp bijvoorbeeld HRC≥55 is, die werd bereikt door afschrikken of chemische behandelingsprocessen, moet het "harde deklaag"-poeder, zoals Ni15Ni60, Fe65of Wc-composietpoeder worden gebruikt.
(6) Zeer versleten niet-passende oppervlakken, zoals waaiers, modderpompschalen, tanden van rotsladers, spiraalvoederoppervlakken enz. moeten worden gemaakt van composietpoeders met een hoge hardheid, zoals Ni15Ni60, Fe65of Wc.
(7) Werkstukken die niet bewerkt kunnen worden op draaibanken en slijpmachines maar wel bewerkt moeten worden, kunnen alleen met de hand gedaan worden met vijlen en andere gereedschappen. Bijvoorbeeld, voor het repareren van plaatselijke littekens op het oppervlak van de geleiderail van een bewerkingsmachine is het gebruik van alleen sproeillaspoeders met een lage hardheid nodig, zoals SH, F103Ni15enz.
(8) Verschillen tussen sproeilassen en boogverharding processen:
Tijdens het sproeilasproces is de verbinding tussen de sproeilaslaag en de matrix een metallurgische binding door diffusie van de oplossing, terwijl bij surfacing een metallurgische verbinding door smelten wordt gebruikt.
De matrix wordt niet gesmolten tijdens het sproeilasproces, maar er is een ontbindingseffect tussen de sproeilaslaag en de matrix, wat resulteert in een diffusie-wederzijdse oplossingszone tussen de twee.
Aangezien de matrix onoplosbaar is, wordt de sproeilaslaag niet verdund door het basismateriaal. De verdunningssnelheid is dus extreem laag, wat zorgt voor goede prestaties van de sproeilaslaag.
De overlay lasmatrix daarentegen wordt gesmolten en de verdunningsgraad van de overlay laslaag is hoog. De prestaties van de laslaag kunnen alleen worden gegarandeerd als de overlay laslaag erg dik is, waardoor het moeilijk is om de randen en hoeken van de contour van het onderdeel te garanderen. Dit kan leiden tot veel voorkomende defecten zoals ondersnijdingen en instorten van hoeken. Bij sproeilassen komen dergelijke defecten echter niet voor.
(1) Gietijzer is een ijzer-koolstoflegering met een koolstofgehalte van meer dan 2%. Het wordt veel gebruikt in verschillende industrieën en bevat meestal 2,5% tot 4% koolstof, 1% tot 3% silicium en kleine hoeveelheden mangaan, zwavel, fosfor, enz. Onder andere, grijs gietijzer wordt het meest gebruikt.
Gietijzer heeft een hoog koolstofgehalte, een lage sterkte en is gevoelig voor temperatuurveranderingen. Tijdens lasreparaties heeft het te maken met plaatselijke verhitting, grote temperatuurverschillen en snelle afkoeling. Als gevolg hiervan is het lassen van gietijzer een uitdaging.
De armen lasbaarheid van gietijzer leidt tot verschillende problemen tijdens lasreparaties:
(2) Het lasreparatiedeel kan gemakkelijk een witte microstructuur ontwikkelen die hard, bros en moeilijk te bewerken is. Een dergelijke structuur heeft ook de neiging om gemakkelijk te scheuren.
(3) De snelle opwarm- en afkoelsnelheden tijdens de lasreparatie kunnen thermische spanningsscheuren veroorzaken. Bovendien verhoogt de aanwezigheid van onzuiverheden zoals zwavel en fosfor in het gietijzer de kans op scheuren bij de lasreparatie.
(4) Poreusheid en slakinsluiting zijn ook veel voorkomende problemen. Door het hoge koolstofgehalte, meer onzuiverheden en de snelle afkoelsnelheden in het lasreparatieproces kunnen gas en oxiden niet op tijd neerslaan en wegdrijven, wat leidt tot de vorming van porositeit of slakinsluiting in het lasreparatieproces. laszone.
Gelukkig kan éénstapsspuitlassen met zuurstof-acetyleen vlamlegeringpoeder deze problemen naar tevredenheid oplossen.
(5) Het smeltpunt van het legeringspoeder dat bij het sproeilassen wordt gebruikt, ligt lager dan dat van de matrix. Tijdens het hersmelten smelt de gietijzeren matrix niet, waardoor het verdunningsprobleem van de sproeilaslaag en het ontstaan van een halfgesmolten zone vermeden wordt. Bij correct sproeilassen ontstaat er dus geen witte microstructuur in het reparatiegebied, waardoor het gemakkelijker te verwerken is.
Omdat de matrix niet smelt, wordt bovendien op natuurlijke wijze voorkomen dat onzuiverheden zoals zwavel en fosfor in de sproeilaslaag smelten, wat scheuren helpt voorkomen.
(6) Het éénstapsspuitlasproces heeft minder warmte-inbreng in het substraat en heeft een lager thermisch effect op het substraat, waardoor het effectiever is in het beheersen van thermische spanningsscheuren. De lage warmte-inbreng is vooral voordelig bij het repareren van onderdelen met een hoge maatnauwkeurigheid.
Daarnaast is het gebruik van zuurstof-acetyleenvlamverwarming, dat langzamer is dan elektrisch lassen koeling, is ook nuttig bij het voorkomen van scheuren en vervorming.
(7) Het legeringspoeder dat gebruikt wordt bij sproeilassen bevat sterke desoxiderende elementen zoals boor en silicium. Deze elementen beschermen de andere elementen in het poeder tegen oxidatieve verbranding en verminderen de oxiden op het oppervlak van de matrix, waardoor de vorming van poriën en slakinsluiting wordt voorkomen.
(8) De sproeilaslaag heeft een compacte en vlakke structuur, is goed gevormd, zonder ondersnijding en vereist slechts een kleine hoeveelheid bewerking. Dit resulteert in materiaalbesparing en een hoge efficiëntie. Voor spuitgelaste gietijzeren onderdelen wordt meestal SH - F103, nikkelbasislegeringspoeder Ni15, enz. gebruikt. Op ijzer gebaseerd legeringspoeder heeft echter een hoog smeltpunt, een hoge brosheid, een aanzienlijke impact op de matrix en slechte prestaties.
(9) Tijdens het sproeilassen is het voorverwarmen van het werkstuk in de eerste plaats bedoeld om vocht van het werkstukoppervlak te verwijderen en enige thermische uitzetting te genereren. Dit verkleint het temperatuurverschil en minimaliseert zo de thermische spanning en bevordert een betere hechting van de sproeilaslaag.
Voorverwarmingstemperaturen liggen meestal tussen 250-300℃ voor staal, 450-500℃ voor austenitisch roestvast staal, 350-400℃ voor nikkel-chroom roestvast staal en 250-300℃ voor laaggelegeerd staal en gietijzer. Voor kleine werkstukken en gemakkelijk geoxideerd staal is de voorverwarmingstemperatuur lager.
De dikte van de spuitlaslaag hangt af van de thermische uitzetting en de koude krimpkenmerken van het werkstuk na het spuiten. De krimp na het hersmelten is meestal ongeveer 25-30%. Daarom moet bij het bepalen van de laagdikte rekening worden gehouden met de bewerkingstoeslag en de diameter van het werkstuk vóór het spuiten, samen met de krimp.
De dikte van de spuitlaag wordt als volgt berekend: Laagdikte vóór omsmelten = (dikte van de spuitlaslaag + bewerkingstoeslag) ÷ (1-0,3).
Gerelateerde lectuur: Hoe gietijzer lassen?
(1) Materialen met een smeltpunt lager dan dat van legeringen, zoals aluminium en aluminiumlegeringen, magnesium en magnesiumlegeringen, messing en brons.
(2) Het werkstuk is een slanke as of een zeer dunne plaat die niet mag vervormen.
(3) De oorspronkelijke ontwerpeisen van het werkstuk zijn zeer streng en de metallografische structuur kan niet veranderen.
(4) Nikkel-chroom-molybdeen gelegeerd staal met hoge hardbaarheid.
(5) Martensitisch hoogchroomstaal met een chroomgehalte van meer dan 18%.
(Opmerking: zeer nauwkeurig sproeillassen kan worden uitgevoerd op lange assen met een buitendiameter van meer dan 28 mm en een lengte van minder dan 8 m).
① Er zijn veel onderdelen in voertuigen en mechanische apparatuur die gemaakt zijn van gietijzer, en verschillende problemen zijn onvermijdelijk tijdens de productie of het gebruik. Het zuurstofacetyleenvlamlasproces is niet alleen een effectieve manier om gietijzer te versterken, maar ook een ideaal middel om verschillende defecten en beschadigingen te repareren, zoals zandgaten, luchtgaten, slijtage en andere beschadigingen in gietstukken.
② Spuitlassen wordt meestal gebruikt om plaatselijke defecten van ijzeren gietstukken te repareren, die variëren in grootte en diepte. Het is geschikt voor spuitlassen in één stap. Spuitpistolen met een klein vermogen moeten zoveel mogelijk worden gebruikt om de warmte-invoer naar het substraat te beperken, afhankelijk van de delen van het werkstuk en de benodigde lasreparatie. Over het algemeen wordt gekozen voor QH-1/h, QH-2/h, QH-4/h, enz.
③ Tijdens het sproeilassen heeft poeder van een nikkelbasislegering (Ni-B-Si-serie) de voorkeur vanwege de slechte lasbaarheid van gietijzeren onderdelen. Het smeltpunt van nikkelbasislegeringspoeder is over het algemeen 950 ~ 1050 ℃, en de matrix zal niet smelten tijdens het hersmelten. Tegelijkertijd heeft de spuitlaslaag van nikkelbasispoeder met een laag koolstofgehalte een lage hardheid en een goede plasticiteit. Ontspanning van spuitlassen stress is nuttig om scheuren te voorkomen, wat uiterst belangrijk is voor ongeschoolde operators.
④ Bij het selecteren van specificaties voor sproeilassen moet rekening worden gehouden met factoren zoals gietijzermateriaal, grootte van defecte onderdelen en eisen aan de werkomstandigheden. Het is belangrijk om te zorgen voor de nodige vlammenergie en tegelijkertijd de warmte-invoer naar het substraat te minimaliseren. De juiste zuurstof- en acetyleengasdruklimieten moeten worden aangehouden en de sproei- en smeltafstand moeten tijdens het poederspuiten en hersmelten goed worden afgesteld om de warmte-inbreng onder controle te houden.
Plaatselijke kleine defecten, zoals luchtgaten en zandgaten, kunnen worden gerepareerd door te lassen zonder voorverwarmen voor het sproeilassen. Het verwarmingsgebied rond de sproeilaslaag moet zo klein mogelijk zijn om het gebied met hoge temperatuur zo klein mogelijk te maken.
Voor de reparatie van lokale kleine en diepe defecten is continu sproeilassen geschikt. Deze methode heeft een hoge poederdichtheid, een snelle diktegroei en een hoog rendement, maar vereist een vaardige bedieningstechnologie om de poedervoeding te coördineren met de sproei- en smeltsnelheid om een uniforme sproei- en penetratiesnelheid te bereiken.
⑦ Voor grote en diepe defecten kan intermitterend sproeillassen worden gebruikt om een toename van de thermische spanning door overmatige verhitting van het substraat te voorkomen. Elektrisch lassen en sproeilassen kunnen ook worden gebruikt en er kunnen lasstaven worden gebruikt om de onderste en bovenste delen te vullen voor het sproeilassen. Als de wanddikte van het gietstuk groot is, kan het voorlassen van sproeidraad worden gebruikt om de hechtsterkte te verhogen, te voorkomen dat de sproeilaslaag loslaat van het basismetaal en een deel van de thermische spanning van het sproeilassen te elimineren.
⑧ Grote complexe gietstukken voor het sproeilassen ondervinden vaak hoge thermische spanning, dus er moeten maatregelen worden genomen om spanningsaccumulatie tijdens het sproeilassen te verminderen, zoals het gebruik van methoden om de verwarmingsspanning te verminderen en de subsectiesymmetriemethode. Voorverwarmen voor het lassen en langzame afkoeling na het lassen kunnen ook goede resultaten opleveren.
Het is belangrijk om de hersmelttemperatuur tijdens het sproeilassen onder controle te houden. Als de temperatuur te hoog is, legeringselementen kan verbranden, kan de matrix oververhit raken en zelfs smelten, waardoor de koolstof in het gietijzer in de sproeilaslaag terechtkomt. Dit verhoogt het koolstofgehalte, de hardheid en vermindert de plasticiteit en kan een grotere thermische spanning veroorzaken die leidt tot scheurvorming. Als de hersmelttemperatuur echter te laag is, kan dit leiden tot asinsluiting of ondoordringbaarheid en de hechtsterkte beïnvloeden. Operators moeten letten op de toestand van het coatingoppervlak tijdens het hersmelten en het hersmeltpistool onmiddellijk verwijderen zodra "spiegelreflectie" wordt weergegeven, wat aangeeft dat het poeder is gesmolten en de slak is komen bovendrijven. De omgesmolten onderdelen mogen niet opnieuw worden verhit.