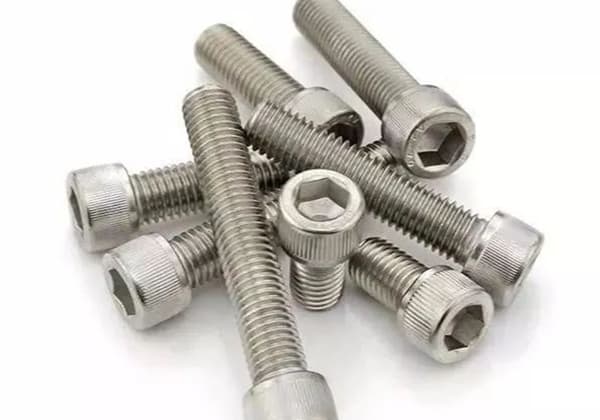
Why is choosing the right hexagon bolt so crucial? Outer hexagon bolts and inner hexagon bolts may seem similar, but their differences in structure, cost, and application can significantly impact your project. This article breaks down their unique features and helps you decide which bolt is best for your needs, whether you’re looking for strength, ease of assembly, or aesthetic appeal. Get ready to enhance your fastening choices and ensure your projects are both efficient and effective.
Currently, hexagon bolts are extensively utilized in the fastener industry. In comparison to straight and cross heads, hexagon bolts offer better assembly due to their reduced slipping tendency, and they also provide high torque.
Furthermore, hexagon bolts have a simple structure and are cost-effective when compared to dodecagonal and multi-tooth head bolts.
Therefore, hexagon bolts have a higher comprehensive price and are the most commonly used type of bolts in automobiles.
Hexagon bolts can be classified into two types: inner hexagon bolts and outer hexagon bolts. What distinguishes these two bolts, and how should one choose between them when applying them?
This article introduces the structure, cost, tightening tools, advantages, disadvantages, and application scope.
Structurally, hexagon socket-head cap screws and outer hexagon bolts are easy to distinguish. There is basically no difference in the threaded part. The outer hexagon refers to the hexagon-shaped head, which has no depression.
To increase the bearing area of the head, outer hexagon flange bolts can also be used. This variant is widely used. The outer edge of the head of the hexagon socket bolt is round, and the middle is a concave hexagon. The most common type is the cylindrical head hexagon, but there are also pan head hexagon socket, countersunk head hexagon socket, and flat head hexagon socket.
Headless screws, stop screws, machine screws, and other similar items are called headless socket cap screws. Hexagon socket bolts can also be made into hexagon socket flange bolts to increase the contact area of the head.
To control the friction coefficient of the bolt head or improve the anti-loosening performance, outer hexagon combination bolts and inner hexagon combination bolts can also be used. These are illustrated in the figure below.
Socket head cap screws and hexagon socket bolts usually have their threads formed by screwing. The screwing plates used for both are essentially the same, and there is no significant difference in cost between them.
However, the head manufacturing process for these two types of bolts is different. Due to the distinct head structures, different molds and processes are required for each.
The manufacturing cost of the hexagon socket bolt’s head is higher than that of the hexagon socket thread due to the differences in manufacturing process.
In my experience, the outer hexagon bolt’s cost is only half that of the inner hexagon bolt.
It can be divided into two parts: assembly in life and production.
For assembly in life, the wrench shape for hexagon socket bolts is “L” shaped, with one side longer than the other. The shorter end is used to screw while holding the longer end can save effort and tighten screws better.
The outer hexagon bolt requires a wrench with an equilateral hexagon head, such as an adjustable wrench, ring wrench, or open-end wrench. As shown in the figure below, you may be familiar with the following two tools if you’ve done daily assembly or maintenance at home.
In order to meet the requirements of tightening quality and automation, assembly in production will be carried out using fixed torque wrenches and high-precision tightening guns. This requires the corresponding tightening sleeves to be matched.
The outer hexagon bolt requires a concave hexagon sleeve, while the inner hexagon bolt requires a convex hexagon sleeve. As shown in the figure below, a series of sleeves will be provided to match the size of the bolt head.
Outer hexagon bolts/screws:
Hexagon socket head bolts/screws:
The outer hexagon bolt/screw:
Hexagon socket head bolts/screws:
It is the advantages and disadvantages of outer hexagon bolt and inner hexagon bolt, so how to choose them in the application?
If a large axial force is required at the tightening point, meaning that the tightening torque is high, and there is sufficient external space for tightening, then an outer hexagon bolt should be used.
However, if there is limited space at the tightening position or a need for a countersunk head to enhance aesthetics, and the axial force required for tightening is small, meaning the tightening torque is low, a hexagon bolt can be used instead.
To illustrate, let us consider a car’s subframe and body connection point, where multiple bolts pass through the subframe’s bottom and tighten onto the body. As the bottom is not visible and has no aesthetic requirements, and there is no hindrance in tightening, a high axial force and torque are necessary (bolts are tightened after yielding).
Therefore, for this connection position, it is recommended to use outer hexagon bolts for tightening.
The interior trim connection is a visible area for the customer and usually requires aesthetic considerations. As such, a countersunk head structure is necessary, and the top of the bolt head must align with the connected part’s structure or be covered with an additional layer of parts.
Furthermore, the required axial force and torque for tightening in such positions are low. Therefore, hexagon socket bolts or screws are highly suitable for fastening in these scenarios.
If you are unsure about how to choose, it will depend on whether the connection position requires an elegant appearance and has limited assembly space. In such cases, it is recommended to choose hexagonal socket bolts/screws.
Otherwise, the outer hexagon bolt/screw can be selected. It is cost-effective and can meet most other requirements.
This explains why outer hexagon bolts/screws are more commonly used than inner hexagon bolts/screws.
Hexagonal-head bolts/screws are widely used in various industries due to their simple structure, convenient usage, moderate price, and ease of tightening.
There are two types of common hexagonal-head bolts/screws: outer hexagon and inner hexagon. The head structure of the two can be clearly distinguished.
In terms of cost, the outer hexagon is half the price of the inner hexagon bolt. Additionally, the tightening tools used for both types have different lifespans and production methods.
Based on the advantages and disadvantages of the two, it is recommended that socket head bolts/screws be selected if the connection position requires delicacy, beauty, and limited assembly space. However, if there are no such requirements, then the outer hexagon head bolt/screw should be chosen.