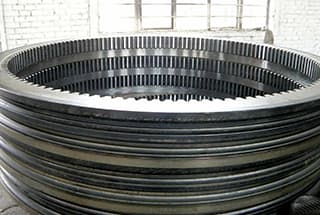
Laten we ter zake komen en direct naar de vraag gaan: Figuur 1 toont het parallelle tandwiel van een megawattmodel van een bedrijf. Het tandwiel is gemaakt van 18CrNiMo7-6 staal en moet worden gecarboneerd en afgeschrikt. De tandmodulus is 10 mm. Met een buitendiameter van 1680 mm, een tandbreedte van 180 mm en een [...]
Laten we ter zake komen en meteen naar de vraag gaan:
Figuur 1 toont het parallelle tandwiel van een megawattmodel van een bedrijf. Het tandwiel is gemaakt van 18CrNiMo7-6 staal en moet worden gecarboneerd en afgeschrikt. De tandmodulus is 10 mm.
Met een buitendiameter van 1680 mm, een tandbreedte van 180 mm en een binnendiameter van 500 mm is het tandwiel ontworpen met een dunne schijf.
Raadpleeg Tabel 1 voor de technische specificaties van het warmtebehandelingsproces.
Fig. 1 Totale afmeting van het tandwiel
Tabel 1 Technische vereisten voor warmtebehandeling van 18HNM7-6 Stalen tandwiel
Effectieve geharde behuizingdiepte/mm | Oppervlak hardheid HRC | Kernhardheid HRC | hardmetaal | Martensiet | Behouden austeniet (%) | Hartweefsel | IGO/mm |
2.9~3.9 | 58~64 | ≥30 | ISO 6336:5MQ-kwaliteit | Fijn naaldachtig | ≤30 | Geen massief ferriet | ≤0.05 |
De processtroom van het bewerken van tandwielen is smeden → normaliseren → ruw draaien → hobben → afschuinen → carboneren en afschrikken → schot peening → halfafwerking → eindafwerking → spiebaan → assemblage → kotteren → tandwielslijpen → magazijn.
Tijdens het proefproductieproces onderging het tandwiel carboneren, hoge temperatuur temperen, afschrikken, lage temperatuur temperen en shot peening. Tijdens het slijpen van het tandwiel werd echter ontdekt dat het tandwiel aanzienlijk vervormd was.
Bovendien bleek na het proefslijpen dat de normaal van het onderdeel onder de vereiste waarde lag.
Bovendien waren er zichtbare slijpsporen aan de wortel van het tandwiel, wat leidde tot de beslissing om het onderdeel te slopen.
Aan het begin van de proefproductiefase werd bepaald dat onderdelen met serienummer H1 zouden worden gebruikt voor de proefproductie op basis van de werkelijke omstandigheden ter plaatse. Dit was te wijten aan het feit dat het tandwiel een diameter-breedteverhouding van 9,3 had, de webplaat dun was, de gaten voor gewichtsreductie groot waren en de onderdelen gevoelig waren voor kromtrekkende vervorming.
Het warmtebehandelingsproces voor de proefproductie wordt geïllustreerd in Figuur 2. Het gebruikte proces was "carboneren - hoog herstel - afschrikken - laag herstel". De temperatuur werd verhoogd met een stapsgewijze verhittingsmethode en het afschrikken gebeurde met een zoutbadmethode.
Fig. 2 Warmtebehandelingsproces van H1-onderdelen (origineel proces)
De onderdelen worden vlak geïnstalleerd met behulp van het gereedschap van een 2 meter diepe putoven. Om de bewerking te vergemakkelijken, werd een onderstel met 8 intervallen gekozen en werden 4 waaiervormige honingraatplaten op intervallen geplaatst, zoals afgebeeld in Figuur 3.
Na het temperen bij hoge temperatuur werd de methode voor het afschrikken veranderd in ophangen, waarbij de ophangpositie het binnenste gat van het onderdeel is, zoals getoond in Figuur 4.
Fig. 3 H1 Onderdelen Carbureren Opladen
Fig. 4 H1 Onderdelen Afkoeling Opladen
Na de warmtebehandeling werden de onderdelen getest op hun fysische en chemische indicatoren, die bleken te voldoen aan de kwalificaties.
Tijdens het slijpen van de tandwielen werd gemeld dat de tanden aanzienlijk vervormden.
De gemiddelde normaal van de onderdelen na het proefslijpen bleek 604,74 mm te zijn, wat onder de vereiste ondergrens van 605,014 mm valt.
Door de aanwezigheid van slijpstappen op sommige tandwortels werden deze onderdelen als schroot beschouwd.
Om de oorzaak van de vervorming in de onderdelen te achterhalen, werden de uitlijngegevens van het H1 onderdeel tijdens het slijpen van de tandwielen verzameld en geanalyseerd.
1) Bekijk het tolerantierapport voor de uitlijning van de tandsectie. Zorg ervoor dat meerdere tandprofielen elkaar correct snijden in de tandrichting en dat de totale tandrichting niet significant vervormd is.
2) Vergelijk de hoge en lage punten van de uitlijning van de slijptanden op zowel het linker- als het rechtertandvlak. Presenteer de bevindingen met behulp van een radardiagram, zoals geïllustreerd in Figuur 5.
Analyse toont aan dat de grootste vervorming plaatsvindt op tandposities 57 tot 82, terwijl de vervorming op andere posities binnen aanvaardbare grenzen blijft.
Fig. 5 Vervorming van linker- en rechtertandoppervlakken van H1-deel
3)Bij het vergelijken van de verdeling van de slijptoeslag van de linker- en rechtertandoppervlakken werd geen significante excentriciteit gevonden tijdens het slijpen van de tandwielen. Er werd voldaan aan de eisen voor het draaien van het binnengat en het eindnulpunt.
4) De uitlijningsgegevens van de slijptanden van de linker en rechter tandoppervlakken werden gemiddeld, zoals getoond in Fig. 6. De analyse onthulde een duidelijke elliptische vorm in de steekcirkel van het onderdeel, met een peervormige trend en een elliptische hoeveelheid van ongeveer 0,18 mm.
Fig. 6 Gemiddelde slijtage van linker- en rechtertandoppervlakken van H1-onderdelen
Op basis van de analyse van de slijp- en centreergegevens van H1-onderdelen is het momenteel onmogelijk om te bepalen of de tandvervorming van de onderdelen te wijten is aan kromtrekken van het eindvlak of tandvervorming.
De onderdelen vertonen een elliptische trend en hebben een peervormig profiel.
Hoewel het niet mogelijk is om te bepalen of een specifieke positie verband houdt met de ophanging, kan uit de eenpuntsophanging worden afgeleid dat de positie van de perengreep (in de buurt van de 148e tand) de plek is waar het gereedschap contact maakt en waar de uitstulping het grootst is.
De positie van de maximale vervorming van de linker en rechter tandoppervlakken volgt geen significant patroon, maar de vervormingstrend is het grootst in de buurt van de elliptische peervormige staart (d.w.z. het onderste deel van de ophanging).
Op basis van de bovenstaande analyse zijn de belangrijkste oorzaken van vervorming van het werkstuk:
1) De willekeurige verdeling van tandvervorming in onderdelen is gerelateerd aan het carboneerproces, inclusief factoren zoals verhittingssnelheid, carboneertemperatuur en andere.
2)Tijdens het carboneren worden slechts vier honingraatschijven op intervallen geplaatst. Tijdens het carboneren kan kruip optreden, wat resulteert in kromtrekkende vervorming van het eindvlak, waardoor de tandrichting kan kruisen.
3)Tijdens het ophangen tijdens het afschrikken kan kruip optreden tijdens het verhitten, waardoor vervorming ontstaat die zich voornamelijk manifesteert als een ellips veroorzaakt door het ophangen tijdens het afschrikken.
4)Wanneer onderdelen worden afgekoeld in een zoutbad, heeft de eerste contactpositie een grotere neiging tot vervorming. Deze positie komt het eerst in contact met het zoutbad en is dichter bij het onderste roerwerk, wat resulteert in een hogere relatieve stroomsnelheid van de vloeistof.
Op basis van de analyse van H1 kon de belangrijkste factor die de vervorming van het onderdeel veroorzaakte niet worden geïdentificeerd.
Als eerste stap naar verbetering werd het warmtebehandelingsproces aangepast. De vervorming van het tandwiel na het carboneren werd bijgehouden om te bepalen of er tijdens de warmtebehandeling significante vervorming was opgetreden tijdens het carboneren.
Het serienummer van het testonderdeel is H2 en de carburatielaadmethode is dezelfde als die voor H1.
Om de thermische stress en vervorming tijdens het carboniseren te minimaliseren, is het proces aangepast zoals geïllustreerd in Fig. 7. De nieuwe aanpak houdt in dat de begintemperatuur van de onderdelen bij binnenkomst in de oven wordt verlaagd, dat de isotherme periode bij zowel 650℃ als 880℃ wordt verlengd, dat het isotherme bereik bij 770℃ wordt uitgebreid en dat de carboneertemperatuur bij het sterk gecarboneerde gedeelte wordt verlaagd.
Fig. 7 Warmtebehandelingsproces van H2 onderdelen (verbeterd proces)
Om de vervorming van het eindvlak van het tandwiel tijdens de carbonisatie te analyseren en de invloed daarvan op het tandprofiel voor de latere uitlijning bij het slijpen van het tandwiel, bootste H2 onderdelen de laadmethode van H1 tandwielen na in de eerste productierun. Ze markeerden het eindvlak na het temperen bij hoge temperatuur en draaiden het eindvlaknulpunt voor voordat ze de tandwieluitlijning op de tandwielslijpmachine slijpen.
Tijdens het draaien van de benchmark ontdekten ze echter een significante uitloop in het eindvlak, zoals te zien is in Fig. 8. De ondersteunde posities van het honingraatpaneel vertoonden allemaal hoge punten, terwijl die zonder opvulling lage punten vertoonden. Het verschil tussen de hoge punten was ongeveer 0,2 mm en het verschil tussen de lage punten was ongeveer 0,25 mm.
Fig. 8 Axiale rondloop van H2 onderdelen na carboneren
De uitlijningsgegevens van de tandwielen geven aan dat de tandrichting van het onderdeel aanzienlijk gekruist is, maar er zijn geen zichtbare ellipsen. Het maximale verschil tussen de hoge en lage punten op het linker en rechter tandoppervlak doet zich voor waar de honingraatplaat niet is opgevuld.
Verder onderzoek naar de carburatielaadmodus voor H2 onderdelen toonde aan dat een te grote axiale circulaire uitloop veroorzaakt door kruip tijdens het carboneren een belangrijke factor is die bijdraagt aan de vervorming van het onderdeel. Om de axiale circulaire uitloop van het tandwiel na carboneren te minimaliseren, is het aantal ondersteunende honingraatplaten aan de onderkant verhoogd van 4 naar 8, zoals weergegeven in Fig. 9.
Deze aanpassing heeft het mogelijk gemaakt om de axiale rondloop van de onderdelen na carboneren en afschrikken onder 0,52 mm te houden.
Fig. 9 Carburatielading na verbetering
Samengevat is de snelle afkoelsnelheid bij ongeveer 1/4 van het onderste deel van het tandwiel een van de factoren die bijdragen aan de vervorming van het tandwiel. Daarom moet het afschrikproces worden aangepast. Voor het testen werden gecarboneerde H2 onderdelen gebruikt en werd een gaasdempingsgereedschap aan de onderplaat toegevoegd om de relatieve vloeistofstroomsnelheid aan de onderkant van het tandwiel tijdens het afschrikken te verminderen.
Om te controleren of de relevante fysische en chemische indicatoren werden beïnvloed, werden tandvormige monsters van dezelfde specificatie met de oven vervoerd. Tabel 2 toont de testresultaten voor het tandvormige monster dat na het afschrikken met de oven werd meegenomen en die aanvaardbaar waren.
Vergeleken met H1 werd de vervorming van H2 onderdelen na het afschrikken enigszins gereduceerd en de gemeenschappelijke normaal van de onderdelen na het tandwielslijpen was 0,03 mm minder dan de ondergrens van de standaardwaarde. Daarom kunnen de onderdelen met enige concessies worden gebruikt.
Tabel 2 Warmtebehandelingsresultaten van H2-onderdelen
Project | Vereiste | Meting | |||||
Effectieve geharde behuizingdiepte/mm | 2.9~3.9 | 3.39 | 3.46 | ||||
Oppervlaktehardheid HRC | 58~64 | 60.26 | 59.62 | ||||
Kernhardheid HRC | ≥30 | 38 | |||||
Hardmetaal | ISO 6336:5 | MQ cijfer | Diffusie | ||||
Martensiet | Fijn naaldachtig | Fijn naaldachtig | |||||
Behouden austeniet (%) | ≤30 | 15 | |||||
Hartweefsel | Geen massief ferriet | Geen massief ferriet | |||||
IGO | /mm | ≤0.05 | 0.025 |
Tijdens de productie van onderdelen met serienummers H3 en H4, worden zowel het carboneerproces getoond in Fig. 8 als de vlakke laadmethode van het volledig leggen van honingraatplaten aan de onderkant tijdens het carboneren (zoals getoond in Fig. 9) gebruikt. Bovendien wordt er tijdens het ophangen van de afschriklading gaasdempend gereedschap aan het chassis toegevoegd om de vervorming van de onderdelen na het carboneren en afschrikken te verbeteren.
Fig. 10 en Fig. 11 tonen de radardiagrammen van de uitlijningsgegevens van de slijptanden van H3-onderdelen, waarbij de positie van tand nr. 109 de steunpuntpositie is bij het ophangen. Uit de figuur blijkt dat de ellips in principe overeenkomt met H1 onderdelen. Bovendien zijn de algemene vervorming en de vervorming van het eerste contactvlak met het vloeistofniveau tijdens het afschrikken aanzienlijk verminderd.
Fig. 10 Linker en rechter tandoppervlakken van H3 delen vervormd
Fig. 11 Gemiddelde slijtage van linker- en rechtertandoppervlakken van H3-onderdelen
Tabel 3 en Fig. 12 tonen de samenvatting van de vervorming van onderdelen na warmtebehandeling met verschillende carboneerprocessen en oplaadmethoden.
Uit de vergelijking blijkt dat de tandvervorming van het onderdeel met ongeveer 40% is afgenomen na het verbeterde carboneerproces, geoptimaliseerde carboneer- en afschriklaadmodus.
Tabel 3 Invloed van verschillende oplaad- en warmtebehandelingsprocessen op de vervorming van het tandwiel
Onderdeelnummer | H1 | H2 | H3 | H4 |
Carbureren opladen | Vlak gemonteerde 4 honingraatpanelen | Vlak gemonteerde 8 honingraatpanelen | ||
Afkoeling opladen | Ophangen en plaatsen van niet-gedempt gereedschap | Gereedschap voor demping ophangen | Gereedschap voor demping ophangen | |
Carbureren en afschrikproces | het oorspronkelijke proces | Proces verbeteren | Proces verbeteren | |
Ellips/mm | 0.18 | 0.14 | 0.14 | 0.15 |
Axiale cirkelvormige uitloop/mm | - | 1.06 | 0.52 | 0.25 |
Grootte van gewone normaal na malen/mm | 604.74 | 604.98 | 605.04 | 605.06 |
Fig. 12 Vak- en lijndiagram van verschillende oplaadmethoden en vervorming tijdens warmtebehandelingsprocessen
Op basis van de ervaring die is opgedaan tijdens het prototypestadium is de tooling voor afschrikken en ophangen geoptimaliseerd van de oorspronkelijke eenpuntsondersteuning naar een tweepuntsondersteuning. Daarnaast is de ellips van het onderdeel teruggebracht van het oorspronkelijke bereik van 0,14-0,18 mm naar 0,05-0,10 mm.
Wat betreft de passing voor koude en warme verwerking, krimpt de algemene normaal van het onderdeel met ongeveer 0,25 mm na carboneren en afschrikken. Daarom moet vóór de warmtebehandeling een toeslag van 0,25 mm voor de normale hobbing worden gecompenseerd.
Als gevolg van deze verbeteringen zijn alle 30 tandwielen die in een kleine batch zijn geproduceerd nu gekwalificeerd.
1)Voor vlakke tandwielen is het belangrijk om ervoor te zorgen dat alle punten op het eindvlak gelijkmatig ondersteund worden tijdens het carboneren. Om de vervorming van het eindvlak door kruip tijdens horizontale carbonering te verminderen, kan de afstand tussen de oorspronkelijke vier honingraatschijven worden gewijzigd in de volledige plaatsing van acht honingraatplaten.
2) Het hangende gereedschap wordt gebruikt voor het afschrikken. Door aan de onderkant van de afschrikplaat een maasdempend gereedschap toe te voegen, wordt de relatieve stroomsnelheid van de afschrikplaat verhoogd. koelmedium en onderdelen wordt verminderd. Dit resulteert in een aanzienlijke vermindering van tandvervorming in het onderste gedeelte van het hangende gereedschap.
3) Om spanning en kruip bij hoge temperatuur tijdens de warmtebehandeling van vlakke tandwielen te verminderen, kan de carboneertemperatuur worden verlaagd, de temperatuurstijgingsstap worden verhoogd, de isothermische tijd worden verlengd en de carboneertemperatuur worden verlaagd.
4) Door de warmtebehandelingslading en het warmtebehandelingsproces te verbeteren, is de vervorming van het tandwieleindvlak verminderd van 1,06 mm tot 0,52 mm. De steekcirkelafloop is teruggebracht van 0,18 mm naar 0,1 mm en de tandvervorming is verminderd met ongeveer 40%. Deze verbeteringen hebben geresulteerd in een kwalificatiesnelheid van 100% voor de productie van kleine series.